1. INTRODUCTION
Recently, Korean traditional paper Hanji has garnered significant attention owing to its use in restoring dozens of world-class paper cultural heritage pieces in Italy and the Vatican. In particular, in 2018, the Italian Center for the Preservation and Restoration of Documentary Heritage (ICPAL) announced that it had restored Leonardo da Vinci’s “Codex on Bird Flight,” which is known to have been produced between 1503 and 1506, using Hanji (Lucilla, 2021). It is believed that the main reason Hanji was used in the restoration of these cultural heritage pieces is because of its durability, softness, and resistance to tearing (Poggi, 2016).
The term “Hanji” appeared in a newspaper “DaehanMaeilShinbo (大韓每日申報)” in 1908 (Bethell, 1908). During the Goryeo Kingdom, it was called “Goryeoji” in China and was reputed for its quality. Furthermore, the cultural flourishing during the Joseon Dynasty was achieved through the extensive use of Hanji, which served as the primary material for large-scale publications. However, there is limited information available in Korean records regarding the technological development or characteristics of Hanji manufacturing during ancient times. It was only recently that research on this topic picked up steam. Early Hanji studies were conducted on the relationship between the production and consumption of Hanji (Lee, 1958) and the paper industry during the Joseon Dynasty (Lee, 1962). It was not until the early 1990s that scientific research on materials used in Hanji began. Studies on Hanji material in the 1990s mainly focused on the mass industrialization of products such as wallpaper made from a blend of Broussonetia × Hanjiana (hereafter Daknamu) bast fiber and wood pulp. Additionally, efforts were made to produce Daknamu pulp by applying the wood pulping technology (Choi and Cho, 1996; Jo, 1995; Yoon et al., 1996, 1997). However, these studies fell short of fully capturing the production technology that embodies the unique characteristics of Hanji. It was not until the 2000s that research on Hanji gained momentum, and it can be broadly categorized into two main themes. The first theme revolves around the Hanji manufacturing process and the examination of its physical properties. The second theme delves into the quality analysis of Hanji and the contemporary status of Hanji usage through the analysis of ancient documents or relics. The former corresponds to the change in physical properties according to the raw materials of Hanji (Lee et al., 2021a, 2021b, 2012c), manufacturing process of Hanji (Cho et al., 2009; Seo et al., 2001; Yoon and Ra, 2013), comparative analysis of preservation characteristics (Ahn and Bae, 2018; Jeong et al., 2012, 2014a, 2014b; Kang and Yang, 2012; Park et al., 2009), analysis of natural dyeing characteristics (Chung, 1996; Jeon and Jin, 2000; Lee et al., 2015, 2016; Park and Yoon, 2009, 2010, 2011; Roh and Jo, 2022; Yoo et al., 2009; Yoon and Kim, 2002), and analysis of surface treatment characteristics (Hyun et al., 2005; Yoon, 2015). The latter is related to the Hanji and its industry in the Goreyo Kingdom (Park, 2010, 2011; Song, 2016) and Joseon Dynasty (Jeon, 2011; Kim, 2002; Lee, 1958, 1962; Park, 2012, 2017; Son, 2003, 2004, 2005, 2007), the situation of Hanji before and after the Japanese occupation period (1910–1945) (Park, 2019, 2023; Shinya, 1909; Song, 2008), and the rediscovery of Hanji (Roh et al., 2021a, 2021b, 2021c, 2021d, 2022a, 2022b, 2023). As described above, Hanji has gained an international reputation in recent years. However, the details regarding the evolution and changes in current Hanji manufacturing techniques are yet to be fully elucidated (Han and Lee, 2021a, 2021b; Han et al., 2021, 2022). Therefore, this study seeks to clarify the current development process of Hanji manufacturing techniques by analyzing manufacturing molds and processes and tracing their evolution since ancient times.
2. MATERIALS and METHODS
The Hanji manufacturing techniques and the related matters used during ancient times were analyzed using various types of historical records and artifacts.
The primary sources of data frequently employed in this study were various forms of literature. The historical changes in Hanji manufacturing were revealed by analyzing contents in the old literature related to Hanji. If necessary, the contents were supplemented by analyzing the relics simultaneously. In addition, the changes in Hanji manufacturing during the Japanese occupation period were investigated by searching articles published in various recording media.
The study utilized various types of data sources, including both Korean and foreign ancient literature, records from the Korean Empire to the Japanese occupation period, modern literature, and photographs.
Korean literature studied included Goryeosa (高麗史), Annals of the Joseon Dynasty Chosunwangjo-sillok (朝鮮王朝實錄), Donggukyeojiseungram (東國輿地勝覽), Ohjuyeonmunjangjeonsango (五洲衍文長箋散稿), Gyeonggukdaejeon (經國大典), Sanlimkyeongjae (山林經濟), and Takjijunjeol (度支準折). Regarding foreign literature, the books of Dard Hunter, a world-renowned authority on paper; books of Seki Yoshikuni (関義城), a Japanese authority on paper; and the writings of Panjixing (潘吉星), a Chinese historian, were used for the analysis.
Records from the Korean Empire to the Japanese occupation period include the reports of the government industrial training center (官立工業傳習所報告), the official gazette of the Japanese Government-General of Joseon (朝鮮總督府官報), the related publications, and newspaper articles during the Japanese occupation period.
Modern literature analyzed in this study mainly includes papers published in academic journals.
3. RESULTS and DISCUSSION
The rough process of Hanji-making includes harvesting Daknamu shoots, steaming, preparation of Black bark, preparation of White bark, boiling White bark, beating or fiberization, mixing the ingredients in a vat, making paper, and drying. On the basis of the related literature, the outline of the process has not changed significantly from ancient times. However, it was found that the types of raw materials, raw material pretreatment methods, chemicals, paper manufacturing molds, and drying methods have changed according to the trend of the times. These changes in Hanji-making process progressed slowly over a long period of time, but abrupt changes occurred during the period of Japanese occupation.
