1. INTRODUCTION
Globally, as the damage from climate change intensifies due to excessive carbon dioxide emissions, efforts are underway to limit these emissions. Concurrently, research focuses on the efficient use of land, improved forest management, developing alternative energy sources to replace fossil fuels, and promoting the use of eco-friendly materials. Notably, trees, which utilize sunlight and carbon dioxide to grow can store significant amounts of carbon, are drawing increased attention (Ahn et al., 2021; Bergman et al., 2014). Wood has been a staple for building and furniture since ancient times and is presently used for diverse purposes, including pulp production (Ghani and Lee, 2021; Lee and Kim, 2022). For wood to serve as a primary long-lifecycle building material and maximize its carbon storage potential, its inherent combustibility must be addressed. In line with this, Korean domestic building regulations mandate the use of noncombustible, Quasi-noncombustible, and flame-retardant materials for interior finishes (e.g., on ceilings, walls, and columns) in larger structures to inhibit flame propagation and ensure safe evacuation (Cho et al., 2019).
To enhance the flame retardancy of wood, developers are exploring flame retardants based on various chemical compounds, including phosphorus, nitrogen, boron, and silicon, for use as single or combined materials (Jin and Chung, 2018). Concurrently, research has been conducted on eco-friendly flame retardants as a way to mitigate environmental pollution (Park et al., 2021). Most of these flame retardants operate by forming a protective layer on the wood surface, thus blocking the supply of oxygen (Xu et al., 2021). Kim et al. (2021) took this a step further by injecting wood with their self-developed flame retardant and then examining its combustion characteristics, focusing on the retardant’s absorption amount and the thickness of the protective layer. Their results confirmed that the treated wood met the quasi-noncombustible criteria set by the State. When evaluating the toxicity and health hazards of various flame retardants, phosphorus-based ones were identified as the safest (Wang et al., 2007). Additionally, there is a significant amount of ongoing research—both nationally and internationally—focusing on enhancing the flame retarding properties of wood, such as delaying ignition (Kim, 2018). Beyond solid wood, researchers are also striving to impart flame-retardant properties to plywood, commonly used in interior materials and furniture (Wen et al., 2020). This includes research on more efficient production techniques and assessing the strength of plywood post-treatment (Liu et al., 2021; Schulz et al., 2021).
On the one hand, the Tulip tree (Liriodendron tulipifera) is known as an excellent afforestation species that is well-suited to the climate and soil conditions of South Korea. Additionally, it is a fast-growing species, showing a growth pattern of slow and steady growth in the first 15 to 20 years and rapid growth thereafter (Ryu et al., 2003). Kim (2013) reported that the annual biomass growth rate of L. tulipifera is 54.0 kg/tree/y, and its carbon dioxide absorption rate is 99.1 kgCO2/Tree/y, indicating vigorous growth and a high carbon absorption rate. As such, abundant biomass production of L. tulipifera is expected, and there is a high potential for its diverse applications in the future as material for interior building, furniture, musical instruments, pulp, etc. Song and Kim (2022) analyzed the potential of L. tulipifera for use in cross-laminated timber, specifically in the z-axis layer, and reported satisfactory performance. However, little research has yet been dedicated to identifying combustion characteristics and flame retardancy for the utilization of L. tulipifera. Moreover, to enable the use of L. tulipifera as interior building material, appropriate processing and finishing treatments are required to protect the wood from external environments and to provide dimensional stability to the wood (Jung et al., 1998; Park et al., 2014). However, to the best of the authors’ knowledge, no research has yet been conducted on the effects of coating treatments on flame retardancy.
Therefore, this study was conducted to verify the flame retardancy of L. tulipifera, which is currently being extensively cultivated, in order to establish measures for its practical use in daily life. Additionally, by analyzing the combustion characteristics of L. tulipifera treated with flame retardants and finished with flame retardants and oil stain, this study aimed to gauge the impact of the finish on the wood’s combustion characteristics.
