1. INTRODUCTION
Various shear strength tests are being used to measure an adequate adhesion strength of bonded-wood products (Hendrik et al., 2019; Park et al., 2020; Steiger et al., 2010). Cohesive failure (within bulk) and adhesion failure (at interphase) are important factors in wood bonding systems (Choi et al., 2020; Collett, 1972; Frihart and Hunt, 2010). In particular, the adhesion in interphase between wood and adhesives is important for bonded-wood products to have suitable adhesion performance (Marshall et al., 2010; Kamke and Lee, 2007). In other words, the resin that requires adequate adhesion performance must satisfy a certain level of the wood failure percentage (WFP). In general, WFP is one of the common adhesion performance evaluations, and used to determine the bond quality of wood-based composites. Therefore, the WFP is often used as a standard requirement of an adhesion performance of wood products such as plywood and glued-laminated timber (Glulam).
The WFP after adhesion strength tests is defined as the percentage of the fractured wood surface area to the total bonded area and is expressed as a percentage graded as 0 to 100 % (Künniger, 2008). The WFP is one of the indicators of measuring the adhesion performance of wood adhesives used in the manufacture of wood products. For example, the WFP of phenol-formaldehyde (PF) resins was closely related to the adhesion performance of the resin as well as visual observation of the degree of penetration of the resin into the wood interphase (Paris and Kamke, 2014). In particular, the WFP of exterior grade adhesives such as resorcinol-formaldehyde (RF) resins, phenol-formaldehyde (PF) resins, phenol-resorcinol-formaldehyde (PRF) resins, or melamine-urea-formaldehyde (MUF) resins is an important requirement that must be satisfied by testing of bonded-wood products (Glavinić et al., 2020; Lim et al., 2020; Roh et al., 2018; Wen et al., 2020). Phenolic resins, including RF, PF, and PRF resins inherently show a dark and reddish-brown color of the bond-line, which makes it easy to identify the fracture area of wood in the bonded area (Cameron and Pizzi, 1985; Clauß et al., 2011; Frihart et al., 2004; Hse, 1972). The characteristic of these resins led to adopt the method of measuring their WFP using image-analysis. This method, which uses distinctive color contrast provided by wood and adhesive, is elaborate method of WFP measurement. This image analysis method is a relatively inexpensive and effective method, and manufacturers have continuously applied image-analysis to WFP measurement (Ellis, 1995; Zink and Kartunova, 1998). In fact, some works were already done for wood specimens bonded with phenolic resins, using image-analysis method (Lin et al., 2015; Gibson and Krahmer, 1980; Ginzel and Stegmann 1970; Yuan et al., 2012).
However, a transparent and color-less adhesives such as UF, MUF, or melamine-formaldehyde (MF) resins makes it difficult to determine the area of wood fracture surface in the bonded area after the shear test (Lubis et al., 2020; Künniger, 2008). MUF resins with low melamine content (~10%) are mainly used for interior grade wood products such as plywood, particleboard or medium density fiberboard (MDF) (Lubis et al., 2019). However, MUF resins with high melamine content (≥20%) are used for manufacturing exterior grade plywood (Lubis et al., 2019), Glulam, or cross-laminated timber (CLT) because they are at low cost and have better resistance to water than UF resins (Dunky, 1998; Galih, 2020; Lim, 2020). In addition, cold-setting MUF resins with high melamine contents are also used for fabricating Glulam or CLT at room temperature (Baxter et al., 1973; Sauget et al., 2014; Frihart and Hunt, 2010; Lhelihe et al., 2016; Park et al., 2004).
Although MUF resins have been used for manufacturing various wood products (Künniger, 2008), this method has not been used for wood products bonded with colorless wood adhesives such as UF, MUF, or MF resins. In particular, a little study on the WFP measurement of cold-setting MUF resins has been conducted. Thus, this study was conducted to quantitatively determine the WFP of the block shear strength (BSS) samples bonded with cold-setting MUF resins, using image analysis method.
2. MATERIALS and METHODS
All MUF resins were synthesized using technical-grade melamine (99%), urea granules (99%), and formalin (37%) purchased from Daejung Chemical, Korea. During the synthesis process, the pH was adjusted by adding aqueous solutions of acetic acid (20 wt%) and NaOH (20 wt%). A mixture of carboxymethyl cellulose, CMC (95%) and formic acid (85%) was used as a hardener (Zhou et al., 2018). The lamina sample (200 x 25 x 15 mm) of Larch wood (Larix kaempferi Carr.) with 9 ~ 10 % moisture content was used for the manufacture of all block shear samples.
