1. INTRODUCTION
Bamboo is a multifunctional plant classified as a type of grass (family: Poaceae) and has been widely used by the Indonesian community for construction materials and furniture. In general, bamboo can be used for laminated boards when it is 2–3 years old, and as a construction material when it is 3–6 years old (Raj and Agarwal, 2014). This is in contrasts to wood, which typically requires 40–50 years to reach maturity before achieving the desired strength. However, bamboo culm generally has strong, impermeable outer surface (exodermis), hollow stems, and uneven thickness, where the thickness is relatively thin at the base, thicker in the middle, and thinner again towards the one-third end of the bamboo culm, leading to non-uniform mechanical properties (Kasmudjo, 2013). The bamboo culm also consists of the nodes and internodes which cause to the different tensile strength (Darwis et al., 2023). It should be noted that due to its high sugar and starch content, bamboo has poor biological durability, therefore some treatments or modification are needed (Arsyad et al., 2020; Lee and Lee, 2021; Maulana et al., 2021; Qi et al., 2019).
Laminated bamboo is an engineered bamboo formed by bonding multiple bamboo strips to enhance the uniformity of mechanical properties compared to natural bamboo (Setyo et al., 2014), which are glued parallel to the fiber direction (Qisheng et al., 2002). As a result, laminated beams exhibit greater strength than single layers with minimal dimensional changes (Morisco, 2006; Setyo et al., 2014). Several studies have investigated the production of laminated bamboo using various methods for preparing raw materials (Galih et al., 2020; Guan et al., 2022; Kim et al., 2003; Nugroho and Ando, 2001; Putri et al., 2023; Sumardi et al., 2022). The physical and mechanical properties of bamboo are generally influenced by the type and age of the bamboo, moisture content, nodes and internodes, and culm position (Janssen, 2000).
In this study, laminated boards were manufactured by utilizing Betung bamboo (Dendrocalamus asper Backer ex K.Heyne). This bamboo variety was selected for its extensive use in construction and furniture manufacturing in Indonesia. It can reach as high as 20–30 m with an internode length of about 20–45 cm and a diameter of 8–20 cm. The wall thickness of the culm is around 6–22 mm (Javadian et al., 2019). The wall thickness of Betung bamboo (5 years old) at the top, middle, and bottom was 11.2 mm, 21.1 mm, and 27.4 mm, respectively (Maulana et al., 2022). Irawati and Saputra (2012) summarized the mechanical properties of Betung bamboo. It indicated the modulus of rupture (MOR) of 134.87 MPa and modulus of elasticity (MOE) of 12.89 GPa. Based on a study of Adam and Jusoh (2019), Betung bamboo has basic density of 0.48–0.73 g/cm3, MOR of 48–228 MPa, and MOE of 1.16–10.67 GPa depending on the culm position.
Liese (1985), Praptoyo and Yogasara (2012) similarly revealed that bamboo culms can manifest diverse properties along their axial direction, specifically at the base, middle, and top. Therefore, evaluating the position of bamboo culm is crucial to determine its optimal mechanical properties. In addition to culm position, it is imperative to consider differences in mechanical properties concerning the laminate direction technique. According to Sharma et al. (2015), the orientation of lamination significantly influences the bending properties. Using vertical lamination, for example, can improve bending properties by up to 18% compared to horizontal lamination. As reported by Kariuki et al. (2014), the mechanical properties of laminated bamboo were affected by fiber orientation. Nugroho and Ando (2001) also stated that vertical orientation could increase the strength of laminated bamboo.
This study aimed to explore how culm position and lamination direction affect the mechanical properties of laminated boards made from Betung bamboo. The objective was to gather insights into the anticipated mechanical characteristics of laminated Betung bamboo, providing guidance for producing boards with optimal mechanical strength by considering the recommended culm position and lamination direction.
2. MATERIALS and METHODS
The type of bamboo used in this study was Betung bamboo (D. asper), which is commonly known as giant bamboo, obtained from Sleman Regency, Yogyakarta. The specified dimensions of the bamboo include mature culms aged over 3 years, with a length of 9 meters (measured from the base of the cut) divided into three sections: base, middle, and top, each measuring 3 meters. The minimum diameter was 15 cm, minimum internode length was 35 cm, and minimum wall thickness was 2 cm. The bottom 0.5 m from the ground of the bamboo culm was removed, and both outer and inner skin were stripped. The adhesive used was Crossbond X4, a branded adhesive based on polyvinyl acetate (PVAc) from Bioindustries, Yogyakarta. The specification of the adhesive was pH of 4.1, specific gravity of 1.15, solids content of 44% and viscosity of 3,500 cps.