2. MATERIALS and METHODS
In this study, L. tulipifera was chosen as the test tree species. Using L. tulipifera lumber, three samples were produced for each of the following three finish types: untreated (A), flame retardant-treated (C), and flame retardant and oil-treated (B). For combustion performance evaluation, the sample dimensions were set in compliance with KS F ISO 5660-1 (Cone Calorimeter Test Specification). Before testing, the samples were stabilized at a constant temperature of 23 ± 2°C and a humidity level of 50 ± 5%. The finalized dimensions of each sample were 100 (R) × 100 (T) × 10 (L) mm3.
The flame retardant developed by the National Forest Science Institute (proprietary name: eGF) was used to impart flame retardancy to the flame-treated sample (C) and the flame-treated and oil-stained sample (B). The flame retardant used in this study comprises eight distinct ingredients, as listed in Table. 1. It is an inorganic, water-soluble formulation. Once the chemicals are adequately diluted, the resultant retardant is colorless and odorless.
Samples were spaced out to avoid overlap and secured before the flame retardant impregnation. The impregnation process followed this sequence: depressurization for 30 minutes (1.5 MPa) → flame retardant injection for 30 seconds → pressurization for 60 minutes (12–15 MPa) → depressurization for 10 minutes (1.5 MPa). The impregnation was carried out using a vacuum pressure resin system (Myung Sung Tech, Gimpo, Korea; Fig. 1). The samples absorbed approximately 25.5% of the retardant.
Post-treatment was performed to prevent splitting caused by contraction and swelling in the flame retardant-treated L. tulipifera samples and to add aesthetic elements. This involved one application of 1–2 g of primer (House oil, Holloway House, Houston, TX, USA), followed by two applications of water-based stain (Stain, Bondex, Søborg, Denmark; Fig. 2).
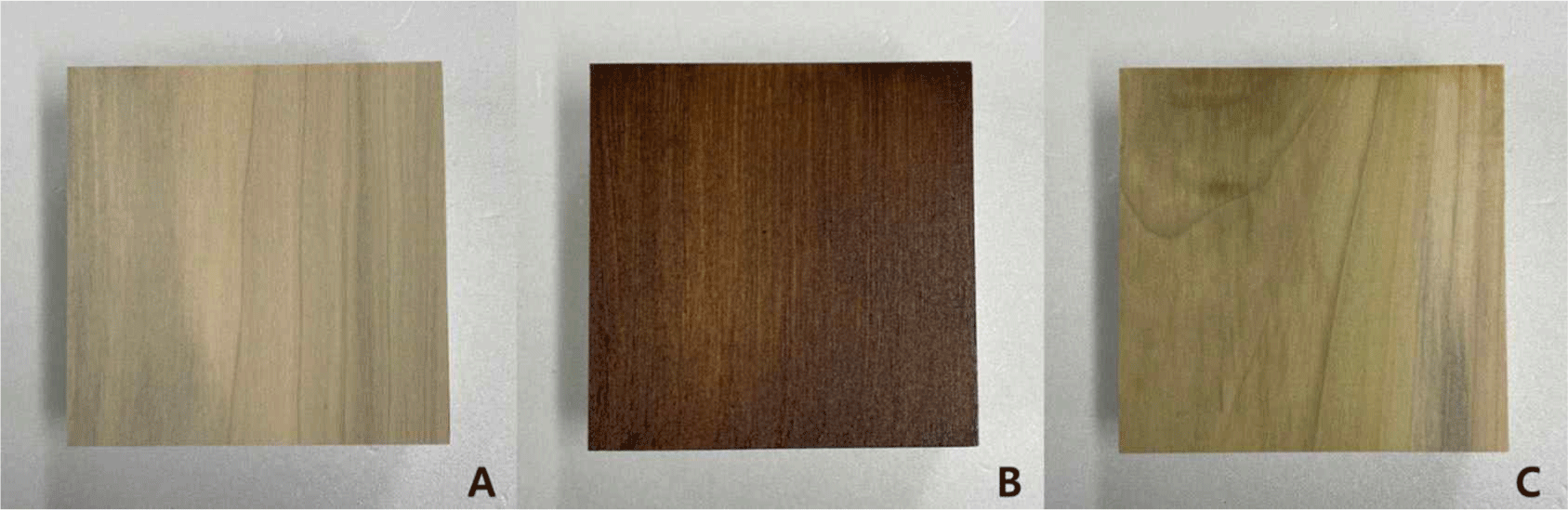
Combustion characteristics of each treatment type of L. tulipifera samples were assessed according to the KS F ISO 5660-1 (Cone Calorimeter Method). This method is mandatory for evaluating noncombustible, quasi-noncombustible, and incombustible materials, as defined in the Enforcement Decree of the Building Act (Kim et al., 2012). The combustion was carried out for 10 minutes. To evaluate incombustibility and quasi-noncombustibility, both the peak heat release rate and the total heat release were investigated. Article 3 of Notification No. 2015 -744 from the Ministry of Land, Infrastructure, and Transport (flame retardant performance of building finishing materials and basic structures to hinder fire spread) specifies the flame retardancy criteria as follows: total heat release should not exceed 8 MJ/m2 within the first 5 minutes for incombustible materials and within the first 10 minutes for quasi-noncombustible materials post the onset of heating, and the peak heat release rate should not exceed 200 kW/m2 for 10 consecutive seconds.
