1. INTRODUCTION
As most of modern life is carried out indoor, and with problems related to indoor environment and interests in health of individuals, interests in eco-friendly construction materials of wood and wooden materials is increasing. Furthermore the wooden materials which were manufactured with conventional materials are slowly switching to eco-friendly materials that combined materials with functionality. In particular, research and development are being made on various eco-friendly materials that consider durability and functionality (Park et al., 2011, 2012; 2013; Ahn, 2009).
Charcoal is a standing out eco-friendly material which can be most easily accessed, and it has been utilized for various uses such as air purification, deodorization, and protection against gases, etc. from the past. As the advantage of an easy accessibility as well as other various functionalities such as deodorization, preservation, filtration, humidification, negative ion generating effect, and electromagnetic shielding, etc. have come to the fore, manufacturing and demand of charcoal are increasing accordingly. Thus, numerous studies are being conducted recently on charcoal as an important raw material for studies on the ecofriendly materials (Park et al., 2011, 2012, 2013; Ahn, 2009; Park and Park, 2011; Kim, 2017; Hwang and Oh, 2017, 2020). Chaff charcoal among other types of charcoal is a strong material for insulation, moisture control, negative ion generation, far-infrared radiation, absorbing toxic substances and odor, mothproofing, and also strong against decomposition in a level comparable to glass-wool insulator which is commonly used. Therefore studies are conducted to develop the chaff charcoal with its excellent insulation performance as an eco-friendly insulating material (Ahn et al., 2013; Lee et al., 2013). A large amount of approximately 1.1 million tons (which is equivalent to 20~25% of rice production) of chaff is used in manufacturing the chaff charcoal production each year in Korea. However, it is being problematic as its apparent density is 0.097~0.125 g/cm3, and it has a large volume when discarded. In addition, it also has a disadvantage where it cannot be disintegrated easily even after being buried due to its low caloric value and high ash content. Thus, it has been mainly used as agricultural compost, and desiccant at a pigsty, etc. (Baek et al., 1998; Kim et al., 2001). Moreover, with usingthe chaff as a material for manufacturing a wooden board, the moisture penetration rate is merely 1/3 of that of sawdust due to its surface covered with setae and siliceous. It also has a difficulty of commercializing in the field of wooden materials since it has poor plasticity and adhesiveness in contrast to lumber (Lee, 1999). However, based on the fact that chaff has about 40~50% of carbon component, and about 30~40% of silicon content, studies are being conducted recently on manufacturing activated carbon from a carbonized chaff and on ceramic made of sawdust and an agricultural by-product of chaff (Oh and Park, 2010; Oh et al., 2005). If the chaff charcoal manufactured by carbonizing the chaff is used as a rawmaterial of a wooden panel product for production, it is expected to achieve various effects such as increasing farm household income, substitution effect of importing lumber, and a large benefit in construction process.
In the meantime, for classification or grading of the lumber products, a nondestructive assessment technologyusing vibration or sound wave on lumber without altering the function of its final use is widely being used (Byeon et al., 2004, 2011; Jin et al., 2015). One method of assessments is using dynamic modulus of elasticity, and the dynamic modulus of elasticity is mostly estimated by measuring acoustic transfer speed or resonant frequency. The acoustic transfer speed can be estimated by using an impact hammer, and the resonant frequency can be estimated by frequency analysis of either vibration or impact hammer.
In this study the static modulus of elasticity, modulus of rupture, and bending strength of a chaff charcoal- sawdust compound board manufactured with differentiated additions of resin and sawdust are measured. Furthermore, it applied both-ends free bending vibration measuring method which is frequently used amongst nondestructive assessment methods to generate the resonant frequency. Then, the frequency was used to calculate the dynamic modulus of elasticity, and analyzed its relationship with the bending strength characteristic.
2. MATERIALS and METHODS
For the chaff charcoal used for manufacturing the board, the charcoal from Daewon GSI Co., Ltd. located in Gyeongsangbuk-do was used. For the sawdust, the dust emerged during the sawing process of pinus radiata was received from a sawmill and utilized. For the uniformity of the samplesat the time of manufacturing the board, the size of particles was selected as 10~20 mesh, and the moisture content was controlled below 9%. For the purpose of manufacturing the board, phenol-formaldehyde resin (Kolon Industries Inc., KNB-100PL) was used. The characteristics of the resin are shown in the Table 1.