The bamboo underwent a conventional solar drying process for one month until it reached an air-dry condition. This drying method was chosen for Betung bamboo because it is simple and can reduce operational costs (Sumardi et al., 2024). After drying, the bamboo was split into slats with a width of 1.5 cm. The slats obtained were then further split into smaller pieces, resulting in bamboo slats measuring 35 cm in length, 1.5 cm in width, and 0.5 cm in thickness. Before lamination, the bamboo slats were first preserved with mixture of borax and boric acid in a ratio of 3:2 at a concentration of 10% and boiled at 55°C–60°C for 2 hours (Sulistyawati, 1997 with modifications). As reported, the application with boron did not significantly affect the density and mechanical properties of laminated Betung bamboo (Aini et al., 2009; Sumawa et al., 2019). Some studies also reported that the preservative treatment on wood with boron did not reduce the density and flexural properties of samama wood (Cahyono et al., 2020) and light red meranti wood (Lee et al., 2024). The bamboo slats were drained and dried again until they reached a moisture content of about 15%. The conditioned bamboo slats were taken randomly and then arranged to form a board measuring 30 cm in length, 30 cm in width, and 3 cm in thickness, then bonded using PVAc adhesive with glue-spread of 280 g/m2 and clamped with a hydraulic press at a pressure of 1 MPa. The bamboo slats were glued horizontally and vertically (Fig. 1). The bamboo assembly was cold pressed for 24 hours and conditioned for one week prior to testing.
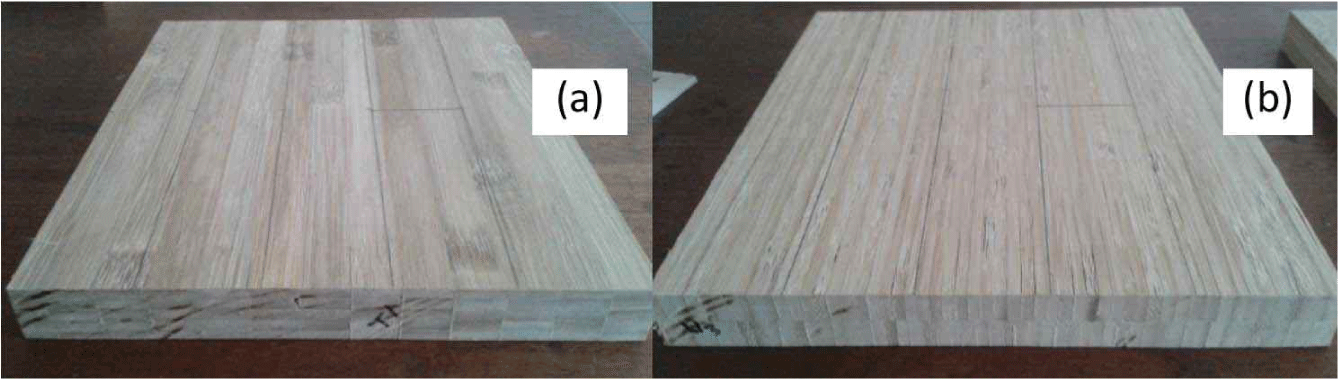
The physical and mechanical properties tested were moisture content and density according to BS 373 (BSI, 1957), static bending strength consisting of MOR and MOE, and hardness test based on ASTM D1037 (ASTM, 1999). The static bending tests were conducted using a sample size of 30 cm × 2 cm × 2 cm (l × w × t), while hardness testing uses a standard with a sample size of 5 cm × 5 cm × 5 cm. The testing was performed using the Universal Testing Machine (UTM) Instron Model 3360.
3. RESULTS and DISCUSSION
The results of testing the moisture content and density of laminated bamboo indicate that the moisture content of the produced laminated bamboo ranges from 14.19% to 15.86%, with an average value of 15.25%. These values are consistent with the typical range of air-dry moisture content found in Indonesia. Furthermore, the density of laminated bamboo has an average value of 0.66 g/cm3. This is higher compared to the generally observed density of common bamboo, which has an average basic specific gravity of 0.61 as reported by Kasmudjo (2013). However, this value was lower than the original Betung bamboo in the study of Irawati and Saputra (2012), which resulted in an average density of 0.72 g/cm3. The difference in density is suspected to be caused by the presence of remaining bamboo skin and the existence of adhesive material that binds between bamboo laminates. Tho and Morisco (2008), elucidated that the mechanical properties are influenced by the presence of skin layers on the strips compared to those without. In general, the values of moisture content and specific gravity of the produced laminated bamboo were not influenced by the variation of culm position and laminate direction.
