1. INTRODUCTION
Heated at a high temperature (160~260°C), the principal components that consist of the cell walls of wood (cellulose, hemicellulose, and lignin, etc.) experience chemical changes like thermal hydrolysis process, which results in changing the physical-dynamic as well as weatherproof performance (Militz, 2002; Park et al., 2016). Various research on wood heat treatment as an environmental-friendly preservative and insect-proof process since the early 2000s has been conducted mainly in Europe. It has been reported that the color of heat-treated wood turns darker, its dimensional stability improves as the hydrophobic property increases, and its weatherproof performance increases (Repellin and Guyonnet, 2005; Esteves et al., 2008; Yoon et al., 2008; 2009; Park et al., 2012; 2014; 2015; 2016). Thanks to such property changes, heat-treated wood is considered to be widely used for garden furniture, fences, pillars, wood storage closets, window frames, doors, furniture, deck materials, outdoor wall materials and flooring materials where dimensional stability or weatherproof performance is required (Esteves and Fereira, 2009; Kim, 2016). The property changes of wood by heat treatment differ depending on the temperature and duration of heat treatment, as well as the types of heat transfer media used for heat treatment (Kim, 2016). Dimensional stability due to the increase of the hydrophobic property has been recognized by many studies on the property changes of heat-treated wood under various conditions (MIlitz, 2002; Homan et al., 2004; Sandberg et al., 2013; Kim, 2016). It has also been reported that the resistance of heat-treated wood to bio-deteriorating factors increases thanks to the chemical changes of the cell walls of wood caused by heat (Homan and Jorrison, 2004; Kim, 2016). However, the weatherproof performance of heat-treated wood varies depending on the heat treatment process, process conditions, and the type of wood, and therefore, the development of an optimal process for target wood is urgently required, and furthermore, heat treatment needs to be carefully considered based on the environmental conditions and usage as it does not exhibit the same weatherproof performance as preservatives against all rot fungi and shows poor weatherproof properties in an environment where wood makes contact with soil or water, and particularly, its resistance to insects is extremely low (Kim, 2016).
Recently, there has been research on the heat treatment with superheated steam on wood (Park et al., 2012; Park et al., 2014; Park et al., 2016; Han et al., 2017; Park et al., 2017a; 2017b). Superheated steam is a steam of which temperature is over the boiling temperature and is used to dry not only wood, but food or sewage sludge (Kim et al., 2008). The heat treatment with superheated steam on wood offers low energy loss and high energy efficiency as the drying and heat treatment of wood are performed at the same time through a single process (Park et al., 2017a). The heat treatment on wood with superheated steam offers superior heat treatment effects to the existing hot air treatment process under the same temperature and duration as the former promotes the thermal hydrolysis process by steam at high temperature and high pressure (Park et al., 2014; Park et al., 2016). This means that the heat treatment with superheated steam causes considerable property changes to wood, such as the increase in the dimensional stability and bending and compressive strengths due to the increase in hydrophobic properties (Park et al., 2016). Furthermore, it has been reported that the decay lab test on heat-treated wood with superheated steam showed that its resistance to brown and white rot fungi greatly increased (Park et al., 2014; Korea Forest Service, 2016).
In the present study, a field decay test was conducted for 12 months to evaluate the deterioration of heat-treated larch with superheated steam. Particularly, the study aimed to evaluate the treated wood's resistance to brown and white rot fungi as well as various insects including termites.
2. MATERIALS and METHODS
In this study, we used larch wood purchased from the Dongbu Wood Distribution Center of the National Forestry Cooperatives Federation, which was felled from an area nearby Donghae, Gangwon. The large wood used for the heat treatment was 2.0 m (L) × 150 mm (W) × 50 mm (T).