Daknamu shoots are steamed to facilitate the easy peeling of its bark, which serves as the raw material of Hanji. This process is called Dakmuji in Korean. In ancient times, steam generation was achieved through a traditional method of heating stones and pouring water onto them within a specialized facility. One of the traditional techniques involved placing Daknamu shoots on top of the heated stones, covering them with soil, and then covering the pile with soil for the steaming. Another way involves using a facility having two spaces in the shape of a gourd, connected by a narrow passage in the middle. In one of the two gourd-shaped spaces, Daknamu shoots are piled up followed by covering them with soil after covering them with pine branches. In the other space, a stone pile is made and a fire is built under it to produce heat, and then covered with soil and poured with water to steam. When steam is generated, it permeates into the adjacent space through a narrow passage in the middle, steaming the Daknamu shoots. Fig. 1 shows a traditional Daknamu steaming facility of traditional Hanji making, recreated in the exhibition hall of the Demonstration Culture Village in Bongsu-myeon, Uiryeong-gun, Korea (Lee et al., 2021c).
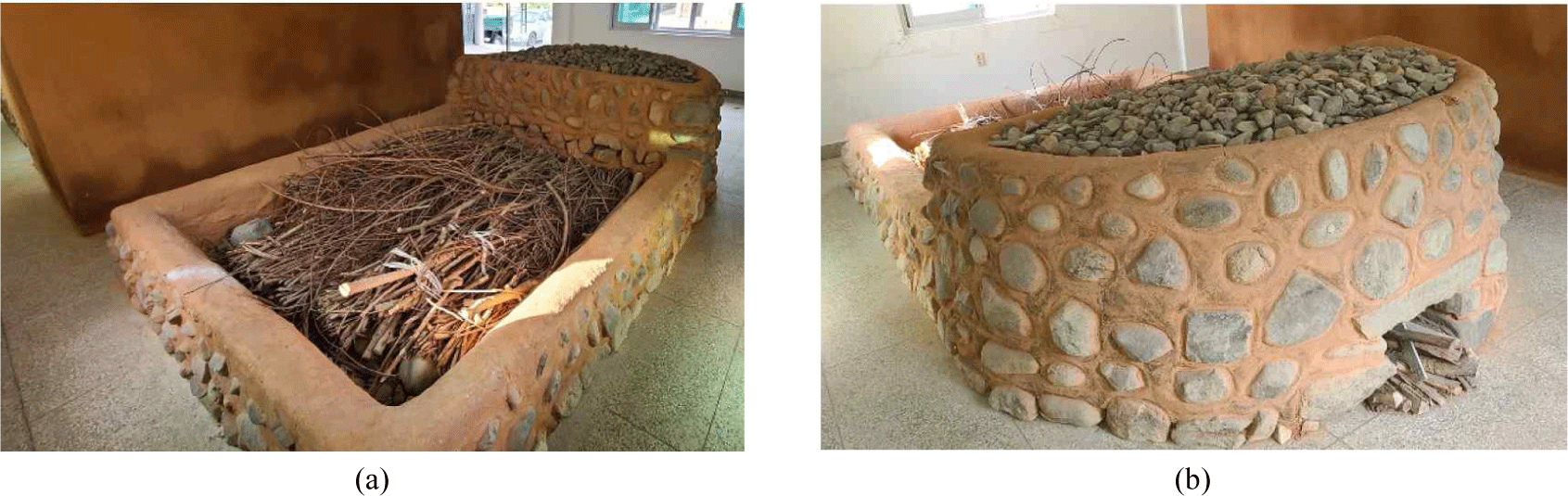
These traditional Dakmuji facilities were also documented during a paper manufacturing survey conducted in Chungcheong-do and Gyeongsang-do during the Japanese occupation period in 1912. The survey noted that the traditional Dakmuji was considered inefficient in terms of wood consumption and labor. As a result, the Japanese-style Dakmuji was introduced and adopted in Korea. In the Japanese-style Dakmuji, a bundle of Daknamu shoots is placed in a cauldron filled with water in an upright state; the protruding part is covered by turning over a long and large wooden barrel, and then the cauldron is heated. This method continued to be used in some regions of Korea until the 1980s (Park, 2023).
Recently, the ondol floor method has emerged as the most commonly used Dakmuji method in Korea. As shown in Fig. 2 (Lee et al., 2021c), in this method, piles of Daknamu shoots are placed on a plate, covered, and subjected to steam by setting them on fire within a fireplace.
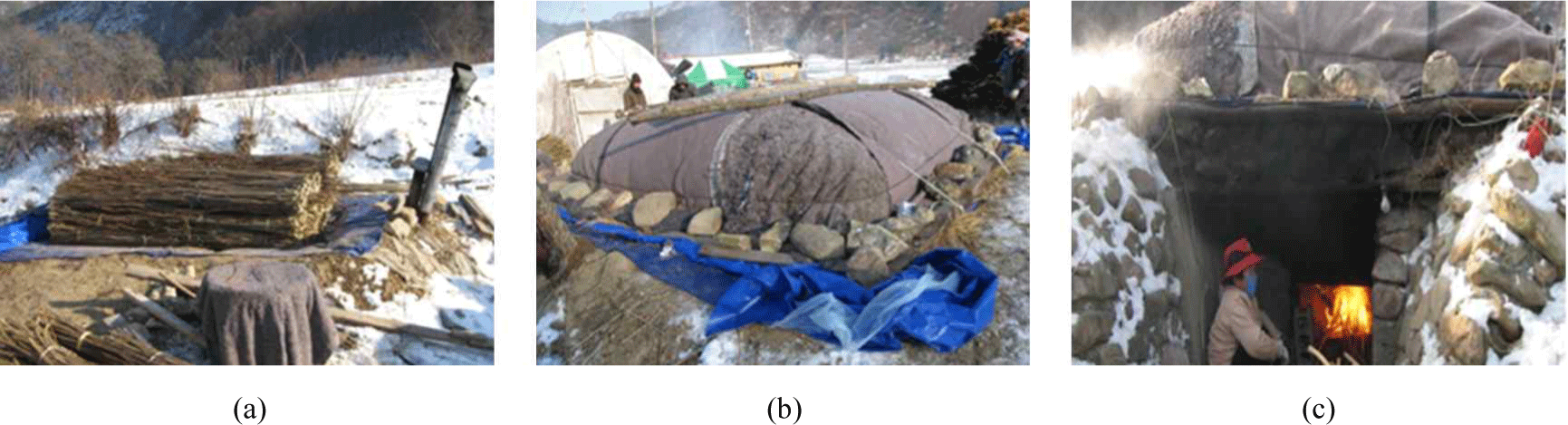
The term “White bark of Daknamu” refers to the inner bark after removing the outer bark. The White bark is boiled in an alkaline solution to dissolve non-fibrous substances in it to facilitate fiberization during the beating process.
