1. INTRODUCTION
Pleasant and healthy indoor air quality is a very important environmental factor for modern-day people who spend more than 80% of their daily lives indoors.
However, various air pollutants generated from interior construction materials significantly affect the human body as a result of the lack of ventilation from improved airtightness and insulation of the construction materials used to save energy, and the extent of damage caused by indoor pollutants is considered to be more than 10 times that of the outdoors (Lee et al., 2007). Finishing materials, paint, and adhesives for interior construction are known to be the sources of such indoor pollutants. Particularly, formaldehyde (HCHO) and volatile organic compounds (VOCs) are emerging as a serious social issue as they threaten public health through the sick house syndrome and such by deteriorating indoor air quality (Ingrosso, 2002).
As a material that has traditionally been used in a variety of commercial distributions and manufacturing processes, HCHO is widely used in construction materials, such as phenols, acetate insulations, plywood, fibers, and furniture adhesives, which release HCHO gas indoors (Oh, 2014a). Formaldehyde not only irritates the eyes, nose, and neck depending on the degree of exposure but also imposes a fatal health risk that directly affects the lungs and leads to death in severe cases (Arts et al., 2006; Casset et al., 2006; Jang et al., 2017).
To remove HCHO, Lee and Kim (2010a) investigated the adsorption of HCHO by charcoal, and Oh (2014a) investigated the deodorization rate of HCHO on particleboards made of oak wood.
While HCHO released indoors can be reduced through physical, chemical, or biomechanical methods, adsorption is one of the physical methods that is typically employed. In the adsorption method, HCHO can be removed using the adsorption mechanism in which a material is adsorbed between the pores of an adsorbent as the material passes through, and the method is popular because of low equipment cost and easy maintenance. Adsorbents, including activated carbon, zeolite, silica gel, and white clay, should be selected based on the purpose of the application, among which activated carbon is the most widely used (Konetic, 2019). The factors affecting the adsorption performance of carbon materials include the type and odor of chemical functional groups, pore characteristics, and polarity (Tanada et al., 1999). Among them, charcoal has an excellent porous wood structure but is influenced by temperature and water content during the manufacturing process, and its scope of application is limited compared to other advanced carbon materials since the physical properties vary significantly depending on manufacturers’ skill level, which may result in distortions and cracks. Woodceramics, a porous carbon material, was developed to compensate for these shortcomings. Woodceramics is a novel porous carbon material prepared by impregnating wood or woody materials with a thermosetting resin and carbonizing them at high temperature in a vacuum state. Since Okabe and Saito first developed and named this material, fundamental research has been conducted on various manufacturing methods and applications (Hwang and Oh, 2020a, 2020b, 2021; Hwang et al., 2021; Oh, 2014b; Oh and Hwang, 2009; Oh et al., 2014; Okabe, 1996). Also, the physical properties of woodceramics vary depending on manufacturing conditions, such as the type and mixing ratio of raw materials.
Charcoal, one of the materials used in this study, is an easily available, eco-friendly carbon material that contains about 80% to 90% of carbon depending on the manufacturing method. It is also a complex carbonaceous polymer containing oxygen, hydrogen, and ash with an charcoal specific gravity of 0.6 to 0.9 and is alkaline at pH 8 to 9. Additionally, since charcoal is excellent in adsorption given its porous structure and large specific surface area of about 100 to 300 m2 per 1 g of weight, it has been used for various purposes such as air purification, deodorization, and poisonous gas prevention, making it an important subject in a number of recent studies on eco-friendly materials (Ju et al., 2020; Lee et al., 2020; Park et al., 2012, 2013; Seo and Lee, 2010b).
As a type of light, far-infrared rays are longer in wavelength than visible rays and shorter than microwaves. The effects of far-infrared rays on the human body include elevated subcutaneous temperature, enlarged microvessels, increased blood circulation, enhanced metabolism between blood and body tissues, reduced blood disorders, and increased tissue regeneration. It is also known to suppress abnormal stimulation of sensory nerves and moderate the function of autonomic nerves (Lee, 2005). The demand has increased due to the positive impact on the human body, and technologies using far-infrared radiation are also being developed for heating devices and other daily necessities.
