1. INTRODUCTION
Cellulose is a natural polysaccharide that is composed of glucose units linked by β-1,4-glycosidic bonds. Glucose is the predominant constituent of lignocellulose biomass, and it is a potential and sustainable resource that can be used for the production of useful chemicals and fuels (Hwang et al., 2021; Iswanto et al., 2021; Zhang et al., 2016). Cellulose and lignocellulosic biomass are hydrolyzed and depolymerized into glucose under conditions of thermal reactions conducted in aqueous and organic solvents in the presence or absence of catalysts (Jung et al., 2022; Park et al., 2020; Ryu et al., 2016; Schulz et al., 2021). The formed glucose can be further converted to other products and chemicals (Girisuta et al., 2007; Kabyemela et al., 1997).
Hemicelluloses are the second most abundant polysaccharides present in lignocellulosic biomass, and it constitutes approximately 20%–35% of lignocellulosic biomass (Saha, 2003; Shin et al., 2015). Hemicelluloses are heterogeneous polysaccharides composed of pentoses such as xylose and arabinose, hexoses such as glucose, mannose, and galactose, and uronic acids such as glucuronic acid and 4-O-methyl galacturonic acid (Girio et al., 2010). Xylose, which is the basic unit of xylan and the second most abundant monosaccharide in hardwoods, is used for the production of value-added chemicals (Mamman et al., 2008; Shin, 2013).
Pretreatment processes for bioethanol production and biorefinery of lignocellulosic biomass have focused on effective solubilization and removal of hemicellulose while minimizing the degradation of xylose into inhibitors of enzymatic hydrolysis and fermentation (Fatriasari et al., 2020; Hendriks and Zeeman, 2009; Maulana et al., 2021; Zendrato et al., 2021). The solubilization and removal of hemicellulose promote the process of enzymatic hydrolysis by increasing the mean pore size of lignocellulosic biomass and the accessibility of enzymes to cellulose (Chandra et al., 2007; Han et al., 2020; Kim et al., 2011; Min et al., 2011).
Useful chemicals such as 5-hydroxymethylfurfural (5-HMF) and levulinic acid are formed under conditions of glucose conversion during the process of biorefining. 5-HMF is a potential building block that can be used to synthesize different types of polymers, pharmaceutical precursors, and organic intermediates (Asghari and Yoshida, 2006). Levulinic acid is a versatile building block that can be used to synthesize fuel additives and precursors of polymers and resins (Bozell et al., 2000). Furfural, the primary dehydration product of xylose, is a versatile derivative that has been used during the industrial production of plastic and pharmaceutical chemicals (Jang et al., 2015). The yields of these compounds vary depending on the type of raw material used, the operating temperature and time, the type of catalyst used, and the concentration of catalyst (Rackemann and Doherty, 2011; Takeuchi et al., 2008). The reactions associated with the conversion of glucose and xylose were investigated under various reaction conditions to improve the yields of the products. The reactions associated with the solubilization and removal of hemicellulose and those associated with the dehydration and conversion of hemicelluloses should be understood to realize the effective organosolv pretreatment method that can be used to treat lignocellulosic biomass (Kim et al., 2015a). Organosolv pretreatment has been considered to be effective for high lignin containing lignocellulosic biomass such as woods due to solubilization of lignin and breakdown of internal lignin and hemicellulose bonds (Holtzapple and Humphrey, 1984; Kim et al., 2015b).
Herein, we report the conversion characteristics of glucose and xylose. These compounds were used as the standards to study the conversion of lignocellulosic biomass. The effect of temperature and catalyst concentration on the process of organosolv pretreatment was studied using ethanol as the organic solvent with dilute sulfuric acid as the catalyst.
2. MATERIALS and METHODS
Glucose (G8270) and xylose (X1500, > 99%) were obtained from Sigma-Aldrich (Yongin, Korea). Ethanol (50%, v/v) was used as the organic solvent, and sulfuric acid [0.5%, 1.0%, and 2.0% (w/w)] was used as the catalyst. Ethanol was purchased from Samchun Chemical (Seoul, Korea).
Organosolv pretreatment was conducted in a reactor consisting of a vessel, an electric band heater, a magnetic drive equipped with a paddle-type impeller, and a control box (HR-8300, Hanwoul Engineering, Gunpo, Korea). The vessel was manufactured using stainless steel (SUS 316), and the capacity of the vessel was 1,000 mL. A Teflon gasket was used to maintain the inner pressure. A thermocouple and a pressure gauge were located inside the reactor, and these were used to measure the internal temperature of the vessel and the pressure generated during the pretreatment process, respectively. A Teflon impeller was placed inside the reactor for regular stirring. The control box was used to control the temperature of the vessel, the heating rate, and the stirring rate realized using the impeller.
