1. INTRODUCTION
Based on the data from the “Wood Supply and Demand Record” of the Korea Forest Service, Korea’s self-sufficiency rate for wood was about 16% from 2015 to 2019, which is extremely low. Furthermore, the situation does not seem to be significantly improving for the time being because the supply and distribution of Korean domestic wood are more challenging compared to those of imported wood; moreover, domestic wood does not meet the industrial requirements in terms of quality and performance. By 2024, according to Article 19 of the “Act on the Sustainable Use of Wood,” > 50% of the total wood consumption should satisfy the requirement of “priority purchase of domestic wood and wood products.” Therefore, there is an urgent requirement to increase the use of domestic wood in Korea. However, larix (also known as larch) wood, which is commonly available in Korea, is difficult to use as a high-value wood product owing to its low quality (Han et al., 2013; Lee et al., 2012; Pang et al., 2017; Prabuningrum et al., 2020; Song and Kim, 2022).
Despite the increase in demand for deck products in the Korean domestic wood markets, most commercially available wood decks are prepared from imported wood. Domestic wood cannot be used in deck products primarily because it has poor durability for outdoor use and is difficult to treat with preservatives. However, tropical hardwoods are typically preferred because they can be used without preservative treatment owing to their high resistance to outdoor weather (Cahyono et al., 2020; Kim, 2016; Kim et al., 2010; Lee et al., 2005; Park et al., 2020a, 2020b). Although larix is a domestic wood that is abundantly available in Korea and has mechanical strength superior to those of other domestic woods, its performance is below the standard required for deck wood. Moreover, it is challenging to meet the performance criteria owing to the substantial distortion due to the shrinkage and expansion of the wood in response to weather changes, in addition to the challenges related to preservative injection (Cahyono et al., 2020; Lee, 2020; Pang et al., 2017). Most manufacturing technologies, according to an analysis of wood-related technologies based on statistics from patent data, are used to produce plywood and bonded wood to increase its durability, and synthetic wood for wood flooring. However, research focused on increasing the board strength and deformation resistance is still lacking.
Research is required to increase the mechanical strength of larix and expand its use, especially in Korea, where most wood used for industrial and daily purposes is imported. In general, hybrid technology containing hetero-materials with distinct properties is popular to increase the mechanical strength of as-prepared wood products and reduce the deformation and distortion caused by shrinkage and expansion (Choi et al., 2020; Choi et al., 2021; Kwon et al., 2015; Lee and Lee, 2014; Park and Jo, 2020; Park et al., 2009). The careful consideration of the chemical compatibility between the materials used to combine the hetero-materials in order to obtain a synergistic effect is necessary. In terms of the particle size and structure of the mixed materials, there should be no phase separation at the interfaces of hetero-particles, and the particles should be evenly dispersed. In addition to using reinforcement materials at the adhesive interface, polymeric adhesives are applied to the wood surfaces to bind wood boards. In this study, larix board samples were prepared by applying an adhesive to the surfaces of sliced larix boards to achieve chemical bonding. The adhesives used were polyurethane (PU), poly(vinyl acetate) (PVAc), phenol–resorcinol–formaldehyde (PRF), melamine–formaldehyde (MF), and urea–formaldehyde (UF) resins. The flexural moduli of the as-prepared board samples were analyzed. The potential application of larix board as a deck wood is closely related to the walk feeling. The comfort in walking depends on the elastic repulsion of the wood board used. The flexural modulus of the as-prepared samples provides fundamental data necessary to understand the elastic repulsion of wood.
2. MATERIALS and METHODS
Larix board was chosen as the wood sample in this study, and it was subjected to microwave drying to achieve a moisture level of 10%–12%. A microwave machine (MAMA-6H, PACEP, Yeongwol, Korea) was used for drying the wood samples, and the moisture content analysis was conducted according to the KS F2201 standard. The wood samples were cut to dimensions of 30 mm × 20 mm × 15 mm. The moisture content was obtained by measuring the weights of the samples before and after drying, and calculating the difference. All measurements were repeated at least ten times and the average value was reported as the moisture content.
