1. INTRODUCTION
Korea depends on imports for 83% of its demand for wood, and accounts for the majority of exports of wood products by reprocessing and exporting imported raw materials. Contributions to global forest protection have prompted the enactment of international laws and timber regulations such as the Lacey Act in the US, the European Union Timber Regulation and, more recently, the Australian Illegal Logging Prohibition Act (Koch et al., 2015). In order to protect the domestic timber industry and actively participate in international efforts, the “Act on The Sustainable Use of Timbers” was amended on March 21, 2017, and enforced on October 1, 2018, so that only legally logged wood can be handled. Items subject to import declaration under Article 18-3 of the “Act on The Sustainable Use of Timbers” include raw timber, sawn timber, preserved timber, fire-retardant wood, laminated wood, plywood, and wood pellets. In addition, wood products are considered culturally valuable to create economic value as cultural products (Han et al., 2021). As for wood used for producing plywood, the use of domestic deciduous larches, which reached the harvesting age, began in earnest due to difficulties in supply and demand owing to the rising import prices and the outflow of foreign currency due to the imports. The Korea Forest Service has been promoting administrative support for the supply of domestic resources, such as announcing the standards for plywood production using domestic wood and designating a plywood production complex in December 2004 (Korea Forest Service, 2005). Plywood is being supplied for construction and civil engineering because it has strong durability. According to the import status of each major item by the Korea Forest Service, plywood imports from Indonesia in 2021 (January-June) were 247,730 m3, signifying an increase of 1.3% compared to the same period in the previous year (Korea Forest Service, 2021).
In general, plywood is a wide panel made by laminating and bonding an odd number of veneers such that the wood grain direction of the veneers is perpendicular to each other. All the layers are veneers but are sometimes made with lumber or particleboard as a core. Plywood is used in various ways, such as for formwork, as interior and exterior materials for construction, and for making furniture. In the early 1990s, Korea's plywood industry faced an unstable supply-and-demand situation for tropical wood raw timber, exacerbating the difficulty in supply and demand for raw materials. Hence, mixed softwood and hardwood plywood was used. In addition, research on ways to improve the use and development of domestic needleleaf trees has been conducted, and anatomical studies are also being conducted on evaluating their suitability for making pulp and paper materials (Marbun et al., 2019; Kim et al., 2020). For domestic and imported wood that are difficult to distinguish with the naked eye, DNA analysis technique, a new wood species identification method, is conducted simultaneously to compliment wood anatomical analysis. This is because a standardized DNA extraction method needs to be established based on the various processing types of wood and the elapsed period of wood according to the distribution process. It is difficult to identify the species of processed imported wood with the naked eye, and DNA analysis is more useful because it enables the species-level identification of samples compared to wood anatomical techniques, which enables only genus-level identification (Jang et al., 2014). Therefore, for wood products that are difficult to identify via microscopy, DNA analysis is used. The prominent characteristics of plywood manufactured using softwood and hardwoods are the distribution of knots and its influence on the strength of immature wood, the different cambiums by region, estimation of planting and harvesting time, and the relatively low production yield (Jin, 1994; Park et al., 2015; Yoo et al., 2021). A study in 1999 examined the possibility of manufacturing plywood using domestic softwood Larch and using it for constructing wooden structures, with the aim of promoting industrialization by improving the added value of the domestic wood industry (Lee et al., 2018). In the plywood manufacturing process, adhesive performance is a major factor that influences the quality of the plywood. In addition to the filler of the adhesive for plywood, the adhesive strength of the plywood is not only affected by the resin content of the surface but also largely depends on the penetration of the adhesive into the wood (Ko and Roh, 2015; Roh and Kim, 2018). Adhesive penetration into the wood tissue is in the order of ray cells, tracheid, and vessels in softwoods, and in the order of pore, ray cells, and fiber in hardwoods. The species used to make plywood are Katsura, Beech, Cypress, Zelkova, Maple, Chestnut, Cherry, Cedar, Pine, Abies, Oak, Walnut, Machilus, Sawara cypress, Apitong, Ash, Ebony, Mahogany, Padouk, Larch, Red lauan, Teak, etc. (Kim, 2008). Korean Pine trees are commonly used not only to manufacture plywood but also to extract their components (Min et al., 2019).
