1. INTRODUCTION
Sewage treatment plants are social infrastructure built in cities as a result of economic development and urbanization. Based on the 2017 sewage statistics, the sewage distribution rate in Korea is 94%, and the number of the sewage treatment plants is reaching 4,072. Due to global warming and extreme weather phenomenon caused by economic growth, the increased importance of water quality management is resulting in the increase in the management costs every year (Hwang and Choi, 2018). Korean sewage treatment plants introduced advanced treatment facilities, reinforced the criteria for discharged water quality, and implemented the Total Water Pollution Load Management System for a stable water quality improvement. With the improvement of sewer lines from the combined pipe type to the separated type, the amount of sewage inflow decreased. However, the actual amount of chemical use is increasing due to the increase in the pollutant load (MOE, 2017). As for coagulant used in Korean sewage treatment plants, the use of inorganic polymer coagulant, PAC (Poly Aluminum Chloride), accounts for 58%. Although it contains a large content of impurities (heavy metal) according to the quality standards, there have been insufficient efforts for reinforcing the standards or technically improving the quality, which led to secondary pollution problems from an excessive coagulant injection (Park, 2009). With the increase in the use of chemicals, the annual amount of sludge generated in sewage is 11,415 m3/d as of 2017, which has been increasing (So et al., 2018). Accordingly, additional solutions for reusing the sewage sludge are being explored, and the reuse rate has also increased by recycling sludge as auxiliary fuel and fertilizer.
However, as dumping sewage sludge in the ocean is now completely prohibited under the London Convention, sewage sludge is finally disposed of through landfill, recycling, and pretreatment on land (Han et al., 2019). Also, landfill treatment is limited since landfilling sewage sludge has been prohibited under the Wastes Control Act recently. For this reason, new solutions for an efficient treatment of sewage sludge are demanded. Accordingly, the necessity for sewage sludge reduction or effective sludge-to-resource and sludge-toenergy using various pretreatment technologies is being raised (Choi et al., 2016). In order to increase the recycling rate of sewage sludge, the sewage sludge is currently being used as auxiliary fuel at thermal power plants through thermal treatment processes including drying, incineration, and carbonization; sludge-to-compost; fertilizer through the aging process; green soil and cover materials; and auxiliary materials for cement production (Yeon et al., 2016). In the case of sludge-tocompost, however, the processing time is too long that it requires too much land, equipment capacity, and high cost. Meanwhile, an environmental safety issue is being raised for the heavy metals included in sludge for the case of using it as fertilizer (Lee, 2004).
In addition to water pollution problems caused by global warming, the forest environment is also facing problems due to the inflow and spread of disease and pests. Although various preventive measures and plans have been developed for trees damaged by disease and pests, such as fumigation and incineration, lack of clear treatment methods had resulted in economic loss of forest resources. As such, it is necessary to find a solution to expand the use of domestic forest resources by applying high-value-adding technology to unused forest resources such as trees damaged by disease and pests and the by-products of forestry processes, etc. (Lee et al., 2015) Accordingly, research on torrefaction for various types of biomass such as the analysis of antioxidants from extracts using torrefied wood powder, farming byproducts, and sewage sludge is in progress (Nam et al., 2018; Gong et al., 2016). In this study, coagulant mixture of torrefied wood powder and natural materials is used for water treatment to evaluate the stability against heavy metals by comparing and analyzing the heavy metal contents after injecting the coagulant mixture and PAC. In addition, the sedimentation and heating values of sludge produced in the processes of mixing and coagulation after injecting the coagulants at a sewage treatment plant are investigated to verify the environmental stability of sludge and its potential of reuse as auxiliary fuel at thermal power plants.
2. MATERIALS and METHODS
In the preparation of coagulant mixture of torrefied wood powder and natural materials, this study selected the same condition withthat of the preparation of torrefied wood pellets in the previous research (Yang et al., 2016), which revealed that torrefied wood powder controls negative charges and adsorbs liquid according to the superheated steam treatment conditions. To make torrefied wood pellets, oak wood pellets with a water content of 12% were used. The researcher had commissioned Company S located in Gumi to have torrefied wood pellets treated at 250 °C for 25 minutes using a superheated steam treatment system. The pellets were then crushed witha laboratory high-speed pulverizer and sorted to a size of 75-106 um (Yang et al., 2017). In preparing the coagulant mixture, an inorganic polymer coagulant of PAC was used. The inorganic polymer compound with a structure of basic polynuclear complexes with cationic charges is strong coagulant for water treatment. PAC is a polymer-based coagulant made of hydrochloric acid and aluminum. In this study, colorless or pale yellow transparent liquid-type PAC was used. For PAC commonly used in Korean sewage treatment plants (10%), the concentration of aluminum oxide (Al2O3) is 10%. In this study, the concentration was reduced to 7% to produce PAC (7%). Finally, the test material for this experiment was made by adding 5 g of torrefied wood powder to 500 ml of PAC (7%), which was prepared according to the mixing ratio developed in the research on the optimal mixing ratio of coagulant mixture of torrefied wood powderand natural materials (Yang et al., 2019) and then stirring at 800 rpm for approximately 5 hours.
