1. INTRODUCTION
Various wood-based composites have been developed (Cha et al., 2022; Lee et al., 2021; Liu et al., 2021; Sumardi et al., 2022; Wibowo et al., 2021). Oriented strand board (OSB) is an engineered wood-based panel based on waferboard. Elmendorf applied for a patent in 1963 as a result of a study that involved turning wafers into strands and orienting them, and OSB products have been commercially available since 1980 (Armin, 1963; Bengston et al., 1988; Zerbe et al., 2015). OSB is often used as a substitute for plywood in light-frame wood structures because the price of plywood has increased owing to the lack of raw wood supply.
In the Korea, there are no OSB manufacturing factories; therefore, the country relies entirely on imports. According to data from the Korea Trade Statistics Promotion Agency, 24 countries exported OSB to Korea between 2007 and 2021, including five countries in the Americas, nine in Europe, one in Oceania, and nine in Asia. During this period, Korea imported 961,351 tons of OSB, with an average annual import volume of 64,090 tons (Fig. 1). Canada was the largest exporter to Korea, with 356,839 tons (37.1%), followed by Romania (196,588 tons) and the United States (153,192 tons).
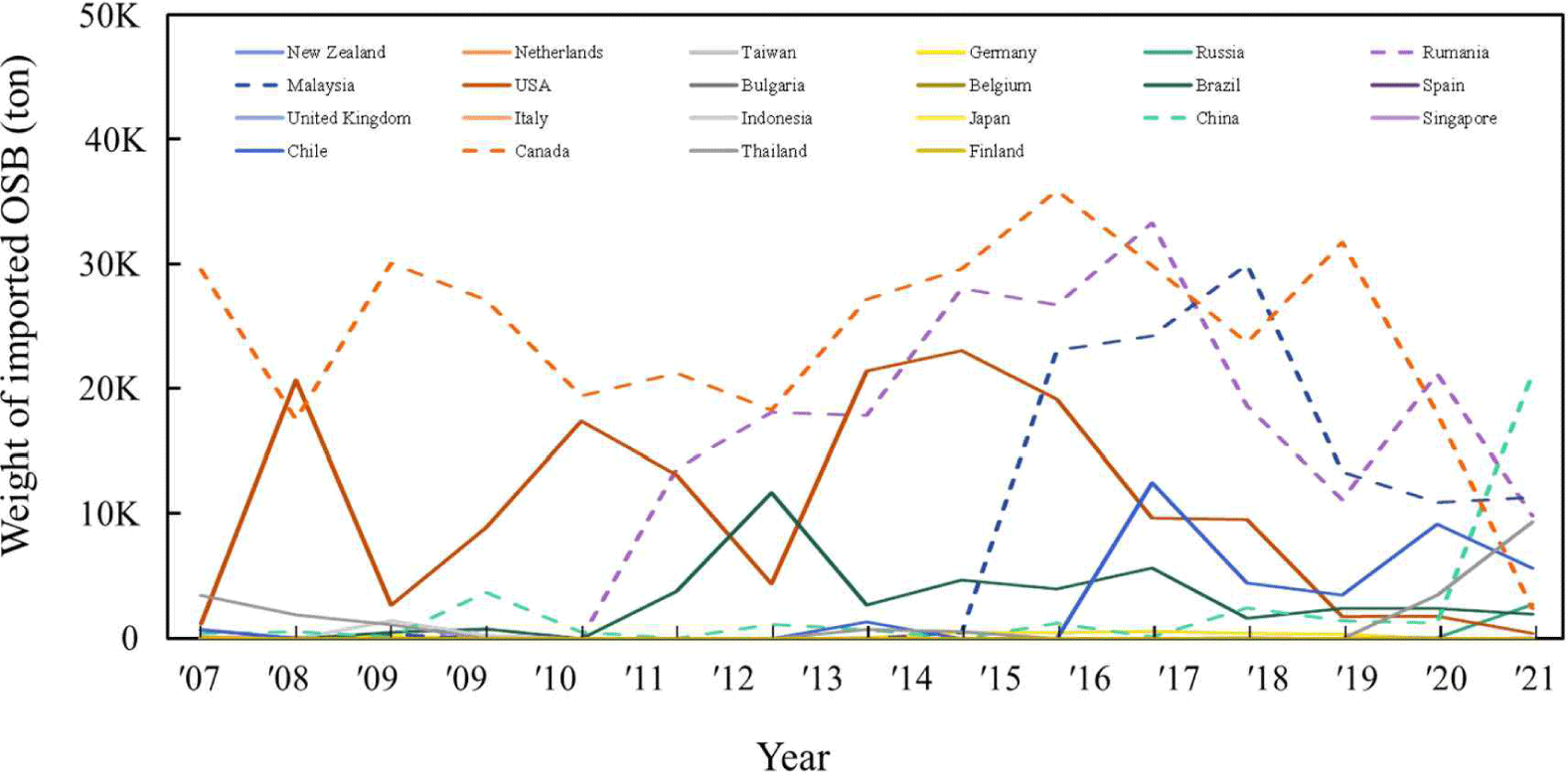
In the early days of OSB imports, these products were mainly imported from North America; however, from 2016, imports have tended to decrease slightly. Romanian OSB imports increased sharply from 2011 and then started to decrease from 2017 to 2021, except for 2020 (Fig. 1). In addition, imports from Malaysia increased in 2015, but decreased in 2018. In particular, OSB imports from China increased by approximately 1,576% by 2020, and imports from Thailand and Russia also showed an increasing tendency. This trend is believed to be caused by the initial high dependence on North American OSB products owing to their high reliability, followed by an increase in OSB production in plants established in other continents based on the differentiation of raw materials and manufacturing technology. In addition, it is thought that the import target country has shifted to those in the Asian region as competition in OSB prices has increased owing to the supply and demand of raw materials, expansion and improvement of the use of no-added formaldehyde (NAF) resin adhesives, and optimization of the manufacturing process. Alternative materials to replace OSB have been sought, and efforts have been made to enhance the physical properties of wood-based panels (Ahn et al., 2021; Cahyono et al., 2020; Hwang et al., 2021; Lee and Oh, 2023; Setyayunita et al., 2022).
The use of imported OSB in Korea is closely associated with light-frame wood houses. As shown in Fig. 2, from 2011 to 2020, the trends in the number of annual light-frame wood houses built and the amount of OSB imports were similar (Korea Trade Statistics Promotion Institute, 2021). According to data from the Korea Forestry Promotion Agency, as shown in Fig. 3, imports of OSB were mainly for packaging in 2014, for structural/exterior use from 2015 to 2017, and for interior use in 2018 (Korea Forestry Promotion Institute, 2014, 2015, 2016, 2017, 2018, 2019).
