1. INTRODUCTION
Recently, a slogan recalling low carbon green growth is frequently encountered in relation to global warming. This is caused by a wide variety of complex causes, but the most influential factor is the increased concentration of carbon dioxide produced by the burning of fossil fuels. Therefore, in order to reduce the concentration of carbon dioxide in the combustion process by even a little, the service life of materials containing carbon needs to be extended. It is also environmentally useful to prolong the life of wood and wood-based materials as they are the world’s most carbon-rich renewable resources.
This research group examined the possibility of dyeing regenerated fibers by reactive, direct, and bat dyes to recycle waste medium density fiberboard (wMDF) as it is currently not recycled at all in spite of it being the most produced wood material in Korea. As a result, it was confirmed that dyeing is relatively easy with certain dyes that are mainly used for dyeing cellulosic materials, and that there is no significant difference in dyeing characteristics between virgin fibers and regenerated fibers (Ju et al., 2017). In addition, optimal dyeing conditions (dye concentration, amount of salt and alkali added, dyeing temperature, and time) were obtained when dyed regenerated fibers from wMDF were stained with Reactive Red H-E3B (Bis-monochlorotriazine (MCT) / MCT type) and Reactive Red RB 133% (Bis-MCT / Vinyl sulphone type)(Ju et al., 2019). However, in order to utilize the wMDF obtained around our lives as a functional molding materials, Re-WDF needs to be manufactured using natural dyes that can be obtained around our lives.
Dyeing with natural dyes is mainly applied to fabrics. Natural dyeing for cellulosic fibers was performed mainly on Hanji. The dye materials used for natural dyeing of Hanji include gardenia, saffron, safflower, cork-tree, pagoda tree, onion-peelings, mugwort, clove tree (Jeon et al., 2000; 2003; 2006), Neolitsea sericea Koidz extract (Jo et al., 2007), sappan wood, gardenia, gallnut (Park et al., 2009; 2010; 2011), flowers of pagoda tree, gardenia (Yoo et al., 2009; 2011), gallnut, leaves of amur maple, nutshell of chestnut, persimmon juice (Lee et al., 2009), Alnus japonica fruit extract (Choi et al., 2009). However, studies of dyeing regenerated woody fibers with natural dyes have not been conducted until now.
Therefore, we obtained regenerated wood fiber from the waste furniture which can be easily accessed around our daily lives, and examined the feasibility of producing dyed regenerated fiber given various color functions by natural dyes. The natural dyes used in this study were examined for the dyeing properties of representative red-based sappan wood, yellow-based gardenia and blue-based commercial indigo.
2. MATERIALS and METHODS
Regenerated fiber was used by dissociating MDF with a specific gravity of 0.62 manufactured from pitch pine (Pinus rigida M.) and urea resin. The regenerated fiber was prepared by 250 ml of distilled water added to 50 × 50 × 12 mm MDF and immersed at 25 °C for 48 hours. After defibrated with a home-use mixer for 5 minutes, the resultant was filtered through a 300 μm screen and dried.
Chinese sappan wood(Caesalpinia sappan L) and gardenia(Gardenia jasminoides E.) were purchased as dyeing materials, and the moisture content was 9.5% and 8.0%, respectively. The extractions of sappan wood and gardenia were carried out using distilled water to set the amount of raw materials to 10, 20, 30, 50, 100 g/L, heated to 90 °C for 50 minutes, and then maintained for 30minutes at 90 °C. Indigo (India) powder was used as is on the market. Aluminum ammonium sulfate dodecahydrate, Copper (II) acetate anhydrous, Iron (II) sulfate heptahydrate (Extra pure, Daejung) as mordants, sodium hydrosulfite and sodium carbonate andydrous (Extra pure, Daejung) as a reducing agent of indigo dye and 0.1M sodium hydroxide solution as a pH control agent were used.
The dyeing was performed in a tall beaker with regenerated fiber and the definite amount of raw materials extracts (10, 20, 30, 50, 100 g/L) at a liquid ratio of 1:50 and for 60 minutes at 60 °C. The effects of dyeing temperature and time of sappan wood and gardenia at 50 g/L of raw materials were examined by varying the temperature of 50, 60, 70 and 80 °C at 60 minutes and dyeing time of 30, 60, 90, 120 and 150 minutes at 60 °C. The premordanting of sappan wood and gardenia were conducted for 40 minutes at 40 °C, 5% (O.W.F) addition of the mordant, in a liquid ratio of 50 : 1, and then filted and washed. Subsequent dyeing was carried out with 50 g/L of sappan wood and gardenia extracts for 60 minutes at a liquid ratio of 1:50 and 60 °C. Indigo, a commercial natural dye, was dyed under the same conditions at indigo concentration of 1, 3 and 5% (O.W.F).
Sheets for measuring the dyeing property, color and light fastness were manufactured by adding the same amount of distilled water to the regenerated fiber dyes in different conditions and blended with a mini-mixer for 2 minutes, and then filtered through the Whatman filtering paper, and compressed for 5 minutes at 50 °C.
The surface color of the Re-WDF was measured using Minolta CM-3800d (Japan). The color difference according to the dyeing was calculated by the difference between the sheets prepared by the same method put the water and the dye solution to the regenerated fiber. The K/S value was calculated by Kubelka-Munk equation after measuring the surface reflectance of each dyed sample.
Light fastnesses of Re-WDF were evaluated using an accelerated weathering tester (QUV / SP, USA). UVB-313 was used as a lamp and evaluated for color difference in CIE Lab color space before and after UV irradiation treatment at a constant illumination intensity of 0.67 W/m2 and temperature of 50 °C.
