1. INTRODUCTION
Amino resins such as urea–formaldehyde (UF), melamine– formaldehyde (MF), and melamine–urea-formaldehyde (MUF) are the most important thermosetting adhesives in wood-based composite panel manufacturing. Compared to other wood adhesives, UF resins have advantages such as fast curing, excellent performance in the panel, water solubility, and low cost. The disadvantage of using UF adhesives is that they are less resistant to the impact of higher moisture and water. MUF resins can replace both expensive MF resins and high-water resistance resins (No and Kim, 2004; Hse et al., 2008; Hse, 2009). The properties and performance of MUF resins are closely related to the resin’s synthesis method and the melamine level. Previous studies have shown that synthesis parameters such as F/(U+M) molar ratio, melamine content, and the sequence of melamine addition (in the case of MUF) significantly affect the properties of UF and MUF resins (Dunky, 1998; Pizzi and Mittal, 2003; No and Kim, 2004; Hse et al., 2008, Gavrilović-Grmuša et al., 2010a, 2010b; Paiva et al., 2012, Hong et al., 2017a,b). These results reported that thickness of the interphase region and the depth of penetration into the wood were related to the resin viscosity. Longterm storage stability is an important factor in the industrial use of MUF resins as wood adhesives. Previous studies have shown that the amount of hydroxymethylated melamine species decrease during storage and that the condensation reaction between hydroxymethylgroups progresses to a certain extent during storage (Malkin and Kulichikhin, 1991; Johromi, 1999; Mijatovic et al., 2002; No and Kim, 2004).
Given the importance, many publications have reported measurements of molecular weight (MW) of MUF resins using gel permeation chromatography (GPC) or size exclusion chromatography (SEC) (Zanetti and Pizzi, 2003; Despres and Pizzi, 2006; Lei et al., 2006; Pendlebury et al., 2010; Paiva et al., 2013; Jeong and Park, 2016, 2019, Jeong et al., 2019, Lubis et al., 2019a, b). For example, MWs and the chain length of MF resins also impacted the storage stability of MF resins (Jahromi, 1999a, 1999b). When the chains are too short, a greater amount of hydrogen bonds may be formed between the chains and the resin will solidify and precipitate. Meanwhile, when the chains are too long, the viscosity becomes too high, which makes the application difficult and reduces the penetration of the adhesive into the wood-based substrate (Johnson and Kamke, 1992; Jeremejeff, 2012; Nuryawan et al., 2014; Jeong and Park, 2016; Jeong and Park, 2019, Hong et al., 2017a, b). Thus, adequate chain length and branches of sufficient branching will prevent the formation of hydrogen bonds and improve the resin’s storage stability (Jahromi, 1999a, 1999b). Although lots of research has focused on the storage stability of MF and MUF resins, there has been very limited work on the estimation of property changes in these resins over storage time. Therefore, we attempted to estimate the changes in properties such as pH, apparent viscosity, MWs, and crystallinity in MUF resins prepared by two different synthesis methods and for three melamine contents as a function of storage time for up to 30 days.
2. MATERIALS and METHODS
Melamine (99%), urea granules (99%), and formalin (37%) used in the synthesis of MUF resin adhesives in this work are of technical grade from Daejung Chemical, Korea. Aqueous solutions of formic acid (20 wt%) and sodium hydroxide (20 wt%) were added to adjust the pH during the resin synthesis process. An aqueous solution of ammonium chloride (20 wt%) was used as a hardener. High-purity (≥99.9%) N,N-dimethyl formamide (DMF) and dimethylsulfoxide (DMSO) of high-performance liquid chromatography (HPLC) grade were purchased from Sigma-Aldrich in Korea and used without further treatment.
Two types of resins, namely MUF-A and MUF-B, were synthesized in this study. First, MUF-A resins were synthesized using an alkaline–acid–alkaline threestep reaction (Jeong et al., 2019). Around 580 g of formalin was placed in a reactor equipped with a mantle heater. The pH was adjusted to 8.2–8.5 by adding sodium hydroxide (20 wt%). First, urea and melamine (at three levels of 5, 10, and 20%) were simultaneously added into the reactor at the F/(M+U) molar ratio of 1.5 under continuous stirring at 40°C. The temperature was increased to 90°C and maintained for 1 h. Then, the pH was adjusted to 6.5–7.0 with formic acid (20 wt%) for the condensation reaction. When the target resin viscosity of the “B” and “C” scale of a bubble viscometer (VG-9100, BYK Gardner, Columbia, Maryland, USA) reached at 90°C. After the target viscosity was reached, the pH was adjusted to 7.5–8.0 with 20% NaOH. Then, the second urea was added into the reactor to obtain MUF-A resins with the final F/(M+U) molar ratio of 1.0, which subsequently decreased the temperature to 60°C and reacted for 20 min. The MUF-A resins were cooled to ambient temperature and the pH was adjusted to 9.0–9.2 prior to further analysis.
