1. INTRODUCTION
The decreasing availability of fossil fuels, which are nonrenewable energy sources, is a critical concern. Concurrently, the dependence on fossil fuels is rising owing to urbanization, industrialization, and population growth, which have led to increased public consumption (Ibitoye et al., 2021). Global energy consumption has reached 15.100 million tons of oil equivalent, predominantly from fossil fuels (EIA, 2022). Recent data indicate that fossil fuels account for approximately 80% of global energy demand. The extensive exploitation and consumption of fossil fuels has led to severe environmental issues, including greenhouse gas emissions and environmental degradation (Ortega-Ramirez et al., 2022). These environmental impacts underscore the urgent need to address the declining availability of fossil fuels and develop renewable, sustainable, clean, and environmentally friendly energy sources. The transition to renewable energy is crucial for mitigating environmental degradation, ensuring clean environments, and promoting healthy living conditions (Ibitoye et al., 2021).
Despite the potential uses of biomass, its application faces challenges. A primary concern is balancing land use between food production and biomass cultivation. Energy crop cultivation does not compromise food security, particularly in developing regions (He et al., 2024; Nemethy and Szemethy, 2019). Additionally, the logistics of biomass collection, transportation, and processing present significant hurdles, particularly in remote areas with underdeveloped infrastructure (Nemethy and Szemethy, 2019). Integrating biomass production with existing agricultural and forestry practices can mitigate some of these issues and create a synergistic relationship that enhances food and energy security (Shanmugam et al., 2024). Moreover, the environmental impact of biomass energy depends heavily on the sustainability of the biomass feedstock. Unsustainable harvesting practices can lead to deforestation, soil degradation, and biodiversity loss (Cao and Wyatt, 2020; Nemethy and Szemethy, 2019; Shanmugam et al., 2024). Therefore, implementing sustainable management practices is crucial to ensure that biomass production does not negatively impact the environment. Life cycle assessments have been extensively used to evaluate the environmental impacts of biomass energy systems and to develop strategies for minimizing negative outcomes (Kikuchi et al., 2020).
In Indonesia, more than 90% of the electricity is generated by coal-fired power plants, which rely on fossil fuels and are not environmentally friendly (Perkasa et al., 2023). To address this issue, the state-owned electricity company Perusahaan Listrik Negara is exploring biomass-based energy as a potential alternative. However, the use of wood for biomass production is not feasible due to the risk of deforestation. As a significant amount of unproductive land remains underutilized in Indonesia (Nurfaizah et al., 2023; Rakuasa et al., 2024), this study aimed to identify shrub species suitable for producing biopellets for co-firing in existing coal-fired power plants. Co-firing, which involves substituting a portion of coal with biomass, offers a promising pathway for reducing carbon emissions and effectively utilizing local biomass resources (Roy et al., 2024).
Various alternative energy sources, such as solar, wind, geothermal, and biomass energy, have been researched and developed. Biomass is a highly profitable energy source because of its abundant availability and rapid renewability (Qizi, 2020; Tareen et al., 2018). Biomass is derived from lignocellulosic organic materials, including forestry products, agricultural by-products, and plantation residues (Siregar et al., 2020). In addition to being plentiful and renewable, biomass is environmentally friendly. Indeed, Siregar et al. (2020) noted that gas emissions from biomass-based fuels are readily absorbed by plants, enhancing their ecological benefits.
Biomass utilization as a renewable energy source often takes the form of pellets known as biopellets. Biopellets are produced by processing biomass into a powder, which is then dried and compressed at high temperature and pressure to form uniform pellets. In Indonesia, biopellets used for power generation must comply with the quality standards set by Indonesian National Standard (SNI) 8951:2020, which require a high calorific value linked to the high carbon content of lignocellulosic materials. Additionally, the raw materials for biopellets should be easy to cultivate and should undergo rapid growth cycles.
The distance between biomass sources and power plants can be prohibitive due to high transportation costs. Therefore, the selection of shrub species is critical for ensuring the feasibility and sustainability of biopellet production for co-firing purposes. This study aims to fill gaps in the research by investigating the properties and potential of four Indonesian shrub species to contribute to the broader goal of enhancing Indonesia’s renewable energy portfolio and reducing its reliance on fossil fuels. In particular, this study explored lignocellulosic materials from shrub species with short rotation periods that are promising for the development of biomass-based fuels suitable for co-firing in electric steam power plants. The goal was to identify the potential of these natural materials as alternative renewable energy sources and to support efforts to reduce fossil fuel use in electricity generation.
2. MATERIALS and METHODS
Branches with a diameter of 3–5 cm of four lesser-known shrub species [bungur {Lagerstroemia speciosa (L.) Pers.}, locong {Ganophyllum falcatum Blume}, latte {Myrsine avenis (Blume) A.DC.}, and terasa {Mischocarpus sundaicus Blume}] from a local community forest in Indonesia were selected as the primary raw materials for producing biopellets. Additionally, paring bamboo (Gigantochloa atter) was selected for comparison because of its high growth rate and availability in nature, which is almost the same as that of shrubs. This bamboo has been widely used as a raw material for biopellets in various studies. The initial densities of these raw materials were 0.78, 0.68, 0.81, 0.65, and 0.64 g/cm3, respectively. The measured moisture contents were 7.14%, 8.70%, 7.34%, 8.11%, and 8.31%, respectively.