3. RESULTS and DISCUSSION
In this study, total heat release is defined as the cumulative amount of heat emitted due to the combustion of a sample. This measure can be used to estimate the potential size of a fire incident in real-world scenarios (Kim and Song, 2016). The combustion characteristics of the samples under three conditions, as measured using the Cone Calorimeter Method, yielded the following results: The average total heat released during 5 minutes following the heating onset was 32.4 MJ/m2 for untreated samples (A), 2.3 MJ/m2 for flame retardant-treated samples (C), and 6.1 MJ/m2 for flame retardant and oil stain-treated samples (B). The average total heat released during 10 minutes following the heating onset was 61.9 MJ/m2 for sample A, 9.4 MJ/m2 for sample C, and 16.4 MJ/m2 for sample B (Table 2). In comparison with the standards set by the Ministry of Land, Infrastructure, and Transport, both treatment conditions (samples C and B)—with the exception of untreated samples (A)—satisfied the incombustibility standards. However, none of the samples achieved the quasi-noncombustibility standards. Among the three sets, the flame retardant-treated samples (C) recorded the lowest total heat release, followed by flame retardant and oil stain-treated samples (B), and untreated samples (A) in ascending order (Figs. 3 and 4). The diminished flame-retardant performance in the flame retardant- and oil stain-treated samples (B) compared to the flame retardant-treated samples (C) is likely due to the increased heat release during the combustion of the oil component of the sample when it reacts with oxygen (Abraham, 1996). For this reason, caution should be exercised regarding potential reductions in flame retardancy when incorporating oil stains for aesthetic or protective purposes.
Samples | Density (g/cm3) | Total heat release (MJ/m2) | |
---|---|---|---|
5 min | 10 min | ||
A | 0.48 ± 0.02 | 32.4 ± 3.0 | 61.9 ± 3.5 |