It is documented that, during the Joseon Dynasty, ash from oyster shells (Kim, 2015a) or wood ash (Kim, 2015b) was used as an alkaline source for the boiling process. Around the Japanese occupation period, at least before 1908, there was a considerable change in the materials used for boiling White bark, and soda ash (Na2CO3, sodium carbonate), also called “Jodal” (曹達), and caustic soda (NaOH, sodium hydroxide) were used as a substitute for a lye solution. Another change was the use of bleaching chemicals in the process (Park, 2019). The introduction of synthetic chemicals in papermaking in Korea may have been influenced by the embracing of the Western culture, but widespread adoption occurred through the “papermaking class” held for decades at paper manufacturing sites across the country. This dissemination policy was implemented under the Japanese Government-General of Joseon to promote Japanese-style papermaking technology. Owing to readily available chemicals, it relieved people of the hassle of obtaining or making ashes, but the quality of paper decreased. Even today, these chemicals are commonly used in Hanji manufacturing facilities across Korea.
Alternatively, the boiled White bark may undergo a bleaching process before fiberization. In the natural bleaching method, White bark taken out of a lye pot after boiling is washed in a stream and then placed under running water for a certain period of time and subsequently exposed to sunlight. However, around the time of the Japanese occupation, the use of bleaching powder, a chemical produced through the reaction of chlorine and lime, became commonplace. It was recognized that while chemicals offered convenience, they could have a detrimental impact on the quality of Hanji. Furthermore, the use of bleaching powder can adversely affect the quality of paper (Ichiro, 1918).
In particular, caustic soda and bleaching agents are chemicals that can decompose cellulose, which is the main component of Daknamu bark and can affect the durability of Hanji. Therefore, presently, traditional Hanji manufacturers do not use chemicals when making traditional Hanji but rather boil White bark with natural lye and bleach under the sunlight.
The White bark that has gone through washing and bleaching becomes fiber through beating. The traditional method involves placing the White bark on a wide and flat stone and beating it with a long wooden bat, a highly labor-intensive process. Such manual beating methods appear to have been common in Korea until the mid-1920s. The transition to mechanical beating started in the 1930s (Hunter, 1936). While mechanical beaters are more widespread today than in the past, the practice of creating and using mechanical mortar and pestle devices that replicate traditional beating principles still exists. In addition, the traditional beating method using a wooden bat is still used to make Hanji.
As there are almost no records or relics of Hanji-making molds that have been handed down from ancient times, the changes were analyzed by comparing them with the molds from Korea, China, and Japan, which have exchanged their papermaking technology since ancient times.
It is not clear when the papermaking technology was first introduced in Korea. However, given geographical proximity, it can be safely assumed that the technology entered Korea shortly after paper was invented in China.
In the early days of papermaking, the primitive papermaking mold was typically prepared by tying four wooden sticks to form a square and securing it with a square-sized woven cloth, as shown in Fig. 3. In addition, willow or rattan was installed in a square frame in place of cloth. These papermaking molds, akin to the temporary container type known as “Gadoomtteugi” in Korean, were originally used in China.

A common method of papermaking involves extracting the fibrous material using a screen from a vat containing a mixture of fiberized raw materials, additives such as plant mucilage, and water. Meanwhile, in papermaking using the molds shown in Fig. 3, the sieve or mesh is submerged in water, and then a certain amount of mixture is poured onto the mesh or sieve so that the fibers are spread evenly over the entire surface. Subsequently, the mold is lifted to strain water and dry to make paper. The mold used in the early days of papermaking technology in Korea was likely similar to these primitive Chinese molds. The downside of this method is that each mold could produce only a single sheet of paper. Consequently, a large number of molds were needed to produce a substantial quantity of paper.
A more advanced form compared with the above primitive papermaking mold is using a mold composed of a screen, a supporting frame, and a deckle or deckle sticks (Fig. 4). A screen is treated as the mesh or sieve of the primitive type molds, and a supporting frame supports the screen. Papermaking is performed first by placing the screen on the supporting frame, then adding deckle sticks on top of the screen, and finally scooping the mixture from the vat. In this process, the mixture is temporarily contained in a room constituting the screen and deckle, and water spontaneously drains because the screen acts as a strainer; as a result, fibers are left on top of it. The wet sheet of fiber is separated from the screen for drying so that the screen can be used for the next batch immediately. That is, multiple sheets of paper can be continuously produced using just one set of molds, significantly enhancing production efficiency.