To prepare the materials, raw shrubs and bamboo were cleaned to remove contaminants such as dirt, stones, and other foreign materials that could negatively affect biopellet quality. After cleaning, the raw materials were naturally dried under sunlight to further reduce their moisture content and maintain environmental sustainability by avoiding additional energy consumption (Hendrik Sanjaya et al., 2024).
Once dried, the shrubs and bamboo were processed into a powder using milling equipment. Initially, the hammer mill broke larger pieces into smaller fragments. This ensured that the materials were manageable for further processing. Subsequently, a ball mill was used to ground the fragments into a fine powder. The ball milling process is critical because it enhances the uniformity and surface area of the powder, which is essential for producing high-quality biopellets (Abdul Latif et al., 2019).
After milling, the resulting powder was passed through a 100-mesh (150 μm) sieve to ensure uniform particle size. The fine powder collected during this process was used for biopellet production. Consistent particle size is vital for the densification process because it affects the mechanical properties and combustion efficiency of biopellets (Yusuf and Inambao, 2019).
Biopellets were produced by compressing the prepared powder into specific shapes and sizes using a hot press. Initially, 4 g of powder from each shrub and bamboo material was carefully measured and placed in a mold. The conditions for imprinting biopellets are listed in Table 1, which outlines the parameters used during the pressing process.
Parameter | Conditions |
---|---|
Pressure | 25 kg/cm2 |
Pressing time | 60 s |
Temperature | 200°C |
The hot press machine was set to apply a pressure of 25 kg/cm2 for 60 s at 200°C. These conditions were chosen based on preliminary tests and existing literature to ensure optimal densification and mechanical stability of the biopellets (Hendrik Sanjaya et al., 2024).
During the pressing process, high pressure and temperature cause the lignin in the biomass to soften and act as a natural binder, which helps bind the particles into a solid form. The application of heat also reduces the moisture content and improves the durability of the biopellets (Mather et al., 2024).
The target dimensions for the biopellets were a diameter of 16 mm and length of 20 mm. Achieving a consistent size and shape is crucial for ensuring uniform combustion properties and handling characteristics in co-firing applications (Hendrik Sanjaya et al., 2024). After pressing, the biopellets were allowed to cool and harden to form a dense and compact structure suitable for power generation.
The produced biopellets, as depicted in Fig. 1, were subjected to a series of quality assessments, including density, moisture content, ash content, and calorific value measurements, to ensure that they met the SNI (8951: 2020) requirements for biomass fuels. These quality checks are essential to confirm the suitability of biopellets for use as renewable energy sources in co-firing processes.
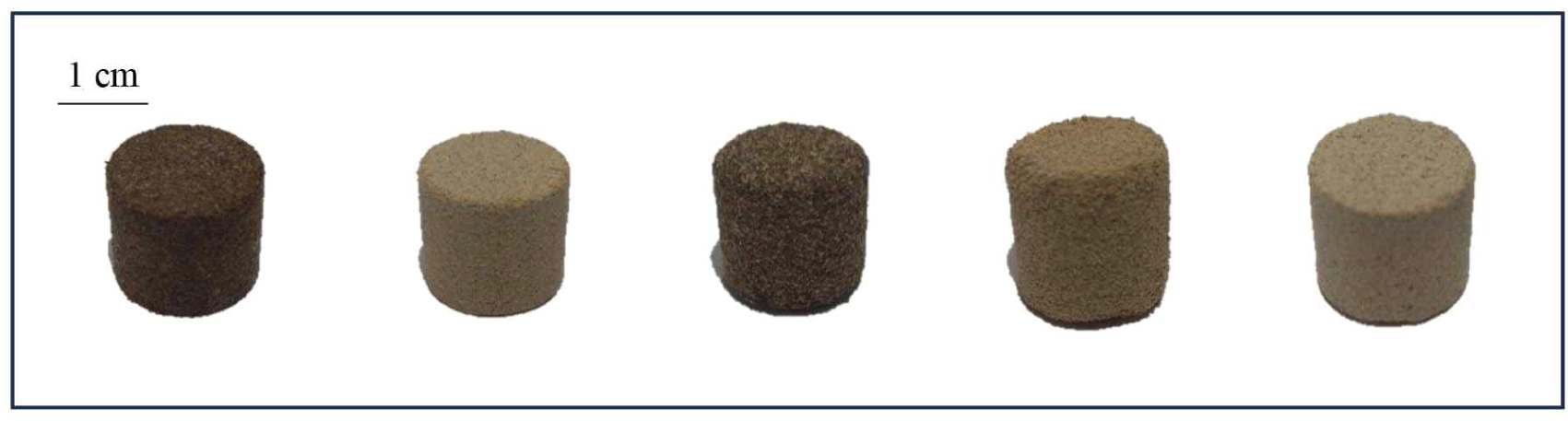
The quality of the biopellets was assessed according to the Indonesian National Standard SNI 8951-2020, which outlines the specific requirements for biomass fuels (Table 2). Quality tests included measurements of density, ash content, moisture content, volatile matter content, fixed carbon content, net calorific value, potassium content, sodium content, and total sulfur content. In addition, the burning rate of the biopellets was tested to evaluate their combustion performance and longevity.
Density: The density of the biopellets was measured to ensure they met the minimum requirement of 0.5 g/cm3 as specified by SNI 8021. High-density biopellets generally exhibit better combustion efficiencies and energy content.
