1. INTRODUCTION
Size reduction and particle classification are vital pre-processing operations associated with the use of biomass in energy production and as a feed for other industries. The designs and choices of the size reduction and classification processes and the equipments are important in enhancing the efficiency of biomass preparation as raw materials (Naimi et al., 2006). The application of pre-processing operations such as size reduction is critical in order to increase the surface area of lignocellulosic biomass prior to various main processes such as chemical reactions, composite material manufacturing, and mechanical densification, Kim et al. (2011) developed popping pretreatment method for enzymatic hydrolysis of waste wood. Jang et al. (2012) developed the technology to produce cellulose nanofibers from plantation resources by hammer mill type continuous grinding process. Cellulose nanofibers were also prepared for polyurethane nanocomposites (Jang et al., 2014) and nanopaper (Park et al., 2015) from Korean white pine through wet disk-milling.
The size, shape, and uniformity of the raw material are important quality characteristics especially in the manufacturing of biomass pellets. Besides biomass pellet the biofuel (e.g. bio-ethanol) industry also requires a proper size reduction of biomass to improve the efficiency of its conversion to biofuel (Zhang, 2014). Hwang et al. (2012) investigated the effect of particle size of woody biomass on the feature of pyrolytic products. Kim and Kim (2019) found that relative crystallinity of the heat treated wood cellulose decreased with decreasing particle size. Lee et al. (2020) ground radiata pine bark to a particle size smaller than 1 mm to extract polyphenols for bio-foam preparation.
Biomass size reduction refers to mechanical treatment processes that significantly change the particle size, shape and bulk density of the material. These processes may involve one or a combination of the following types of actions: cutting, shearing, tearing, impact stress, compression and friction (Miu et al., 2006).
Devices for physical separation such as vibrating sieves, air-screen cleaners, and classifiers are usually used to classify comminuted biomass based on physical properties. Yang et al. (2019) used mechanical sieves to screen proper sized particles from pulverized sawdust to analyze chemical characteristics. Ju et al. (2020) also screened ground carbonized materials with a vibratory sieve shaker for manufacturing wood charcoal briquettes. Sieves are generally utilized for large-scale particle separation in the industry and for particle size distribution analysis in laboratories. This separation method is assuming the homogeneous and uniformly-shaped particles on a screen based on the theoretical passage through an aperture. Therefore, the heterogeneous and irregular particles such as biomass should receive significant attention (Yang, 2007). The needle-like shape of particles for some biomass such as Miscanthus renders separation using standard method involving sieves inadequate for particle size classification (Lee, et al., 2018).
There are generally big differences in characteristics of size reduction and classification due to biomass species. One of the main reasons why Miscanthus sacchariflorus Goedae-Uksae 1 is not utilized efficiently may be the imperfections in processing technologies such as the efficient size reduction and the reliable screening for this biomass. Therefore, for the best use of this biomass, it is necessary to look for ways to improve this biomass feedstock preparation for processing (Kadziuliene et al., 2014).
In this work cone-type grinder was combined with air-classifier to enhance the efficiency of raw material preparation process for Miscanthus sacchariflorus Goedae-Uksae 1. Miscanthus sacchariflorus Goedae-Uksae 1 was comminuted, classified and collected simultaneously. And the performance of this system was evaluated by the yield of proper particles.
2. MATERIALS and METHODS
Bioenergy Crop Research Center in Muan, Korea provided the air-dried samples of Miscanthus sacchariflorus Goedae-Uksae 1. The average moisture content of samples measured using the oven-drying method was 9.1% (wet basis). A forage chopper (Model No. SC4500, Hwangso Co., Korea) with a 2.25 kW electric motor was used to chop samples to lengths of 18, 40, 80, and 160 mm.
Some of chopped samples were comminuted using a laboratory-scale knife mill (Model No. LKM2015, Drying Engineering, Inc., Korea) equiped with a 3.75 kW electric motor with a rotation speed of 1720 rpm. The gap between the knives and the cutting bars was set at 3 mm and the aperture size of knife mill screen was 3 mm.
Air classification system was composed of cyclone (diameter 300 mm, height 600 mm), turbo blower (motor power 1.5 kW, air flow rate 40 m3/min, static pressure 285 mmAq), bag filter (diameter 300 mm, length 1600 mm), and ducting systems (diameter 100 ~ 150 mm) (Fig. 1). Magnetic vibrating feeder with maximum vibrations per minute (VPM) of 3600 (Model No. HMF-00B, Hwashin Co., Korea) was installed with chute at the slope angle of 8o in front of suction duct inlet to distribute particles uniformly. Linear relationship between VPM of vibrating feeder and material feeding rate was found through the preliminary test with feed rate per charge of 40 g as shown in Fig. 2. Each test was repeated three times to minimize the experimental error. For example, 40 g of feed could pass through the vibrating feeder in about 13 seconds at VPM of 2520. For this study VPM was set at 2520.
