1. INTRODUCTION
As a result of an increasing interest in the environment, such as climate change and certified emission reduction (CER), both in Korea and around the world, the attention and demand for wood, which is an ecofriendly and sustainable material, are increasing as well. Unlike other materials, wood has higher specific strength, is easy to process (including cutting and bonding), and acts as an insulator against electricity, sound, and heat. However, wood has its weakness in that it changes in size and/or decays when exposed to humid conditions. Because wood is a hygroscopic material, it always contains some moisture in its natural state. The moisture in the wood affects its properties; in particular, itis directly involved in the dimensional change of wood. In other words, when the amount of moisture in the wood increases, the wood swells, and when it decreases, the wood shrinks. This change in the dimension of wood serves as a disadvantagethat hampers the structural stability of the wood in use. Therefore, there have been a variety of studies to reduce these dimension changes of wood in accordance with its moisture content.
Heat-treatment of wood is a process that involves applying heat ranging 160–260°C to improve its physico- mechanical properties and resistance against wood rot fungi (Militz, 2002; Park et al., 2014). Various heat-treatment methods have been studied and their effects have been evaluated (mainly in Europe) because of the advantages of improved durability in an environmentally friendly method. Numerous studies have reported that heat-treatedwood has enhanced hydrophobicity, which leads to improved dimensional stability, darkened surface color, and increased decay resistance against various fungi, bacteria, and insects. (Cho et al., 2015; Esteves et al., 2008; Kang et al., 2018; 2019; Kim, 2016; Kim and Kim, 2019; Kim et al., 2018; Lee and Lee, 2018; Park et al., 2012; 2014; 2015; 2016; 2018; Repellin and Guyonnet, 2005; Yoon et al., 2008; 2009). These characteristic changes enable the application of heat-treated wood for different uses that require dimensional stability or biological durability such as outdoor furniture, fences, columns, cabinet, window frame, doors, decks, exterior, and floors (Boonstra et al., 1998; Esteves and Pereira, 2009; Kim, 2016).
The changes in wood properties due to heat-treatment depend on the temperature, duration, and heattransfer media of heat-treatment (Kim, 2016). Specifically, as the heat-treatmenttemperature and duration are increased, the effect of heat-treatment improves. However, the relationship between the temperature or duration and the effect of heat-treatment is not linear; this makes it exceedingly difficult to identify heattreatment conditions (temperature, duration, etc.) that result in specific material properties. Accordingly, a lot of time and energy is used in the process of identifying the suitable heat-treatment conditions to achieve properties that meet the purposes of using heat-treated wood. To this end, this study aimed for presenting the measurements of swelling and anti-swelling effectiveness (ASE) in larch wood, which accounts for the majority of artificial coniferous forests in Korea, as basic database. In addition, this study attempted to analyze the causes of the changes in swellings by heat-treatment through observation of the cell-wall microstructure. To achieve this, changes in the cell-wall microstructure of larch wood heat-treated at 190°C and 220°C for 12, 18, and 24 hours were observed through scanning electron microscopy (SEM), and the amount of absorbed water, swelling, and ASE of the heat-treated wood were measured.
2. MATERIALS and METHODS
For this study, the lumber of larch wood (Larix kaempferi) that was sawn and dried in the Jungbu Lumber Distribution Center (Yeoju-si, Gyeonggi-do) of the National Forestry Cooperative Federation was purchased. The dimensions of the larch lumber were 50 mm (thickness; radial direction) × 150 mm (width; tangential direction) × 2,400 mm (length; longitudinal direction).
As shown in Fig. 1, depending on the heat-treatment duration, 2,400-mm long larch lumber was divided and cut into four sets: non-treated, 12-hour heat-treatment, 18-hour heat-treatment, and 24-hour heat-treatment. During heat-treatment performed by putting the other threesets excluding the non-treated set into the reactor, the experiment was conducted in a method such that each set was taken out from the reactor in accordance with the heat-treatment duration. The heat-treatment temperature was set to two conditions of 190°C and 220°C, and 12 lumbers were used for each heat-treatment temperature.
Changes in the cell-wall microstructure of wood by heat-treatment were evaluated. Some cubical specimens with a side length of 5 mm were made to avoid any knots or cracks from the middle of the lumber. The specimens were softened and oven-dried to remove moisture. Then, the specimens were coated with gold and their cell-wall microstructures were observed through 20-kV SEM (SEMCOX EM-30, COXEM, Korea).
