1. INTRODUCTION
Wood possesses certain characteristics that make it a unique material. Studies have confirmed that qualitative characteristics exhibit endogenous, age-related, and interspecific variabilities (Ikonen et al., 2008; Jagodziński et al., 2014; Poorter et al., 2012). The properties of the individual products obtained from the wood biomass also changed significantly. This resource can be divided into the following key types of raw materials used in industry: stem wood, woody greenery (including the most valuable needles), bark, roots, and branches.
The trunk of a tree is the most valuable resource in the forestry industry. It is used to produce lumber, plywood, and furniture. The remaining waste is recycled and used to produce various products. One of the priority areas of waste processing in wood-processing enterprises is the production of various composite materials. One of the most common solutions is the production of fiberboard using a wet production method. This method of obtaining materials is more environmentally friendly than the dry method. This is because of a significant decrease in the use of harmful binder materials in the form of phenol-formaldehyde resins. In some cases, these resins can be completely eliminated. Notably, this is only possible for woody biomass of coniferous wood species.
This composite material is distinguished by specific properties that make it more competitive than lumber, plywood, and other sheet materials. The most important qualitative characteristics are the resistance to changes in humidity in the environment and almost equivalent properties in different directions (inside the board). More importantly, the inclusion of various additives in the material can provide unique characteristics, such as strength and fire resistance.
To date, the most widespread production of fiberboard is the dry-and-wet method. Using the dry method of plate production, technological chips are ground in a single step in a disk refiner. The result is a coarse-ground fibrous mass with a high content of non-ground fiber bundles. Such wood-fiber semi-finished products have weak binding properties, which necessitate the use of phenol-formaldehyde resins that reduce the environmental friendliness of the obtained products. Using the wet method of fiberboard production, chip grinding is performed in two stages on a defibrator and then on a refiner. The resulting wood-fiber semi-finished product does not contain unpolished fiber bundles. The fibers are long and have a well-fibrillated surface, which explains the high binding properties that allow the use of resins in some cases. This feature of the production of semi-finished wood fiber from chips in two stages of grinding allows companies such as Gutex and Pavatex to produce insulating materials with high environmental friendliness without the use of phenol-formaldehyde resins.
The challenge of increasing the efficiency of the forest industry, particularly logging, has been studied by many researchers (Lipiäinen et al., 2022; Novak et al., 2011; Sumardi et al., 2020). At the same time, the directions of scientific research are extremely wide: obtaining new products, improving the quality of existing products, optimizing logistics, increasing forest productivity, and changing the ways of caring for forest plantations. Furthermore, the role and importance of forests in implementing the principles of sustainable development, conservation of natural ecosystems, and maintenance of the quality of life of society are universally recognized (Aussenac, 2000; Chien et al., 2023; del Río et al., 2017; Wang et al., 2023).
Logging leaves many valuable resources in forested areas. These volumes vary significantly depending on the technology and availability of forest plots. In Russia, the logging waste is not used to produce valuable products. However, the prospects for both the technological and economic aspects of this area are significant. According to the author, tree greenery is one of the most valuable resources, and its involvement should provide a powerful impetus for the development of the industry.
Wood needles are used in various fields in the forestry industry. In addition to traditional forest chemical applications, they are used in the production of building structures, pulp and paper, energy, and other areas (Ghosh and Ghosh, 2011; Lal et al., 2013). From an economic perspective, the production of composite materials with wood greenery can be considered one of the most effective solutions. Individual technical solutions have also been presented in the scientific literature (Gupta et al., 2010; Singha and Jyoti, 2013; Sinha et al., 2018). At the same time, if for some materials wood greenery is one of the possible elements of the structure, then its use as a component in others is allowed in extremely limited quantities.
This aspect is regulated by the standards for the production of individual products and quality certificates. However, in addition to the theoretical possibilities of involving this valuable resource in production, there are also practical possibilities. The volume of wood greenery is not involved in the production of composite materials because of the absence of processing enterprises specializing in the production of acceptable products near the places of formation. This highlights the need to explore the possibility of using wood greenery in the production of various materials that have traditionally made little use of this resource. Within the framework of this study, the possibility of using coniferous wood greenery in fiberboard production was investigated.