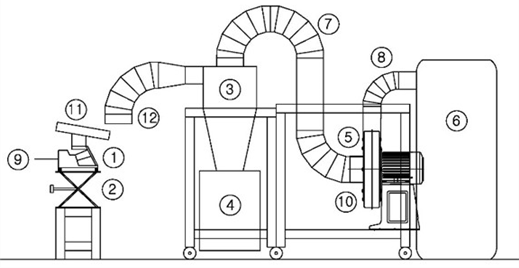
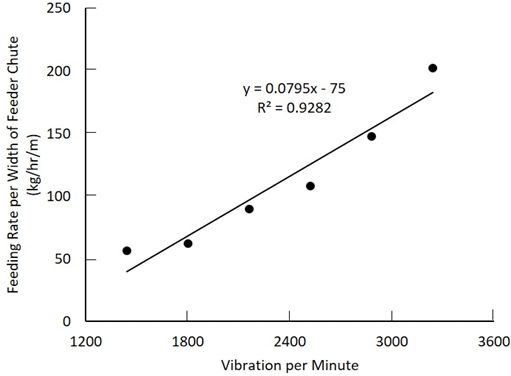
Air velocity at the inlet of suction duct was measured by vane-type digital anemometer and controlled by frequency control type inverter. Regression equation between frequency set at the inverter and air velocity was predicted as Eq. (1).
where is air velocity at the inlet of suction duct and
is the frequency set value of inverter.
Particles were pneumatically conveyed into cyclone and most of them were collected in duct storage. Too small particles that could not be collected by cyclone was finally collected in bag filter. Therefore, the yield of this air-classification system was represented as the ratio of mass of collected particles to total mass of particles fed by vibrating feeder.
A flatbed scanner (Canon-scan 4400F, Canon U.S.A. Inc., Lake Success, NY) provided digital image (4800 dpi × 9600 dpi) that were used to analyze aspect ratios, circularities indices, hydraulic diameters, and equivalent spherical diameters of large particles that were produced by knife mill and could be collected at each air velocity of air classifier. For imaging, 6 ~ 9 larger particles among each collected sample were selected by naked eyes (Fig. 3). All the image processing procedures and analysis conditions were same as the previous study by Lee et al. (2018). The acquired image were converted into binary form through a 8-bit gray scale image before analysis using the Image J software (Ferreira and Rasband, 2012). The 8-bit gray scale images were converted to binary images with a threshold of 100. Finally, the dimensional characteristics of the particles on the images such as areas, perimeters, circularities, and aspect ratios were determined. Seo et al. (2018) also measured sizes of particles for particleboard and oriented strandboard with image processing technique.
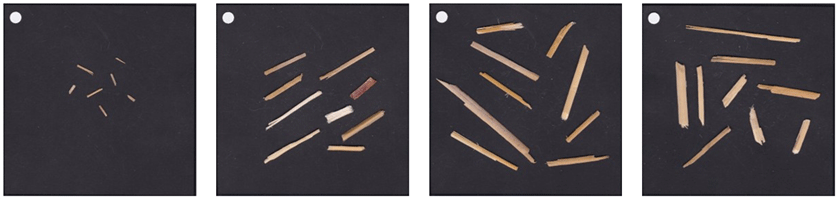
Lee et al. (2018) found that most particles of Miscanthus sacchariflorus comminuted by knife mill had needle-like shape even after screening by sieve shaker. This means that pre-processing of Miscanthus sacchariflorus with knife milling and sieve-screening is expected to produce proper particles for pelletization at extremely low yield rate.
Cone grinder is generally applied to crush and comminute stones or mineral materials by combined actions of shearing, tearing, compression, and friction. In this study a laboratory scale cone grinder with inner diameter of 200 mm was designed and built (Fig. 4). This cone grinder had five wheels with teeth around the circumference. Five grinding wheels were piled up to form a trapezoid and the inner wall of grinder was grooved like teeth. either. Diameter of the smallest and the largest grinding wheel was 154 mm at the top and 194mm at th bottom of this trapezoid in grinding chamber, respectively. With this design the gap between grinding wheel and inner wall decreased gradually from inlet to outlet of cone grinder. Therefore, large particles could be comminuted to smaller ones stepwise. Inlet duct of air classifier was installed at the outlet of cone grinder to collect particles with proper size and the oversized particles were discharged through the cone grinder chute.