The mechanical properties serve as a measure of an object's resistance to external forces that tend to alter its original shape (Bowyer et al., 2007). In this study, the static bending strength test was conducted to obtain the values of MOE and MOR for the produced laminated bamboo. The average MOR values and the results of the variance analysis are presented in Tables 1 and 2. Based on the analysis of variance, the MOR test results indicated no significant differences in the factors of stem position, lamination direction, or their interaction. Therefore, in terms of MOR, there was no significant influence observed in either the culm position or lamination direction to the MOR values, although it can be seen in Table 1 that the higher culm position resulted in higher MOR (83.91 MPa, 103.86 MPa and 111.87 MPa for lower, middle and upper culm position, respectively) and vertical lamination resulted in higher average MOR (107.10 MPa) than that of horizontal lamination (93.99 MPa). Nevertheless, the average MOR value reaches 100.55 MPa. As a comparison, the MOR values of this study were lower than the study of Setyo et al. (2014) which resulted in an average MOR of 130.98 MPa by using UF resin as adhesive. However, the result of MOR value was higher compared to the general MOR of whole bamboo culms, which is 33.58 MPa (Kasmudjo, 2013). This improvement in strength is attributed to the lamination process and bonding technology, as highlighted by Setyo et al. (2014).
The average MOE values and the results of the analysis of variance were presented in Tables 3 and 4. Based on the analysis of variance, the MOE test results show significant differences in culm position and lamination direction, but the interaction between these two factors does not yield significant differences. The results of honestly significant different (HSD) test at significant level of 1% test results indicate significant differences between the lower position and both the middle and upper positions, while the middle position does not show significant differences from the upper position. Figs. 2 and 3 presented the histogram of the relationship between culm position, lamination direction and MOE of laminated bamboo board. The middle and upper position of bamboo culm resulted in MOE of 12.54 and 12.43 GPa, respectively. It was higher than the lower culm position of 10.01 GPa. Similar findings are also mentioned by Oka et al. (2014), indicating that the culm position of bamboo significantly affects mechanical properties, especially in tensile, compressive, and shear strength tests. The difference shows that vertical lamination provides 12.77% higher flexural modulus than horizontal lamination. The vertical direction resulted in an average MOE of 12.36 GPa, while the horizontal one resulted in an average MOE of 10.96 GPa. This follows the finding that vertical laminate increases static flexural strength (Nugroho and Ando, 2001; Sharma et al., 2015). However, the results of this study are slightly lower than the expression of Sharma et al. (2015), who mentioned that the vertical laminate arrangement direction improved the average MOE value by 18%. Compared to the study of Setyo et al. (2014), the average MOE values of this study were quite lower (11.66 GPa compared to 12.42 GPa). It was understandable since they used UF resin in laminated bamboo production.
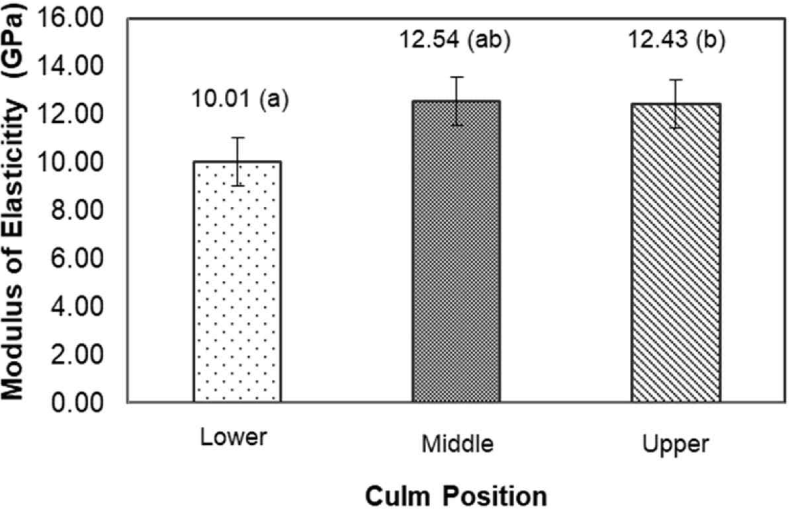
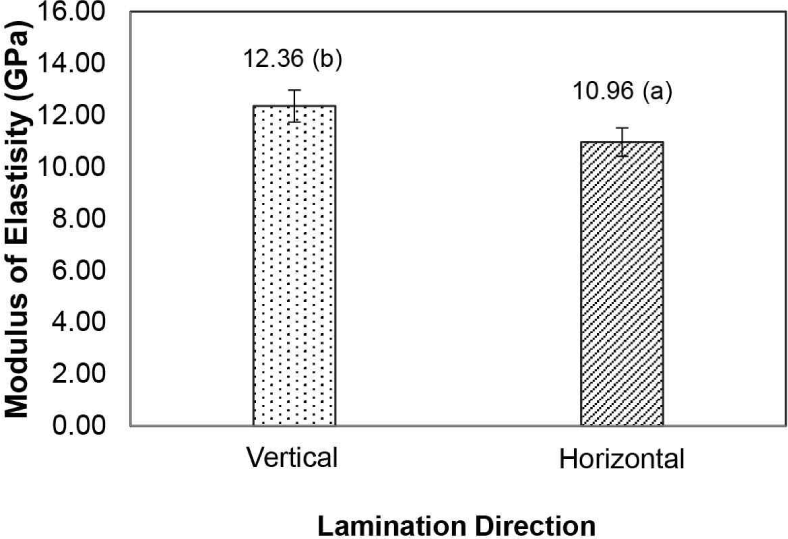
The results of the hardness testing for different culm positions and lamination directions were presented in Table 5. To determine the variation of the average hardness value based on the factors of stem position and lamination direction, the variance analysis is presented in Table 6. The histogram depicting the relationship between culm position, lamination direction and hardness of laminated bamboo board was presented in Figs. 4 and 5. Based on the analysis of variance, the hardness results showed highly significant differences in both and culm position and lamination direction, while the interaction between the two did not yield significant differences. The HSD 1% test results indicate highly significant differences between the base position and both the middle and end positions. Regarding lamination direction, the HSD 1% test results show highly significant differences between the vertical and horizontal lamination directions. Therefore, considerations for hardness properties also consider both culm position and lamination direction, even though only one of them is being considered. The overall average total hardness value for lamination direction was 1.046 kgf/cm2, a value significantly higher than the natural hardness of Betung bamboo, which is only 250 kgf/cm2 (Kasmudjo, 2013). This improvement in strength was attributed to the bonding process in lamination technology, as highlighted by Setyo et al. (2014).