Fig. 1 shows the heat treatment device with superheated steam used in this study (Park et al., 2016). It consists of a reactor, a condenser, a feed tank, and a vacuum pump. The reactor is a cylinder with the internal diameter at 640 mm, its length at 2.2 m, and its internal volume is about 0.7 m3. Using the ceramic heater installed inside the surface of the reactor, the temperature can be increased by up to 400°C, and there is one pressure sensor which can measure the internal steam pressure, three temperature sensors that can measure the temperature of internal steam, and three temperature sensors that can measure the temperature of the inside of the wood during the heat treatment process. The measured pressure and temperature values can be monitored in real-time by a computer linked to the reactor. The condenser collects and condenses the flammable organic compounds from the wood as well as the moisture vaporized from the wood whereas the feed tank is used to inject distilled water to generate superheated steam when the process starts, and finally the vacuum pump is used to remove internal air when the process starts.
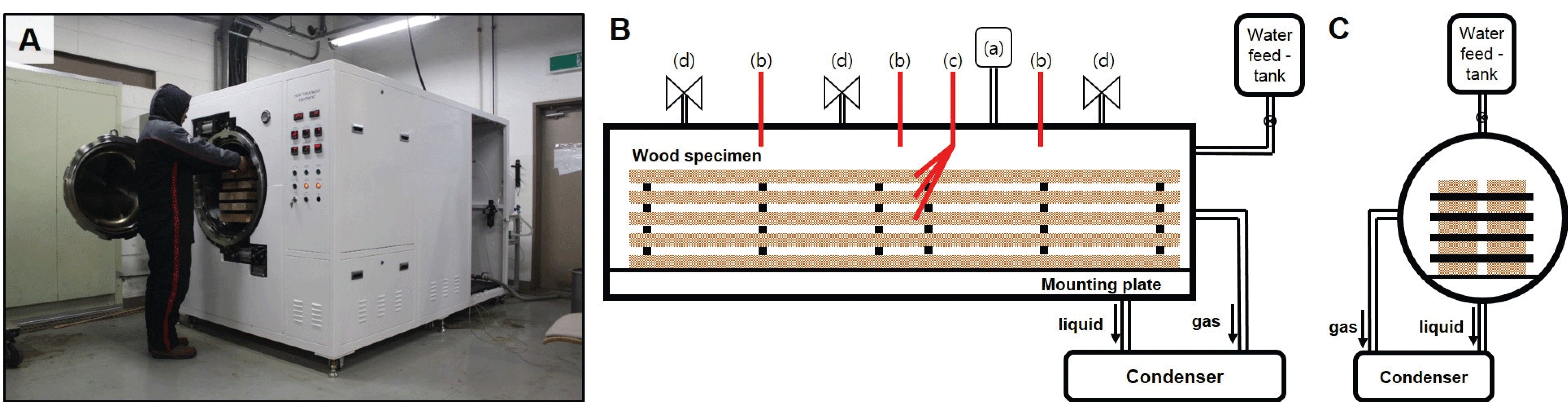
The heat treatment process with superheated steam is as follows. First, larch specimens are piled inside the reactor, and after the reactor is sealed, the distilled water is inserted to generate superheated steam. At this point, the amount of distilled water is determined by the specific volume of superheated steam and the volume of the reactor at the target temperature and pressure conditions. Under the target condition of 0.5 MPa at 250°C, the specific volume of superheated steam is 0.47 m3/kg, and the volume of the reactor is 0.7 m3, and thus, the amount of the required moisture to generate superheated steam is about 1.48 kg. However, twice as much as the required amount of distilled water, 3.0 kg, was injected to have the reactor filled with steam fast in the initial stage of the process. After decreasing the internal pressure of the reactor at or below 0.01 MPa by removing internal air with the vacuum pump, the heater is operated to evaporate the distilled water injected to the reactor and increase the internal pressure. Once the internal reactor pressure reaches the target pressure, the target pressure is maintained by taking out the excessive amount of steam with the pressure control valve. The internal temperature is maintained at the target temperature with the On/Off system of the heater. The heater is operated for 18 hours.
For the field decay test, we produced 40 specimens from the heat-treated 2.0 m long larch wood, each of which was 300 mm in length (fiber direction) and 38 mm in width and thickness (transversal direction).