A sliced wood board was cut and trimmed based on the size and shape standards of wood bending tests (Korean Standards Association, 2020). The boards were sliced into square bars with a cross-section of 30 mm × 30 mm, and a length of 450 mm in the fiber direction. Glulam-type laminated wood samples with 2- and 3-ply structures were fabricated from sliced boards with a thickness of 15 and 10 mm, respectively, to afford a total thickness of 30 mm.
Representative chemical types among the commercial adhesives were selected to bind the sliced wood boards (Table 1). The PU adhesive was prepared via a curing reaction after mixing the adhesive (MPU500, Okong, Incheon, Korea) and isocyanate-based curing agent (HH60, Okong). UF adhesive was prepared by mixing resin (UR-40, Taeyang Chemical, Incheon, Korea) and harder (NH4Cl, 20% of a resin). All adhesives were cured according to the conditions (time and temperature) recommended by the manufacturer. The reinforcement material used with the adhesive was a mesh sheet composed of basalt fiber (5 mm grid type, 220 g/m2, 0.7 mm thickness), which contains silica (45%–52%), alumina (12%–16%), iron oxide (6%–18%), and alkaline earth metal (10%–20%).
The flexural modulus was measured using a universal testing machine (UTM, KDMT-156–5, Kyung Do Precision, Siheung, Korea). All laminated wood samples were prepared and measured in 30 replications, and the results are presented as the average of the measured values. The wood samples prepared for the flexural modulus analysis are classified into five types, as shown in Fig. 1. A larix wood sample, cut to (w) 30 mm × (h) 30 mm × (l) 450 mm, was used as a reference sample [Std., Fig. 1(a)]. The cross-sectional structures of the 2- and 3- ply samples with reinforcement are shown in Fig. 1(b–e).
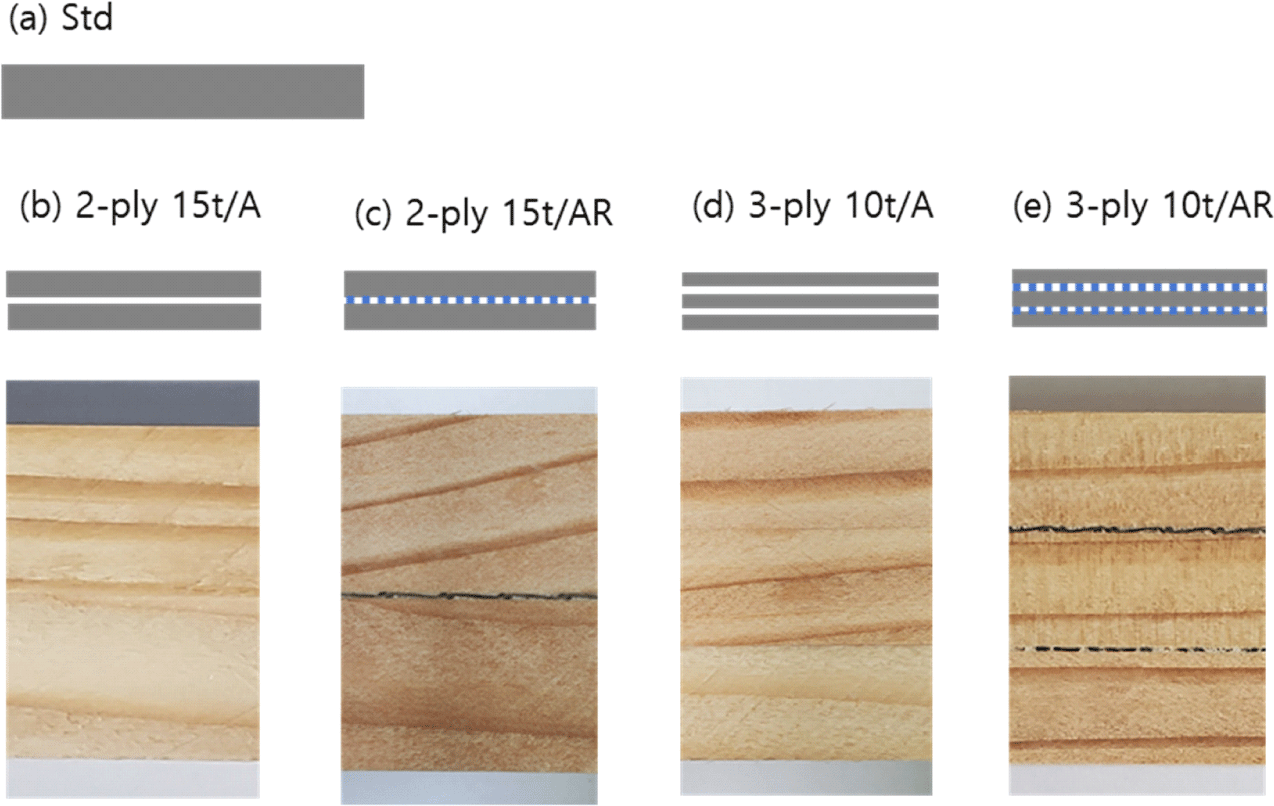
3. RESULTS and DISCUSSION
As shown in Fig. 1, the laminated wood samples were prepared by applying one of the five types of adhesives to sliced wood boards and binding them together. Wood lamination commonly involves the use of resin-based adhesives such as PU, PVAc, PRF, MF, and UF. These adhesives were applied to the sliced board surfaces and cured at room temperature (~25°C) to produce the laminated wood samples. The flexural moduli of the as-prepared samples