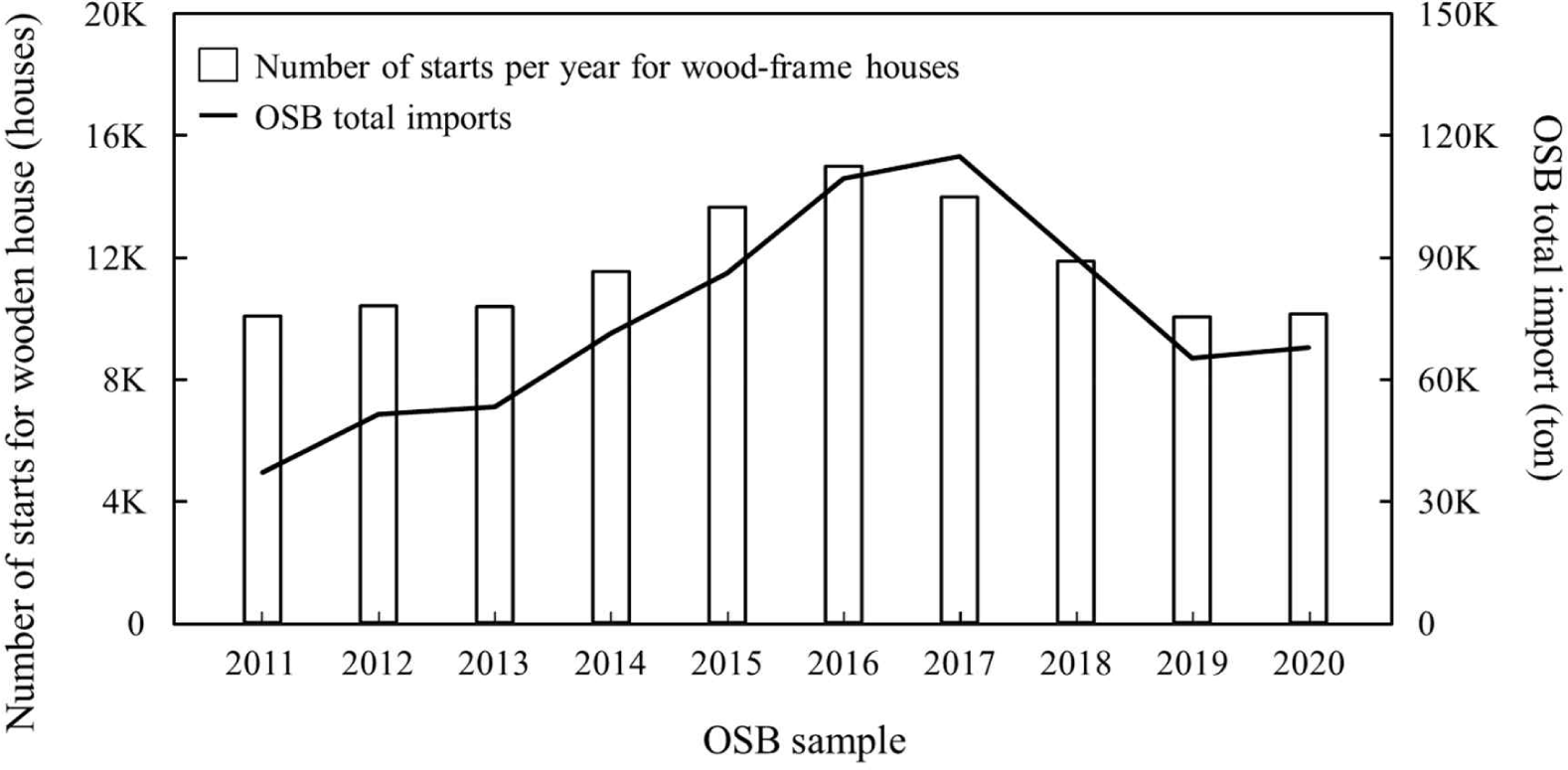
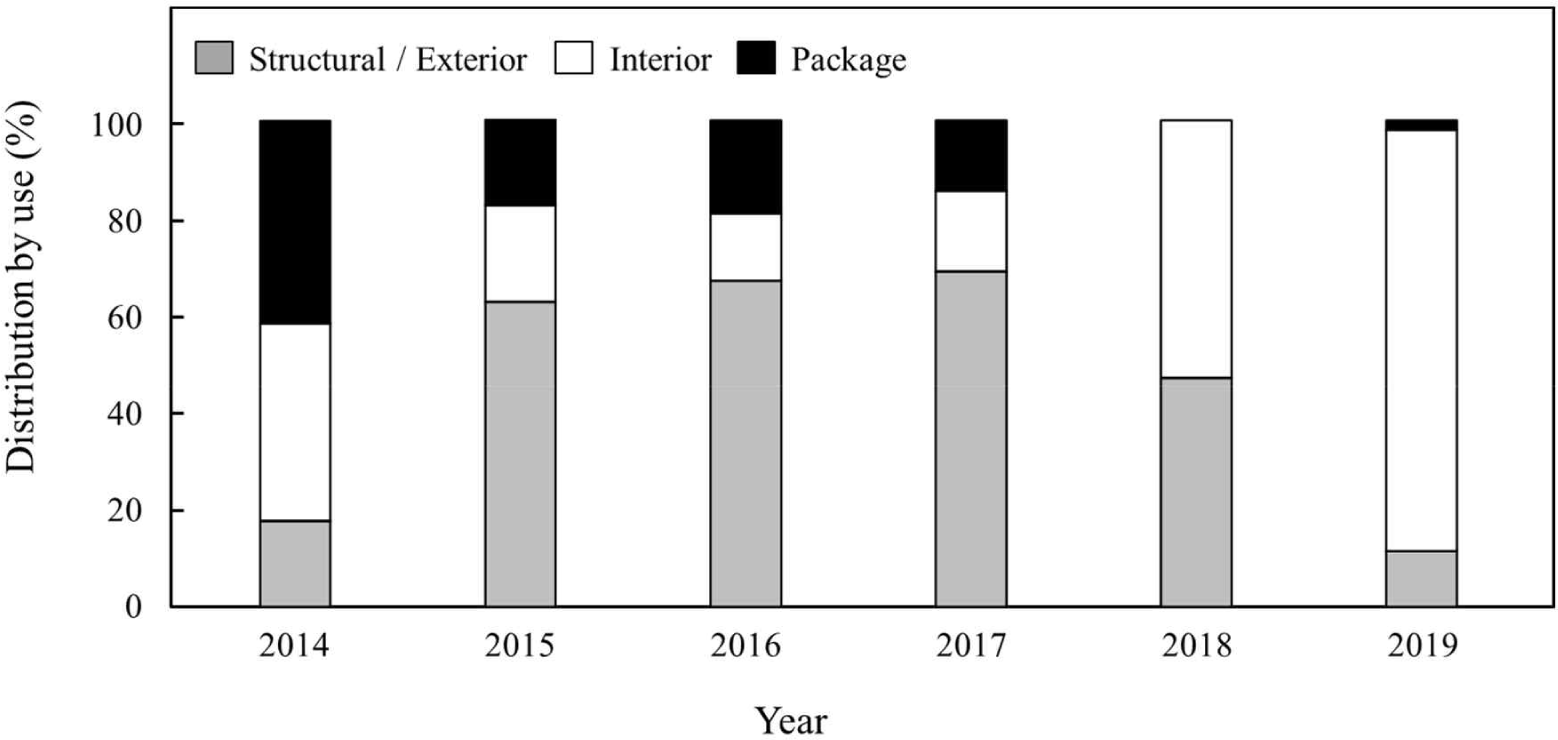
The demand for structural OSB is expected to increase as the demand for construction materials increases; however, the usage of structural OSB has not increased as expected. In contrast, trade statistics show that OSB imports for use in interiors have increased. Currently, in Korea, a quality mark is legally required for wood products. Nevertheless, some construction sites use the product for a purpose different from its original purpose, without verifying the quality standards. Additionally, because the OSB distributed in the country is imported from various countries, changes in performance of the product may occur depending on the manufacturing date, storage period, transportation process, and storage conditions after being imported. Incorrect usage and changes in product quality can affect consumers. In the long term, this will lower consumers’ trust and prevent them from using OSB products.
Therefore, in this study, imported OSBs distributed in the Korean market were purchased and their mechanical performance was evaluated according to the International Organization for Standardization (ISO), Japanese Industrial Standards (JIS), and Korean Industrial Standards (KS) test methods to confirm whether they met the indicated grade mark. In addition, based on the results of the performance evaluation, we examined the trends of domestic wood-based panel supply and the lines of research on OSB.
2. MATERIALS and METHODS
Ten types of OSBs distributed in Incheon and Gyeonggi provinces were purchased. The purchased OSBs had three different thicknesses, 11.0, 15.0, and 18.0 mm, and their size was 1,220 mm by 2,440 mm. Detailed information on the collected OSBs is presented in Table 1.
The collected OSBs were classified into wall and floor types, based on their quality grades and thicknesses. Each of the classified OSBs could be divided into North American, Asian, and European products produced by different manufacturers in five countries. Each product was classified according to thickness into 11.0, 11.5, and 15.0 mm for walls and 18.0 mm for floors. The grades were divided into rated sheathing for walls, rated stud-I-floor for floors, and premium subflooring products. These grades are arbitrarily assigned by manufacturers according to the American Plywood Association (APA) standards. European and Asian products were classified into load-bearing (LB) grades for both walls and floors according to the ISO standard. The adhesive performance was classified into Exposure 1 grade, which is the APA standard, and regular (REG) and moisture-resistant (MR) products, which are ISO standards. Only European and Asian products were marked for formaldehyde emissions and rated as E1 and E0, respectively.
The mechanical properties of ten types of OSBs distributed in Korea were tested according to ISO (2009). First, for each type of OSB, five panels were selected from a total of 20 panels and used as samples. The sample (1,220 mm × 2,440 mm) was cut and distributed according to the specifications of each test piece so that each part of the sample could be evenly included in all tests.
ISO (2009) classified OSBs into general purpose non-load-bearing OSB for interior fitment for use in dry conditions (GP-REG), load-bearing OSB for use in dry conditions (LB-REG), load-bearing OSB for use in humid conditions (LB-MR), and heavy duty load-bearing OSB for use in humid conditions (HLB-MR; Table 2). The performance of the OSB was evaluated by dividing it into general requirements, requirements for specified mechanical and swelling properties, and requirements for moisture resistance. Accordingly, thickness (ISO, 2003b and 2003c), moisture content (MC; ISO, 2003e), density (ISO, 2003a), formaldehyde emission (ISO, 2016), flexural strength (ISO, 2003d), modulus of elasticity (ISO, 2003d), internal bonding strength (ISO, 2009), thickness swelling (ISO, 2003g), and internal bonding strength after boil (ISO, 2003f) were selected as evaluation items, and the performance was evaluated according to the ISO test method.