Secondly, MUF-B resins were synthesized using an alkaline–alkaline–acid three-step reaction. Formalin was added to the reactor and the pH was adjusted to 8.2–8.5 by adding sodium hydroxide as in the MUF-A resin synthesis. The relevant amounts of melamine to achieve the final content of melamine of 5, 10, and 20%, respectively, were added to the reactor under continuous stirring at 40°C. Then, the temperature was increased to 90°C and was maintained for 1 h. Then, the first urea was added to the reactor to adjust the same F/(M+U) molar ratio of 1.5 for all three versions of different final melamine contents and maintained for 10 minutes. Then, the pH was adjusted to 6.5–7.0 with formic acid (20 wt%) for the condensation reaction until the target resin viscosity was between the “B” and “C” scale of the bubble viscometer. After the target viscosity was reached, the pH was adjusted to 7.5–8.0 with 20% NaOH. Then, the second urea portion was added to the reactor to obtain the final F/(M+U) molar ratio of 1.0, which consequently decreased the temperature to 60°C, which was maintained for 20 min. Finally, MUF-B resins were cooled to ambient temperature and the pH was adjusted to 9.0–9.2 prior to further analysis.
The water-tolerance value was determined by adding a certain amount of water to a 1 g resin sample in the tube by checking the clouding point of the resin samples at 20°C. The viscosity of all resins was measured with a cone-plate viscometer (DV−II+, Brookfield, Middleboro, MA, USA), using spindle No. 2 at 25°C and 60 rpm. The non-volatile solids content of each sample was calculated by measuring the resin mass before and after drying in the oven at 105°C for 3 h. The gelation time of all the resins was measured at 100°C by adding 3 wt% NH4CI (added in the form of a 20wt% solution) based on the resins solids content using a gel time meter (DAVIS, Sunshine Instruments, USA).
A GPC (YL9100, Younglin, Korea) system equipped with a refractive index (RI) detector was used to measure the MW of the resins. The columns used were KD 801, 802, and 806 M (SHODEX, Japan). The GPC was performed at 50°C for the column and detector temperatures and a flow rate of 0.5 ml/min (Jeong and Park, 2017). The universal calibration of MW between 106 and 25,200 Da was performed using polyethylene glycol (PEG) standards from Polymer Standards Service GmbH, Germany. A HPLC-grade DMF was used as the mobile phase. The resin samples were dissolved in a mixture of 10% DMSO and 90% DMF and kept in an oven at 50°C for 3 h before injection. The sample solution was then introduced via the injection loop of the GPC through a 0.45 mm filter. The weight-average molecular weight (Mw), number-average molecular weight (Mn), polydispersity (PDI), and low molecular weight (LMW) and high molecular weight (HMW) fractions were calculated using YL-Clarity chromatography software (Younglin, Gyeonggi-do, Korea).
X-ray diffraction (XRD) (D/Max-2500 Rigaku, Tokyo, Japan) was used to investigate the crystallinity of the two types of MUF resins with the three melamine contents after different storage times. The MUF resins were thoroughly cured at 120°C for one day after 3 wt% NH4CI (added in form of a 20 wt% solution). Cured MUF resins then were ground to obtain the powder resins with 180-250 μm size. The powder samples were analyzed at ambient temperature using a CuKα1 X-ray source with a wavelength (λ) of 1.540 Å in the angular range 10–60° of 2θ with a step of 0.02°/min. The percent crystallinity of MUF-A and MUF-B resins with three melamine contents during aging was determined by deconvoluting the total area of the diffractograms and obtaining the individual contributions of the crystalline and amorphous regions. Thus, the degree of crystallinity by weight was obtained by applying the least-squares fit procedure elaborated by Hindeleh and Johnson (1971).
3. RESULTS and DISCUSSION
Table 1 presents the properties of two MUF resins at three melamine contents. MUF–A resins had similar resin solids content, while those of MUF-B resins slightly increased as the melamine content increased. This could be due to the melamine content and amount of the second urea for MUF-B resins. The viscosity of these resins increased gradually as the melamine content increased. Moreover, the gelation time of the MUF-B resins was much shorter than those of the MUF-A resins and it decreased as the melamine content increased. The water tolerance values after their synthesis were close together even though they were lower than the target values, indicating proper control of the synthesis of these resins.