were determined (Table 2). For each sample type, the results have a relatively large distribution of +/–10 N/mm2, which may have been caused by the differences in the number and size of knots distributed in the sliced wood boards. Even for the wood samples prepared under the same conditions, the differences in the tissue structure and knot characteristics of the individual wood slices significantly affect the mechanical properties of the laminated wood samples.
“A” and “AR” in the sample name indicate adhesive and adhesive with reinforcement, respectively. For a detailed explanation of the sample names, refer to the script of Fig. 1.
For all structures, the samples laminated with PU adhesive demonstrated higher flexural modulus than that of the 30-mm-thick reference sample (Std). The increase in flexural modulus was greater in the samples (15t/AR & 10t/AR each sample structure is shown in Fig. 1) prepared using both adhesive and reinforcing materials than in the samples prepared using only adhesives (15t/A & 10t/A). However, the samples prepared with PVAc, PRF, MF, and UF resin adhesives had flexural moduli equivalent to or lower than those of the corresponding reference samples (Std). This was confirmed by the structural analysis of fractured samples with different resin adhesives after measuring their flexural moduli. As shown in many fractured samples [(Fig. 2(a)], the separation of the laminated interface proceeded along with the fracture of the wood sample, caused by a shear force being generated at the binding interface, where interfacial failure occurred owing to differences in bending radii between the layers. Under these conditions, if the interfacial adhesive force of the laminated wood sample is lower than the shear force because of the force applied in the vertical direction, the fracture (delamination) of the interface proceeds before sample destruction. Therefore, the flexural modulus may be lower. This phenomenon often occurs when the interfacial interaction between the wood sample and the adhesive is weaker than the intramolecular interaction between the adhesive polymers. However, the delamination of the adhesive interface was not observed in the fracture cross-sections after measuring the flexural modulus of the wood samples laminated with PU.