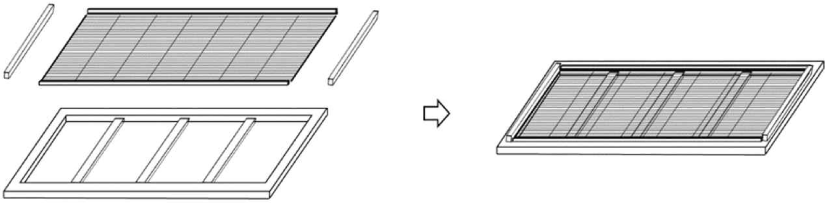
A papermaking mold using a frame deckle instead of deckle sticks, as shown in Fig. 5, was used in Japan. In this setup, the screen is placed on the supporting frame, and the frame deckle is placed on top of the screen. Paper is then made by scooping the vat while holding the frame deckle. As this method does not use cumbersome deckle sticks, the associated procedure is more convenient. However, in this case as well, it is not possible to completely preempt the difficulty involved in removing the frame deckle every time.
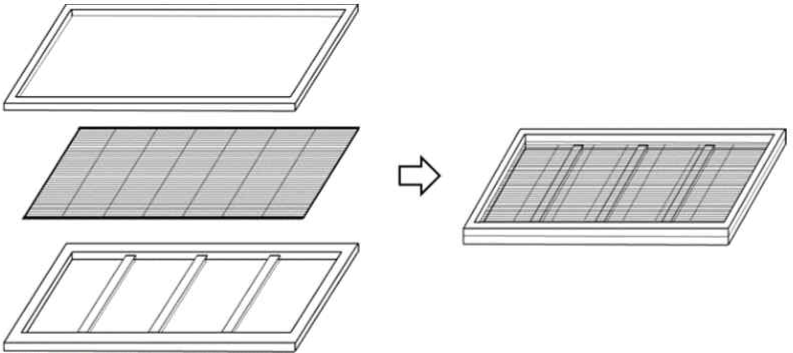
As a solution to the inconvenience of detaching the frame deckle every time, a more advanced mold was developed. This innovation involved connecting the frame deckle and the supporting frame with a hinge (Fig. 6). This hinge-fixed papermaking mold is still the most commonly used technique in Japan.
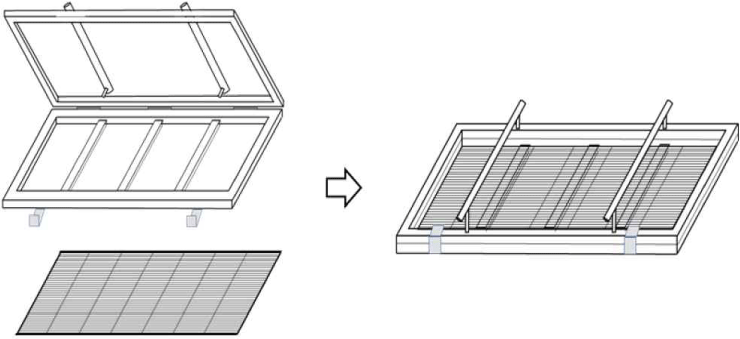
Two types of papermaking molds have been developed in Korea. One is Gadoomtteugi mold, which operates similarly to those used in China and Japan, as described earlier. The other one is the Heulimtteugi mold, which was developed only in Korea.
Korea has developed a unique papermaking mold that is different from those of other countries, called the Heulimtteugi mold. This mold does not constitute deckle or deckle sticks. It is simply composed of a screen and a supporting frame (Fig. 7). The Heulimtteugi mold is the only type of mold that has been used in Korea for making traditional Hanji up to the present time.
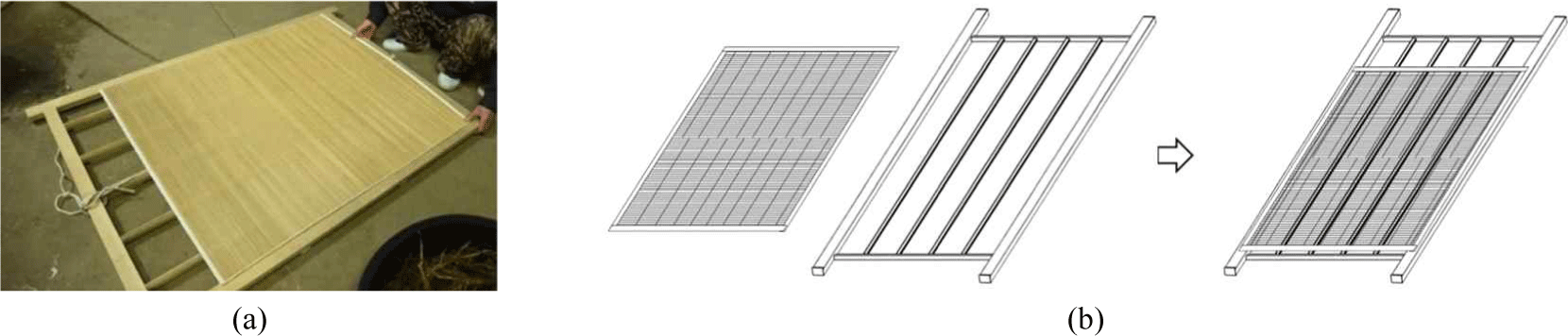
A picture with a precise description of the old Korean-type Gadoomtteugi mold was found in Dard Hunter’s book titled “A PAPERMAKING PILGRIMAGE to Japan, Korea, and China,” published in 1936. This is a Hanji-making mold (Fig. 8) that Dard Hunter collected in 1933 from a papermaking village in Eunpyeong. According to the book, this mold consists of a screen with thick wooden ends attached to the left and right ends, a supporting frame, and two deckle sticks at the upper and lower ends. It also said that this mold was used for making flooring paper. When manufacturing Hanji using this mold, the two wooden ends mounted on the left and right sides of the screen and two deckle sticks at the top and bottom act as a deckle. The operation principle of the mold is similar to that used in the Chinese mold, as shown in Fig. 4, but the location and size of the two deckle sticks are different.
