1. INTRODUCTION
Wood is a type of material that has aesthetic patterns and is easy to process into different shapes, causing it to be commonly used for a long time as interior/ exterior building materials and furniture materials in residential spaces (Seo et al., 2015; Seo et al., 2016; Park et al., 2019). In general, consumers believe that wood is vulnerable to fire, and to address the issue, flame resistant agents and retardants are required to be developed. Wood, as a combustible material, is pyrolyzed to emit flammable gases to be ignited and burned, so it has been processed with anti-inflammatory agents to improve its combustion performance (Cha et al., 2011).
By definition, flame retardant refers to a chemical treatment to prevent continuous combustion or spread even when a combustible is ignited with a flame by restraining the combustion of the material through physical and chemical combinations with the material (Kim et al., 2014). Flame retardants may be classified into three types depending on their effects (Son, 1988). The first type is phosphorus compounds that restrain the generation of volatile substances created when a flammable material is burned by alternating the pyrolysis process. The second type is an ammonia and boron compound that disrupts the air supply to combustion by coating the surface of the material or generating non-combustible gas around the material. The third is a halogenated compound, which is free radical obstruction agent that prevents flaming combustion from spreading.
In Korea, phosphorus compounds have often been used to fire-proof wooden cultural heritage sites (Kim et al., 2014). The flame retardants to preserve wooden cultural heritage sites must be certified by the Cultural Heritage Administration and the National Research Institute of Cultural Heritage for distribution. Each flame retardant has the different numbers of application and spreading concentrations. Generally, it is reported that the agents are applied 2 to 3 times and approximately 200-1,000 g/m2 is applied each time. Commercial flame retardants consist of guanidine, phosphorus, HEDP (1-hydroxy ethylided-1, 1-diphosphonic acid), etc.
There is research in progress on the performance of flame retardants by application. One research found that a Korean red pine with 300 g/m2 applied on it meets flame retardancy requirements in Korea. Application of 400 g/m2 or more reportedly forms white deposit on the surface of the material (Seo et al., 2017). The Korean red pine that met the flame retardancy requirements with commercial flame retardants showed the carbonized length of 74-93 mm and the carbonized area of 2650-3970 mm2 (Seo et al., 2017; Choi et al., 2011).
Anti-inflammatory treatment methods include: application, which sprays or directly coats flame retardants on the surface of the wooden material, lining, which attach metal plates or other non-combustible materials, and impregnation, which penetrates flame retardants into the wooden material, depending on the characteristics of the combustible material (Kim and Hyun, 2009; Cha et al., 2011). For wood materials and wooden products, the anti-inflammatory method of spraying or brushing flame retardants has been typically used after the materials or products are installed in the structures (Min et al., 2012), and research has been conducted on flame retardant impregnation times from 10 minutes up to 240 minutes to apply the impregnation method (Lim et al., 2008; Park et al., 2011; Kim et al., 2012; Kim et al., 2013). As it was reported that application of commercial retardants to a Korean red pine is more effective than impregnation (Choi et al., 2011), research is required to present appropriate treatment methods for different types of flame retardants and treated materials.
Combustion characteristics and flame retardancy of the material to be treated are critical factor in ignition prevention and fire suppression in the initial stage of a fire (Cha et al., 2011; Dobele et al., 2007; Lim et al., 2008). The flame retardancy methods may be separated by the direction and material of combustion, and metrics during combustion (Min et al., 2012). In Korea, flame retardancy is measured with the 45° Meckel’s burner method and the methylamine method.
The evaluation criteria of the performance based on the flame retardancy standards of the National Fire Agency (announcement no. 2019-2) include remaining flame time (time after the flame is removed until the combustion with flame stops), smoldering time (time after the flame is removed until the combustion without flame stops), carbonized area (area combusted by the flame), and carbonized length (the longest part of the combustion by the flame).
This research evaluated flame retardancy depending on the spreading concentration and impregnation time of phosphorus flame retardant by measuring carbonization length and area on four types of wooden materials based on the flame retardancy through the 45° Meckel’s burner method.
