1. INTRODUCTION
Biomass densification through pelletizing has currently become a priority for various stakeholders, as pellets can be developed into a renewable energy resource (Jang, 2022). In recent years, the development of renewable energy has been prioritized worldwide owing to the intensification of fossil-fuel use, which has accelerated environmental problems and climate change (Connolly et al., 2011; Jung et al., 2015). Biomass is a potential renewable energy source, especially plant biomass. Biomass is a carbon-neutral material as the emissions produced by its utilization will be absorbed by other plants during their growth (Yokoyama and Matsumura, 2008). Indonesia is a tropical country with large plantations and agricultural resources; thus, biomass is a potential energy source, with an estimated value of 32.77 GW if solely converted for electricity (Primadita et al., 2020). Pelletizing is the densification of homogenously sized biomass materials into pellets of certain shapes and energy quantities (García-Maraver et al., 2011). Biomass in the form of pellets is also advantageous; for instance, they are easier to store and transport (Damayanti et al., 2017). Torrefaction is one of the processes used to improve the quality and appearance of pellets, especially to increase their energy density and hydrophobicity (Sutapa and Hidyatullah, 2023). Torrefaction is a mild thermochemical pre-treatment comprising the slow heating of biomass in an oxygen-free chamber with a temperature between 200°C and 300°C. Compare with original biomass, torrefied biomass is more hydrophobic, compactable, and grindable, has higher energy density, and has a lower oxygen to carbon ratio (O/C; Prins et al., 2006; Shankar Tumuluru et al., 2011; Tumuluru et al., 2021). Condensable and non-condensable volatiles in the pellets are also released during torrefaction (Yun et al., 2021). Another factor that affects the quality of a pellet is the particle size or dimensions of the raw material. Decreasing the particle size increases the density, durability, and calorific value (CV) of the pellets (Harun and Afzal, 2016; Hidyatullah et al., 2022).
Nyamplung trees are found in the coastal areas of Indonesia and are estimated to cover 480,000 ha of land (Bustomi et al., 2012; Zalsabila et al., 2024). Nyamplung seeds, which account for 40% of the fruit, have been used as a raw material for biofuel production, leaving behind the seed shells as waste after their extraction. Waste Nyamplung seed shell can also be used as a biomass energy source (Kartika et al., 2017; Leksono et al., 2014, 2017, 2019). As a charcoal briquette, Nyamplung seed shells have a CV of 5,431.35 cal/g (Hazra and Sari, 2011). Senthil and Mohan (2015) conducted proximate and ultimate analyses of Nyamplung seed shells and found that the moisture, ash, volatile matter, and fixed carbon contents (FCCs) were 9.56%, 1.75%, 69.04%, and 19.65%, respectively. Based on ultimate analysis, Nyamplung seed shells contained carbon (76.46%), hydrogen (6.46%), oxygen (5.29%), mineral matter (1.93%), nitrogen (0.31%), and sulfur (trace amounts; Senthil and Mohan, 2015).
In this study, we aimed to evaluate the effects of particle size and torrefaction temperature on the quality of Nyamplung seed-shell pellets (NSPs). Pellet samples were produced using the single-pellet method. Lee and Kim (2020) stated that the single-pellet process is an appropriate, fast, and low-cost method to obtain samples for small-scale tests to examine the pellet quality. The quality of torrefied NSPs was evaluated by measuring the properties of produced pellets, in accordance with the Indonesian National Standard (SNI) for household purposes (Badan Standardisasi Nasional, 2018).
2. MATERIALS and METHODS
The raw materials, namely, Nyamplung seed shells, used in this study were obtained from Purworejo, Central Java, Indonesia, which is a vast Nyamplung plantation in Indonesia that has been developed as a home industry for Nyamplung/Tamanu oil production. A completely randomized research design was employed with two treatment factors, namely, particle sizes (0.18–0.25, 0.25–0.43, and 0.43–0.84 mm) and torrefaction temperature (200°C, 225°C, and 250°C), with five replications. Variant analysis was applied to all research data, followed by Tukey’s honestly significant difference test to determine the significant differences in the average values.