To evaluate the stability, sludge sedimentation rate, and sludge heating value of the coagulant mixture, effluent from the primary sedimentation tank of Daejeon Sewage Treatment Plant, having a high organic content in water, was collected. A jar test was performed to examine the stability of the coagulant mixture according to its conditions; supernatants were collected with the operation conditions of 140 rpm 2 min for rapid mixing, 40 rpm 20 min for slow mixing, and 30 min for settling. When collecting the supernatants, they were filtered through a syringe filter having 45 μm pores. Analysis items included Cr, Fe, Zn, Cu, Cd, As, Pb, Ni, and Hg, which are in the heavy metal category of “The Criteria For Water Quality Assessment (No. 2017-4)”, and the sedimentation rate and heating value of sludge generated after the jar test were analyzed.
In order to analyze the stability of the coagulant mixture prepared in this study, an analysis of heavy metals including Cr, Fe, Zn, Cu, Cd, As, Pb, Ni, and Hg, which are subject to “The Criteria For Water Quality Assessment (No. 2017-4)”, was performed. The analysis was commissioned to FITI Testing & Research Institute for sample analysis where spectrophotometry, luminescence spectroscopy, and mass spectrometry instrument analysis were performed three times.
In the experiment of the sedimentation of sludge generated in the sedimentation process through the mixing and coagulation processes of aquatic contaminants using the coagulant mixture, the sedimentation volume of flocs was measured for a certain period of time - every 1-10 min for 30 min - using a measuring cylinder. The flocs generated after the jar test were moved to a 1,000 ml measuring cylinder so that they do not break. For the comparison and analysis of sludge sedimentation with the existing water treatment agent, the sludge sedimentation of the coagulant mixture prepared in this study and PAC (10%) was compared based on the optimal injection amount.
To reuse sewage sludge as auxiliary fuel, it must satisfy the requirement of auxiliary fuel at thermal power plants: over 3,000 kcal/kg. To measure the heating value of sewage sludge, sludge settled after the Jar test was collected and dried in a drying oven at 105 °C to achieve water content of 10% or lower. For the measurement of the higher heating value, which is the criteria for absolute dry specimen, the value (kcal/kg) was measured five times using the Bomb Calorimeter (SDC series Calorimeter, YEONJIN S-TECH INC.), and then the lower heating value was calculated.
3. RESULTS and DISCUSSION
A jar test was conducted using effluent from the primary sedimentation tank at the DJ sewage treatment plant. After injecting 10 ml/L of each coagulant, which is the optimal amount based on the previous research, supernatants were collected, and then heavy metals (Cr, Fe, Zn, Cu, Cd, As, Pb, and Ni) were analyzed. The results are shown in Fig. 1.