Resin types | Powder resin (novolak type) |
---|---|
|
|
Items | |
Solid content (%) | 99 |
Melting point (°C) | 80-95 |
Celation time (sec.) | 80-120 |
Plate flow (mm) | 30-35 |
In order to manufacture the board, the phenol-formaldehyde resin was sufficiently combined with the uniformly selected chaff charcoal and sawdust. Then, it was inserted into a stainless square mold located on the plate of a thermal compressor. The height of the upper sample was adjusted consistently, and the sample was thermo-pressure molded to manufacture the board with the dimension of 260 mm × 260 mm × 11 mm. For the manufacturing condition of the board, the density was fixated to 0.6 g/cm3, the sawdust addition as 10%, resin additions as 10, 15, 20 and 25%, and density as 0.6 g/cm3, resin addition as 10%, and sawdust additions as 10, 15, 20, 25 and 30%, producing four boards for each condition, total of 36 boards. At this point, the thermo pressure temperature was set at 190°C, the pressure was set at 45 kgf/cm2 → 35 kgf/ cm2 → 20 kgf/cm2 (3-phase pressurization), and pressurization time as 6 minutes → 5 minutes → 4 minutes (3-phase pressurization time). In order to maintain a uniform thickness of the board during the pressurization process, a distance bar was used. Furthermore, a Teflon plate was used to prevent attachment of upper, lower surfaces of the board with the thermal plate due to the heat.
An accelerometer (B&K) for receiving vibration was attached in the middle of the specimen, and an impact hammer (Type 8203, B&K) was used to tap its one end lightly. Then, the frequency response function acquired from the impact hammer and accelerometer was analyzed using a FFT analyzer (Type 3065, B&K) to measure natural frequency (f0). Each specimen was lightly tapped 5 times, and an average natural frequency (f0) was used to calculate resonance frequency (f) which considered moment of inertia and shear impact, and this resonance frequency was used to estimate the dynamic modulus of elasticity (dMOE). The resonance frequency and dynamic modulus of elasticity were calculated by using the equation (1) and equation (2) (Kataoka and Ono, 1975).
Here, f0 refers to the natural frequency (the value obtained from the frequency analyzer), α is constant 8.2 by vibration form, h is the thickness of specimen, and l is the length of specimen. The value f, the resonance frequency corrected in the equation (1), was used in the equation (2) to estimate the dynamic modulus of elasticity.
Here, ρ refers to density, l is the length of specimen, f is resonance frequency, m is constant 4.73 by basic vibration, and h is the thickness of specimen.
The bending strength experiment for the manufactured board was performed according to Korean Industrial Standard KS F 3104-2016. Universal strength tester (Shimadsu, AGS-10 kN, Autograph) was used to measure it with the condition of load speed at 10mm/min, and the equations (3) and (4) were used to estimate static modulus of elasticity (sMOE) and bending strength or Modulus of Rupture (MOR).
Here, P refers to load, l is the length of span, b is the width of specimen, h is the thickness of specimen, and y is displacement.
Here, P refers to a maximum load, l is the length of span, b is the width of specimen, and h is the thickness of specimen.
3. RESULTS and DISCUSSION
The values of resonance frequency, bending strength, static modulus of elasticity, and dynamic modulus of elasticity of a board manufactured according to resin additions after fixing the density as 0.6 g/cm3, and sawdust addition as 10% were shown in the Table 2. When the resin addition of the chaff charcoal-sawdust compound board was gradually increased from 10% to 25%, the following ranges were emerged: 227.53~333.63 Hz for resonance frequency, 9.22~28.91 MPa for bending strength, 320.62~963.48 MPa for dynamic modulus of elasticity, and 92.06~322.92 MPa for static modulus of elasticity. Overall, it was indicated that resonance frequency, bending strength, dynamic modulus of elasticity, and static modulus of elasticity were all increased as the resin addition increased. This result showed a similar tendency with Kawai et al. (1986) who statedthat adhesiveness between samples were increased as the resin addition increased when manufacturing the board, as well as the study by Lee and Yoon (1994) and Oh et al. (2012) which stated that bending strength increased as the resin addition increased. Moreover, the bending strength of the board manufactured with the resin addition ratio of 15% satisfied KS F 3104 particle board’s quality standard 15.0 type, whereas the board manufactured with the resin addition ratios of 20% and 25% satisfied type 18.0. In the aspect of mechanical performance, the chaff charcoal-sawdust compound board manufactured with resin addition ratio of 25% seems to be an optimum condition.