Nyamplung seed shells were air-dried until the moisture content (MC) reached ± 12% and grounded until their size was homogeneous. Grounded raw material was sieved to 0.18–0.25, 0.25–0.43, and 0.43–0.85 mm. The resulting powders were densified (pelletizing) using a single pelletizer with hydraulic power at a pressing rate of 68 mm/min until a maximum compressive load of 150 kg/cm2 was reached. The die hole had a diameter and height of 8 and 55 mm, respectively, with a cylindrical pusher with a length of 100 mm.
Torrefaction was conducted at temperatures of 200°C, 225°C, and 250°C for 15 min. Torrefaction was conducted in a furnace with the following specifications: Thermolyne FB 1410M-33, single setpoint with a capacity of 2.1 L, power consumption of 1,520 W, temperature range of 100°C to 1,100°C, temperature stability of ± 5.0 at 1,000°C, and electrical requirements of 240 V at 50/60 Hz. Pellets without torrefaction were used as controls. Furthermore, the yield of the torrefaction treatment of NSPs was evaluated based on the weight loss of the sample.
The quality of the torrefied samples was evaluated by examining the compressive strength (CS) according to ASTM (2001), MC according to ASTM (2007), volatile matter content (VMC) according to ASTM (2007), ash content (ASH) according to ASTM (2007), FCC according to ASTM (2007), and CV according to ASTM (2010).
The yield was determined using torrefied pellets. The yield was calculated using the following Equation (1):
W1: pellet weight before torrefaction (g); W2: weight of the torrefied pellet (g).
The CS was evaluated as follows: the NSPs were placed between two flat metal surfaces on a Universal Testing Machine, and a load pressure was applied to determine the maximum CS of the samples.
The proximate description analysis of the pellets provided the basic characteristics of the pellet according to the following parameters: MC, VMC, and ASH based on the ASTM D176-84 standard, and FCC based on the ASTM D1762-84 standard.
The Equations (2) to (5) for the proximate evaluation are as follows:
a = weight of the air-dried sample (g).
b = weight of the sample after drying at 105°C (g).
c = weight of the sample after heating at 950°C (g).
d = weight of the sample after heating at 750°C for 6 h (g).
3. RESULTS and DISCUSSION
