1. 서 론
국내산 낙엽송은 우리나라의 임목축적의 12%를 차지하며 소나무 다음으로 공급량이 많은 수종으로 제재목의 가격은 소나무보다 약 40% 저렴하다 (Forestry Statistics Annual Report, 2017). 또한 국내 산 낙엽송(0.61)은 소나무(0.47)와 잣나무(0.45)에 비 해 비중이 높고, 휨 강도와 압축강도가 소나무와 잣 나무에 비해 약 1.3배 높으며(Forest and forestry technology, 2012), 나이테의 간격이 조밀하고 단단 하여 다른 수종들에 비해 병충해로부터 받는 피해가 적어 수명이 길다. 뿐만 아니라 국내산 낙엽송은 뛰 어난 내구성과 내수성을 가지며 잔가지가 적고 수간 이 통직하게 생장하여 장재 생산에 적합하고 그 용 도와 쓰임이 건축용 재료에 적합하다.
건축용 구조용재는 제작 길이에 제한이 없고 대단 면으로 제작이 가능하여야 여러 분야에 활용되고 자 유로운 설계가 가능하다. 대표적 공학목재인 집성재 는 층재를 종접합 한 후 적층하기 때문에 길이와 두 께에 제한이 없어 그 활용도가 높다. 낙엽송 소경각 재를 층재로 하는 소경 각재 적층목도 층재의 종접 합으로 장대재의 휨 부재 제작이 가능해지면 적층시 집성재보다 접착제 사용량이 적고 심미성이 우수한 고부가가치의 공학목재로 활용될 것으로 기대된다.
HIRST 등(2008)은 Oak 각재를 사용하여 Scarf joint 등 4가지 시험편을 제작 후 접착제를 사용하지 않고 직경 19 mm Wood pin을 수직 또는 수평으로 삽입 후 휨 강도 실험을 실시하였다. 실험결과 Lap joint와 Hooked scarf joint 시험편이 가장 우수한 휨 성능을 보였다. 낙엽송 집성재에 봉형 GFRP를 삽입 하고 접착제로 목재와 간극을 충진시켜 실시한 인발 시험에서는 폴리우레탄 접착제를 사용하였을 때보다 에폭시 접착제를 사용하였을 때 우수한 성능을 보였 고, 에폭시 접착제를 사용하여 접착층 두께 2 mm, 선 공깊이 7D로 제작하였을 때 가장 우수한 성능을 보 였다(Jung 등, 2015). 그리고 Karastergiou 등(2005)이 European Spruce를 사용하여 실시한 Scarf joint의 각 도에 따른 성능 비교 실험은 joint의 경사비 1.75/1일 때 가장 우수한 성능을 발휘하는 것으로 보고되었다.
목재를 이용한 종접합 연구는 Finger joint와 Scarf joint 등 기본 구조에 한정되어 있다. 또한 판재, 층 재 등의 비교적 작은 시험편을 사용한 연구들이 주 로 진행되어 소경각재의 종접합에 대한 데이터가 부 족한 실정이다.
따라서 본 연구에서는 소경각재의 종접합 방법으로 접합물을 사용하지 않은 스카프 조인트 등의 4가지 형상의 시험편과 봉형 GFRP를 삽입한 2가지 형상의 시험편을 제작하여 종접합 내력 성능을 검토하였다.
2. 재료 및 방법
공시재료로는 평균 기건 비중 0.52, 평균 함수율 16%의 국내산 낙엽송 소경각재(89 (T) × 120 (W) × 3600 (L) mm)를 사용하였다. 소경각재는 훈데거 사 의 K2i 1259 프리컷 가공기계(CNC: Computer numerical control)로 종접합부를 정밀 가공하였다(Fig. 1).
인장시험편은 길이 1200 mm, 표점거리 780 mm 표점부 단면적 60 × 89 mm가 되도록 가공하였다. 종접합 형상은 Fig. 2와 같이 6가지 종류로 각 유형 별 5개씩 총 30개의 시험편들을 제작하였다(Fig. 2).