The ratio of the standard material to the solvent was 1:100 (5 g:500 mL). Ethanol (50%, v/v) was used as the organic solvent, and sulfuric acid [0.5%, 1.0%, and 2.0% (w/w)] was used as the catalyst. The pretreatment method was performed with a consistent output of the electric band heater until the internal temperature reached the target temperature (120°C, 130°C, 140°C, 150°C, 160°C, 170°C, 180°C, 190°C, 200°C, 210°C, or 220°C). Once the target temperature was reached, the vessel was cooled in an ice chamber, and the temperature was brought down to room temperature.
Glucose, xylose, various degradation products (5-HMF, furfural, etc.), organic acids (levulinic acid, formic acid, etc.), and other constituents were identified and characterized following the NREL Laboratory Analytical Procedure (Sluiter et al., 2008a, 2008b). The liquid hydrolysate was filtered through a hydrophilic polytetrafluoroethylene syringe filter (pore size: 0.45 μm); (Advantec, Tokyo, Japan), following which the sample was analyzed using the high-performance liquid chromatography (HPLC) technique (HP 1100 series, Agilent Technologies, Santa Clara, CA, USA) at the National Instrumentation Center for Environmental Management (NICEM, Seoul, Korea). The HPLC system was equipped with an Aminex HPX-87H column (300 mm × 7.8 mm; ID × 9 μm, Bio-Rad Laboratories, Richmond, CA, USA), and the column temperature was maintained at 40°C during operation. Sulfuric acid (0.1 N) was used as the mobile phase, and the flow rate was maintained at 0.5 mL/min. The refractive index detector (RID) and diode array detector (DAD) were operated at 210 nm and 284 nm, respectively. RID was used for quantitative analysis, and DAD was used to confirm the presence or absence of organic acids and double-bond-containing compounds (C = O and C = C unit-containing molecules); (Sasaki et al., 2000). The peaks were identified by comparing the peak retention times, and the ultraviolet (UV) absorbance patterns were recorded for the samples and standard constituents. Calibration curves of the peaks were obtained using the standard compounds. The concentrations of the standards were varied, and these were used to determine the linear relationship between the peak area and concentration.
3. RESULTS and DISCUSSION
The organosolv pretreatment process for glucose was carried out in the temperature range of 120°C–220°C, depending on the sulfuric acid (catalyst) content [0.5%, 1.0%, and 2.0% (w/w)]. When the hydrothermal treatment process is conducted under acidic conditions, glucose is converted to 5-HMF, which is further converted to levulinic acid and formic acid under the same conditions (Kang et al., 2018). During the process, small amounts of biproducts (such as fructose) are formed under conditions of glucose isomerization. Levoglucosan (1,6-anhydro-β-D-glucopyranose), 1,6-anhydro-β-D-glucofuranose, isomaltose, and gentiobiose are also produced under conditions of glucose reversion reactions (Harris and Feather, 1973; Harris and Feather, 1975; Helm et al., 1989). The major products obtained under conditions of acid-catalyzed organosolv pretreatment during glucose conversion were 5-HMF, furfural, levulinic acid, and formic acid. The products were formed at all concentrations of sulfuric acid. The nature of the conversion profiles varied based on the reaction temperature and sulfuric acid concentration (Fig. 1).