Fig. 1 is the result of analyzing correlation between resin addition ratio, bending strength, dynamic modulus of elasticity, and static modulus of elasticity of the board with the aim of identifying the effect of resin addition ratio on strength performance of the chaff charcoal-sawdust compound board. A lineal correlation is made between resin addition ratio, bending strength, dynamic and static modulus of elasticity, and the coefficients of determination (R2) were 0.7474, 0.7363, and 0.7738. Thus, significance level of 1% was admitted and it was revealed that resin addition ratio was a major factor which largely effects the mechanical properties of the chaff charcoal-sawdust compound board. From this result, it can be determined that the dynamic and static modulus of elasticity, and bending strength can be predicted from the resin addition amount of the chaff charcoal-sawdust compound board.
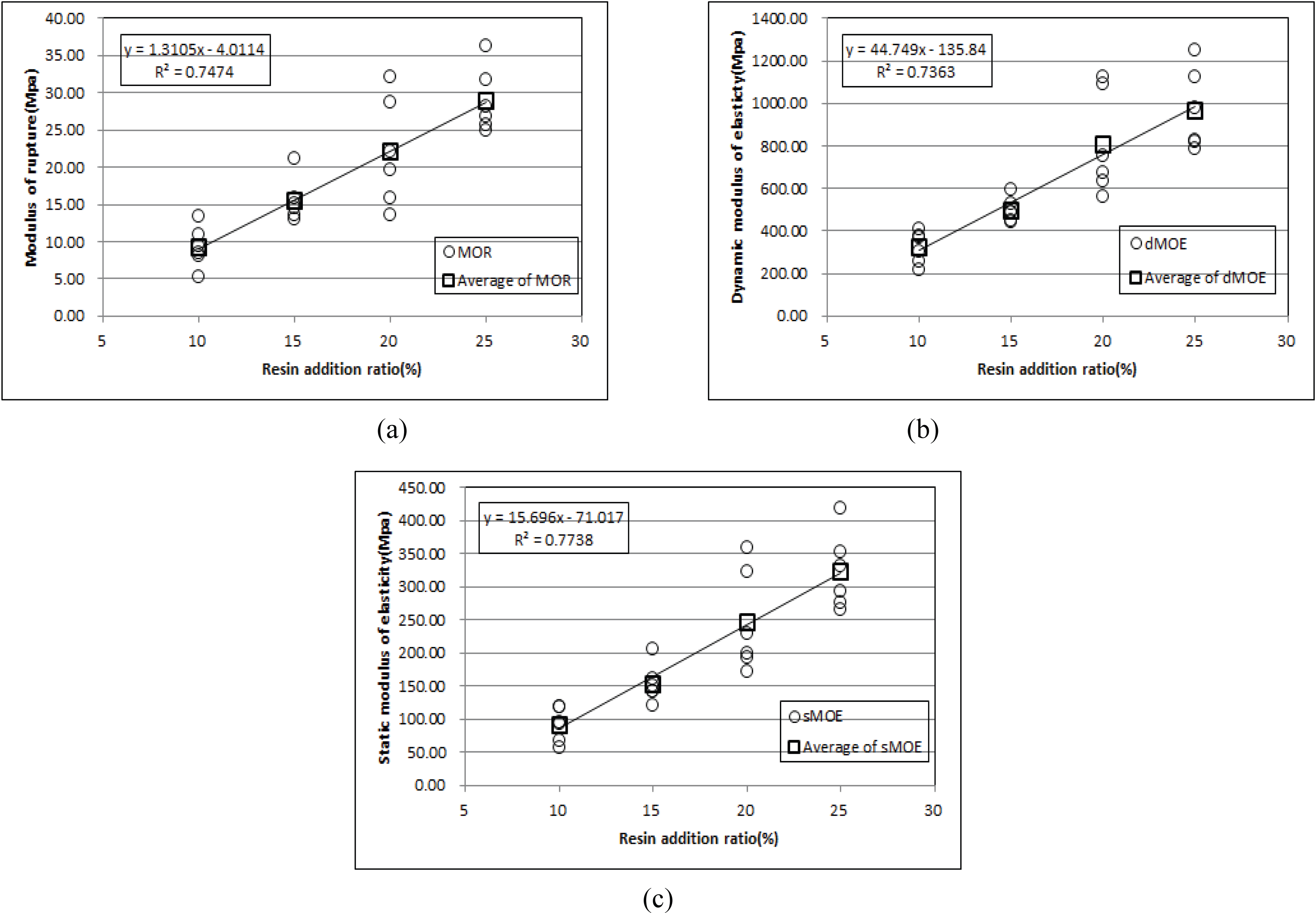
The values of resonance frequency, bending strength, static modulus of elasticity, and dynamic modulus of elasticity of the board manufactured according to sawdust addition with the density as 0.6 g/cm3, and resin addition as 10% were shown in the Table 3. When the sawdust addition ratio of the chaff charcoal- sawdust compound board increased from 10% to 30%, the following ranges were emerged: 222.73~244.82 Hz for resonance frequency, 8.41~12.46 MPa for bending strength, 320.62~367.81 MPa for dynamic modulus of elasticity, and 86.50~106.54 MPa for static modulus of elasticity. Overall, it was shown that as the sawdust addition increased, the resonance frequency, bending strength, dynamic and static modulus of elasticity were increased gradually. This is considered to be for the contribution of sawdust