The results and appearance of the torrefied NSPs are shown in Fig. 1. The average CS values and proximate evaluation results for the torrefied NSPs are listed in Table 1.
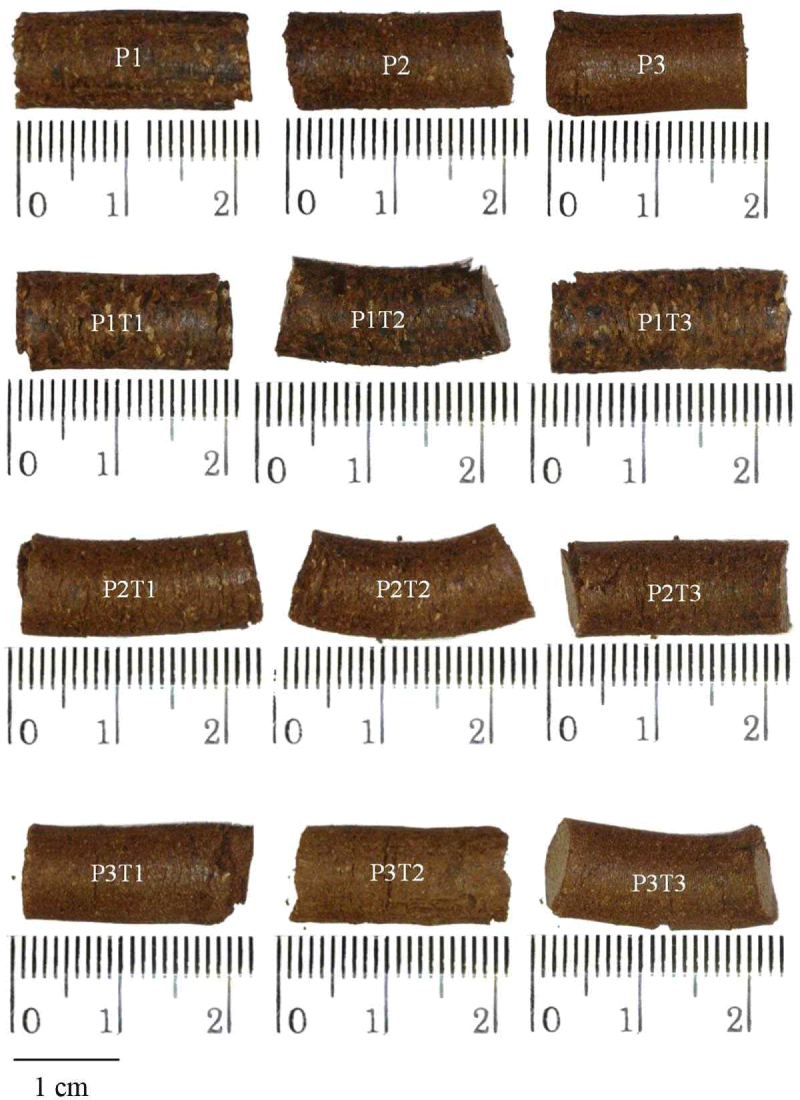
The torrefied NSPs exhibited slight deformation and color changes. The color became slightly darker, the shape of the torrefied pellet was slightly bent, and a few voids appeared on the entire surface. This color change is in accordance with the findings of Kim and Kim (2019), who reported that temperature treatment of P. tomentosa branches resulted in a color change from light brown to deep brown.
In this study, we showed that the torrefaction temperature had a significant effect on the yield of torrefied NSPs; the highest yield (91.39%) of torrefied NSPs was obtained at a torrefaction temperature of 225°C (Fig. 2). The decrease in the amount of torrefied biomass or mass loss, which is expressed in terms of the number of yields, is caused by the initial VMC that is easily removed with high-temperature treatment along with the torrefaction or activation process of biomass (Chandra et al., 2009; Kim, 2016; Sutapa and Hidyatullah, 2023).
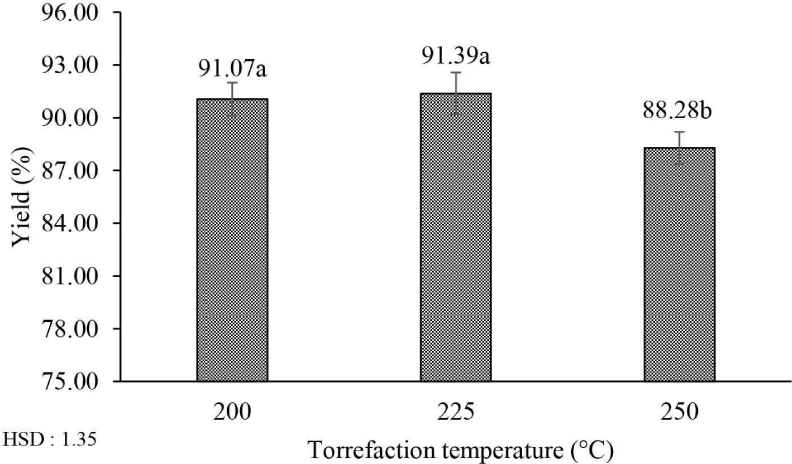
The CS of a pellet depends on the inner forces of the mechanical interlocking of particles established during the densification process (Yang et al., 2019). Analysis of variance (ANOVA) indicated that the interaction between the particle size and torrefaction temperature had a significant effect on the CS of NSPs at the 1% precision level. The CS of the torrefied NSPs ranged from 50.55 to 201.34 N, which was lower than that of Calliandra wood pellets after torrefaction treatment at a temperature of 250°C for 30 min, namely, 328.70 N, as indicated by Sutapa and Hidyatullah (2023). In this study, the highest CS value (201.34 N) of the torrefied NSPs was observed in pellets derived from a particle size and torrefaction temperature of 0.43–0.85 mm and 200°C, respectively. This CS value was higher than that of the control pellets (68.16 N). Increasing the torrefaction temperature and decreasing the particle size resulted in a decrease in the CS of torrefied NSPs (Fig. 3). The CS of torrefied NSPs with torrefaction temperatures of 200°C–250°C decreased by 15.83%–26.40%. These findings are consistent with