1. INTRODUCTION
Due to an increase in the interest in wood as an environmentally friendly construction material as well as in wooden materials, research development is being actively carried out on handling increasing wood and wooden material consumption, along with new wooden compound materials based on composition between daily waste materials, agricultural waste materials, etc. and wooden materials for the purposes of achieving a stable supply of wooden raw materials as well as developing a replacement raw material for insufficient wooden resources (Kim et al., 2001). Although the sawdust used in this study, which is a by-product in the sawing process, is produced in large amounts, due to its properties which require a large amount of resin, as well as thermo compression time which lengthens during manufacturing of boards, only a small quantity of sawdust had been used to achieve the smoothness and surface hardness of Particleboard. Also, despite the fact that the boards which utilized ricehusk, an agricultural by-product, had many difficulties in commercialization due to the properties of the material, research had progressed in various ways (Oh et al., 2005; Oh et al., 2010; Oh, 2014). On the other hand, wooden raw materials are being gradually transformed from thoseoriginally manufactured only for wooden materials into compounded environmentally friendly materials which include functionality. A variety of research and development in particular is making progress regarding environmentally friendly materials which take into consideration their durability and functionalities (Park et al., 2013; Park et al., 2012; Hwang and Oh, 2017). Charcoal is the most easily accessible environmentally friendly material, and its usable field is being widened as further new use methods are being developed after identifying numerous features such as air and water purification, far-infrared radiation release, electromagnetic wave shielding, etc. Also, with the increase of interest in health, products which utilize charcoal have been produced in large quantity such that the use of charcoal has shown a noticeable recent increase. As such, charcoal is being newly recognized as an environmentally friendly raw material, and shows large utilization.
Choi et al. (2000) manufactured boards which utilized waste wood materials and charcoal and measured the material properties, and confirmed the result that its strength properties were relatively lower than existing boards but due to the low preservability and heat conductivity of strawberries, and checked its use potential as an ecological material, whereas Lee et al (2004, 2005) manufactured boards in various conditions by using fine charcoal, measured their material properties and confirmed their performance, and confirmed the release amount of far-infrared radiation atthe same level with fine charcoal, and an extraordinary adhesiveness of ethylene gas. Lee et al. (2006) confirmed the formaldehyde radiation reduction effect of boards made of black coal manufactured by carbonizing daily waste. Also, Seo & Lee (2010) manufactured black coal boards by using biologically and environmentally friendly natural plasmatic concentrated additive, and confirmed that it could be utilized as a residential environmental material for indoor air quality management. Also, Park et al. (2012, 2013) used green tea, charcoal and wooden fabric to manufacture the compounded boards in various conditions andmeasure their material properties, and carried out research relevant to material development as an environmentally friendly material. Hwang & Oh (2017) investigated the material properties of boards manufactured using rice husk and charcoal, whereas Kim (2017) had manufactured boards by using ricehusk and charcoal to develop insulating materials for structural purposes.
This study manufactured board per mixing ratio and density of ricehusk and charcoal by adding charcoal, an environmentally friendly raw material,to ricehusk, an agricultural by-product, and sawdust which emerges during the sawing process, as a part of functional development, measured its physical properties and reviewed its usability.
2. MATERIALS and METHODS
The sawdust which emerges in the sawing process of thinned logs of Larix kaemferi C was used by purchasefrom a market sawmill, and for evenness of the sample during the manufacture of the board, particle size was selected as 18mesh by using a sorter (Shinchang, vibrator), while the water content percentage was adjusted to less than 6%.
The ricehusk was purchased from a market rice mill, dried in the shade, and ground with a grinder (Hanshin, J-NCM) in order to increase coherence during the manufacture of the board, while particle size was selected as -18mesh, and the water content ratio was adjusted to below 6%.
For oak charcoal, black coal with -100mesh size was used after purchasing from Geumhanguam Co.
To manufacture boards, powder-type phenolic resin (Kolon Industry Co., KNB-100PL) was used, and the properties of the resins are indicated in Table 1.