Property | ISO (2009) | JIS (2015) | KDS (2018) | Test method | ||||||||
---|---|---|---|---|---|---|---|---|---|---|---|---|
GP-REG1) 10-18 mm | LB-REG2) 10-18 mm | LB-MR3) 10-18 mm | HLB-MR4) 10-18 mm | Structural PB/OSB 9 mm | Structural OSB | |||||||
≥ 11 mm | ≥ 15 mm | ≥ 18 mm | ||||||||||
ISO | General requirements | Thickness (mm) | ± 0.8 | ± 0.8 | ± 0.8 | ± 0.8 | - | - | ISO (2003b) | |||
Moisture content (%) | 2-12 | 2-12 | 2-12 | 2-12 | - | - | ISO (2003e) | |||||
Tolerance on the mean density within a board (g/cm3, %) | ± 15 | ± 15 | ± 15 | ± 15 | - | - | ISO (2003a) | |||||
Formaldehyde emission (mg/L) | - | - | - | - | - | - | ISO (2016) | |||||
Requirements for specified mechanical and swelling properties | Bending strength (MPa) | ||5) | ≥ 18 | ≥ 20 | ≥ 20 | ≥ 28 | - | - | ISO(2003d) | |||
∠6) | ≥ 9 | ≥ 10 | ≥ 10 | ≥ 15 | - | - | ||||||
Modulus of elasticity in bending (MPa) | || | ≥ 2,500 | ≥ 3,500 | ≥ 3,500 | ≥ 4,800 | - | - | |||||
∠ | ≥ 1,200 | ≥ 1,400 | ≥ 1,400 | ≥ 1,900 | - | - | ||||||
Intemal bond (MPa) | ≥ 0.28 | ≥ 0.32 | ≥ 0.32 | ≥ 0.45 | - | - | ISO (2003h) | |||||
Swelling in thickness (%) | ≤ 25 | ≤ 20 | ≤ 15 | ≤ 12 | - | - | ISO (2003g) | |||||
Requirements for moisture resistance | Internal bond alter boil test (MPa) | - | - | ≥ 0.13 | ≥ 0.15 | - | - | ISO (2003f) | ||||
JIS | Bending strength in wet conditions (N/mm2) | || | - | - | - | - | ≥ 9 | - | ISO (2005) | |||
∠ | - | - | - | - | ≥ 9 | - | JIS (2015) | |||||
Nail-head pull-through force (kN) | - | - | - | - | ≥ 1 | - | JIS (2015) | |||||
Lateral nail resistance (kN) | || | - | - | - | - | ≥ 1 | - | JIS (2015) | ||||
∠ | ||||||||||||
KDS | Allowable bending strength for structural wood-based panels (MPa) | || | ≥ 6.9 | ≥ 7.3 | ≥ 6.7 | KSA (2017) | ||||||
∠ | ≥ 2.1 | ≥ 2.6 | ≥ 2.7 | |||||||||
Allowable modulus of elasticity in bending for structural wood-baed panels (MPa) | II | ≥ 6,500 | ≥ 7,400 | ≥ 7,800 | ||||||||
∠ | ≥ 1,200 | ≥ 1,700 | ≥ 1,600 |
Moreover, according to JIS (2015) and ISO (2005), the bending strength of each OSB was measured to compare its water resistance performance. Additionally, nail head pull-through and lateral nail resistance tests were conducted to evaluate the nail joint performance. To assess the structural bending performance of the OSB, the KSA (2017) method was employed for bending tests on structural wood-based panels, and the results were evaluated and compared with the Korean Design Standard (KDS, 2022) criteria for wood-based structural materials and allowable stress.
3. RESULTS and DISCUSSION
Table 3 presents the results of evaluating the physical and mechanical performances of 10 types of OSBs for walls and floors in Korea. The average thicknesses of the four types of OSB products for walls (A, B, C, and E) with a target thickness of 11 mm ranged from 11.04 to 11.65 mm. Product D, which has a target thickness of 11.5 mm, measured 11.93 ± 0.10 mm. Product F, with a target thickness of 15 mm, measured 15.55 ± 0.11 mm, which slightly deviates from the target thickness but still meets the standard (target thickness ± 0.8 mm). For the floor, product J, with a target thickness of 18 mm, measured 17.65 ± 0.07 mm. The other three products exceeded the target thickness, but they still satisfied the standard (target thickness ± 0.8 mm).
The MC of the OSBs used for the walls ranged from 4.17% to 8.02%. Product B had the lowest MC of 4.17 ± 0.82%, whereas product C had a higher MC with a SD of 4.14%. Products D and E had the highest MC levels, at 8.01% and 8.02%, respectively, compared to the other products. It should be noted that these results may be influenced by various factors such as manufacturing, packaging, transportation, and storage conditions. Nonetheless, all the tested OSB products met the standard MC range of 2%–12%.
The density of the four types of OSBs for walls was between 0.59 and 0.68 g/cm3. The densities of products A, B, and C were 0.60–0.67 g/cm3, whereas those of products D and E were 0.68 ± 0.04 g/cm3 and 0.59 ± 0.01 g/cm3, respectively. Moreover, the density of product F was 0.59 ± 0.03 g/cm3. Regarding the density of products for floors, those of products G and H were 0.67 ± 0.04 g/cm3 and 0.64 ± 0.04 g/cm3, respectively, that of product I was 0.59 ± 0.04 g/cm3, and that of product J was 0.61 ± 0.02 g/cm3. Overall, products E and F for the walls and products I and J for the floors showed relatively lower densities. The partial density was examined based on the average density of each sample. For walls, it was as follows: product A, 0.57–0.83 g/cm3; product B, 0.45–0.72 g/cm3; product C, 0.56–0.75 g/cm3; product D, 0.57–0.88 g/cm3; product E, 0.48–0.75 g/cm3; and product F, 0.50–0.68 g/cm3. For flooring, it was as follows: product G, 0.57–0.84 g/cm3; product H, 0.40–0.75 g/cm3; product I, 0.48–0.70 g/cm3; and product J 0.55–0.72 g/cm3. The wide-range density distribution in an OSB is influenced by factors such as the proportion of raw materials and target density of the board, compaction ratio, and product grade setting. As such, the range of the partial density of OSB is wider than that of MDF or PB, and is expected to affect the actual physical properties.
Formaldehyde emissions were not observed in the OSBs from North America. OSBs are marked as E0 for Asian products and E1 for European products. However, as a result of measuring the formaldehyde emission of each product, it was classified as SE0 grade at 0.04–0.14 mg/L (Fig. 4). It has been reported that OSBs manufactured by North American companies mainly use exterior resins, that is water-resistant phenol-formaldehyde resin adhesives and methylene diphenyl diisocyanate (MDI) resins (APA, 2017; Gonçalves et al., 2021). The adhesives used by OSB manufacturers in Europe are distributed as follows: 75% polymeric MDI resin, 10% urea-formaldehyde resin adhesive, and 15% melamine-urea-formaldehyde resin adhesive (Mantanis et al., 2018). This trend is expected to be similar for OSB manufacturers in Asia; however, recently, the proportions of MDI and NAF resins have increased slightly. The increase in usage of MDI resin could affect the transportation and storage periods. Therefore, formaldehyde emissions from imported OSBs are generally expected to be less than 1.5 mg/L.
