1. INTRODUCTION
The South Korean government has proposed a 31% reduction in greenhouse gas (GHG) emissions by the end of 2020. One of the strategies for achieving this ambitious goal is the construction of green buildings by strengthening energy standards for new buildings, and promoting energy efficiency improvements for the existing ones. The development and manufacture of super-insulation materials is vital to achieve this goal. Currently, petroleum- and chemical-based insulation materials, such as styrofoam and urethane foam, are the most widely employed in the domestic insulation market in South Korea. These materials suffer from a number of disadvantages, including poor biodegradation and the associated pollution issues upon disposal. However, the use of wood resources is necessary to promote the recycling of forest resources and the long-term storage of carbon under the GHG-reduction policy and new climate system (i.e., post-2020) reduction target under the Framework Act on Low Carbon, Green Growth. In addition, the law surrounding the sustainable use of wood (Korean Law no. 16711 2020) must reconsider the value of timber resources and expand the utilization of unused domestic wood resources to support the policy of promoting domestic timber for revitalizing the timber industry. In this context, the development of safe and reliable methods for the mass production of eco-friendly raw materials by utilizing domestic wood resources and manufacturing bio-composite materials is essential.
In 2019, South Korea's total timber imports were approximately 2.6 million m3, and more than 75% of them constituted radiata pine (Pinus radiata; KFS, 2020). In the wood-related industry, tree bark, which makes up 9 to 15% of the total wood employed, is treated as waste, and is typically collected in the wood peeling process for use as a fuel resource or for mulching. To date, various studies have utilized pine bark and wood resources for cosmetics and medical purposes (Mun, 2008; Mun et al., 2010; Kim et al., 2018; Nam et al., 2018; Masendra et al., 2019). In South Korea, the applicability of mulching agents (Park et al., 2014), heavymetal adsorbents (Song et al., 2009; Mun et al., 2010), and dye stuffs (Mun et al., 2010) has been examined. Polyphenols comprise 50 to 60% of these pine barks, and proanthocyanidin (PA), which can be extracted using hot water, is the most important constituent (Ku et al., 2007). PA is a catechin-based polymer comprising a large number of hydroxyl groups. The structural properties of these polyphenols originating from pine bark render them suitable substitutes for the polyols used in the production of bio-foams. Indeed, a variety of approaches have been employed to add value to wood and bark extracts, for example, to use them in foam manufacturing (Tondi et al., 2008; Zhou et al., 2013; Basso et al., 2014).
The transition from bark and waste wood to petroleum- based insulation materials would contribute greatly to the economy and the environment in countries such as Korea, where the majority of wood is imported. The development of cost-efficient methods for the extraction of polyphenols from pine bark is essential. The purpose of this study is to establish a cost-efficient and effective method for the extraction of polyphenols from pine bark, in addition to determining their utility as raw materials in bio-foam manufacturing through structural analysis.
2. EXPERIMENTAL
The radiata pine bark was collected from a lumberyard in Unid Co., Ltd. (Gunsan-si, Korea), and the dirt, scales, and inner barks were removed from the raw bark. The bark was then ground to a particle size of ≤ 1 cm and processed using a high-speed grinder to give a powder with a particle size of ≤ 1 mm. The prepared bark powder was stored at 4 °C. A NaOH solution (93%) was used for alkali extraction of the polyphenols from the bark. All chemicals employed herein were of American Chemical Society (ACS) grade and were purchased from DaeJung Chemical & Metals (Sihungsi, Korea) and Sigma-Aldrich (St. Louis, MO, USA).
The prepared bark powder (150 g) was sieved to give samples of 5 different mesh sizes, i.e., 40, 40 to 80, 80 to 100, 100 to 200, and 200 mesh. The hot water and 1% NaOH extracts were prepared using TAPPI test methods (T-207 cm-99 2008; T-212 om-02 2002), and ash and total lignin contents were determined (TAPPI T-211 2002; T-222 om-11 2011). However, the lignin content of the pine bark obtained using the Klason method was overestimated due to the presence of polyphenols. Therefore, the bark polyphenols were initially removed (obtained) by extraction with 1% NaOH, and thereafter the polyphenol-corrected lignin value was determined using the residues obtained following 1% NaOH extraction.