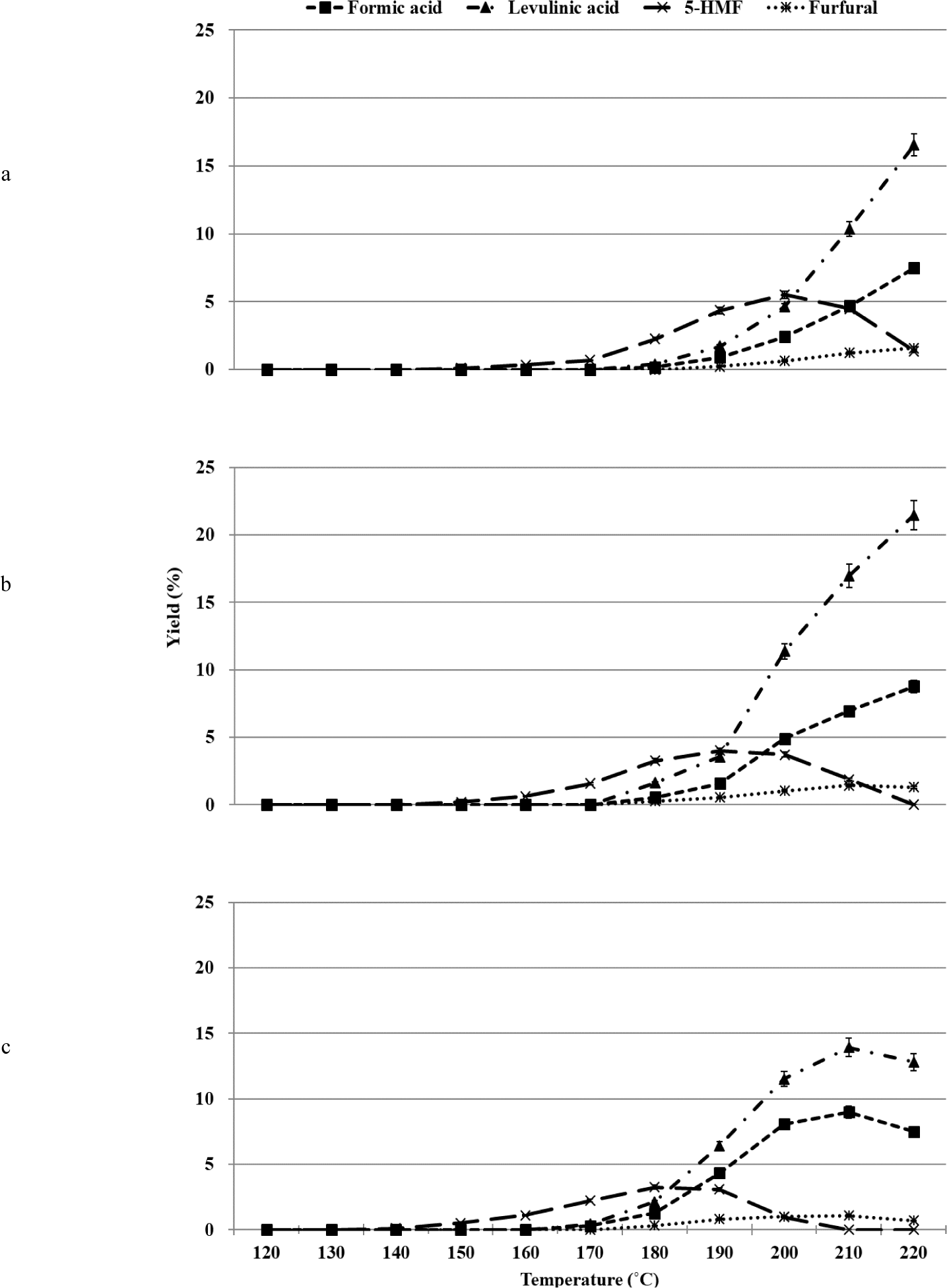
The dehydration of glucose resulted in the production of 5-HMF under conditions of elevated temperature during the organosolv pretreatment method. The produced 5-HMF was further degraded and converted into Levulinc acid and formic acid when hydrated (Fig. 1). The formation of 5-HMF was induced at 150°C when 0.5% and 1.0% of sulfuric acid were used for the reactions. The maximum yield was recorded at 200°C and 190°C, when 0.5% and 1.0% of sulfuric acid were used, respectively. And then, the yields decreased. When 2.0% of sulfuric acid was used as the catalyst, 5-HMF was formed at 140°C, and the maximum yield was recorded at 180°C. The complete decomposition of glucose was realized at 210°C. As the sulfuric acid concentration was increased from 0.5% to 2.0%, the formation of 5-HMF was induced. Complete decomposition of glucose was realized at low temperatures, and the maximum yield of 5-HMF decreased from 5.5% to 3.3%.
Under acidic or neutral conditions, 5-HMF is formed as the primary product during glucose conversion. Carboxylic acids (C2 to C5) are formed as the main products under alkaline conditions (Yin et al., 2011). The yield of 5-HMF varied with the reaction conditions such as temperature, residence time, type of acid used, concentration, and type of reaction medium. As the temperature and residence time increased, the yield of 5-HMF increased, reached a maximum value, and then decreased (Yin et al., 2011). It was also observed that the yield of 5-HMF decreased as the sulfuric acid concentration increased and the pH value decreased below 2.0 (Asghari and Yoshida, 2006; Girisuta et al., 2007). Hence, it can be inferred that the results reported herein agree well with the previously reported results.
It has been previously reported that the yield of 5-HMF produced from glucose was lower than the yield of 5-HMF produced from fructose under the same conditions. The percentage yield of 5-HMF was recorded to be 53% when fructose was the substrate, and the reaction was carried out in the presence of sulfuric acid (Antal et al., 1990). It is known that the rate of dehydration of fructose is higher than the rate of dehydration of glucose (Kuster, 1990). It has also been reported that when glucose is converted using sulfuric acid (0.1–1.0 M) in the temperature range of 140°C–200°C, the maximum yield of 5-HMF that can be obtained is 10.0%. The rate of conversion of 5-HMF to levulinic acid was significantly higher than the rate of conversion of glucose to 5-HMF (Girisuta et al., 2006, 2007). We observed that 5-HMF was obtained in significantly low yields (< 5.5%) when glucose was used as the substrate. As seen in the above two studies, fructose was not detected. Thus, it can be inferred that any fructose formed from glucose is rapidly converted into 5-HMF, which is then rapidly converted into levulinic acid and formic acid.