Fig. 1 shows the change of pH of MUF-A (Fig. 1a) and MUF-B resins (Fig. 1b) at 25°C as a function of the storage time. The pH of the two resins linearly decreased over the storage time for up to30 days. Based on the slope of the equation of MUF-A resins showed a greater decrease in pH than those of MUF-B resins, indicating the instability in their storage. A decrease in the pH could be due to the hydrolysis of hydroxymethylated ureas, which disintegrate into ammonia(NH3) and isocyanic acid(HNCO), which quickly decomposes to NH3 and carbon dioxide(CO2) (Mattheij et al. 2005). NH3 reacts with formaldehyde to produce slightly basic hexamethylenetetramine. Thus, the effects of CO2 will prevail during resin storage, which will consequently decrease the pH of either MUF-A or MUF-B resins. In addition, the Cannizzaro reaction is a base-catalyzed disproportionate reaction of an aldehyde, devoid of α-H atoms, decrease the pH. All linear equations between the pH and storage time showed high regression coefficients and made it possible to estimate the pH change over the storage time.
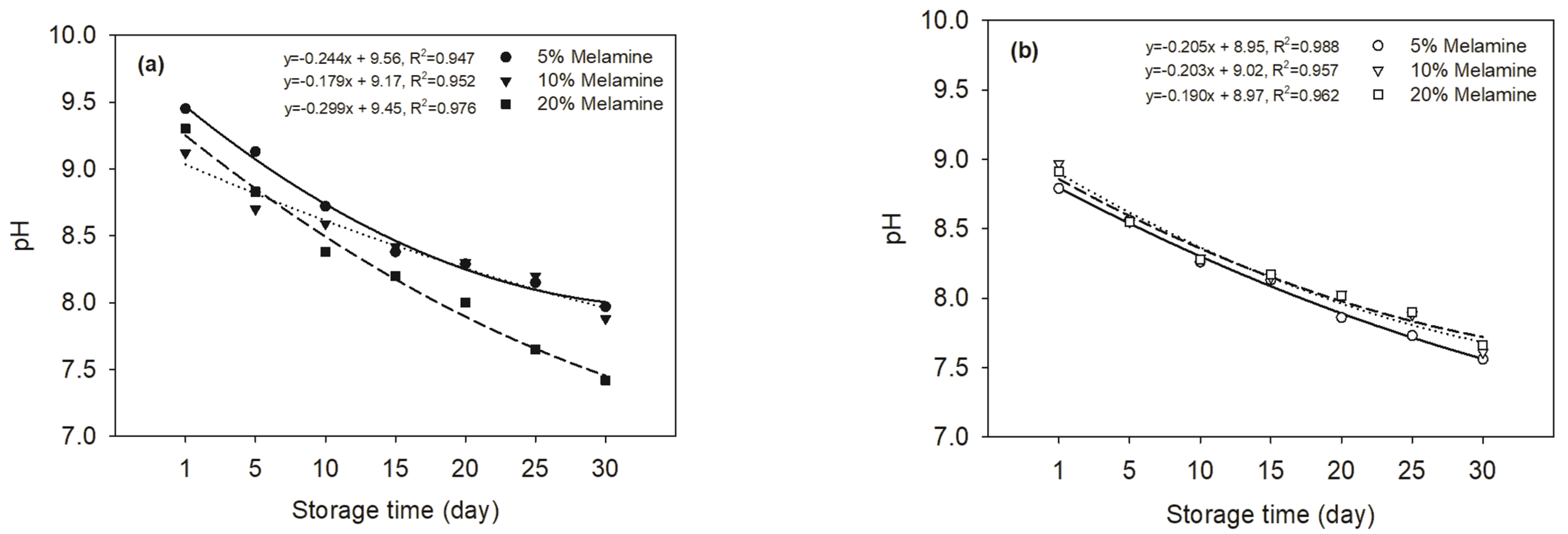
As shown in Fig. 2, the apparent viscosity of two MUF resins linearly increased at 5 and 10% melamine content. However, it exponentially increased at 20% melamine content, regardless of the synthesis method. As expected, these results indicate that the resins prepared with the lower melamine contents are relatively stable in storage for up to 30 days. However, the 20% melamine addition limited the safe storage stability for the two resins to only about 20 days. These results could be responsible for chemical changes during storage. For example, Early (Malkin and Kulichikhin, 1991; Johromi, 1999; Mijatovic et al., 2002; No and Kim, 2004) studies showed that the amount of hydroxymethyl melamine and substituted melamine compounds decreased during storage and the condensation reaction between hydroxymethyl groups preceded to a certain extent during storage. In addition, it was reported that the most widespread change during the storage of MUF-A resins was the formation of hydrogen bonds between the chains (Siimer et al., 2005). Hydrogen bonds were formed between fully lone electron pairs of carbonyl oxygen and hydroxymethyl groups and hydrogen of electronegative atoms of free amine groups. Water present in the resin was also likely involved in the formation of hydrogen bonds. The number of hydrogen bonds increased over time and hence the viscosity, making even the application of the adhesive more difficult (Siimer et al., 2005).