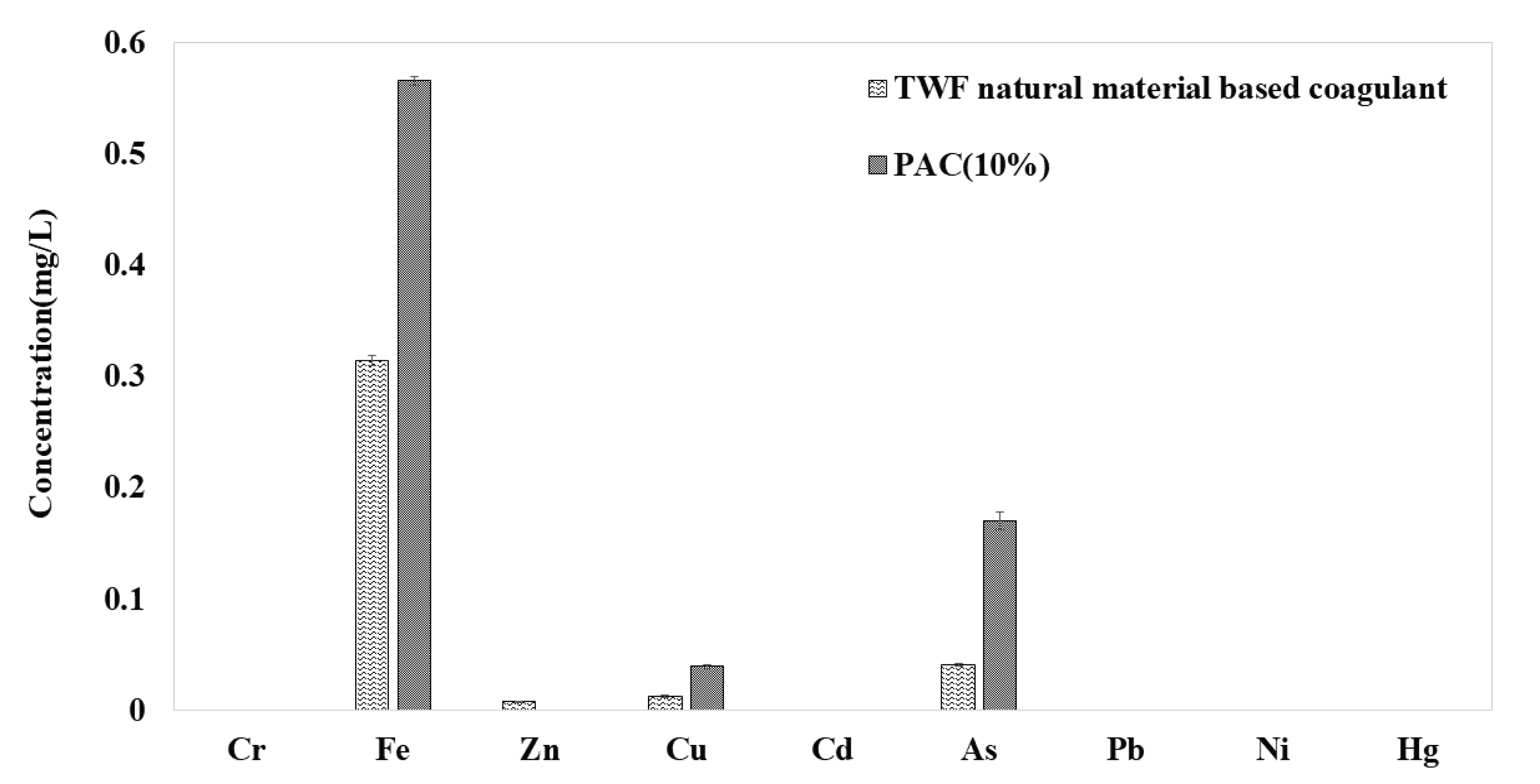
As a result of mixing, coagulation, and sedimentation processes using the same amount of PAC (10%) and the coagulant mixture, metals such as Cr, Cd, Pb, Ni, and Hg were not detected. It was alsofound that higher concentrations of Fe, Cu, and As were appeared in the water treated with PAC (10%) coagulation. The post-test results for Fe with different types of treatment agents showed that the average of the coagulant mixture was 0.3143 mg/L, while that of PAC (10%) was 0.5647 mg/L; the latter was approximately 0.25 mg/L higher. The results of the t-test verifying the differences between the groups (t=-60.914 and p=.000) showed a significant difference at the level of p <0.01. The post-test results for Cu with the different treatment agents showed that the average of the coagulant mixture was 0.012 mg/L and that of PAC (10%) was 0.038 mg/L; the latter was approximately 0.026 mg/L higher. The results of the t-test verifyingthe differences between the groups (t=-15.922 and p=.000) revealed a significant difference at the level of p <0.01. The post-test results for As showed that the average of the coagulant mixture was 0.0397 mg/L, while that of PAC (10%) was 0.17 mg/L; the latter was approximately 0.13 mg/L higher. The results of the t-test verifying the differences between the groups (t=-22.316 and p=.000) showed a significant difference at the level of p<0.01. According to the previous research on the adsorption of torrefied wood powder (Yang et al., 2016), the adsorption performance of iodine depending on the carbonization temperature was 590 mg/, which was a half of the maximum activated carbon. Therefore, the reason behind merely adding torrefied wood powder in the conventional PAC resulting in the reduced heavy metal contents in the water was because the powder adsorbed heavy metals in the coagulant mixture and lowered the contents. As for thecoagulant mixture, only a minimal amount of Zn (0.007 mg/L) was detected, which was confirmed to be significantly lower than the criteria of Zn for drinking water (3 mg/L). Therefore, if water treatment is performed usingthe coagulant mixture developed in this study, the concentrations of heavy metals could be less than half of that of the commercially available coagulant and it will be environmentally stable.