In this study, ceramics were prepared by adding charcoal, a porous material, to rice husk, an agricultural by-product, and sawdust generated during the sawing process and impregnating resin at different mixing ratios. Then, the HCHO deodorization effect and the far-infrared emission characteristics were evaluated to review the application potential as an interior construction material.
2. MATERIALS and METHODS
Sawdust, which had been produced in the sawing process of Larix kaempferi C., was purchased from a commercial sawmill, and rice husk was purchased from a rice mill (Jeonju, Korea), shade-dried, and ground with a grinder (Hanshin, J-NCM, Ansan, Korea) to increase adhesion during the preparation of boards. The particle size of the sawdust and rice husk was sorted in 18 mesh, and the moisture content was adjusted to 6% or less. Oak charcoal was purchased in the size of 100 mesh from Geumhan Farm (Imsil, Korea).
In addition, powdered phenol resin (KNB-100PL, Kolon Chemicals, Seoul, Korea) was used to prepare boards, and liquid phenol resin (KPD-L777, Kolon Chemicals) was used for impregnation to prepare ceramics. The characteristics of the resins are summarized in Table 1.
To prepare boards, the phenol resin powder was sufficiently mixed with uniformly selected sawdust, rice husk, and charcoal, and the mixture was placed in a square stainless mold on a heat plate of a hot press (Daeyang Machinery, DYMSP-001-026, Bucheon, Korea) and was pressed into 260 mm × 260 mm × 11 mm boards while maintaining the height at the top of the samples constant. As the conditions for preparing boards, the resin content and density were fixed at 10% and 0.6 g/cm3, respectively, and four types of boards were prepared by varying the mixing ratio between sawdust, rice husk, and ash to 50:35:5, 50:30:10, 50:25:15, and 50:20:20. During this stage, the hot press temperature was maintained at 170°C, the applied pressure was 40 kgf/cm2 → 30 kgf/cm2 → 20 kgf/cm2 (three-stage press), and the press time was 9 minutes → 2 minutes → 1 minute (three-stage press time). A thickness bar was used to keep the thickness of the boards constant during the hot press process, and Teflon plates were used to prevent the top and bottom of the boards from adhering to the heat plates due to heat.
The prepared boards were cut to a thickness of 11 mm and a cross-sectional size of 120 mm × 120 mm, and their density was calculated. In order to keep the test conditions constant, samples with a density of ± 0.03 g/cm3 were selected. The prepared samples were placed in an impregnation tank (inner diameter Φ31 cm) containing the liquid phenol resin and were subjected to decompression (76 cmHg) and ultrasonic treatment (frequency: 28 kHz, output power: 564 W) simultaneously for 20 minutes, followed by a 20-minute rest at the atmospheric pressure. The impregnation rate was adjusted by changing the interval time. After impregnation, the samples were shade-dried for 8 hours and were placed in a drier again to be dried and cured at 60? for 8 hours and 130? for 8 hours consecutively.
Ceramics were prepared using the impregnated boards with a resin impregnation rate of 40 ± 2% and mixing ratios of sawdust, rice husk, and charcoal of 50:35:5, 50:30:10, 50:25:15, and 50:20:20 in a vacuum carbonization kiln (KOVAC KSF-200V, Korea Vacuum, Daegu, Korea) at a carbonization temperature of 800?. During this process, the temperature was raised by 4?/min from room temperature to the set temperature, which was maintained for 2 hours before being cooled down by circulating cooling water around the carbonization kiln.
The samples prepared with sawdust, rice husk, and charcoal at various mixing ratios were cut to 40 mm × 40 mm and were sealed in a 5 L reactor. The test gas was injected at an initial concentration of 20 μmol/mol, and the concentration of the test gas was measured at the start and after 30 minutes, 60 minutes, 90 minutes, and 120 minutes using gas detection tubes. The temperature and humidity during the test were maintained at 23°C and 50%, respectively. A separate test was conducted without any sample to measure the blank concentration. Deodorization rate of the test gas for each time period was calculated by the following equation (1).
where DR is the deodorization rate, CB is the blank concentration, and CS is the sample concentration.