Rod 시험편의 횡단면은 단거리와 연단거리의 길이 를 동일하도록 선공을 하였으며, 목질부와 봉형 GFRP (glass fiber reinforced plastic) 사이의 간극이 1 mm가 되도록 가공하였다(접착층 1 mm). 구멍의 깊이는 봉형 GFRP직경의 7배가 되도록 가공하였다. 직경 18 mm, 길이 252 mm의 봉형 GFRP를 에폭시 접착제를 사용하여 선공된 횡단면에 삽입 접착하였 다(Fig. 2-A). Rod + Lap 시험편은 Fig. 2-B와 같이 Lap 접합부 형상으로 가공한 후 각 횡단면 정중앙에 선공을 하였다. 선공 및 접착조건은 Rod 시험편과 동 일하게 하였다. Lap 시험편은 두께대비 2배 길이의 턱을 가공하였다(Fig. 2-C). Double Lap 시험편은 Lap 접합부 형상이 연속으로 가공된 형상이다. 첫 번 째 Lap 형상은 22.25 mm로 가공하였고 두 번째 Lap 형상은 44.5 mm 깊이에 22.25 mm 턱을 더 가공하였 다(Fig. 2-D). Scarf 시험편은 경사비 1.73 : 1로 가공 하였다(Fig. 2-E). Hooked scarf 시험편은 Scarf 시 험편과 같은 경사비로 제작한 후 Hooked의 깊이를 15 mm로 가공하였다(Fig. 2-F). 봉형 GFRP를 삽입 하지 않은 시험편들은 PRF (Phenol Resorcinol Formaldehyde)접착제를 사용하여 종접합하였다. 모 든 시험편은 일정한 압체압력으로 24시간 상온경화 하였다. Fig. 3은 프리컷 가공된 인장시험편의 횡단 면 사진과 종접합된 인장시험편의 모식도이다.
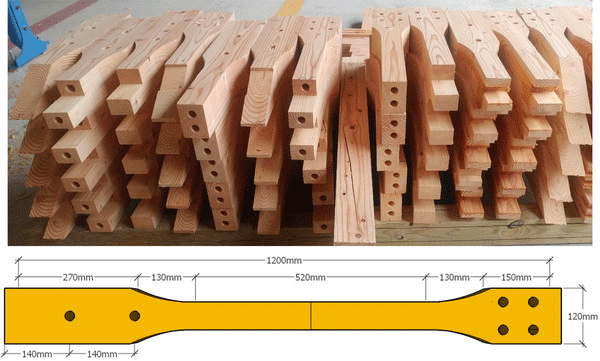
시험편은 Fig. 4와 같이 하단부 끝 단면부터 표점 부까지를 Stopper로 바닥과 고정하고, 상단부 끝 단 면부터 표점부까지 감싸는 치구를 설치하였다. 완성 된 치구는 30T 수직제하장치를 사용하여 분당 5 mm의 하중속도로 시험을 실시하였다. 인장강도는 다음 식으로 산출하였다.
σmax: 인장 강도(N), Pmax: 최대 하중(N), A: 접착 단면적(mm2)
휨 시험편들의 종접합 형상은 6가지로 각 유형별 3개씩 총 18개의 시험편을 제작하여, 대조군인 무종 접합 소경각재와 휨 강도 성능을 비교 검토하였다. 모든 시험편의 종접합 유형은 인장시험편과 동일하 며, Rod 시험편과 Rod + Lap 시험편은 단면적을 고 려하여 횡단면에 4개의 구멍을 가공하였다(Fig. 5). Lap 시험편과 Rod + Lap 시험편은 두께대비 3.5배의 길이로 턱을 가공하였다.
완성된 낙엽송 각재 종-접합 시험편은 Fig. 6과 같 이 3등분 4점 휨 강도 시험을 실시하였다. 경간은 2100 mm, 하중점간 거리는 700 mm로 하중 속도는 분당 10 mm로 실시하였다. 휨 파괴계수(MOR)는 다 음 식으로 산출하였다.
Pmax: 최대하중(N), L: 경간(mm), S: 하중 간 거리(mm), b: 시험편의 폭(mm), h: 시험편의 두께 (mm)
3. 결과 및 고찰
Table 1은 인장시험편들의 평균 최대접합내력 및 인장강도이며, Fig. 7는 시험편 형상별 파괴모드 사 진이다. Scarf 시험편은 접착층과 목질부 사이에서 계면파괴가 관찰되었다(Fig. 7-f). Hooked scarf 시험 편은 턱을 가공한 부분에서 목부파단이 발생하였다 (Fig. 7-g, 7-h). Lap 시험편은 Double Lap 시험편보 다 인장강도가 양호하였으며, Lap 시험편의 횡단면 을 제외한 접착면에서 95% 이상의 목부파단율이 관 찰되었다(Fig. 7-c, 7-e). Rod 시험편은 접착면의 계 면파괴 직전에 최대 인장강도가 측정되었다. Rod + Lap 시험편은 Rod 시험편보다 접착면적이 더 넓은 것에 기인하여 양호한 인장강도를 나타냈다. Scarf 시험편의 평균 인장강도가 7.1 MPa로 가장 양호하 였다.