As shown in Fig. 1, as the sulfuric acid concentration increased from 0.5% to 2.0%, levulinic acid and formic acid were formed under conditions of low temperatures. The formation of levulinic acid and formic acid was initiated at 180°C when 0.5% and 1.0% of sulfuric acid were used, respectively. As the temperature increased to 220°C, the yield increased progressively. When 2.0% of sulfuric acid was used during the reactions, levulinic acid and formic acid were formed at 170°C. The maximum yields were recorded at 210°C. Beyond this temperature, the compounds decomposed.
Levulinic acid and formic acid were formed in an equimolar ratio under all conditions. These acids remained stable in the temperature range of 150°C–230°C and the acid concentration range of 3.5%–10% (w/w). Other processing conditions also influenced the yields of the compounds (Girisuta et al., 2007; Rackemann and Doherty, 2011). The formic acid to levulinic acid molar ratio considered by us was greater than 1.0. The yield of levulinic acid decreased at temperatures above 210°C and in the presence of 2% sulfuric acid. This indicated the occurrence of unknown reactions that promoted the conversion of levulinic acid. The results indicate that the reactions associated with the conversion of glucose under conditions of acid-catalyzed organosolv pretreatment in the presence of ethanol were different from the reactions associated with glucose conversion realized under acid-catalyzed conditions in an aqueous medium.
Analysis of literature reports reveals that researchers have plotted glucose concentration and yields of the products as a function of reaction time to study the process of glucose conversion. The experiments were conducted at a certain temperature and catalyst concentration. Herein, the changes in glucose concentration and the yields have been presented as a function of temperature. The process of glucose conversion was divided into three stages depending on the reaction temperature, and the temperature range of each stage was varied based on the sulfuric acid concentration (Fig. 2). Rapid conversion of glucose was observed in the first stage. The percentages of residual glucose were recorded to be 55.3%, 54.2%, and 52.4% when 0.5%, 1.0%, and 2.0% of sulfuric acid were used as the catalyst at 160°C, 150°C, and 150°C, respectively. The slow conversion of glucose was recorded in the second stage. The glucose percentages recorded when 0.5%, 1.0%, and 2.0% of sulfuric acid were used at 180°C, 170°C, and 170°C were 53.0%, 52.5%, and 49.4%, respectively. Interestingly, in this stage, only 1.7%–3.0% of glucose could be converted, and the extent of conversion depended on the sulfuric acid concentration. Rapid glucose conversion was again observed in the third stage, and almost complete glucose conversion was realized at 220°C.
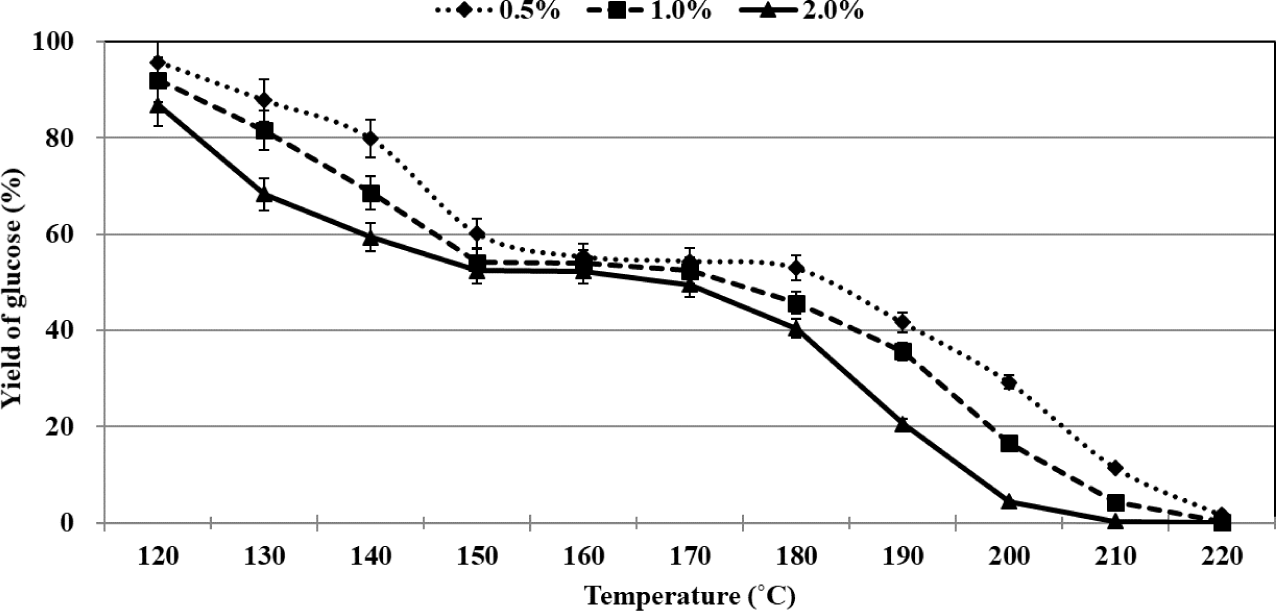