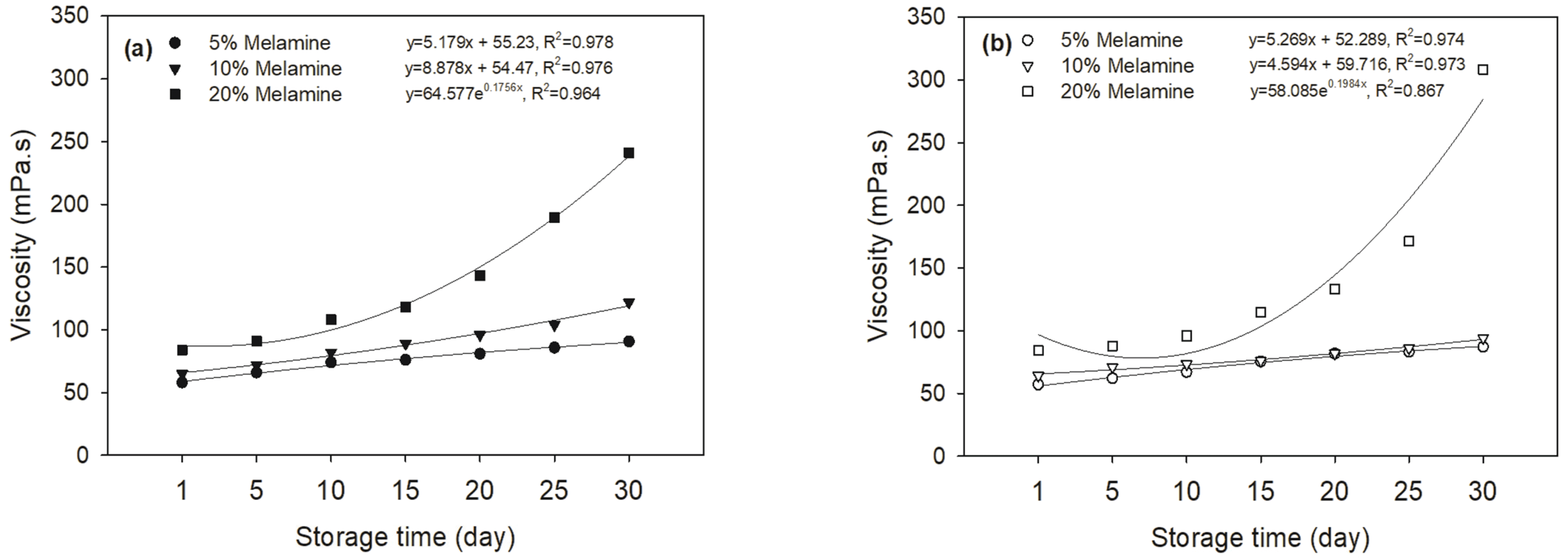
To understand the increase in resin viscosity, the molecular weights (MWs) of the two MUF resins were determined by GPC. Fig. 3 presents the typical GPC chromatograms of the two resins with three melamine contents resins immediately after their synthesis. The two types of resin have four major peaks. These two resins with 20% melamine content showed higher and wider peaks than those with low melamine content, indicating greater MW. The MW of a polymer chain also affects the storage stability. If a chain is too long, more hydrogen bonds may be formed between the chains and the resin will then solidify and precipitate. The long chains with their high MW increase the resin viscosity, making it difficult to apply the resin uniformly and reducing the adhesive penetration into the substrate. Thus, moderate length chains with sufficient amounts of branches will prevent the formation of hydrogen bonds and improve the stability of resin storage (Jahromi, 1999a).