3. RESULTS and DISCUSSION
Dyeing characteristics of regenerated fibers from wMDF with red-based sappan wood which are generally known as polychromatic natural dyes and yellow-based gardenia monochromatic natural dyes were studied. The sappan wood contains dozens of pigments, but brazilin, a dihydropyran type dye and has many benzene cyclic structures, is known as a major coloring material (Lee et al., 2002). The gardenia is a carotenoide type dye and is known to be yellow by water-soluble crocin which is mainly crocetindigentiobioside (Tak et al., 2010). In order to prepare the Re-WDF from wMDF using sappan wood and gardenia, the dyeing characteristics of regenerated fiber were examined by different amounts of dyeing materials. First, the dyeing solution was obtained by extracting 10, 20, 30, 50, 100 g/L of sappan wood and gardenia for 50 minutes at 90 °C.
The dyeing yield (K/S) of Re-WDF with each dyeing solution at liquid ratio 50:1, 60 °C for 60 minutes is shown in Fig. 1. The dyeing yield of the two dyes at the wavelength of 450 nm increased as the amount of dye materials increased, and gardenia’s dyeing yield was very high compared to sappan wood’s. It was found that the maximum absorbance of the gardenia dyed fiber on the UV-VIS spectrum was shown at 450nm. This is very similar to the results reported by Watanabe et al. (1998) that the 441 nm absorption peak corresponds to crocin and crocetin.
The color and color difference of Re-WDF dyed by different amounts of sappan wood and gardenia and its color of before and after a UV treatment for 24 hours are shown in Table 1.
The hue of regenerated woody fiber(control) is a yellow tone of 0.2Y. The color of Re-WDF dyed with sappan wood displayed 9.0 ~ 9.9YR. There is almost no change despite of the fact that the amount of dye materials increased from 10 g/L to 100 g/L. The increased a* and b* indicates that red and yellow becomes stronger. As the amount of dye materials increased, the color difference of Re-WDF dyed with sappan wood also increased. The color difference at dye materials of 10 g/L was 3.33 which corresponds to “appreciable” by the National Bureau of Standards (NBS). The color differences at 20, 30, and 50 g/L were 6.99, 8.76, and 11.10, respectively, and that corresponds to “Much appreciable” (color difference 6.0–12.0) meaning they were colored with extremely marked changes. In addition, as the amount of sappan wood increased from 10 to 100 g/L, the values decreased slightly from 7.4 to 6.7, while chromas increased from 4.0 to 5.9.
For gardenia, its hue showed no change from 0.9 to 0.6Y even with the increased the amount of dye materials from 10 g/L to 50 g/L, and 9.5YR at 100 g/L. As the amount of gardenia increased, both a* and b* increased indicating that red and yellow became stronger. In particular, the color difference of Re-WDF stained with gardenia of 10 g/L was 21.71 as it corresponds to another color of NBS's “very much” (12.0+). Gardenia’s coloring power was excellent and its color difference became larger as the amount of dye materials increased.
Fig. 2 shows the light fastness of Re-WDF regarding the amount of sappan wood and gardenia as they were evaluated by the color difference in CIE Lab color space before and after a 24hr UV irradiation with an illumination of 0.67-W/m2 at a temperature of 50 °C using accelerated weathering tester.
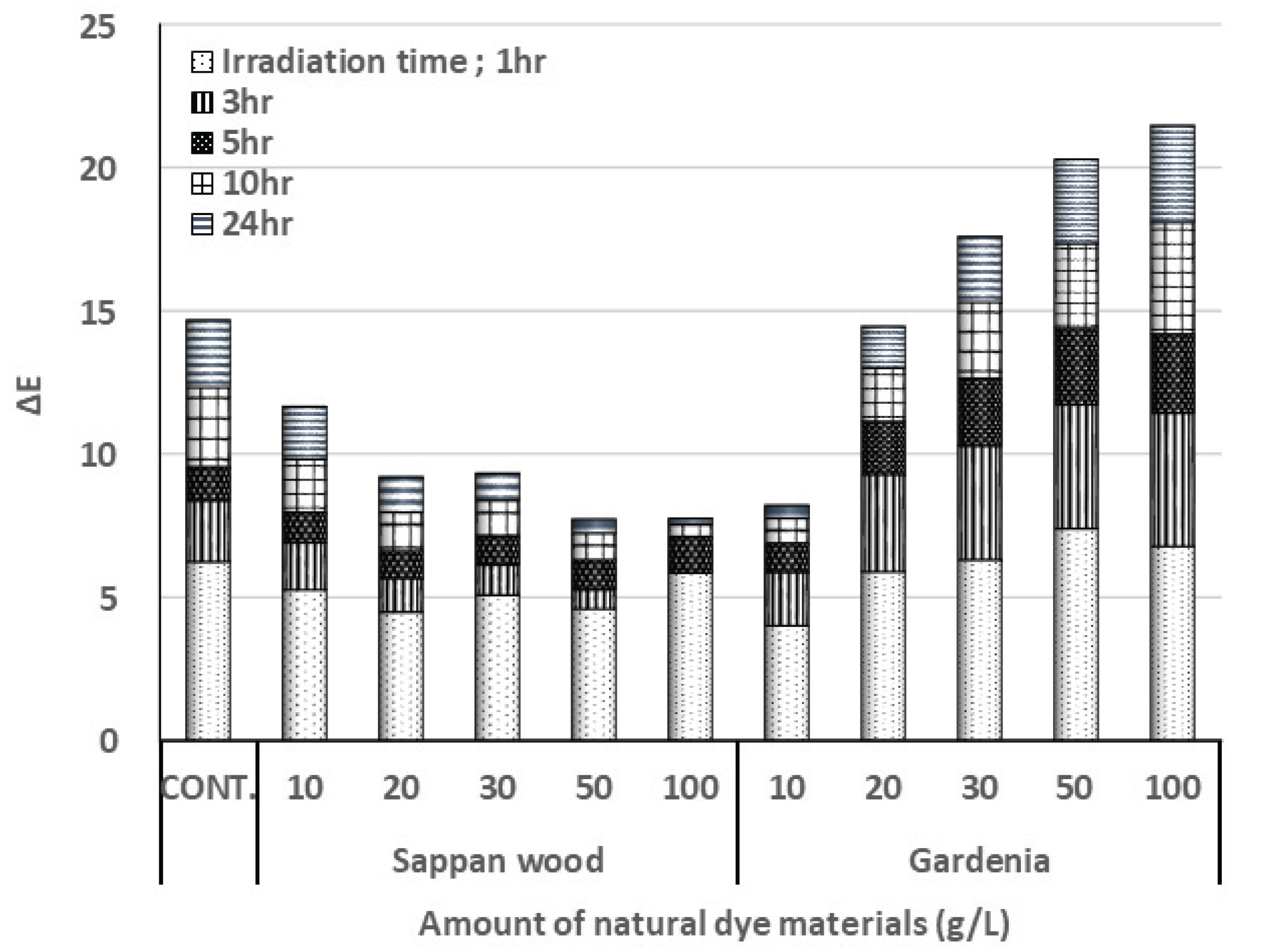
