1. INTRODUCTION
Thanks to the improvement in the quality of life among South Korean people, there has been a growing interest in housing environment, such as DIY furniture and interior remodeling. Accordingly, the furniture market has recently shown a continuous growth, and as a result, the use of medium density fiberboards (MDFs) and particle boards (PBs), which are the raw materials for furniture, has also increased. Since the entrance of global furniture company IKEA to South Korean market in 2014, the overall growth of the furniture industry as well as the increase in the use of one- or two-person households, the expansion of the remodeling market, as well as the increase in the use of pallet have led to the overall production and import of, and demand on PBs and MDFs (Korea Trade Commission in Ministry of Trade, 2016).
The manufacturing process of MDF and PD is as follows: waste wood or raw wood materials are processed into particles or textile; adhesives are applied to them; and they are dried, formed, and heat-pressured. The adhesives used here are amino-group resin adhesives like urea–formaldehyde resin and melamine–urea–formaldehyde resin, which induce the combination of chips or fiber and are key elements of boards, to form boards (Meyer et al., 1985). Formaldehyde, one of the key materials for adhesives is regulated as class 1 carcinogen by WHO, and many other countries control the emissions or daily intake of this harmful substance. By examining the effect of formaldehyde exposure on human body, it was noted that short-term exposure to formaldehyde strongly irritates the respiratory system and mucous membranes, and causes dizziness and headache. Long-term exposure to formaldehyde would cause respiratory diseases such as rhinitis, asthma, bronchitis, allergic contact dermatitis, and cancer (Nelson, 1986).
Therefore, formaldehyde is controlled by the South Korean government with the enactment of the indoor air quality control act by the Ministry of Environment in 2004 and South Korean people’s interest in its effect has grown. The indoor air quality control act regulates all products used in daily life such as furniture, indoor flooring, and finishing materials (Jang et al., 2017). In addition, since 2016, Korean Standard (KS) regulates wood materials used indoor to be E0 or below, and globally, the formaldehyde emissions regulations have been established on wood-based boards. While each country has different measurements on standard formaldehyde emissions, the regulations are becoming stronger along with the more stringent environmental regulations (Park et al., 2005).
As such, not only South Korea, but countries globally recognize the risk of formaldehyde emitted indoors and continue to strengthen regulations on formaldehyde emissions. Formaldehyde emissions can be measured by various methods, such as perforator, desiccator, or small chamber method used in South Korea. The desiccator method, which has been standardized and used for a long time in South Korea, is the simplest and less expensive for testing. Due to this, it has often been used for quality control in manufacturing plants. However, it cannot measure HCHO and VOCs. Small chamber method can measure formaldehyde emissions under a constant amount of ventilation close to the actual indoor space and allows for the measurement of HCHO and VOCs. However, measurement takes long time and is based on the measurement of the surface emissions so that compared to the desiccator method wherein four sides are exposed, it results in under-evaluation of formaldehyde emissions. Furthermore, highly specialized techniques are required for analysis and the analysis equipment (e.g., HPLC and GC/MS) is expensive. As mentioned, in South Korea, most manufacturing plants are standardized to the desiccator or small chamber methods, which are used in various certification and regulation processes.
Since the enactment of the act on the sustainable use of wood in 2013, the quality control of wood-based plates is compulsorily done via the desiccator method according to the specifications and quality standards of the wood products. Moreover, according to the research due to continuous interest and risks in indoor air environments, the Ministry of Environment grants environmental certification marks for the small chamber method and desiccator method. Based on the standard specifications for the environmental certification marks for furniture or flooring materials, and the furniture supplier conformity standard (KC) by the Ministry of Trade, Industry and Energy allows the suppliers or importers to select one of the two methods so that they can directly control them.
Accordingly, industries that produce or use wood-based plates use the desiccator method for quality control, which allows for convenient and easy testing at sites due to the lack of specialist requirement and spatial limitations. In contrast, the small chamber method requires expensive equipment and specialists. While the desiccator method allows for quick tests for measuring emissions compared with other formaldehyde emissions test methods, it requires 24 h of collection time. Thus, it cannot be immediately used in quality control at production sites. Therefore, it is necessary to develop a method that allows for immediate quality control, simple analysis, and fast determination of the concentration of formaldehyde emissions.
Therefore, this study aimed to develop an accelerated collection method that reduced the measurement and collection time by revising and complementing the desiccator method primarily used in quality control of wood-based plates and in furniture manufacturing sites and to evaluate the formaldehyde emissions by the implementation of the developed accelerated collection method. This study managed to develop an accelerated formaldehyde collection process that allowed fast and accurate measurement based on the advantages of the desiccator method, offering easy analysis, and the advantages of the small chamber method, allowing the measurement of formaldehyde emissions by applying the amount of ventilation close to the actual indoor space. Moreover, this study verified the applicability of the developed process to wood-based plates and furniture manufacturing sites by comparing the characteristics of the formaldehyde emission measurement by the desiccator and small chamber methods.