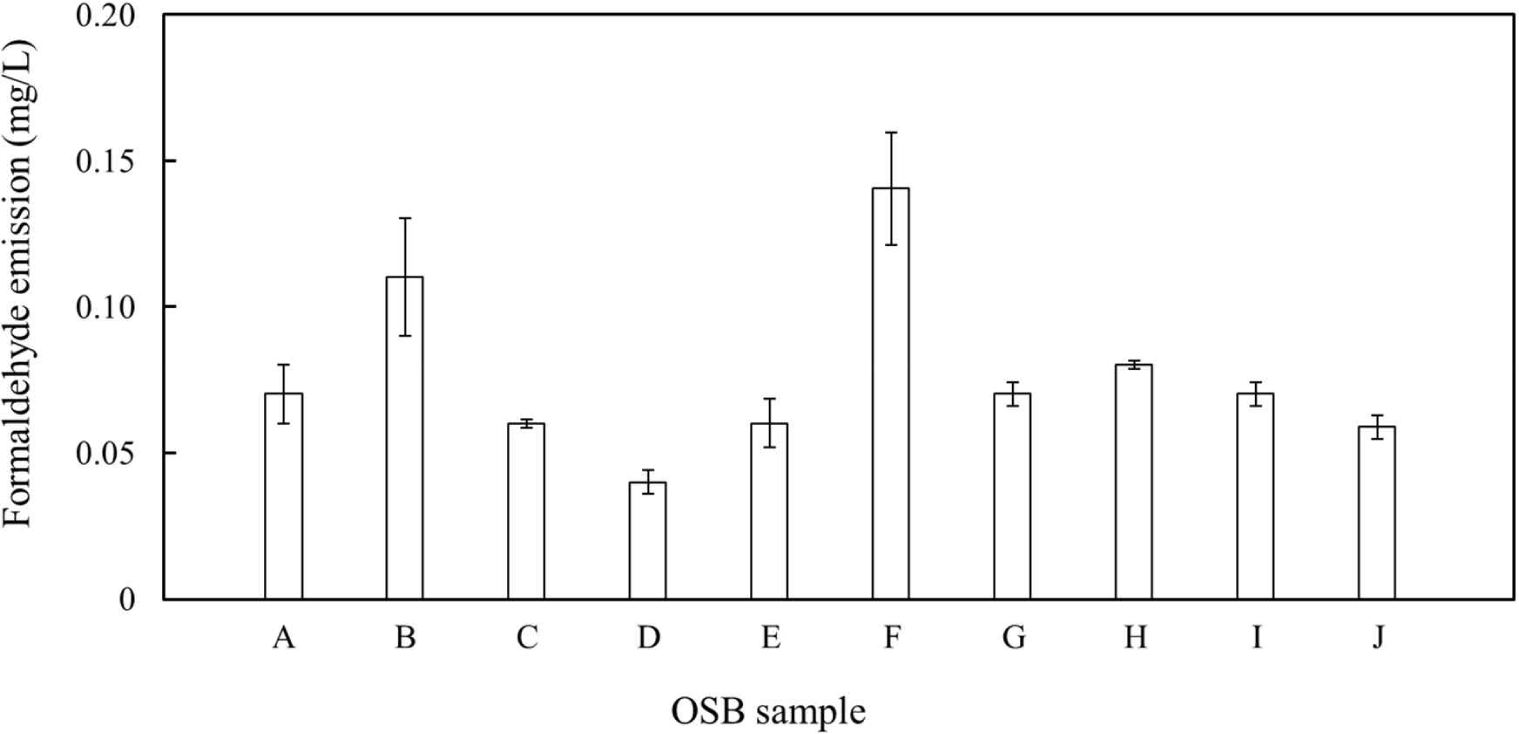
The bending strengths of the specimens are shown in Fig. 5. In the case of the OSBs for walls, both the main and minor axes of product F satisfied the LB grade standard, whereas the other products exceeded the indicated quality mark. For the OSBs used on floors, two products were classified as HLB-MR grade, whereas the other products were LB grade. However, after considering the modulus of elasticity in the bending standards for the major and minor axes, all the OSBs for the walls were classified as LB (Fig. 6). In particular, the moduli of elasticity (minor axis) of the D and H products were higher than those of the other products. For the floors, product G received an HLB-MR grade, whereas the other products satisfied the LB grade. Based on these results, the bending strength of the imported OSB distributed in Korea was determined to be LB grade.
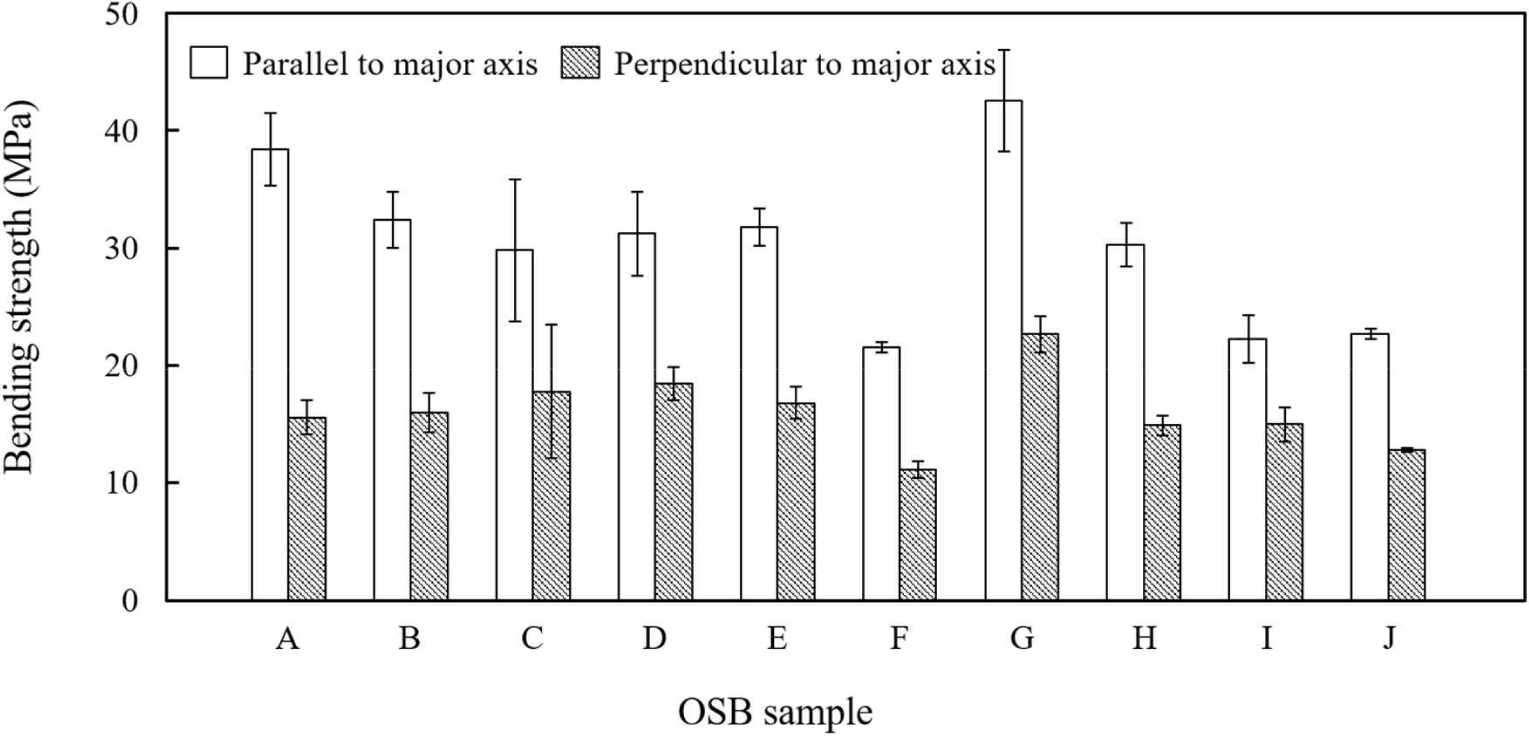
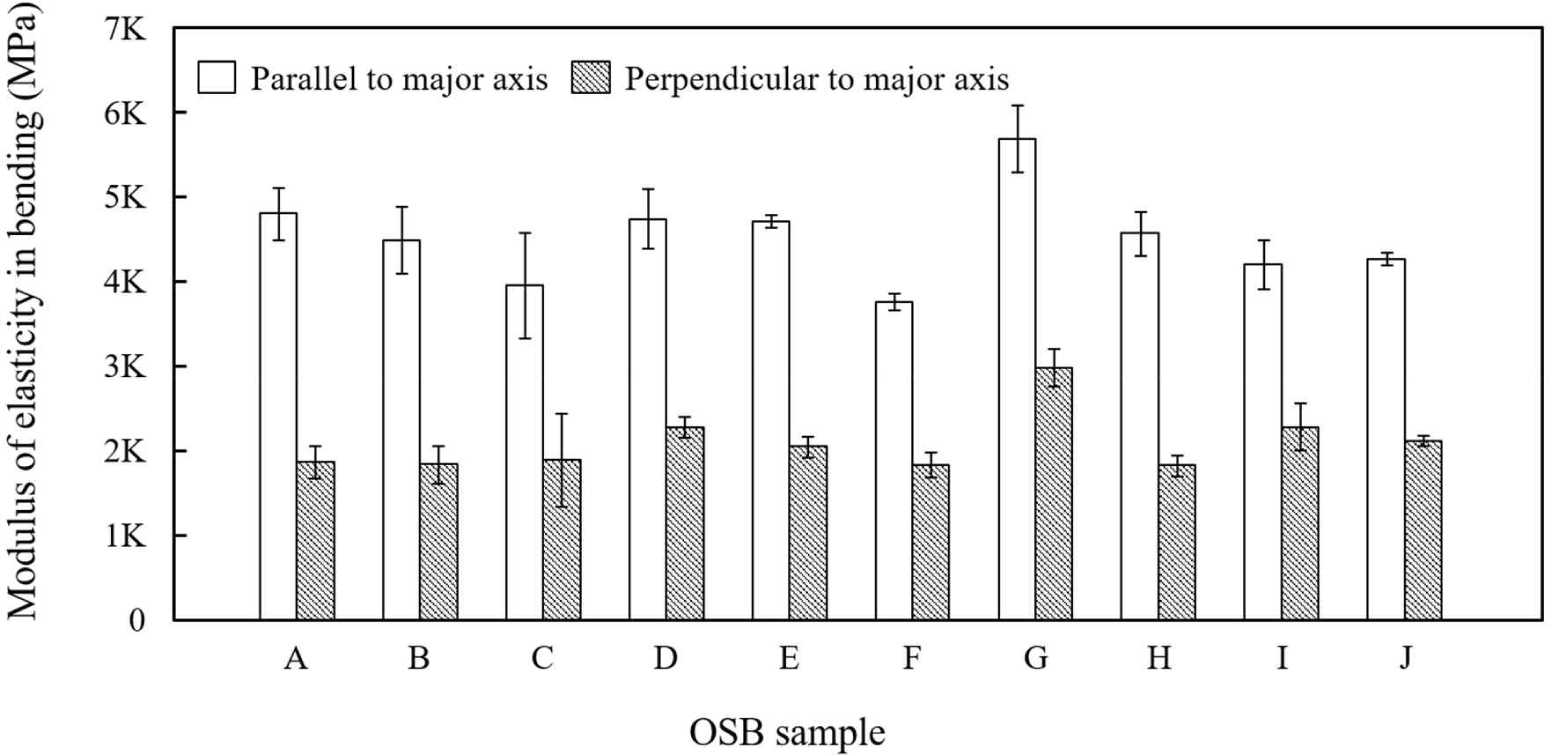
The internal bonding strength of six types of OSBs for walls ranged from 0.28 to 0.84 MPa (Fig. 7). Product B was labeled as Exposure 1 grade, but the test results showed that it was GP-REG grade. Products C, E, and F were LB grade, whereas products A and D were labeled Exposure 1 and LB-REG, respectively, but were determined to be HLB-MR. The product G for floor was HLB-MR grade with a strength of 0.96 ± 0.07 MPa, and product J was LB grade with a strength of 0.37 ± 0.02 MPa. However, the other two products did not meet the GP-REG grade standard and therefore did not match the indicated grade.