The color difference of the un-dyed regenerated wood fiber from wMDF showed a great color difference by irradiation of ultraviolet and it was confirmed that the wood fiber itself was discolored by ultraviolet. The light fastness of Re-WDF prepared by varying the amount of sappan wood and gardenia tends to be opposite. As the amount of sappan wood increased, the color difference of Re-WDF after a UV irradiation for 24 hours decreased, while gardenia increased. This is due to the insufficient dyeing at low sappan wood and its color difference of Re-WDF is affected by discoloration of the fiber itself. Gardenia has a very poor light fastness. Therefore, it is thought that dyeing yield increases as the amount of gardenia increases and the color difference becomes larger and the light fastness tends to decrease.
From the results above, it was possible to produce Re-WDF of YR or Y series by sappan wood and gardenia and the optimum amount of dye materials was 30 ~ 50 g/L.
Generally, a sappan wood extract, a polychromatic dye, is known to show different colors by pH. Park et al., (2010) reported that a cotton fabric dyed with a sappan wood extract, a* values were significantly reduced and b* values were significantly increased by addition of acetic acid and colored to yellow in acid and red in alkali. However, the color of dyeing by sappan wood extract is not influenced by pH alone, but is considered to be greatly affected by mordants and the type of water used. After adjusting the pH of sappan wood extract (50 g/L) to 4.5 ~ 12.3 with 0.1M NaOH solution, the resulting color properties of Re-WDF are shown in Table 2.
Both color yield and color difference showed the highest value at pH 9.1. The a* was 10.31 at pH 4.5 but increased to 13.07 at pH 9.0 and the b* increased to 34.62 from 30.44. The results showed that both the red and yellow were strengthened. However, the hues of Re-WDF with sappan wood at pH 4.5 ~ 12.3 were 9.4YR ~ 8.1YR. The hues were slightly reddish yellow rather than red and closer to reddish yellow with an increasing pH. Therefore, the color of dyed woody fiber with sappan wood can be expressed in various colors by other factors such as the type of water used in dyeing, pH, etc. Thus, it is regarded that more careful attention is required to develop a consistent color.
Dyeing of the fibers is accomplished by diffusing the dye onto the fiber surface, adsorbing it onto the fiber surface, and diffusing it into the fiber. The dyeing time depends on the diffusion speed of dye into the fiber and when the dyeing temperature is increased, the kinetic energy of the dye molecules increases to accelerate the dyeing speed, shortens the dyeing equilibrium time, and affects the amount of dye fixation. When dyeing regenerated wood fiber by sappan wood and gardenia at dye materials of 50 g/L, the dyeing yield according to dyeing temperature and dyeing time is shown in Fig. 3 and 4, respectively. At 60 minutes of dyeing time, the dyeing yield of Re-WDF dyed by changing the dyeing temperature to 50 ~ 80 °C showed little difference between 1.77 ~ 1.96 in sappan wood. The gardenia showed its highest 7.04 at 60 °C and then decreased again. Hues and color differences of Re-WDF dyed with sappan wood by changing the dyeing temperature also showed no significant difference between 9.0 ~ 9.5YR, 12.93 ~ 14.44, and Gardenia 0.4 ~ 1.2Y, 58.02 ~ 59.51. Therefore, the temperature should be above 50 °C for the sappan wood and 60 °C for the gardenia.