The flexural modulus of the wood sample laminated using PU adhesive was significantly higher than that of other samples because the heterogeneous interfacial binding force between the sliced boards of the laminated sample and the adhesive is higher than the intramolecular binding force of the adhesive itself. The primary components of wood (cellulose and lignin) are natural polymers that contain many hydroxyl groups (–OH). The urethane groups (–NHCOO–) of the PU adhesive applied to the wood surface form hydrogen bonds with the –OH groups of cellulose or lignin, thereby forming strong hydrogen bonds between the wood surface and the adhesive interface. This strong bonding is considered the reason for the high flexural modulus of the laminated wood sample. Fig. 2(a) shows the fracture cross-section of a laminated wood sample prepared using PVAc resin adhesive and reinforcement. During the flexural tests, the laminated interfaces were easily separated (red arrows in the figure). Higher magnification images from an optical microscope [Fig. 2(a1) and (a2)] show that the adhesive was not densely filled between the sliced boards and the reinforcement, the adhesive layers were separately deposited around the surfaces of the board and reinforcement fibers, thus resulting in the separation of the laminated interfaces. However, Fig. 2(b), (b1), and (b2) show images of the wood sample laminated using urethane adhesive and reinforcement, where the adhesive was densely filled between the sliced boards and the reinforcement. The images in Fig. 2(c) and (c1), and Fig. 2(d) and (d1) show the interfacial condition of the laminated wood samples using urethane and urea resin adhesives, respectively. All of these laminated interfaces were very dense and strongly bonded.
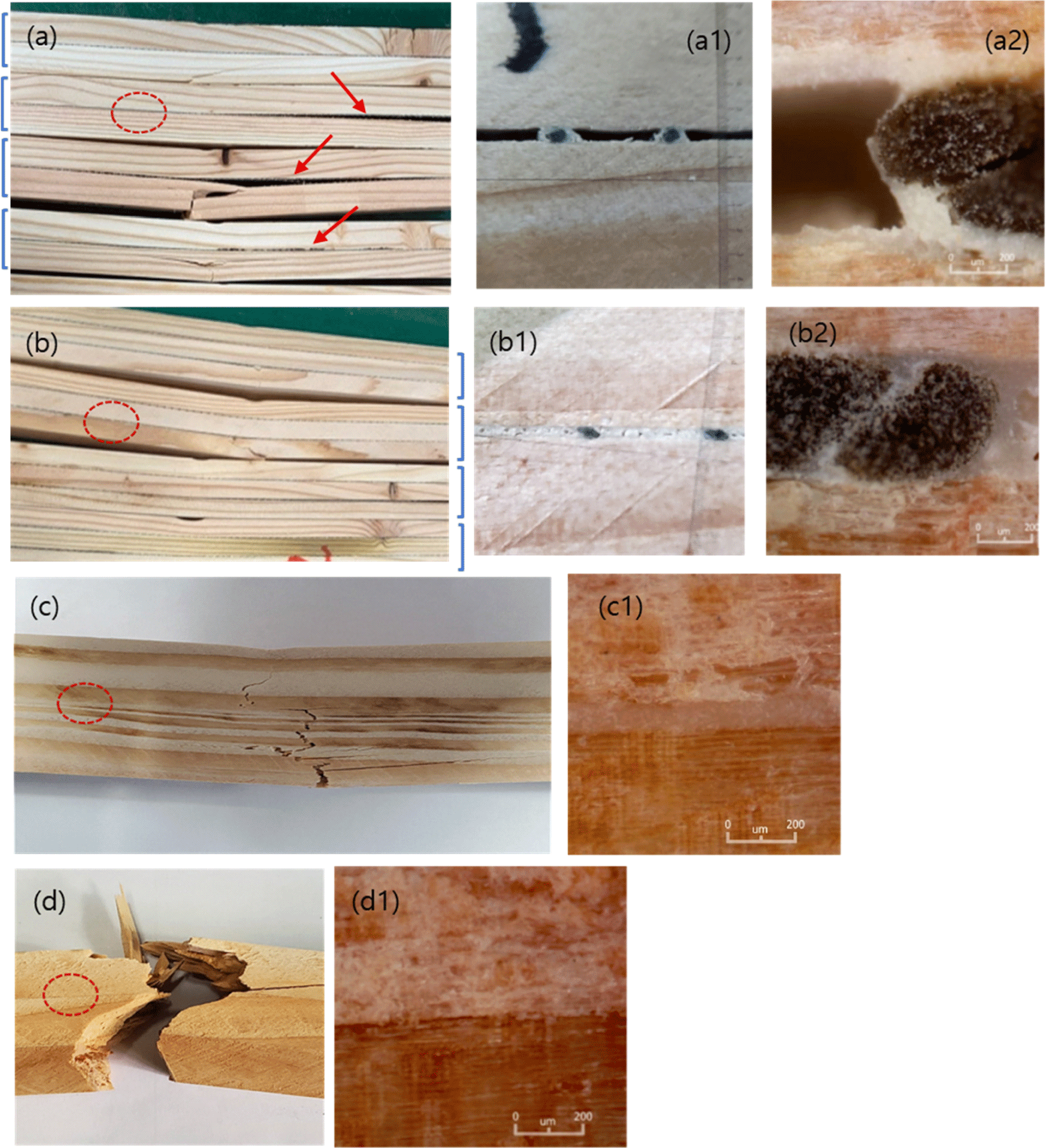
Fig. 3(a) shows the flexural modulus of the wood samples laminated using PU adhesive and cured at room temperature (~25°C) or 60°C. The curing density can be increased at higher temperatures, and this was validated by measuring the flexural modulus. The flexural modulus values of the wood samples cured at room temperature are presented in Table 2. As described above, the flexural modulus of the wood samples prepared using PU adhesive and cured at