Ash content: The ash content, which should not exceed 4%, was determined using the SNI 06-3730 method. Lower ash content is preferable because it results in less residue and cleaner combustion.
Moisture content: The moisture content was tested according to SNI 01-1506 and limited to a maximum of 12%. A low moisture content is crucial for efficient energy release during combustion and for preventing mold growth during storage.
Volatile matter content: The volatile matter content was assessed using the SNI 06-3730 standard, with a maximum allowable limit of 70%. This parameter affects the ease of ignition and the combustion characteristics of the biopellets.
Fixed carbon content: The fixed carbon content, which should be at least 14%, was tested using the SNI 06-3730 method. A higher fixed carbon content indicates better fuel stability and energy density.
Net calorific value: The net calorific value, a critical parameter for evaluating the energy content of biopellets at constant pressure, was determined using SNI 01-6235. The minimum requirement was 4,040 kcal/kg.
Potassium (K2O) and sodium (Na2O) contents: The potassium and sodium contents were measured in terms of K2O and Na2O to ensure that they did not exceed 20% and 5%, respectively, as outlined in SNI 8951. High levels of these elements can cause slagging and fouling of combustion equipment.
Total sulfur content: The total sulfur content, which should not exceed 0.01%, was assessed to ensure compliance with SNI 8951. A low sulfur content is essential for minimizing SO2 emissions and reducing environmental impacts.
Burning rate: Burning rate tests were conducted to investigate the burning performance and lifetime of biopellets. This involved measuring the mass loss of the biopellets in grams per minute during combustion. The tests were performed in a furnace at 950°C for 7 min. The burning rate provides insight into the combustion efficiency and duration of biopellets under high-temperature conditions (Sutanto and Jelita, 2024).
By adhering to these stringent quality standards, the biopellets produced from the selected shrub species and bamboo were evaluated to ensure their suitability as renewable energy sources for co-firing applications. This contributes to sustainable energy solutions for Indonesia (Sutanto and Jelita, 2024).
3. RESULTS and DISCUSSION
Fig. 2 shows that the density of the biopellets produced met the SNI requirements for utility purposes. Similar findings were reported by Hajad et al. (2023) and Yunianti et al. (2024) for biopellet production using shrubs such as Calliandra tetragona, Lantana camara, Chromolaena odorata, Leucaena leucocephala, and Gliricidia sepium, finding that biopellets from these shrubs provided a density ranging from 0.6 to 1.3 g/cm3, depending on the production method and particle size of the raw material. The high density of the biopellets was caused by a reduction in porosity owing to the small particle size of the raw material (< 0.15 mm), which led to smaller gaps between the biopellet particles (Sutanto and Jelita, 2024). Previous research has shown that a biomass particle size below 100 mesh (< 0.15 mm) results in low ash content, high calorific value, and high carbon content (Ju et al., 2020).
As shown in Fig. 2, M. sundaicus biopellets had the highest density, whereas G. falcatum biopellets had the lowest. Despite the similar weight of the raw material and volume of the molding tool used for both shrubs and bamboo, the density of the generated biopellets varied. This variation was attributed to the springback effect of the biopellet immediately after the compression load was removed. This phenomenon also reported during wood compression treatment at high temperatures was observed in this study (Yunianti et al., 2019). The height of the mold was set at 20 mm; however, M. sundaicus and G. atter biopellets measured 21 mm in length, compared to 24 mm for G. falcatum and L. speciosa biopellets, indicating a higher springback. Thus, it can be concluded that a higher springback results in a lower density. This finding aligns with that of Ratnasingam et al. (2022), who reported that springback increases with wood density, thereby affecting the overall density of the compressed material.
Recent studies have highlighted the importance of particle size and compression conditions in determining the density and quality of biopellets. For instance, Mather et al. (2024) found that smaller particle sizes and higher compression pressures lead to higher densities and better mechanical properties of biopellets. Additionally, Lee et al. (2019) confirmed that optimizing the particle size and compression parameters significantly improved the density and combustion efficiency of the biopellets.
The results of the ash content measurements in Fig. 3 show that the ash content of the biopellets produced from all materials tested met the SNI requirements for utility purposes. A low ash content in shrub biopellets (L. leucocephala and G. sepium) was also reported by Yunianti et al. (2024), ranging from 1.7% to 2.7%. The ash content of shrub biopellets (C. tetragona, L. camara, and C. odorata) studied by Hajad et al. (2023) was lower, ranging from 0.5% to 0.6%. This indicated that each type of shrub contained varying amounts of ash.
Additionally, shrub-derived biopellets have a lower ash content than those derived from bamboo. This finding is consistent with that reported in Yang et al. (2021), which found that bamboo generates higher ash content than wood, potentially causing serious technical safety problems during the combustion process.
Among the raw materials tested in this study, the biopellets produced from M. avenis had the lowest ash content. This suggests that using M. avenis as a source for biopellet production can minimize the negative impact of ash. Additionally, a low ash content is associated with a high calorific value and carbon content (Eka Putri and Andasuryani, 2017; Iskandar et al., 2019; Muzakir, 2017).
Compared to recent studies, Abdul Latif et al. (2019) biopellets with lower ash content typically exhibit improved combustion efficiency and reduced emissions, supporting the suitability of M. avenis for high-quality biopellet production. Furthermore, Hendrik Sanjaya et al. (2024) highlighted that a lower ash content in biomass fuels can significantly enhance their thermal properties and reduce the maintenance frequency in combustion systems, which is consistent with the findings of this research.