2. MATERIALS and METHODS
MDFs used in the test were 4.5 mm, 15 mm, and 18 mm in thickness, which were often used for furniture and other interior products, and the thicknesses of the applied PBs were 15 mm and 18 mm. MDFs were received from Company A in Incheon while PBs were from Company B in Incheon. The properties of the used materials were tested to be suitable based on the density and moisture content ratio of PBs (KS F 3104, 2016) and MDFs (KS F 3200, 2016), the results of which are shown in Table 1.
To quickly and accurately collect formaldehyde emitted from wood-based plates, this study divided the area into three sections: the air injection part, the volatilization part, and the collection part. The air injection part is linked to 12 air injection pipes so that the air produced by an air compressor can be emitted through them, and to a control valve is installed to control the air flow. The volatilization part used a transparent glass container offering high heat absorption rate and temperature control inside the incubator; a rubber ring was installed between the glass bottle and the cover to prevent the leakage of formaldehyde. To prevent the specimen inside the volatilization part of the glass bottle from blocking the injected air, a specimen support plate was placed for smooth air flow. The collection part has a digital air flow measurement device to measure the flow of air emitted through the installed pipe, and GL45 by DURAN was used to connect between the glass bottle at the collection part and the polyurethane pipe. Fig. 1 should the schematic of the air injection, volatilization, and collection parts of wood-based plates, and Fig. 2 shows the actual test.
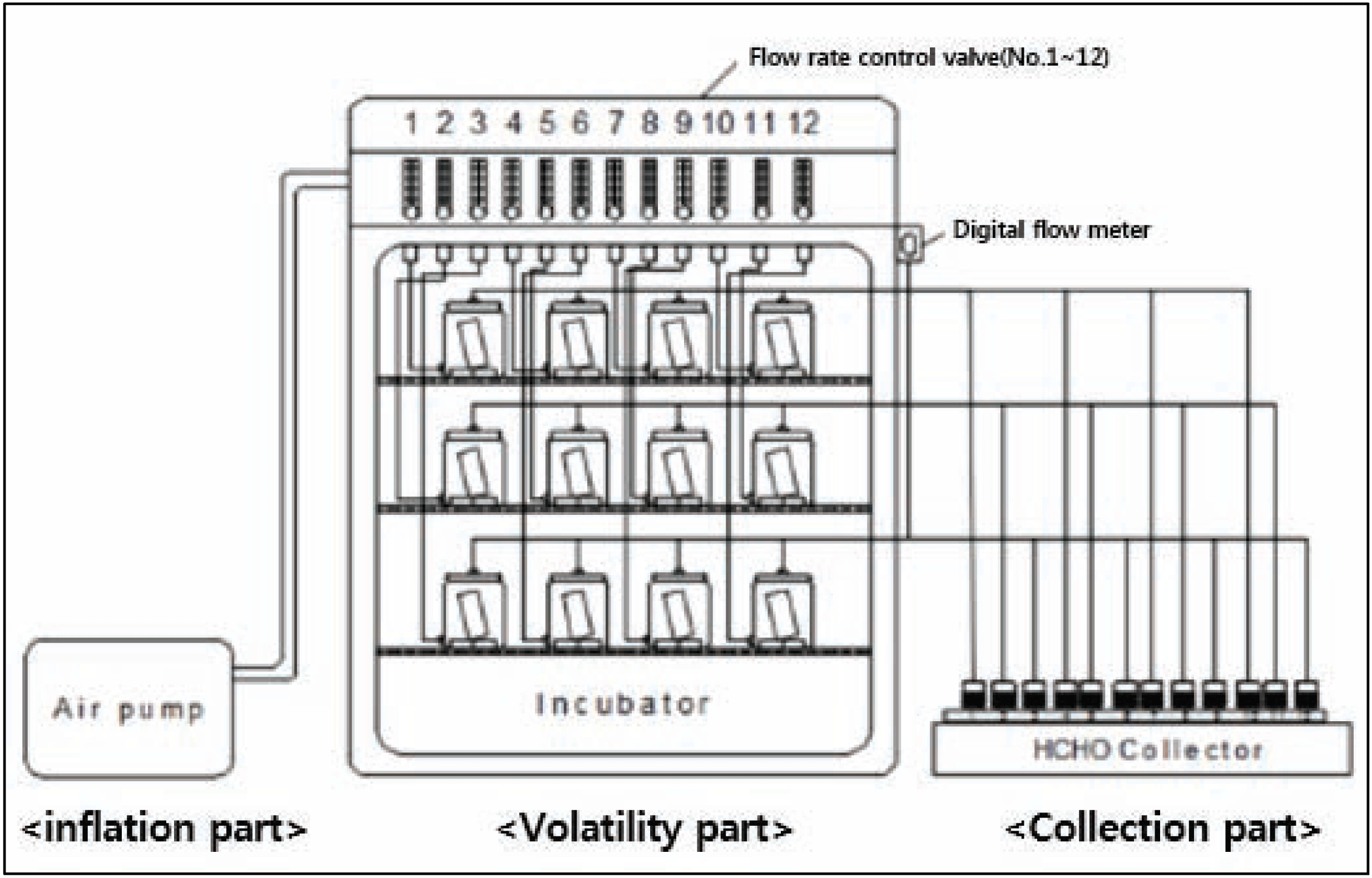
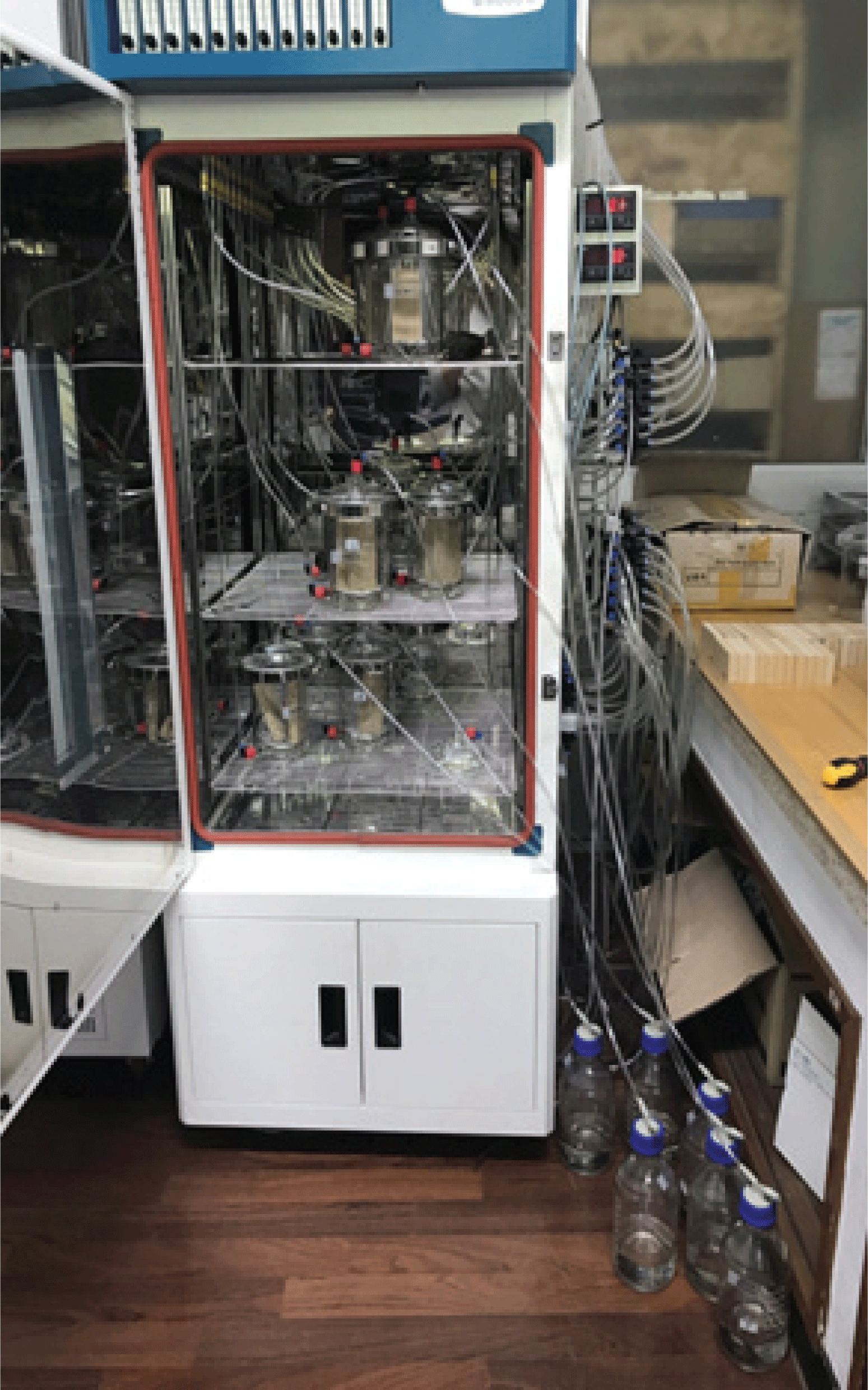
To determine the formaldehyde emissions from the wood-based plates used in the test, the study conducted a test based on the formaldehyde emission test method (KS M 1998, 2017). The number of specimens based on the surface area of each board (1,800 cm2) was determined, and the pre-process was conducted for seven days at 20 ± 2 °C and 65 ± 5% relative humidity until the mass change ratio of the specimens reach at or below 0.1%. After the pre-processing, the specimens were inserted into distilled water (300 mL) inside the desiccator, and formaldehyde was collected at 20 ± 1 °C for 24 h inside a thermo–hygrostat. The distilled water absorbed formaldehyde forming acetylacetone, which was measured using a spectrophotometer at the wavelength of 412 nm.
The test used the collection test device, designed according to the accelerated collection method for the wood-based plates. The size of specimens and test conditions for the application of the accelerated collection method are as follows.
In the desiccator method, the number of the specimens in 5 cm × 15 cm is determined based on the surface area of 1,800 cm2 with the size of the desiccator being 11 L. This was done considering in the test device, the size of the glass bottle in the volatilization part is 1,000 mL, the size of the specimen surface area inside the glass bottle of the volatilization part was reduced to 1/11, and the specimens at 5 cm × 15 cm were used to set the exposure surface area to 163 cm2.
Subsequently, the test conditions for the accelerated collection method are as follows. According to Park (2004), and Lee and Kim (2012), the formaldehyde emission test by the desiccator method showed the increase in the emissions as the measurement temperature increased. Also, Kim (2012) pointed out that the measurement of the formaldehyde collection ratio by volatilization temperature and the amount of nitrogen at the device separating the volatilization and collection parts, as a method for fast detection of formaldehyde mixed in wood and feed, showed that the amount of nitrogen was 40 cm3/min, and the maximum collection ratio of 94.8% at 100 °C for 30 min.
Based on previous studies, the test conditions for developing the accelerated collection method that reduced the measurement and collection time, the ultimate aim of this study, were the amount of air flow at 40 cm3/min, the temperature at 100 °C, 60 °C, and 25 °C for the formaldehyde emissions to compare the formaldehyde emission properties between the accelerated collection method and the desiccator method by temperature and time.
The formaldehyde emissions may change based on the specimen surface area of the wood-based plates and collection time when testing formaldehyde emissions by the desiccator or small chamber methods. In the former case, the standard conditions were 1,800 cm2 for the specimen’s exposed area and 24 h for the collection time, and in the latter case, the emission value is determined by the amount of the unit area (g/m2·h) in time when showing the emission results to identify the standardized value against the evaporated amount of formaldehyde emissions. Therefore, it was determined that the accelerated collection method in this study needed to find the exposed area of the standardized specimens and the optimal collection time.
Therefore, this study aimed to reduce the collection and evaporation process time by increasing the surface area of the specimen exposed to the volatilization in the collection process is designed to have two (163 cm2×2) or four (163 cm2×4) specimens with their exposed surface area set to 163 cm2 during the formaldehyde emission test with the temperature and time set to improve the efficiency of the collection and volatilization processes. Using the collection test device designed according to the accelerated collection method, the study compared its formaldehyde emission properties based on the exposed area with those of the desiccator method.
3. RESULTS and DISCUSSION
The desiccator method was used to measure three times the formaldehyde emissions by the grade of the formaldehyde emissions from five types of wood-based plates, MDF 4.5 mm, MDF 12 mm, MDF 18 mm, PB 15 mm, and PB 18 mm. Fig. 3 shows the formaldehyde emission concentration measurement results in terms of the material and thickness.