Koch (2015) stated that wood identification is very important for consumer protection as lower grade alternative wood is being imported at a noticeably increasing rate. Also, the necessity of anatomical analysis of wood to identify major species was raised in France considering that the supply of tree species for plywood manufacturing has diversified. Findings of such analysis can be used as basic data detailing the anatomy and characteristics of the species of wood to be used for repairing wooden cultural assets (Passedat et al., 2009; Han et al., 2016; Lee and Bae, 2021). In this study, species identification of plywood was performed to reveal the importance of the anatomical analysis of wood products according to the distribution of legal wood and the anatomical characteristics of mixed light hardwood plywood distributed in Korea.
2. MATERIALS and METHODS
Samples were obtained from four companies trading plywood from major domestic plywood producers. Douglas fir (Pseudotsuga menziesii (Mirb.) Franco.) and Larch (Larix kaempferi (Lamb.) Carriere) plywoods of standard size [14.5(15) × 1,220 × 2,440 mm] sold by each company were purchased and analyzed. The species with the highest sales volume among 7 ply and 9 ply was selected (Fig. 1).
Company | Type | Douglas fir plywood (purchase) | Type | Larch plywood (purchase) | ||
---|---|---|---|---|---|---|
A | 1 |
![]() |
![]() |
1-1 |
![]() |
![]() |
7 ply | 7 ply | |||||
B | 2 |
![]() |
![]() |
2-1 |
![]() |
![]() |
9 ply | 9 ply | |||||
C | 3 |
![]() |
![]() |
3-1 |
![]() |
![]() |
7 ply | 9 ply | |||||
D | 4 |
![]() |
![]() |
4-1 |
![]() |
![]() |
7 ply | 7 ply |
Softwood plywood (Douglas fir and Larch) was cut to about 1 cm3 in size to identify the species of each layer. This was immersed in distilled water for about 2 days, and all the layers were separated from the face to the back using a cross-sectional view (Fig. 2). Sections with a thickness of 15-20 µm were prepared from the separated veneer using a sliding microtome. The three prepared sections were stained with 1% safranin (Jourez et al., 2001), dehydrated with increasing concentrations of ethyl alcohol (50%, 70%, 90%, 95%, and 99%), and then observed under an optical microscope (Imager A1, Carl Zeiss, Germany).
3. RESULTS and DISCUSSION
Analysis of the multiple types of plywood with the highest sales volume in domestic plywood companies was performed based on the thickness of the plywood and the number of veneers. Larch was included in the main forest plantation species detailed in the Basic Forest Policies that began to be implemented in 1973. Since 2000s, its new uses as structural lumber and laminated wood have been established, making it a representative timber resource dominating the era of domestic timber (Bae et al., 2012). Hemlock, Douglas fir, and Spruce imported from North America were all called “Pinus menziesii” in the Korean raw wood market in the 1960s and 1970s. This is because the bark of all three species was similar to that of a pine tree. However, Douglas fir is the correct name, not “Pinus menziesii” or “Pinus koraiensis”, another name for “Pinus menziesii.”
In Table 1, 1 and 1-1 are the same company, as are 2 and 2-1, 3 and 3-1, and 4 and 4-1. The plywood from company 1 (7 ply) was made with a Pinus species of the Pinaceae family. The cross section of the face layer was indistinguishable as it was too thin to perform hand-cutting. The remaining layers 2–7 were observed to be made with a Pinus species of the Pinaceae family (Fig. 3). The tissue components of tracheid, vertical and horizontal vessels, the epithelial cells, ray parenchyma, and ray tracheid found in Pinus species were identified. The characteristic tissues were the ray tissues in the radial section with pinoid pits. The tangential section was composed of uniseriate and fusiform rays (Jeong and Park, 2008; Eom 2005; Kim et al., 2018; Kwon, 2020). The sample from company 1-1 (7 ply) was made of a mixture of softwood, and the layers were observed to be made of Larch (1, 3, 5, and 7 layers) and Pine (2, 4, and 6 layers) (Fig. 4). As a larch of the Pinus species, there were vertical vessels in the cross section, the ray tissues in the radial section had ray parenchyma and a ray tracheid with piceoid or cupressoid pits, and the tangential section was composed of uniseriate and fusiform ray tissues. In addition, it had horizontal and vertical epithelial cells (Han, 2017). The sample of company 2 (9 ply) shown in Fig. 5 was made with Populus species of the willow family (1–9 ply). It was made with Populus species of the willow family (1–9 ply). It was a diffuse-porous wood with pores of almost constant diameter evenly distributed in the cross section throughout the annual rings. The vessel element had a simple perforation plate. The rays consisted only of uniseriate rays, and parenchyma cells were arranged longitudinally (Jeon, 2020). The sample of company 2-1 (9 ply) had a mixture of Larch (1, 3, 5, 7, and 9 layers) and Poplar (2, 4, 6, and 8 layers) ply (Fig. 6). The characteristic tissue structure was identical to Fig. 3 and 4. The sample of company 3 (7 ply) was observed to be made of a Pinus species of the Pinaceae family (Fig. 7), and that of company 3-1 (9 ply) was made of Larch (1–8 ply) and Poplar (9 ply) (Fig. 8), i.e., only the back layer of the sample of company 3-1 was identified to be a Populus species. The sample of company 4 (7 ply) shown in Fig. 9 was observed to be a Pinus species of the Pinaceae family, and that of company 4-1 (7 ply) shown in Fig. 10 had Larch (1, 3, 5, and 7 layers) and Pine (2, 4, and 6 layers) ply (IAWA, 1989, 2004; Jeong and Park, 2008; Eom, 2015; Eom, 2018). Their anatomical description was identical.
