1. INTRODUCTION
Recently, many scientists and industries have been interested in nanopolymer composites mixed with various nanoparticles because of the remarkable improvement of the matter properties. Although various petroleum-based polymer materials have been used to develop nanocomposites, the development of nanocomposites using biodegradable polymers derived from nature has attracted great interest due to the global warming and the various environmental regulations surrounding the disposal of polymers. Poly (3-hydroxybutyrate) (PHB), poly (lactic acid) (PLA), cellulose acetate (CA) and poly (caprolactone) (PCL) are popular biodegradable polymers replacing petroleumbased polyolefin polymers (Gutierrez et al., 2012).
Cellulose acetate, a cellulose derivative, as a representative biodegradable polymer, is synthesized through acetylation of cellulose and excessive acetic anhydride by sulfuric acid catalyst (Korea Textile Development Institute, 2012). CA is widely used for the development of composite materials such as expensive spectacle frames, high-grade fibers, and window frames because of its transparency, stiffness, heat and impact resistance. It is also widely used in water treatment fields such as reverse osmosis, ultrafiltration and nanofiltration because of its low price, good chlorine resistance, bio and water affinity. In addition, due to the non-toxicity, biocompatibility and absorbability of CA, a natural material, it has recently been widely used in the study of medical engineering materials for drug delivery and hemodialysis (Candido et al., 2017; Dumitriu et al., 2018; Liu et al., 2016, Chun et al., 2012; Sukul et al., 2015). Despite these advantages, however, its low mechanical strength has been an impediment to the long-term use of CA in such applications.
Nanocellulose, which can be obtained through a mechanical or chemical treatment on plant cell walls, can be supplied from nature, and therefore, it is possible to continuously produce nanoparticles because of its sustainability. And since it has competitive price, it is being used for a variety of application fields requiring high-tech materials. Cellulose nanocrystals, a kind of nanocellulose, are nano-sized crystalline particles having a diameter of 5-70nm and a length of 100 nm. CNC nanoparticles have a low density (1.6 gcm-3) and a high specific surface area (300 m2g-1) and shows high tensile strength (7.5-7.7 GPa) and elasticity (143 GPa) (Gwon et al. , 2018; Majoinen et al., 2011; Ljungberg et al., 2006; Moon et al., 2011). These features of CNCs are good enough for researchers to use as a reinforcing agent to increase the strength of polymer composite materials (Jo et al., 2015; Masruchin et al., 2015; Park et al., 2016). Moreover, the CNCs surface structure with many hydroxyl groups (-OH) similar to that of the CA main chains makes it possible to fabricate composites in a simple process, compared to the studies in which the surface of hydrophilic CNCs was modified to hydrophobicity (Gwon et al., 2016) for use as a reinforcing agent for hydrophobic polymer composites. Many hydrogen bonds between the two materials can be expected to serve as effective enhancers in the CA composite materials.
To date, the majority of CA application research has focused on the production of materials by electrospinning, using chemicals or organic solvents that have big environmental load such as dichloromethane and methanol. On the other hand, there are relatively few studies on the CA production using molten extrusion and injection methods which are advantageous for mass production for industrialization. Therefore, the aims of this study are to introduce the development of CA polymer composite materials using CNCs as a reinforcing agent by applying an extrusion and injection method and to investigate the mechanical and thermal properties of CA composite materials made according to the CNCs content.
2. MATERIALS and METHODS
Cellulose acetate (Mn ~ 50,000 Da, Sigma-aldrich) is used as a base polymer and has 39.7 wt.% of the acetyl group. (For improving flowability of CA during extrusion and injection processes, triethyl citrate (TEC, Mw ~ 273.3 Da, Alfa Aesar) was used as an environmentally friendly plasticizer with low volatility at the processing temperature.) Cellulose nanocrystals were prepared according to the previous experimental method (Gwon et al., 2016) using 64% of the sulfuric acid in a cellulose powder (W-50, KC Flock) with a particle size of 50 μm. The diameter of CNCs fabricated was about 6.0±1.2 nm, and the length was 155±15 nm [Fig. 1(a)]. Before using the melting process, the CNC suspension solvent was refrigerated at 5°C after replacing distilled water with acetone to disperse CNC nanoparticles in the CA resins in advance.