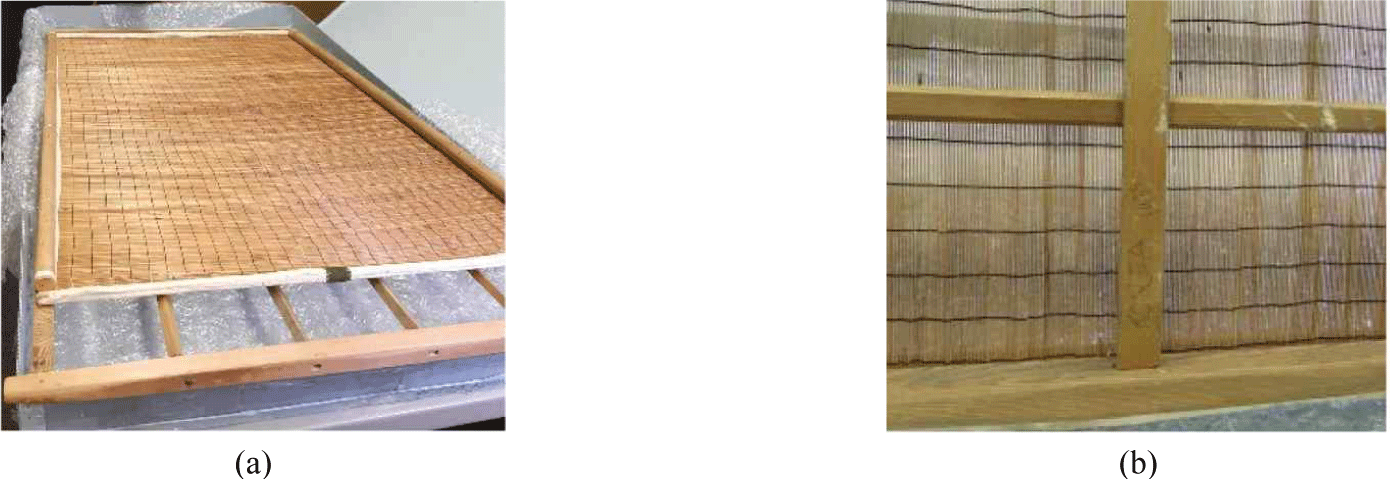
The mold shown in Fig. 8 is probably the only Korean traditional Gadoomtteugi mold that has been reported so far, with a detailed description of the structure and materials. To provide further clarity regarding the mold, an investigation on the artifact mentioned in Hunter’s book was carried out by the authors’ team at the Robert C. Williams Museum of Papermaking in the United States in 2022. The investigation confirmed that the wooden ends, which are wrapped with white cotton cloth, and the two deckle sticks can act as a deckle [Fig. 8(a)]. The picture on the Fig. 8(b) shows a handwritten inscription “KOREA 1933,” which was written in a flat cross-piece in the back, displaying the country of collection and year of the mold. Because there is a strong tendency to accept that Heulimtteugi is the only traditional papermaking technique in Korea, this confirmation of Gadoomtteugi’s historical presence becomes especially significant in establishing it as one of Korea’s traditional papermaking techniques.
However, the Korean traditional Gadoomtteugi mold and methods have not been handed down to the present age. This can be attributed to the widespread influence of the generalized Japanese-style Gadoomtteugi mold shown in Fig. 6, which was introduced and adopted in Korea during the Japanese occupation period, subsequently spreading throughout the country.
There has been a shift in the material used for Hanji-making screens. Currently, the screens for Hanji-making commonly seen are thin, round bamboo strips, known as “laid,” which are interlaced using a fiber string or horse hair. Furthermore, historical records indicate that screens made from silver grass (Miscanthus spp.) were used for Hanji-making in Korea during the 1910s to 1930s (Hunter, 1936; Park, 2023). Thus, screens made of silver grass as well as bamboo strips were used to make Hanji in the ancient days, but it appears that the tradition of using a screen made of silver grass disappeared during the Japanese occupation period.
Relics and old photographs of the screens for papermaking indicate that the Korean screen has evolved in its shape, distinguishing it from screens used in other countries. In most other countries, the horizontal length parallel to the direction of the laced bamboo strips is longer than the vertical length in the direction of the string. But it is the other way around in Korean screens. This can be easily seen by comparing the lace line or string directions, which is sometimes referred to as a chain-line, of the Korean screen, as shown in Fig. 7 and the Chinese and Japanese screen, shown in Figs. 4-6. Another characteristic of the Korean screen can be found in the way of lacing bamboo strips up with string. In many cases of Korean screens found in recent years, as shown in Figs. 7 and 9, the bamboo strips in a screen are laced in a staggered direction from the middle of the screen. However, it can be seen that the screens used in Korea, China, and Japan in the 1930s, shown in Figs. 4, 5, 6, and 8 were tied straight, not staggered.
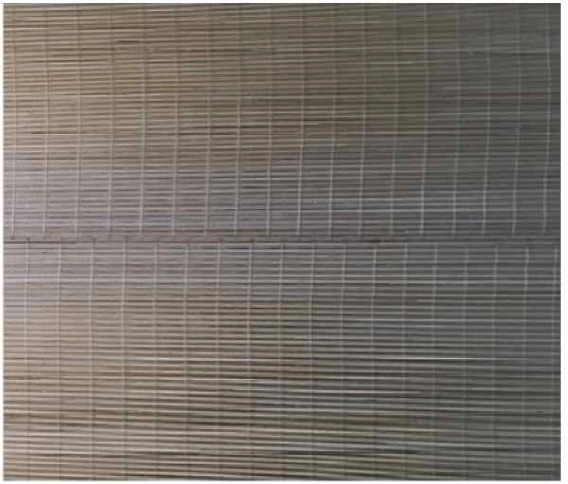
As described in the previous sections regarding Hanji-making molds, Gadoomtteugi is a papermaking technique where a mold with a deckle is employed to temporarily contain an aqueous fibrous mixture within a set of screen and deckle. The wet sheet of fibers forms as water strains through the screen. It can be seen that the Korean-type Gadoomtteugi mold shown in Fig. 8 and its operation methods existed until the 1930s. Currently, Japanese-type Gadoomtteugi mold and technique are being practiced in Korea, which was introduced to Korea around the period of Japanese occupation.