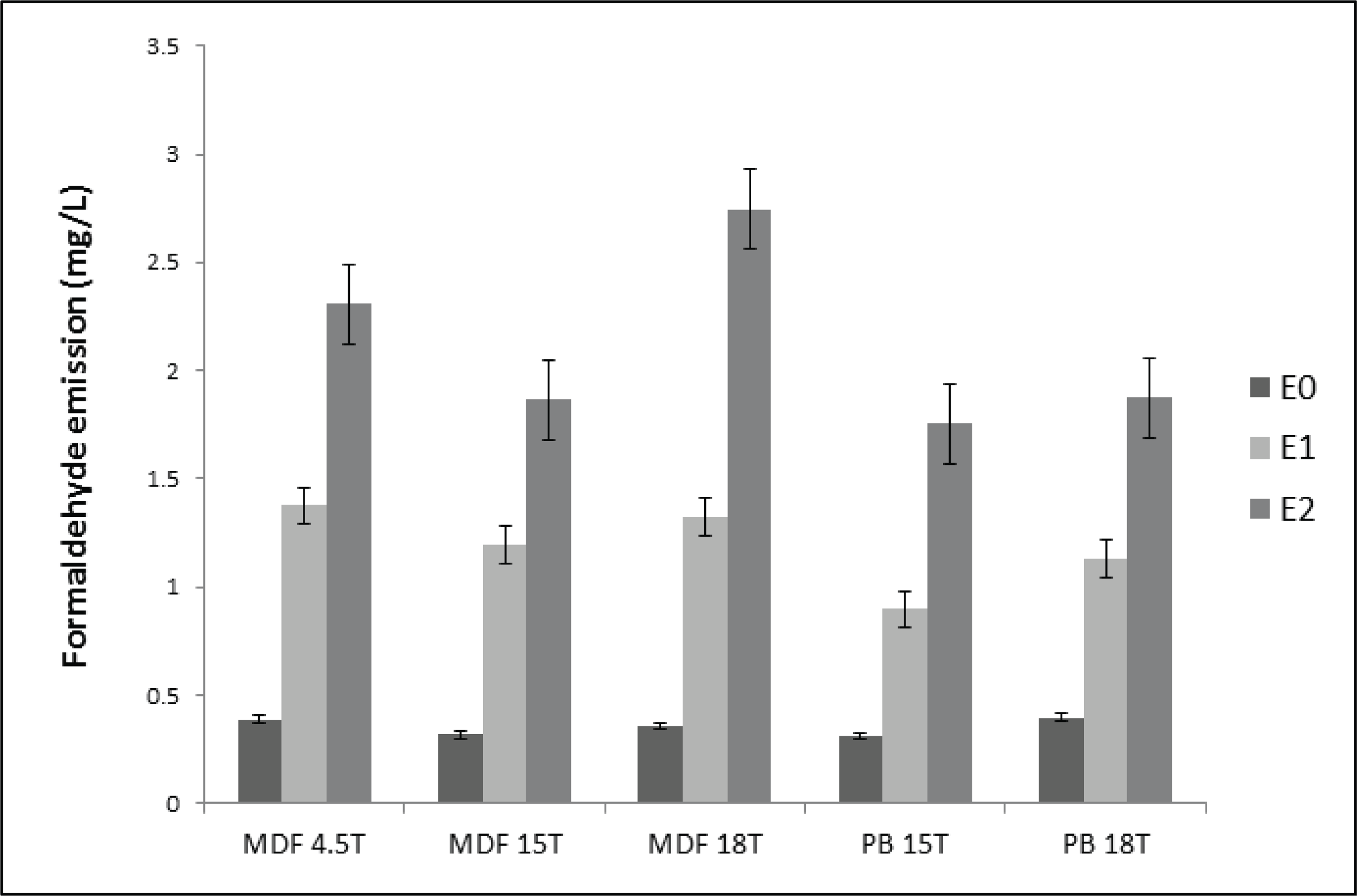
First, at the temperature of 25 °C and 60 °C, MDF 4.5 mm and PB 15 mm were used to measure three times the formaldehyde emission concentration by grade at the collection test device designed for the development of the accelerated collection method. The formaldehyde emissions from the accelerated collection test device at 25 °C for 1 h, 2 h, and 3 h for MDF 4.5 mm and PB 15 mm were undetectable (detection limit: 0.05 mg/L) for all E2, E1, and E0 grades. At 60 °C, it was also undetectable for MDF 4.5 mm and PB 15 mm for 1 h and 2 h. At 25 °C and at 60 °C, E1 and E0 grades were undetectable, and E2 grade was detected with a concentration of 0.08 mg/L for MDF and 0.09 mg/L for PB.
As shown in the formaldehyde emission results from the collection device at 25 °C and 60 °C, the formaldehyde emissions can only be measured at 60 °C and over 3 h. According to Lee and Kim (2005) on the formaldehyde emission properties of wood-based plates with time and temperature, the formaldehyde emissions continued to increase with time, and the higher the temperature, the more the width of the emission change became between six and 12 hours.
As such, to quickly measure formaldehyde emissions, which was the main aim of this study, it was determined that the collection temperature should be at 100 °C, higher than the previous temperature conditions, to quickly collect evaporated formaldehyde as the evaporation speed would increase.
To determine the optimal collection time at 100 °C, the study first repeated the test three times with MDF 4.5 mm each for 1, 2, 3, 6, and 12 h, and the results are shown in Fig. 4. At 100 °C, the formaldehyde emissions by the collection test device are shown to