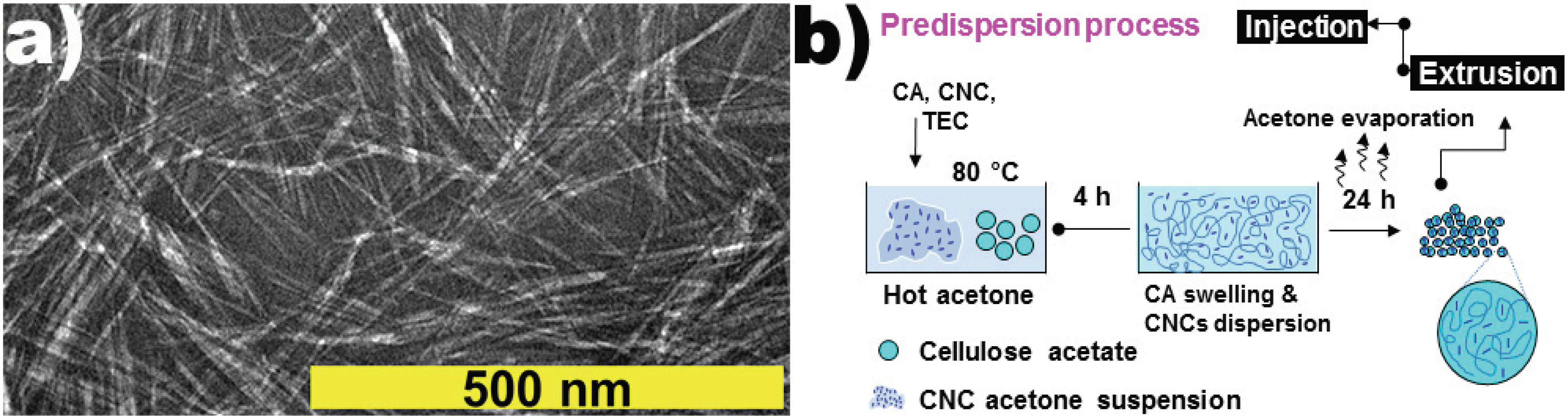
To investigate the properties of CA nanocomposites based on the CNC's content, we divided the CNCs content into 0, 1, 3, 5, and 10 wt.%. TEC, a plasticizer added to improve the efficiency of the melting process was set to 30 wt.% of the total weight. To effectively disperse the CNC nanoparticles between the CA main chains, a predispersion method using solvents was applied to the process (Gwon et al., 2018). When nanocomposites are fabricated through the melting process, the viscosity of the polymer is high at the molten state of the polymer, and therefore, the nanoparticles do not sufficiently disperse in the matrix, and an aggregation occurs so that the function of the nanoparticles as a reinforcing agent is difficult to carry out. Hence, nanoparticles are made to be predispersed in a solvent, and when the solvent penetrates into the spaces among the chains by inducing the expansion of the polymer chains in the solvent, the nanoparticles are moved with the solvent to the space when removing the solvent used later. Therefore, introducing the predispersion method make the nanoparticles possible to highly dispersed state in the molten polymer matrix.