A NaOH solution was used for extraction of the bark polyphenols. The alkaline extraction conditions were optimized by studying various extraction parameters, such as the bark-to-NaOH ratio, the liquor ratio, and the extraction time. All experiments were carried out using 1 g (o.d.) samples of radiata pine bark. Initially, the samples were extracted using 1% NaOH solutions in ratios (w/w) of 6.25, 12.5, 25, and 50 to the bark weight, and the yields of the 1% NaOH extracts were determined along with their pH values. Subsequently, the amount of NaOH used for the extraction was fixed, and the yields of the NaOH extract were studied as a function of the liquor ratio. In addition, using a fixed concentration of the NaOH, the NaOH extract yields were measured at different extraction times (5 to 120 min). Finally, the extraction yield and pH were measured upon variation in the NaOH dose (12.5, 17, or 18%) at a fixed extraction time (1 h) and fixed liquor ratio (5).
One milligram of each freeze- and vacuum-dried extract (either hot water or NaOH extract) was mixed with KBr (100 mg) and ground in an agate mortar to prepare a powder that was used to prepare a thin disc. The prepared sample disk was mounted on the device and was scanned 10 times in a range of 400 to 4000 cm−1 using an FTIR spectrophotometer (8201 PC, Shimadzu, Kyoto, Japan) to obtain the transmission spectrum.
The samples obtained after neutralization of the NaOH extracts contained large amounts of salt, and were barely soluble in the acetone-d6/D2O solvent system used for 13C NMR analysis. Therefore, desalting was performed using a cation-exchange resin (Amberlite IR 120 H, Alfa Aesar, Haverhill, MA, USA) to ensure complete dissolution of the sample. The desalted solutions were lyophilized, and a sample (100 mg) of the resulting powder was dissolved using a ~1:1 ratio (v/v) of acetone-dd6 to D2O in a 10 mL conical flask. The sample solutions were transferred to 1.7 mL microtubes and subjected to centrifugation at 15,000 rpm for 10 min at 20 °C. The resulting solutions were passed through a pipette containing glass wool and transferred an NMR tube. For comparison, the hot water extracts were taken up in a ~1:1 mixture (v/v) of acetone-dd6 and D2O, filtered, and transferred to an NMR tube. The samples were analyzed using a 400 MHz NMR spectrometer (AL-400, JEOL, Tokyo, Japan) in the center for university-wide research facilities at Jeonbuk National University.
3. RESULTS AND DISCUSSION
Table 1 shows the chemical composition of the radiata pine bark sample in terms of ash, hot water extract, 1% NaOH extract, and Klason lignin contents (before and after 1% NaOH extraction). The contents of ash, hot water extract, and Klason lignin after 1% NaOH extraction (polyphenol-corrected lignin content) were 0.70, 28.42%, and 14.44%, respectively. The 1% NaOH extract yield was 69.60%, and the polyphenols content was 51.88%. The polyphenols were calculated by subtracting the Klason lignin after 1% NaOH extraction from the Klason lignin before 1% NaOH extraction. Polyphenols represented 75% of the 1% NaOH extract. Because the majority of polyphenols present in radiata pine bark were extracted by alkali (Ku et al. 2007), the content of 1% NaOH extracts can be used as a measure of the total polyphenol content.