As a control group, we used non-treated (dried) wood and preservative wood. 40 dried larch stakes and 40 ACQ-II (Alkaline Copper Quaternary) preservative-treated larch stakes of H3 grade, both of which were 300 mm in length (fiber direction) and 38 mm in width and thickness (transversal direction), were purchased from the Dongbu Wood Distribution Center at the National Forestry Cooperatives Federation.
For the field decay test, the estimation testing site at Nambu Experiment Forest, Seoul National University, located at Mt. Baekun, Gwangyang, Jeollanam-do, was selected. The testing site was prepared at a high hill region far from fields and paddles so that chemicals like weed killers or agricultural pesticides cannot be introduced. Referring to AWPA Standard E7-15 『Standard Field Test for Evaluation of Wood Preservatives to be Used in Ground Contact (UC4A, UC4B, UC4C); Stake Test』, the ground was dug up to 150mm and all specimens were buried in length so that half of the length of the specimens was put under the ground and the other half was exposed to the air (Fig. 2). The 40 specimens buried on the same day were divided into four groups, each of which was retrieved after three months, six months, nine months, and 12 months, respectively. While AWPA Standard stipulates that bare-eyed observation is used to determine the degree of decay of wood, the result of such an evaluation may vary by the evaluator's opinions, and therefore, we aimed to evaluate the change of the weight of specimens after the field decay test by measuring the weight of the specimens before and after the test. Equation (1) was used to evaluate the mass reduction ratio of specimens after the field decay test. At this point, the effect of the moisture content ratio was excluded from the evaluation by measuring the oven-dry weight of the specimens.
where Wbefore is the oven-dry weight (g) before the field decay test, and Wafter is the oven-dry weight (g) after the field decay test.
To evaluate the amount of the remaining preservatives inside the preservative-treated wood, the copper content in the preservative specimens after the field decay test was measured. The preservative wood without the field decay test, the preservative-treated wood after the field decay test for three, six, nine and 12 months, and non-treated larch wood without preservatives were pulverized at or below 0.5 mm, and the copper content included in the wood flour by sending the specimens to the Center for the Analysis of Soil Contamination, the National Instrumentation Center for Environmental Management at Seoul National University. The measurement used the ICP (Inductively Coupled Plasma) Mass Spectrometer (Varian 820-MS, Varian, Australia).
Using the copper ion content (G) and the density of the preservative-treated wood (ρ) measured by KS F 2155 (Method of Determination for Preservatives Absorption of Treated Wood), the mass of the copper compound (CuO, Go) was calculated, and with the copper compound mass and the volume (V) of the preservative-treated wood, the amount of the remaining preservatives (R) was determined . (Eq. (2), Eq. (3))
3. RESULTS and DISCUSSION
Fig. 3 shows the temperature change in wood and the temperature and pressure changes of steam during the heat treatment with superheated steam. Initially, the wood temperature and the steam pressure and temperature soared rapidly. When the steam temperature and pressure reached the target values (250°C and 0.5 MPa), the internal temperature of wood reached the steam saturation temperature (151.84°C) at 0.5 MPa, which was maintained for about three hours. Park et al. (2014) reported that during the heat treatment with superheated steam, the wood dried up at the point in which the wood temperature increased after it maintained for some time. In other words, while the wood temperature maintained for some time, the internal moisture was completely removed, and the thermal energy that had been used for removing moisture started to be used to raise the wood temperature, resulting in the rise of the temperature. The wood temperature when the process completed was about 220°C. Considering that it was between 160 and 260°C when the chemical changes of the main components of wood occurred due to the heat treatment, it is determined that the wood has been heat-treated for about ten hours.