Even before the official Japanese occupation period, the Japanese Empire promoted a policy of disseminating the Japanese-type Gadoomtteugi technique in Korea, and the governmental industrial training center established in Seoul in 1907 was actively used for this purpose. At that time, Japan took effective control of Korea and established the “Department of Applied Chemistry” in the government industrial training center to teach Japanese-type Gadoomtteugi technique. Further, the graduates were sent across the country to disseminate the technique by conducting papermaking classes. These classes not only covered the papermaking process but also included instructions on how to cultivate Daknamu, providing valuable knowledge to local paper makers. The papermaking classes continued until the 1930s, after the government training center was promoted to “Gyeongseong Technical School” and renamed “Gyeongseong Technical High School,” and soon, the Japanese-type Gadoomtteugi method became commonplace all over the country. The main purpose of spreading the Japanese-type Gadoomtteugi method was to turn the Hanji-making industry into a production base for Japanese paper (Park, 2023).
In the paper manufacturing process using Gadoomtteugi, the worker either holds the mold steadily in a balanced position after scooping up the aqueous fibrous mixture or rocks the mold back and forth. In the former case, the bast fibers in the paper are arranged without a specific direction, and in the latter case, the bast fibers tend to be arranged in the front-back direction, which is the direction of the chain line. Most of the papers made using the Japanese-type Gadoomtteugi method fall under the latter category.
Heulimtteugi is a unique papermaking method practiced only in Korea, which eliminates the need for deckle sticks or a deckle. In this method, an aqueous mixture is not temporarily contained within the mold because of the absence of the deckle. The Heulimtteugi worker scoops an aqueous fibrous mixture from the vat with the mold from the front and tilts it in the opposite direction to let the mixture flow down. This technique is called “Apmuljil” in Korean. Subsequently, the mixture is scooped using the mold possessing previously mounted fibers from one of the sides and tilted to the opposite side, letting the mixture flow down. This technique is called “Yupmuljil” in Korean. Fibers on the screen are oriented in a back-and-forth direction by Apmuljil and side to side by Yupmuljil on top of the fibers in the direction of back and forth. This process when repeated results in paper with multiple layers of crossly bounced fibers.
The graph in Fig. 10 shows the results of measuring the tensile index in the laid direction and the chain line for the paper produced by Gadoomtteugi and Heulimtteugi techniques at the National Research Institute of Cultural Heritage. As shown in this graph, the tensile index of the paper made using the Gadoomtteugi shows a significantly higher value in the chain-line direction than in the laid direction. In contrast to that, the tensile index of the paper made using the Heulimtteugi is similar in both directions. Such paper has similar contraction-expansion rates or tensile strength in the horizontal and vertical directions, making it difficult to tear in either direction.
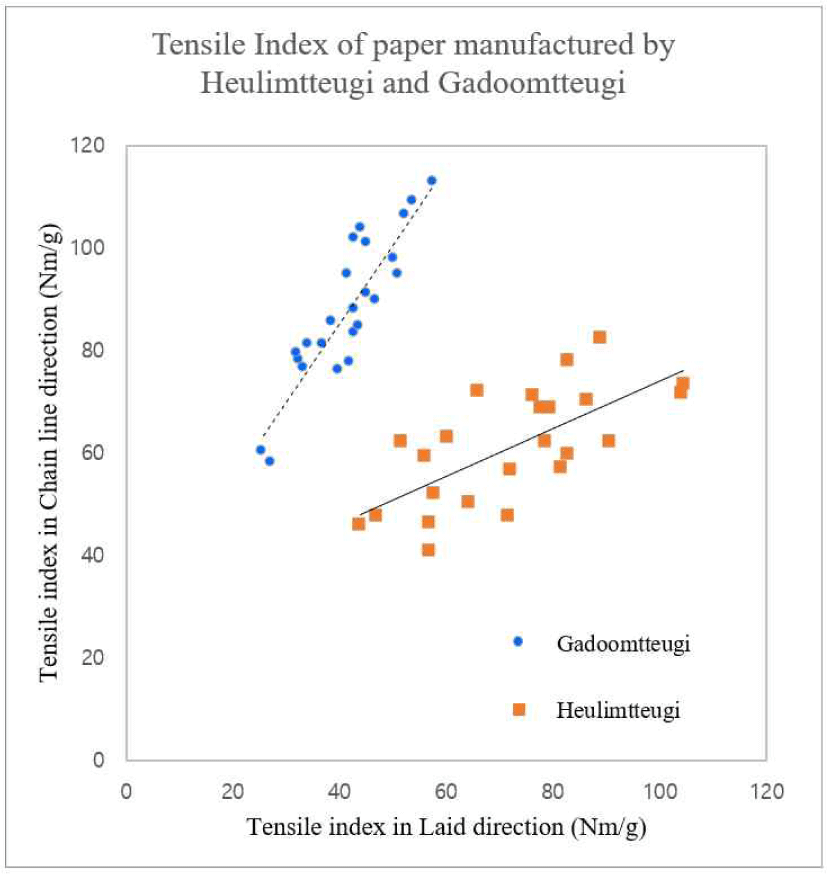
Thus, paper characteristics are dependent upon the directions of the strands of bast fibers, which are arranged differently using different paper molds and manufacturing methods.
Currently, the only method that has been handed down as the Korean traditional Hanji-making method is Heulimtteugi.