During the overall organosolv pretreatment method, the rate of glucose conversion was fastest at 2.0% sulfuric acid, where 13.2% of glucose was converted at 120°C, whereas most glucose did not remain at 210°C. As mentioned above, in the second stage, there was little difference in the remaining glucose at the concentrations of 0.5%, 1.0%, and 2.0% sulfuric acid. The second stage was allowed to proceed for 5–6 minutes according to the sulfuric acid concentration. It has been previously reported that the maximum extent of glucose conversion was achieved in the middle of the conversion process when the reactions were carried out in an aqueous medium using an acid catalyst (Ya’aini et al., 2013). However, we observed that the minimum extent of glucose conversion was achieved during the middle of thme organosolv pretreatment process. In other words, the glucose conversion profile recorded during the process of acid-catalyzed organosolv pretreatment that was conducted using ethanol as the organic solvent of choice was different from that recorded for the acid-catalyzed process conducted in an aqueous medium. Table 1 gives yield of levulinic acid from glucose using various types of conditions.
Substrate conc. | Solvent | Catalyst | Catalyst conc. | Temp. (°C) | Reaction/residence time | Levulinic acid Yield (wt%) | Reference |
---|---|---|---|---|---|---|---|
Glucose (1:100) | Ethanol (50% v/v) | H2SO4 | 1% | 220 | 22.5 | This work | |
Glucose (2 w.t%) | Water | H2SO4 | 0.5M | 180 | 15 min | 42 | Rackemann et al. (2014) |
Glucose (5 w.t%) | Water | H2SO4 | 5% | 170 | 1 h | 80.7 | Chun et al. (2006) |
Glucose (2 w.t%) | Water | H2SO4 | 1M | 140 | 2 h | 38 | Girisuta et al. (2006) |
The organosolv pretreatment method for xylose was carried out in the temperature range of 120°C–220°C under conditions of varying sulfuric acid (catalyst) content [0.5%, 1.0%, or 2.0% (w/w)]. Furfural was produced as the major product during xylose conversion, and the profile of xylose conversion and the yield of furfural varied depending on the reaction temperature and sulfuric acid concentration (Fig. 3). It has been previously reported that furfural is the primary product produced during the acid-catalyzed dehydration of xylose and xylan (Yemiş and Mazza, 2011). It was proposed that the dehydration of xylose to produce furfural involved the direct conversion of the C5 pyranose ring structure of xylose to the C5 furan ring structure of furfural. It has been hypothesized that the process does not involve the participation of the open-chain form of C5 sugar (Antal et al., 1991). This was also confirmed by conducting ab initio molecular dynamics simulation studies and quantum mechanical calculations (Nimlos et al., 2006; Qian et al., 2005).
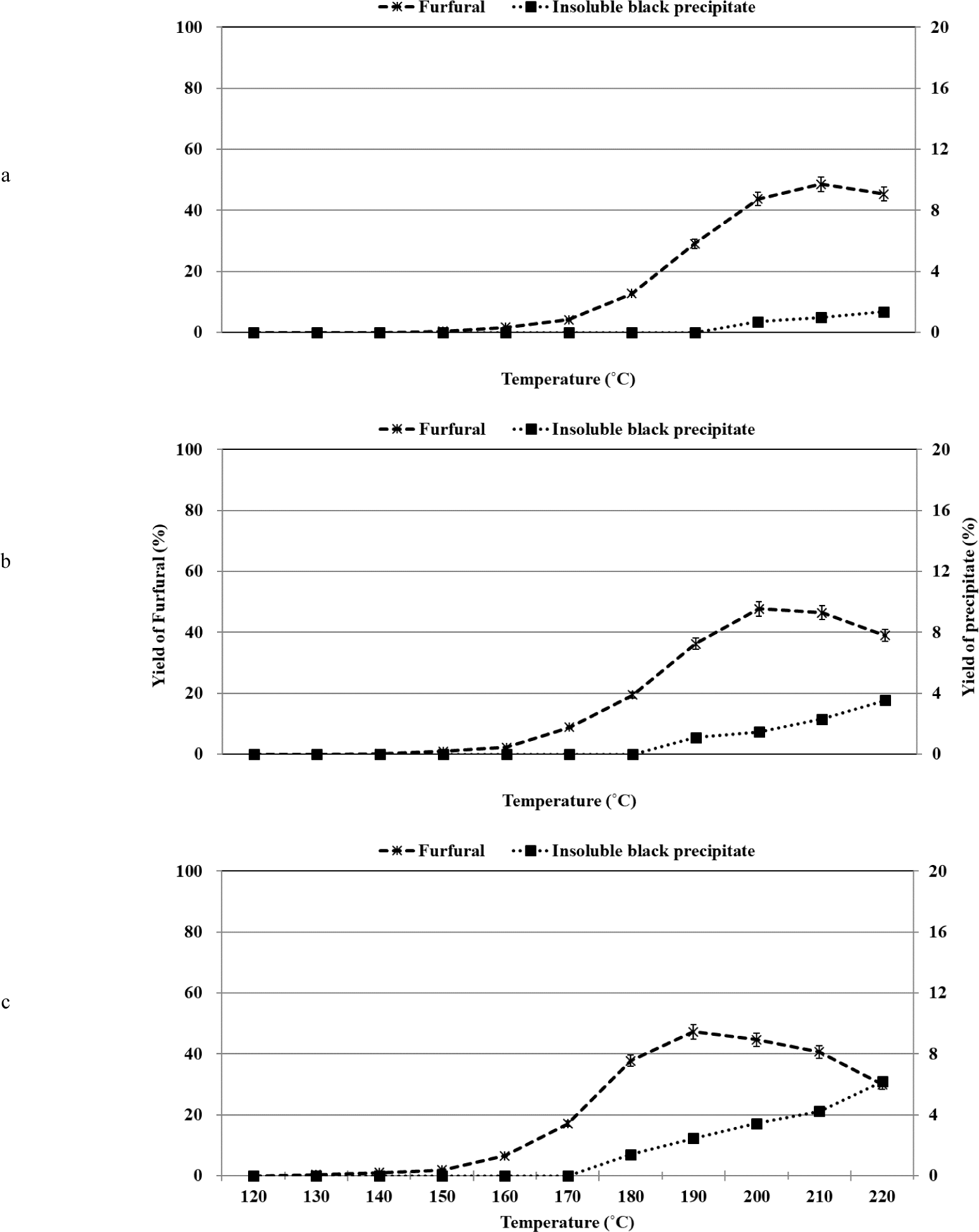