2. MATERIALS and METHODS
The basis for conducting the experimental studies was technological chips that meet the requirements of GOST 15815-83 “Technological chips. The technical conditions are shown” (Fig. 1). This standard is used throughout Russia to obtain composite materials in the form of fiberboards using a wet production method. Chips were obtained under laboratory conditions using a drum-chopping machine (Fig. 2).
The results of many years of research by the team of authors and the analysis of literary sources indicate the dependence of the qualitative parameters of wood fiber and fiberboard based on the type of wood. Consequently, this study was conducted per the optimal parameters for steaming and grinding chips (tested under both laboratory and industrial conditions). The raw materials were wood waste generated during the sawmilling process and low-quality wood. The species composition corresponded to coniferous wood by 93 ± 3.4%.
The fractional composition of the chips is 2.5 ± 0.5 cm. Based on a series of experiments, this characteristic was determined to be optimal. It should be noted that the stability of the fractional composition leads to a higher board quality owing to the uniformity of the hydrothermal treatment. This parameter was strictly controlled throughout the study period.
The raw material in the form of a semi-finished wood fiber product was obtained under production conditions in RT-50 defibrators and RR-50 refiners at one of the largest timber enterprises in Russia. This method of production was used because of the desire to be close to the production conditions and characteristics of the process. During the production of the semi-finished product, the following optimal parameters were used for the defibrator and refiner: the gap between the grinding discs was 0.1 mm, the feed screw speed was 12 revolutions per min, and the concentration of wood fiber in the second stage of grinding was 2.5%. These characteristics were established based on previous comprehensive research conducted by the authors.
It should be noted that the experiment was conducted under real production conditions, necessitating an assessment of the wear of the grinding system. The analysis revealed that the study was conducted with system wear in the amount of 40%–50%.
Five semi-finished wood-fiber samples were prepared to ensure the accuracy of the experiment. The characteristics were evaluated in parallel. Sampling took place at least 2 h apart, which ensured a change in the fiber mass of more than 80%.
Wood greenery test samples were obtained from trees of different ages (young, mature, and overgrown). Four twigs were selected from twenty trees of different species from the lower, middle, and upper parts of the crown. The following species were used in the study: fir, Siberian pine, spruce, and pine, which grow in the Angara-Yenisei district of the Krasnoyarsk Territory (Russia). To eliminate unwanted impurities, the twigs and greenery were washed with water. The length and moisture content of the obtained samples were measured.
The raw materials for the additive to the fiberboard were used in three ways: after separation of essential oils (extraction of the oils contained in the woody greens by steam), separation of essential oils, and extraction with petroleum ether without additional chemical treatment.
Essential oils from woody greenery were isolated by a standard hydro distillation method under atmospheric pressure using Clevenger devices. The yield was determined volumetrically, taking into account its dissolution in the cubic residue and recalculated by the mass of absolutely dry raw materials; in the experiments, 200 g of raw materials and 500 mL of water were used.
The extraction was performed under laboratory conditions in a Soxhlet apparatus using petroleum ether (Fig. 3). A direct series of extraction experiments was conducted for 3 h with 50 g of woody greenery and 250 mg of petroleum ether.
The raw materials were dried in drying cabinets in special boxes to a moisture content of 10%–15%, which made it easier to grind and obtain materials for direct addition to the fiberboard.
The moisture content (W) in the studied samples (%) was determined using the following formula:
Where A is the mass of an empty box (g); B is the mass of the box with woody greenery before drying (g); C is the mass of the box with woody greenery after drying (g).
The woody greenery was crushed experimentally (Fig. 4). This machine allows the grinding of wood (and other) raw materials to a fraction of less than 0.2 mm (Fig. 5).
The woody greenery was separated into fractions using a solid particle fractionator (Fig. 6).
Fractionated raw materials from woody greenery (Fig. 7) were used as additives for wood fiber mass.