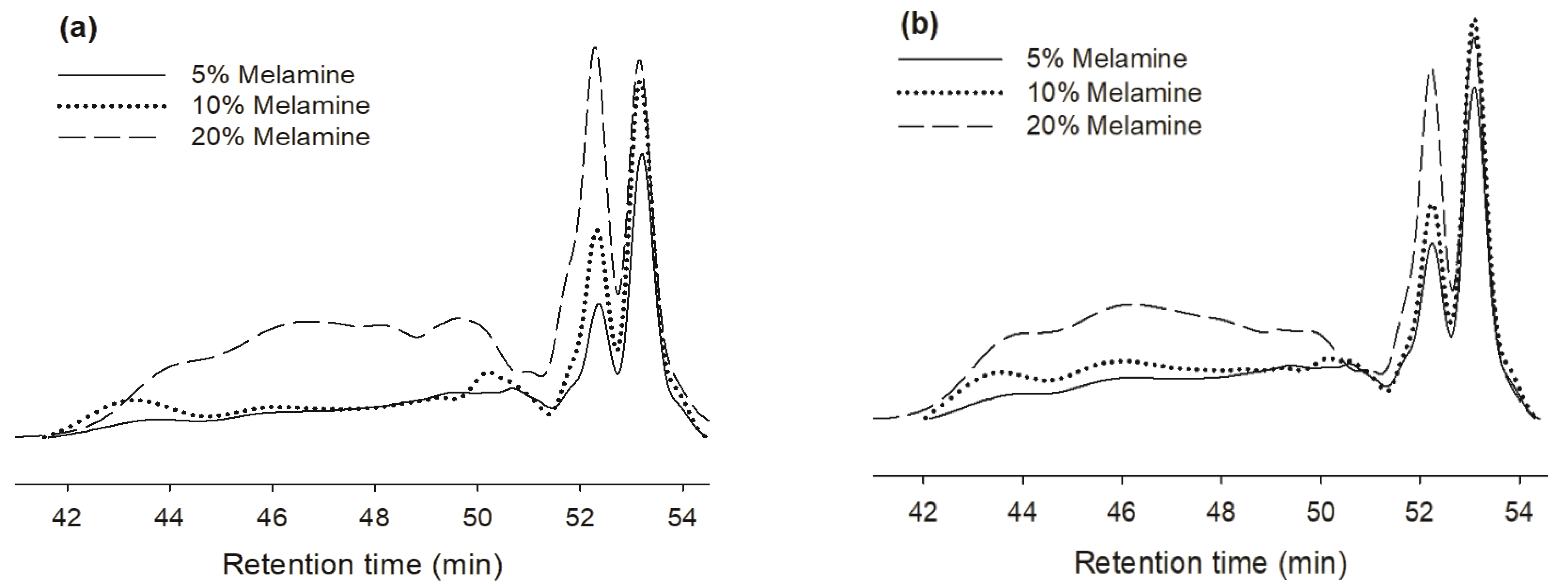
Fig. 4 and Table 2 compare the fraction of low MW (LMW) within closer the retention time near 54 minutes and high MW (HMW) within closer the retention time near 46 minutes in the two types of resins prepared with the three melamine content levels at different storage times. As the melamine contents increased in the two MUF resin types, the HMW fraction increased and the LMW fraction decreased. In addition, the HMW fraction of the two MUF resin types clearly increased as the storage time increased. After 30 days, the LMW fraction decreased and the HMW fraction increased. As the storage time reached 30 days, the LMW fraction of the MUF-A resins became greater than those of the MUF-B resins. However, the HMW fraction of the MUF-B resin was much greater than its counterpart in the MUF-A resins, which may be due to differences in how melamine reacts with formaldehyde before urea (Kim et al., 2006). In other words, melamine, formaldehyde, and urea react simultaneously for MUF-A resins, which produce a greater amount of the LMW fraction. When the melamine reacts with formaldehyde first and then with urea, the MUF-B resins result in a lesser amount of the LMW fraction.
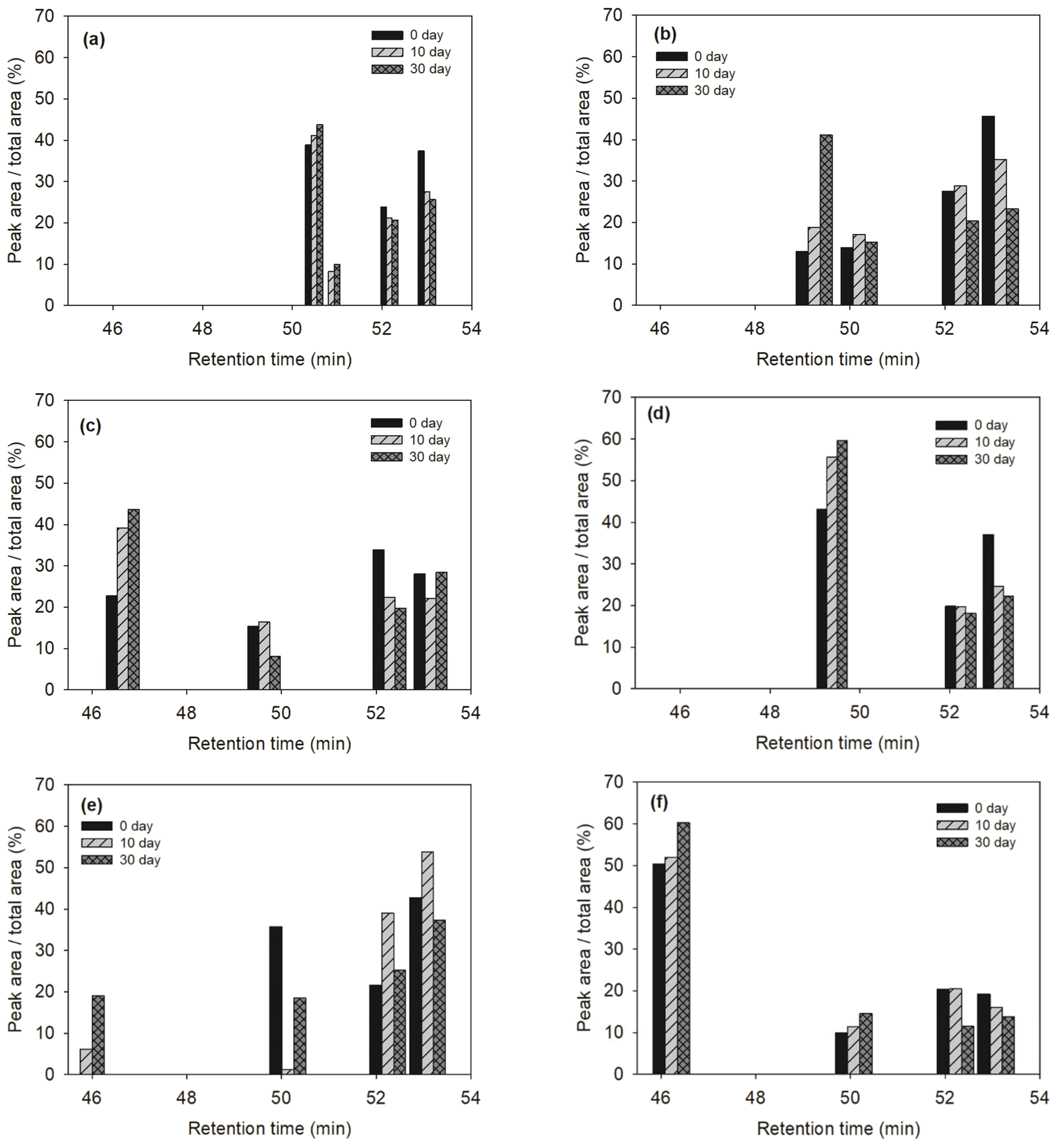