increase with time. It was determined that when the results from the desiccator method were compared with these results, similar emission intensity was noted at 2 h. Therefore, additional tests on formaldehyde emissions were conducted with MDF 15 mm, MDF 18 mm, PB 15 mm, and PB 18 mm at 100 °C for 2 h, and the results were compared with those of the desiccator method to determine the correlations. When the formaldehyde emissions by the desiccator method were compared to those by the developed accelerated collection method, MDF showed a high correlation with r2=0.8936, and PB with r2=0.8872 (Figs. 5 and 6).
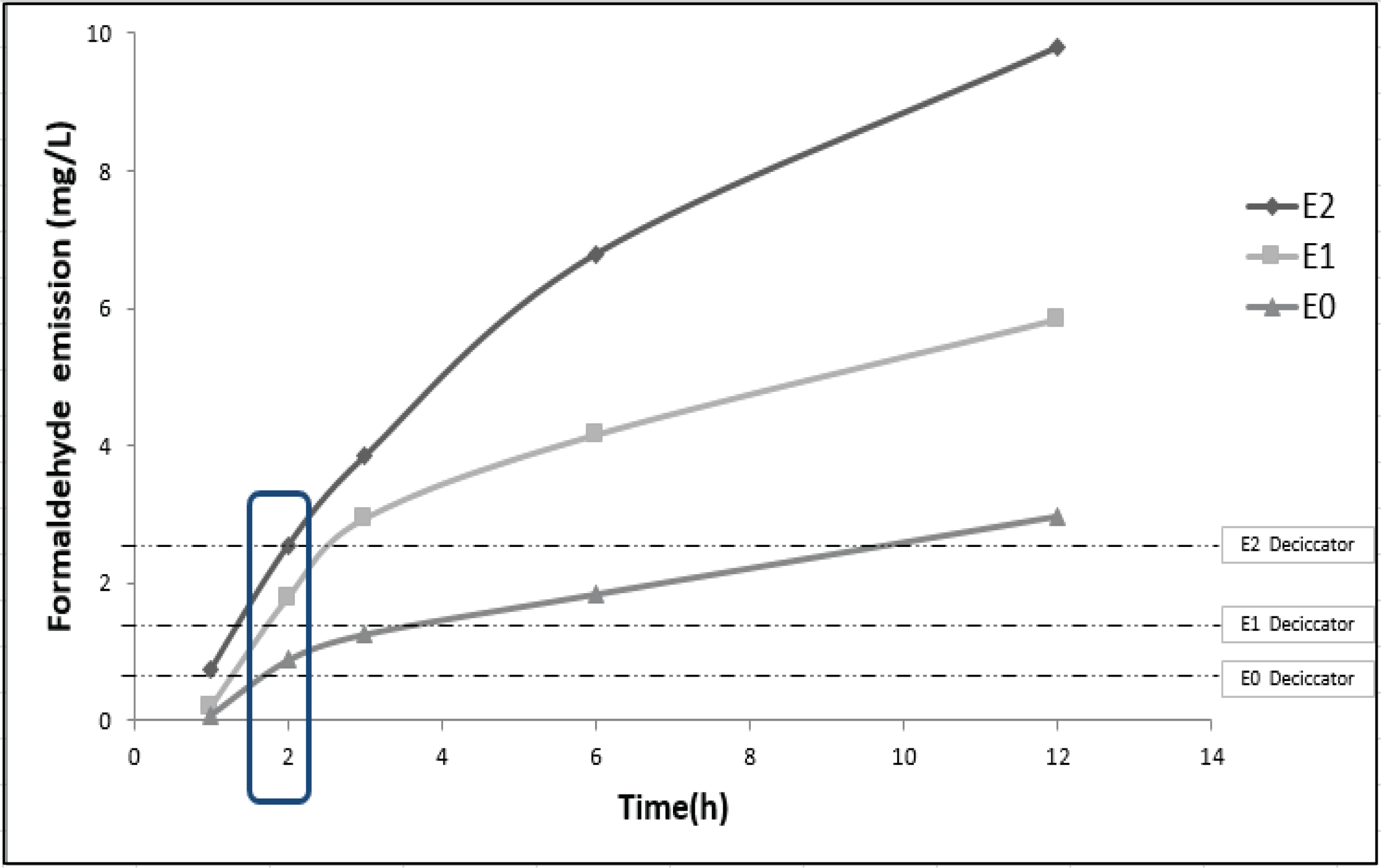
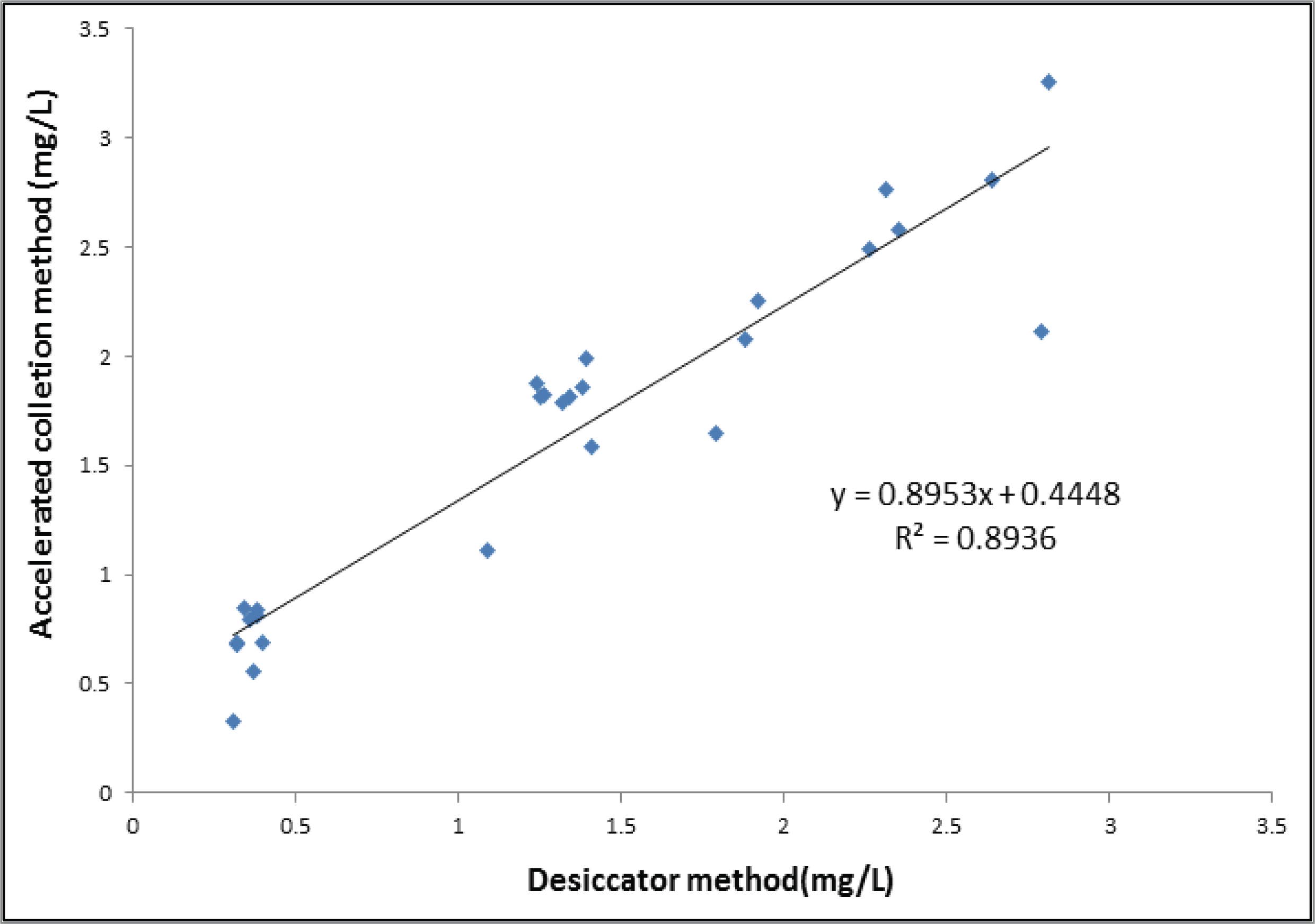
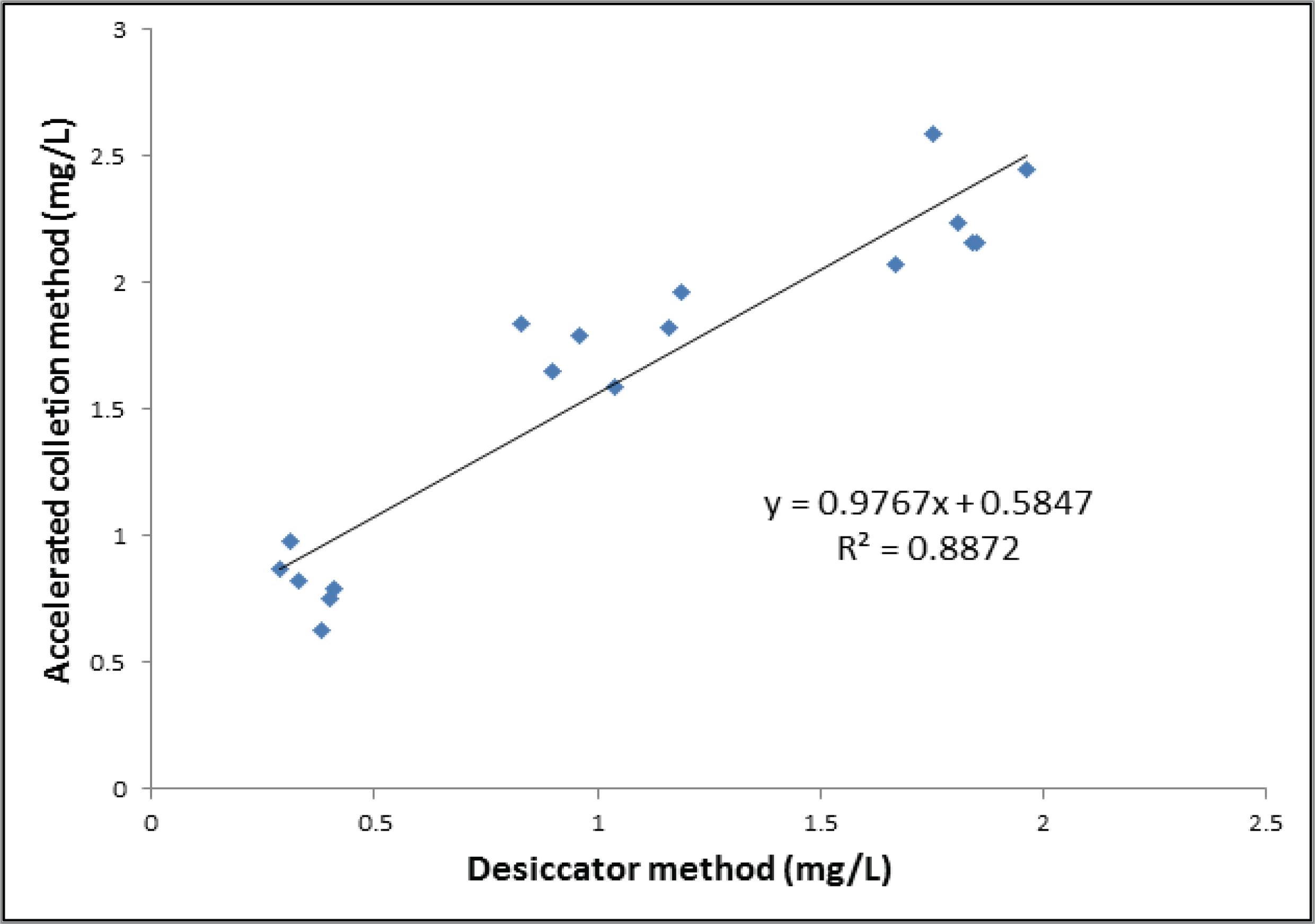
Based on the formaldehyde emission results with changes in temperature and time, these were shown to have a similar emission intensities to those of the desiccator method with the exposed area of 163 cm2, temperature of 100 °C, and the time of 2 h. Thus, with the temperature set to 100 °C, and the collection time set within 2 h, the increase in the exposed surface of the specimen where formaldehyde is emitted would increase the amount of formaldehyde emissions per hour, which would allow for fast collection and measurement.
First, to find the optimal collection time at the set temperature of 100 °C with the collection test device designed for the development of an accelerated collection method based on the exposed area, the study used MDF 4.5 mm and PB 18 mm. Two specimens and four specimens with the exposed area of 163 cm2 were tested three times for 1 and 2 h each and the results were averaged and compared with those of the desiccator method. The results were shown in Figs. 7 to 10.