A series of experiments were conducted under standard and uniform conditions. Using coniferous raw materials allowed the possibility of abandoning a binder in the form of phenol-formaldehyde resin. Two additional components were used: paraffin emulsion and sulfuric acid (p = 1.834 g/cm3, t = 18°C). The first was used to provide water resistance to the composite material, and the second was used as a precipitator.
The final parameters of the pressing mixture used to produce the composite materials are listed in Table 1.
Component | Mass fraction, % of absolutely dry matter |
---|---|
Wood | 82–97 |
Aqueous solution of sulfuric acid | 1.0 |
Paraffin emulsion | 1.0 |
Woody greenery of coniferous species | up to 16 |
During the series of experiments, several factors were not controlled (Table 2).
The formation of a fiberboard carpet in the form of a felting process occurred at a laboratory casting facility (Fig. 8). Felting was accompanied by cold pre-pressing, which was necessary for approximating the production conditions.
Hot pressing of the board was performed using a two-story laboratory hydraulic press (Fig. 9).
The fiberboard made with the help of a laboratory press has dimensions of 250 × 250 × 2.5 mm.
Standard-size samples were obtained from the materials to assess their physical and mechanical properties. The analysis was conducted in the laboratory of an industrial enterprise that evaluates finished products intended for consumers.
The physical and mechanical parameters of the fiberboard were determined using standard methods developed for quality control of the products and the production process. The dimensional and physicomechanical characteristics of the finished board (density, tensile strength under static bending, water absorption in 24 hours, swelling in thickness in 24 hours) were determined according to GOST 19592-80 “Fiberboard. Test methods”. This standard is used by all specialized enterprises in Russia.
Density Pl, kg/m3, was calculated with an accuracy of 10 kg/m3 using the following formula:
Where m is the sample mass (kg); where L, B, and S are the length, width, and thickness of the sample, respectively.
The tensile strength during static bending of the fiberboard was determined by the stress at which the prototype collapsed under the action of the bending force. This parameter is a key indicator for assessing the quality of a composite material.
The bending strength, Pr, MPa, with an accuracy of 0.1 MPa, was determined by the formula:
Where P is the loading force acting on the sample at the moment of destruction and N.
l: the distance between the centers of the supports (mm), b: sample width (mm), h: sample thickness (mm).
Water absorption in 24 h, S, %, with an accuracy of 0.1 %, is determined by the formula:
Where m is the mass of the sample before immersion in water (g); m2 is the mass of the sample after extraction from the water (g).
The swelling in the thickness of the sample at 24 h, R, %, was calculated with an accuracy of 0.1% according to the formula:
Where h is the thickness of the sample before immersion in water (mm); h1 is the thickness of the sample after extraction from water (mm).
The obtained results were used for further evaluation and construction of statistical and mathematical equations.
The general scheme of the conducted research is shown in Fig. 10.
The assessment of physical and mechanical parameters was carried out following GOST 4598-86 Fiberboard for group B plates: bending strength, from 33 MPa; thickness swelling in 24 h, up to 23%; density — 800–1,100 kg/m3, water absorption in 24 h, not normalized; humidity, up to 10%, the thickness of the plate is 2.5 ± 0.3 mm.
3. RESULTS and DISCUSSION
The best indicators of the physical and mechanical properties of fiberboard were obtained by adding woody greenery, which underwent procedures for extracting oils with steam (fir-making) and petroleum ether.
The highest yield of essential oils from woody greenery was obtained from fir tree greenery (Grebner et al., 2022; Pankiv et al., 2012). The results of a study on the dependence of the yield of essential oils and lipids on the location of the crown and the age of the tree as a whole are of significant industrial interest and are presented in Medvedev (2011). However, a series of experiments assessing the effect of age and endogenous variability on board quality parameters showed that these factors had practically no effect on the final results.
This is due to the pretreatment of woody greenery, which leads to the extraction of substances (oils and lipids) that can affect the binding abilities during the formation of fiberboard. At the same time, boards obtained with unprocessed greenery containing many substances tend to be stratified and therefore cannot be used for their intended purpose. Consequently, the experimental data on the stratified boards were excluded from the results presented in this paper.