It is desirable that the conditions of the solvent used here satisfy both the affinity to the nanoparticles and the good solvent for the polymer resin. In this study, we used the predispersion method that uses acetone, and it's shown in Fig. 1b. The suspension of CNCs replaced with acetone was put into acetone which was about twice as heavy as the CA weight. Then, the mixture was stirred at 14,000 rpm for 5 minutes using a high-speed homogenizer (Ultra Turrax T25, IKA). After that, temperature of the mixture was raised to 80°C by using a hot water bath. When the temperature rose, CA and TEC were added to completely dissolve CA, and then the solvent was evaporated in the hood for 24 hours after casting it into the stainless-steel mold. After the evaporating process, the solvent was removed and then a CA/CNC composite film was formed in the mold. The size of this fabricated film was about 400×400×1 mm (width × length × thickness). The film (5×3 mm) was pelletized by using a pelletizer (Bautek Co.) and then dried it in an 80°C oven for 24 hours before starting extrusion process. The pelletized films were extruded by a co-rotating twin-screw extruder (19 mm diameter, 40 L/D ratio, Bautek Co.). The extrusion temperature and screw speed were 170~185°C and 150 rpm respectively. Extruded materials were immediately conveyed to an injection machine (Minijet II, Thermo Scientific) for preventing any strand formation.
The mechanical (tensile and flexural) properties of the prepared CA/CNC nanocomposites were evaluated by using a universal testing machine (GB / H50K, Hounsfield test equipment Ltd.). The five specimens were tested according to the ASTM D638 and D790 methods and the test speed was 10 mm/min. The thermal properties of composites were obtained using TGA (Thermogravimetric Analyzer, Perkin-Elmer TGA8000) at a 10 °C/min in the 40 °C to 600 °C temperature range under helium.
3. RESULTS and DISCUSSION
Fig. 2 shows the tensile and flexural properties of CA/CNC nanocomposites based on the CNCs content. The tensile strength of the composites showed a maximum value of about 36 MPa when the content of CNCs was 3 wt.%, which was a strength increase of about 24% compared to that of CA without CNCs. Tensile modulus tended to increase as the content of CNCs increased, and the maximum elongation at break dramatically reduced when the content of CNCs was 3 wt.%. Like the tensile strength, the flexural strength showed a maximum value of 43 MPa when the content of CNCs was 3 wt.