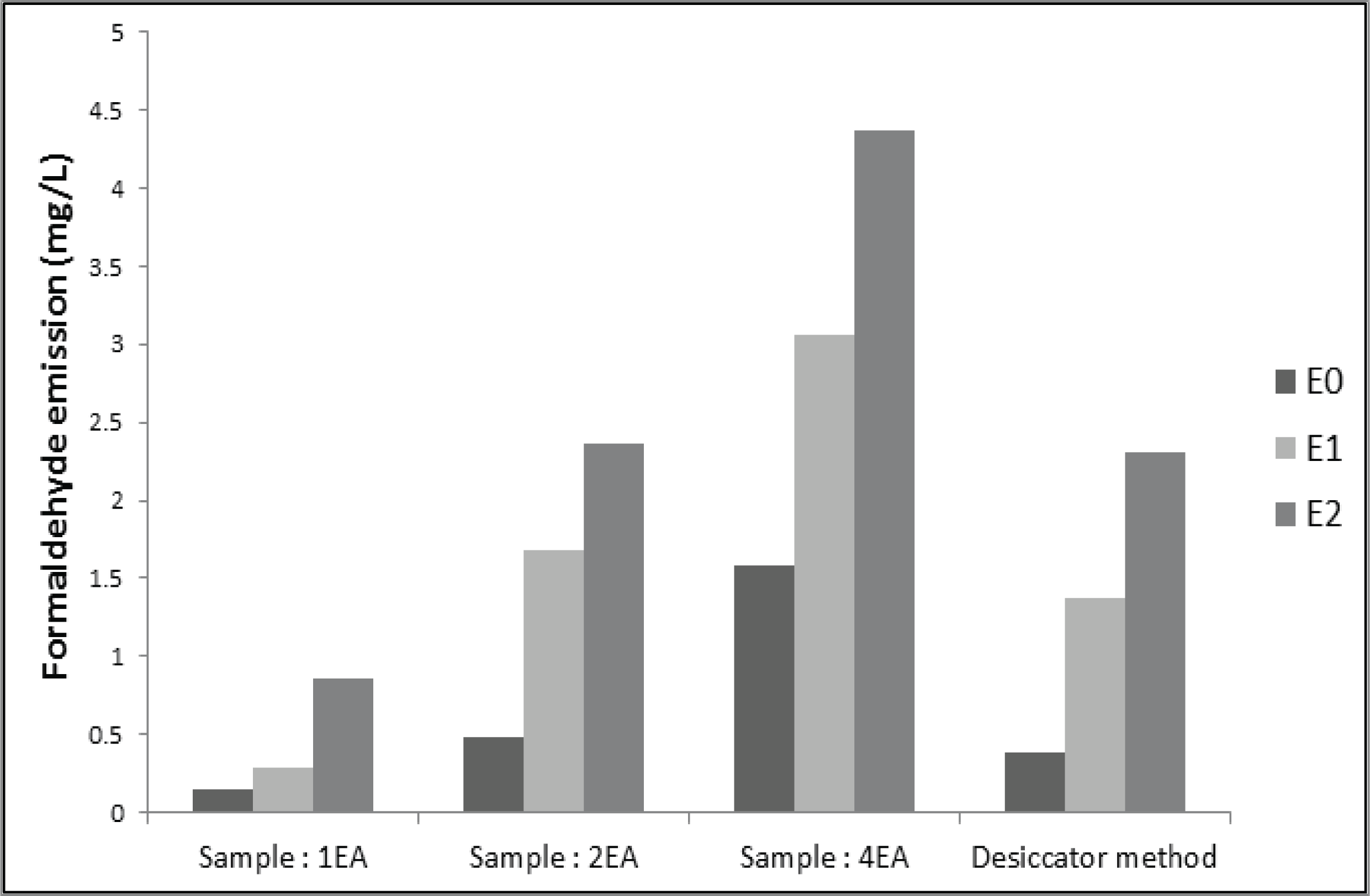
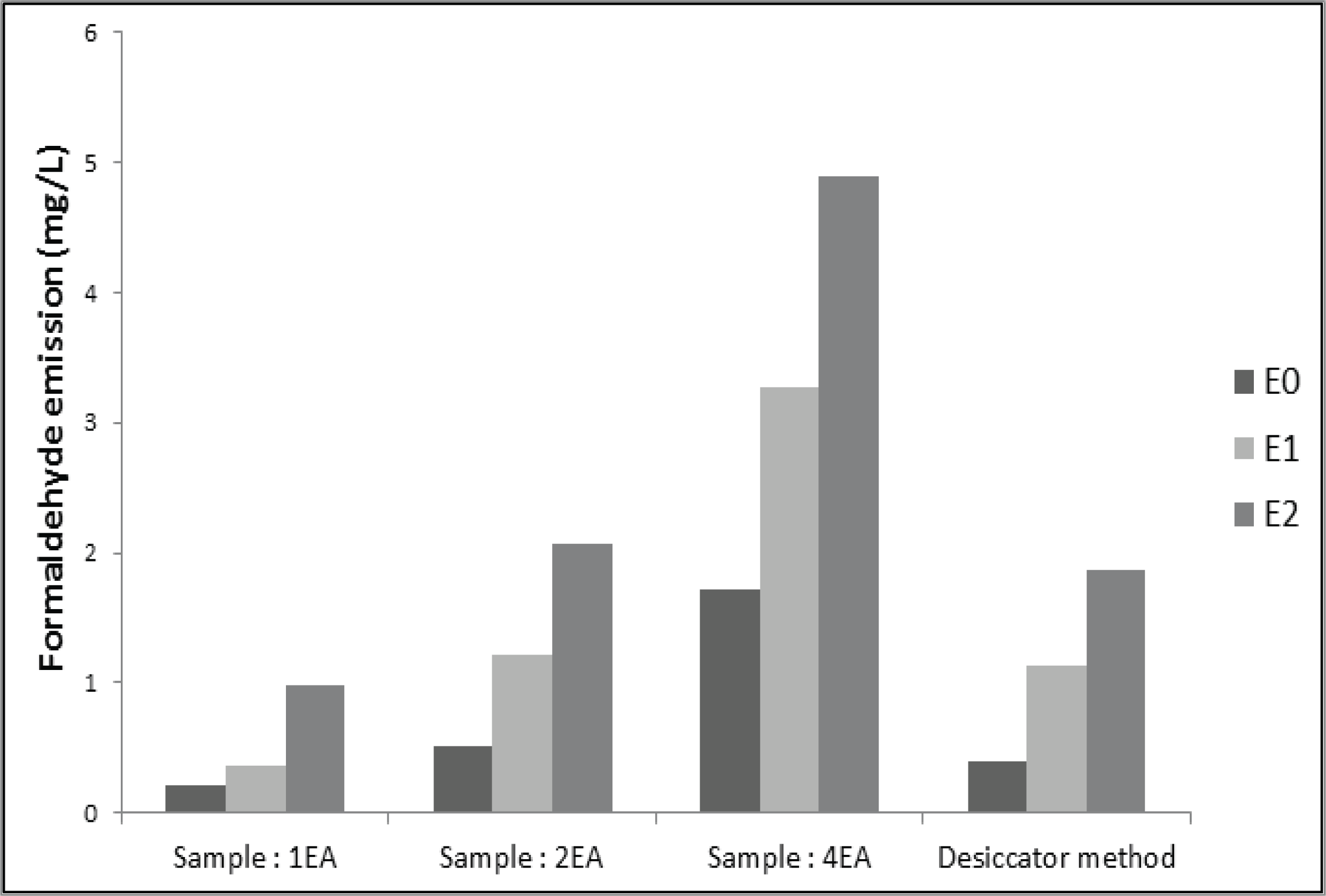
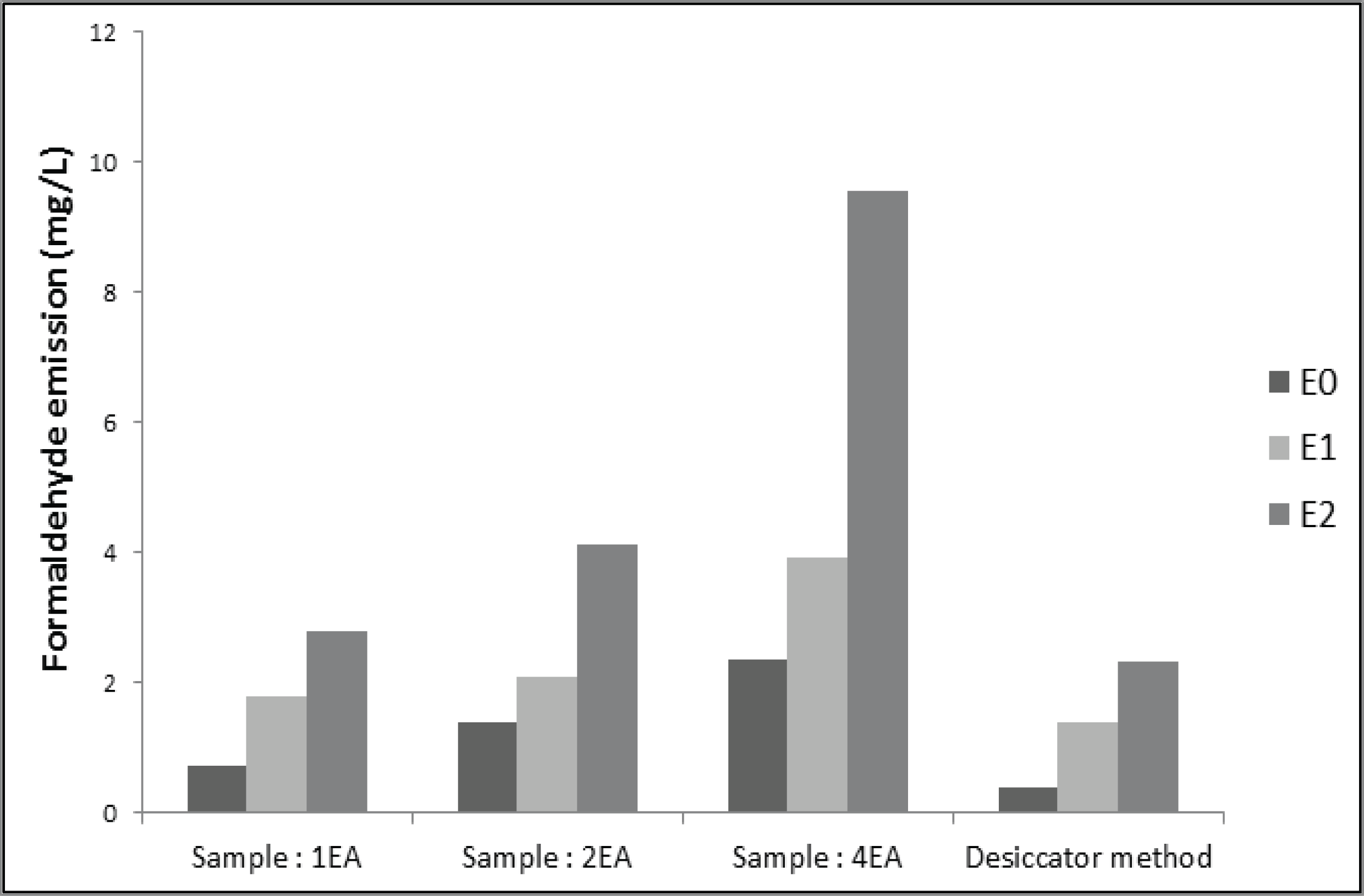
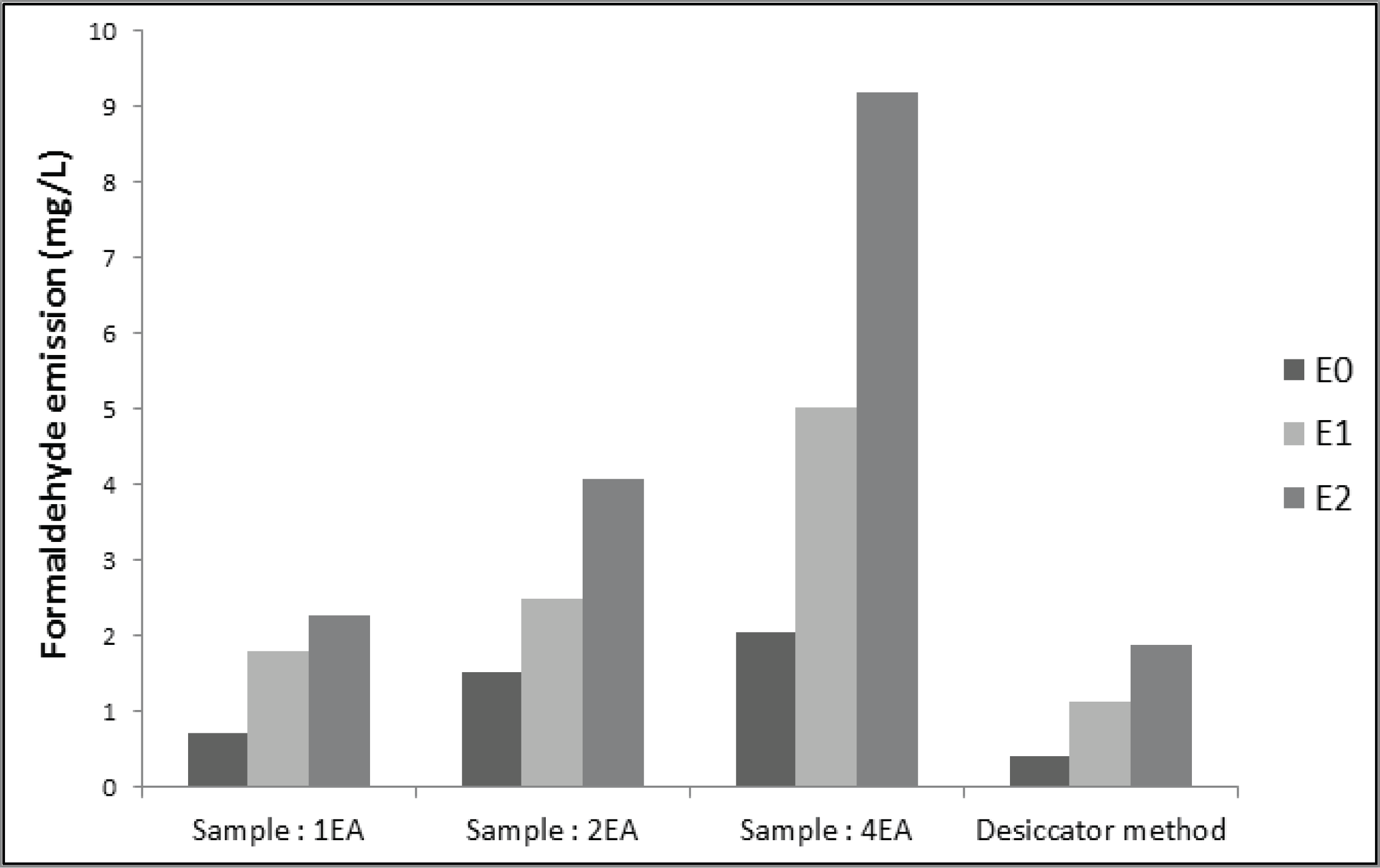
As shown in Figs. 7 to 10, from the comparison between the emission values by grade based on the desiccator method and those from the collection test device set by this study, it was determined that the condition at which the similar emission intensity would result for a short time was two specimens with the exposed area of 163 cm2 for 1 h. Thus, with two specimens at 100 °C for 1 h, the formaldehyde emissions of MDF 15 mm, MDF 18 mm, and PB 18 mm by grade were measured by the collection test device, the results of which were compared with those of the desiccator method to examine the correlation between the two results. It showed a high correlation with r2=0.8988 for MDF (163 cm2×2) and r2=0.8921 for PB (163 cm2×2) (Figs. 11 and 12).