Ash (%) | Hot water extract (%) | 1% NaOH extract (%) | Polyphenols (%) | Klason Lignin (%) | |
---|---|---|---|---|---|
Before 1% NaOH extraction | After 1% NaOH extraction | ||||
0.70 | 28.42 | 69.60 | 51.88 | 66.32 | 14.44 |
The sample powders were separated according to their particle sizes using 40-, 80-, 100-, and 200-mesh sieves. As shown in Table 2, the 80 to 100 mesh particles (150 to 180 μm, 40.4%) were the most dominant in the raw radiata pine bark powder. The 1% NaOH extract and total lignin (Klason lignin plus acid-soluble lignin) contents of the bark powder were also determined, and the results are presented in Table 2. As the particle size of the radiata pine bark powder decreased, the amount of 1% NaOH extract increased, while the Klason lignin and acid-soluble lignin contents decreased.
The optimum particle size required for efficient bark extraction was determined from the extraction yield. Higher particle sizes, i.e., powders that passed through the 80 mesh sieve, showed polyphenol contents of ≥ 70% based on the 1% NaOH extract content (Table 2). The raw bark powder (i.e., non-sieved bark powder) consisted of ≥60% of these particles, with only 6.4% of the powder failing to pass through the 40 mesh. In addition, the powder that passed through the 200-mesh comprised of 86.62% of 1% NaOH extract, which indicated that this powder size was superior in terms of bark polyphenol extraction. However, the total content amounted to only 10% of the total bark. Overall, these results suggest that the powder obtained by the passing through the 1 mm sieve is suitable for the extraction of polyphenols from radiata pine bark.
The extraction of polyphenols from radiata pine bark is facile using an alkali solution (Ku et al., 2007). Thus, the optimal and most economic alkali extraction conditions to obtain extraction yields of ≥ 60% were determined. Fig. 1 show the extraction yields obtained using different ratios (w/w) of the 1% NaOH solution (i.e., 6.25, 12.5, 25, and 50) to extract 1 g of the bark powder.