2. MATERIALS and METHODS
The flame retardancy test used Korean pine (pinus koraiensis) plywood, Japanese larch (larix kaempferi) plywood, Japanese cypress (chameacyparis obtusa) planks, and perforated birch (betula platyphylla) plywood boards. The dimensions of the test specimens were 190 mm (width) × 290 mm (height) × 10 mm (thickness) as specified in the 45° Meckel’s burner method based on the flame retardancy standards of the National Fire Agency. The birch plywood boards were perforated with 980 holes per unit area (m2). Four types of wooden products were used to measure flame retardancy by the spreading concentration of flame retardant, and perforated birch plywood boards to measure the performance by the impregnation time. Korean pine plywood, Japanese larch plywood, and Japanese cypress planks were selected because they are commonly used as interior finish and building materials in Korea (Lim et al., 2007; Song et al., 2015). Perforated birch plywood boards were selected because it is often used as a high-end finishing material and has superior strength and durability, and research was published to develop mass-productive objects through laser processing (Song, 2011). The test specimens were manufactured in sufficient quantities to repeat each process three times including untreated control groups. The manufactured specimens were humidified for 24 hours until they reached constant weight in a thermo- hygrostat under the conditions of 23°C and 50% humidity and retained for 2 hours in a desiccator with silica gel in it based on the flame retardancy standards before being used for testing. Refer to Table 1 for abbreviations related to the specimens used in the experiments.
Phosphorus flame retardant was used for application and impregnation. The flame retardant was a phosphorus and boron compound that mainly consisted of diammonium phosphate ((NH4)2HPO4), sodium borate decahydrate (Na2B4O7 H2O), phosphoric acid (H3PO4), and polyethylene glycol #600 (H(CH2CH2O)nOH). This inorganic flame retardant is transparent without any color to expose the grain and patterns of the wood while maintaining the clean surfaces.
The amount, method, and number of applications to analyze the flame retardancy with different spreading concentrations were determined based on the results of preceding research on commercial flame retardants (Son and Han, 2014; Seo et al., 2017). It was determined to apply 300 g/m2 and 500 g/m2 to the Korean pine plywood, Japanese larch plywood, and Japanese cypress planks and 150 g/m2, 300 g/m2, and 500 g/m2 to the perforated birch plywood boards. The application method involved brushing the flame retardant until the surfaces of the specimens were sufficiently soaked, drying them for 24 hours at a temperature of 23 °C and a 50% humidity, reapplying the agent, and repeating the process three times. The impregnation time of 10, 30, 60, 90, 120, and 240 minutes was also determined to analyze the flame retardancy with different impregnation times in flame retardant based on the conditions of a precedent study (Lim et al., 2008; Park et al., 2011, Kim et al., 2012; Kim et al., 2013) where the specimens were immersed for each treatment time in containers providing complete submergence of the specimens at a temperature of 23 °C and a humidity of 50%. Refer to Table 2 for the flame-retardant treatment methods.
The flame retardancy was assessed through the 45° Meckel’s burner method stated in Article 20-2 “Flame retardancy standards for flame-resistant objects (the National Fire Agency announcement no. 2019-2)” of the enforcement decree of the Act on Fire Prevention and Installation, Maintenance, and Safety Control of Fire-Fighting Systems. As shown in Fig. 1, the experiment used the 45° combustion measuring device for the wood combustion, and butane gas as specified in KS M 2150 (liquefied petroleum gas) to fuel combustion. The specimens were secured on the support in the 45° combustion measuring device and the flame from a heating device with a 65 mm length contacted the bottom in the center of the specimens. Each specimen was heated for two minutes and for the specimens that caught the flame, the heating device was removed two seconds after the specimen caught fire. The flame retardancy was measured through the remaining flame time (s), smoldering time (s), carbonized length (mm) and carbonized area (mm2) of each specimen. Refer to the “flame retardancy standards for flame-resistant objects” for definitions of each anti-inflammatory metrics. The standards require the remaining flame time (after the flame of the burner is removed until the combustion with flame stops) to be 10 seconds or shorter, the smoldering time (after the flame of the burner is removed until the combustion without flame stops, excluding the time that the flame remains) to be 30 seconds or shorter, the area carbonized by the flame to be 5,000 mm2 or smaller, and the carbonized length (the length carbonized by the flame) to be 200 mm or shorter.
3. RESULTS and DISCUSSION
Table 3 and Fig. 2-5 show the remaining flame time, the smoldering time, the carbonized length, and the carbonized area measured by the 45° Meckel’s burner method with different spreading concentrations applied to the four type of wood products. Regardless of application of the flame retardant, both the remaining flame time and the smoldering time were 0 seconds, meeting the flame-retardant performance standards. However, the topic requires further study as smoke poses a bigger threat than continuous combustion in the event of a fire (White, 2000).