those of Stelte et al. (2013), who found that after torrefaction at a temperature of 250°C–300°C, wheat stem-powder pellets showed a decrease in CS. Increasing the torrefaction temperature resulted in a change in the chemical composition of the pellet in the form of cellulose and hemicellulose degradation, which caused a decrease in the radial CS of the pellets. This is because at temperatures above 250°C, cellulose begins losing its stability and degrades, and its polymerization number decreases (Stelte et al., 2013). However, a lower CS provides benefits during the crushing and grinding of pellets used in the praxis of co-combustion with coal as the energy required for grinding and crushing is lower for pellets with lower CS (Stelte et al., 2013; Sutapa and Hidyatullah, 2023).
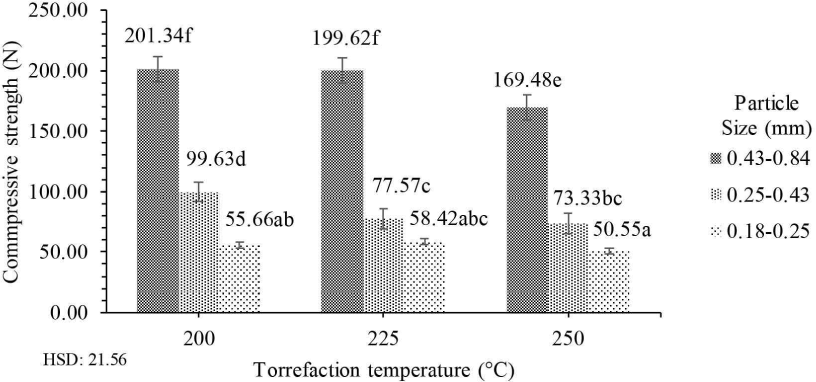
The ANOVA results showed that the interaction between particle size and torrefaction temperature had a significant effect on the MC of torrefied NSPs at the 1% precision level. The MC of torrefied NSPs ranged from 5.70% to 10.32%. In this study, the lowest MC value of torrefied NSPs (5.70%) was observed in pellets with a particle size of 0.43–0.84 mm and torrefied at a temperature of 250°C. This value is lower than that of control pellets with a particle size of 0.43–0.84 mm, namely, 14.10%. In this study, increasing the torrefaction temperature and decreasing the particle size significantly decreased MC (Fig. 4). The MC of NSPs with particle sizes of 0.43–0.84 and 0.25–0.43 mm torrefied at temperatures of 200°C and 250°C decreased by 26.64% and 26.45%, respectively. This phenomenon is consistent with the biomass drying stages; namely, the non-reactive drying (50°C–150°C), reactive drying (150°C–200°C), and destructive drying (200°C–300°C) phases. During heating at temperatures from 50°C to 150°C, water evaporates, and chemical changes occur as the result of the decrease of biomass weight and water content (Shankar Tumuluru et al., 2011). This result of NSPs is consistent with that of pellets from Southern Yellow Pine sawdust; namely, after torrefaction at a temperature of 250°C, the MC of these pellets decreased by 6.22%–1.45% (Manouchehrinejad and Mani, 2018). The MC of torrefied NSPs ranged from 5.70% to 10.32%, thereby fulfilling SNI 8675:2018 (≤ 12%).