To compare and analyze the sludge sedimentation rate between the coagulant mixture prepared in this study and PAC (10%), the optimal amount, 10 ml, of the two was injected, and the sedimentation rates of sludge acquired from the mixing and coagulation processes were analyzed. Fig. 2 shows the sedimentation rates of sludge at a certain time interval.
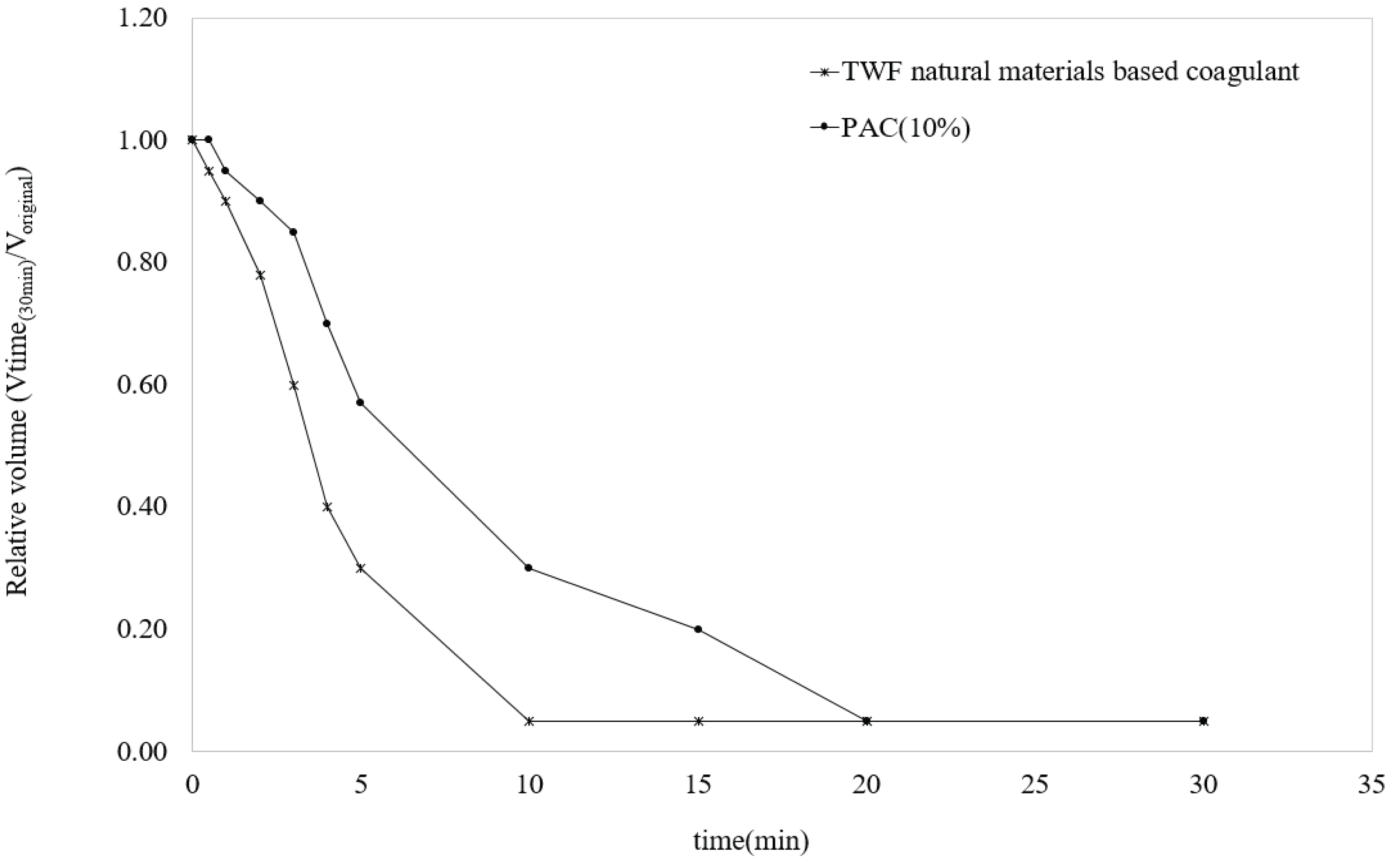
The sedimentation of sludge is basically divided into 4 types: independent, coagulation, interfacial, and compression sedimentations. When a uniform concentration of suspended matter is put in a measuring cylinder, light particles dispersed in stages are settled independently just as independent particles or coagulating particles. If sedimentation continues, interfacial sedimentation occurs and a clear layer is formed on the top, creating a distinct boundary. Finally, compression sedimentation is caused by the weight of agglomerated particles continuously applied (Baik et al., 2014). As shown above in Fig. 2, the sedimentation rate of the coagulant mixture within the first 5 minutes was approximately twice the conventional coagulant, PAC (10%). After approximately 10 minutes, the sedimentation of the coagulant mixture was almost completed, while the sedimentation of PAC (10%) took approximately 20 minutes for completion. The comparison of the slopes of the graph indicates that the sedimentation rate of the coagulant mixture is higher than that of PAC (10%). The faster sedimentation is considered to be because contaminants in the water cling together centering on torrefied wood powder of 75 μm or less, which was added to the coagulant mixture, forming larger-sized flocs than when only PAC is added.