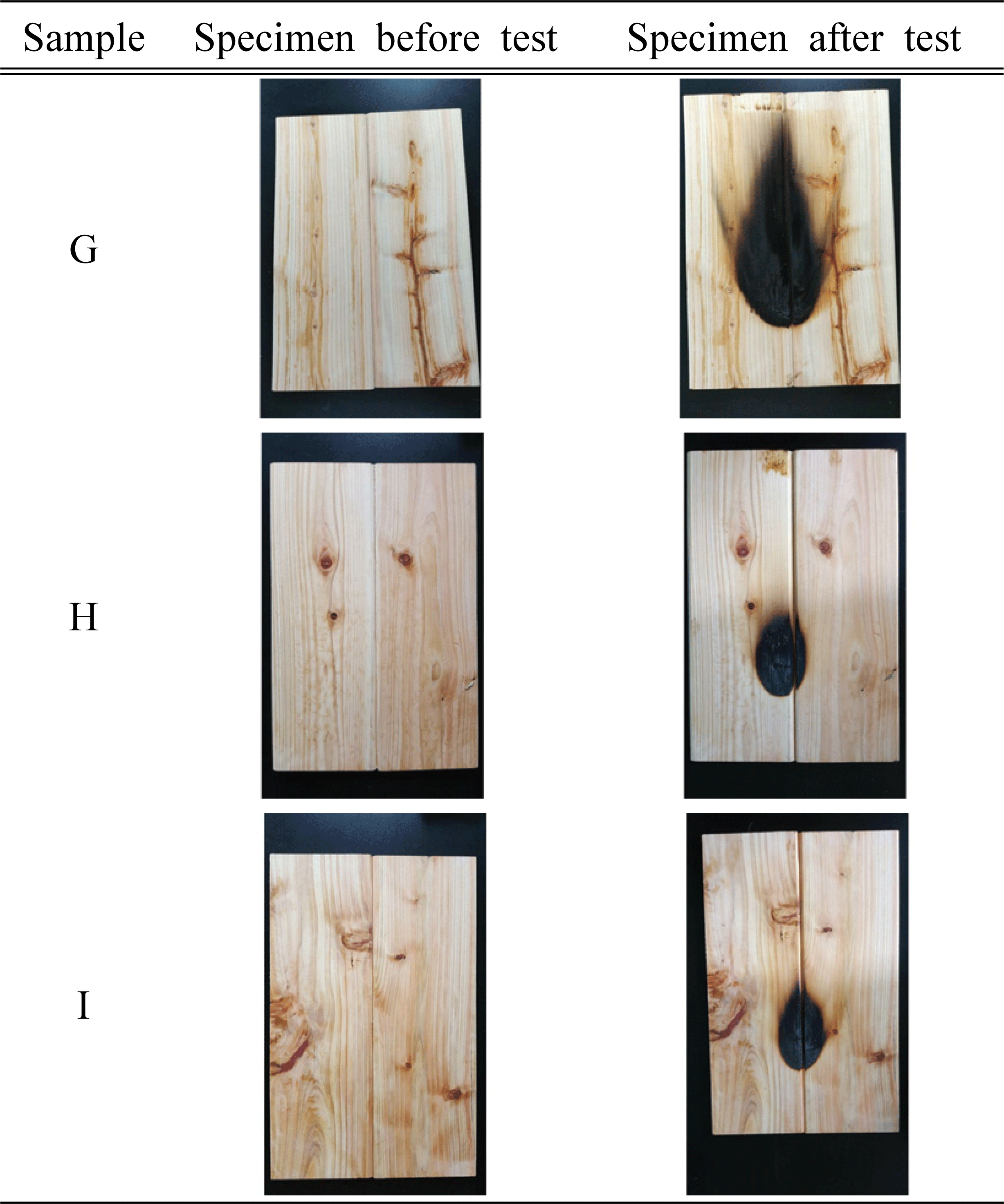
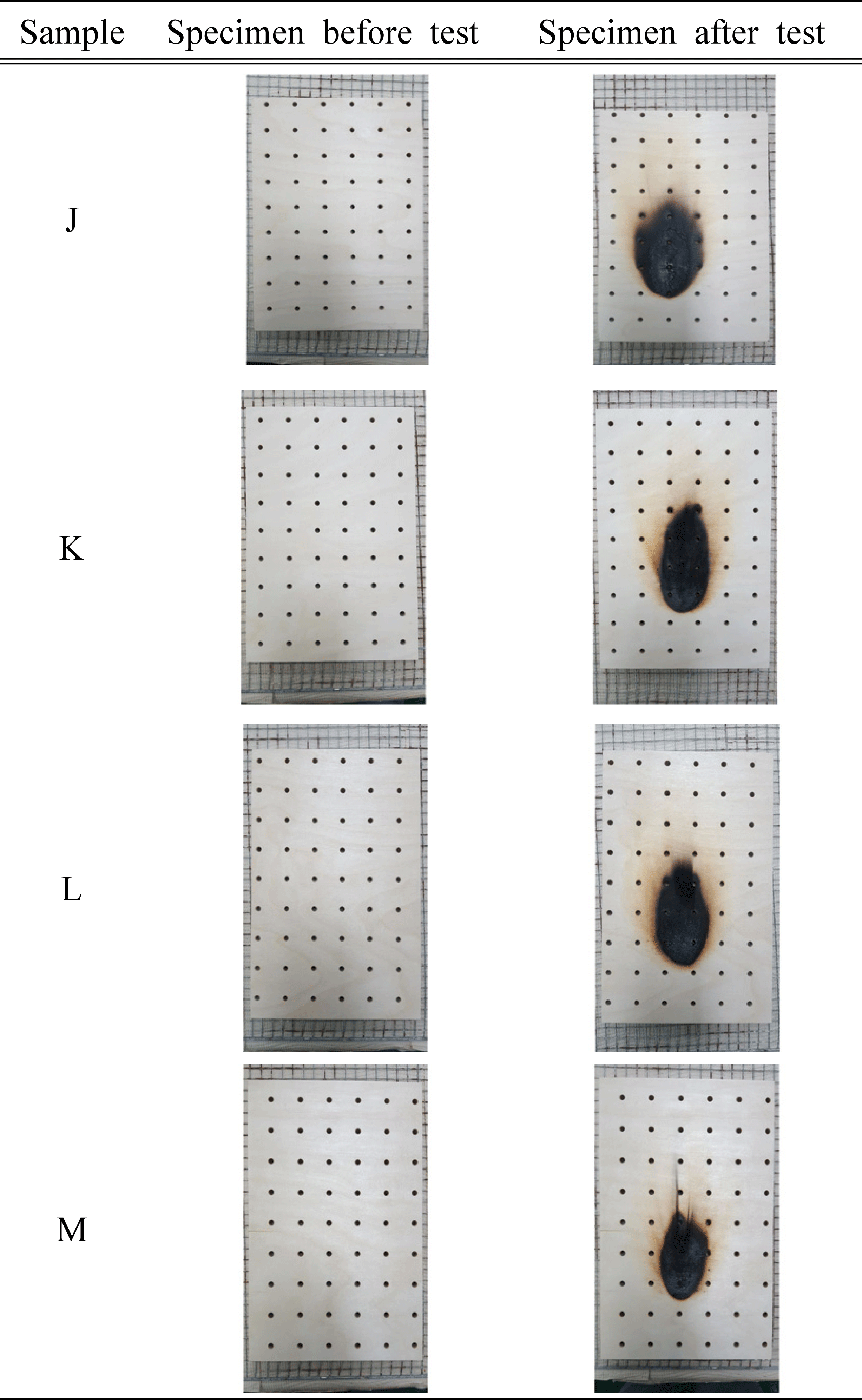
The test of untreated specimens showed a carbonized length of 127.8-176.2 mm and the treated ones showed a length of 81.1-116.5 mm, satisfying the flame-retardant performance standards of 200 mm. The carbonized areas of the untreated specimens ranged from 7461 to 8987 mm2, failing to meet the standards requirement of 5000 mm2, while the testedspecimens treated with the flame retardant, except for the ones with spreading concentration of 150 g/m2, showed up to 4019 mm2 of the area, which meets the standards.