The results in Fig. 4 show that the moisture content of the biopellets produced from shrubs and bamboo met the SNI requirements for utility purposes. Compared to the moisture content of shrub biopellets in previous studies, which ranged from 4.9% to 7.0% (Hajad et al., 2023; Yunianti et al., 2024), the moisture content of the shrub biopellets in this study was slightly lower, ranging from 3.2% to 5.7%. There are a lot of possible factors that influence the difference in moisture content, including the moisture content of the raw materials, shrub species, and the storage conditions of the biopellets.
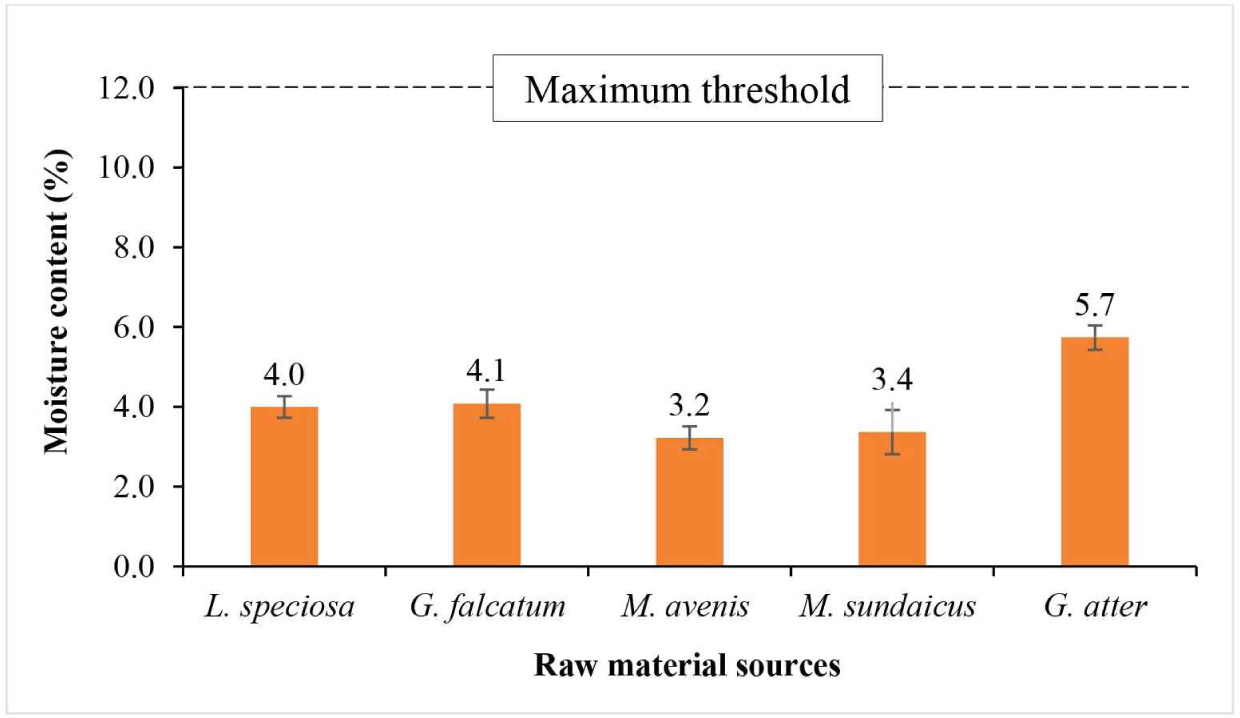
The moisture content of the shrubs and bamboo was reduced by approximately 30%–60% after pelletization. This significant reduction was due to the high temperatures (200°C) used in the biopellet production process, which degraded the free hydroxyl groups of the primary chemical components of the raw material. Consequently, the hygroscopicity of the biopellets decreases. Consequently, the hygroscopicity of the biopellets decreases. Lower moisture content results in faster ignition times, indicating better quality and increased profitability for consumers (Tun et al., 2020).
Previous studies reported that the moisture content of biopellets negatively affects their mechanical properties, making them more susceptible to damage (Cubero-Abarca et al., 2014; Hendrik Sanjaya et al., 2024). Among the five raw materials tested, the biopellets made from M. avenis had the lowest moisture content, whereas those made from Paring bamboo had the highest. Nonetheless, the felt shrub also needs to be considered a good raw material, as it had a slightly higher moisture content than M. avenis but exhibited the greatest reduction in moisture content during pelletization.
Fig. 4 also shows that raw materials from shrubs produced biopellets with a relatively lower moisture content than those from bamboo. This aligns with the findings of other recent studies. For instance, San Juan et al. (2018) reported that lower moisture content in biomass pellets leads to improved combustion efficiency and stability. Additionally, Ahmad Fauzy et al. (2023) found that optimizing the drying process and controlling the moisture content are critical for enhancing the durability and performance of biomass pellets.
The results of the test for the volatile matter content of the biopellet products indicate that the volatile matter content of the biopellets was slightly above the maximum threshold required by SNI (Fig. 5). The same phenomenon was observed in biopellets made from shrubs of L. leucocephala, G.sepium, C. tetragona, L. camara, and C. odorata. Shrub biopellets have been reported to produce volatile substances ranging from 73.5% to 74.4% (Hajad et al., 2023; Yunianti et al., 2024). These results suggest that the five materials tested have the potential to cause excessive air pollution. Therefore, further studies are needed to explore methods for reducing the volatile matter content of the biopellets produced in this study, such as pre- and post-treatments at high temperatures.