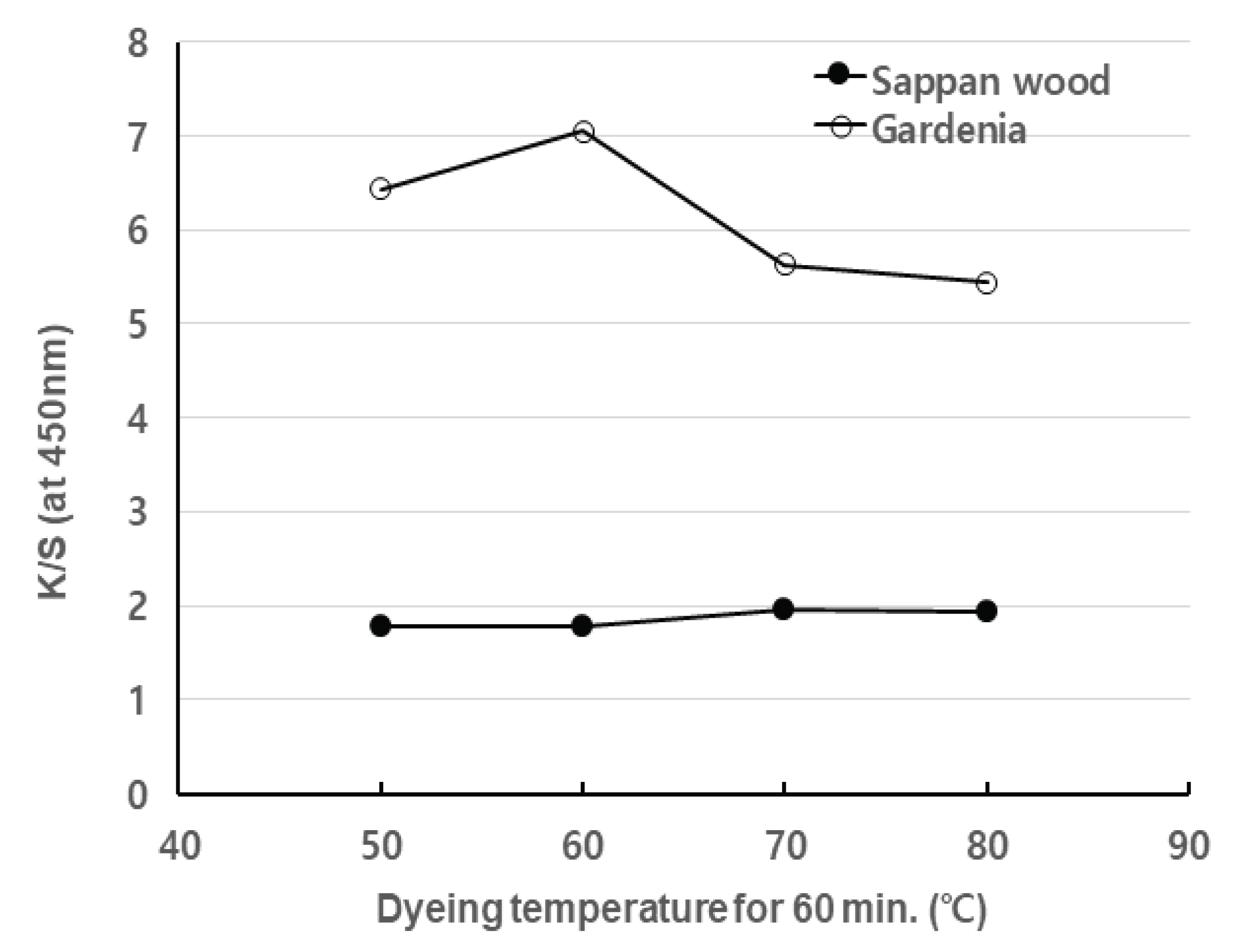
By varying the dyeing time to 30 ~ 150 minutes, the dyeing yields of Re-WDF dyed with sappan wood and gardenia at 60 °C of dyeing temperature were slightly higher at 60 minutes but there were little difference between 30 ~ 150 minutes in 2 type natural dyes. Hues and color differences of Re-WDF dyed by changing the dyeing time also showed no significant difference between 9.0 ~ 9.5YR, 12.93 ~ 14.44 in sappan wood, 0.4 ~ 1.2Y, 58.02 ~ 59.51 in gardenia, respectively. Therefore, the dyeing time at 60 °C should be sufficient for 60 minutes.
Based on the results above, we concluded that dye materials of 50 g/L, dyeing temperature of 60 °C and dyeing time of 60 minutes are suitable for the production of Re-WDF by sappan wood and gardenia.
The most important things in dyeing regenerated fibers are the adsorption and bonding between the fibers and the dyes. In general, hydrogen bonds or van der Waals forces form bonds between the components of the natural dyes and fibers. However, inducing coordination bonds by adding metals can increase the dyeing yield and improve the light fastness. The mordanting methods of natural dyes include premordanting, postmordanting and simultaneous mordanting as the color and color yield of dyed fibers vary by the these methods. Re-WDFs are prepared according to premordanting with aluminum ammonium sulfate dodecahydrate (Al), Copper (II) acetate anhydrous (Cu), Iron (II) sulfate heptahydrate (Fe), then they get dyed with sappan wood and gardenia extracts solution. The absorbance curves of these for each wavelength are shown in Fig. 5.