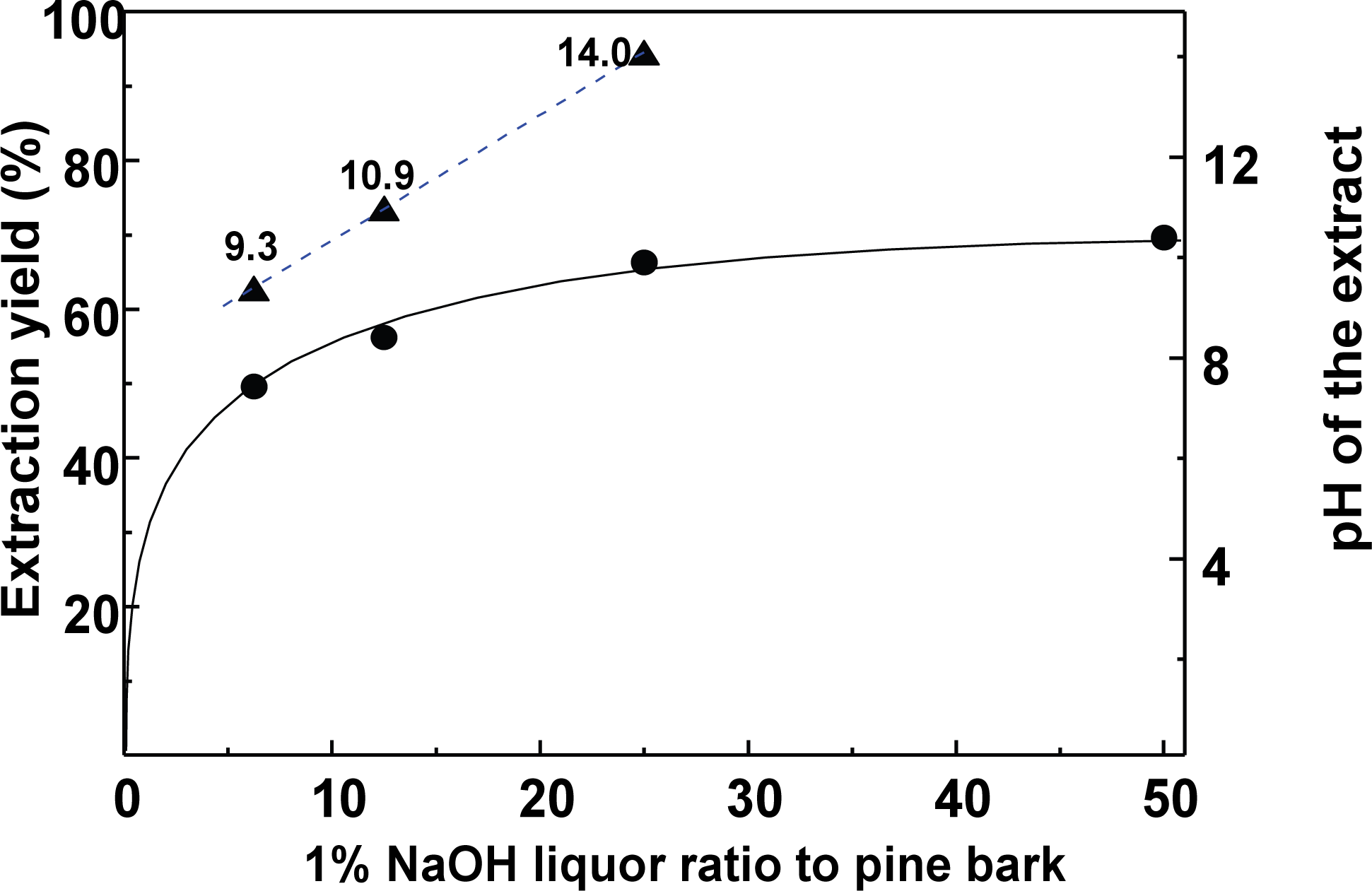
The extract yields increased upon increasing the ratio of the 1% NaOH solution, which was attributed to an increase in the amount of NaOH present in solution. Using a ratio of 12.5, an extraction yield of 56% was achieved, along with an extract pH value of 10.9, while a ratio of 25 gave a yield of ~66% and a pH of 14. It was apparent that the extraction yield and pH were dependent on the total amount of NaOH added. The ratio of 12.5 was considered optimal, despite the target goal not being reached. Next, the effect of the extraction yield upon variation in the liquor ratio with fixed amount of NaOH (i.e., 0.125 g) was investigated.
As outlined in Table 3, when the NaOH amount was fixed and liquor ratio was the only variable, the extraction yield was determined. Even upon increasing the extraction liquor ratio, the extraction yield remained almost constant at 56 to 57%, indicating that the efficiency of the bark extraction was completely dependent on the weight of NaOH employed. This indicates that polyphenol extraction from the pine bark was greatly dependent on the amount of NaOH present in solution.
Liquor Ratio (w/w) | NaOH (g) | Extraction Yield (%) |
---|---|---|
5 | 0.125 | 56.99 |
6.25 | 57.37 | |
8 | 56.93 | |
12.5 | 56.20 |
Because the extraction yield was greatly dependent on the alkali concentration, in consideration of the economic efficiency, the extraction liquor ratio was examined using a lower liquor ratio of 5 to determine its influence on the extraction time. The liquor ratio and the amount of NaOH were fixed at 5 and 12.5% relative to the bark weight, respectively, and the variation in extraction yield with the extraction time was examined.
As shown in Fig. 2, approximately 52% of the extract (i.e., containing the polyphenols) was extracted within 5 min, and the extraction equilibrium was reached within 20 min. However, in the extraction of large quantities of bark polyphenols, an extraction time of 1 h would be recommended.