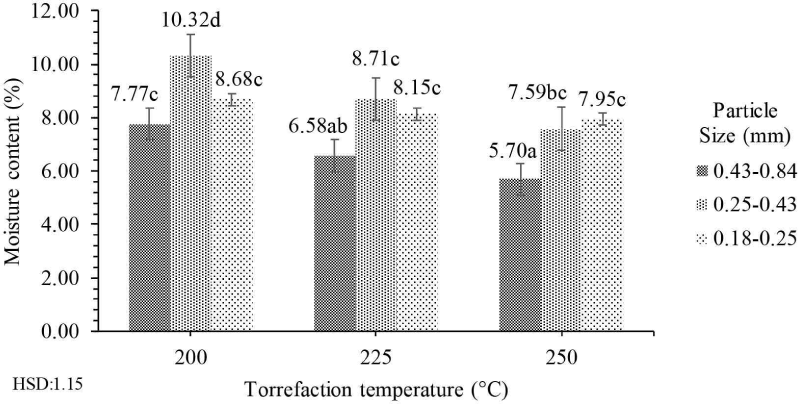
The component that evaporates at high temperatures in the absence of air is known as VMC (excluding water vapor). We observed a correlation between volatile compounds and quantity of smoke released during combustion. The bound carbon content of pellets is correlated with the amount of VMC in their components (Cahyani et al., 2023; Speight, 2015). In several countries, such as Korea, Japan, and the European Union, VMC from wood pellets is regulated by atmospheric environmental standards as it contributes to the emission number (Yang and Han, 2018). ANOVA indicated that the interaction between particle size and torrefaction temperature had a significant effect on the VMC of torrefied NSPs with 1% precision. The VMC of the torrefied NSPs ranged from 77.33% to 79.95% (Fig. 5). The lowest VMC of torrefied NSPs (77.33%) were observed in pellets with a particle size of 0.18–0.25 mm and torrefied at a temperature of 225°C; this value is lower than that of control pellets (4.55%) with a particle size of 0.18–0.25 mm. The VMC of torrefied NSPs with a particle size of 0.18–0.25 mm and a torrefaction temperature of 250°C was 77.95%. This value is higher than that of pellets derived from Merbau waste (76.57%), which was torrefied at 250°C for 15 min (Sutapa and Prasetyadi, 2023), and lower than that of Calliandra wood pellets (78.68%) torrefied at a temperature of 250°C for 60 min (Sutapa and Hidyatullah, 2023). In this study, increasing the torrefaction temperature and decreasing the particle size decreased the VMC of the torrefied NSPs (Fig. 5). The VMC of NSPs with particle sizes of and 0.43–0.84 and 0.18–0.25 mm and torrefied at temperatures of 200°C to 250°C decreased by 2.28% and 1.57%, respectively. This decrease was caused by the evaporation of water vapor and the decrease in the VMC materials during torrefaction. The internal process during torrefaction changes from endothermic, which forms volatile substances, to exothermic, which forms ash at a temperature of ± 270°C (Ju et al., 2020; Yun et al., 2021). The high VMC of wood pellets ranges from 70% to 86% of the dry weight; therefore, they are more reactive when burned compared with coal, whose VMC is only 35% (van Loo and Koppejan, 2008). The VMC of torrefied NSPs ranged from 77.33% to 79.95%, and these values are in accordance with the SNI quality standard (≤ 80%).