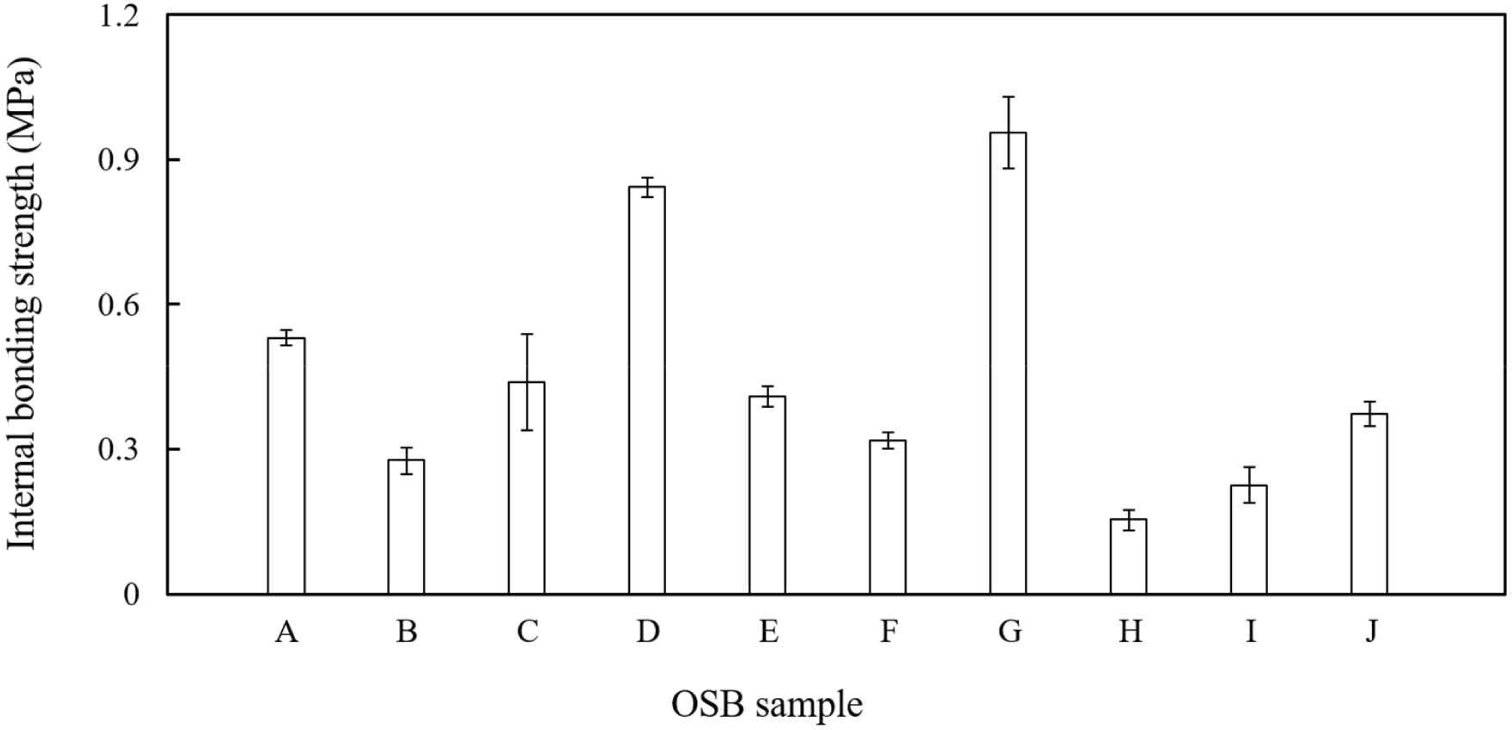
In terms of thickness swelling, products C and F, classified as GP-REG, exhibited lower performance than products A and B, which were classified as LB-REG, as shown in Fig. 8. Product E was classified as LB-MR, whereas product D was classified as HLB-MR. Overall, products E and D showed relatively better performances than the other products. Product H was classified as GP-REG, while product J was classified as LB-REG. Product I was classified as LB-MR, and product G was classified as HLB-MR, indicating that products I and G exhibited better performances than the others.
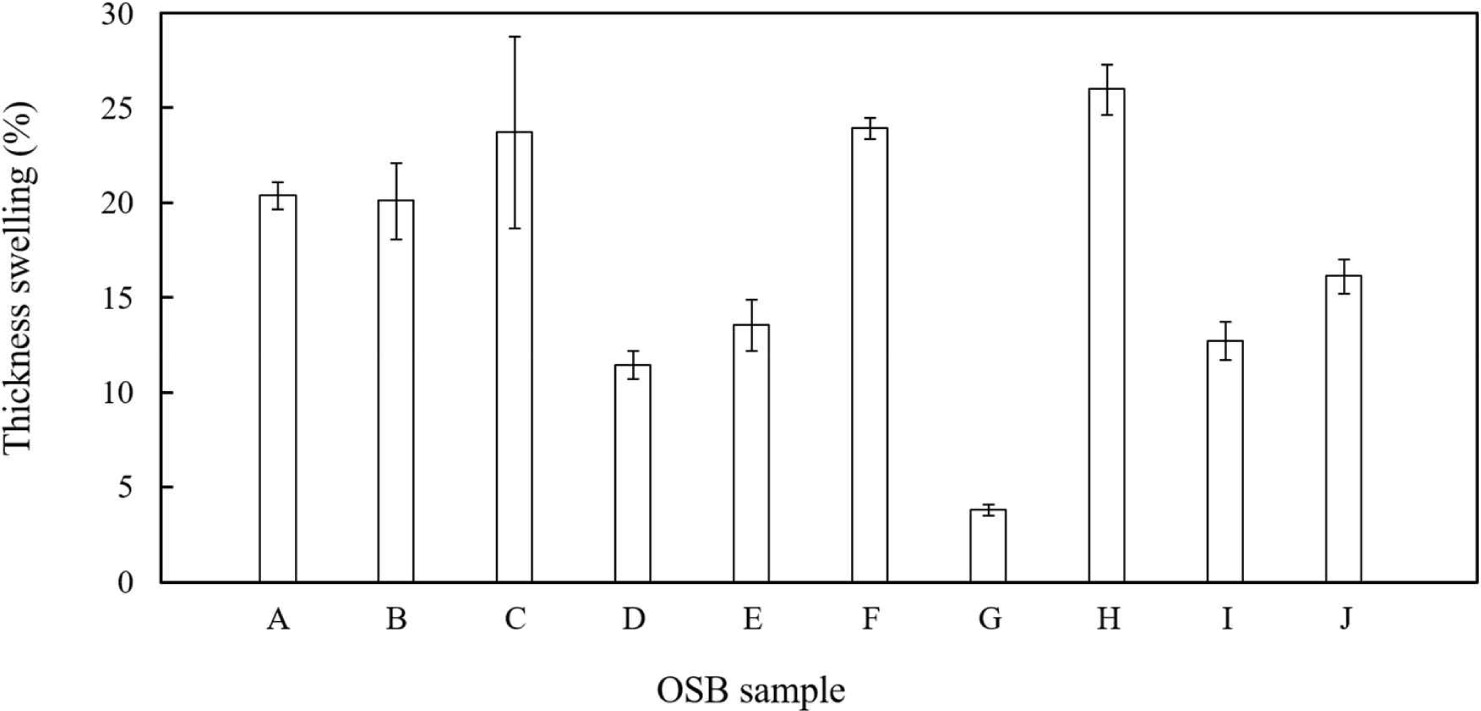
According to the standards for LB-MR-grade products, the bending strength must be maintained after boiling. Products F and J were tested for bending strength after boiling and did not meet the standard (above 0.13 MPa) with results of 0.08 ± 0.01 MPa and 0.12 ± 0.02 MPa, respectively (Fig. 9). However, product D for the walls and product G for the floors exceeded the required grade and satisfied the HLB-MR standard. All other products were rated as LB-REG. Even under wet conditions, the bending strengths of products D and G satisfied the standard of more than 9 N/mm2 on the main and minor axes, respectively (Fig. 10). Products A, B, C, and E for walls and H for floors satisfied the standard for the main axis only, whereas products F, I, and J did not satisfy the standard for either the main or minor axes.
