1. INTRODUCTION
Wood is a renewable natural resource, abundantly available and serves various functions for human life, e.g., paper making, construction materials, particle boards, energy resources, and as raw material for various industrial needs. In general, there are two characteristics of wood, namely high-density and low-density wood.The low-density wood lacks strength and has low dimensional stability, thus limited in use. Most low-density wood is being used for fuel purposes; however, this type of wood can be used for other purposes (e.g., furniture, home construction, and office equipment) after the wood quality enhancement process such as the thermal compression (Lee and Lee, 2018), heat treatments (Priadi et al., 2019), Heat treatment and hygroscopic performance (Chang et al., 2019) and the polymer impregnation (Oh and Park, 2015).
The impregnation process can improve the wood mechanical properties by compacting the wood density to a higher level without damaging the cellular structures (Kamke, 2006), increasing resistance to termite attack (Arsyad et al., 2019). This process resulted in a better physical and mechanical wood properties compared with the immersion process (Hadi et al., 2019). Thus, the application of newly developed impregnation technology can expand the use of low-density wood for structural applications that were previously limited. A recent study reportedthat low weight phenol formaldehyde (PF) resins can be used to improve wood properties through impregnation (Izreen et al., 2011; Furuno et al., 2004; Shams et al., 2004; Hartono et al., 2016). PF resins can penetrate and swell the wood’s cell walls and increase the wood’s dimensional stability (Franke et al., 2017; Shams and Yano, 2004; Gabrielli and Kamke, 2010; Farmers, 1967), form the rigid cross-tissues in the drying process (Stamm, 1959), and reduce hygroscopicity (Hill, 2006). The impregnation and compregnation processes are the most commercially successful methods to increase the wood’s dimensional stability that resulted in up to 75 and 95% anti-swelling efficiency (ASE) at 35 and 30% weight gain (WPG) (Stamm, 1959).
PF penetration into the cell wall is a parameter of the impregnation effectiveness level. Furuno et al. (2004) reported that the wood cell walls can be well penetrated with low PF molecular weight (MN) with an average of 290-480. Meanwhile, a higher PF (i.e., 820 MN) is difficult to penetrate the wood cell walls, thus did not significantly affect the wood’s dimensional stability. A low molecular PF impregnation has a plasticizing effect on the wood’s cell walls (Shams and Yano, 2004). Therefore, the wood cell walls were not damaged when pressure applied during the PF impregnation process and subsequently cure PF in the wood cell walls (Furuno et al., 2004).
The PF impregnation process into the wood cell walls is one of the most effective ways to increase wood density which improves its physical and mechanical properties. For that reason, this study aimed to improve the physical and mechanical properties of a low-density falcataria woodto increase its utilization as one of the materials originated from renewable natural resources.
2. MATERIALS and METHODS
Falcataria (Paraserianthes falcataria(L) Nelson) wood was provided from the local source. Each wood specimens used for the physical and mechanical properties testing have the measurement of 20 mm × 20 mm × 300 mm and were free of defects referred to the British Standard for Testing Small Wood Specimens, BS-373: 1957. All samples were conditioned at 25°C and 65% RH up to constant weight before the impregnation process. The moisture content of the Falcataria samples was 12% with wood density ranging from 0.23 to 0.30 g/cm3. The phenol formaldehyde (PF) resin used has a solid content of 42.05% and an average molecular weight of 780 and was supplied by PT. Palmolive Indonesia (Table 1).
Resin Properties | Value |
---|---|
Viscosity @ 25°C(poise) | 2.27 |
Specific Gravity @ 25°C/4˚C | 1.200 |
Gelation Time 135˚C(min.) | 12’50’’ |
Resin Content @135°C(%) | 42.05 |
Molecular Weight (Mn) | 780 |
pH (meter/25°C) | 12.45 |
The impregnation process was carried out at room temperature and after the sample’s moisture content was stabilized at approximately 12%. Samples were placed in an impregnation chamber and vacuum-pressured at 50 cm Hg for 5 minutes. A load is placed on top of the test sample to prevent the sample from floating during the impregnation process. Then, phenol formaldehyde resin was inserted through available channels in the chamber until the test sample sank. The chamber was closed again and vacuum-pressed to 10 kg/cm2 with different timings accordingly. The samples were then removed from the chamber and the excess PF was removed from the sample surface.