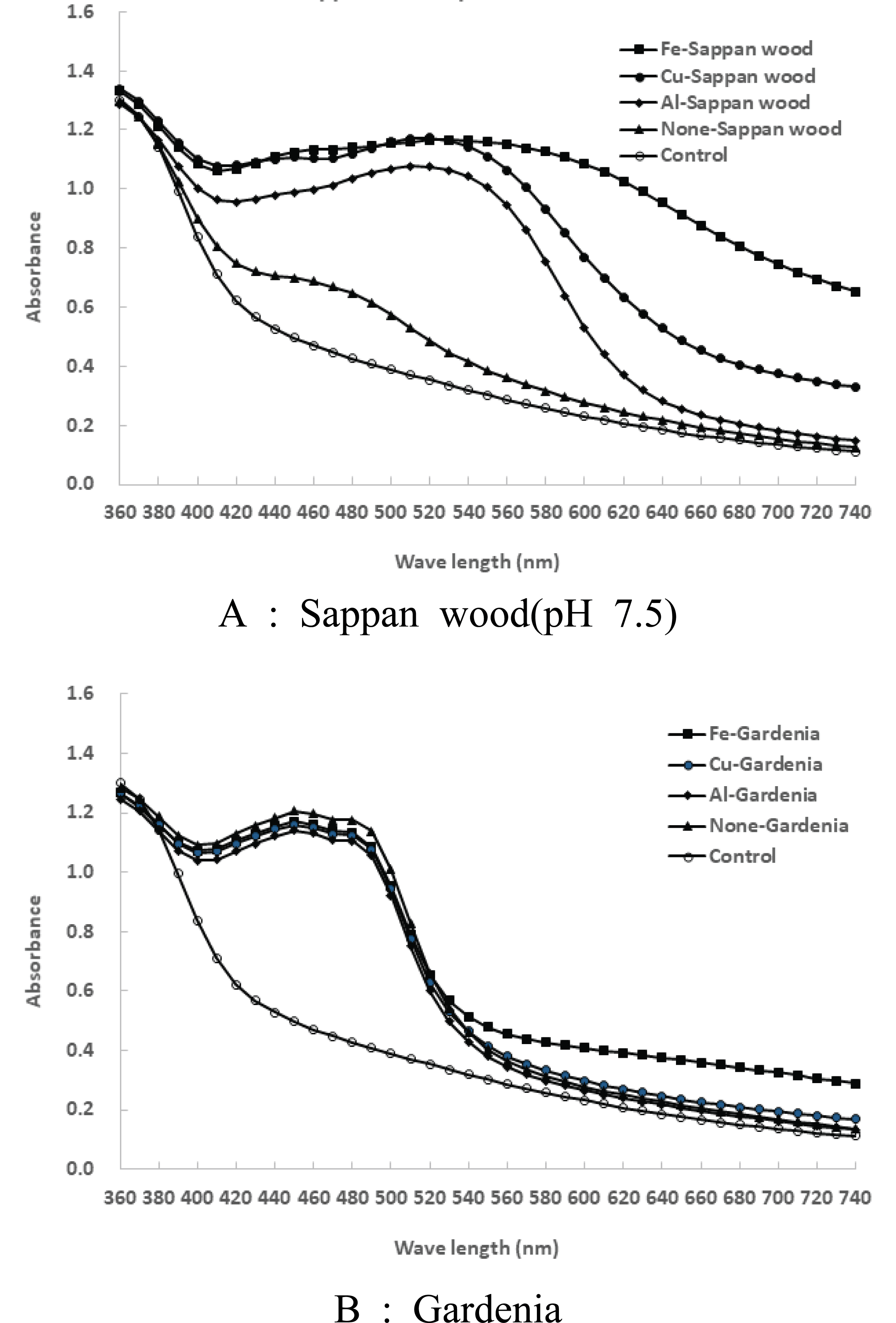
The absorbance of the regenerated fiber dyed with sappan wood (pH 7.5) was higher in Al, Cu and Fe mordant than in no mordant. The wavelength showing the maximum absorbance shifted to 510 nm for Al, 520 nm for Cu, and 530 nm for Fe. However, in case of gardenia it was thought that there was almost no difference in color according to the mordants because it showed almost no difference in the wavelengths showing the maximum absorbance and absorbance curve patterns regardless of the mordant type.
Fig. 6 shows the dyeing yield of Re-WDF dyed with sappan wood and gardenia after premordanting by Al, Cu and Fe mordants at λmax. The dyeing yield of nonemordant Re-WDF with sappan wood was 1.53, but Al premordant was 5.01, Cu was 6.47, and Fe was 6.35. The dyeing yields were greatly increased by premordanting from the three type mordants. On the other hand, the dyeing yield was the highest in nonemordanting in the case of gardenia and there was no significant difference from the three different mordants.