Specimen |
Pmax Ave. (kN) |
Strength Ave. (MPa) |
COV (%) |
---|---|---|---|
Rod | 22.8 | 4.3 | 23.9 |
Rod + Lap | 32.5 | 6.1 | 18.6 |
Lab | 17.2 | 3.2 | 19.4 |
Double lap | 12.6 | 2.4 | 17.5 |
Scarf | 37.8 | 7.1 | 28.5 |
Hooked scarf | 29.1 | 5.4 | 30.8 |
종접합된 소경각재의 휨 강도 하중-변형 곡선은 Rod + Lap 시험편을 제외한 모든 시험편이 하중초기 부터 파괴될 때까지 소성역이 거의 나타나지 않고 탄성역이 주를 이루었다(Fig. 8). 종접합이 없는 대조 군 시험편의 평균 휨 파괴계수는 50 MPa, 평균 초기 강성은 544 N/mm로 측정되었다. GFRP rod를 횡단 면에 삽입한 시험편들이 비교적 우수한 휨 파괴계수 값이 측정되었다. Rod 시험편의 휨 파괴계수는 27 MPa로 대조군 시험편의 59% 강도 값이 측정되었다. Rod + Lap 시험편의 휨 파괴계수는 30.5 MPa로 대 조군 시험편의 66% 강도 값이 측정되어 모든 시험 편 중 가장 양호하였다. Rod를 삽입하지 않고 접착 제로만 종접합한 시험편들은 대조군 시험편 강도비 0.20~0.22의 휨 파괴계수 값이 측정되었다. Table 2.
휨 강도 시험편들의 파괴형상은 다음과 같다. 대 조군 시험편은 최외각 인장부위에서 초기파단이 발 생하였고 섬유방향으로 할렬이 진행되었으며, 일부 시험편은 압축부위까지 파괴가 진행되었다. 모든 시 험편들의 횡단면과 횡단면 접착부위는 접착층과 목 질부 사이에서 계면파괴가 발생하였다. Rod 시험편 은 횡단면 접착부위의 계면파괴 발생 후 봉형 GFRP 가 서서히 인발되었다. Rod + Lap 시험편은 중앙 접 착면의 목파와 봉형 GFRP의 인발이 동시에 진행되 었다. Scarf 시험편 경우 접착면의 접착층과 목질부 사이에서 계면파괴가 발생하였다. Hooked scarf 시험 편은 후크 부분에서 목파가 발생하였다. Lap 시험편 의 접선단면이 접착된 부분은 높은 목파율이 측정되 었다. Double lap 시험편의 경우 최외각 인장부의 접 착층이 파괴된 후 할렬이 진행되었다.
4. 결 론
낙엽송 소경각재를 이용하여 신뢰성 높은 대단면 장대재의 휨 구조재를 제작하기 위한 일환으로 층재 로 사용할 소경각재의 종접합 형상 및 접합성능 평 가를 실시하였다. 6가지 종접합 형상의 시험편을 제 작하여 인장 및 휨 강도로 성능을 검토하였다.
인장강도로 봉형 GFRP를 삽입 접착한 Rod 시험 편이 가장 양호하였다. 휨 강도 성능은 봉형 GFRP 를 삽입 접착한 Rod + Lap 시험편이 가장 양호한 성 능을 보였으며, 이는 무 종접합 각재의 강도비 0.66 에 해당하였다. 봉형 GFRP를 삽입 접착하는 종접합 방법은 균일한 접착 성능을 나타내고 있으나 Scarf 및 Hooked scarf 종접합 방법은 접착 접합 정밀도에 따라 접합 내력의 변동이 크고 접착작업의 용이성이 크게 떨어지는 것을 확인하였다. 또한 경사비를 크게 하는 가공이 용이하지 않으며 수율이 저하되어 소경 각재 종접합 방법으로서는 부적합 하였다. 소경 각재 종접합 방법으로서는 봉형 GERP를 삽입 접착하는 방법의 접합 내력 및 작업의 용이성이 양호한 것을 확인하였다.