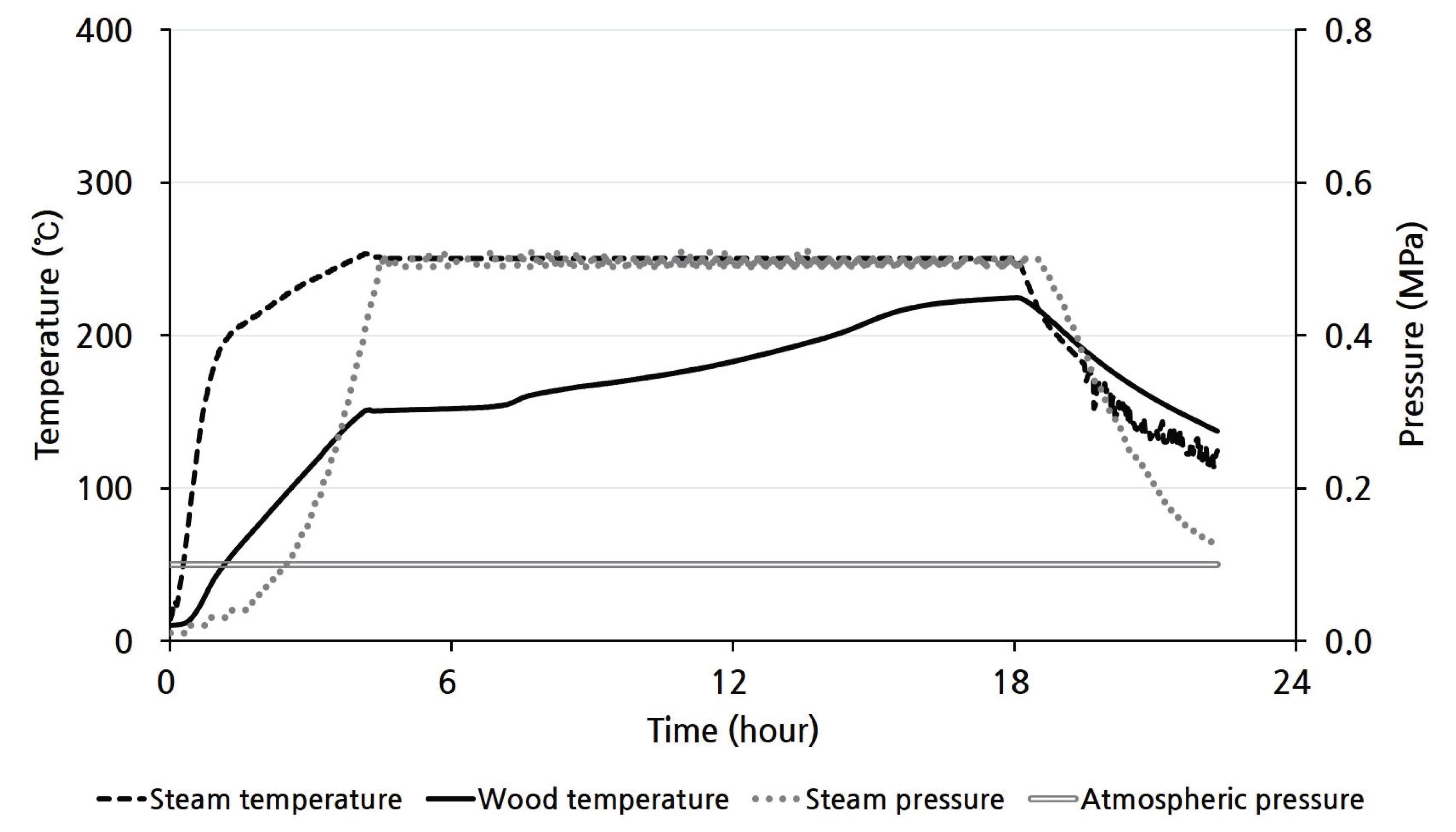
Fig. 4 shows the mass reduction ratios after the 12-month field decay test. The mass reduction ratio of the non-treated wood changed from 3.70% → 4.05% → 4.62% → 5.19%, showing a 3.7% mass decrease in the initial three months, and a gradual mass increase as the test continued whereas that of the preservativetreated wood changed from 3.60% → 5.09% → 4.80% → 4.36%, and similar to that of the non-treated wood, it was around 4%, regardless of the duration of the test. On the other hand, the mass reduction ratio of the heat-treated wood with superheated steam changed from 1.10% → 1.06% → 0.60% → 1.06%, which was around 1% regardless of the duration of the test.