For Japanese larch plywood, the carbonized length and the carbonized area decreased from 100.9 mm and 4019 mm2 to 79.6 mm and 2848 mm2 as the spreading concentration increased from 300 g/m2 to 500 g/m2. On the other hand, the preceding study using a commercial flame retardant containing guanidine and polyphosphate (Ho and Seong, 2004) found that even the spreading concentration of 500 g/m2 did not meet the flame retardant performance standards. This demonstrates that the phosphorus flame retardant is more effective for Japanese larch plywood and perforated birch plywood boards. It is known that effective flame retardant first decomposes and carbonizes cellulose, which is a main ingredient of wood, at a lower temperature (< 300 °C) and generates fewer volatile substances (Park et al., 2012).
The perforated birch plywood boards showed the carbonized length and area of 116.5 mm and 5151 mm2 with 150 g/m2 of the agent applied, which does not live up to the standards, however, as the spreading concentration increased to 300 g/m2, the length and the area were significantly reduced to 95.1 mm and 3694 mm2, reaching the flame retardant performance standards. Although the carbonized length and the carbonized area tend to decrease as the spreading concentration increases, improving the flame-retardant performance as mentioned above, Table 3 demonstrates that the tendency is not pronounced with Korean pine plywood and Japanese cypress planks. This is consistent with the outcomes of the previous study, where an increase in the concentration of the flame retardant did not significantly affect the carbonized area in coniferous trees (Park et al., 2012). It is thought that the difference between the species of tress is caused by the application, which only spreads on the surface of wood.
The performance of the flame retardant used in this study satisfied the standards set by the National Fire Agency with the spreading concentration of common commercial flame retardants. However, different wood products and tree species shows different effect of the improvement in the flame retardant’s performance as the spreading concentration increases, implying the necessity of additional study on the species of trees. Since the perforated birch plywood boards with 150 g/m2 applied exceeded the standards, a study should be conducted to verify the cost-effective spreading concentration that passes the flame retardant performance standards with 300 g/m2 or less for the industrial use of flame retardants.
Table 4 and Fig. 6 show the remaining flame time, the smoldering time, the carbonized length and the carbonized area measured for perforated birch plywood boards through the 45° Meckel’s burner method with different impregnation times.
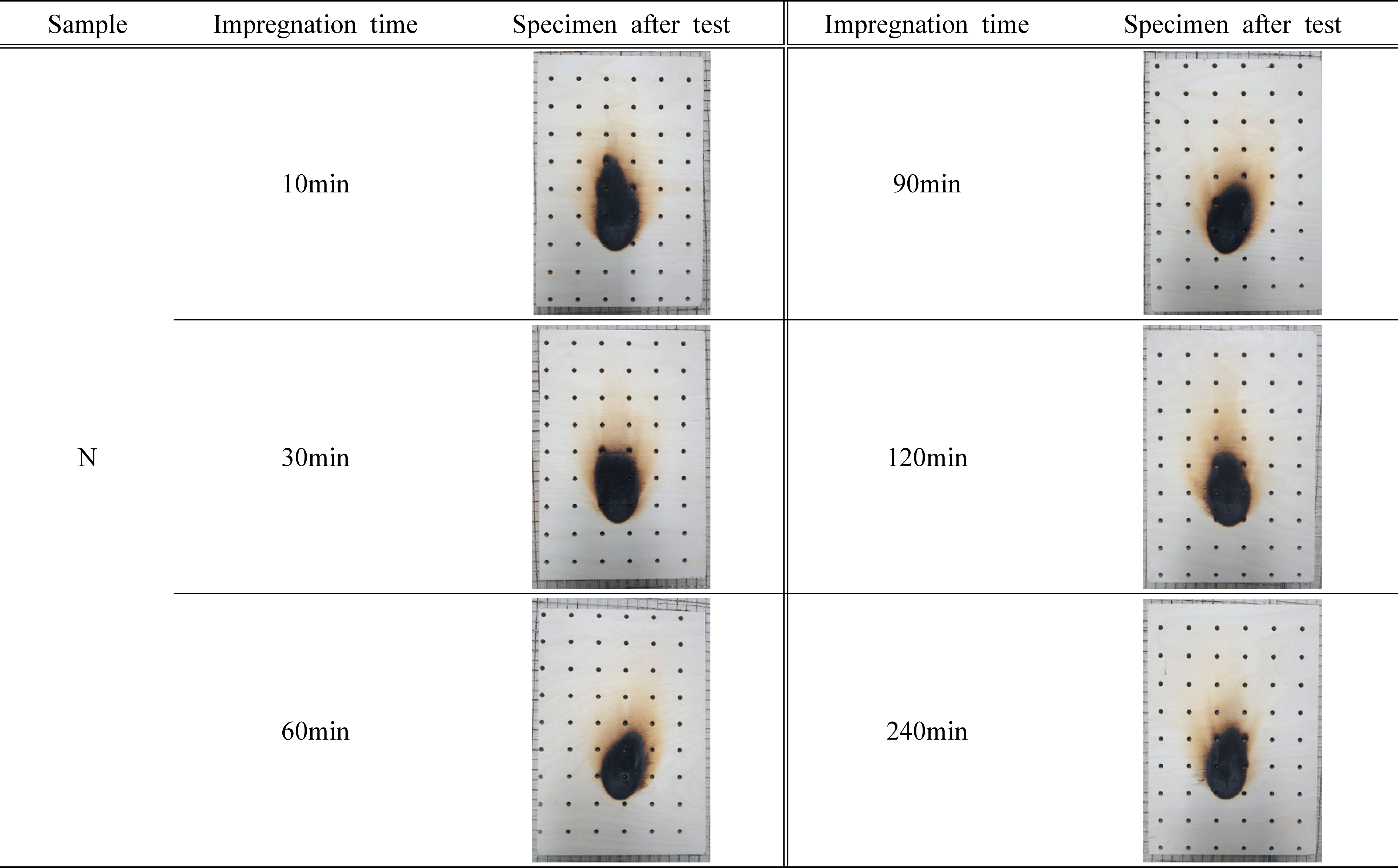