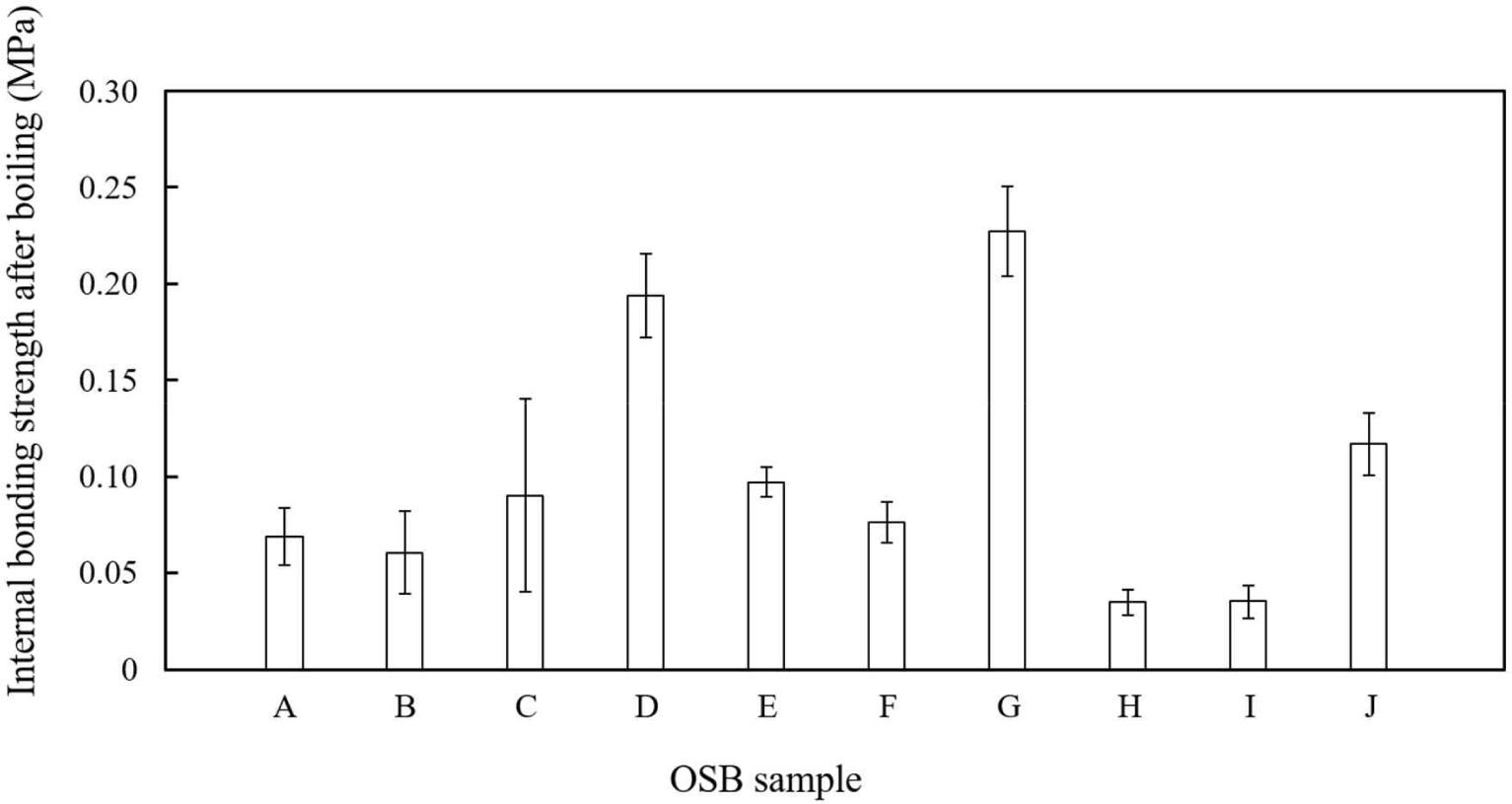
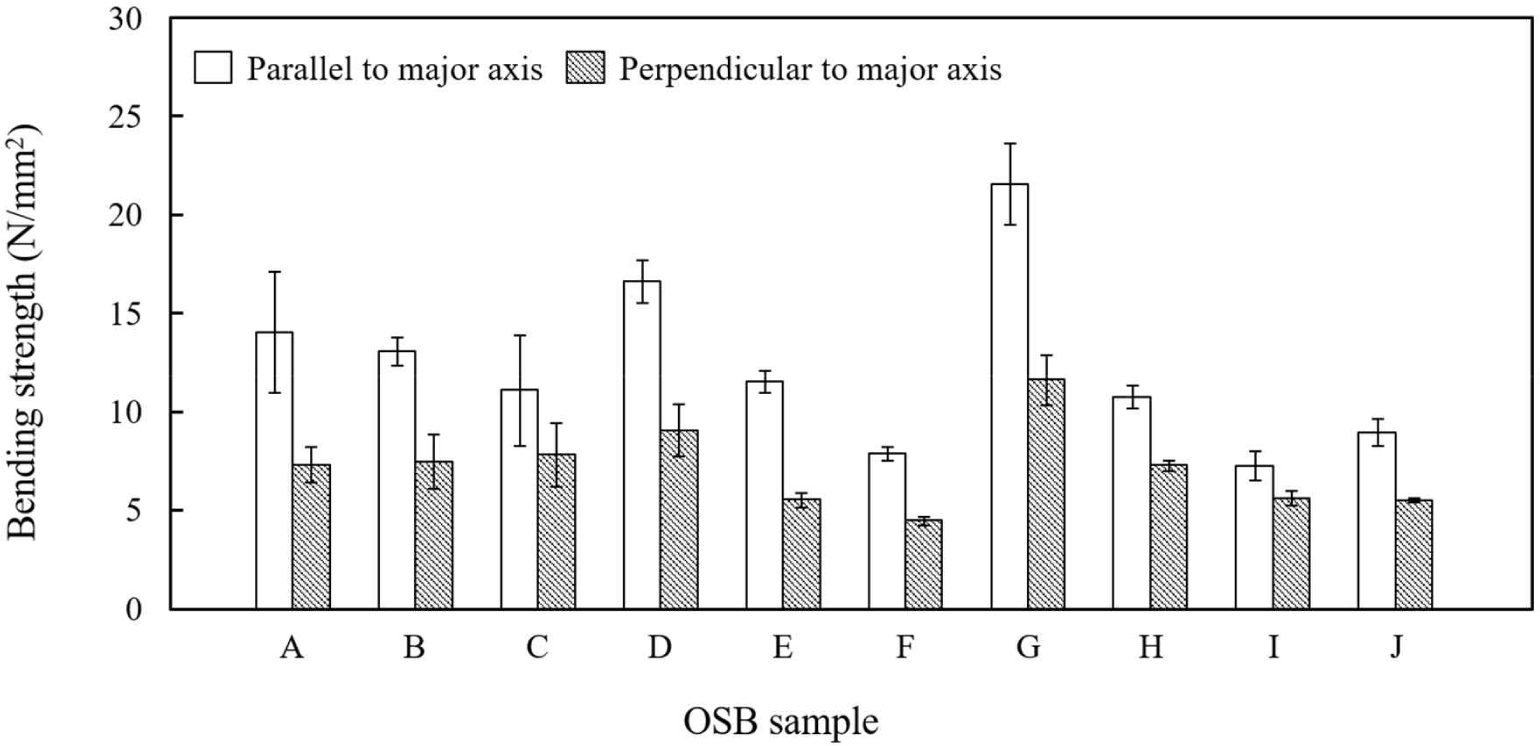
Fig. 11 shows the results of the nail head pull-through force measurements. According to the JIS standards, all OSB products for walls and floors satisfied the standard requirement of 1.0 kN. OSB is composed of oriented wood strands and is similar to plywood. The stacking state of the material, specific gravity of the raw material, and density of the OSB can affect its mechanical properties.