Next, specimens were wrapped with aluminum foils and cured at 90°C for 24 h and conditioned at 25°C and 65% RH for 1 month until the moisture content stabilized. In every stage of the process, the specimens’ weight was measured to determine the polymer loading. The different treatment used were: a) concentration PF of 15% with various pressure time: 0, 15, 30, 45, 60, 90 and 120 minutes; b) pressure time 45 minutes with various concentration PF: 0, 5, 10,15, 20 and 25%.
The weight percent grain (WPG) after impregnation process was calculated as shown in the Equation 1.
WPG = weight percent grain (gr)
W0 = weight before impregnation (gr)
W1 = weight after impregnation (gr)
Beforetesting, the samples were conditioned in a room at a relative humidity of 65% and a temperature of 25°C. Dimensional stability was evaluated by thickness swelling (TS) and anti-swelling efficiency (ASE) by measuring the mass and volume changes before and after swelling. Each specimen was weighed and measured in thickness, width, and length to determine their volume. Ten samples with a dimension of 20 mm × 20 mm × 20 mm were soaked in immersion water for 24 hours to represent the swelling conditions. Samples’ weight and volume were then measured again. Thickness swelling (TS) was calculated using an average thickness measurementand represents the amount of swelling in wet conditions at 12% moisture content (Eq. 2). ASE was calculated using the formula described in Eq. 3.
where TS is volumetric swelling coefficient, V1 is volume after water test, and V0 is 12% MC volume after impregnation process.
where ASE is anti-swelling efficiency, S1 is volumetric swelling impregnated-wood specimen, and S0 is volumetric swelling coefficient of control specimen.
Modulus of elasticity (MOE) and modulus of rupture (MOR) were evaluated before and after the impregnation process using the bending strength tests following the British standard 373. The three-point bend test was carried out using a universal testing machine (UTM) by placing the load on the sample until the sample breaks. The loading speed was 10 mm/minute and supporting spans was 280 mm test sample. There were five replication samples in this test which were determined under an air-dried condition.
To identify the PF impregnation into the cell wall, random specimens were selected from each treatment and inspected visually by macro photographs (50× magnification) and observed by SEM analysis on the transverse surface.
The data gathered was analyzed using one-way analysis of variance (ANOVA) followed by Duncan’s multiple range test to analyze differences between levels. All statistical tests were carried out using SAS (SAS Institute Inc, 2004) at a 95% confidence level.
3. RESULTS and DISCUSSION
In general, the density increased alongwith increasing concentration PF and pressure time as shown in Table 2. Air-dry density values of the specimens ranged between 0.26 – 0.30 g/cm3 (Table 2). The density of impregnated wood was higher compared to control specimens. The impregnated wood with pressure time of 120 minutes had a WPG increase up to 7.12%. The 25% PF concentration also increased the WPG up to 10.53%. The combination of PF concentration of higher PF concentration and longer pressure time could increase the density of impregnated wood compared to control specimens. The increase of impregnated- wood density was probably related to the permeability properties of wood. The vacuum process during impregnation resulted in a higher wood porosity, thus it was easier for PF to penetrate the cell wall (Fig. 1).