Cold-setting MUF resins were synthesized by as reported in Jeong et al., 2019. Formalin was added to a reactor equipped with a mantle heater. The pH was adjusted to 8.5 by adding NaOH solution (20 wt%). Simultaneously, melamine (20, 30 or 40% solid content) was added to the reactor with continuous stirring at 40°C. The temperature was then increased to 90°C and maintained for one hour. The first urea preparation was added to the reactor at an F/(M + U) molar ratio of 1.7 and held for 10 minutes. At this time, the pH was adjusted to 7.5–8.0 with 20 wt% acetic acid. The condensation reaction was maintained at 80°C until the target viscosity scale (J-K) of a bubble viscometer (VG-9100, Gardner Holdt, USA). At this time, the condensation reaction was stopped and the target water tolerance (150%) was checked by the clouding point. The pH was adjusted to 7.5–8.0 and the resins were cooled to 60 °C. After cooling, the second urea preparation was added and maintained for 20 minutes to obtain the final molar ratio (F/(M+U) = 1.2). Once the reaction was completed, the MUF resins were cooled to ambient temperature and the pH was adjusted to 9.0–9.2.
Carboxymethyl cellulose (CMC) is dissolved in water and the solution is left to hydrate well for 24 hours. Afterwards, formic acid solution is added and then dissolved for 24 hours prior to use (Mansouri et al., 2009; Pizzi, 2003).
The properties of cold-setting MUF resins such as non-volatile solid contents, viscosities, and water tolerance were evaluated. The viscosity was measured with a cone-plate viscometer (DV II +, Brookfield, NY, USA) operated at 25 °C and 60 rpm, using a spindle No. 2 for the cold-setting MUF resins. The non-volatile solids content of each sample was calculated by comparing the resin mass before and after drying the resins for 3 hours at 105 °C in oven. The water-tolerance value was determined by adding a certain amount of water into 1 gram resin sample in the tube, and checking the clouding point of the resin sample at 20°C.
Prior to preparing the BSS samples of Larch wood, a 100 part of MUF resins were mixed with 15 part of the hardener based on the total mass of MUF resins (Choi, 2020). Fig. 1 shows a schematic diagram of the block shear specimens. And, Fig. 2 presents the process of BSS test using block shear specimens manufactured according to Fig. 1. The BSS samples were prepared by bonding two Larch wood laminae together with cold-setting MUF resins at a glue spread of 250 g/m2 for both surfaces, and pressed for four hours under a pressure of 10 kgf/cm2 at ambient temperature.
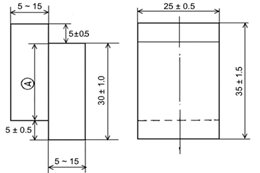
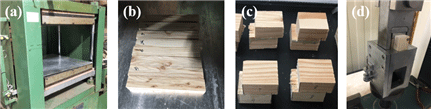
Twenty BSS specimens (25 x 25 x 15 mm) were prepared by cutting the bonded laminae, and then tested under shear stress at a 1 mm/min of the cross-head speed using an universal testing machine (H50KS, Hounsfield, Redhill, England) depending on the procedure of Korean standard (KS M 3705). The BSS values in either dry or wet state were measured. Dry BSS value was obtained by testing 10 specimens at room temperature. By contrast, 10 specimens for wet BSS were treated for four-hour soaking in boiling water, twenty-hour drying in an oven, and then four-hour soaking in boiling water prior to testing them under shear stress. An average of the dry and wet BSS was determined by testing 10 specimens for each MUF resin at three levels of melamine content, respectively.
The fractured specimens after the BSS test were collected for WFP measurement with a further processing. The wood fractured surface of specimens was closely inspected by naked eyes, and then the boundary of the wood fractured surface was specifically colored as black, using oil-borne black color pen for further process. Then, images of the fractured surface of a specimen were captured to obtain an average WFP computed by image-processing software (IMT solution ver.22.5, Vancouver, British Columbia, Canada). Ten specimens for each dry and wet condition were tested for block-shear test, and the facture surface of these ten specimens were used to measure WFP using the image analysis. A minimum of three images per specimen was captured to obtain an average WFP of thirty samples for each.
Fig. 3 shows typical images of the fracture surface (Fig. 3(a)), wood fractured surface in black color (Fig. 3(b)), and processed images of wood fractured surface for the WFP measurement (Fig. 3(c)). As shown in Fig. 3 (a), it is difficult to identify the wood fractured area in the fracture surface due to transparent color of cold-setting MUF resins. To solve this problem, the wood fractured area was identified by naked eyes, and then marked as black color. As shown in the Fig. 3 (b), the wood fractured area is clearly identifiable after the black coloring. Then, images of the fracture surface were used for further processing with the image-analysis software (Fig. 3(c)). This software semi-automatically calculated the WFP by dividing the black-colored area with the total surface area.