It has been previously reported that several organic acids, such as pyruvic acid, formic acid, glycolic acid, lactic acid, and acetic acid, were formed when the hydrothermal and acidic degradation of xylose was realized in the temperature range of 180°C–220°C (Fusaro et al., 2015). Formic acid, glycolic acid, lactic acid, and acetic acid were formed during the alkaline decomposition of xylose at 79°C (Oefner et al., 1992). In addition, under hydrothermal conditions of xylose with and without an acid catalyst at 250°C, lyxose and arabinose from xylose isomerization, furfural, and organic acids (formic acid and lactic acid) were identified using HPLC (Antal et al., 1991). However, in this study, at 190°C, only pyruvic acid was identified by HPLC with RID and DAD, but it is not plotted in Fig. 3 because its yield was less than 0.1%. However, products other than furfural and pyruvic acid could not be identified using the HPLC technique using RID and DAD. In the temperature range of 120°C–190°C, a large peak corresponding to an unidentified constituent was observed at a retention time that was similar to the retention time of the peak corresponding to the lactic acid standard. The UV absorption spectral profile of the unidentified compound was recorded, and it was observed that the profile differed from the profile recorded for the lactic acid standard. Thus, it was inferred that the unidentified compound was not lactic acid. It was also observed that as the temperature increased from 150°C to 220°C, the yield of the unidentified constituent decreased. This result was contrary to the results reported in a literature report where it has been mentioned that the yield of lactic acid increases under similar conditions (Oefner et al., 1992). The presence of a small peak at the retention time similar to the retention time of the peak representing the formic acid standard was also observed. Analysis of the UV absorption spectral profile recorded for the unidentified compound confirmed that the unidentified compound was not formic acid.
Various parameters such as the reaction temperature, residence time, solid-to-liquid ratio, initial pH, and type of acid catalyst used reportedly influence the yield of furfural (Agirrezabal-Telleria et al., 2011; Weingarten et al., 2010; Yemiş and Mazza, 2011). The yield of furfural was significantly influenced by changes in the temperature and initial pH. We observed that as the temperature increased during the process of organosolv pretreatment, furfural was formed from xylose under conditions of dehydration. The rate of formation of furfural was the maximum when 2.0% sulfuric acid was used for the reactions. When the sulfuric acid concentration was increased from 0.5% to 2.0%, the formation of furfural was induced at a low temperature. It was observed that the formation of furfural could be initiated at the initial temperature of the second stage associated with xylose conversion under all sulfuric acid concentrations.