To evaluate the possibility of reuse of the coagulant mixture by comparing and analyzing its sludge heating value, the optimal amount (10 ml) of the coagulant mixture and PAC (10%) was injected, and the heating value of formed sewage sludge was measured. The water content of sewage sludge, which was generated after the jar test with effluent from a primary sedimentation tank, was approximately 90%. This was dried in a drying oven at 105 °C to reduce the water content to 10% or lower, and the heating value was measured. Fig. 3 shows the results of the dry-basis heating value of the sewage sludge.
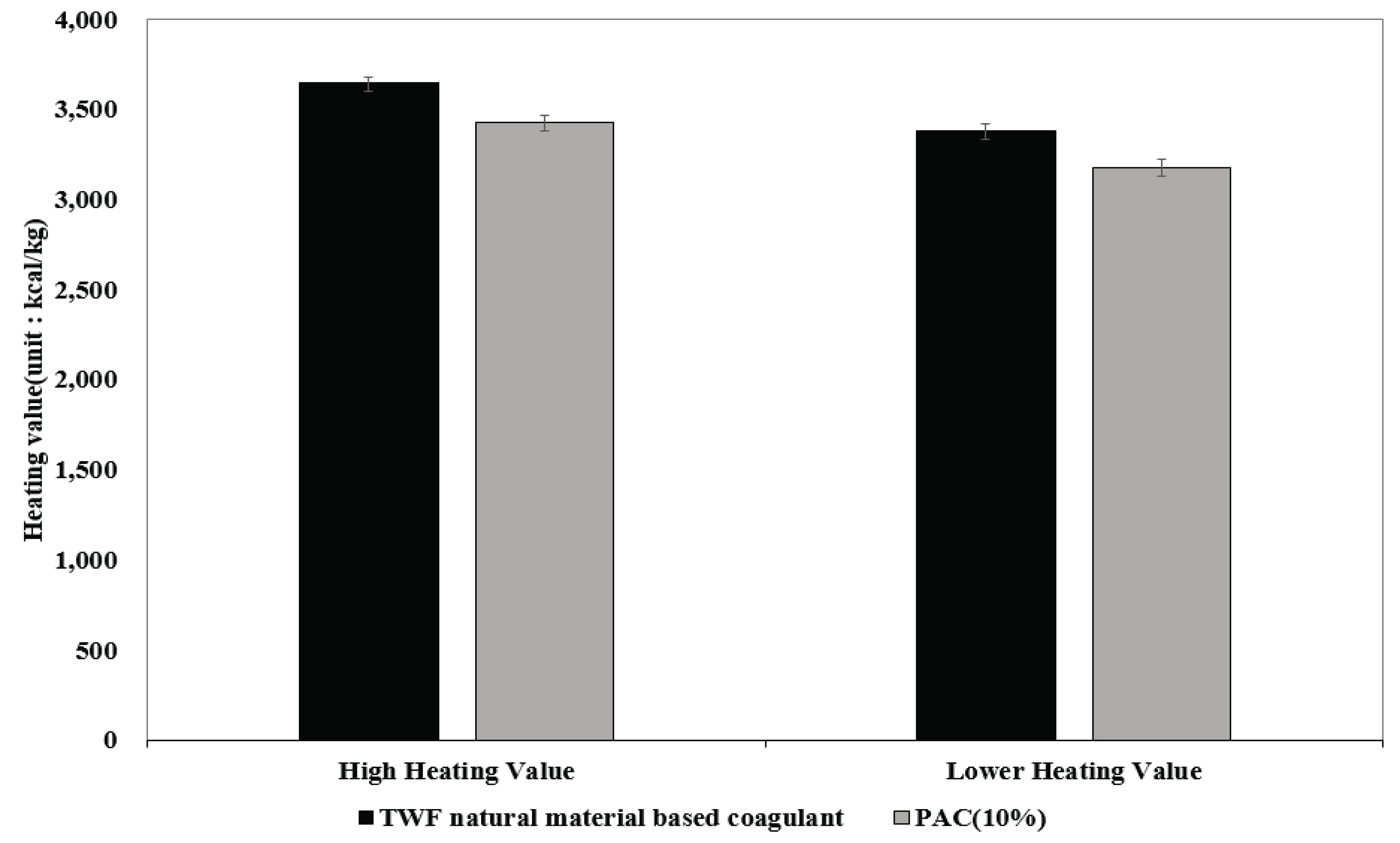
As a result of the post-test of the higher heating values based on different treatment agents, the average of the coagulant mixture was 3,656 kcal/kg, while that of PAC (10%) was 3,428 kcal/kg; the PAC group showed approximately 227 kcal/kg lower result. The t-test verifying the difference between the two groups (t=7.247 and p=0.002) showed that there was a significant difference at the level of p<0.01.
Before analyzing the heating values of the coagulant mixture and PAC (10%), it is essential to perform a drying process to achieve the water content of less than 10%. During the same drying process, the coagulant mixture containing torrefied wood powder took less drying time than PAC (10%). The drying process is necessary, and it should satisfy the condition of more than 3,000 kcal/kg to be used as auxiliary fuel at thermal power plants. The dry-basis lower heating value of sewage sludge produced by injecting the coagulant mixture was 3,378 kcal/kg, and that of sewage sludge produced by PAC (10%) was 3,171 kcal/kg; although both coagulants satisfied the requirements of the auxiliary fuel, the lower heating value of the coagulant mixture was revealed as higher by approximately 200 kcal/kg.
As a result, it was confirmed that the heating value of sewage sludge generated by the coagulant mixture developed in this study is approximately 200 kal/kg higher than that of the conventional coagulant. Thus, the coagulant mixture can produce sludge with higher heating values compared to that of the commercially available coagulant, PAC (10%), and the possibility of achieving its stable utilization for energy reduction as an auxiliary fuel is confirmed.