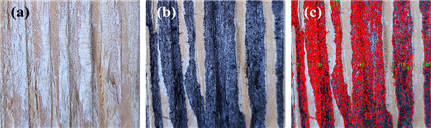
3. RESULTS and DISCUSSION
Table 1 presents the properties of cold-setting MUF resins with three melamine contents. The non-volatile solids content of MUF resins increased as the melamine content increased. The gelation time was also accelerated with an increase in the melamine content. This is reasonable because MUF resins with high melamine content generally have high condensation and molecular weight resins (Jeong and Park, 2019; Jeong et al., 2020; Tohmura et al., 2001). The water tolerance of both resins was maintained at about 150 % as it was controlled in the synthesis. The viscosity of MUF resins increased as the melamine content increased.
Figs. 4 and 5 show typical images of the fracture surfaces of BSS specimens bonded with cold-setting MUF reins at three melamine contents for measuring the WFP after the BSS test in dry and wet state. As presented in Figs. 4 and 5, the wood fractured area of the specimens clearly increases as the melamine content increases for dry and wet state. The WFP of MUF resins at 20% melamine shows the smallest area of wood fracture when compared with those at 30 and 40% melamine content.
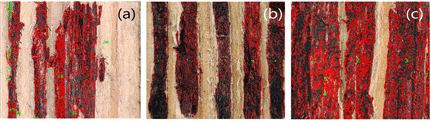
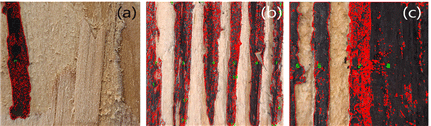
This could be due to that the adhesion of cold-setting MUF resins was improved with an increase in the melamine content (Zanetti et al., 2002). In other words, the MUF resins that have penetrated into wood tissues in the interphase of bond-line will form a strong bond-line as the melamine content increased (Jeong et al., 2019; Aydin I, 2004; Kenai, 2011). In general, both melamine content and shear strength are related to WFP (Properzi et al., 2001). That is, high WFP values at the high melamine content resins indicate a strong adhesion of the resins.
Fig. 6 shows WFP and BSS of the cold-setting MUF resins at different melamine contents in dry and wet state. The results clearly showed that the WFP was closely related to the BSS as the melamine content increased. In the shear strength test, strong adhesion causes greater WFP. Therefore, it is necessary to see if the WFP measured by the method is related to the BSS. Obviously, WFP values in dry state were higher than in wet state for all levels of melamine content because the boiling process in hot water weakened the bond-line of the block-shear specimen, which affected the WFP results. And, cold-setting MUF resins containing 40% melamine content in both dry and wet state showed highest WFP values (dry: 97.5%, wet: 88.4%). This is consistent with the results showing the largest area of wood fracture at high melamine content (Figs. 4 & 5). These WFP values of the resins met the requirement level (≥65%) of glulam in both dry and wet conditions specified by the Korean Standard (2015).
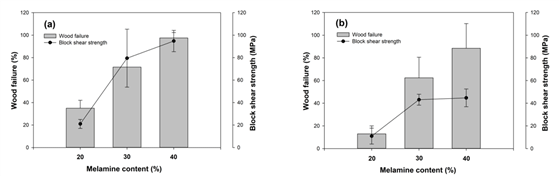
As expected by the WFP, the BSS increased with an increase in the melamine content of MUF resins. The MUF resins containing 40% melamine also showed the highest BSS in dry and wet conditions. These results show that the BSS consistently increased as the WFP did. All dry BSS values were much higher than those in wet state, regardless of the melamine content. So, it is believed that increasing the melamine content results in high BSS and WFP by forming rigid bond-line between the resins and wood. In other words, the WFP of the cold-setting MUF resins measured by this image analysis method has a close correlation with BSS as a function of the melamine content. Therefore, this proposed method of measuring WFP seems to have a potential to be used for wood-based composite as well.
4. CONCLUSION
In this study, the method of measuring the WFP of the BSS specimens bonded with cold-setting and transparent MUF resins is presented. After the block shear test, the broken part (wood failure) was marked as black color to capture the images of fracture surface, and then these images were processed using an image analysis software for the accurate measurement of WFP. As expected, the WFP values measured by this method increased as the BSS increased in the dry and wet condition. It is thought that as the melamine content of the resin increases, a rigid bond-line is formed between the resin and substrates (wood), resulting in high shear strength and WFP. In other words, the proposed method of measuring the WFP is reliable, and will be worthwhile for industrial application. In addition, this method could be used to measure the WFP of not only MUF resin but also other transparent and color-less adhesives in future.