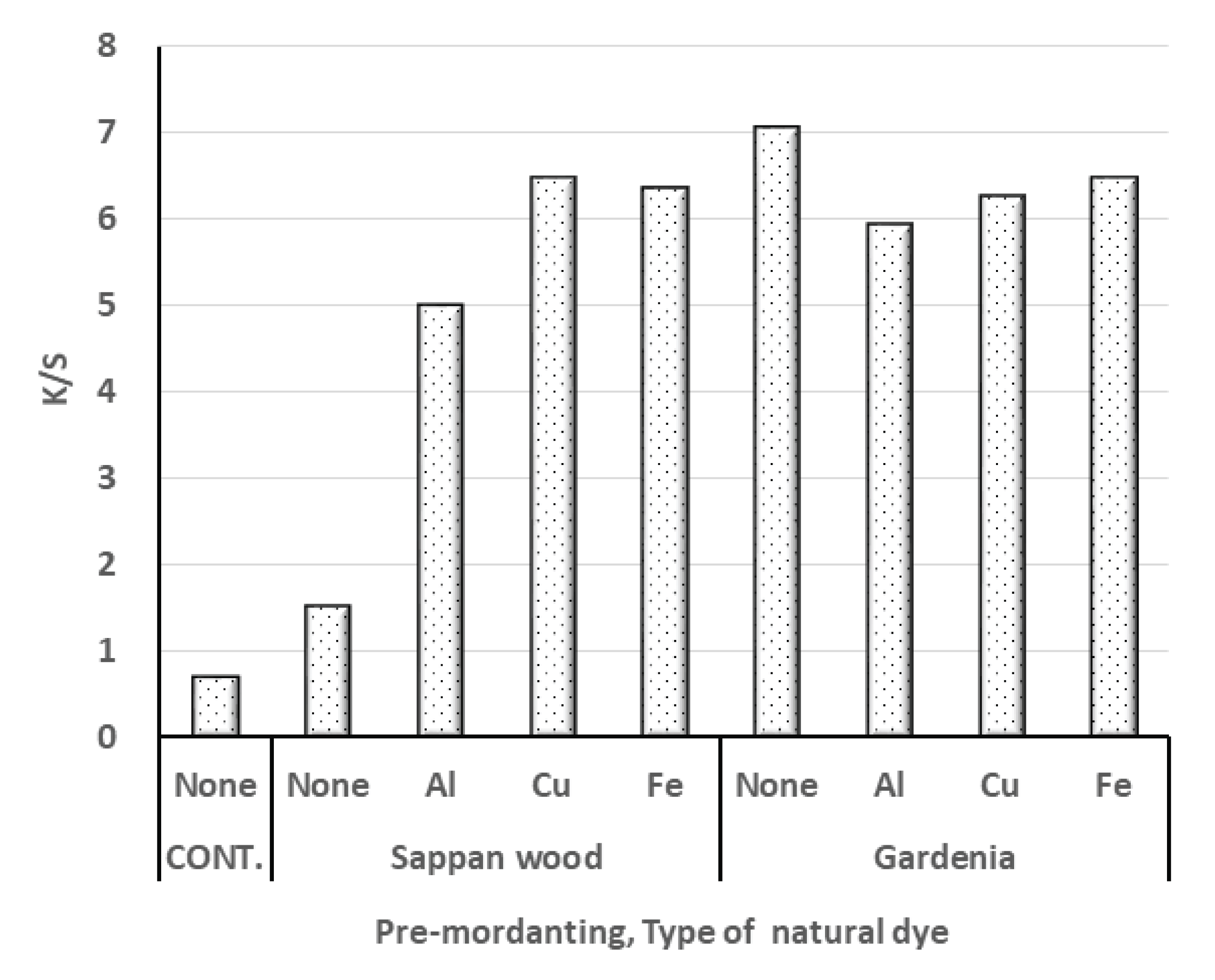
Table 3 shows the color characteristics of Re-WDF dyed with sappan wood and gardenia after premor-danting with Al, Cu and Fe mordants. The color difference of Re-WDF dyed with only sappan wood was 11.7, Al premordanting was 42.39, Cu 43.16, Fe 48.68 and the colors completely changed by premordanting. The hue of Re-WDF dyed with only sappan wood was reddish yellow (9.2YR), Al premordanting was 4.6R, Cu 4.2R, but Fe premordanting was colored purplish red (6.9R). The hue of Re-WDF dyed with gardenia, all three types of mordants were 0.8 ~ 2.8Y, which is slightly darker than 0.4Y of nonemordanting, and there was little difference in color according to mordants. The color of the Re-WDF dyed with nonemordanting sappan wood showed almost no difference between 9.2YR before a 24 hours of UV treatment and 8.9YR after treatment. However, the color of Re-WDF dyed with sappan wood after Al premordanting was varied from 4.0R to 9.0R by a UV treatment for 24 hours, and Cu premordanting was transformed from red to slightly yellowish red (from 4.2R to 1.9YR), and Fe premordanting from 5.7 YR to 6.9 RP. On the other hand, there was almost no change in color after a 24 hours of UV treatment in the case of gardenia for either none or premordanting with three type of mordants.
Fig. 7 showed the color difference after a 24 hours of UV irradiation treatment for Re-WDF which was dyed with sappan wood and gardenia after premordanting by three mordants of Al, Cu and Fe. The color difference of regenerated wood fiber after irradiating the ultraviolet for 24 hours was much greater comparing to the color before the ultraviolet irradiation. This means that the undyed regenerated fiber is also greatly discolored by ultraviolet irradiation. The color difference of undyed regenerated fiber after a UV treatment was greater than that of Re-WDF with sappan wood but was smaller than that of gardenia. From this result, it was confirmed that light fastness was somewhat improved by dyeing with sappan wood, but was deteriorated by dyeing with gardenia. To rank the degree of light fastness regarding types of mordants, the highest was Fe premordanting regenerated fiber at both sappan wood and gardenia dye followed by Cu and Al mordant.