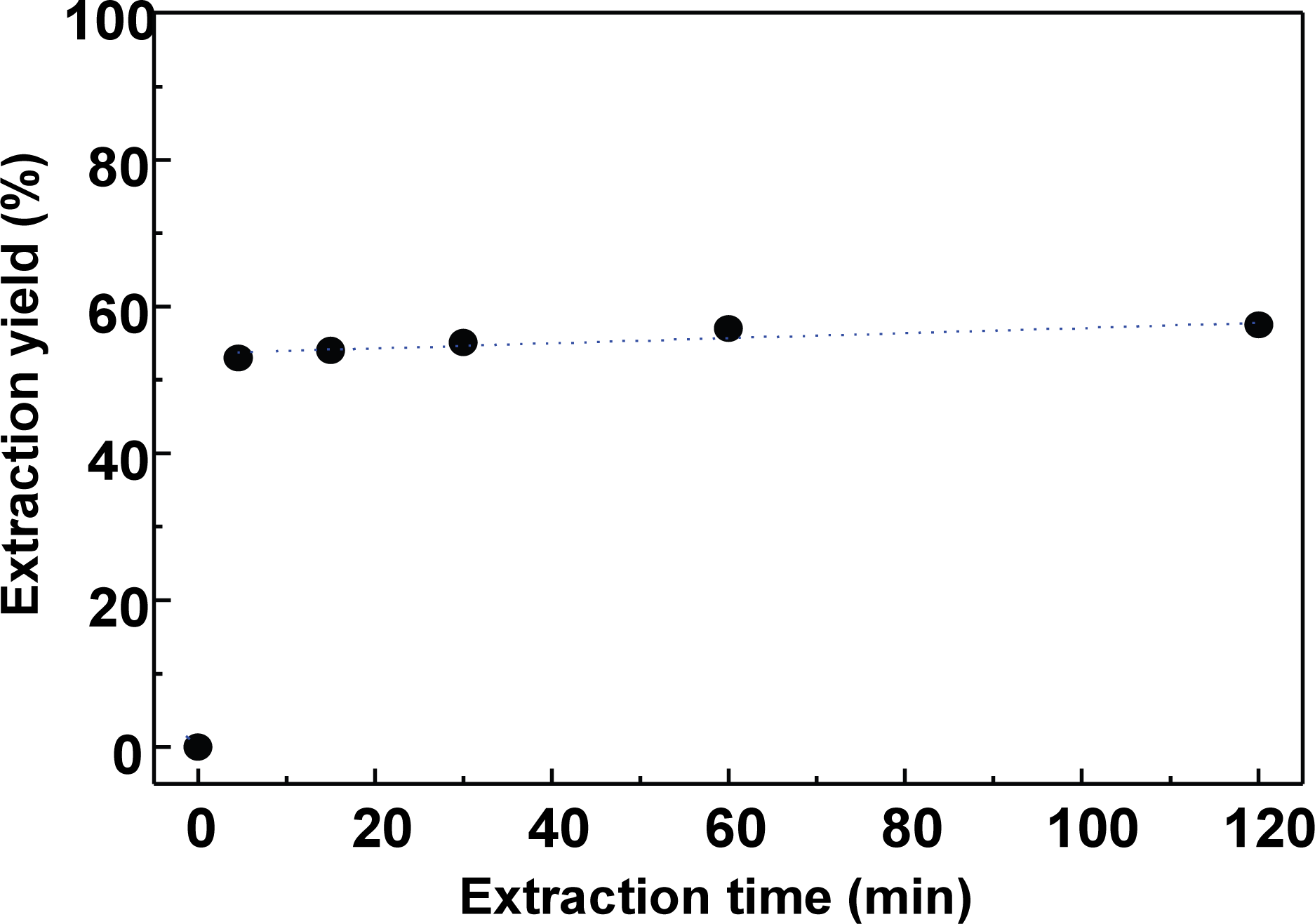
It should be noted here that the purpose of this study was to obtain suitable conditions to obtain >60% of extracts, so the amount of NaOH required to achieve this target was investigated. Thus, with an extraction time of 1 h and a liquor ratio of 5, the extraction yield and extract pH were determined. As presented in Table 4, when 17 and 18% of NaOH relative to the bark weight were used for the polyphenol extraction, yields of 61 and 62% were obtained, in addition to pH values of 11.9 and 12.1, respectively. Therefore, to obtain the targeted yield of >60% and pH value of 11 to 12, the optimum extraction conditions were a liquor ratio 5, 17 to 18% NaOH, an extraction temperature of 100 °C, and an extraction time of 60 min.