Fig. 5 presents both Mn and Mw of two MUF versions with three melamine contents. As the melamine content increased, both the Mn and Mw of two MUF resins increased (Fig. 5a and b), which was compatible with an increase in the resin viscosity. However, the Mn and Mw of MUF-B resins were higher than those of the MUF-A resins, indicating that more polymeric materials were formed. In addition, the MUF-B resins had higher MW than the MUF-A resins; this is because the addition reaction of formaldehyde to melamine is much easier and more complete than those of urea (Kim et al., 2006).
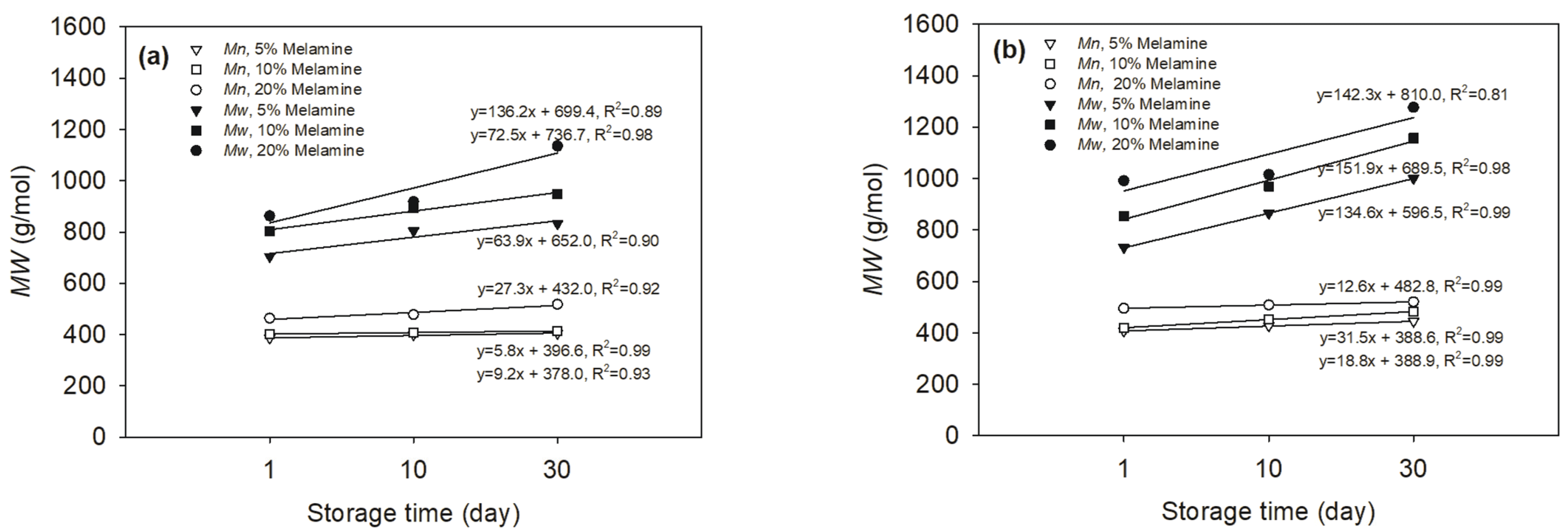
Linear relationships between MW and storage time were established for two MUF resins with three melamine contents, making it possible to estimate the change of Mn and Mw over the storage time. In particular, MUF-A and MUF-B resins showed a significantly rapid increase in the Mn and Mw for the 20% melamine level, especially for MUF-B type. In addition, the polydispersity index (PDI= Mw/Mn) values of these resins increased as the melamine content increased (Table 3 and 4), which was consistent with the changes of Mn and Mw. However, the PDI values of these resins showed an inconsistency over the storage time (Table 4). The PDI values of the two MUF resins slightly increased at the 10% melamine content level as the difference between Mn and Mw widened over 10 days of storage. Then, the PDI decreased except the MUF-B resins with 20% melamine content.
Resin type | Melamine content (wt %) | PDI | ||
---|---|---|---|---|
0 day | 10 days | 30 days | ||
MUF-A | 5 | 1.83 | 2.00 | 1.86 |
10 | 2.01 | 2.19 | 1.92 | |
20 | 2.06 | 2.29 | 2.19 | |
MUF-B | 5 | 1.80 | 2.03 | 2.00 |
10 | 2.02 | 2.15 | 2.00 | |
20 | 2.25 | 2.40 | 2.45 |
Fig. 6 shows the typical XRD patterns of two MUF resins with three melamine contents at 30 days. As shown, the sharpness and intensity of the crystalline region decreases markedly as the melamine content increases, indicating a decrease in the resin’s crystallinity. In other words, the two types of resins showed crystallinity with up to 10% melamine content, indicating that these resins contain crystals or crystalline domains in the cured state. The resins at 20% melamine content were amorphous after more than 10 days of storage although at the start of the storage the crystallinity of the 20% MUF-A resin was higher compared to the 20% MUF-B resin. The crystallinity of the MUF-A resins slightly decreased up to 10 days of