In a common Heulimtteugi technique currently practiced in Korea, the far end of the supporting frame usually is tied to a cross bar installed above the center of the vat so that one person can handle the large mold (Fig. 11). Notably, there is no historical record indicating when Koreans began employing the crossbar and cord to secure the supporting frame in Heulimtteugi. However, tying one end of the mold to hang with a cord closely resembles the method used in the Japanese Gadoomtteugi technique.
The practice of hanging one end of the mold can be attributed to a single person required to manage a large mold effectively, especially when crafting larger sheets of paper. It is inferred that such a Hanji-making method was not common in Korea until the early 1900s. One piece of evidence supporting this inference is the absence of a crossbar for hanging the frame in an old drawing depicting Hanji-making. This drawing appears on the cover page of the Hanji sample book titled “Paper of Gyeongsangbuk-do,” published in 1926. In addition, we do not observe a cross bar or tying support of a cord for a mold in any of the photos captured in the 1930s in Korea. As an additional clue, according to the contents of the “Government Industrial Training Center Report” published in 1909, small white papers (length 60 cm, width approx. 24–27 cm) were produced by one person, whereas large papers (length 75–78 cm, width approx. 51–54 cm) were produced by two persons. However, currently, the larger Hanji sheets (93 cm in length and 63 cm in width) than those produced by two persons as described above can be produced by one person using the Heulimtteugi mold, which is tied on a cord to be suspended.
Therefore, it can be seen that it was not common to suspend the Heulimtteugi mold on a cross bar to make Hanji in Korea in the 1930s.
In contrast, in Japan, the papermaking technique involving suspending a mold frame from a cord has been used since at least 1745 (Seki, 1965).
It was found that the Chinese were already using the papermaking technique of hanging a papermaking mold using a cord to make large pieces of paper. This technique was introduced to Japan in the 1700s, as evidenced by the book titled “Drawings of Paper Making and Paper Store of All Times (故今紙漉,紙屋圖絵).” The oldest drawing of papermaking using a hanging mold in Japan is found in the book. According to the accompanying description, this papermaking method using a hanging mold is of Chinese origin.
Based on the findings from the investigation, it is clear that the Japanese developed their own papermaking tools and methods by adapting the Chinese technique that uses a hanging mold operated by one person. That is the Japanese Gadoomtteugi method that was introduced to Korea in the early 1900s and has been generalized in Korea today.
No historical records indicate that the Heulimtteugi technique, involving the use of a hanging mold, was practiced in Korea prior to the introduction of the Japanese Gadoomtteugi method. Moreover, although there is some emotional evidence, there is no direct evidence that Koreans applied the Japanese technique of mold-hanging to the Korean Heulimtteugi. As a result, the origin of the cross bar and the cord for the Heulimtteugi method needs to be clarified to understand how the Korean traditional papermaking method, Heulimtteugi, developed.
Meanwhile, a Heulimtteugi technique that required two individuals to create a large piece of Hanji existed. In this technique, one person holds the handles tied at both ends of the mold and the other person grips the opposite end to operate the mold. Fig. 12 depicts a scene of papermaking using Heulimtteugi with two persons. This technique is not common anymore in the Korean Hanji-making field.
For preparing a large piece of Hanji without suspending a mold by one person, another Heulimtteugi technique called “Moknamutteugi” was carried in Korea. To perform this technique, two-thirds of a long cylindrical wood called “Moknamu” (Fig. 13) is immersed in a vat at an angle such that one-third of it is stuck out of the water and falls back on the frame of the vat. Subsequently, the papermaker places a papermaking mold on the stuck-out part of Moknamu horizontally while holding the opposite side of the mold. For papermaking, the papermaker then scoops and tosses the aqueous mixture using the mold balancing on Moknamu as shown in Fig. 14. This technique has been in use in some villages of Gyeongsang-do and Gangwon-do, but it has almost disappeared from the traditional Korean paper production site in Korea. Pictures are Moknamutteugi scene filmed by an American handmade-paper researcher Tim Barrett in Shinheung-Ri near Samcheok, Gangwon-do in 1977.
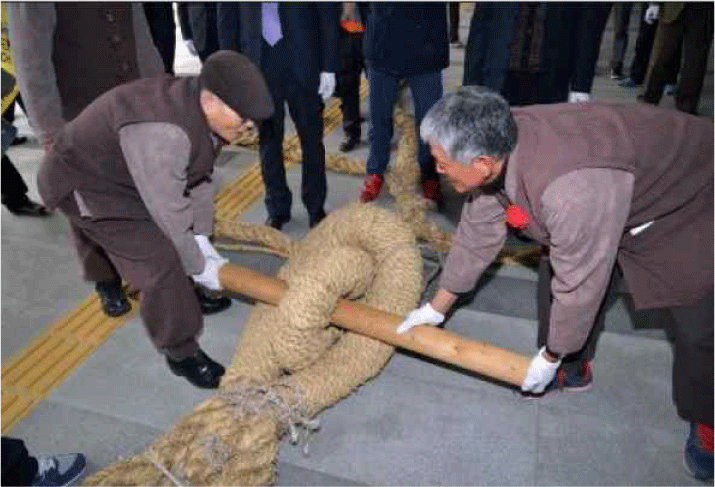