Liquor ratio | NaOH (g) | Extraction time (min) | Extraction yield (%) | pH |
---|---|---|---|---|
5 | 0.125 | 60 | 56.99 | N.D |
0.17 | 60.91 | 11.9 | ||
0.18 | 62.26 | 12.1 |
Fig. 3 shows the IR spectra of the reference hot water extract and the neutralized sample after NaOH extraction. In the case of the hot water extract, absorption bands indicating the presence of polyhydric flavonoids were found at 3368, 1612, and 1067 cm−1, while bands at 1530 and 780 cm−1 indicated the presence of hydroxyl groups in the B-ring of the flavanol moiety (Yazaki and Hillis 1977; Sotoet al. 2005).
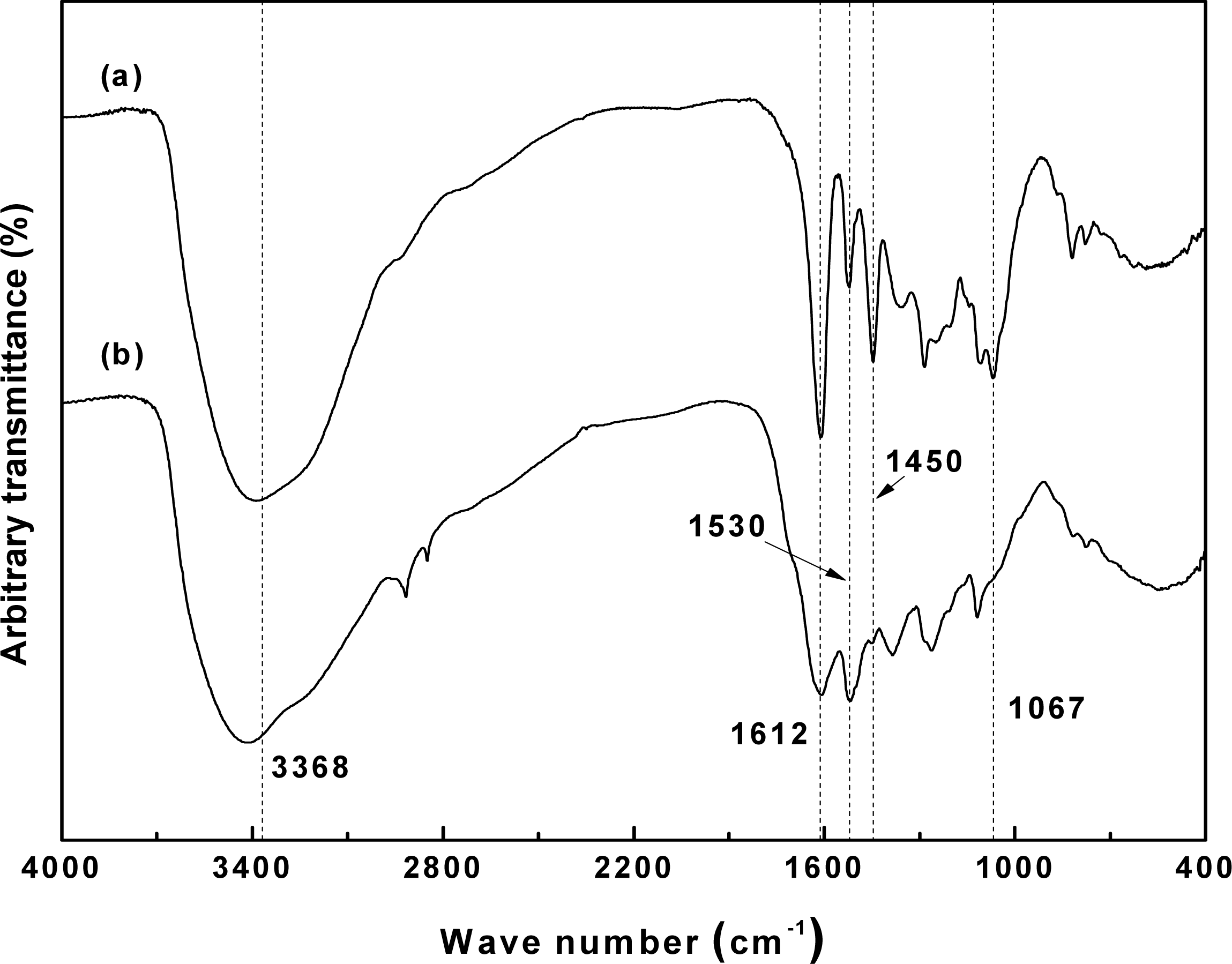
However, the neutralized extract displayed considerably weaker absorption bands, with the exception of that at 3368 cm−1, which was caused by the severe denaturation of the bark polyphenols. These observations concur with the report by Basso et al. (2014), whereby phlobaphene generation, rearrangement, and condensation reactions occur during the extraction process of pine bark.
For NMR analysis of the bark polyphenols, the majority of samples exhibited a good solubility in a mixture of deuterated acetone and D2O. However, after dissolution of the neutralized extract in D2Obut upon the addition of deuterated acetone, neutral salts in the sample were precipitated. To address this issue, the mixture was heated to improve the sample solubility. Upon cooling, some precipitation occurred, and the viscosity increased, thereby rendering transfer of the