To establish the regularities of the influence of the needle particle size and their content in the fibrous mass on the physical and mechanical properties of the finished board, a two-factor experiment according to the second-order B-plan was planned and implemented to optimize the studied process. The values of the studied parameters, according to the experimental plan, varied in the following ranges: (4 ± 0.1) ≤ q ≤ (16 ± 0.11) %; (0.2 ± 0.01) ≤ f ≤ (0.8 ± 0.02) mm.
The results of the experiments conducted by the authors are presented in Table 3.
The data obtained were processed using Statistica and the quasi-Newton method.
The regression dependencies describing the effects of the particle size of the needles and their content in the fibrous mass on the physical and mechanical parameters of the board are as follows:
The significance of the coefficients presented in the models was assessed using Student’s t-test, corresponding to generally accepted methodological approaches. Verification of the models using Fischer’s F-test demonstrated their adequacy. The natural designations of these factors are indicated in the proposed models. This allows for a detailed and visual analysis of the results obtained, and practical applications (testing in real production conditions).
Obtaining the presented regression equations is required for several reasons:
-
A reliable description of the processes under study.
-
Determine the magnitude of the impact of the control factors necessary to compensate for the influence of disturbances and stabilize the output factors of the process under study.
-
Calculation of the values of various parameters of the resulting composite materials.
To visually demonstrate the results obtained, as well as for a better analysis of the dependencies of various fiberboard parameters on the content of needles in the total mass and particle sizes of the needles, three-dimensional models were constructed. These represent the response surfaces, are reflected in Figs.
From the graphical dependence shown in Fig. 11, the size of the needle particles has little effect on the density index of the fiberboard, which increases slightly from 945 kg/m3 to 980 kg/m3 with an increase in the size of the needles particles from 0.2 mm to 0.8 mm. With an increase in the content of needles in the total weight from 4% to 16%, the density of the fiberboard systematically increased, reaching 1,140–1,150 kg/m3. The increase in the density of the board with an increase in the needle content in the total mass and the size of its particles was attributed to the increase in the mass of the fiberboard while maintaining the geometric dimensions.
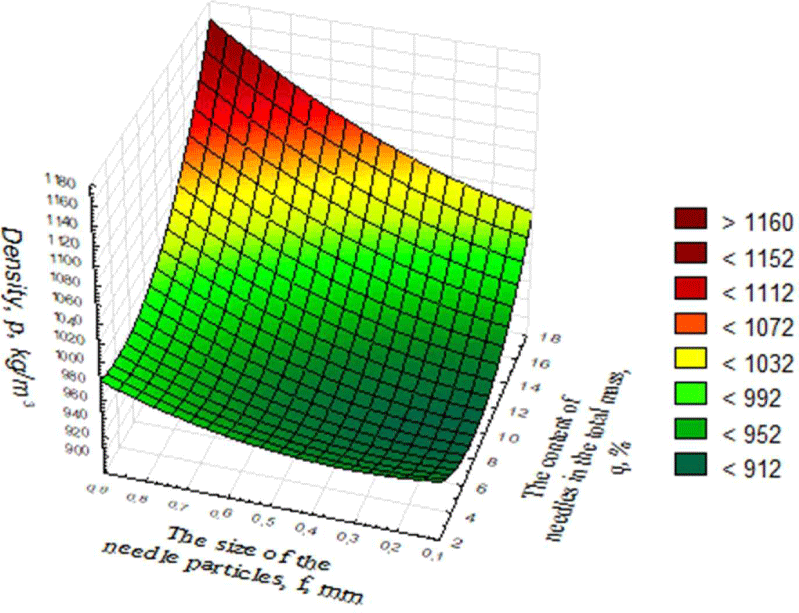
The increase in the value of the density index of the fiberboard with an increase in the addition of coniferous wood greens is primarily due to the fact that the needles fill the empty inter-fiber space in the body of the slab acting as a filler. This helps preserve the geometric dimensions of the plate while increasing its mass.
