1. INTRODUCTION
Natural dyes have been used since ancient times, however, their use significantly diminished upon the discovery of synthetic dyes (Ado et al., 2014). Natural dyes can be extracted from many plants, some animals, and minerals. Among these, plant dyes are most commonly used in natural dyeing and they are derived from roots, bark, stems, leaves, flowers, fruits, and shells of plants (Sivakumar et al., 2011; Geetha and Sumathy, 2013). The advantages of natural dyeing include soft color formation, being environmentally friendly, and their hypoallergenicity. Despite this, natural dyes were not industrialized for a long time due to complicated pigment extraction and dyeing processes, low color fastness, low reproducibility, and high cost (Chang et al., 2000; Mirjalili et al., 2011; Samanta and Konar, 2011; Hooda and Rangi, 2015). On the other hand, synthetic dyes are known to have superb color fixation, are easily mass produced, and are inexpensive (Hooda and Rangi, 2015). However, these days there are growing concerns about environmental pollution, stemming from dyeing wastewater, and human toxicity issues related to synthetic dyes (Mirjalili et al., 2011; Samanta and Konar, 2011; Kant 2012; Hooda and Rangi, 2015; Mani and Bharagava, 2018). The worldwide global demand for natural dyes is over 10,000 tons, which is equivalent to 1% of the world synthetic dye consumption (Sivakumar et al., 2011). The characteristics and production of natural dyes needs to be investigated as the demand for natural dyes is expected to grow. However, most are not practical for industrial use, therefore, it is necessary to develop eco-friendly and economical (cost-effective) new natural dyes.
Most pine barks contain polyphenols as a major component unlike wood xylem (Min et al., 2019; Ku and Mun, 2008;Mun and Ku, 2006). The main component of the polyphenols is known as proanthocyanidin (PA) as shown in Fig. 1. In particular, the bark derived from P. radiata wood, which is imported in large quantities to Korea every year, contains higher polyphenolic content than the domestic P. densiflora bark (Ku et al., 2007). In addition, the derived products from P. radiata bark are sold as health supplements and cosmetic additives under the name of Enzogenol® and Pinoradiol® (Ghosh and Mukherjee, 2009; Choi et al., 2018). The extracts obtained from P. radiata bark was also found to have potential as a termite deterrent (Mun and Nicholas, 2017) and as an adhesive for particle board production (Pizzi, 1982).
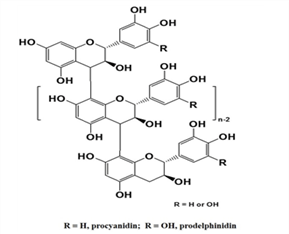
There are only a few dyeing studies about P. radiata bark extract (Song et al., 2009; Wang and Song, 2011; Jung and Song, 2012), and in particular, no dyeing studies have been conducted regarding the NE obtained by extracting P. radiata bark with NaHCO3, which was investigated in our previous study (Mun et al., 2020).
Lee et al. (2020) reported that when the bark of P. radiata was extracted in highly alkaline conditions, over 60% of the alkaline extract was obtained. However, the extract had low solubility in water due to the condensation reactions and structure rearrangements that took place during the extraction process. Therefore, the weak alkaline extraction of P. radiata bark was considered economical as reported before since this extraction method had higher yield than hot water extraction. In addition, the extracts had high antioxidant activity which would be beneficial as a functional natural dye.
The color of NE dyed fabrics were expected to be brown since NE was mainly composed of PAs which belongs to condensed tannins. Throughout history, many natural dyes have been used for brown dyeing and some examples are juice from green persimmon and extracts from acorn cupules or chestnut shells (Lee, 2004). However, these are impractical for industrial utilization because they require repetitive process and long time to express brown color and are seasonal.
In this study, we extracted P. radiata bark with aqueous NaHCO3 solution and prepared the neutral extract (NE). The dyeabilities of NE were evaluated using silk and cotton fabrics.
2. MATERIALS and METHODS
The bark used in this experiment was collected from logs, 70 - 80 years of age, at the timber yard of Baeksan Wood Co., Ltd. (Gunsan-si, Korea). Outer bark scales, inner bark, and dirt were removed and then the refined bark was crushed into small pieces. The crushed bark was ground with a blender (Primaire, Hanil, Korea) to make a fine powder. The ground bark was sieved and a 40 mesh-pass was taken as the material for this study. Silk (100%, 40 g/m2) and cotton (100%, 150 g/m2) fabrics purchased from Jeil Fabrics (Jeonju-si, Korea) were used for dyeing.
The NE used in this experiment was the same sample previously reported by the authors (Mun et al., 2020). A 100 g of the bark was extracted with 500 mL of 0.8% NaHCO3 aqueous solution in a 1 L round bottom flask. The flask fitted to a condenser was then placed in a PEG #400 bath preset at 110℃. The extraction was carried out with occasional shaking for 1 h when the mixture inside the flask started to boil. After extraction, the slurry was filtered through a 25G3 glass filter to obtain NE and the residue was washed with 500 mL of hot distilled-deionized water. After washing, the glass filter was dried in a convection oven (FO-600M, Jeio Tech, Korea) at 105℃ for 48 h. The yield of the neutral extracts was then calculated as follows (1):
where, BP is bark powder (g), o.d. is oven dried weight, and RE is residue after extraction.