Resin types | Powder resin (novolak type) |
---|---|
|
|
Items | |
Solid content (%) | 99 |
Melting point (°C) | 80~95 |
Specific gravity | - |
Celation time (sec.) | 80~120 |
Plate flow (mm) | 30~35 |
viscosity (cps) | - |
To manufacture boards, powder-type phenolic resins were sufficiently combined in sawdust, ricehusk and charcoal which were evenly selected, inserted intoa stainless square mold placed on top of a hotplate of a thermo compressor (Daeyang Machinery, DYMSP-001-026), adjusted for height of the upper portion of the sample in a constant manner, and underwent a thermo-pressurizing formation to produce a board with dimensionsof 260mm × 260mm × 11mm. For the manufacturing conditions of the board, the water content addingratio was fixed to 10%, the density was fixed to 0.6g/cm2, the adding quantities of sawdust, ricehusk and charcoalwere differentiated as 50:35:5, 50:30:10, 50:25:15 and 50:20:20 to produce 4 different kinds, and the adding quantities of sawdust, ricehusk and charcoal were fixed to 50:20:20 and had densities set to 0.5, 0.6, and 0.7g/cm3 to produce 6 sheets each, for a total number of 42 sheets. The thermo compression temperature at this point was set to 170°C, the pressure was set to 40 kgf/cm2 → 30 kgf/cm2 → 20 kgf/cm2 (3 phase pressurization), and the pressurization time was set to 9 minutes → 2 minutes → 1 minute (3 phase pressurization times). In order to maintain a constant thickness of the board in the process of the thermo pressurization, a thickness bar was used, and a Teflon plate was used to prevent attachment of the board’s upper and lower surfaces to the hotplate due to its heat.
In order to measure the water absorption and thickness swelling, a test specimen of 50mm × 50mm × 11mm was produced, on which a standard line was drawn along the middle in the direction of the width and length, and weight and dimensionswere measured. After that, the test specimen was soaked in water at 20±1°C for 24 hours, the remaining water was removed, and weight and dimensions were measuredagain. The water absorption (WA) and thickness swelling (TS) based on the water absorption was calculated by using the following formula (1, 2).
Here, W24 refers to the weight (g) of the board test specimen 24 hours after soaking in water, and W0 to the weight (g) of the board test specimen before soaking in water.
Here, T24 refers to the thickness (mm) of the board test specimen 24 hours after soaking in water, while T0 refers to the thickness (mm) of the board test specimen before soaking in water.
In order to measure the internal bond strength, a test specimen of 50mm × 50mm × 11mm was produced, a standard line was drawn down the middle in the directions of its width and length, and dimensions were measured. To identify the adhesive performance of the board, metal blocks were added on both sides of the test specimen with hot melt resin according to KS F 3104 regulation, tensile load was applied to the test specimen surface in a perpendicular direction, maximum load (P) when the internal bond was destroyed was measured, and internal bond strength (IB) was calculatedby using the following formula (3). In this case, the tensile load speed was set to 2mm/min.
Here, IB refers to the internal bond strength (N/mm2), P to themaximum load when the internal bond is destroyed (N), b to the width of the sample (mm), and h to the length of the sample (mm).
To measure the Brinell hardness, a test specimen of 50mm × 50mm × 11mm was produced, and Durville pouring which measures the Brinell hardness by pressing in a steel ball on the board’s surface was used. By using the pressing-in mark area that emerges by pressing in a steel ball with a certain radius on the board’s surface at a constant pressure, the Brinell hardness was calculated by using the following formula (4).
Here, HB refers to Brinell hardness (kgf/mm2), P to the load, D to the radius of the steel ball, and d to the diameter of the pressing-in surface.
3. RESULTS and DISCUSSION
The result of measuring the water absorption after soaking the board manufactured per manufacturing conditions in water at 20±1°C for 24 hours is shown in Fig. 1. The water absorption of the board manufactured by density by setting the addingratios of sawdust, ricehusk and charcoal at 50:20:20 showed that the resin-adding ratio at 10% was 131.19% when the density was 0.5g/cm2, 96.26% when the density is 0.6g/cm2, and 82.13% when at 0.7g/cm2, indicating a tendency of reducing water absorption with anincrease in density. The relationship between the density and water absorption was indicated as a determination coefficient (R2) of 0.9112 through which it was shown that the density had largely affected the water absorption. The quantities of compressed sawdust, ricehusk and charcoal increased with the increase in density, and this result of reduction in water absorption is considered to be achieved as contact with water, or the movement of the water became difficult with the result of reducing porosity since the gaps between and the makeup of particles of the board were densely produced after pressurization. The coefficient of linear expansion and water absorption of the sawdust board manufactured by Lee and Yoon (1994) with MDI resins had decreased as its proportion was increased, while Oh (2003, 2013) had stated that the water absorption decreased with the increase in density of the sawdust board manufactured by thinned logs and the compound board manufactured fromsawdust and Mandarin peels, and Oh et al. (2012) had also reported that the water absorption of the board manufactured with giant miscanthus particles decreased with an increase in density, while the result of this research as well had showed an equivalent tendency with this result.