B | 0.68 ± 0.03 | 6.1 ± 1.5 | 16.4 ± 4.2 |
C | 0.66 ± 0.05 | 2.3 ± 0.8 | 9.4 ± 1.5 |
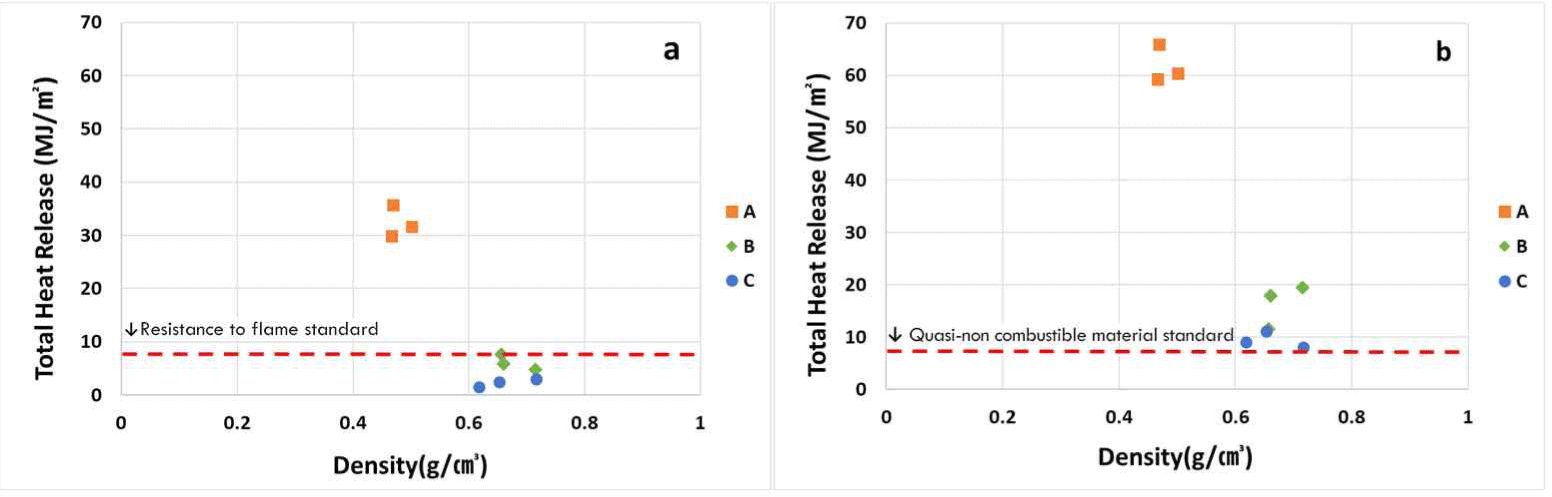
Heat release is determined by inversely measuring the amount of oxygen consumed during the combustion of a sample. The initial growth rate and size of a fire can be estimated from the peak heat release rate observed in its early stages (Lee et al., 2004). The average peak heat release rate, measured over 5 minutes after the start of heating, was 137.1 kW/m2 for untreated samples (A), 8.5 kW/m2 for flame retardant-treated samples (C), and 11.5 kW/m2 for flame retardant and oil stain-treated samples (B). During the subsequent 10-minute period, the average peak heat release rates were 185.7 kW/m2 for samples A, 56.7 kW/m2 for samples C, and 71.8 kW/m2 for samples B (Table 3). The average results from all three conditions met the incombustibility and quasi-noncombustibility standards set by the Ministry of Land, Infrastructure, and Transport. When wood is exposed to heat, its heat release rate tends to hit two peaks (Grexa and Lübke, 2001). This phenomenon occurs because the carbonized layer, formed after volatile components evaporate during combustion, hinders the influx of air, thereby slowing the diffusion of heat. The degree of carbonization corresponds directly to the duration of heat exposure (Xu et al., 2015). This study also observed a similar pattern, with the flame retardant-treated samples (C) displaying the lowest heat release rate, followed, in ascending order, by flame retardant and oil stain-treated samples (B) and untreated samples (A). Similar to the observations on total heat release, the heat release rate also seemed to be influenced by the oil stain. Son and Kang (2015) documented that treatment with flame retardants can lead to an 85% decrease in the peak heat release rate. Consistently, this study illustrated a decrease in the peak heat release rate when samples were treated with flame retardants (Figs. 5 and 6).