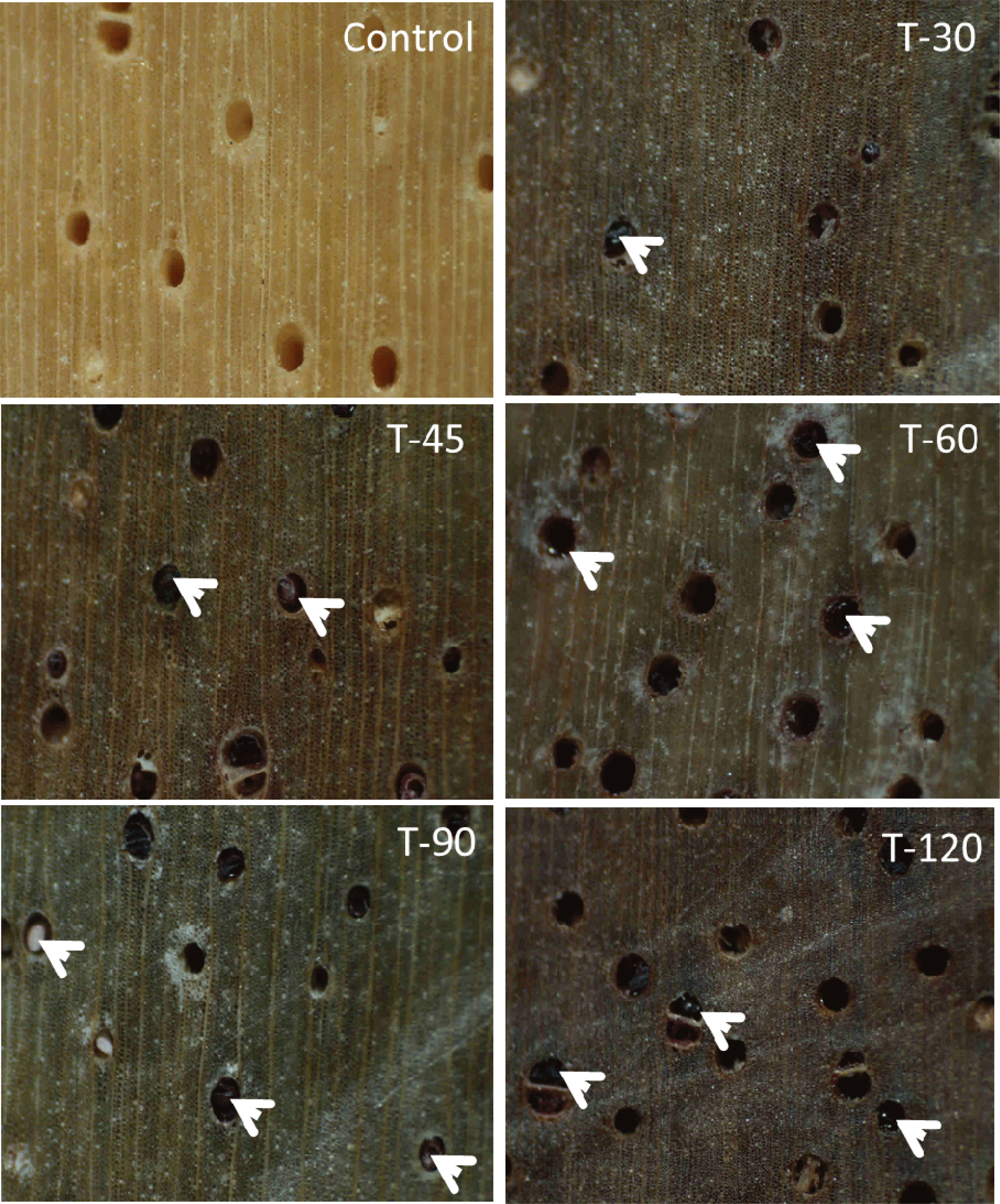
The stained wood cell walls (Fig. 1 T30-T120) indicate the presence of PF. The color difference made it easy to identify the PF penetration in the cell walls. The density of the impregnated wood increased, even with the use of high molecule PF. This result is contrary to a study of Furuno et al. (2004) where a high molecule PF cannot penetrate the cell wall.
Fig. 2 provides a qualitative SEM analysis of 15% PF at different pressure times. As shown in the figure, PF with high molecule weight could penetrate to Falcataria wood cell walls. The dark color was related to PF penetration into the lumen cell (Fig. 1). Several studies showed that high molecular weight PF resins can increase the dimensional stability of solid wood and composite wood, although the increase in stability was lower when using low molecular weight PF (Grinins et al., 2019; Biziks et al., 2019; Franke et al., 2018; Stamm and Baechler, 1960). Furthermore, Rowell (1999) suggested that low molecular weight resins are easier to penetrate the wood’s cell walls compared to high molecular weight resins, thus the wood becomes more stable.