The analysis of the information presented in Fig. 12 shows that as the particle size of needles increases from 0.2 mm to 0.4 mm, the strength index of the fiberboard tends to decrease, reaching 19–20 MPa. With a further increase in the particle size of the needles to 0.8 mm, there was a slight increase in strength, reaching 23–24 MPa. As the content of needles in the composite material increased from 4% to 8%, the strength increases to 43–44 MPa.
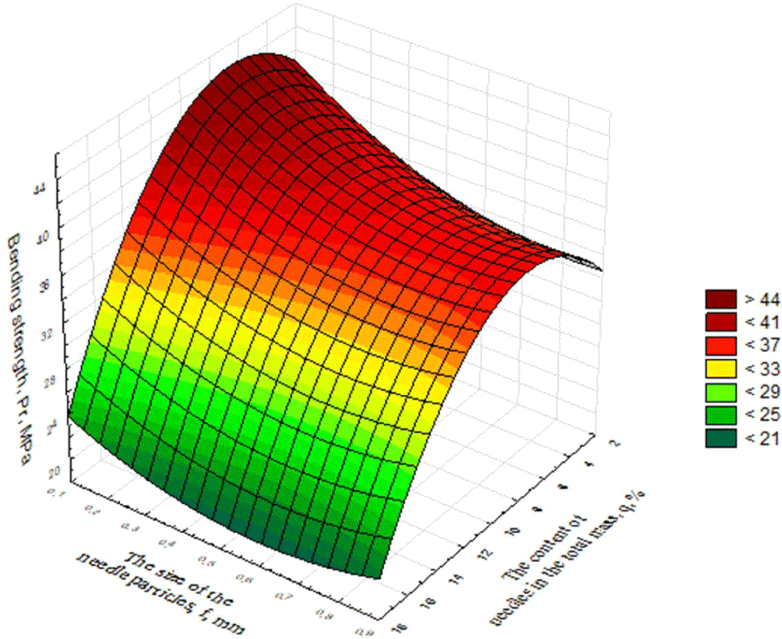
However, a further increase in the addition of needles (up to 16%) led to a sharp drop in strength to 25–26 MPa. The maximum values of the strength index of the fiberboard are explained by the fact that needle particles with a size of 0.4–0.6 mm in an amount of 8%–10% are able to form adhesive bonds with wood fiber and act as a binding material, which is clearly demonstrated by the photo presented in Fig. 13.
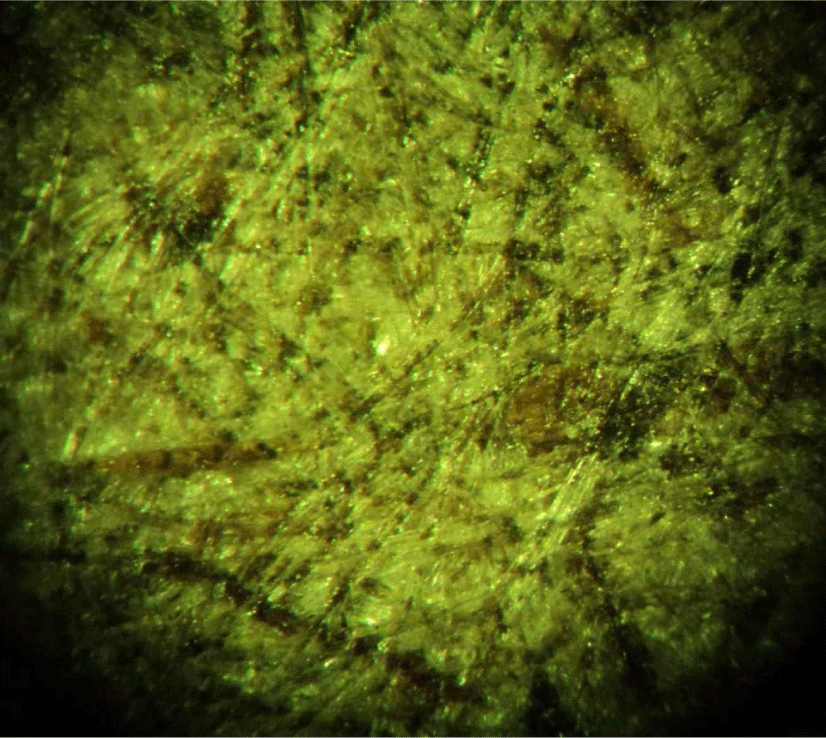
With a further increase in the particle size of needles and its content in the total mass, needles begin to act as a filler without participating in bond formation, as can be seen in the photo shown in Fig. 14. This leads to a decrease in the strength index of the fiberboard.