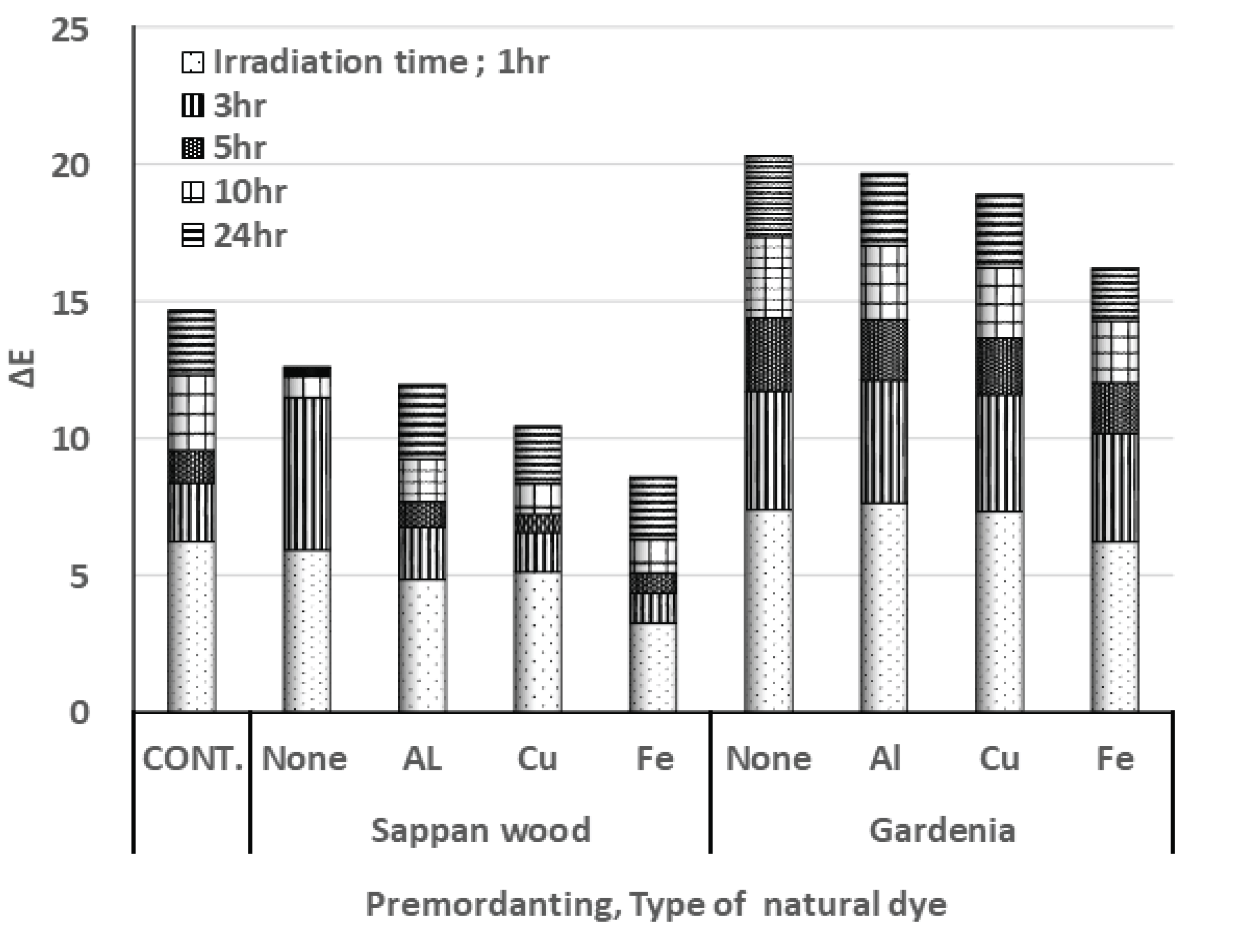
Indigo is a classic blue-based natural dye obtained by extracting and fermenting from Persicaria tinctoria. Indigo is not soluble in water and is used to make water-soluble leuco compounds by reducing them with a reducing agent such as sodium hydrosulfite under alkali for dyeing. The leuco compound has a strong affinity with cellulose and it is dyed blue when absorbed into cellulose and oxidized with air or an oxidizing agent. In this study, the possibility of producing blue tone Re-WDF was investigated with commercially available indigo powder, sodium hydrosulfite and sodium carbonate anhydrous as reducing agents, and by air oxidation. The color and color difference of Re-WDF dyed with different indigo concentrations of 1, 3 and 5 (%, O.W.F) and the colors before and after a 24 hours of UV treatment are shown in Table 4. The maximum wavelength of indigo-dyed regenerated fibers was 650 nm, and as the concentration of indigo increased from 1% to 5%, the dyeing yields increased from 0.43 to 6.69.
In addition, the color difference was 13.03 at indigo concentration of 1%, and it greatly increased as the concentration increased. The color of the Re-WDF with different concentrations of indigo was greenish yellow series (2.0GY) at 1%, green series (9.4G) at 3% and blue series (7.9B) at 5%. Therefore, it is possible to manufacture Re-WDF exhibiting a green and blue-based color by adjusting the concentration of indigo.
Fig. 8 showed the color difference of Re-WDF with different indigo concentrations by ultraviolet irradiation time. As the concentration of indigo increased from 1% , 3% to 5%, the color difference after a 24hr UV irradiation decreased to 11.88, 7.73, and 4.25, and that greatly improved light fastness. Most natural dyes have changed to another color with NBS units of color difference of 12 or more after a 24 hours of ultraviolet irradiation, but indigo is “appreciable” (critical remark of color difference of NBS). The color fastness of indigo was relatively good.