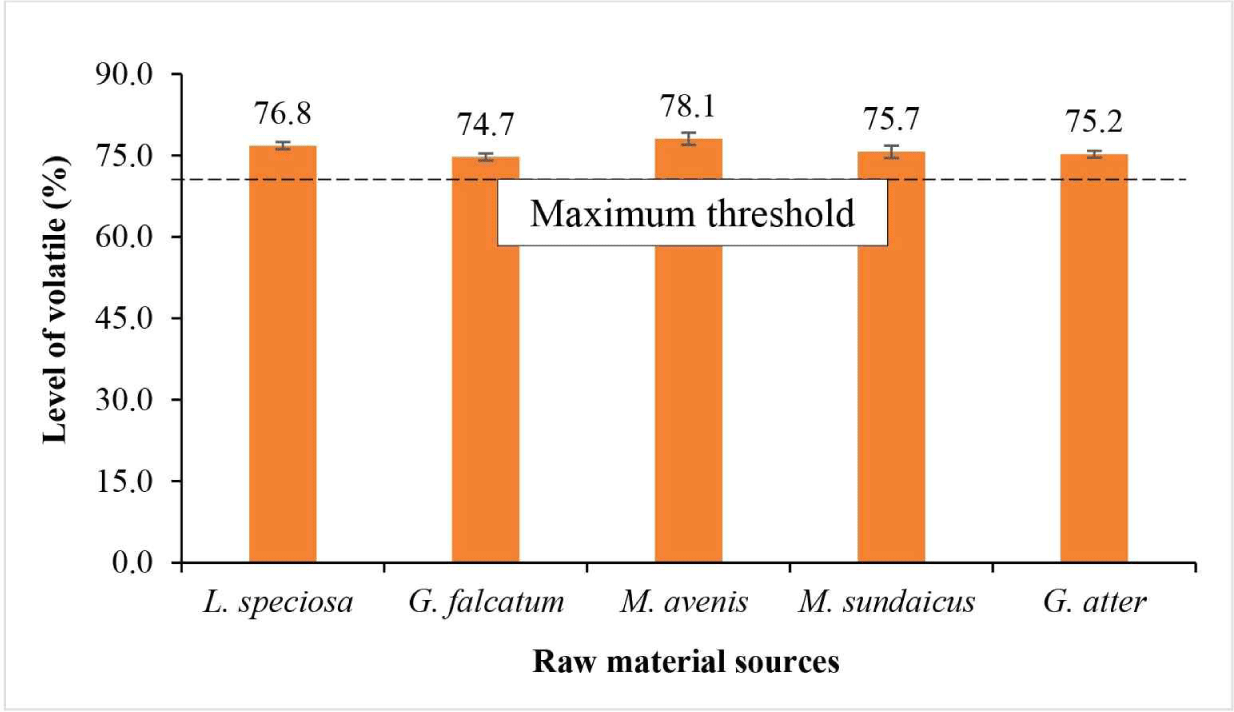
A high organic matter content, including carbon, hydrogen, and oxygen, in biomass is reported to cause high levels of volatile matter (Ibitoye et al., 2021; Jamradloedluk and Lertsatitthanakorn, 2017; Kansai et al., 2018; Lee et al., 2019). The high levels of volatile matter in biomass-based raw materials present a significant challenge for their utilization as energy sources.
Chen et al. (2019) found that reducing the volatile matter content in biomass pellets can improve combustion stability and reduce emissions. Additionally, Nugraha and Hantoro (2019) determined that pretreatment processes, such as torrefaction, can significantly lower the volatile matter content in biomass, enhancing its suitability for energy production. Further research is required to address the high volatile matter content observed in biopellets in this study.
The fixed carbon content of biopellets from the five types of raw materials tested in this study was above the minimum threshold required by SNI for the utility product category (≥ 14%; Fig. 6). M. sundaicus had the highest fixed carbon content (18.0%) among the raw materials tested. These results are similar to those reported by Hajad et al. (2023) and Yunianti et al. (2024), where the fixed carbon content of shrub biopellets produced from L. leucocephala, G. sepium, C. tetragona, L. camara, and C. odorata ranged from 18.7% to 18.9%. Previous research has attributed the high carbon content to the high lignin content of biomass, as lignin contains more carbon than other primary components of wood, such as cellulose and hemicellulose (Jeguirim et al., 2014).