As shown in Fig. 5A, the damage by termite was identified on the non-treated wood after the three-month field decay test while the preservative-treated wood and heat-treated wood with superheated steam did not show any damage by termite (Fig. 5B, C). The result was contrary to previous studies which reported that heat-treated Korean pine (Pinus koraiensis S. et Z.) and lodge-pole pine (Pinus contorta Dougl.) were extremely prone to termite (Ra et al., 2012). The property change of heat-treated wood is believed to be much varied by the type of wood, the treatment temperature and duration, and the thermal media used in the treatment. Ra et al. (2012) performed the heat treatment of Korean pine and lodge-pole pine at 170, 180, 200, 220, and 230°C for 90, 120, 180, 240, and 270 minutes, whereas this study performed the heat treatment on larch with steam at 250°C for 18 hours. Since the wood was exposed to steam over 160°C for about ten hours, and therefore, the specimens were exposed to the high-temperature longer than in the previous studies. Furthermore, the heat treatment with superheated steam promotes the thermal hydrolysis process by the superheated steam, which is reported to have more heat treatment effects than the existing, hot air-based, process (Park et al., 2016). A considerable amount of hemicellulose, one of the key components of wood, is decomposed, and the decomposed products from hemicellulose are crosslinked with lignin to create high lignin molecules (Esteves et al., 2008; Park et al., 2017b). Such chemical changes lead to the reduction of the number of -OH groups, the increase in the hydrophobicity of wood, and the reduction of the equilibrium moisture content based on the relative humidity. That is, it is determined that the extremely high heat treatment causes the chemical changes and consequently property changes of the wood, and the growth condition of organisms like rot fungi or termite change, and thus, the weatherproof performance of the heat-treated wood with superheated steam improves. However, to determine whether the field decay test on the heat-treated wood with superheated steam was effective, a long-term observation for more than 12 months would be required.
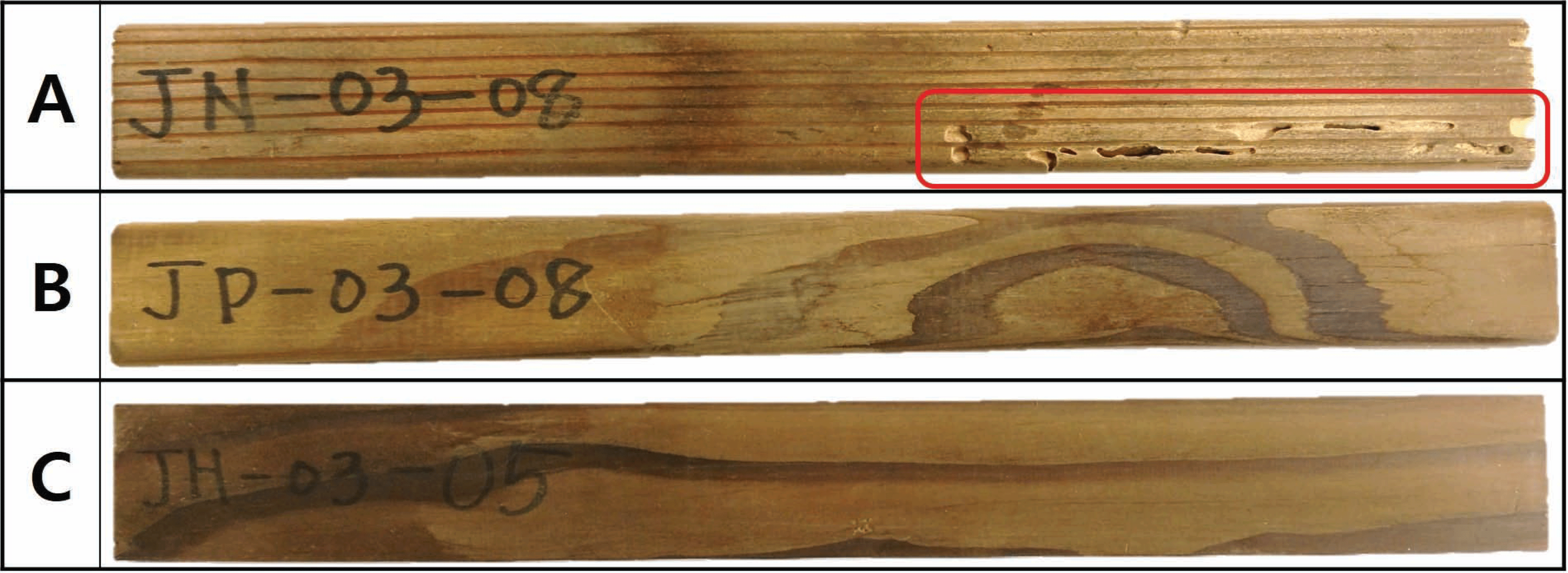
The mass reduction ratio of preservative-treated wood in the field decay test was shown to be similar to that of the non-treated wood despite the fact that there was little damage by termite or rot fungi. To evaluate the potential elution of preservatives injected into the wood during the field decay test, the amount of the remaining copper ion, one of the key components of the preservatives, was measured. As shown in Fig. 6, the copper ion content in the preservative-treated wood that was not used in the field decay test was about 4.2 g/kg whereas the one used in the field decay test was between 1.5 and 2.5 g/kg. The unit (g/kg) used in this measurement means the copper ion content included in 1kg of preservative-treated wood. Also shown in Fig. 6 is the remaining preservative content determined by the measured copper ion content (G), the density of the preservative-treated wood (ρ), and the volume of