To investigate the far-infrared emission characteristics of the ceramics, samples were prepared as a testing material with a size of 30 × 30 × 2 mm, and far-infrared emissivity was measured with an FT-IR spectrometer over the range of 5–20 μm at 40°C according to the standard method (KICM-FIR-1005) provided by the Korea Conformity Laboratories.
3. RESULTS and DISCUSSION
Table 2 shows the results of measuring the HCHO deodorization rate of the boards prepared with sawdust, rice husk, and charcoal at various mixing ratios with the board density fixed at 0.6 g/cm3. Overall, the deodorization rate was found to increase as the running time increased. The deodorization rate also slightly increased from 80% to 81% and 84% as the charcoal ratio increased from 5% to 10% and 20%, respectively. Oh (2014a) reported that the deodorization rate of particle boards prepared at a density of 0.6 g/cm3 using oak wood was 81.9%, similar to the experimental result of this study. However, the deodorization rate of the boards prepared with sawdust, rice husk, and charcoal in this study was at least 70% after 30 minutes, which was higher than that of the boards made of oak wood at 55.7% and demonstrated a superior initial deodorization effect. It is believed that the addition of charcoal powder increases the surface area given the same weight, resulting in effective initial deodorization performance.
Table 3 provides the results of measuring the HCHO deodorization rate of the ceramics prepared with sawdust, rice husk, and charcoal at various mixing ratios with the board density of 0.6 g/cm3, resin impregnation rate of 40 ± 2%, and carbonization temperature of 800°C. The deodorization rate tended to increase from 85% to 88% and 89% as the charcoal ratio increased from 5% to 15% and 20%. It is believed that the surface area increases with the addition of charcoal powder, which improves deodorization performance. Also, all of the samples demonstrated a very high initial removal rate as more than 80% was removed after 30 minutes.
When comparing the deodorization effect of the boards and ceramics at each mixing ratio, the ceramics were overall 5% or higher in deodorization effect than the boards prepared at the same mixing ratios. Generally, adsorption performance is determined by the surface area, and the specific surface area and pore volume of wood or woody materials are increased by the carbonization process (Lee and Kim, 2011). Thus, it is believed that the ceramics that have undergone the carbonization process has an increased surface area and is superior in deodorization effect than the mixed boards. Also, since the deodorization effect is overall measured to be 80%–90% after 120 minutes, it is deemed feasible to use the boards and ceramics prepared in this experiment for deodorization.