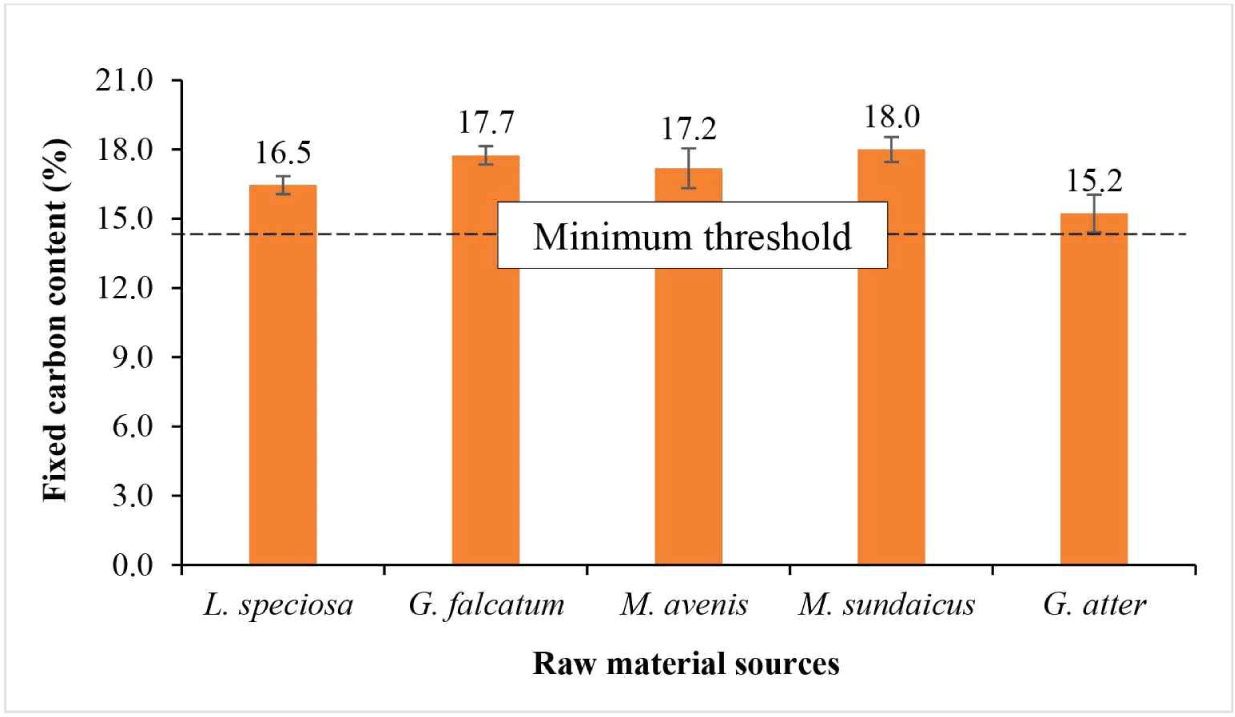
A high fixed carbon content in biopellets is beneficial because it indicates better energy density and combustion efficiency. Recent studies support these findings. For instance, Mather et al. (2024) found that biomass with a higher lignin content tended to produce biopellets with higher fixed carbon content and improved thermal properties. Similarly, Sutanto and Jelita (2024) demonstrated that optimizing the lignin content of biomass materials could significantly enhance the fixed carbon content, thereby improving the overall performance of biopellets.
Among the raw materials tested, M. sundaicus stood out due to its high fixed carbon content, making it a promising candidate for high-quality biopellet production. This aligns with the results of recent research, emphasizing the role of lignin in enhancing the fixed carbon content and thermal stability of biomass fuels (Ahmad Fauzy et al., 2023).
Although the carbon content of the biopellet samples produced in this study met the SNI requirements, the calorific value was slightly below the minimum threshold required by the SNI for the utility product category (4,040 kcal/kg). This contrasts with previous studies which reported that biopellets made from shrubs of L. leucocephala, G. sepium, C. tetragona, L. camara, and C. odorata provided slightly higher calorific values, ranging from 4,204 to 4,682 kcal/kg (Hajad et al., 2023; Yunianti et al., 2024). The differences in the amounts of lignin and extractives in the biomass caused this phenomenon.
The low calorific value produced in this study might have been caused by the low content of lignin and extractives in the shrubs, as the calorific value of biomass is highly dependent on the amount of these chemical components. As reported by Rahman et al. (2013), the lignin content in shrubs is only approximately 6% of the dry weight, whereas in wood, it is approximately 21%–29%, depending on the type of wood. Furthermore, although there has been no research reporting the amount of extractives in shrubs, there was no indication of odor or color in the presence of flammable extractives in the raw shrubs used in this study.
Fig. 7 shows that the calorific value of biopellets produced from shrubs tended to be higher (3,776 kcal/ kg) than that of biopellets produced from bamboo (3,694 kcal/kg). This is because shrubs retain most of the chemical characteristics of wood, whereas bamboo is mostly composed of starch stored in the parenchymal tissue.