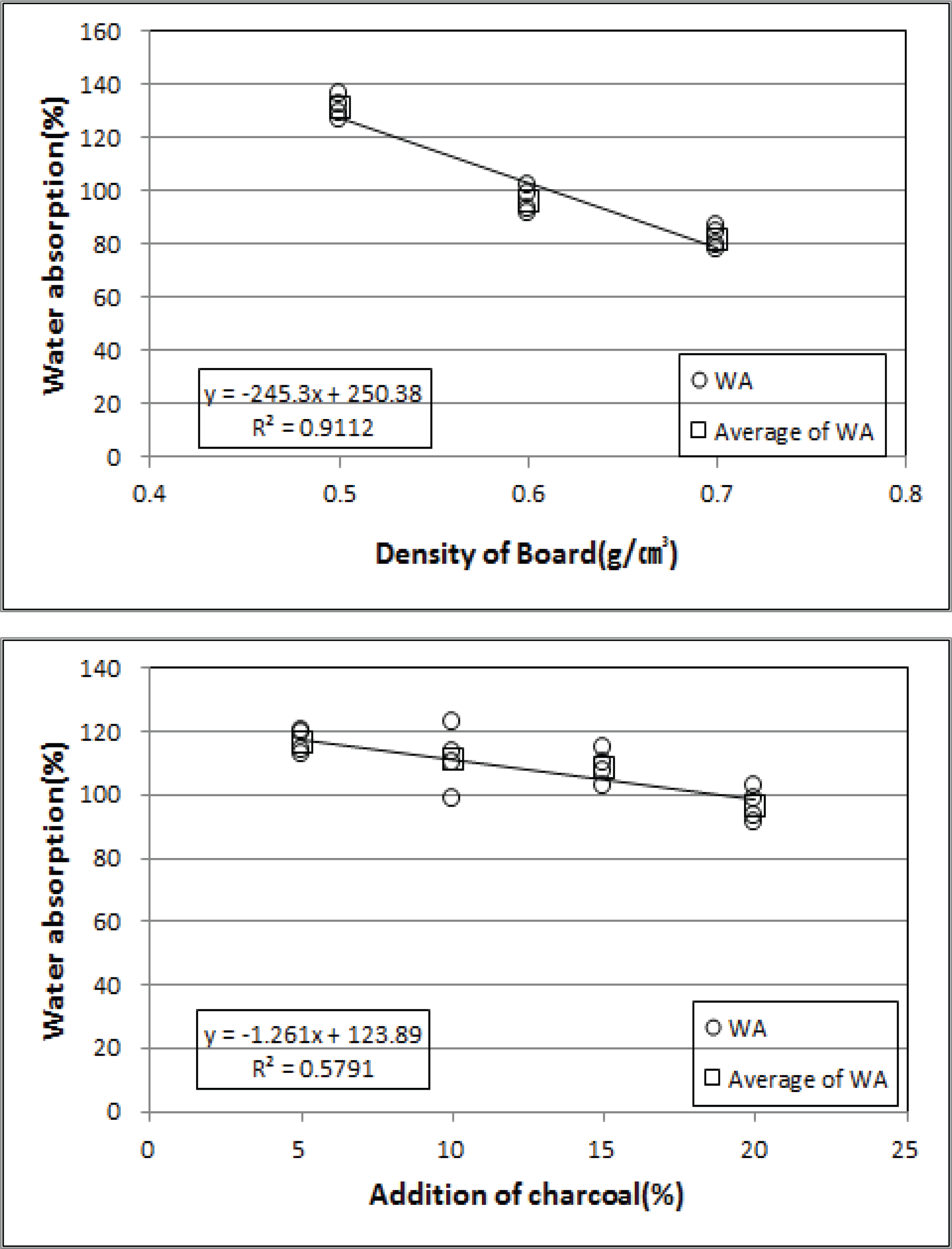
Also, the water absorption of the board manufactured with a density of 0.6g/cm3 by differentiating the addingratios of ricehusk and charcoal was 116.49% when the ratio of ricehusk and charcoal was 35:5, 108.71% when it was 25:15, and 96.26% when it was 20:20, showing a tendency of gradually decreasing water absorption with the increase in the adding ratio of the charcoal.This is thought to be a reduction of water absorption since the mobility of water becomes difficult if the adding ratio of the powder-state charcoal particles increases, in which the charcoal particles will be set at a porosity between the particles of sawdust and ricehusk. However, the relationship between the adding ratio and water absorption of the ricehusk and charcoal had showed alow determination coefficient (R2) at 0.5791; thus, it was able to be confirmed that the adding ratio of the ricehusk and charcoal had less affected the water absorption. Such a result is considered to be that, although the charcoal particles set at this porosity interfere with the mobility of water, if the adding quantity of the charcoal particles increases, because the volume to be pressurized decreases during manufacturing ofthe board, the adhesiveness would be degraded relatively despite the same density, resulting in an increase in the porosity ratio, and that the adding ratios of the ricehusk and charcoal have less of an effect on water absorption.