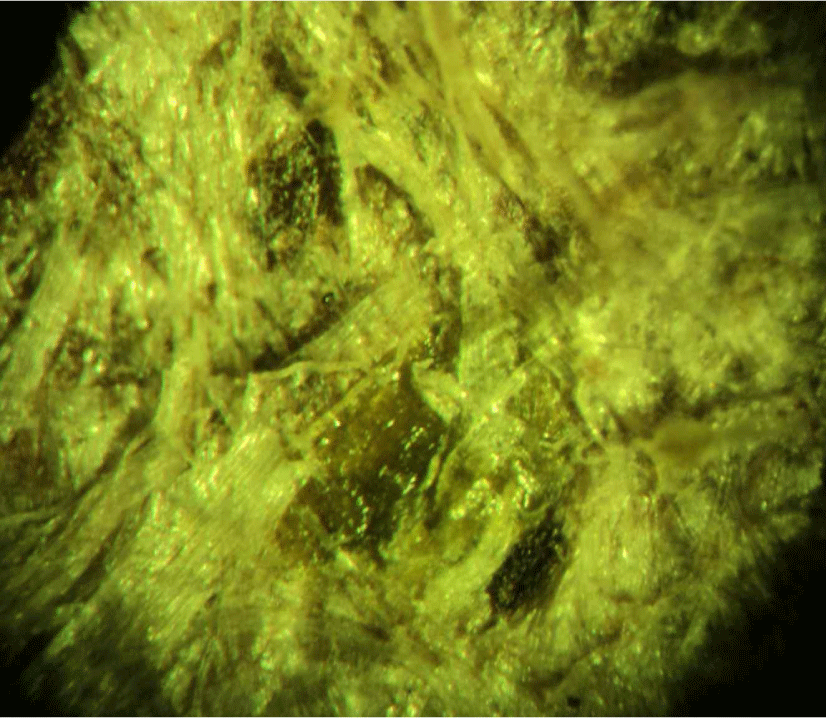
The analysis of the information presented in Figs. 15 and 16 indicates that the values of the swelling and water absorption of the board at 24 h tended to decrease, reaching 10%–12% and 20%–22%, respectively, with a content of 6%–10% of the total weight of needles. At the same time, with an increase in the size of the needle particles, there is a slight deterioration in the indicators of water absorption and thickness swelling of the fiberboard in 24 hours. This is due to the fact that needles, comprising up to 10% of the total weight, participate in bond formation, preventing water from entering the body of the board and causing stratification.