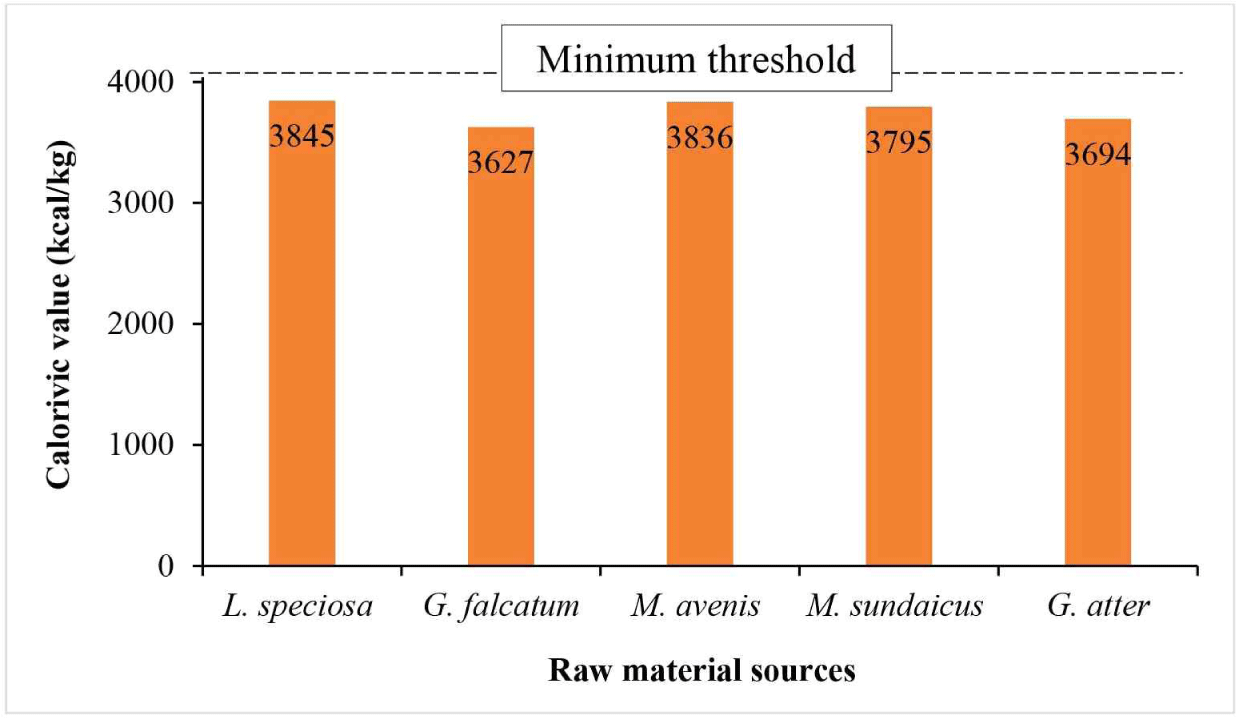
M. avenis and L. speciosa had almost the same calorific value, at 3,836 and 3,845 kcal/kg, respectively, which were higher than those of the other tested materials. To increase the calorific value of biopellets from M. avenis and L. speciosa to meet the SNI requirements, it is recommended to mix them with other raw materials, such as coconut shell waste (4,634 kcal/kg), that provide a higher calorific value (Ahmad Fauzy et al., 2023).
Recent studies have highlighted the importance of optimizing the blending of raw materials to enhance the calorific value of biomass pellets. For instance, Triani et al. (2022) demonstrated that mixing high-calorific-value materials with lower-value ones could significantly improve the overall energy output of biomass pellets. Additionally, Hendrik Sanjaya et al. (2024) demonstrated that incorporating of agricultural residues with high calorific value can enhance the combustion efficiency and calorific value of biopellets.
Biomass contains various minerals in quantities smaller than those in its primary components. Some of these minerals such as potassium (K2O), sulfur (S), and sodium (Na2O) are harmful to the environment. Therefore, the National Standardization Agency of Indonesia has set maximum limits for the contents of these minerals, as presented in Table 2. Fig. 8 shows that the amount of K2O in all biopellet raw materials tested in this study was very low compared with the maximum amount permitted by SNI (20%). The average amount of K2O in the biopellet samples produced from shrubs was the same as that produced from bamboo (0.26%). These values were much lower than those for shrub biopellets from L. leucocephala (1.5%) and G. sepium (2.9%) reported by Yunianti et al. (2024). For this quality parameter, M. avenis showed the best results, with the lowest K2O content (0.18%) among the biopellets.
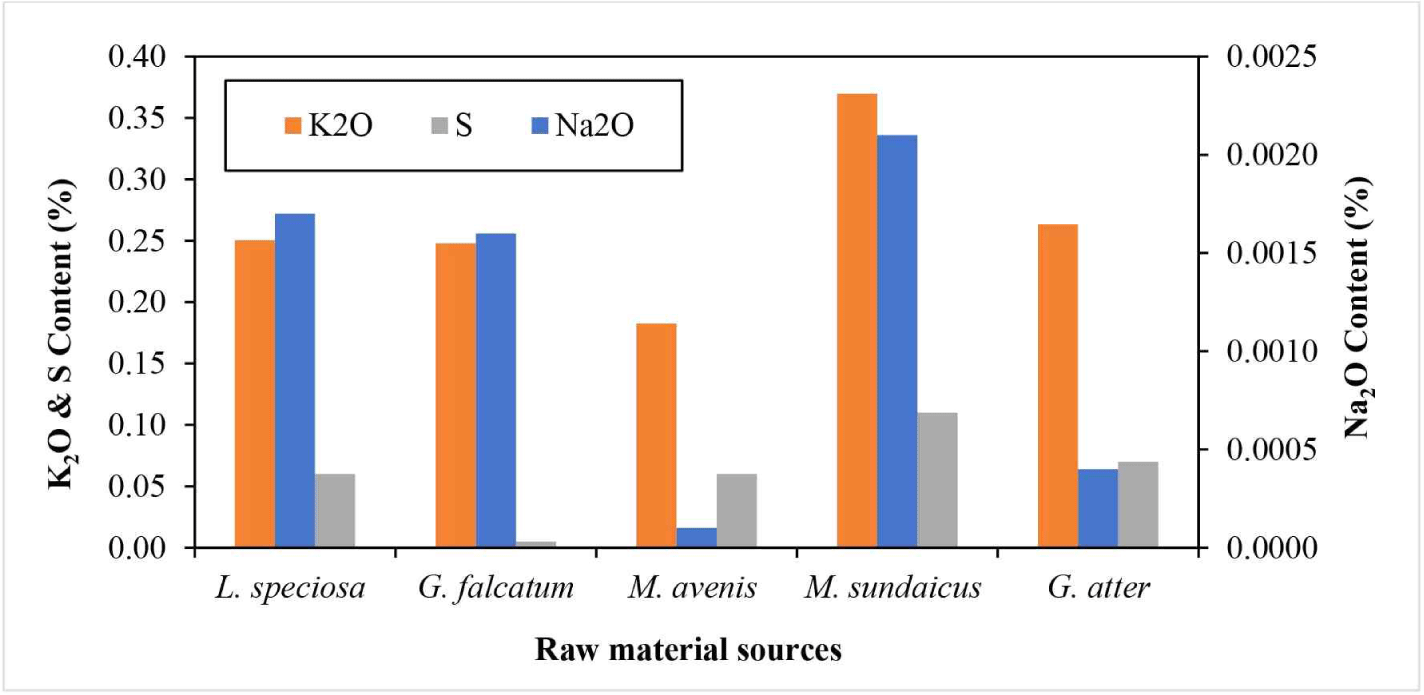
Compared to K2O, the amount of S in the biopellet samples was lower. The average S content in the shrub biopellets was approximately 0.06%, whereas that in the bamboo biopellets was approximately 0.07%. Although the amount of S in the shrub biopellets was lower than that in the bamboo biopellets, both met the SNI requirements (0.1%). G. falcatum biopellets had the lowest S content among all samples tested.
However, analysis of the Na2O content showed impressive results. Both the shrub and bamboo biopellets had Na2O amounts far below the maximum threshold permitted by the SNI (5%). M. sundaicus biopellets had the highest Na2O content, whereas M. avenis had the lowest. Although all the tested materials met the SNI requirements, M. sundaicus produced the highest levels of K2O, S, and Na2O.
Recent studies have highlighted the importance of minimizing the mineral content of biomass to reduce environmental impacts and improve combustion efficiency. For example, Hendrik Sanjaya et al. (2024) reported that lower potassium and sulfur contents in biomass fuels reduce slagging and fouling in combustion systems. Additionally, they emphasized that controlling the mineral content, especially that of potassium and sodium, is crucial for enhancing the thermal stability and emission characteristics of biomass pellets.