The result of measuring thickness swelling after soaking the board manufactured in water at 20±1°C for 24 hours is shown in Fig. 2. The thickness swelling of the board manufactured by density with adding ratios of sawdust, ricehusk and charcoal at 50:20:20 andadding ratio of resin at 10% was shown as 5.54% with density of 0.5g/cm3, 7.95% with density of 0.6g/cm3, and 10.73% with density of 0.7g/cm3, showing a tendency toward increased thickness swelling with an increase in density. The relationship between the density and thickness swelling had the determination coefficient value (R2) of 0.7399 in which the density had largely affected the thickness swelling. Generally, in case of a board manufactured with the same resin adding ratio, it is known that as the proportion of the board increases, the dimensional stability will decrease (Sun et al., 1994). This is decided to be an effect caused by an increased quantity of particles able to expand while absorbing water after manufacturing the board due to an increase in quantities of pressed sawdust and ricehusk during the manufacturing process, althoughwater absorption increased with the increase in its density. Also, this result is considered to be combined with the properties of the press-formed particles that tend to revert to the condition before its formation due to the water absorption. Thus, the thickness swelling is considered to be more affected by the density than water. This result had satisfied the quality standard of KSF 3104 Particleboard. Oh (2003, 2013) had stated that as the densities of the sawdust board manufactured with thinned logs and the compounded board manufactured using sawdust and Mandarin peels increase, the thickness swelling increases; and Piao (2004) had reported that as the density of the compounded board manufactured using the sawdust and ricehusk increases, the thickness swelling increases steadily.
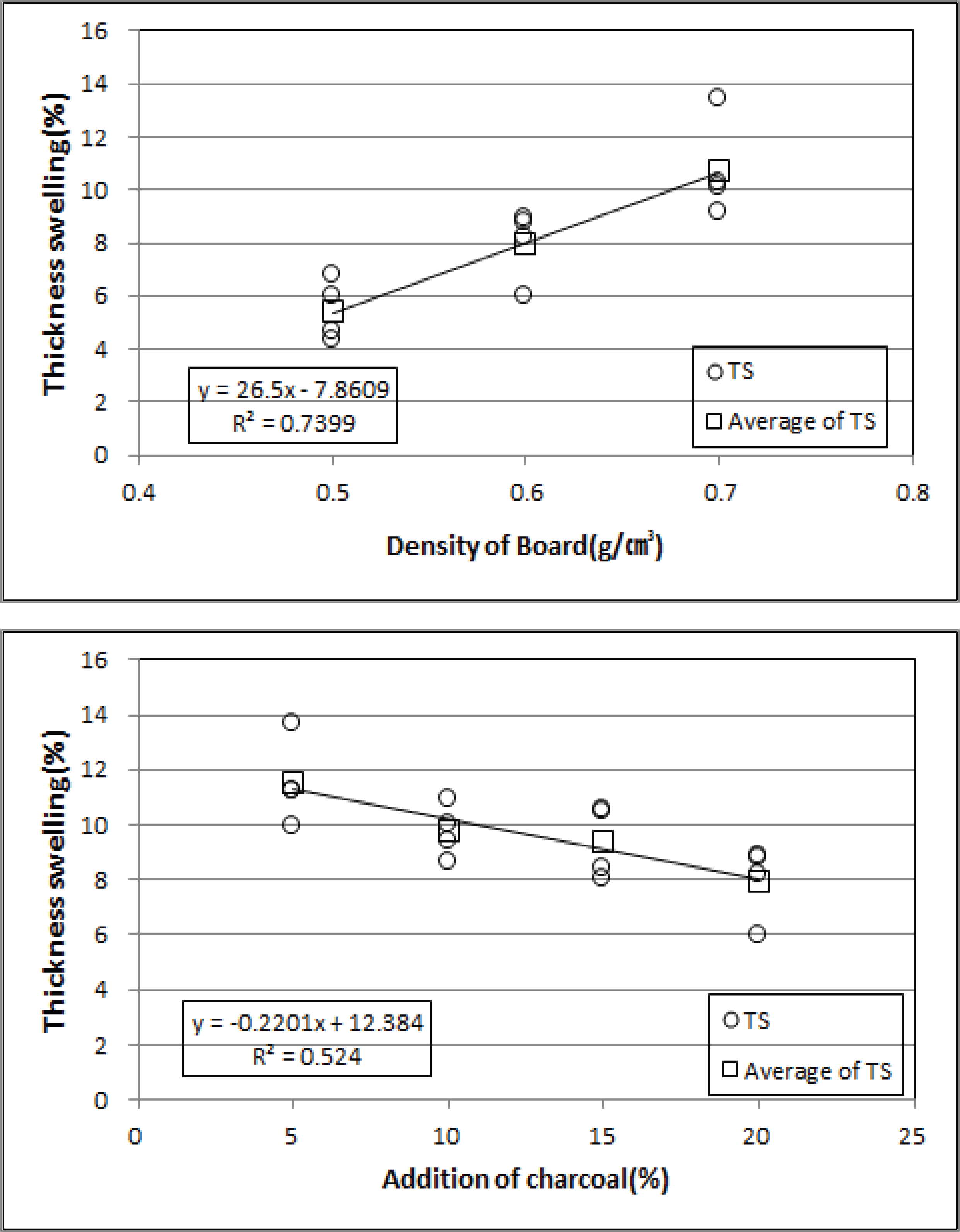
On the other hand, the thickness swelling of the board manufactured with a density of 0.6g/cm3 by setting the adding ratio of sawdust to 50% and differentiating the adding ratios of ricehusk and charcoal was shown as 11.49%when the ratio of ricehusk and charcoal was 35:5, 9.73% for 30:10, 9.36% for 25:15, and 7.95% for 20:20, showing a tendency toward asteady decrease in thickness swelling as the adding ratio of ricehusk decreases and that of charcoal increases. This result had satisfied the quality standard of KSF 3104 Particleboard. Generally, as