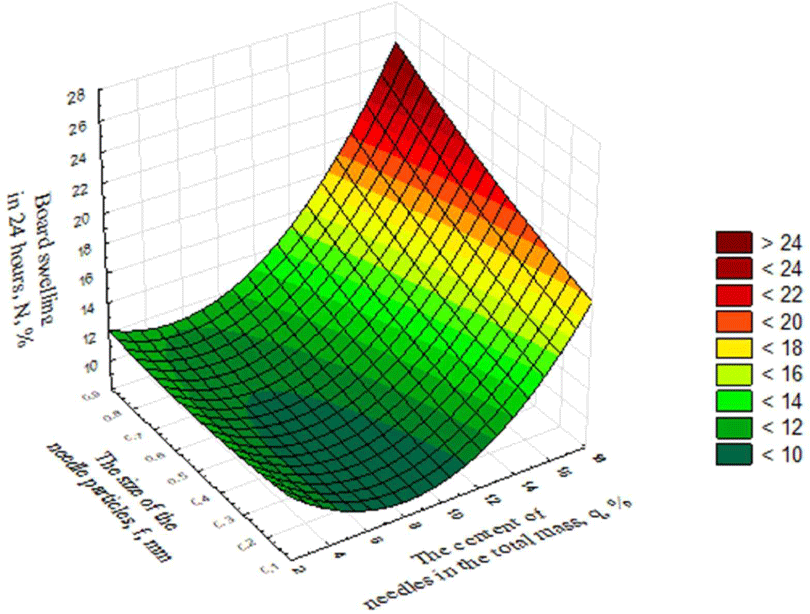
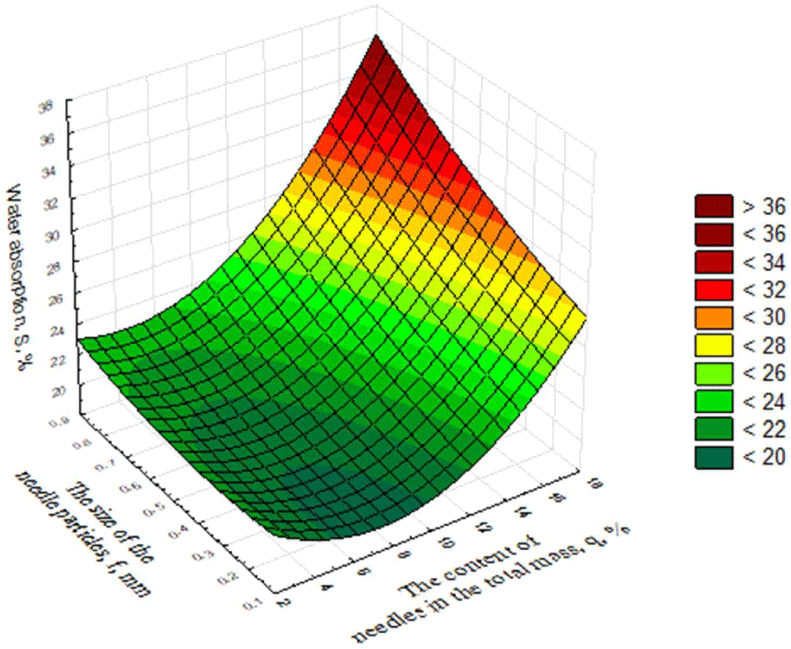
An analysis of the addition of various materials to wood pulp during the production of fiberboards to impart specific properties showed that Antonov et al. (2011) increased the fire resistance of boards by adding vermiculite. Ribiy and Petrusheva (2019) increased the insulating properties of boards by adding coniferous bark. Morozov (2016) in his research proposed increasing the strength of fiberboard by adding recycled sawdust.
During the research it was established that coniferous wood greenery has found its wide application in agriculture, pharmacology and perfumery. However, only a small portion of this valuable renewable raw material has been applied. It was established that on average, 80% of wood greenery is utilized by means of burning or burial. Considering that wood fiberboard can be imparted various properties by introducing various additives, the feasibility of producing a board with pretreated needles was theoretically substantiated for the first time, which was confirmed in practice during the production of a batch of finished commercial products.
4. CONCLUSIONS
The indicators of the physical and mechanical properties of the fiberboard reach their maximum values with a particle size of 0.4–0.6 mm conifer needles and its content in the total mass of 8%–10%. As a result, the addition of crushed needles up to 10% of the total mass volume makes it possible to produce boards with excellent physical and mechanical properties, which expands the scope of their applications. Overall, the involvement of logging waste in board production positively affects the timber industry and increases the sustainability of its development.
Thus, the use of woody greenery after pretreatment by extraction (with water or other solvents). As a result, a closed production cycle is formed, where forest chemical production products (extraction of wood greenery) are obtained, and secondary wood raw materials (spent wood greenery) are used to produce composite materials (fiberboards).