Fig. 9 shows that shrub biopellets had a higher burning rate (0.39 g/min) than bamboo biopellets (0.36 g/min). A high burning rate indicates that biopellets burn more easily and quickly. Although the carbon content of the shrubs was higher than that of the bamboo (Fig. 6), they burned faster. Specifically, L. speciosa and M. avenis had higher carbon levels than other biopellet materials (Fig. 6) but burned faster (0.42 and 0.41 g/min, respectively) than G. falcatum (0.38 g/min), M. sundaicus (0.38 g/min), and G. atter (0.37 g/min). This result contrasts with that of Mendoza Martinez et al. (2019), who reported that high carbon content indicates a low burning rate.
This phenomenon is attributed to variations in density and moisture content between the material sources. Higher density and moisture content resulted in a slower burning rate. As presented in Figs. 1 and 3, G. atter biopellets had high moisture content and density, leading to a slower burning rate. In contrast, M. avenis had the lowest moisture content among the tested materials, which resulted in a higher burning rate. Although G. falcatum exhibited the lowest density, its high moisture content resulted in a relatively low burning rate.
Recent studies have also examined the impacts of moisture content and density on the burning rate of biopellets. For instance, Nugraha and Hantoro (2019) found that biopellets with lower moisture content and higher density tend to burn faster owing to their reduced ignition resistance and more efficient combustion. Similarly, Jiang et al. (2020) reported that optimizing the moisture content and density of biomass pellets can significantly enhance their combustion performance, which supports the findings of this study.
4. CONCLUSIONS
The shrub and bamboo biopellets met the quality parameters of density, moisture content, ash content, carbon content, and mineral content required by the SNI. The biopellets from shrubs were superior, exhibiting higher density, lower moisture content, lower ash content, higher fixed carbon content, and higher calorific values than the bamboo biopellets. The volatile and mineral contents of the shrub and bamboo biopellets were relatively similar.
Different shrub species exhibited advantages. For example, L. speciosa generated the highest calorific value (3,845 kcal/kg), G. falcatum had the lowest volatile matter (74.7%) and sulfur content (0.005%), and M. sundaicus exhibited the highest density (0.85 g/cm3) and fixed carbon content (18%). However, M. avenis was the most promising overall, with the lowest moisture content (3.2%), ash content (1.5%), K2O content (0.18%), and Na2O content (0.0001%) and a relatively high calorific value (3,836 kcal/kg). These characteristics make it a strong candidate for co-firing. Such biomass sources can be developed on unproductive land owned by communities near steam power plant sites.
Unfortunately, the volatile matter and calorific value of both the shrubs and bamboo did not meet the SNI requirements. Therefore, further research is needed to reduce the levels of volatile matter in shrubs and increase their calorific value. Moreover, the addition of other materials that meet the SNI requirements, such as wood, should be considered as an alternative to increase the calorific value and reduce volatile matter in shrub biopellets.