The NE was lyophilized for 24 h in a freeze dryer (FDU-540, Eyela, Japan). The freeze-dried NE was dried again in a vacuum drying oven (SACO-36, Sancheon Tech Ind. Co. Ltd., Korea) at room temperature to obtain a moisture-free sample.
The PA content in NE was determined by UV spectrophotometry. A 10 mg of NE was dissolved in 50 mL of 50% (v/v) ethanol solution, diluted appropriately for UV determination, and then the absorbance at 280 nm was recorded. The standard calibration curve was constructed using pure PA. It was also dissolved in 50% (v/v) ethanol solution and the absorption was measured the same way as NE. PA content in NE was determined by comparing the UV absorbance of NE.
Dyeing of silk and cotton fabrics was conducted in a 100 mL beaker at four different NE concentrations of 0.5%, 1.0%, 1.5%, and 2.0% o.w.b. (on the weight of bath). The fabric to liquid ratio, dyeing temperature, and dyeing time were 1 : 50, 90oC, and 90 min, respectively, as the fixed condition. The beakers were covered with a watch glass and the fabrics were occasionally stirred while dyeing. After dyeing, the dyed fabrics were washed sufficiently with water and dried at room temperature.
For colorfastness, deodorization, and antibacterial activity assessment, the silk and cotton fabrics were dyed with NE concentration of 1.5% o.w.b.
The surface color of the dyed silk and cotton fabrics was measured to determine the dyeability of NE on the fabrics. The Munsell’s color hue (H), value (V), chroma (C), and CIE L*, a*, b* were measured by Color Reader (CR-20, Konica Minolta INC., Japan).
Colorfastness due to washing, rubbing, and light of the dyed fabrics were evaluated according to the Standard Test Methods KS K ISO 105-C06:2018, KS K ISO 105-X12:2017, and KS K ISO 105-B02:2015, respectively. After washing the dyed fabrics in Launder O meter at 40±2℃ for 30 min with ECE detergent, washing fastness of fade and stain was measured and evaluated by a gray scale and chromatic transference. Rubbing fastness was measured by Crockmeter method both in the dry and wet conditions. Light fastness was measured by light irradiation during the standard fading hours using a Xenon arc lamp. This assessment was conducted at Korea Apparel Testing & Research Institute (KATRI, Ansan-si, Korea).
Deodorization assessment was performed using the ammonia (NH3) gas detection tube method at KATRI (Ansan-si, Korea). In a 1 L container containing 10 cm ⅹ 10 cm dyed fabric, a 500 g/mL of ammonia was injected. The deodorization rate was measured every 30 min from 0 - 120 min at 20℃ room temperature and 65% humidity. The rate of deodorization was calculated from the following equation (2):
where, A = gas concentration of the blank and B = gas concentration under specimen.
Antibacterial activity was conducted according to the standard test method KS K 0693-2016 at KATRI (Ansan-si, Korea). The bacteria used for the test were Staphylococcus aureus (ATCC 6538) and Klebsiella pneumoniae (ATCC 4352), and those were injected into the dyed fabrics. After 18 h, antibacterial activity was calculated from the following equation (3):
where, C = the numbepr of microbes in the blank and D = the number of microbes in the specimen.
3. RESULTS and DISCUSSION
NE prepared by treating P. radiata bark with 0.8% NaHCO3 aqueous solution was obtained in 44% yield, which was about 11% higher than that of hot water extract (HWE) prepared from the same bark before, and its pH of 1% solution was nearly neutral (6.66). This indicates that mild alkaline extraction using 0.8% NaHCO3 solution was effective for preparing neutral PA-rich extracts from the bark. The dried NE dissolved well in cold water. The PA content in NE was 87% as determined by UV absorbance using pure PA as a reference. Other compounds in NE, although not quantitatively characterized, included small amount of monomeric flavonoids and carbohydrates as analyzed by 13C NMR and FT-IR techniques (Mun et al., 2020).
The dyeability of NE to silk and cotton was determined by surface color assessment of the fabrics. Surface color assessment was performed after dyeing with 0.5 - 2.0% o.w.b. of P. radiata bark NE in a DI-water ratio of 1 : 50 at 90℃ for 90 min. Table 1 shows the H and V/C values of fabrics dyed with NE at different concentrations. The color of the dyed silk and cotton fabrics ranged between 2.5 – 3.0 YR (brown) and 4.1 – 4.7 YR (light brown), respectively. The dyeability of silk fabric was good even at 0.5% but the dyeability of cotton was significantly poorer at 2%. It seemed that like most natural dyes, the neutral extract was also adsorbed only onto the surface of the cotton fabric and not chemically bonded with the fiber structure. Therefore, further studies will be needed to increase the dyeability of cotton fabrics, in order to use NE of P. radiata for cotton dyeing. Fig. 2 shows the surface color L* a* b* values of fabrics dyed with NE at different concentrations in two dimensions. Color value of all dyed fabrics were located in the middle of the a+ and b+ area, and this indicated that they were brown colored. The color difference could not be distinguished with the naked eye when the silk fabric was dyed with NE concentration of 1.5% and 2.0%, and their coordinates of L* a* b* values were close to each other. This result was similar to previous studies which observed that the dyeing sites in the silk fiber were almost saturated at concentrations above 1% o.w.b of P. radiata bark extracts (Song et al., 2009).