carbide goes through the carbonating process, hydrophilic groups such as hydrogen, oxygen, etc. change to hydrophobic groups, and the chance of forming secondary combinations with water decreases (Park et al., 2007). Thus, if the adding ratio of charcoal increases, being a carbide, the adding quantity of ricehusk particles which could swell when absorbing water decreases. It is considered that with this result the thickness swelling had decreased, leading to an increase in dimensional stability. However, the relationship between the adding ratios of sawdust, charcoal and thickness swelling showed a low determination coefficient (R2) at 0.5240 in which the adding ratios of ricehusk and charcoal can be seen as affecting the thickness swellingless. In order to confirm the precise effect of charcoal, it is considered to be necessary to carry out tests by further increasing the adding ratio of the charcoal.
The result of measuring the internal bond strength based on the density of manufactured board, adding ratios of ricehusk and charcoal is shown in Fig. 3. The internal bond strength of board manufactured per density by setting the adding ratios of sawdust, ricehusk and charcoal to 50:20:20, and adding ratio of resin to 10% was shown as 0.10N/mm2 with a density of 0.5g/cm3, 0.23N/mm2 for 0.5g/cm3, and 0.49N/mm2 for 0.7g/cm3, showinga tendency of increasing internal bond strength as density increased. The relationship between the density of the board and the internal bond strength had shown a determination coefficient (R2) of 0.7838 in which board density had been shown to largely affect the internal bond strength. Generally, board density is a crucial factor in determining the mechanical properties of board in which as the density increases, mechanical property increases. This is considered to be a result caused by increased quantities of pressed sawdust, ricehusk and charcoal with the increased density and densely producing the gaps between and organization of particles of the board after pressing to strengthen their joining force. Oh et al. (2012) had reported that the internal bond strength of board manufactured by giant miscanthus particles increased with the increase in the density, and this research as well had shown the same tendency. Also, this result had satisfied the quality standards of 8.0-type for 0.5g/cm3 density, 13.0-type for 0.6g/cm3 density, and 18.0-type for 0.7g/cm3 density with respect to the quality standard for KSF 3104 Particleboard.