the preservative-treated wood (V). While H4-graded preservative-treated wood should be used for the field decay test that makes contact with the ground, the present test used H3-graded preservative wood. But the preservative content of the preservative-treated wood used in the study was about 4.9 kg/m3, which was similar to the minimum preservative content of H4-graded wood, and thus, it was determined that the H3-graded preservative-treated wood would be suitable for the test. Although there was no tendency in the amount of the eluted preservative in relation to the duration of the test during the field decay test, the remaining preservative content decreased drastically compared to the preservative-treated wood not used in the test so that it was believed that the preservative was eluted. In other words, the mass reduction of the preservativetreated wood was not only due to the deterioration by rot fungi or weathering, but also by the elution of the preservative injected to the wood.
4. CONCLUSION
In this study, we evaluated the resistance performance of heat-treated larch wood with superheated steam against rot fungi and insects through the field decay test. The heat treatment process with superheated steam was conducted under the superheated steam conditions of 0.5 MPa at 250°C for 18 hours of the heater operation, at which the maximum internal temperature of the wood was 220°C, and under the temperature at or over 160°C when the heat treatment of wood is performed, wood was exposed to the steam for about ten hours. As a control group for the field decay test, the study used the non-treated wood and H3-graded preservative wood injected with ACQ-II preservative (preservative content: 4.9 kg/m3).
The results of the 12-month field decay test showed that the mass reduction of the heat-treated wood with superheated steam was about 1%, and the visual inspection showed no damage by rot fungi or termite. On the other hand, the mass reduction of the non-treated wood was about 5%, and there was marked damage by termite. The mass reduction of the preservative-treated wood was also about 5%, but there was no termite damage. The measurement of the remaining preservative content injected in the preservative-treated wood showed that some of the preservatives were eluted. In other words, the mass reduction of the preservative-treated wood during the field decay test was not only by the rot fungi or weathering, but also by the elution of the preservative.
While the existing studies have reported that the resistance of heat-treated wood to termite was extremely low, the results of the present study after the 12-month field decay test showed that the resistance performance of the heat-treated larch wood with superheated steam against termites was extremely high. It is believed that this is because of the huge heat treatment effect as the wood was exposed at the high temperature for a long time. However, due to the characteristics of the field decay test that requires long-term observation, the results from a long-term test over 12 months would be required to determine the resistance performance of heat-treated wood against rot fungi and insects.