The maximum furfural yield was recorded when 0.5%, 1.0%, and 2.0% of sulfuric acid were used at 210°C, 200°C, and 190°C, respectively. The yield decreased with a further increase in temperature. The maximum yield of furfural was recorded when 0.5% of sulfuric acid was used. When the sulfuric acid concentration was increased from 0.5% to 2.0%, the maximum yield decreased from 48.5% to 47.3%. It has been reported that the yield of furfural reaches the maximum value, following which the yield decreases with an increase in the temperature (Yemiş and Mazza, 2011). The loss in the furfural content observed during the acid-catalyzed conversion process can be attributed to the cross-polymerization reactions occurring between furfural and the intermediates formed during the conversion of xylose to furfural. The loss can also be attributed to the self-polymerization reactions of furfural (Zeitsch, 2000). It has also been reported that the production of insoluble humin-type polymers results in a loss in the furfural content (Wildschut et al., 2009). The solubilities of the polymerized products varied depending on the temperature and polarity of the medium (ethanol/water mass ratio). When 0.5%, 1.0%, and 2.0% of sulfuric acid were used, an insoluble black precipitate began to form at 200°C, 190°C, and 180°C, respectively. As the temperature and the sulfuric acid concentration increased, the content of the insoluble black precipitate increased. However, at higher temperatures, the decrease in furfural was greater than the formation of the insoluble black precipitate. This indicated the presence of soluble polymerized products in the mixture. When the organosolv pretreatment method was used to treat furfural at 220°C, 29.7% of the total furfural content was decomposed, and this result supported the assumption that self-polymerization of furfural occurs under these reaction conditions. The results suggest that the loss of furfural was associated with the formation of an insoluble black precipitate. The yield of furfural decreased at high temperatures, and this could be attributed to the occurrence of various polymerization reactions.
The yields of residual xylose and furfural recorded during the organosolv pretreatment method were plotted as functions of temperature. The process of conversion of xylose could be divided into three stages (similar to the process of conversion of glucose). The temperature range of each stage varied based on the sulfuric acid concentration (Fig. 4). Rapid conversion of xylose was realized in the first stage, and the percentages of residual xylose were recorded to be 61.1%, 62.0%, and 60.3% when 0.5%, 1.0%, and 2.0% of sulfuric acid were used as the catalyst at 150°C, 140°C, and 130°C, respectively. In the second stage, the xylose that remained was very slowly converted, and the xylose contents in 0.5%, 1.0%, and 2.0% sulfuric acid at 160°C, 160°C, and 150°C were 59.2%, 57.7%, and 55.9%, respectively. Interestingly, in this stage, only 1.9%–4.4% of the xylose was converted, and the extent of conversion was influenced by the sulfuric acid concentration. It has been previously reported that the maximum extent of xylose conversion was realized during the middle of the process when xylose conversion was carried out in an aqueous medium with an acid catalyst (Dias et al., 2005). We observed that the extent of xylose conversion was the minimum in the middle of the process. The results indicated that the xylose conversion profile recorded during the acid-catalyzed organosolv pretreatment process using ethanol as the organic solvent was significantly different from the profile recorded during the acid-catalyzed process conducted in an aqueous medium. Rapid conversion of xylose was again recorded during the third stage, and 0.5%, 1.0%, and 2.0% of sulfuric acid were used as the catalyst at 210°C, 200°C, and 200°C, respectively. Xylose was almost completely converted, but at 220°C, complete decomposition of xylose did not occur.