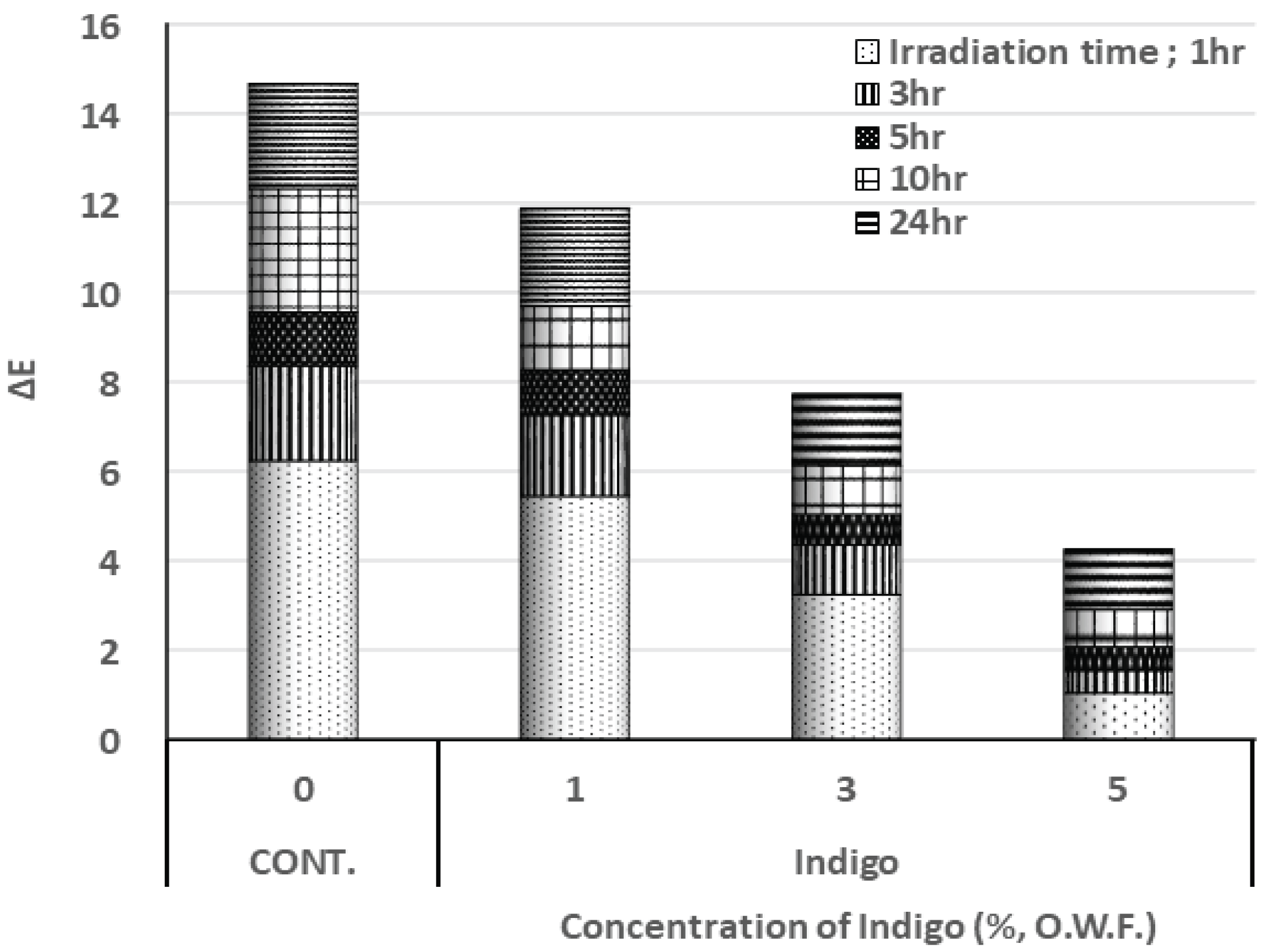
Based on the results above, the colors that can be developed by natural dyes such as sappan wood, gardenia and indigo on Re-WF from wMDF are shown in Table 5. It was possible to prepare Re-WDF with sappan wood showing R- and YR-based color by Al, Cu premordanting and RP-based color by Fe premordanting. In the case of gardenia, only Y-based color was developed by none, Al. Cu and Fe premondanting. Indigo was able to produce Re-WDF that exhibited GY tone color at 1% concentration, G tone at 3%, and B tone at 5% or more.
4. CONCLUSION
The results of the dyeing characteristics of regenerated fiber from wMDF made of pitch pine and using natural dyes such as sappan wood which is polychromatic natural dyes as red series, monochromatic gardenia as yellow series and indigo as blue series were as follows.
Indigo was able to produce Re-WDF that exhibited GY tone at 1% concentration, G tone at 3%, and B tone at 5% or more. Indigo had the best light fastness, followed by sappan wood and gardenia. However, in the case of sappan wood, the light fastness was somewhat improved by premordanting, but gardenia’s was poor by premordanting.
The dyeing yield and color difference of Re-WDF dyed with sappan wood and gardenia increased as the amount of dye materials increased from 10 g/L to 100 g/L. The optimum dyeing temperature and dyeing time were examined at 50 g/L of dye materials for 60 minutes at 60 °C. Under these conditions, Re-WDF dyed with sappan wood developed YR series color, and gardenia Y series color. The colors of Re-WDF with sappan wood extract solution (distilled water) adjusting to pH 4.5 ~ 12.3 were 9.4YR ~ 8.1YR, which were yellow with a little bit of red. The hue of RE-WDF dyed with only sappan wood was reddish yellow (9.2YR), Al and Cu premordanting were Red (Al 4.6R, Cu 4.2R), but Fe premordanting was purplish red (6.9R). In the case of gardenia, only Y-based color was developed by none, Al, Cu and Fe premondanting.
It is possible to manufacture blue, red, and yellow Re-WDF by natural dyes, but more research is needed to improve the light fastness and discuss the relationship between the dye, water, mordanting method, and pH, etc.