Samples | Wood density (g/cm3) | Peak heat release rate (kW/m2) | |
---|---|---|---|
5 min | 10 min | ||
A | 0.48 ± 0.02 | 137.1 ± 50.4 | 185.7 ± 25.8 |
B | 0.68 ± 0.03 | 11.5 ± 0.4 | 71.8 ± 5.1 |
C | 0.66 ± 0.05 | 8.5 ± 2.7 | 56.7 ± 14.4 |
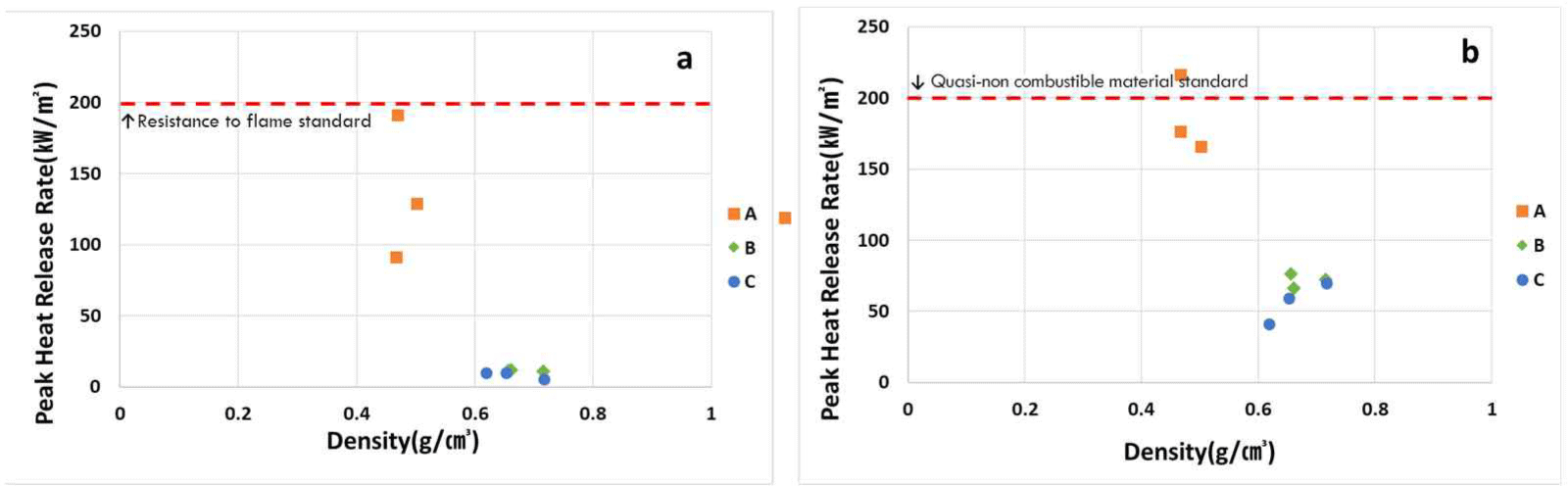
The testing material of this study is the diffusive porous wood of L. tulipifera, a broadleaf species with its large vessels being randomly scattered within the growth ring boundaries. The diameters of these vessels range from 50 to 100 μm, and they are present in large quantities. Additionally, the top and bottom surfaces of the vessel elements are interconnected with scalariform perforation plates, leading to high porosity (Kang et al., 2011). Apart from these vessel elements, there are thick-walled wood fibers with minimal intracellular lumina.
Previous research using the same cone calorimeter method to investigate the relationship between the density and combustion characteristics of diffusive porous wood has shown that as the density increases, both the total heat release and peak heat release rate tend to rise in all selected species (Table 4, Fig. 7). The performance deterioration during the combustion of wood is determined by changes in its components, depending on the species and moisture content (Ragland et al., 1991). Park et al. (2020) reported differences in flame retardancy in their study investigating the combustion characteristics of deciduous Quercus, birch, cypress, and pine. They emphasized the need for further research on various species and wood products. From this, it can be inferred that differences in combustion characteristics may be due to the content of wood fibers that determine the density of diffusive porous wood.
Combustion properties data of other wood. Data from Seo et al. (2015, 2016); Son and Kang (2014).
4. CONCLUSIONS
In this study, we analyzed the combustion characteristics of L. tulipifera, which is one of the major afforestation species in Korea. To assess its flame retardancy, we examined the combustion characteristics of flame retardant-treated and untreated samples. Given their potential use in interior building materials, we also included test samples coated with finishes designed to provide pest resistance, preservative functions, and aesthetic enhancements.
In the analysis of the combustion performance across the three sample conditions, flame retardant-treated samples (C) showed the highest flame retardancy, followed by the flame retardant- and oil stain-treated samples (B), and the untreated samples (A).
The reduced flame retardancy of the flame retardant and oil stain-treated samples (B), used for protective and aesthetic purposes, compared to the flame retardant-treated samples (C) is likely due to the increased heat release during combustion of the oil component of the sample when it reacts with oxygen. Nevertheless, as combustion occurs slowly, this factor is not believed to significantly impede its application.
A comprehensive analysis of the results of previous studies and the present study revealed that wood density strongly correlates with its combustion performance. This suggests that variations in combustion performance might be associated with the wood’s inherent components, warranting further analysis in subsequent research.