having a large size of raw material and a larger modulus of elasticity than chaff charcoal increases, and that of charcoal having a lower modulus of elasticity than sawdust decreases. This result was consistent with results of other numerous studies reporting that strength performance of a particle board decreases as mixture ratio of different materials with lower strength performance increases (Park et al., 2011, 2012, 2013; Jin et al., 2015). However, although the bending strength of the board manufactured with sawdust addition satisfied KS F 3104 particle board’s quality standard type 8, it is considered to be difficult to use it for durable parts.
Fig. 2 shows the result of analyzing correlation between sawdust addition ratio, bending strength, dynamic modulus of elasticity, and static modulus of elasticity of the board. The aim is to identify the effect of sawdust addition ratio on strength performance of the chaff charcoal-sawdust compound board. This figure reveals the coefficients of determination (R2) between sawdust addition ratio, bending strength, dynamic and static modulus of elasticity as 0.4012, 0.0809, and 0.1971, respectively, indicating a relatively low correlation. This can be interpreted that sawdust addition rate has a small effect on bending strength performance. In addition, the relationship between sawdust addition ratio, dynamic and bending modulus of elasticity, showed a low significance of 1%. This is considered to be because the effect of addition ratio was small due to the low sawdust addition ratio of the compound board. It seems an additional test is required to be conducted with various addition ratios of sawdust in order to identify optimum manufacturing condition for improving mechanical performance.