The material remaining in the pellets after burning contains ash, and its primary constituents are silica, calcium, potassium, and magnesium. The amount of ash present affects the thermal energy generated; the greater the amount of ash, the lesser is the generated energy (Cahyani et al., 2023; Poddar et al., 2014). Furthermore, pellets with higher ASHs are not recommended for industrial use (Wistara et al., 2017). The ANOVA results indicated that the interaction between particle size and torrefaction temperature had a significant effect on the ASH of torrefied NSPs at the 1% precision level. The ASH of torrefied NSPs ranged from 2.47% to 6.11%. In this study, the lowest ASH (2.47%) of torrefied NSPs was observed in pellets with a particle size of 0.43–0.84 mm and torrefied at a temperature of 250°C; this value is lower than that of control pellets with a particle size of 0.43–0.84 mm (2.76%). In this study, increasing the torrefaction temperature and decreasing the particle size increased ASH (Fig. 6). This result is consistent with that of Cahyanti et al. (2020), who found that increasing the torrefaction temperature increased the ASH. Other studies on the torrefaction of rice husks at temperatures of 210°C, 240°C, 270°C, and 300°C indicated that the ASH increased from an initial value of 15% before torrefaction to 16.20%, 16.90%, 20.20%, and 23.40%, respectively (Chen et al., 2018). These results are similar to the previous results on pellets derived from mixed raw materials of fir, pine, and spruce, which comprised two different particle sizes of 1.00–2.00 and 0.25–0.50 mm, and both materials were treated with the same torrefaction temperature of 240°C; the results indicated increasing ASHs of 0.40% and 0.52%, respectively (Wang et al., 2017).
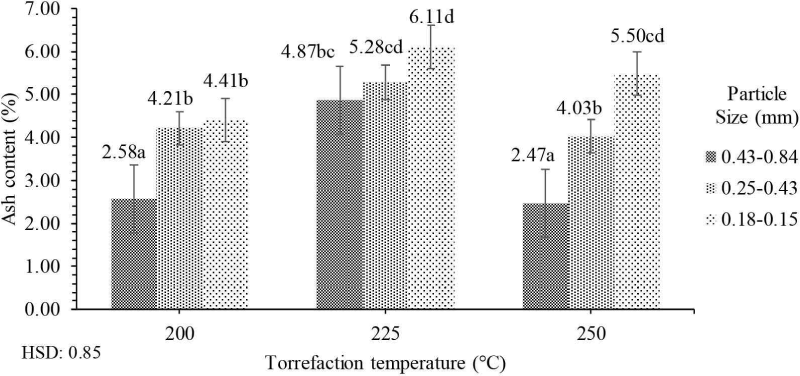
According to Manouchehrinejad and Mani (2018), smaller particles are more easily penetrated by heat during heating processes, such as torrefaction. Pellets with small particle sizes require shorter heating times; thus, they experience low mass losses, including ash, as non-combustible materials. The average ASH of torrefied NSPs was 4.38%, which already fulfilled SNI 8675:2018 (≤ 5%).
The FCC of the torrefied NSPs ranged from 15.72% to 19.42%. ANOVA showed that the interaction between particle size and torrefaction temperature significantly influenced the FCC of the torrefied NSPs at a 5% precision level. In this study, the highest FCC of torrefied NSPs (19.42%) was observed in pellets with a particle size of 0.43–0.84 mm and torrefied at a temperature of 250°C. The FCC of torrefied NSPs with a particle size of 0.43–0.84 mm and torrefaction temperatures of 200°C–225°C and 250°C increased by 1.31% and 11.61%, respectively (Fig. 7). The FCC of torrefied pellets increased owing to the decrease in VMC and MC (Aytenew et al., 2018). Furthermore, previous studies have found that as the torrefaction process reduced the O/C and H/C ratios, the carbon content of Larix kaempferi wood chips increased with increasing temperature and torrefaction duration (Lee et al., 2015). The increase in FCC of NSPs is consistent with the findings of Sutapa and Hidyatullah (2023), who stated that the FCC of Calliandra wood pellets increased when the torrefaction temperatures were increased to 250°C and 300°C. The FCC results for the torrefied NSPs fulfilled the SNI standard (minimum of 14%).