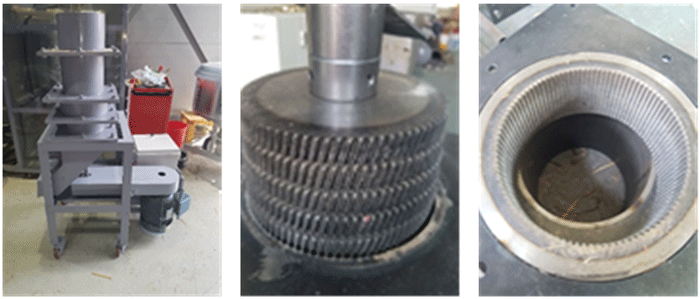
The oversized particles were fed again into cone grinder to simulate multi-step process of cone-grinding and air-classifying as Fig. 5. Three steps were simulated and mass of collected particles was measure at each step. Finally, the ratio of sum of total mass of collected particles through these three steps to input mass was represented as the yield of this combination system.
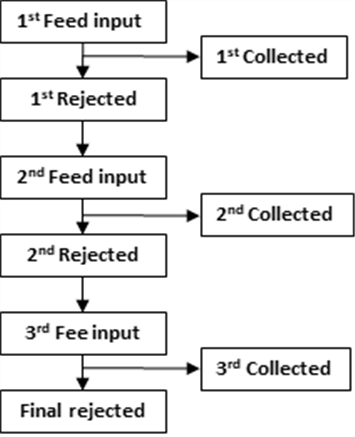
Miscanthus sacchariflorus chopped to lengths of 18, 40, 80, and 160 mm were prepared as feeds for cone grinder. Feed rate was set at 30 g per charge for stable and continuous feeding and each test was repeated three times to minimize the experimental error.
3. RESULTS and DISCUSSION
Fig. 6 shows the mass ratio of collected particles to input mass of Miscanthus sacchariflorus comminuted by knife mill. This mass ratio increased as air velocity increased as expected. Preliminary test results for average aspect ratio and circularity index from particle shape image analysis did not show significant relationships with air velocity. Meanwhile, average equivalent spherical diameter (ESD) of particles showed highly significant relationship with air velocity as Fig. 7.
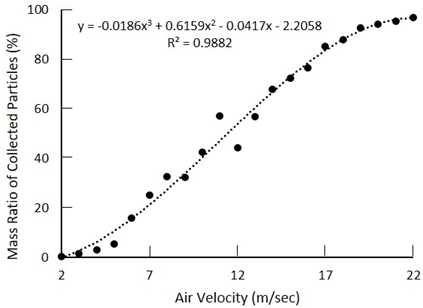
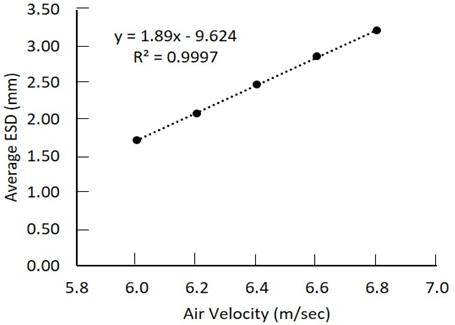
Pelletizing process requires particle size smaller than 4 mm for pellet diameter of 8 mm in general. ESD of large particles collected at air velocity of 7 m/sec was estimated as 3.61 mm. Therefore, the air velocity range to classify particles proper for pellet manufacturing was determined as 6.0 ~ 6.8 m/sec.
where is ESD of particle (mm) and
is volume of particle (mm3).
Based on the law of pneumatic conveying for solid particles the lowest air velocity required to convey solid particles pneumatically is equal to the terminal velocity. When sum of drag force and buoyancy force is equal to gravity acceleration of gravity is 0 and a solid particle descends at uniform velocity. This uniform descending velocity is called as terminal velocity (Mills, 2004).
where is terminal velocity (m/sec),
is acceleration of gravity (= 9.81 m/sec2),
is diameter of particle (m),
is drag coefficient,
is density of solid particle (kg/m3), and
is density of air (= 1.16 kg/m3 at 30℃).
Reynolds numbers for the air velocity range of 6.0 ~ 6.8 m/sec were calculated as Table 1.
Air velocity (m/sec) | 6.0 | 6.2 | 6.4 | 6.6 | 6.8 |
---|---|---|---|---|---|
![]() |
37419 | 38667 | 39914 | 41161 | 42409 |
where is Reynolds number,
is inner diameter of pipe (= 0.1 m), and
is dynamic viscosity of air (= 1.860 x 10-5 kg/m/sec at 30℃).