% and a strength increase of 26% when compared to CA without CNCs. The flexural modulus also increased as the CNC nanoparticle content increased. The reason for the improvement in strength is due to the reinforcing effect of the CNC nanoparticles, and when the CNC is well dispersed in the CA resin, it prevents the CA resin from being broken by force from outside. The area that we need to take a closer look at is where the strength of CNC nanocomposites with CNCs shows a maximum value when the content of the CNC nanoparticles was 3 wt.%. Afterwards, the strength tends to decrease as the content decreased. The reason for this decrease in strength is due to the flocculation phenomenon of CNC 'nanoparticles'. In other words, the external forces are focused on the place where the particles agglomerate without being evenly distributed. The cause of the reduction in strength due to the flocculation of rodshaped nanoparticles such as CNCs can be explained in detail by mechanical percolation (Leite et al., 2016; Dufresne 2008; Dong et al., 2012; Azizi et al., 2005). In the case of studies where percolation is an infinite connection in terms of mechanical properties, this phenomenon can be seen as a phenomenon in which percolation network formation of CNC nanoparticles occurs at the molecular level by a means of hydrogen bonding at a specific content or above. The content that starts this flocculation is the mechanical percolation threshold (νRc) which can be obtained from the following equation:
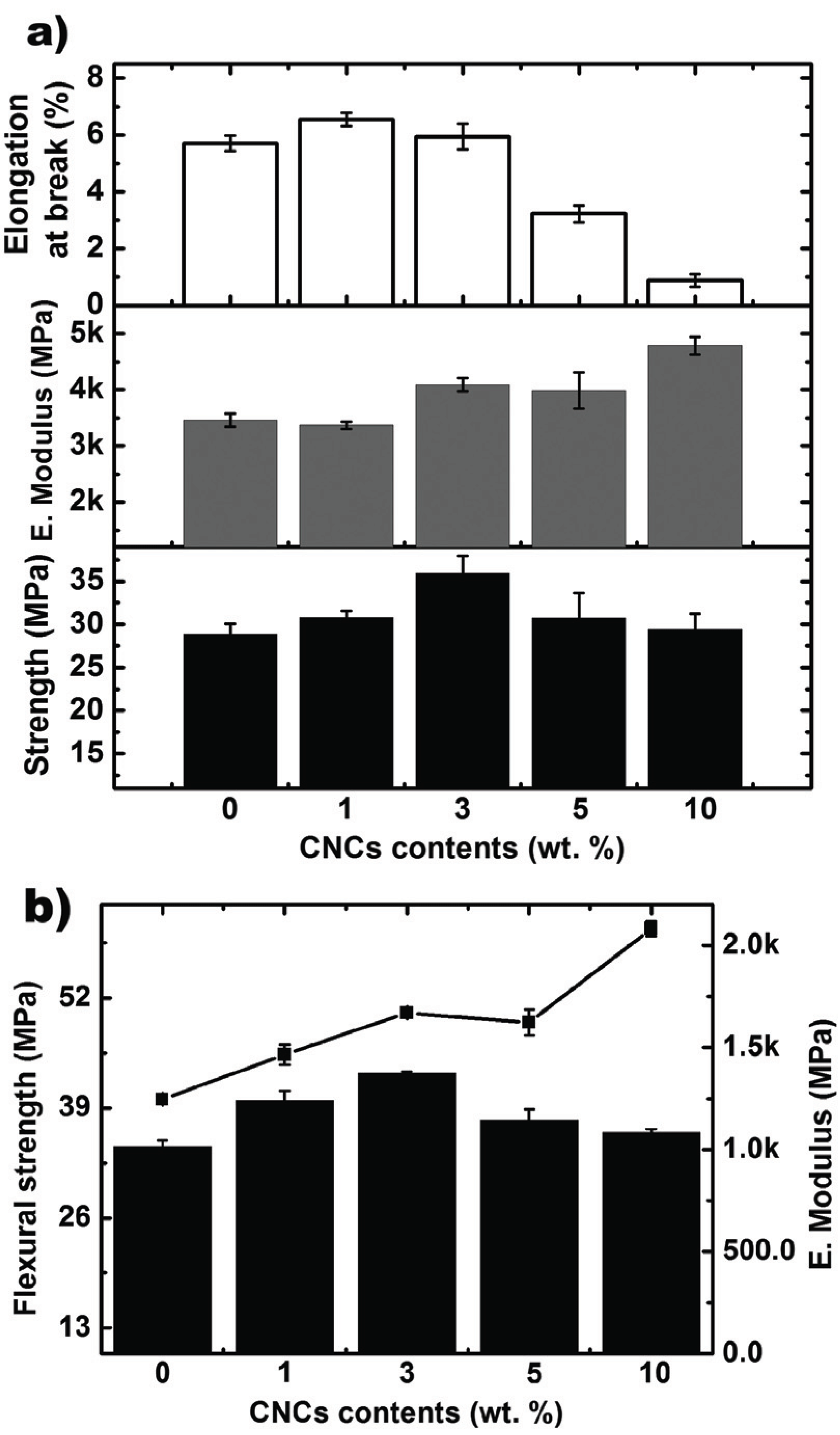
In the case of CNCs used in this study with L/D being the aspect ratio of the nanoparticles, L/D was about 26, and νRc was 2.6 vol.%. Considering that the density of CNCs is 1.5 gcm-3 (Leite et al., 2016), flocculation of CNCs occurs at about 4.0 wt.%, which is one of the reasons why the reduction in strength occurs. The modulus is the stiffness of the material, and even though the CNCs agglomerate due to the strong CNC particles, external stress can be transferred to both the resin and the particles. Therefore, the stiffness of the composite material itself may increase as the content of the nanoparticles increases. The enlogation at break is the capability of a resin to exhibit viscoelasticity, but in this study, the CNCs were simply used as a filler, so that the enlogation at break of the resin itself could not be improved. When a filler is added, the maximum elongation at break can be reduced because the resin endures greater force and breaks without any deformation. After the nanoparticle flocculation occurs, the maximum load value becomes smaller and a flocculation phenomenon occurs. Therefore, the value is lowered because the composite material may be broken with less force.