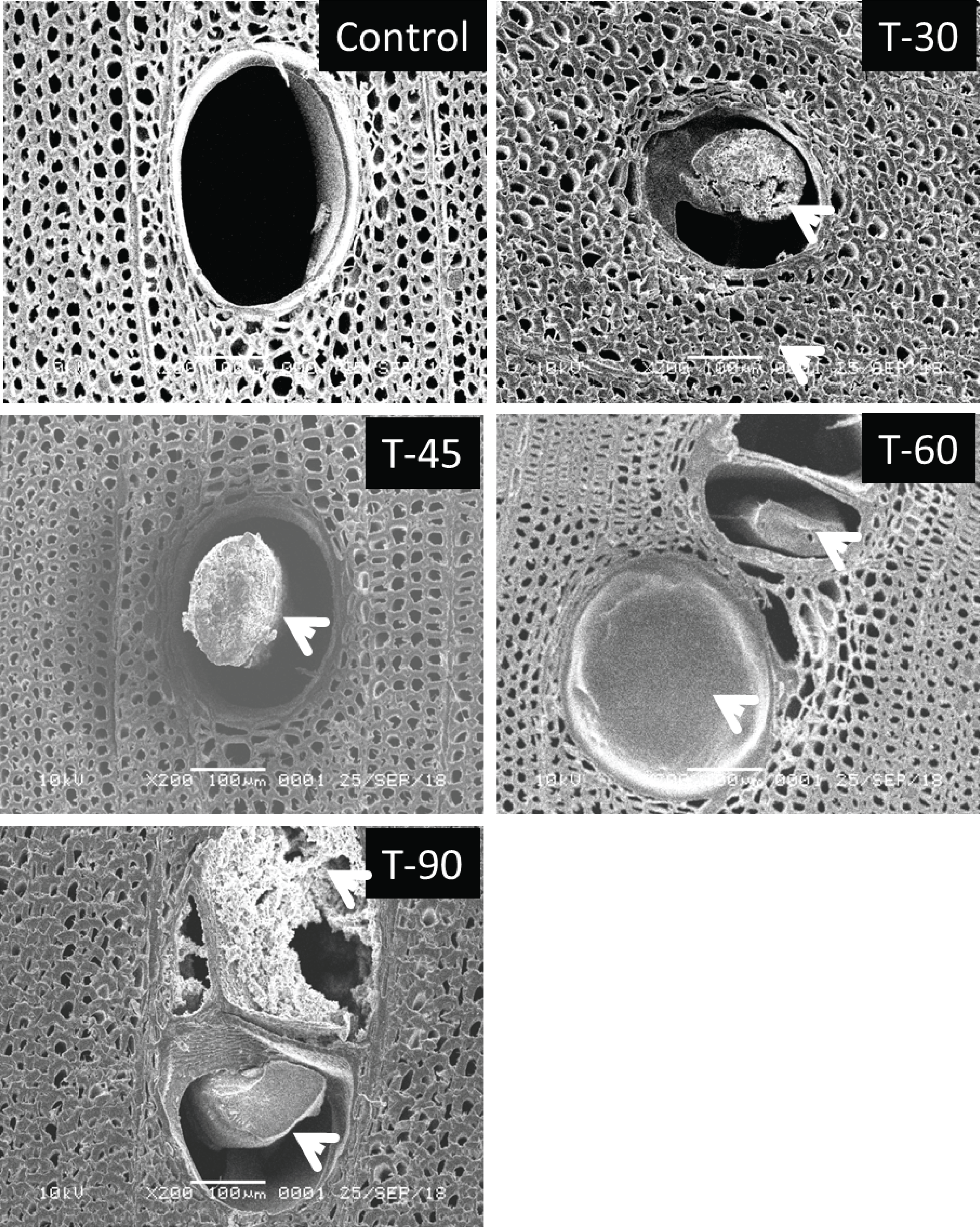
Dimension stability of impregnated wood was evaluated through TS and ASE tests. A Table 3 showed analysis of variance (F test) for TS. The concentration and pressure time are shown to have affected significantly at 99 and 95% confidence levels, respectively. According to Table 4 showed the TS results after the water immersion test. At 5% PF concentration, the average thickness swelling was 6.10%. However, as the PF concentration increases (10-25%), the increase in thickness (TS) was significantly reduced compared to control and 5% PF. The reduction of TS indicated the stability of impregnated wood. A 25% PF concentration could produce wood with good dimensional stability with an ASE value of 29%. This result indicates that a high molecular weight PF could be used for Falcataria wood impregnation and significantly increased the wood’s dimension stability at 99% confidence level (Table 3).
Treatments | Sum of Square | df | F value | sig |
---|---|---|---|---|
Concentration | 9.594 | 5 | 6.959** | 0.001 |
Pressure time | 2.832 | 6 | 2.851* | 0.005 |
The pressure time also affected TS and ASE in the same trend as the PF concentration. TS decreased with increasing pressure time, an indication that the wood stabilized more after a longer period of impregnation. In contrary to TS, ASE or stability dimension increased with increasing PF concentration. Fig. 1 showed macro images of impregnated wood at 15% PF concentration with different pressure times. A higher stability could be reached at a higher densification level (Table 2 and 4).