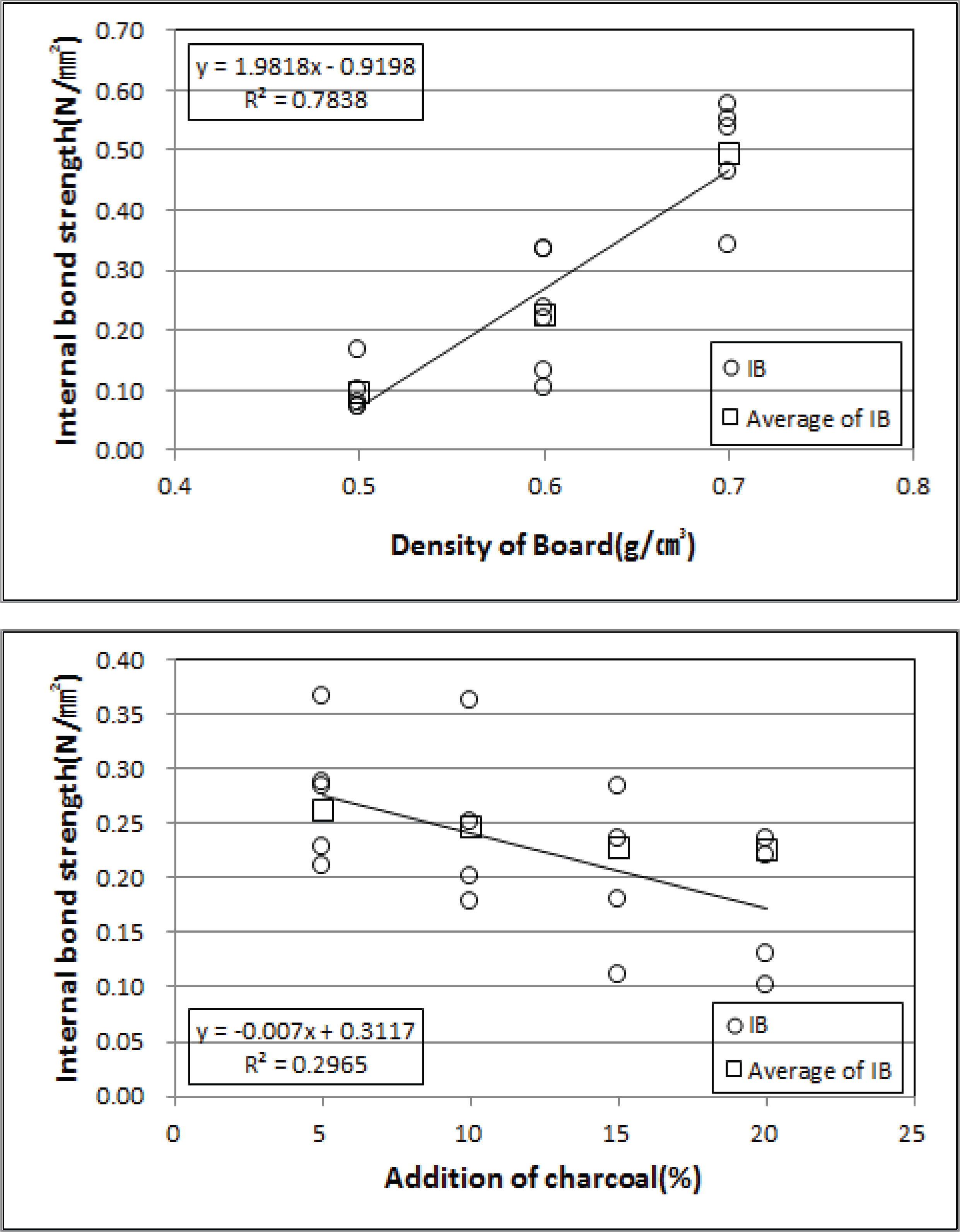
On the other hand, the internal bond strength of board manufactured at 0.6g/cm3 density by differentiating the adding ratios of ricehusk, charcoal, and setting the adding ratio of sawdust at 50% was shown as 0.25N/mm2 for a 35:5 ratio of ricehusk and charcoal, 0.25N/mm2 for 30:10, 0.23N/mm2 for 25:15, and 0.23N/mm2 for 20:20 in which itshowed a tendency of steadily decreasing internal bond strength as the adding ratio of ricehusk decreases, and that of charcoal increases. This is decided to be a result caused by degradation of internal bond strength with reduced pressed quantity during the manufacturing process if the adding ratio of ricehusk in particle-state becomes less than that of charcoal in a powder state. Also, Park et al. (2007) had reported in matter property measurementsfor particleboard manufactured with waste wood carbide that the internal bond strength had decreased with the increase in the adding quantity of the carbide. This had shown a similar tendencywith a result stating that because the strength of the carbide itself is weaker than the strength of theparticles, it had directly impacted the internal bond strength. However, the relationship between the adding ratios of ricehusk, charcoal and internal bond strength had shown adetermination coefficient (R2) of 0.2965 in which the adding ratios of ricehusk and charcoal had less of an effect on the internal bond strength. It is considered to be necessary to carry out additional tests with various adding ratios since the adding ratio of charcoal was inadequate. Also, this result had satisfied the quality standards of 15.0-type for 35:5 and 30:10 ratios of ricehusk and charcoal, and 13.0-type for 25:15 and 20:20 ratios with respect to the quality standards for KSF 3104 Particleboard.