Fig. 3 shows the thermal behavior of CA/CNC composites by TGA (thermogravimetric analysis). The weight reduction rate of the composite materials by the thermogravimetric analysis is shown in Fig. 3a, and the derivative value thereof is shown in 3b. The pyrolysis of CA/CNC composites with plasticizer has been reported to occur mainly in three stages (Leite et al., 2016). The first stage is caused by the evaporation of residual water remaining in the composite material at 130-240 °C. The second stage occurs in a temperature range of 250-330 °C where the acetyl group decomposes from the main chains of CA while forming acetic acid. The decomposition of TEC plasticizers occurs extensively in the temperature ranges of the first and second stages. The last stage, or the third stage, occurs at 350 to 425 °C due to thermal degradation of the main chains of CA (Claro et al., 2016; Leite et al., 2016).
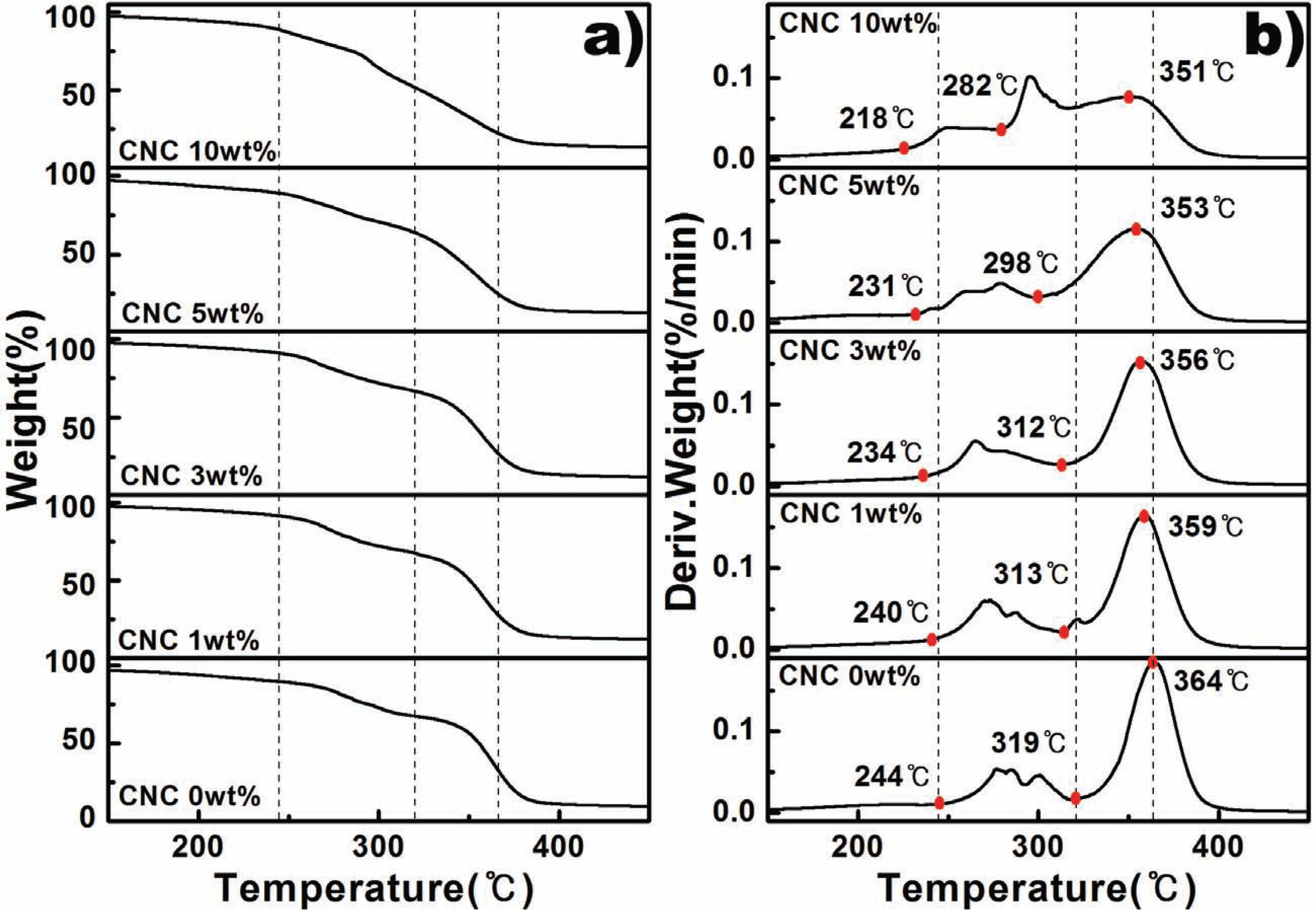
In this study, thermal behavior caused by residual moisture in the composite materials was not seen, because the pressure and injection process using high temperature (>160 °C) was used when the composite materials were being fabricated. As shown in Fig. 3b, the CA/CNC composite materials are thermally degraded in two stages, having a main peak between about 200-320 °C and 320-400 °C. Therefore, it is thought that the acetyl groups in the main chains of TEC and CA, which are plasticizers, are decomposed in the first pyrolysis zone, and the main chain of CA is decomposed in the second thermal degradation zone. There are two points to be noted in the differential graph of the weight reduction rate (Fig. 3b). The first is the decomposition behavior of sulfuric acid-treated CNCs. CNCs produced by sulfuric acid hydrolysis is mainly pyrolyzed at over 170 to 250 °C (Gwon et al., 2016). Unsulfurized CNCs begin decomposition at 330 °C (Leite et al., 2016). However, CNCs produced by sulfuric acid hydrolysis start to decompose at about 170-180 °C due to the catalyzed thermal degradation teaction of sulfate functional groups on CNCs surface. However, in this study, the decomposition behavior of the composite materials with CNCs added at the above temperature was not observed. The reason is that the thermal stability of the CNC is improved between the CNCs surface and the CA main chains by strong hydrogen bonding. The second point to