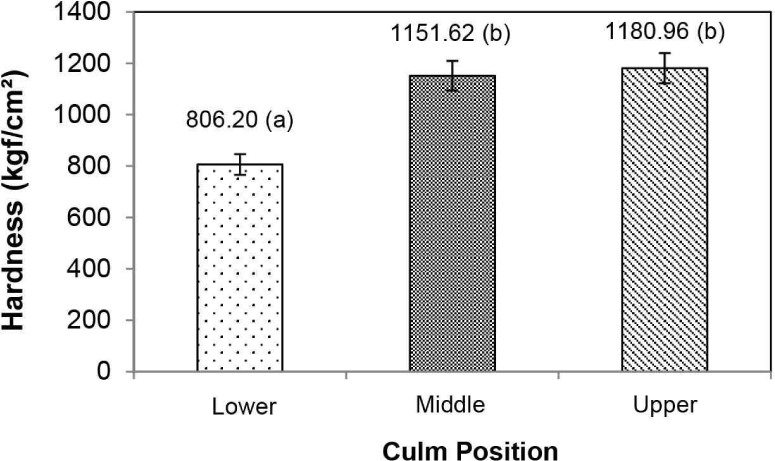
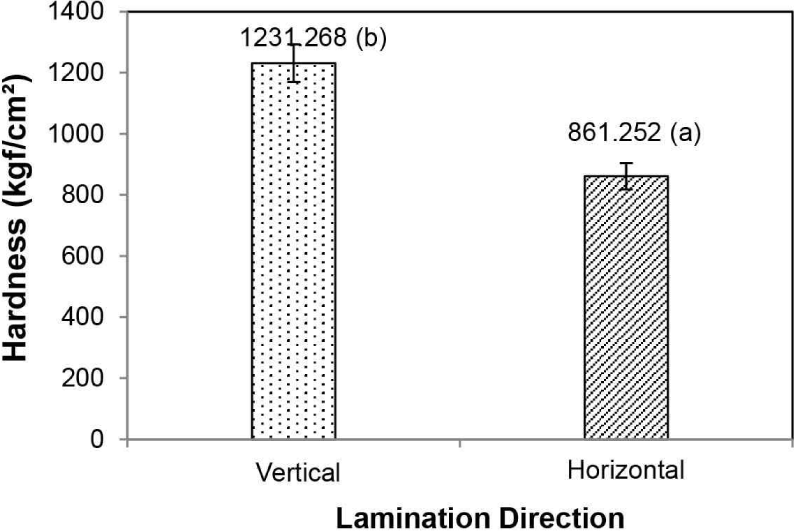
4. CONCLUSIONS
Research on the effect of different culm positions and lamination directions on the physical and mechanical properties of laminated Betung bamboo resulted in the average moisture content of 15.25%, density of 0.66 g/cm3, MOR of 100.55 MPa, MOE of 11.66 GPa and hardness of 1.046 kgf/cm2. Furthermore, it is concluded that there is no interaction between culm position and lamination direction concerning the physical and mechanical properties of laminated bamboo. In MOE and hardness, the higher the stem position, the greater the strength value, while the vertical lamination direction has greater strength than the horizontal lamination direction. Culm positions with a high likelihood of being utilized for laminated bamboo boards are primarily the middle and upper sections, particularly for applications in building materials and high-strength furniture. The lamination direction with the feasibility of being used was the vertical lamination direction.