room temperature was higher than that of the reference sample (Std), regardless of whether reinforcement was added. Similar results were obtained for the wood samples prepared with PU adhesive and cured at 60°C. The wood samples in which PU adhesive and reinforcement were used and cured at room temperature demonstrated a higher modulus than the wood samples prepared using adhesive alone. When cured at 60°C, the 3-ply samples using the reinforcement showed a higher modulus.
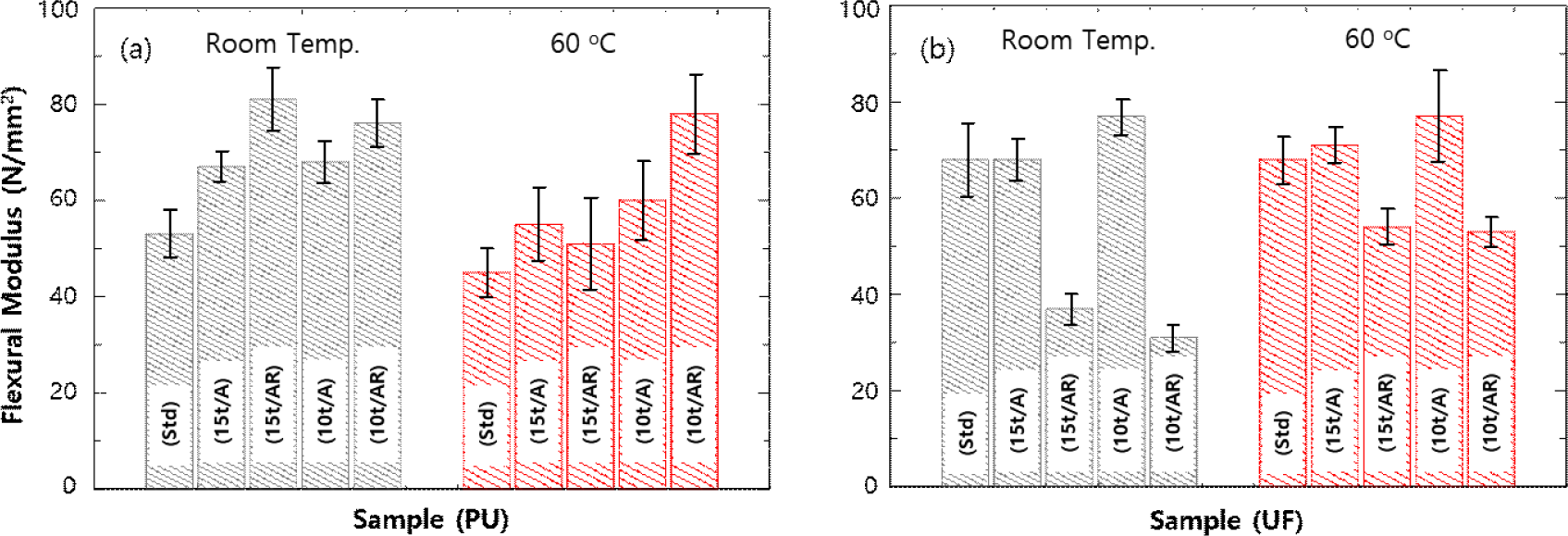
Fig. 3(b) shows the flexural modulus of wood samples laminated using UF adhesive at cured at room temperature (~25°C) or 60°C. The samples without reinforcement (15t/A & 10t/A) had the same or slightly higher modulus compared with Std when cured at room temperature; however, the flexural modulus was significantly lower for the samples with reinforcement. The results of the samples cured at 60°C are similar to those of the samples cured at room temperature (~25°C). However, the reduction in the modulus of the samples with the use of reinforcement was less severe than that of the samples cured at room temperature. The apparent decrease in the modulus caused by the addition of reinforcement is attributed to the relative weakening of the binding force. The wood sample laminated with UF adhesive and reinforcement was identified to have a structure similar to the cross-sectional images shown in Fig. 2(a). The laminated wood samples were very vulnerable to bending deformation due to the presence of many porous gaps at the cross-sectional interface. The urea groups of UF adhesive can also make hydrogen bonds with wood surface for the same reason as PU adhesive. However, the less dense and porous interfacial structure as shown in Fig. 2(a) seems to be because the adhesive resins are good adhesion to the polar surface of the wood as well as the reinforcing material, so that the adhesives are attracted to both the wood surfaces and the reinforcing materials, resulting in delamination of the interfaces. On the other hand, the improvement of the flexural modulus in the wood samples laminated with PU adhesive can be interpreted as the result of the PU adhesive resins good attracting with the wood surfaces, the reinforcing materials, and