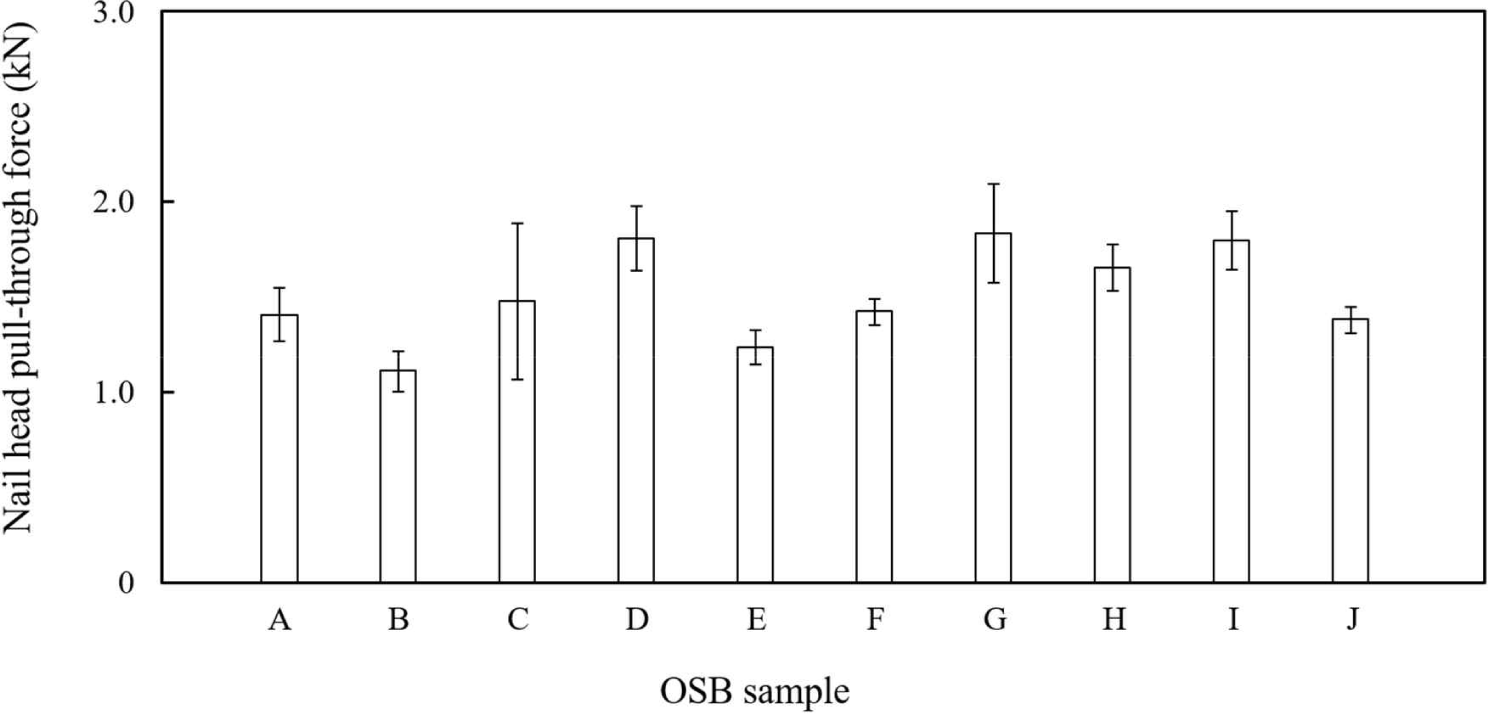
In the lateral nail resistance test, the performance of the OSB was measured by dividing it into main and minor axes based on its orientation. The results showed that all the products met the JIS standard of 1.0 kN, as depicted in Fig. 12. Generally, the minor axis, which corresponded to the width direction of the OSB, exhibited higher performance than the main axis, which corresponded to the longitudinal direction.
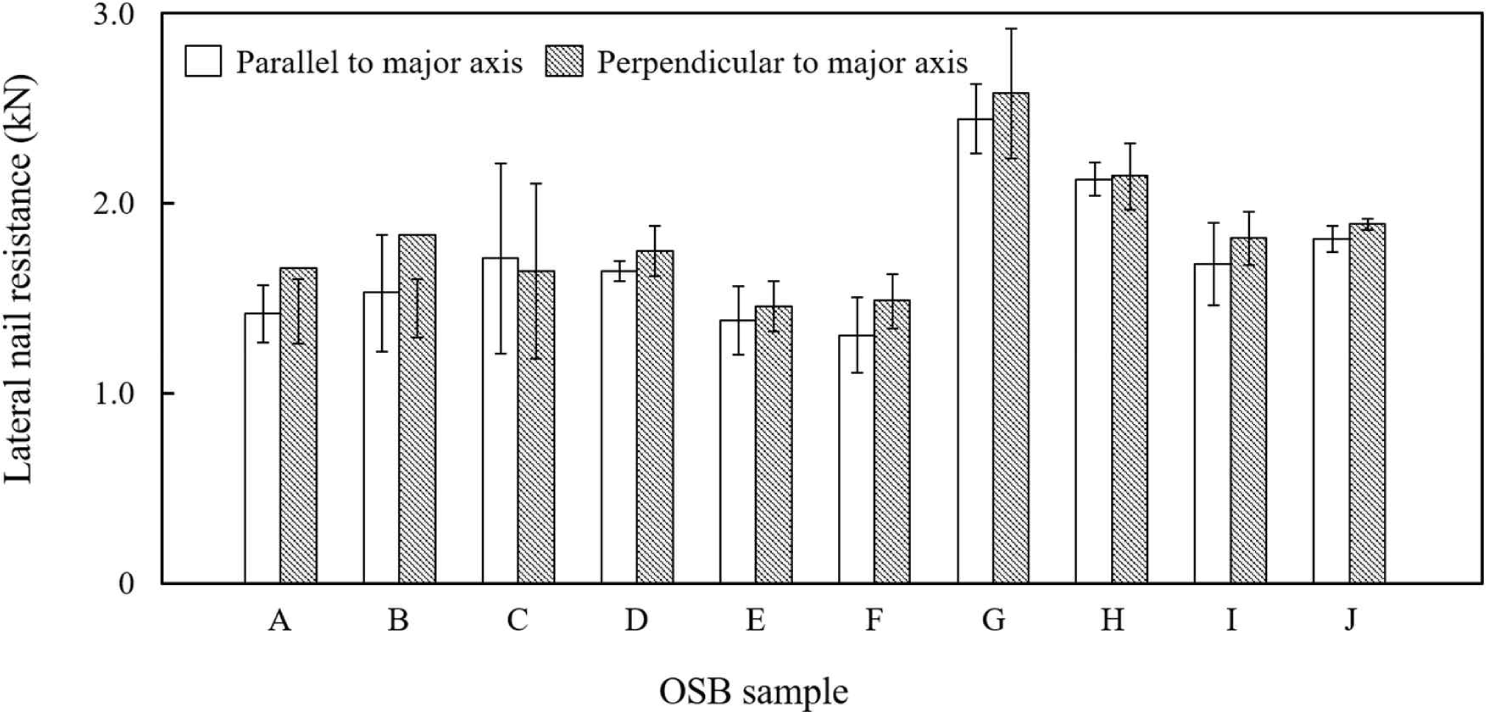
Table 4 presents the results of bending strength tests (measured at four points) conducted on the OSBs to evaluate their structural performance. The KS method was employed in these tests.
All the specimens met the KDS standard for allawable bending strength in both the major and minor axes, as shown in Fig. 13. However, among the wall OSBs, product F showed comparatively lower properties, whereas the higher-density products among the floor OSBs exhibited relatively higher properties. The modulus of elasticity of the wall OSBs satisfied all KDS standards by thickness, as depicted in Fig. 14. However, for floor OSBs, products H, I, and J did not exceed these standards. The test results indicated that the failure of the floor OSBs to meet the standards was due to their wider density distribution than that of the wall OSBs and other factors including wood species, thermal pressure conditions, and storage conditions.