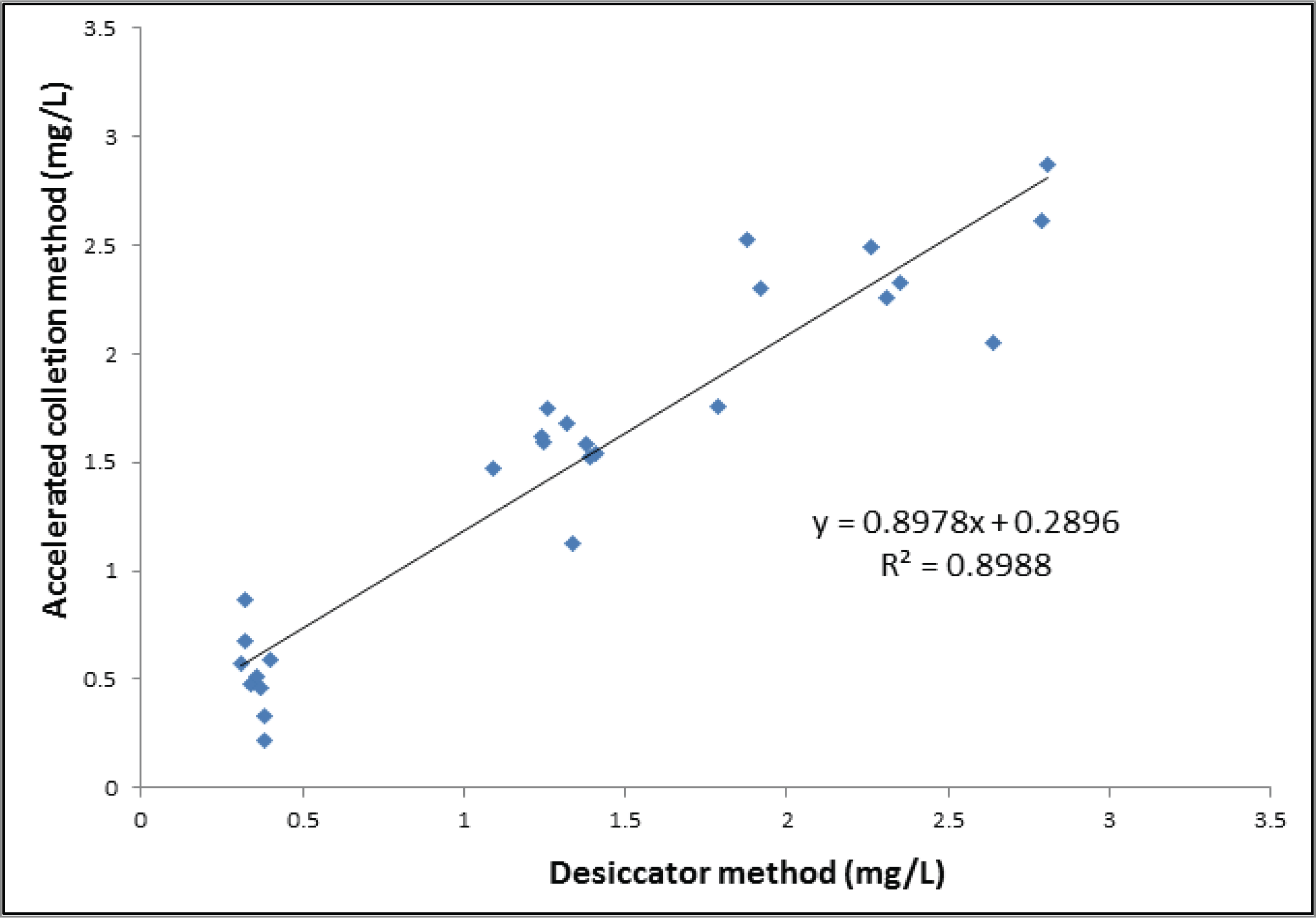
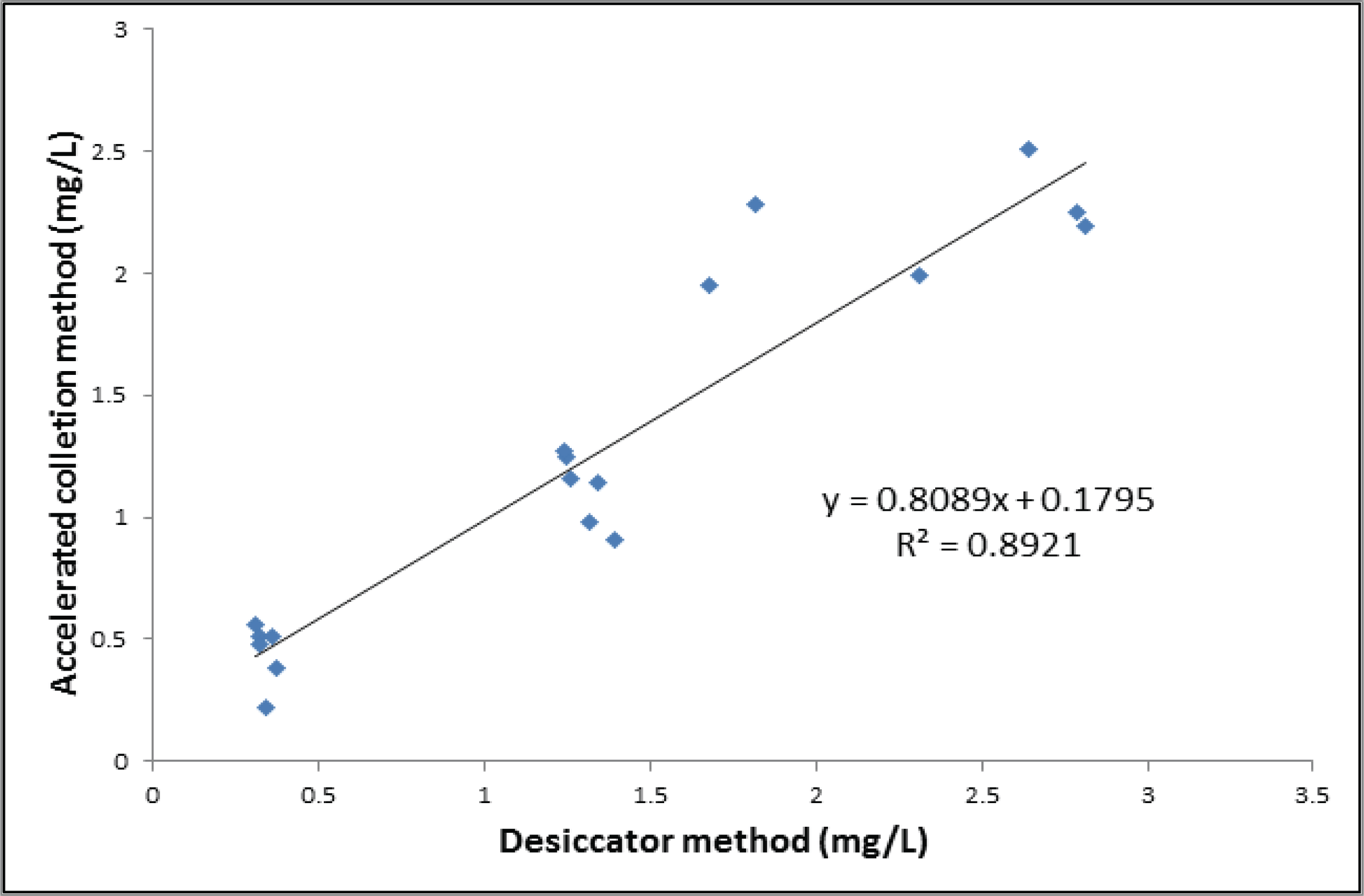
The overall formaldehyde emission results in the above collection process shows that the correlation between the formaldehyde emissions of the desiccator method and those of the developed method was relatively high when the exposed area was 163 cm2, the temperature was 100 °C and the time was 2 h, as well as when there were two specimens with the exposed area at 163 cm2 (163 cm2×2), at temperature of 100 °C and collection time of 1 h. However, since the aim of this study was to rapidly measure formaldehyde, the two specimens with exposed area of 163 cm2 (163 cm2×2), temperature of 100 °C and collection time of 1 h were set to the standardized conditions.
Based on the standardized conditions set in this process, the study conducted a test with specimens unused in the actual test after commissioning Korea Conformity Laboratories (KCL) to conduct a test based on the desiccator method to evaluate the accelerated collection method. The leftover specimens were cut to fit into the exposed area of 163 cm2, and the formaldehyde emissions were measured by the accelerated collection method three times per material for 10 different materials.
The formaldehyde emissions were measured with the collection test device at two specimens (163 cm2×2), at 100 °C for 1 h, and the measured emission values were compared with those of the desiccator method to determine the correlation. To verify the applicability of the accelerated collection method, the formaldehyde emissions from the desiccator method were compared with those of the developed collection process, which showed a high correlation at r2=0.8971 (Fig. 13).