Model for determining proper air velocity to classify particles smaller than target size was developed assuming that the terminal velocity required to collect the particle with the certain maximum size is equal to that proper air velocity. Futhermore, diameter of particle is assumed to be ESD because the shapes of particles is too irregular to determine the particle diameters. Comminuted particles of Miscanthus sacchariflorus showed pin-type shape as Fig. 3. Drag coefficient can be derived from Eq. (3). Therefore, drag coefficients were determined using Eq. (5) and the relationship between
and
was estimated as Eq. (6) from the experimental data.
where is ESD (m). Finally, the model for determining proper air velocity was developed as Eq. (7).
Table 2 shows the predicted proper air velocity for the maximum ESD that could be collected. For example, the proper air velocity to collect particles with sizes smaller than ESD of 4 mm for pellet manufacturing was predicted as 6.9 m/sec for Miscanthus sacchariflorus. ESD of the largest particle collected at air velocity of 6.8 m/sec was estimated as 3.67 mm according to this experimental data.
Max. ESD to be collected (mm) | 1.0 | 2.0 | 3.0 | 4.0 | 5.0 |
---|---|---|---|---|---|
Proper air velocity (m/sec) | 5.0 | 6.0 | 6.6 | 6.9 | 7.1 |
Table 3 shows the results of the simulation tests for the combination system of cone grinder and air classifier. Air velocity at the inlet duct of air classifier was set at 6.8 m/sec that could guarantee the collection of particles with average ESD smaller than 4.0 mm.
Step | Chopped length (mm) | |||
---|---|---|---|---|
160 | 80 | 40 | 18 | |
After 1st step After 2nd step After 3rd step |
45.1% 39.1% 52.8% |
47.7% 46.6% 46.8% |
47.4% 41.4% 49.6% |
46.1% 44.2% 44.1% |
Total mass ratio (%) | 84.2% | 85.1% | 84.5% | 83.2% |
The ratios of mass of collected particles to mass of feed for four lengths of chopped Miscanthus sacchariflorus were 45.1 ~ 46.1%, 39.1 ~ 46.6%, and 44.1 ~ 52.8% at the first, second, and third step, respectively. Total mass ratios of collected particles to feed were 83.2 ~ 84.2% with an average of 83.7%. No significant difference due to chopped length or number of steps could be found.
The mass ratio of collected particles to mass of knife- milled feed was below 20% at air velocity of 7 m/sec for air classifier in Fig. 6. Therefore, it was revealed that cone grinder could comminute Miscanthus sacchariflorus with higher performance than knife mill.
Womac et al. (2007) recommended a multiple-stage grinding process for proper size reduction of biomass. Lee et al. (2018) found that knife milling with vibrating sieve screening method could not prepare appropriately sized particles from Miscanthus sacchariflorus. Fig. 8 shows the images of Miscanthus sacchariflorus particles collected at various air velocities after comminuting by cone grinder. Most particles prepared with this combination system had small size and fibrous shape that could be helpful for pelletizing process. This fibrous shape of particles seems to be mainly due to the actions of cone grinder, especially shearing, tearing, and friction, while the main actions in knife milling or hammer milling are cutting and impacting.
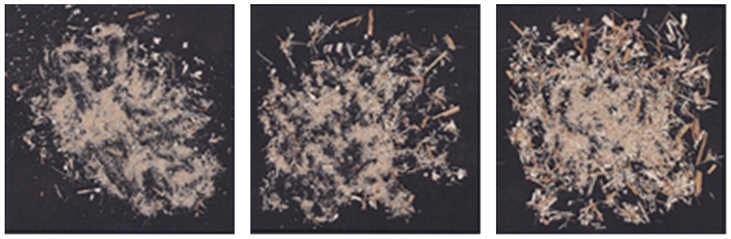
4. CONCLUSION
A laboratory scale combination system of cone grinder and air classifier were designed and built to improve the performance for pre-processing of Miscanthus sacchariflorus Goedae-Uksae 1. Air velocity of 6.8 m/sec at the inlet duct of air classifier was determined for the collection of particles with average equivalent spherical diameter smaller than 4.0 mm. At this air velocity for air classification total mass ratios of collected particles to inputs were 83.2 ~ 84.2% with an average of 83.7% when simulating three-step cone-grinding and air-classifying system. This high yield and fibrous shape of particles with proper size are expected to enhance the efficiency of following-up processes, such as pelletization.