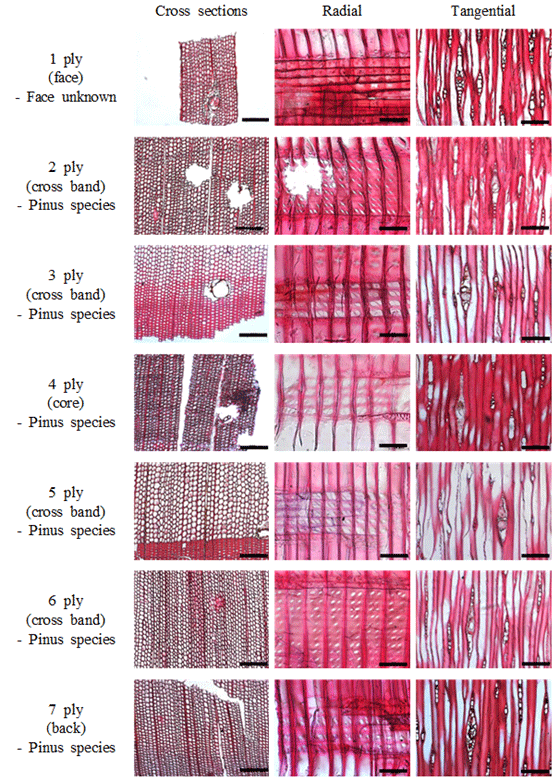
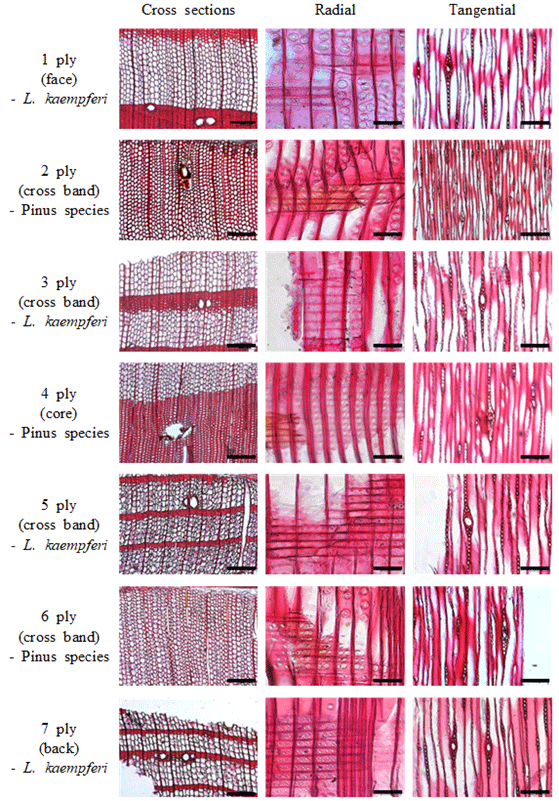
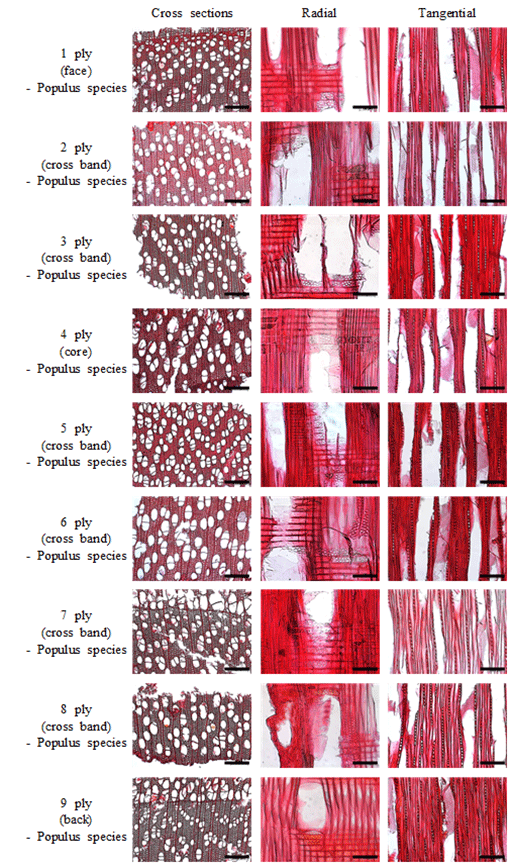
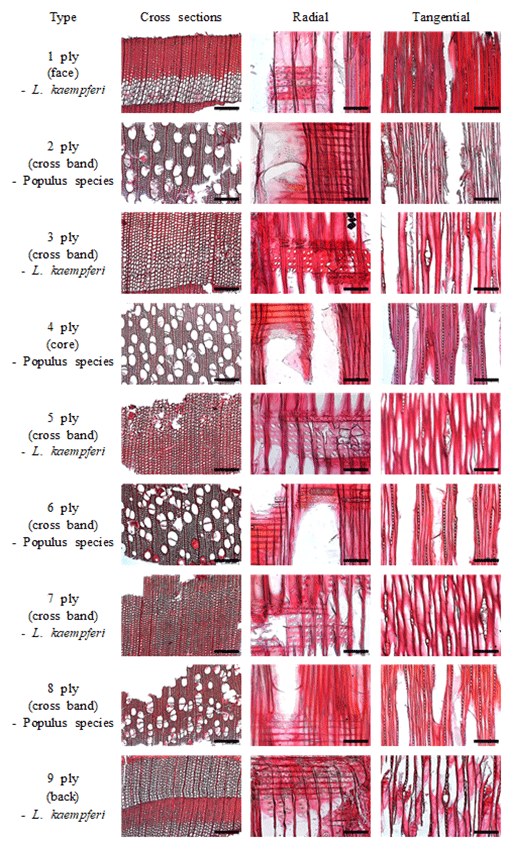
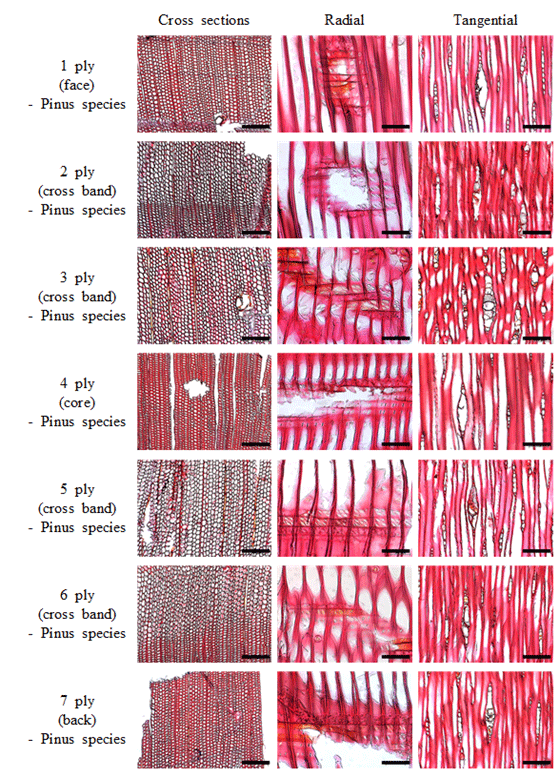
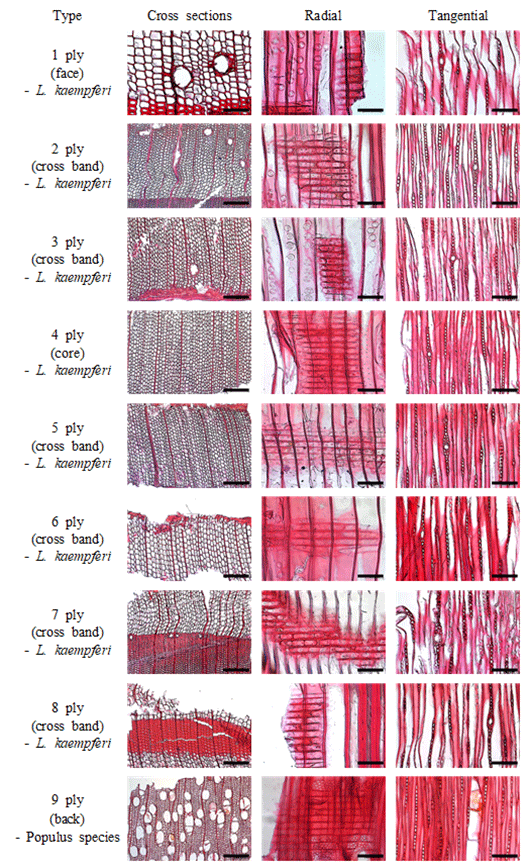
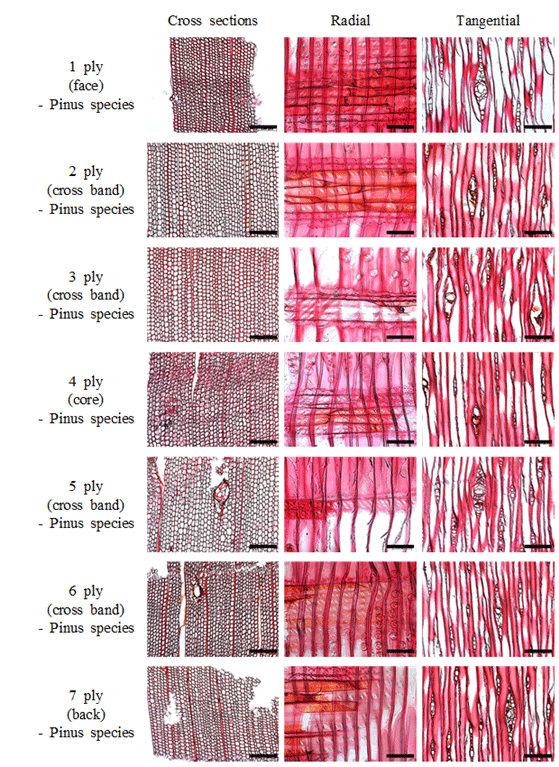
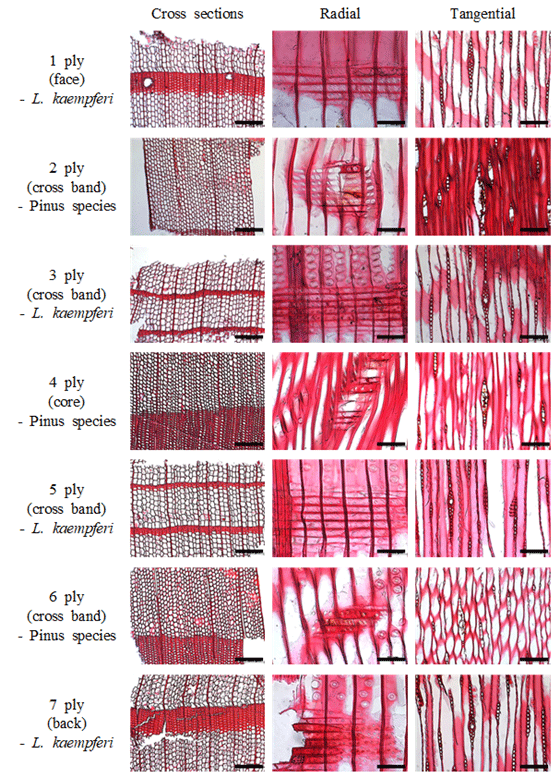
In conclusion, the layers of Douglas fir plywood from different companies did not match, but the layers of Larch plywood from every company did match.
Therefore, since the “deception of tree species” occurs in the production or distribution of plywood, this will play an important role in protecting the wood industry by identifying the species used in domestically distributed and imported plywood and provide reliable measures.
4. CONCLUSION
In this study, plywood distributed by domestic distributors was compared and analyzed based on anatomical characteristics. The Douglas fir and Larch plywoods of the four companies were found not to be made of a single species but rather a mixture of softwood and hardwood. Further, the species used for making the face layer to the back layer were found to be different.
Among the domestically manufactured plywoods sold as Douglas fir, three 7 ply plywoods were made of Pinus species and one 9 ply plywood was made of Populus species. Among the Larch plywoods manufactured overseas, two 7 ply plywoods were not made from a single tree species but rather a mixed species of Larix and other Pinus species and two 9 ply plywoods were made of mixed species of Larix and Populus species. This study provides basic data for tree species identification for wood and wood products imported and distributed in Korea.