PU polymer chains, and well-balanced with these attractive interactions. These explanations could be supported by the densely-filled interfaces of Fig. 2(b) and (c). Urethane and urea groups of PU and UF adhesives are both polar functional groups, so hydrogen bonding with the lignin and cellulose components of wood is effective. In addition, these groups are capable of polar interaction with the inorganic oxide particles, which are the main components of the reinforcing material, so that the interfacial adhesion with the reinforcement is good.
Considering the overall results, if both adhesives and reinforcing materials are used to increase the flexural moduli of laminated wood samples, it is necessary to examine the comprehensive synergistic effects on the interfacial binding force between the materials used. The binding properties of the adhesive with the larix surface were significantly dependent on the chemistry of the adhesive used in this study. Even when a mesh-type reinforcement is composed of basalt fibers (which have SiO2 and Al2O3 as the main components) along with an adhesive, the flexural modulus is still significantly dependent on the interfacial binding forces between the adhesive and reinforcement/wood surfaces.
4. CONCLUSIONS
The characteristics of the adhesives were analyzed by measuring the flexural moduli of the laminated larix samples prepared using five types of adhesives. The wood samples prepared using PVAc, PRF, and MF demonstrated a much lower modulus than the pure wood reference sample. Thus, it is impossible to expect an increase in the flexural modulus for wood samples prepared using adhesive alone or in combination with the reinforcement. The delamination of the adhesive interfaces was mostly observed in the fractured cross-sections of the samples laminated with these adhesives. This implies that the adhesive interactions with other adhesive polymers are stronger than its interactions with the surfaces of the wood. However, in the fractured cross-sections of wood samples laminated with PU adhesive, there was no delamination of the adhesive interfaces, and the flexural modulus was significantly higher than that of the control. This demonstrates that PU provided effective binding between the wood surfaces.