The colorfastness assessment was performed to determine the durability of NE dyed fabrics for washing, friction, and light exposure. The results of washing, rubbing, and light fastness of NE dyed silk and cotton fabrics are shown in Table 2. Overall, the colorfastness was very good to excellent except for the light fastness and fade of washing fastness on both silk and cotton fabrics. Fastness to washing was measured for fading color, which indicates the degree of change from the initial color, and staining fastness, which indicates the degree of contamination with other fabrics when washing dyed fabrics. Durability of the fade was moderate (3) and stain excellent (4-5) for both silk and cotton fabrics. In the case of rubbing fastness, irrespective of the dry or wet measurement methods, both the silk and cotton showed very good to excellent fastness of 4 to 4-5. Fastness to light of dyed fabrics were poor (1-2). The silk dyed with NE showed similar characteristics to that of silk dyed with PinuxTM, a commercial product derived from P. radiata bark (Song et al., 2009).
Colorfastness | Silk | Cotton | ||
---|---|---|---|---|
Washing | Fade | 3 | 3 | |
Stain | Cotton | 4-5 | 4-5 | |
Silk | 4-5 | - | ||
Wool | - | 4-5 | ||
Rubbing | Dry | 4-5 | 4 | |
Wet | 4 | 4 | ||
Light | 1-2 | 1-2 |
The deodorization property of NE dyed fabrics were determined by the ammonia gas detection tube method. The deodorization over time of the untreated and NE dyed fabrics is shown in Table 3. Both NE dyed silk and cotton fabrics exhibited higher deodo-rization properties than untreated ones. In general, it is known that silk has higher ammonia deodorization properties than cotton (Hwang et al., 2007). The deodorization property of dyed silk had no significant difference from untreated silk because the untreated silk already had deodorization property. The dyed cotton had a constant deodorization property of 80% regardless of time, but untreated cotton showed 40-60%. This result indicated that NE had good ammonia deodorization properties. The low affinity between the cotton fabric and NE was considered as the reason for the constant deodorization property of dyed cotton regardless of time.
Time (min) | Ammonia deodorization (%) | ||||
---|---|---|---|---|---|
Silk | Cotton | ||||
Untreated | Dyed | Untreated | Dyed | ||
30 | 90 | 92 | 40 | 80 | |
60 | 93 | 94 | 48 | 80 | |
90 | 95 | 98 | 55 | 80 | |
120 | 97 | 99 | 60 | 80 |
The antibacterial activity with official test bacteria was performed to determine the antibacterial effects of NE dyed silk and cotton fabrics. The antibacterial activity was measured 18 h after the injection of bacteria to the dyed fabrics and the results are shown in Table 4. Both NE dyed silk and cotton fabrics exhibited excellent reduction rate at 99.9% for S. aureus. Also, dyed silk had stronger antibacterial property for K. pneumoniae than cotton. Dyed silk showed good rate at 94.7% while cotton showed 68.5% for K. pneumoniae. Although there were some differences in the rate of bacteriostatic reduction depending on the bacteria, overall strong antibacterial property of NE dyed fabrics was confirmed as expected from the strong antioxidant property of NE.
Test fabric | Bacterial reduction rate (%) | |
---|---|---|
Staphylococcus aureus | Klebsiella pneumoniae | |
Silk | 99.9 | 94.7 |
Cotton | 99.9 | 68.5 |
4. CONCLUSION
When P. radiata bark was extracted with 0.8% NaHCO3 solution, the extract was 44% and its pH was almost neutral of 6.6. NE was mainly composed of PA and its content was 87%. The appropriate NE dyeing concentration of silk and cotton fabrics was 1.5% with a fabric to liquid ratio of 1 : 50, dyeing temperature of 90℃, and dyeing time of 90 min. The color of the dyed silk and cotton fabrics ranged between 2.5 – 3.0 YR (brown) and 4.1 – 4.7 YR (light brown), respectively. Dyed silk and cotton showed good colorfastness in terms of washing and rubbing, but not in light fastness. Dyed silk had excellent ammonia deodo-rization rate (99% after 120 min) and the dyed cotton had a constant deodorization rate of 80% regardless of time. Dyed silk and cotton exhibited antibacterial activity with a reduction rate of 99.9% against S. aureus. NE had strong antibacterial activities and deodorization properties, so it was thought to be used as a natural brown dyestuff and could be applied as a functional underwear and beddings for the children and elderly. Further studies will be needed to improve the affinity between the cotton fabric and NE to extend its usability.