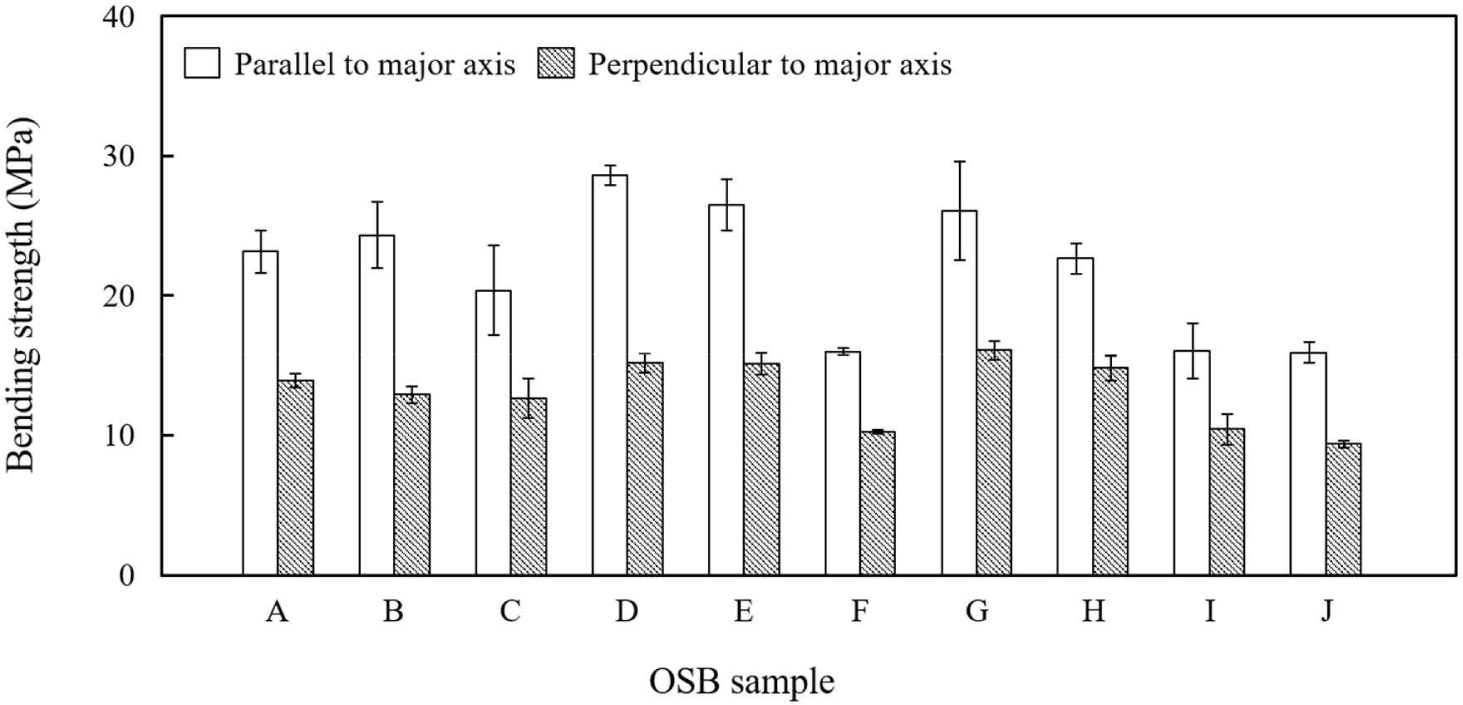
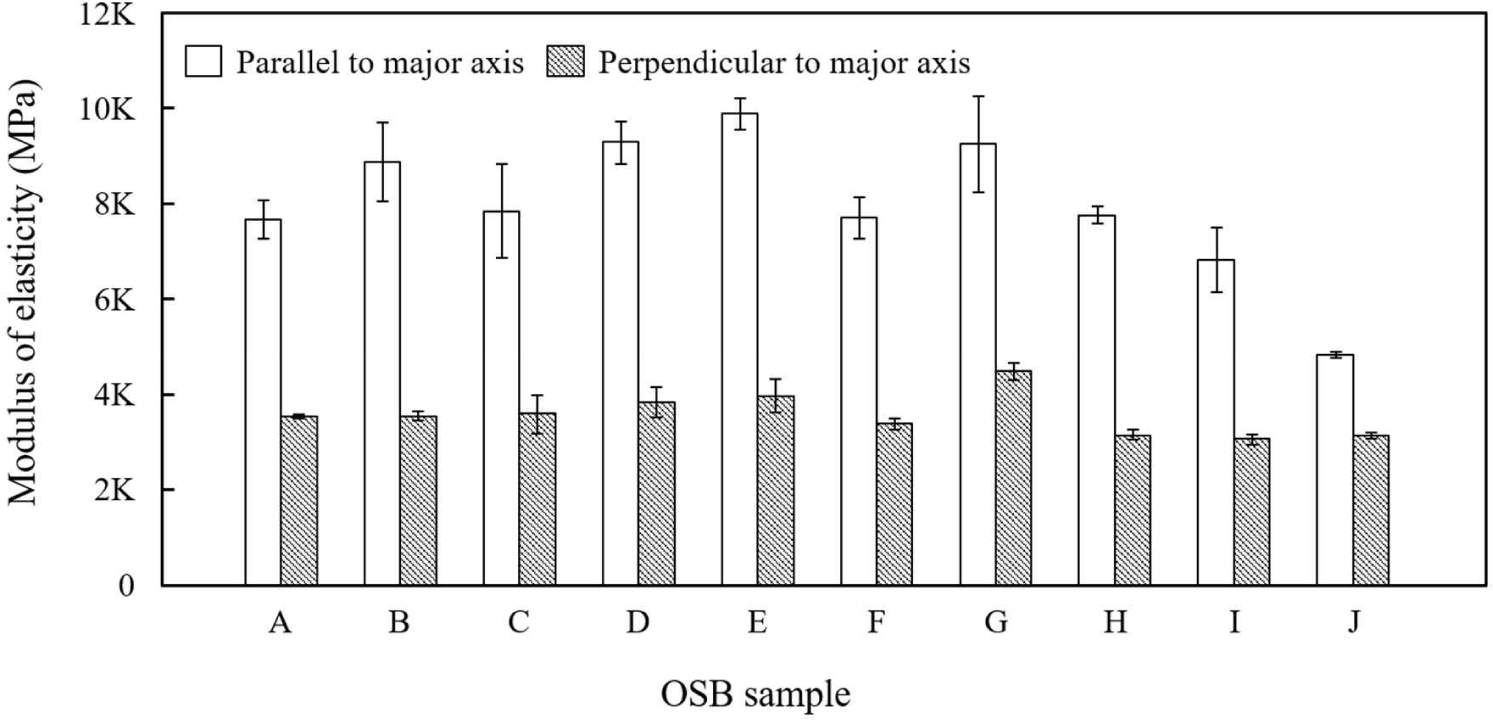
4. CONCLUSIONS
This study was conducted to evaluate the performance of OSBs imported in Korea and determine whether these products meet the ISO standards and labeled grade. This study collected six types of OSBs for walls and four types for floors and evaluated their performance based on the ISO (2009), JIS (2015), and KDS (2022) standards. The thickness, MC, and density of each product met the ISO standards, and the formaldehyde emission were of SE0 grade for products marked as grades E1 and E0. All the products satisfied the LB grade standards for bending strength, nail head pull-through force, and lateral nail resistance. However, product B did not meet the standard for the GP-REG grade, and products H and I did not meet the standard even with GP-REG grade. The thickness swelling of products A, B, C, F, and H did not meet the LB-REG grade standard, whereas products D and G had a relatively lower thickness swelling and exceeded the standard for internal bonding after boiling and bending strength under wet conditions, satisfying the HLB-MR grade.
In terms of structural bending strength, the six types of OSBs for walls exceeded the standards for bending strength and modulus of elasticity. All floor products satisfied the bending strength standards; however, all products, except product G, failed to meet the standards in terms of elastic modulus. From these results, it was determined that the water resistance performance of the seven OSB products did not meet the standards, making them unsuitable for structural use. Additionally, 10 types of products did not match the labeling grade, indicating that countermeasures were required.
To ensure the proper use of imported OSBs distributed in Korea as a domestic wooden house material, management plans for importers, along with continuous management and inspection, should be prepared in accordance with the Timber Usage Act in Korea. Simultaneously, efforts should be made to develop wood-based materials for structural use that can be produced domestically and can replace the imported OSB. Developing a domestic structural panel using domestic resources and revitalizing the timber industry will contribute to achieving the 2050 goal of carbon neutrality. Therefore, continuous research on the development of raw material manufacturing technology for the dissemination of Korean-style urban wooden houses should be conducted, and policies for this purpose should be supported.