Wood specimens impregnated with PF for 120 minutes showed a darker color compared with the ones impregnated with shorter periods (i.e., 90, 60- and 30-minutes; see Fig. 1). This indicates that PF has successfully penetrated the compressed cells lumens, especially into the vessel cell. Indeed, wood samples with higher ASE values were obtained from a higher PF concentration and longer pressure time (Table 4).
In this study, the highest stability value was achieved at 45 minutes of pressure time and 25% PF concentration. This treatment was considered as an optimum impregnation condition which resulted in better physical properties and stability. A higher amount of PF entering the wood structure will trigger the wood's ability to expand again, a condition that could be maintained by curing PF resin. An explanation for this was offered by Shams et al. (2004) that mentioned the plasticizing effect of PF resins on wood cell walls. Therefore, the swelling ability can be reduced if the specimen was placed in a high moisture condition.
The young’s modulus (MOE and MOR) of impregnated wood was increased after being treated by different concentrations and pressure timesat various treatments (Fig. 3 and 4). The impregnated wood showed a higher MOE compared to the control specimen. The increasing pressure time affected young’s modulus up to 90 minutes and after that the value of young’s modulus was stagnant. Young’s modulus slightly increased gradually. This finding was also supported by density results (Table 2).
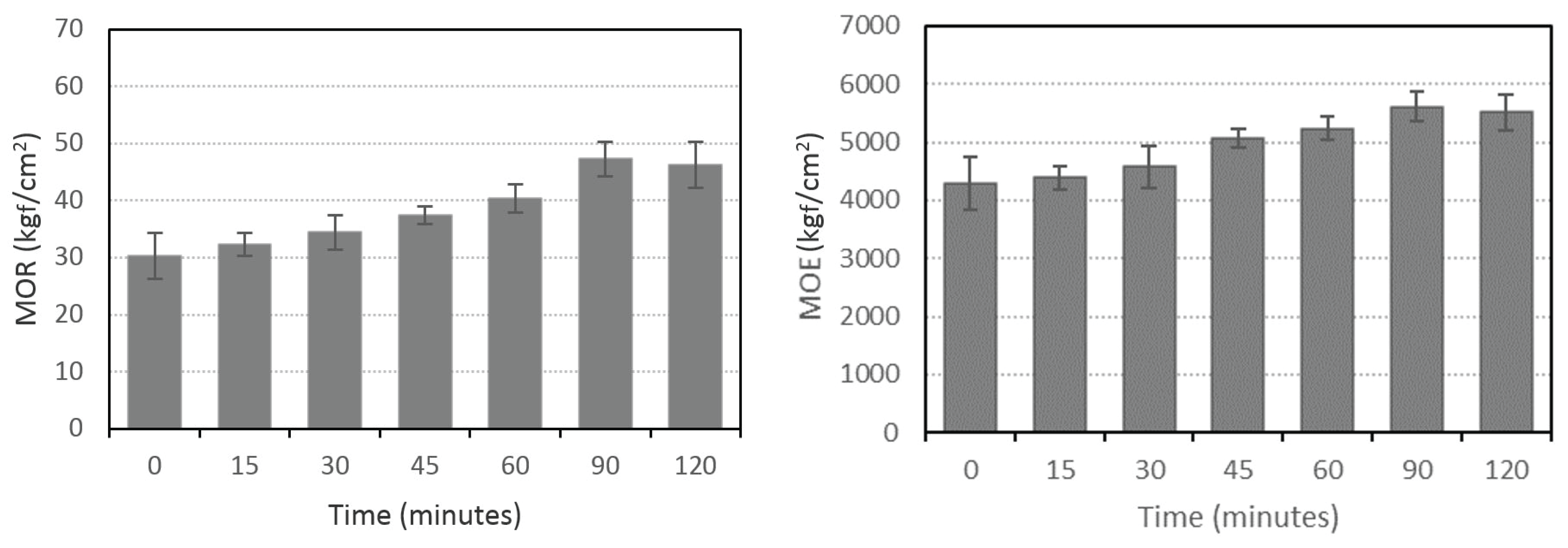
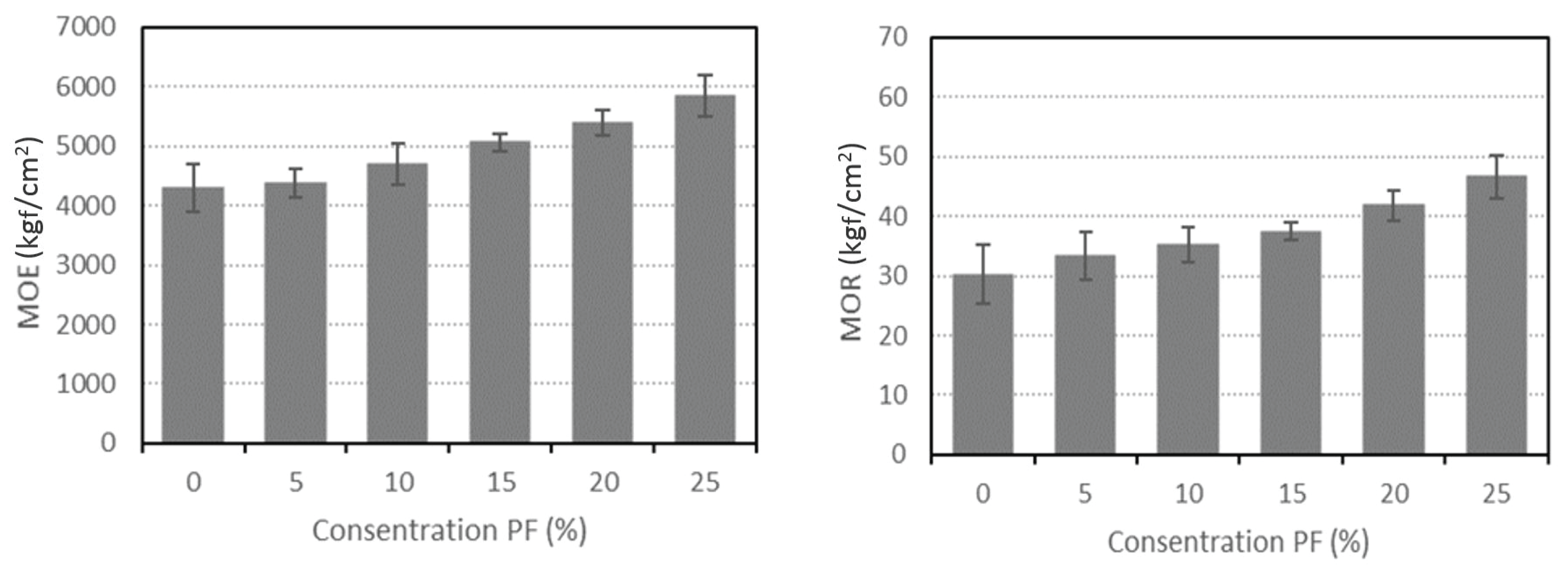