Fig. 1 shows the far-infrared emissivity and emission power of the boards prepared at different mixing ratios of rice husk and charcoal with the board density fixed at 0.6 g/cm3. Far-infrared emissivity and emission power tended to increase with the decreasing charcoal ratio and increasing rice husk ratio; 0.928 and 374 W/m2 at the rice husk and charcoal ratio of 20:20, 0.925 and 373 W/m2 at 25:15, and 0.933 and 0.376 W/m2 at 35:5, respectively.
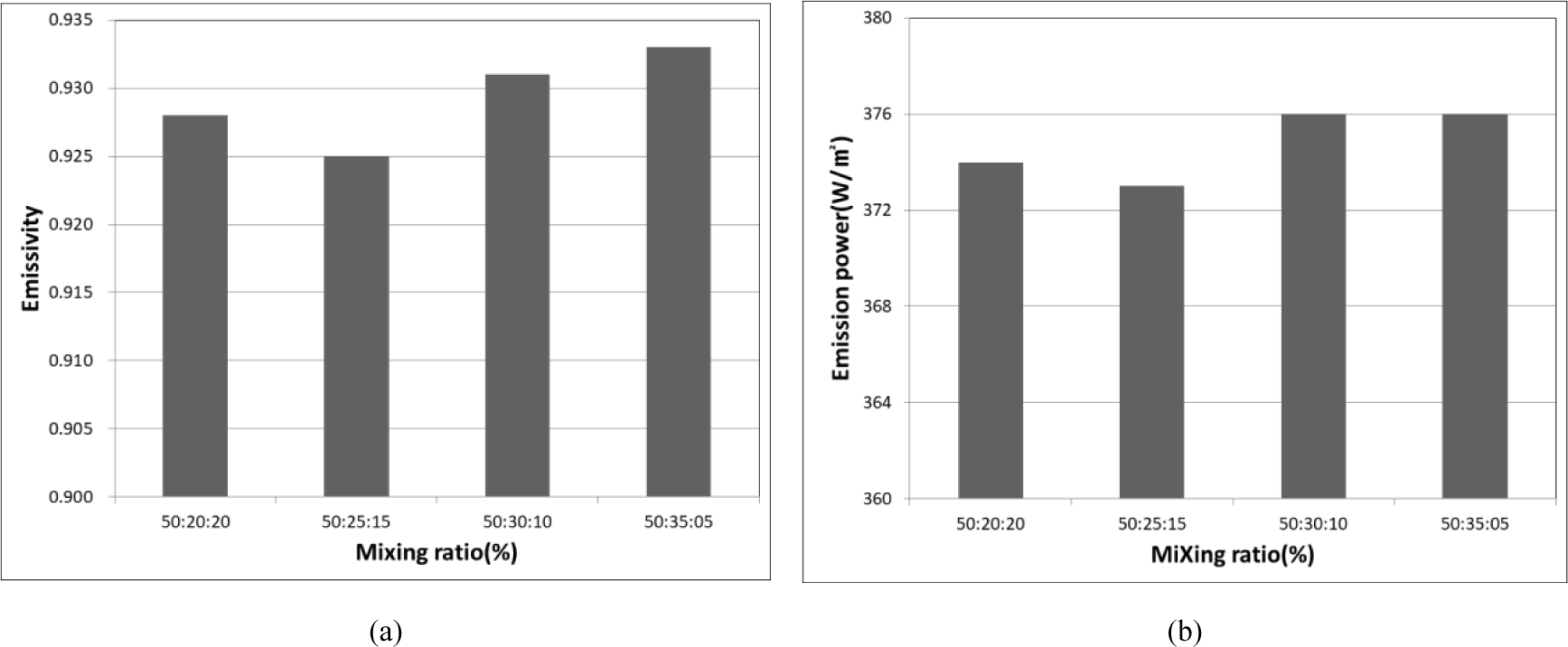
These far-infrared emissivity values were higher than that of silica sand (0.60 to 0.80), quartz-porphyry (0.90), and SiO2 (0.83) and were similar to that of charcoal (0.93), graphite (0.93), and ceramic coating plates (0.924; KFIA, 2000). Particularly, the values were higher than the emissivity value of 0.80 of the woodceramics carbonized at 800°C as an MDF material by Okabe (1996) and that of the woodceramics prepared with thinned logs by Oh and Byeon (2006). The values were also higher than the far-infrared emissivity value of 0.923 of the ceramics prepared by Oh (2016) with sawdust and rick husk and measured at the same impregnation rate and carbonization temperature as in this study. Lee and kim (2010) reported that the far-infrared emissivity of commercially available domestic charcoal was 0.89 and 0.87 with traditionally manufactured black coal and white coal, respectively. In this case, it is thought that the addition of charcoal affected far-infrared emissivity. Additionally, the measured values of the ceramics prepared by Hwang (2011) with mandarin peels and sawdust exhibited a similar tendency.
4. CONCLUSIONS
In this study, charcoal, a porous material, was added to rick husk, an agricultural by-product, and sawdust generated during the sawing process to prepare boards and ceramics at different mixing ratios, and the HCHO deodorization performance and far-infrared emission characteristics were measured.
The deodorization performance of the boards and ceramics prepared with sawdust, rice husk, and charcoal was found to improve as the amount of added charcoal increased. Also, the ceramics exhibited a higher deodorization rate by 5% or more than the boards prepared at the same mixing ratios. This is attributed to the increased specific surface area and pore volume through carbonization, improving the deodorization effect. Since the deodorization effect of the boards and ceramics was measured to be 80%–90%, they are deemed suitable to be used for deodorization purposes.
While far-infrared emissivity and emission power tended to increase as the rice husk ratio increased, the differences were minimal. Also, the far-infrared emissivity of the ceramics prepared in this experiment was similar to that of charcoal (0.93), graphite (0.93), and ceramic coating plates (0.924), demonstrating sufficient applicability.
Additional experiments on the specific surface area are needed to understand the effect of material mixing ratios on the pore structure.