The ASE of the heat-treated larch wood was measured according to the ASTM D4446 “Anti-Swelling Effectiveness of Water-Repellent Formulations and Differential Swelling of Non-treatedWood When Exposed to Liquid Water Environments.” However, because ASTM D4446 is for determining the ASE for different coating applications on wood specimens, the coating applications were replaced with heat-treatment conditions for this study. The specimen was made in the dimensions of 127 mm (length; tangential direction) × 38 mm (width; radial direction) × 6 mm (thickness; longitudinal direction) from the middle of the lumber and ten specimens were used for each heattreatment condition. The specimens were humidified in a room at a constant temperature of 23±2°C and a relative humidity of 50±5% until they reached the constant weight. The humidified specimen was immersed in distilled water for 30 minutes to absorb water and swell as shown in Fig. 2. The weight change in the specimen before and after immersion was measured to determine the amount of water absorbed by the specimen, and the tangential length of the specimen before and after immersion was measured using a swellometer to determine the swelling (β). In addition, the ASE was calculated using Equation (1) with swelling measurements of non-treated and heat-treated larch wood in each condition to quantify the effects of heat-treatment on the changes in wood dimensions.
where, βn indicates tangential swelling (mm) of non-treated wood, and βh indicates tangential swelling (mm) of heat-treated wood.
3. RESULTS and DISCUSSION
Figs. 3 and 4 show the graphs of temperature changes for the surface and core of the wood during heat-treatment at 190°C and 220°C, respectively. At the 6-hours into the process at both temperature conditions, the temperature on the surface and in the core reached the target temperature of 190°C and 220°C, and the temperature remained constant until the end of the process. The temperature difference between the surface and core did not vary significantly; thus, it is thought that the effect of heat-treatment would be similar for all the wood specimens. The moisture content was 0% at the end of heat-treatment.
Fig. 5 shows the 1,000-magnified cross-sectional SEM images of the non-treatedand heat-treated larch wood at 190°C and 220°C. For non-treated wood, the thick S2 layer in the cell wall was cut smoothly, while the ones in heat-treated wood specimens were cut roughly. Moreover, the cells were deformed out of the original shapes with breakages and dents, and the intercellular spaces were widened as though the cells were disconnected. These tendencies were more remarkable in the larch wood that was heat-treated at 220°C than in those heat-treated at 190°C. It is known that heat-treatment of wood results in the decomposition of hemicellulose, which is one of the major elements of cell walls,and the mass decreases as heat-treatment is continued (Kim, 2016; Park et al., 2017; Welzbacher et al., 2009). This pyrolysis of the major element of wood cell walls weakens the cell walls, causing rough cutting surfaces. Moreover, as hemicellulose is decomposed, the number of hydroxyl groups decreases. Accordingly, it is considered that the hydrogen bonds between cells weakened, disconnecting cells from each other, eventually widening the intercellular spaces.
Fig. 6 shows the results for the amount of absorbed water, swelling, and ASE measurements for different heat-treatment conditions. Table 1 shows moisture content of specimens before and after immersion. Both amount of absorbed water and swelling measurements tended to decrease as the heat-treatment temperature and duration increased. In heat-treated wood, the number of hydroxyl groups decreased, increasing the hydrophobicity (Esteves and Pereira, 2009; Kim, 2016; Park et al., 2014; 2015; 2016). Therefore, it seemed that as heat-treatment continued, the increasing hydrophobicity reduced the amount of absorbed water, which in turn decreased the swelling.