The effect of PF concentration on young’s modulus has a similar trend with pressure time. The MOE increased from 4200 kgf/cm2 to 5800 kgf/cm2 (Fig. 4) or increased 47% compared to the control specimen. The MOE strength was created by polymerization of PF resin bonding process after the curing process was successful. This property could influence the resin allocation into the cell wall (Fig. 2). Besides that, excess resin during the impregnation process may change the cell structure which was darker than the control specimen when the resin was forced to fill up the porous components. A possible explanation is a fact that a high amount of concentrated resin did not makethe samples brittle because WPG was only increased by 10% (Table 2). In general, high dimensional stability could be achieved by a high WPG by combining high PF concentration and longer pressure time. High WPG increased the wood’s mechanical properties due to the presence of PF in wood tissue which made it more rigid.
4. CONCLUSION
Dimensional stability and mechanical properties of Falcatariawood were successfully improved through the impregnation process using phenol formaldehyde resin. The impregnation process of PF was able to improve the mechanical properties and the density from 0.26 g/cm3 to 0.30 g/cm3 with only 10% weight percent grain. The dimensional properties improved along with increasing resin concentration and pressure time. A higher increase in Young's modulus was reached at the higher resin concentration levels. The darkened color of impregnated-wood was associated with more PF penetrated into the wood’s cells.