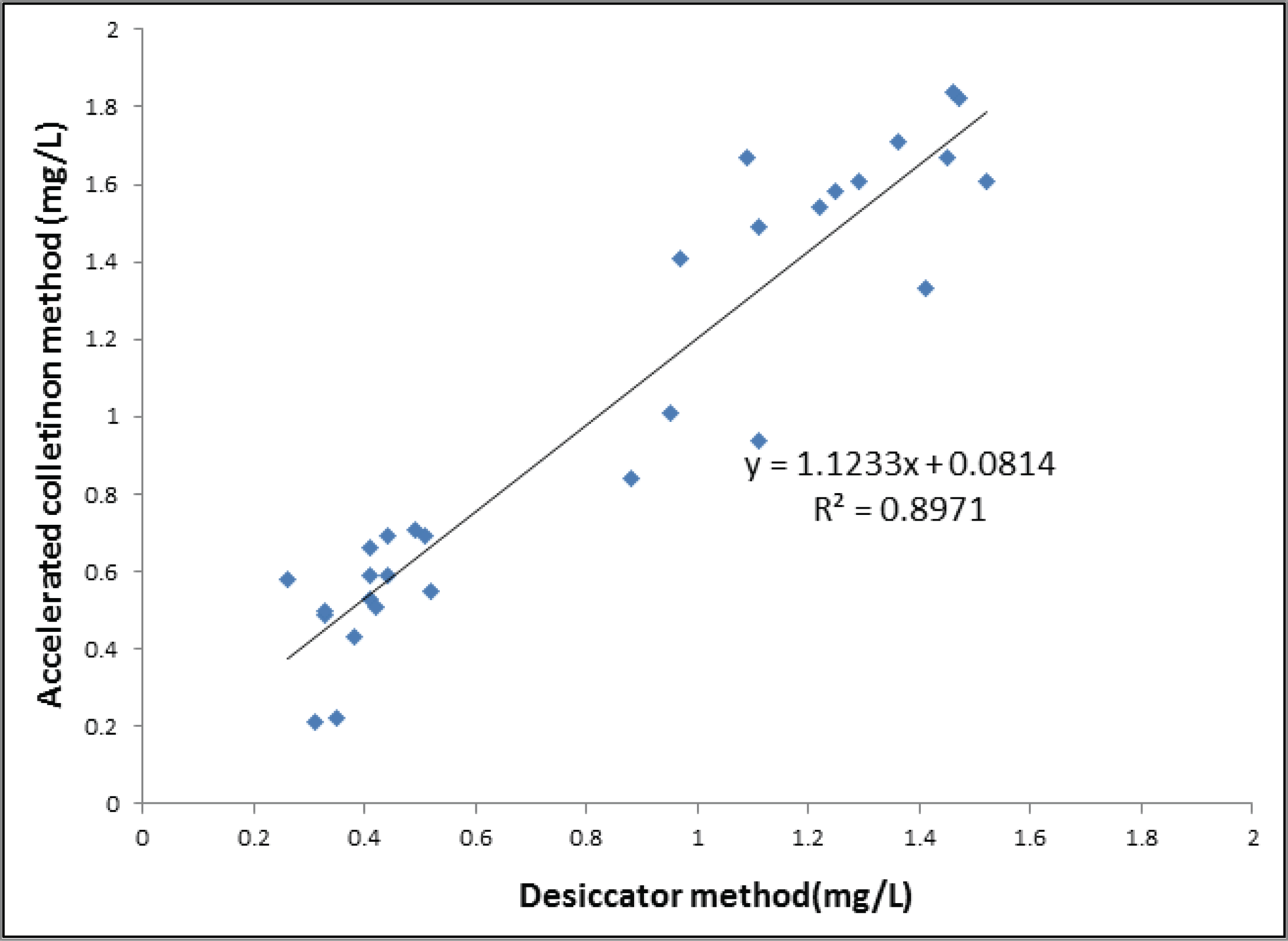
However, when the average results of the three test sets on the desiccator and accelerated collection method were compared, the application of the accelerated collection method often showed somewhat higher results than those of the desiccator method (Fig. 14), and the emission results from the desiccator method corresponded to E0 grade, but sometimes, the accelerated collection method showed emission results corresponding to E1 grade. Furthermore, the formaldehyde emissions by the desiccator method corresponded to E1 grade, but the accelerated collection method sometimes showed E2 grade.
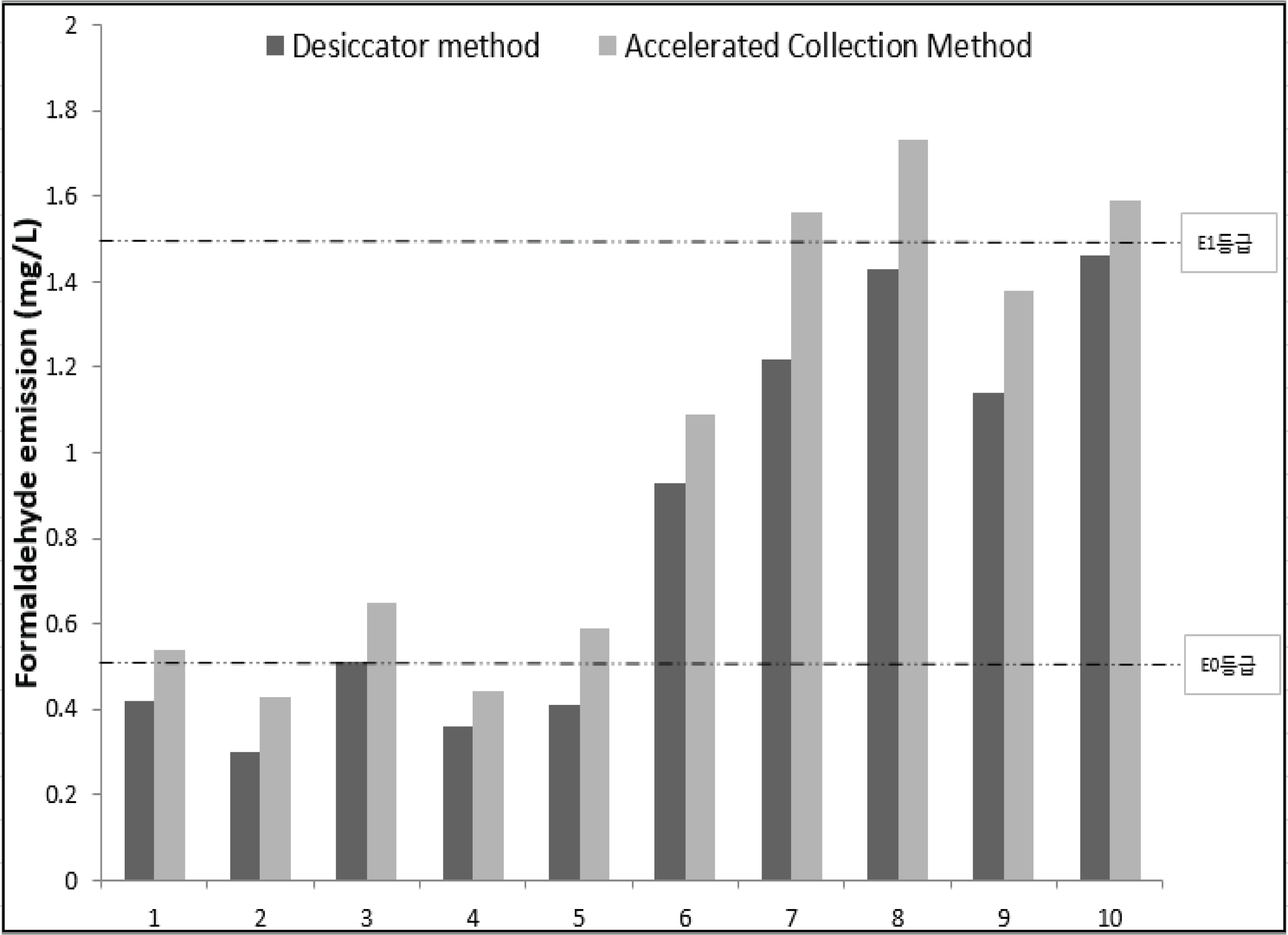
4. CONCLUSION
This study was conducted to develop an accelerated formaldehyde collection test process for swift and accurate measurement and evaluate the formaldehyde emissions based on the developed process. Toward this end, the study measured the formaldehyde emissions by the desiccator method and determined the optimal conditions, such as temperature, time, and exposed area, based on the accelerated collection method. The evaluation results of the developed process provided the following conclusions.
As for the optimal temperature and time under the accelerated collection method, the comparison of the formaldehyde emissions by the desiccator method by grade to those from the developed process showed that the formaldehyde emission intensity was relatively similar in the two methods when the temperature was 100 °C and the collection time was 2 h. Therefore, the analysis of the correlation between the formaldehyde emissions by the desiccator method and those of the developed collection process showed a high correlation with r2=0.8936 for MDF and r2=0.8872 for PB.
Under the collection test conditions at 100 °C for 2 h, set above, the emission values were measured with different exposure areas for faster measurement. The results were compared with those of the desiccator method, which showed that the two results were somewhat similar when two 163 cm2 specimens (163 cm2×2) were used at 100 °C for 1 h, and thus, the formaldehyde emissions by the desiccator method were compared to those from the developed collection process with the two 163 cm2 specimens (163 cm2×2) at 100 °C for 1 h, and the correlation between the two emissions was analyzed. The result showed a high correlation with r2=0.8988 for MDF (163 cm2×2) and r2=0.8921 for PB (163 cm2×2).
As shown in the above results, the conditions at which the fastest and most accurate formaldehyde emission measurement under the accelerated collection method were two 163 cm2 specimens (163 cm2×2) at 100 °C for 1 h, and to verify the applicability of the accelerated collection method, the specimens left after the commissioned test of the desiccator method by the KCL were used to conduct a test based on the standardized accelerated collection method, the result of which was then compared with the result of the desiccator method. The results showed a relatively high correlation at r2=0.8971.
However, when the average values of the test results from the desiccator method and the accelerated collection method were compared, the accelerated collection method, in most cases, showed somewhat higher results than the desiccator method. Compared to the emission results of the desiccator method, the results of the accelerated collection method were often one grade higher.
It was determined that since the formaldehyde emission grade from the accelerated collection method was one grade higher, the developed process could be sufficiently applied to manufacturing plants from the perspective of quality control. If the developed process is set to E0 grade for quality control, the results from the desiccator method would show SE0 emissions, which is higher in quality than E0 grade, and if it is set to E1 grade, the lowest emission scope, for quality control, E0 grade level control would be possible. Therefore, the implementation of the developed process to manufacturing sites would be able to replace the desiccator method, which would take 24 h for testing, and thus, would enable the measurement of formaldehyde emission for only 1 h, leading to faster quality control.