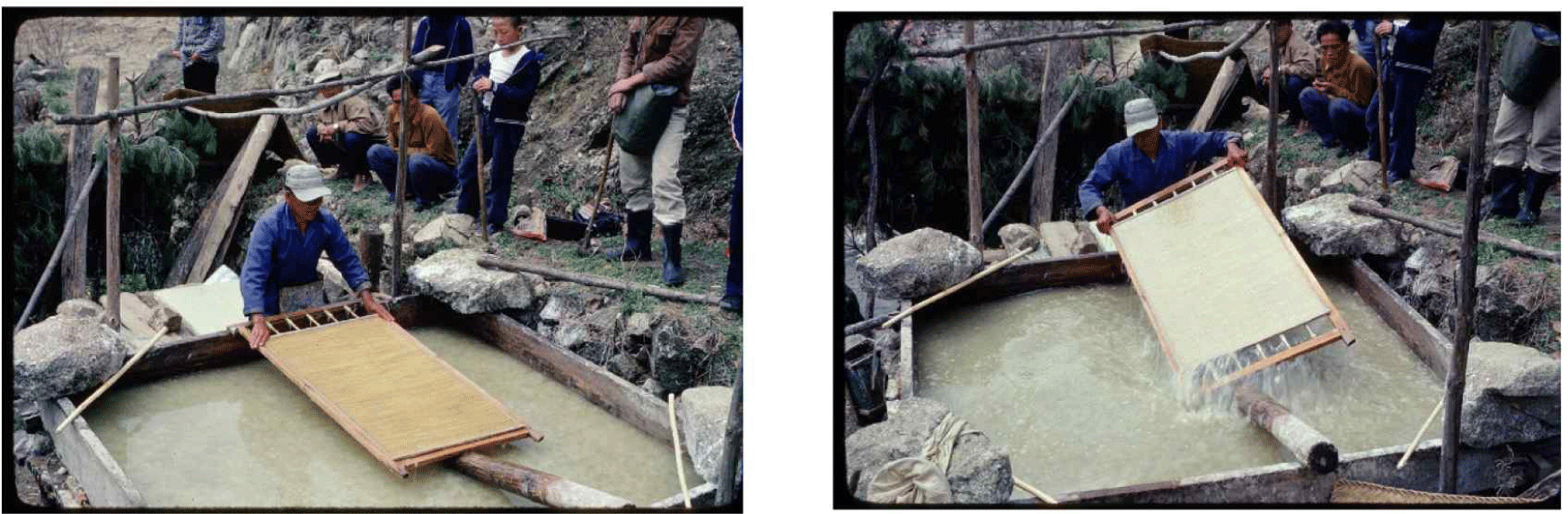
For reference, Moknamu is a piece of cylindrical wood that is usually inserted between the two ropes of the tug-of-war, and is also called a “Binyeomok,” which is a Korean traditional hairpin, according to the Encyclopedia of Korean Folklore published by National Folk Museum of Korea.
As shown in Fig. 3 wet fibers mounted on a primitive papermaking mold were dried in the sun. However, with the introduction of a separate screen in papermaking, the production of multiple sheets of paper became possible, leading to the adoption of various drying methods. There is a record in “Cheongonggaemul (天公開物)” published in 1637 during the reign of the Ming Dynasty stating that a wall was installed and heated to dry the wet paper attached to it (Hunter, 1932; Xing, 1991). It is presumed that there was a similar drying facility in Korea in the past.
Meanwhile, it was reported that a paper-drying facility in the form of a floor warming system “Ondol” was used in the early 1900s in Korea (Park, 2023). Nevertheless, in the cases of thick or large paper, they were dried under the sun by spreading them out on a grassy field at that time (Hunter, 1936; Park, 2023). Furthermore, around the 1920s, wooden panels and dryer facilities were introduced in Korea for drying paper (Park, 2023).
Even today, the drying method using wooden panels and the dryer is predominantly used for drying Hanji in Korea.
4. CONCLUSIONS
To unravel the evolution of traditional Hanji-making techniques up to the present day, we analyzed the Hanji manufacturing molds and manufacturing techniques dating back to ancient times.
Regarding the changes in the pretreatment technology in Hanji-making, natural materials were historically used for an extended period. However, as time passed, new materials or chemicals were introduced to improve work efficiency. Nevertheless, the fast and convenient modern methods can compromise the quality of Hanji. Consequently, traditional pretreatment methods are adhered to as much as possible to produce high-quality traditional Hanji.
Regarding changes in Hanji-making molds, this study revealed the existence of Korean traditional Gadoomtteuji molds and techniques, which are similar to those from the Chinese techniques. It was found that both Gadoomtteugi and Heulimtteugi molds were traditionally used in Korea. However, Korean traditional Gadoomtteuji faded out, and Japanese-style Gadoomtteugi techniques became common in Korea following the Japanese occupation period. Conversely, Heulimtteugi has emerged as the predominant traditional papermaking method in Korea, distinguished by its absence of a deckle frame or deckle sticks, even though the exact time of its inception remains uncertain. Heulimtteugi is a unique Hanji-making technology used only in Korea, and it continues to represent the traditional Hanji-making method to this day. Notably, unlike in other countries, the vertical length in the direction of the chain line is longer than the horizontal length in the laid direction on the papermaking screen.
The manufacturing method of Hanji has evolved in tandem with the changes in manufacturing molds. The Korean traditional Gadoomtteugi method, which involves one person making small paper and two people making large paper, transformed during the Japanese occupation period into the Japanese-style Gadoomtteugi, where mold is suspended from a cord, allowing a single person to operate the mold. In addition, it was discovered that to make a large piece of Hanji involving one person in the Heulimtteugi method, a technique of hanging a mold on a cord and a cross bar became prevalent. However, the Moknamutteugi technique, once used in many regions of Korea, has since disappeared. Furthermore, the Heulimtteugi technique conducted by two persons is no longer a common practice in Korea.
For the first time, this study introduces the high likelihood of the adoption of the mold-hanging technique into the Heulimtteugi method from techniques developed in foreign countries. However, it is important to note that further evidence is required to fully substantiate this claim.
In summary, this study finds that the raw materials, molds, and techniques used in Hanji-making remained relatively consistent from ancient times to the Joseon Dynasty. However, there have been significant changes during the Japanese occupation period, including the disappearance of the traditional Gadoomtteugi method, the changes in raw materials, names, and size, and the possible influence of the mold hanging in Heulimtteugi. Currently, some traditional names of Hanji have been reintroduced, Daknamu bast fiber remains the main raw material of the traditional Hanji, and Heulimtteugi is treated as the traditional Hanji-making method.