The result of measuring the Brinell hardness based on density of manufactured board and adding ratios of ricehusk and charcoal is shown in Fig. 4. The Brinell hardness of board manufactured per density by setting adding ratios of sawdust, ricehusk and charcoal to 50:20:20, and adding ratio of resin at 10% was shown as 34.1kgf/mm2 for 0.5g/cm3 density, 42.7kgf/mm2 for 0.6g/cm3, and 60.8kgf/mm2 for 0.7g/cm3 which showed a tendency of increasing Brinell hardness with the increase in density. Also, the relationship between the board density and Brinell hardness had shown a determination coefficient (R2) of 0.6593, which showed that the density of board affects the Brinell hardness. It had indicated the same result with the research stating that generally, the Brinell hardness of wood increases proportionally with weight (Lee et al., 2008). This is a result caused by increased quantities of pressed sawdust, ricehusk and charcoal as density increases in manufacturing of the board, and strengthening the joining force by producing gaps between and an organization of the particles of the board after pressing. Oh (2003) had reported that Brinell hardness increases with the increase in density of sawdust board manufactured by using thinned logs, while Oh and Park (2009) had reported that Brinell hardness increases with the increase in density of board manufactured by using wooden parts of paper mulberry. This result had shown the same tendency with the abovementioned reports.
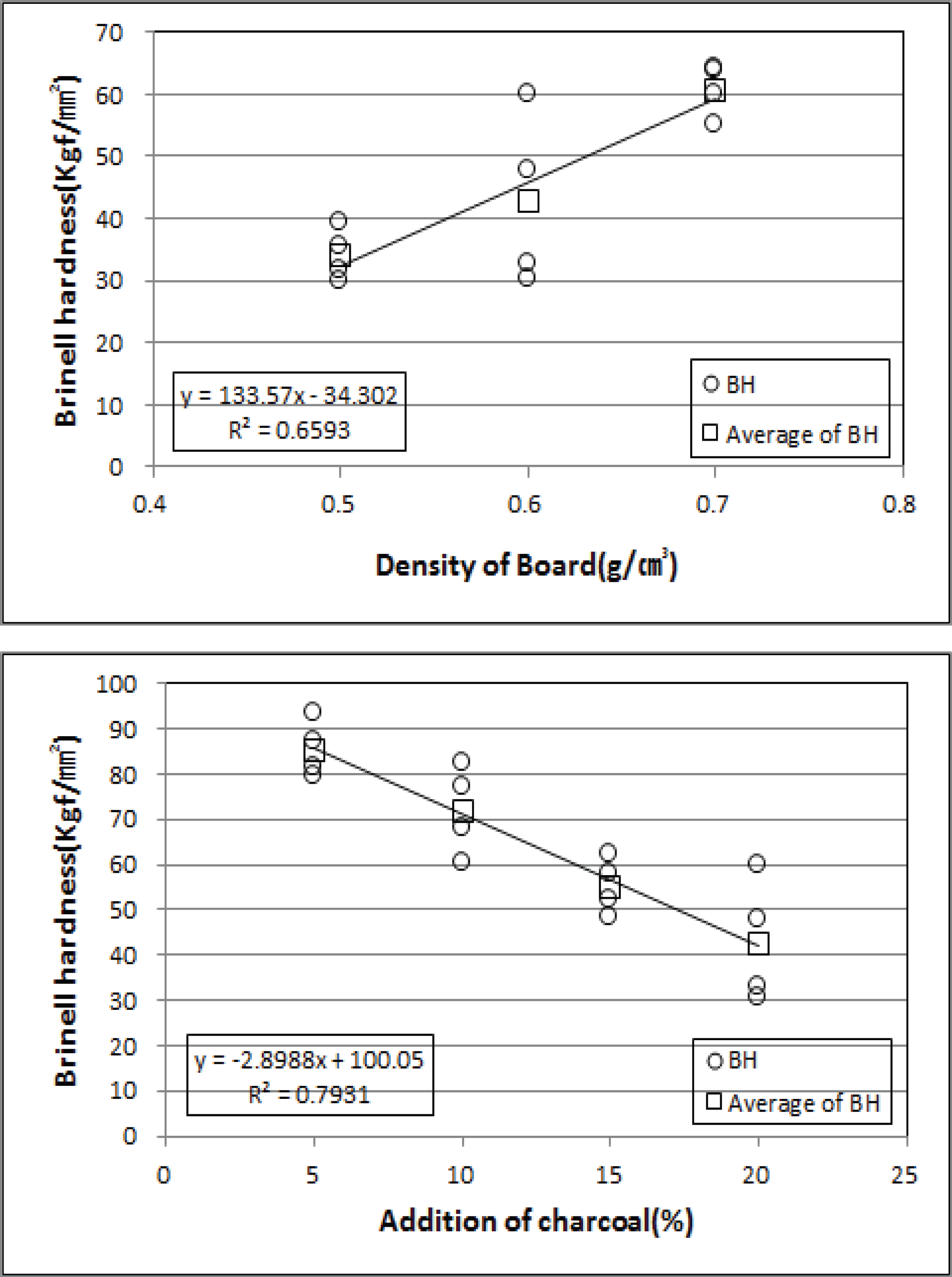
Also, the Brinell hardness of board manufactured with 0.6g/cm3 density by setting the adding ratio of sawdust as 50%, differentiating the adding ratios of ricehusk and charcoal was shown as 85.4kgf/mm2 for 35.5 ratio of ricehusk and charcoal, 72.0kgf/mm2 for 30:10, 55.2kgf/mm2 for 25:15, and 42.7kgf/mm2 for 20:20 which showed a tendency of decreasing Brinell hardness with the decrease in adding ratio of ricehusk, and an increase in the adding ratio of charcoal. The relationship between the adding ratios of ricehusk, charcoal and Brinell hardness had shown a determination coefficient (R2) of 0.7931 in which the adding ratios were indicated as affecting the Brinell hardness. Same with the internal bond strength, this is considered to be a result of degrading internal bond strength with decreased amount of pressed quantity during the manufacturing process if the adding ratio of ricehusk becomes less than that of charcoal.