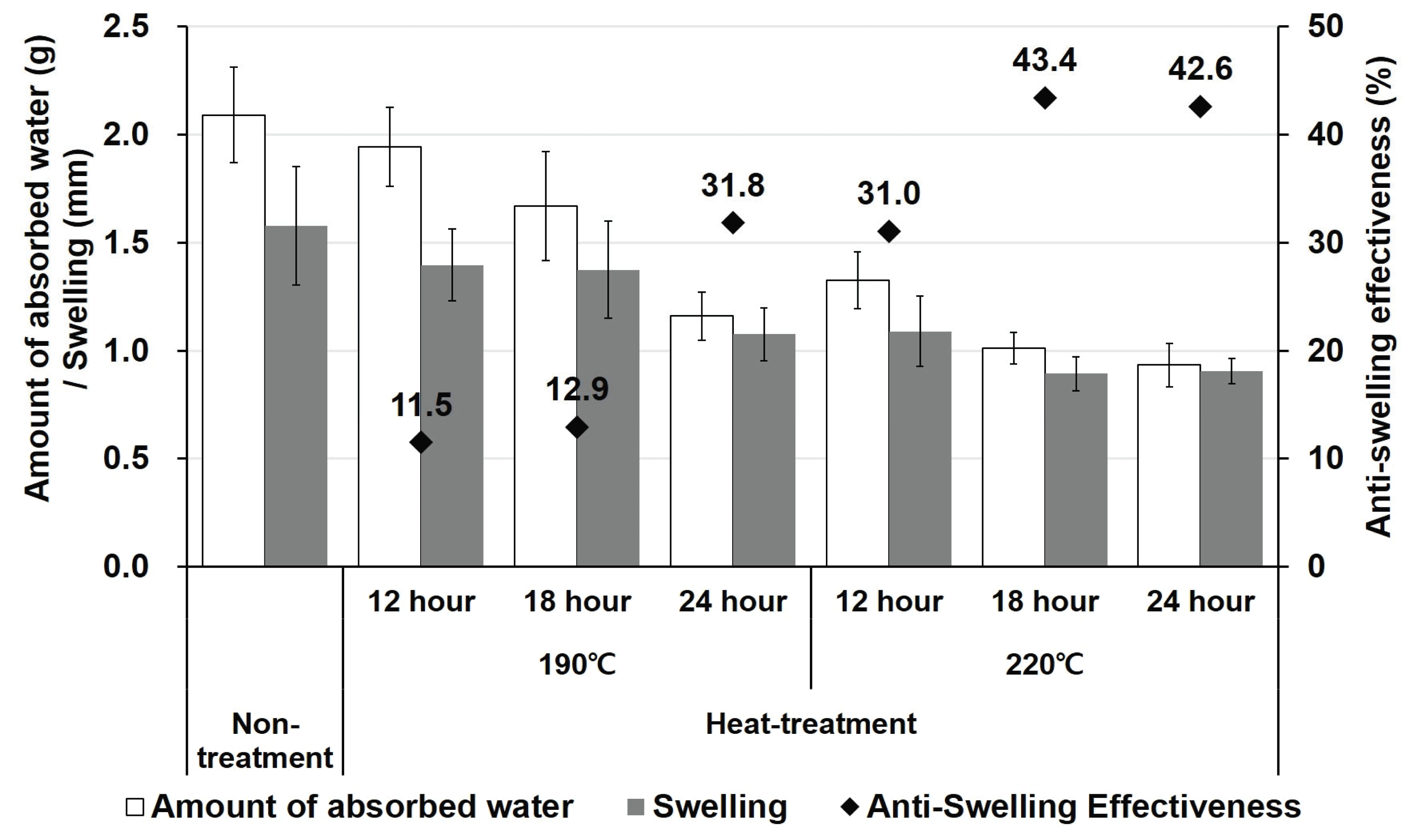
However, although the amount of absorbed water showed a tendency to decrease continuously as heattreatment continued, the swelling did not. The amount of absorbed water was largely affected by the chemical changes in wood caused by heat-treatment, while swelling was affected by the chemical changes as well as by physical changes such as the cell-wall microstructure. When wood is heat-treated, the amorphous regions of cellulose (where the moisture can penetrate into and cause swelling) decompose (Esteves and Pereira, 2009; Kim, 2016). Furthermore, if moisture penetrates the gaps (that have been widened due to heat-treatment) between the cells, the cell walls do not swell. This indicates that swelling is influenced by a combination of chemical changes such as an increase in hydrophobicity due to reduction in the number of hydroxyl groups and physical changes such as changed cell-wall microstructure.
The ASE showed similar tendencies with swelling. At 190°C heat-treatment, the ASE was similar for 12- hour (11.5) and 18-hour (12.9) heat-treatments; at 220°C heat-treatment, it was similar for 18-hour (43.4) and 24-hour (42.6) heat-treatments. Moreover, the ASE was similar for 24-hour heat-treatment at 190°C (31.8) and 12-hour at 220°C (31.0). The effect of heat-treatment increases both when the heat-treatment duration is increased while keeping the temperature constant and when the heat-treatment temperature is increased while keeping the duration constant. In other words, similar properties can be observed in case of heat-treatmentat lower temperatures for a longer duration and in case of heat-treatmentat higher temperatures for a shorter duration. Yang et al. (2018) applied the concept of heat-treatment degree to explain this, and Chung et al. (2019) conducted a study to quantify the heattreatment degree in a cumulative function. In this regard, heat-treatment at 190°C for 24 hours and the one at 220°C for 12 hours would have similar heat-treatment degree.
4. CONCLUSION
In this study, the cell-wall microstructure and ASE of heat-treated larch wood were evaluated, and the causes of change in the swelling with heat-treatment were anlayzed through changes in the cell-wall microstructure. As heat-treatment decomposed major element of cell walls, including hemicelluloses, cell walls wereweakened and cut roughly, resulting in failure to maintain their original shapes. In addition, the cells were detached from each other, which widened their intercellular spaces. These phenomena became more severe when the wood was heat-treated at higher temperatures. As the heat-treatment temperature and duration was increased, the amount of absorbed water and swelling decreased. However, the reduction in the amount of absorbed water was not proportional to the decrease in swelling because the decomposition of the major chemical element due to heat-treatment was not proportional to temperature or duration of heat-treatment. Moreover, there were additional effects such as the absorbed water was not bound within the cell walls but penetrated the widened gaps between the cells, failing to contribute to the swelling. Overall, the effects of decreased swelling and improved dimensional stability were considered to be associated with the increase in hydrophobicity and intercellular space due to decomposition of the cell-wall element.