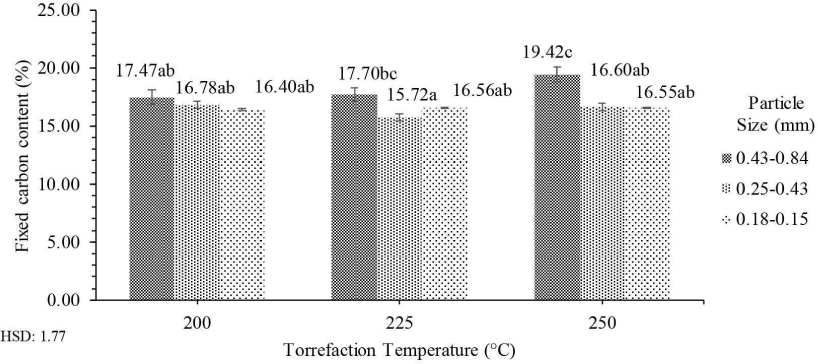
The CV can be increased by increasing the temperature and lengthening the torrefaction period (Lee and Kim, 2020; Matali et al., 2016; Sutapa and Hidyatullah, 2023). The ANOVA results indicated that the torrefaction temperature significantly affected the CV at the 5% precision level. The CV of torrefied NSPs ranged from 4,245.6 to 4,528.00 cal/g. In this study, the highest CV of torrefied NSPs (4,528.00 cal/g) was observed in pellets with a particle size 0.18–0.25 mm and torrefied at a temperature of 225°C; this value was higher than that of control pellets with a particle size 0.18–0.25 mm (4,277.80 cal/g). Our results indicated that an increase in torrefaction temperature from 200°C to 225°C and 250°C increased the CV by 3.79% and 3.11%, respectively. The CV values of this study are in line with the results of torrefied Calliandra wood pellets and torrefied palm fronds obtained by Sutapa and Hidyatullah (2023) and Lau et al. (2018), respectively; both studies reported an increase in the CV resulting from the increase in heating temperature. The CV of palm fronds increased by 29.58% at a heating temperature of 300°C for 30 min. Fig. 8 shows that the highest CV (4,433.93 cal/g) was obtained at a torrefaction temperature of 225°C, which is higher than the CV of NSPs torrefied at a temperature of 250°C. Therefore, this result implies that the limitations of the torrefaction temperature must be considered to obtain NSPs with good CV, because such pellets will lead to lower energy consumption and greater profitability from an economic perspective. The CV of torrefied NSPs ranged from 4,245.6 to 4,528.00 cal/g, thereby meeting the SNI standard (≥ 4,000 cal/g).
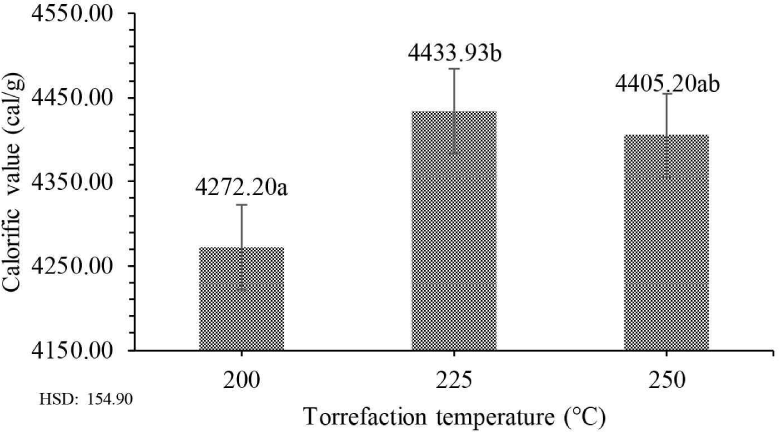
4. CONCLUSIONS
Our results indicated that Nyamplung seed shells are a promising material for pellet production. Our results showed that the interaction between the particle size and torrefaction temperature significantly affected the CS and proximate values of NSPs. Increasing the torrefaction temperature and decreasing the particle size resulted in a decrease in the CS, MC, and VMC of the torrefied NSPs and an increase in ASH and FCC. The CV of torrefied NSPs increased with increasing torrefaction temperature but decreased after a temperature of 225°C. The optimal parameters for producing NSPs are as follows: particle size of 0.18–0.25 mm and torrefaction temperature of 225°C. These parameters will result in a product with a high CV of 4,528.00 cal/g; this value fulfils the SNI standard (≥ 4,000 cal/g).