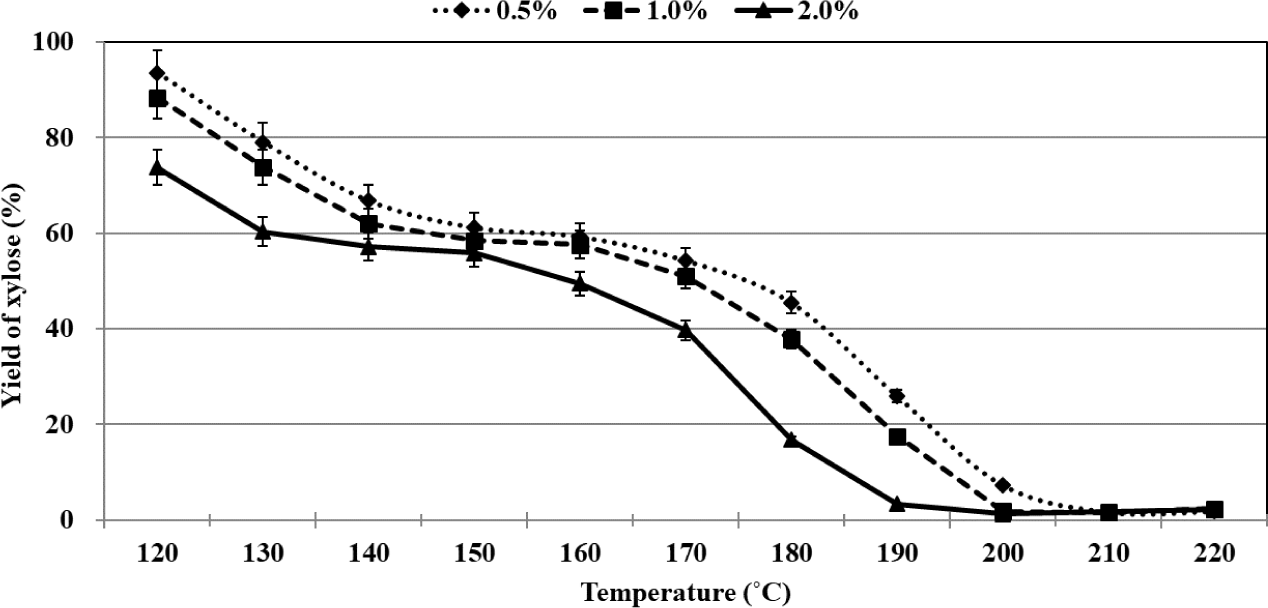
The maximum rate of xylose conversion was recorded when 2.0% of sulfuric acid was used during the organosolv pretreatment method. At 120°C, 6.5%, 11.6%, and 26.3% of xylose could be converted to products using 0.5%, 1.0%, and 2.0% of sulfuric acid, respectively. This suggests that a small amount of xylose is converted to the products at relatively high concentrations of sulfuric acid when the temperature is below 120°C. The process of xylose conversion in the second stage was similar to the process of glucose conversion in the second stage. It was observed that the temperature at which xylose conversion was realized was lower than the temperature at which glucose conversion was realized. At the end of the third stage, the percentage of residual xylose was in the range of 1.8%–2.4%. It is noteworthy that the complete decomposition of residual xylose was not observed under these conditions. Some researchers have hypothesized that the interconversion between xylose and xylofuranose occurred via the mutarotation of xylose. It has also been reported that xylofuranose was stable under acid-catalyzed hydrothermal conditions at 250°C. The presence of residual xylose was detected under conditions of prolonged residence time (Antal et al., 1991). We proposed that residual xylose existed in the form of xylofuranose at temperatures above 200°C during the organosolv pretreatment process. Table 2 gives yield of furfural from xylose using various types of conditions.
Substrate conc. | Solvent | Catalyst | Catalyst conc. | Temp. (°C) | Reaction/residence time | Furfural yield (wt%) | Reference |
---|---|---|---|---|---|---|---|
Xylose (1:100) | Ethanol (50% v/v) | H2SO4 | 0.5% | 210 | 48.5 | This work | |
Xylose (80 g/L) | o-nitrotoluene (75% v/v) | Formic acid | 20 g/L | 190 | 1 h 15 min | 74 | Yang et al. (2013) |
Xylose (1:6) | Water | - | - | 220 | 50 min | 50 | Jing and Lü (2007) |
Xylose (1 w.t%) | Water | CrCl3 | 6mM | 145 | ∼80 min | 17 | Choudhary et al. (2012) |
4. CONCLUSIONS
The conversion characteristics of glucose under conditions of acid-catalyzed organosolv pretreatment method were investigated. The glucose conversion process can be divided into three stages, and a slow rate of glucose decomposition was recorded in the second stage. The identification and confirmation of furfural, 5-HMF and the formation of ethyl levulinate through the esterification of levulinic acid with ethanol were the most representative features during organosolv pretreatment. The hydrolysis and conversion characteristics of cellulose standards can be investigated, and the effects exerted on the physicochemical properties during the progress of the organosolv pretreatment method can be studied based on the results presented herein. These results reveal that lignocellulosic biomass can be effectively utilized when subjected to conditions of the organosolv pretreatment process.
The characteristic properties of the hydrolysis and conversion reactions for xylose were recorded under conditions of the acid-catalyzed organosolv pretreatment method. The obtained results can potentially help understand the characteristic conversions of hemicellulose in lignocellulosic biomass for biorefinery. Furfural, a major product of xylose, was obtained in high yields. This indicated that under optimal production and separation conditions, a large amount of furfural could be produced from lignocellulosic biomass, and the produced furfural can find its application in industries. Furthermore, to utilize xylose hydrolyzed in liquid hydrolysate, its influence on the inhibition of enzymatic hydrolysis and fermentation by furfural and the effective removal of furfural should be evaluated.
In conclusion, on the basis of the conversion characteristics of glucose and xylose, which is major components in lignocellulosic biomass, evaluation of those influences on physicochemical properties of lignocellulose biomass during organosolv pretreatment is needed in order to overcome the lignocellulosic biomass recalcitrance.