be note is that the onset temperature of the above two zones decreases as the CNCs content increases. As described above, plasticizer was added to the first thermal degradation zone, and CNCs were added to the acetyl group decomposition zone of CA. CNCs themselves increase their decomposition temperature through interaction with CA. However, it seems that the temperature that starts thermal degradation in this zone rose because CNCs themselves act as an acid catalyst promoting pyrolysis due to the sulfate group attached to the surface. As the CNCs content increases, the thermal decomposition of the CA main chains of the second zone is sped up because CNCs generate large amount of decomposition gas during thermal degradation, and these gases form a lot of voids in the polymer resins and induce decomposition of the polymers to cause a change in the thermal diffusion mechanism (Leite et al., 2016). Consequently, the addition of sulfuric acid-treated CNC nanoparticles does not improve the thermal stability of the polymer composites because of the sulfate groups formed on the surface by sulfuric acid. However, since CNCs are a highly compatible chemical with CA, CNCs' surface can be chemically modified or overcome this issue by introducing a flame retardant.
4. CONCLUSION
This study analyzed how the addition of CNCs using the predispersion and the extrusion and injection methods affects the fabrication and properties of CA nanocomposites. In fabricating CA composites, the predispersion method has improved the dispersibility of CNCs in the material, which leads to the reinforcing effect that improves the strength of the composite material. However, when the content of CNCs was more than 3 wt.%, flocculation associated with the percolation effect of CNCs occurred, resulting in a decrease in strength. It was confirmed that the addition of CNCs did not improve the thermal stability while reducing the pyrolysis temperature of CA nanocomposites slightly. However, it can be overcome by surface modification of CNCs and injection of flammable materials. Therefore, CA nanocomposites with CNCs fabricated by the predispersion method and the pressure/injection method can be used in many industrial fields, and it is a manufacturing method capable of improving low mechanical strength, which has been a disadvantage of CA composite materials, and enabling mass production.