storage and then leveled off as the storage time increased from 10 days to 30 days, whereas the MUF-B resins with the two lower melamine contents showed different behavior, but all in all no big changes (Fig. 7).
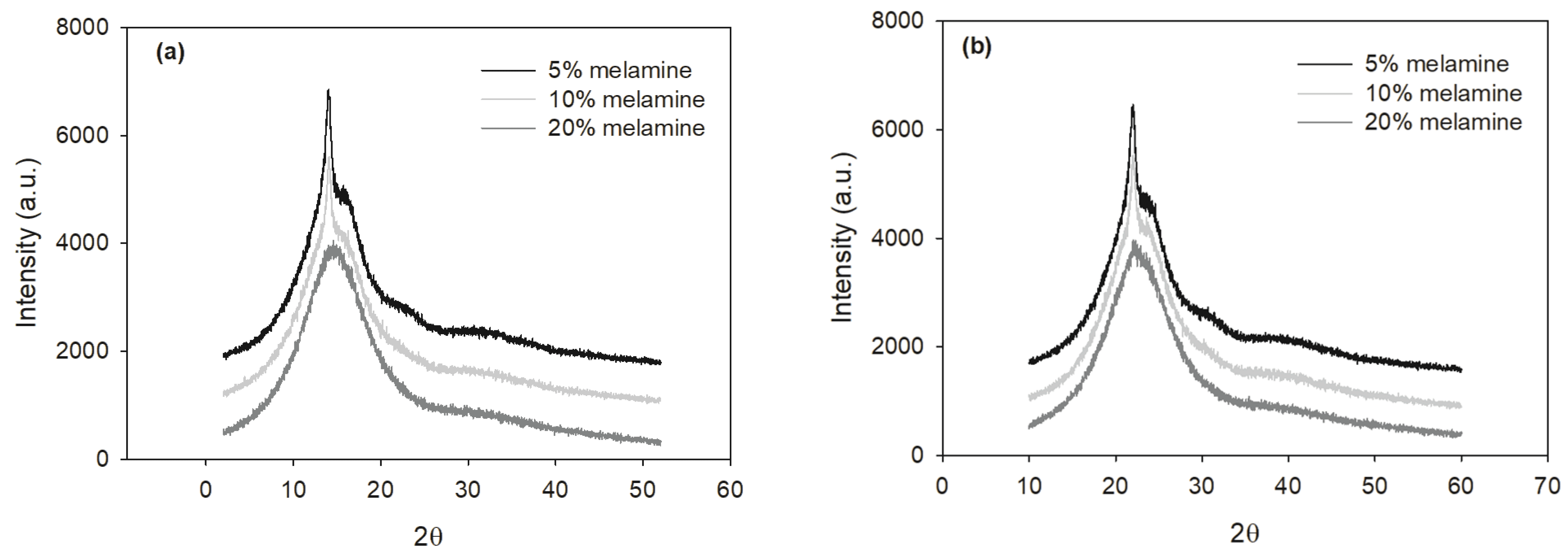
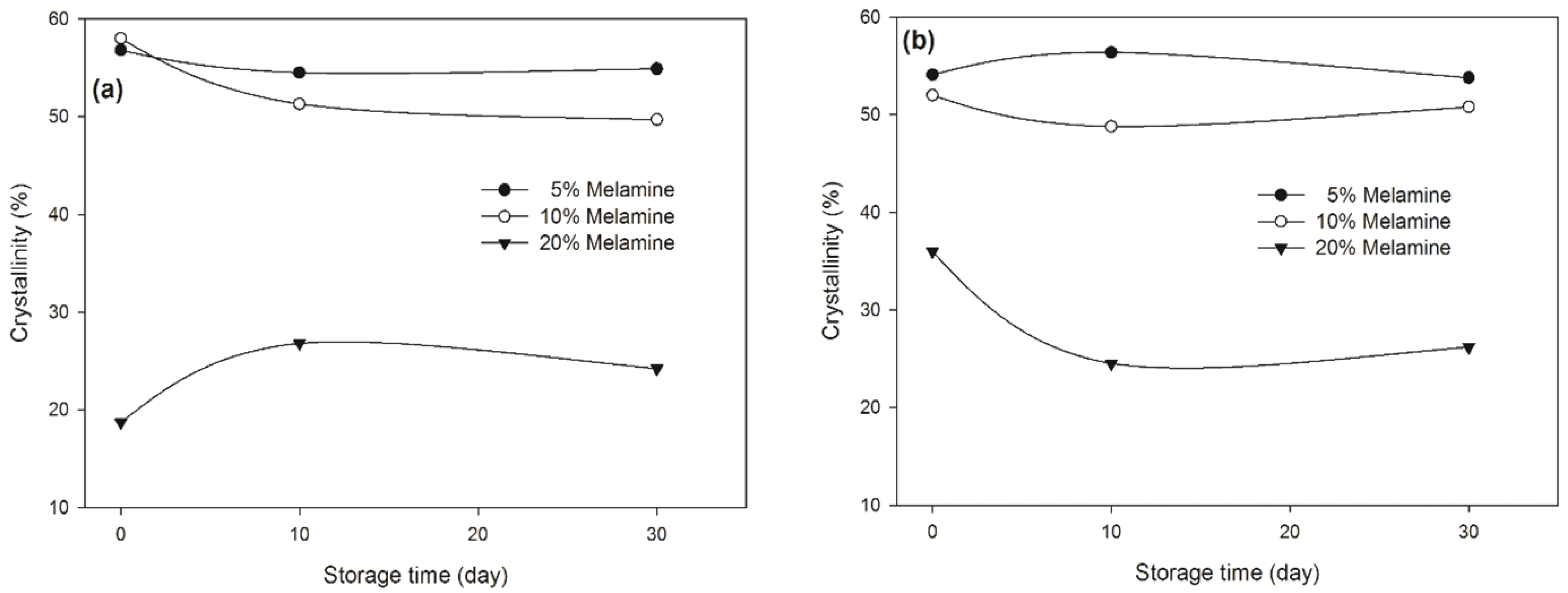
4. CONCLUSIONS
This study attempted to estimate changes of the properties of two types of MUF resins prepared with different synthesis methods and melamine contents over their storage time of up to 30 days. We investigated the pH, apparent viscosity, molecular weights, and crystallinity for estimation in industrial practice. The pH values of the MUF-A and MUF-B resins decreased linearly over the storage time while the apparent viscosity increased linearly at low melamine contents (5 and 10%) but exponentially at 20% melamine content. As expected, the molecular weights (Mw and Mn) linearly increased over the storage time, with steeper increase for Mw, especially for the MUF-B version with 20% melamine. The two resins with 5 and 10% melamine level show crystallinity in the cured resin, whereas the two 20% versions remained amorphous. These relationships between the resin properties and storage time help to predict resin properties over storage time.