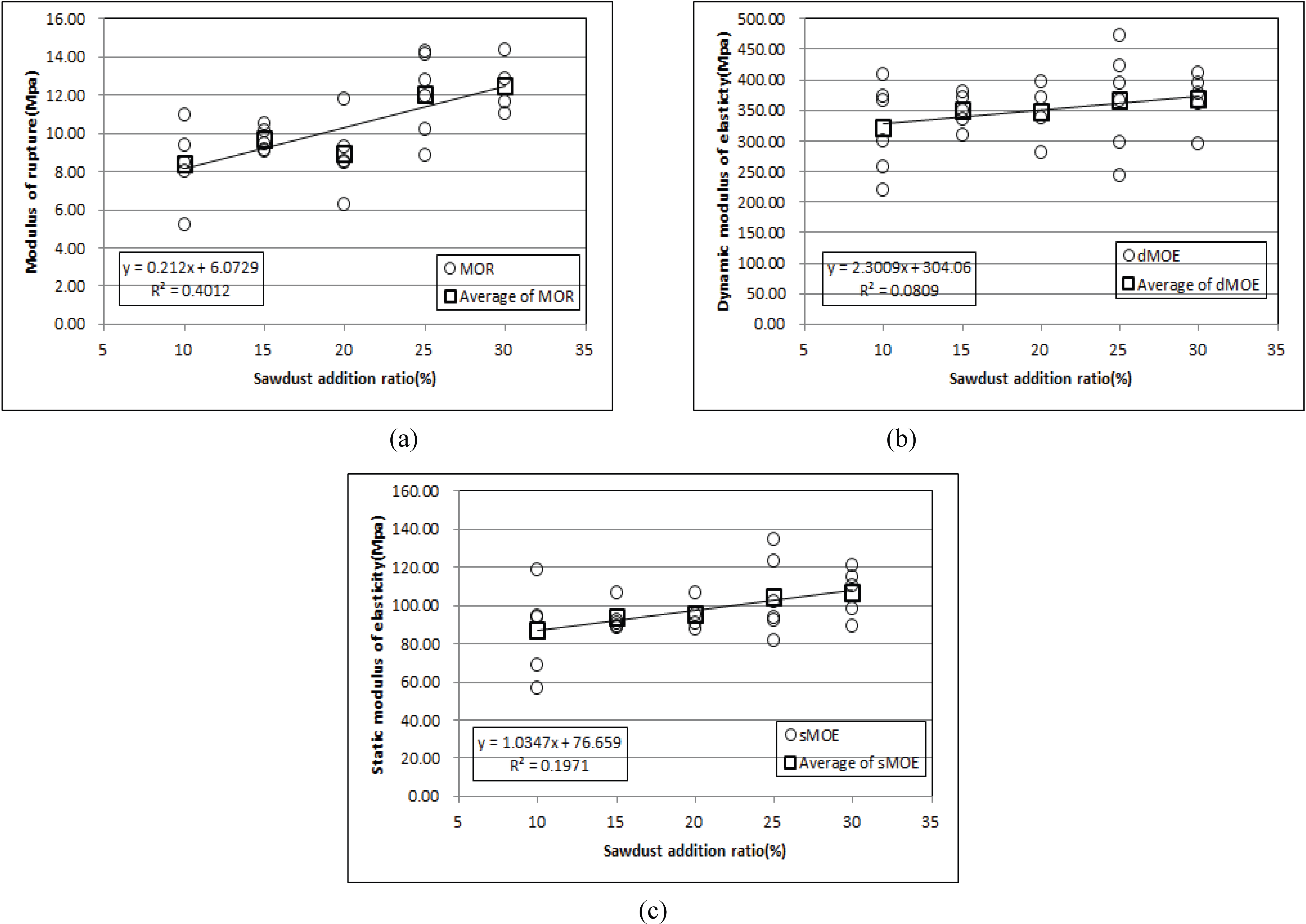
Table 4 indicates correlation between dynamic modulus of elasticity, static modulus of elasticity, and bending strength of the board manufactured at different addition ratios of resin and sawdust. The coefficients of determination (R2) in the relationship between dynamic modulus of elasticity, static modulus of elasticity, and bending strength of the entire chaff charcoal-sawdust compound boards manufactured at different resin addition ratios were 0.9521 and 0.8948, respectively, and it showed a quite high correlation with confidence level of 1%. Furthermore, the coefficients of determination (R2) in the relationship between dynamic modulus of elasticity, static modulus of elasticity, and bending strength of the entire compound boards manufactured at different sawdust addition ratios were 0.7797, and 0.7200, respectively, and this also indicated a high correlation with confidence level of 1%. Fig. 3 shows a correlated regression graph of dynamic modulus of elasticity, static modulus of elasticity, and bending strength of the entire compound boards regardless of resin addition ratio, and sawdust addition ratio of the chaff charcoal-sawdust compound board. The coefficients of determination (R2) between dynamic modulus of elasticity, static modulus of elasticity, and bending strength were 0.9612, and 0.9122, respectively, and it indicated a quite high correlation. This result is consistent with many studies reporting that a close correlation is shown between dynamic modulus of elasticity, static modulus of elasticity, and bending strength of lumber and wooden materials (Park et al., 2011, 2012; Jin et al., 2015). Therefore, it is considered to be possible to predict static modulus of elasticity, and bending strength from dynamic modulus of elasticity obtained from the both-ends free bending vibration test.