4. CONCLUSION
This study had added the environmentally friendly material charcoal to ricehusk, an agricultural by-product, and sawdust which emerges during the sawing process to produce board per mixing ratio and concentration level of ricehusk and charcoal, investigated its physical properties for usage development purposes and achieved the following result.
It was able to be confirmed that as the density of board increased, the particles became more densely integrated. It was also possible to confirm that as the adding ratio of charcoal particles increases, the surface color darkens, and a greater amount of charcoal particles locate in the pores and particle surface.
The water absorption and thickness swelling of the compounded board produced per adding ratios of ricehusk and charcoal had showed the tendency to gradually decrease with the increase in adding ratio of the charcoal, and as the density of the compounded board increased, the water absorption decreased, while the thickness swelling increased.
The internal bond strength of the compounded board had indicated a highest value of 0.49N/mm2 at the density of 0.7g/cm3. It had showed a tendency toward increasing internal bond strength with the increase in density, and satisfied the quality standard of 8.0-type for 0.5g/cm3 density, 13.0-type for 0.6g/cm3, 18.0-type for 0.7g/cm3 with respect to the quality standard for KSF 3104 Particleboard. The internal bond strength of the compounded board manufactured per adding ratio of ricehusk and charcoal had showed a maximum value of 0.26N/mm2 for an adding ratio of ricehusk and charcoal of 35:5, and showed a steady decrease with the decrease in the adding ratio of the ricehusk, and an increase in the adding ratio of the charcoal. Also, in cases in which the ratio of the ricehusk andcharcoal in KSF 3104 quality standard were 35:5 and 30:10, it satisfied the quality standard of 15.0-type; whereas it satisfied the 13.0-type quality standard if the ratios were 25:15 and 20:20.
It showed a tendency of increasing hardness of the compounded board with anincrease in density, and decreasing the hardness with the increase in the adding ratio of the charcoal.