solution to the NMR tube challenging. Thus, the precipitate was instead removed by centrifugation, and the supernatant was subjected to 13C NMR analysis. However, no peaks were obtained, so the neutralized extracts were desalted by passing through a cation exchange resin. The desalted samples were dissolved in acetone-d6/D2O solvent systems, and some remaining precipitates were removed by centrifugation. The 13C NMR spectra of the obtained samples are shown in Fig. 4, whereby the asterisk (*) in Fig. 4(b) represents the peak corresponding to the peak of the reference hot water extract. Fig. 5 shows the chemical structure of proanthocyanidin from radiata pine bark.
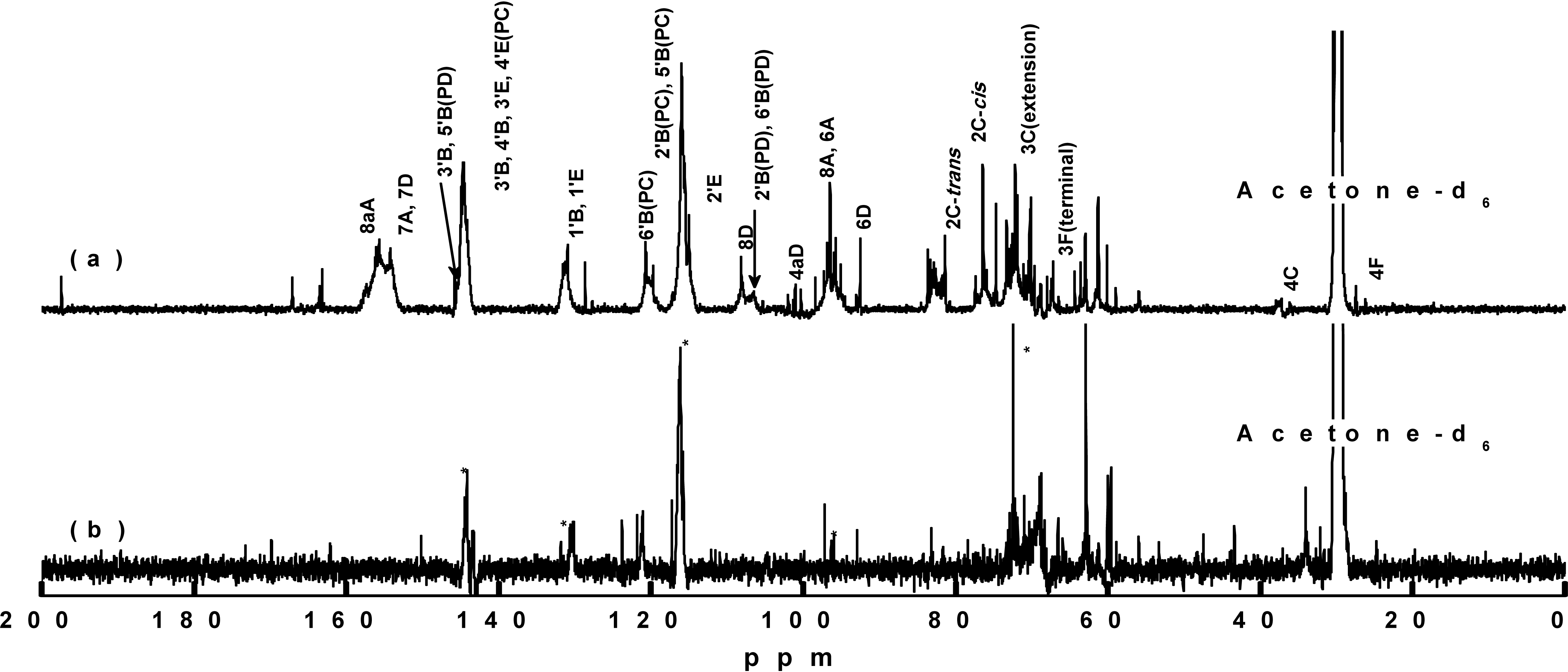
The 13C NMR spectra of the two samples were analyzed based on the previous reports (Czochanska et al. 1980; Porter et al. 1982; Davis et al. 1996), and peaks corresponding to procyanidin (PC) and prodelphinidin (PD) were identified for the neutralized extract. The peaks observed at 116 ppm (2'B, 5'B), 120 ppm (6'B), and 145 ppm (3'B, 4'B, 3'E, 4'E) indicated the existence of PC units in the PAs. All three peaks were observed in the reference hot water extract sample, but only those at 116 and 145 ppm were observed in the neutralized extract. Peaks corresponding to the 6A, 8A, 1'B, and 1'E carbon atoms were observed, and no other peaks associated with PAs were found. These results indicated that some low molecular weight products resulted from severe chemical modifications of the bark polyphenols during the alkali extraction process, which correlates with the above-described IR spectroscopy observations.
4. CONCLUSIONS
The use of alkaline extract from radiata pine (Pinus radiata) bark as raw materials for bio-foams is of current interest. Through this study the optimal conditions for the mass extraction of polyphenols from radiata pine bark was determined. The optimal extraction conditions were a liquor ratio of 5, a 17 to 18% ratio of NaOH based on the bark weight, a temperature of 100 °C, and an extraction time of 60 min. Under these conditions, the yield of the alkaline extract obtained from the pine bark powder was ~60%, and its pH value was ~12. Structural analysis of the alkaline extract prepared using these optimized conditions indicated that significant chemical modification took place in the bark polyphenols during alkali extraction. The alkaline extract of radiata pine bark was barely soluble in the solvent employed for structural analysis due to the condensation reactions and structure rearrangements that took place during the alkali extraction process. For the production of bio-foams, chemical modification is required to increase the solubility of the alkaline extract in polyol. In the future study, chemical modification, such as hydroxypropylation, of extract or development of a new alkali extraction method should be conducted. Then, the alkaline extract could be used to prepare the bio-foam as substitution of polyol.