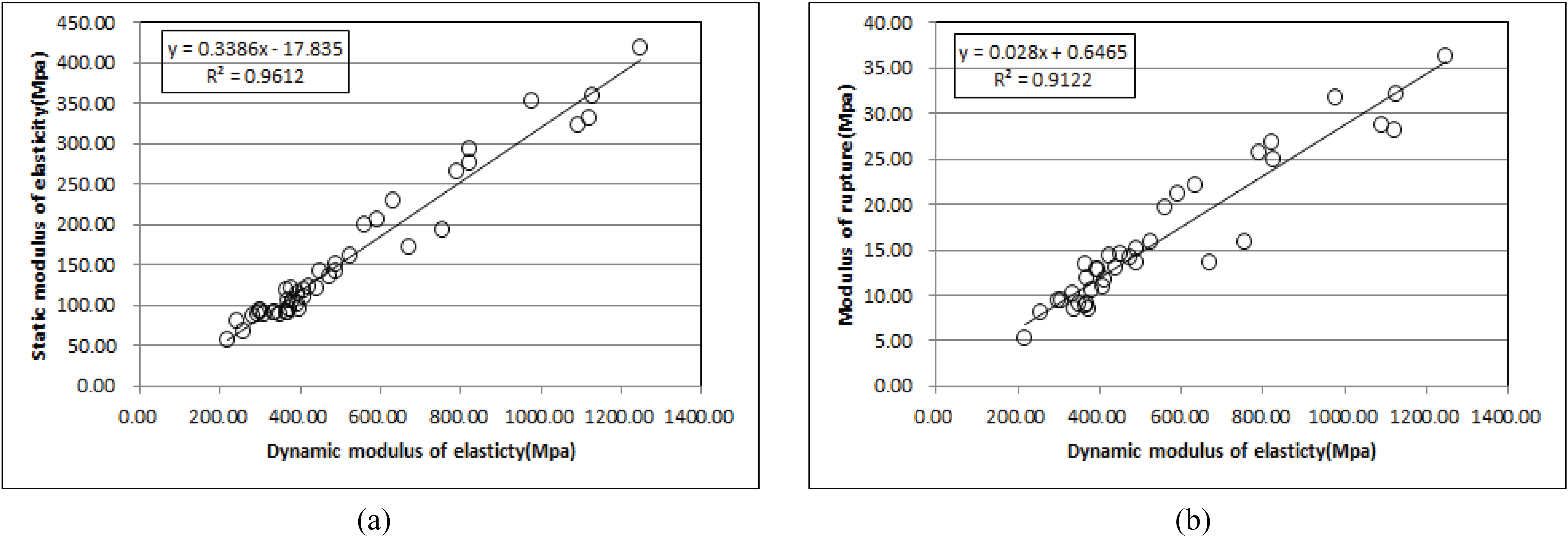
4. CONCLUSION
This study used chaff charcoal made by carbonizing chaff, an agricultural by-product that emerges from rice pounding process, and sawdust to manufacture boards at different addition ratios of resin and sawdust. In addition, the study investigated the effects of resin and sawdust addition ratios on dynamic, static modulus of elasticity, and bending strength, as well as the relationship between the dynamic modulus of elasticity, the static modulus of elasticity, and thebending strength, and obtained the following results:
As resin addition ratio of the chaff charcoal-sawdust compound board increased to 10~25%, the bending performance increased, indicating that resin addition ratio largely effected the bending performance.
Although the bending performance increased gradually with the increase of sawdust addition ratio, the coefficients of determination (R2) between sawdust addition ratio, bending strength, dynamic and static modulus of elasticity were 0.4012, 0.0809, and 0.1971, respectively, indicating a relatively weak correlation and suggesting that sawdust addition ratio has a small effect on bending performance.
Since a high correlation is confirmed between the dynamic modulus of elasticity, the static modulus of elasticity, and bending strength of the chaff charcoal-sawdust compound board, it was confirmed that the static modulus of elasticity, and the bending strength can be predicted nondestructively from the dynamic modulus of elasticity.
It seems to be necessary to conduct a test in the future to manufacture the board by increasing the addition of sawdust by more than 25%, and reducing the ratio of resin addition amount.