4. CONCLUSION
This study used the commercially available coagulant, PAC (10%), and coagulant mixture of torrefied wood powder and natural materials for water treatment and compared and analyzed the heavy metals in treated water to evaluate the stability against the heavy metals, and analyzed the sedimentation and heating values of sludge generated after the injection of the coagulants. As a result, the following conclusions were drawn:
The analysis of heavy metals from the coagulant mixture and PAC (10%) revealed that the amounts of Fe, Cu, and As detected from PAC (10%) were more than double compared to the coagulant mixture.
The analysis of the sludge sedimentation rates of the coagulant mixture and PAC (10%) revealed that the rate of the coagulant mixture was higher than the conventional coagulant, PAC (10%), within the first five minutes, and the sedimentation is completed for coagulant mixture in 10 minutes, while it took 20 minutes for PAC (10%). The sedimentation rate of the coagulant mixture was faster than that of PAC (10%).
The dry-basis lower heating value of sewage sludge produced by injecting the coagulant mixture was 3,378 kcal/kg, and that of sewage sludge produced due to PAC (10%) was 3,171 kcal/kg; both coagulants met the requirements to be used as auxiliary fuel at thermal power plants.
In conclusion, it was revealed through the lab scale results that using the coagulant mixture prepared with torrefied wood powder in this study for water treatment in mixing and coagulation processes can result in better stability against heavy metals, faster sedimentation in sedimentation tanks, shorter sewage process time, and approximately 200 kal/kg higher heating value compared to the conventional coagulant, PAC (10%). Going forward, it is necessary to conduct additional empirical studies on the application of the coagulant mixture in actual sewage treatment plants.