Regardless of the impregnation time, both the remaining flame time and the smoldering time were 0 seconds. All the test specimens treated with impregnation met the standards of the carbonized length of 200 mm and the carbonized area of 5000 mm2. The impregnation time and the flame retardant’s performance showed a positive correlation for the first 60 minutes, but the curve grew flatter gradually after that. After 90 minutes into the impregnation, the carbonized length and the carbonized area rose. This demonstrates that little flame retardant penetrates into wood after 60 minutes, which is consistent with the preceding study (Kim et al., 2013), where the weight of imported sawn wood hardly increased after the first 60 minutes of impregnation. The flame-retardant performance of birch plywood boards with different impregnation times in this study was similar to a previous study that found a significant improvement of the flame-retardant performance after 30 minutes of impregnation for Korean ash trees, maple trees, and oaks (Lim et al., 2008). However, considering a preceding study that resulted in arelatively low flame-retardant performance with the carbonized length and area of 105.0 mm and 4750 mm2 respectively after pine wood specimens were immersed for 72 hours, it seems that the optimal impregnation time depends on the species of the tree. An earlier study on the flame retardant’s performance after poplar was immersed in APP (ammonium polyphosphate) for 10 minutes concluded thatammonia and water generated by decomposed APP dilute combustibles to enhance the performance (He, 2016). Therefore, it is believed that diammonium phosphate used in this study was pyrolyzed to generate ammonia and water, raising the performance of perforated birch plywood boards.
The flame retardant’s performance of the perforated birch plywood boards met the performance standards of the National Fire Agency after 10 minutes of impregnation, but the appropriate impregnation time was determined to be 60 minutes. In addition, further studies on a variety of tree species and wood products are required to verify the most effective impregnation time for popular wood materials in Korea.
4. CONCLUSION
This study analyzed the flame retardancy with different spreading concentrations and impregnation times of four types of planks by measuring the remaining flame time, the soldering time, the carbonized length, and the carbonized area and concludes the following:
Flame retardant performance testing resulted in performance improvement through decreased carbonized length and area with increased spreading concentration of flame retardant on Japanese larch plywood and perforated birch plywood boards, but the tendency was not distinct for Korean pine plywood and Japanese cypress planks; and
Flame retardant performance testing showed a positive correlation between the impregnation time and the flame retardance performance until 60 minutes into impregnation of perforated birch plywood boards, but the curve was gradually flattened after that time.
This study verified the flame retardancy of the four types of wood plates and as a result, phosphorus flame retardant effectively prevented flames for Japanese larch plywood and perforated birch plywood boards, and the best impregnation time for perforated birch plywood boards was 60 minutes.