1. INTRODUCTION
Wood is the most in-demand construction material worldwide and widely used in various areas from civil engineering to landscaping, furniture and flooring materials. Its demand is on the rise. According to the forest industry statistics by Korea Forest Service (2018), wood self-sufficiency has been maintained at around 16% for the last three years. While it depends on the economy or the price of import materials, wood self-sufficiency is expected to gradually increase as various measures are actively promoted to activate the use of domestic wood materials, including forest green policies. Accordingly, it is necessary to efficiently use wood and promote high value addition. However, the universal use of wood as industrial materials is limited, and the main reason is the change of physical and dynamic properties caused by moisture. If problems caused by the contact with moisture are solved, the value of wood can be highly improved, and in terms of the material use, it can be used instead of plastic, inorganic materials, or metals. In addition to physical properties, the dynamic properties of wood limit the use of wood as materials. Still, wood is known to be as useful as other materials thanks to its lightweight and high strength while its absolute strength is weak. Wood density, the primary evaluation standard of wood properties, has a decisive effect on the physical and dynamic properties of wood. Thus, a method that could promote density improvement and dimensional stabilization, which would lead to the increase in wood strength, may allow wood to be used in various areas more efficiently in terms of environmental and economic perspectives.
As such, the specific gravity of wood, the primary property in testing the quality of wood, has a direct correlation with the dynamic properties of wood, and the improvement in the specific gravity will lead to the improvement of its dynamic properties. As a method that would promote the mechanical properties of wood, thermal compression of wood reduces the volume of the material in the same mass, which results in the specific gravity and increases the mechanic properties of wood. As the results of such research, the research team of this study confirmed the marked improvement of the strength properties when the specific gravity of the domestic soft wood species was improved by the thermal compression process (Hwang et al., 2014).
Thermal compression aims to acquire high specific gravity by changing and fixing the shape of wood, which has low specific gravity and consequently has weak mechanical properties, by applying heat and pressure. This method is one of the forming processes often used to improve the mechanical properties as the specific gravity increases. In Japan, active research has been conducted on the thermal compression of Japanese cedar (Inoue et al., 2008). Furthermore, it was very impressive that Hida Industries in Japan used bending processing, one of the forming processes, on furniture. The most important property of wood when its specific gravity is improved by forming processes like thermal compression or the bending process is dimensional stabilization. It is well-known that the dimensional recovery of processed wood by the penetration of moisture causes fatal mistakes, resulting many problems in the use of wood. The heterogenous properties of wood, which is a bio material, causes irregular shrinking or swelling, making it difficult to manage wood at sites. Without guaranteeing the dimensional stabilization of thermally compressed wood, the elastic energy stored in the wood is resolved by heat and moisture, and wood becomes memory-forming material whose shape is recovered. Such form recovery causes defects on the floor when thermally compressed wood is used as flooring materials like deck materials. To overcome this issue, various methods, such as resin process (Inoue et al., 1991), chemical process (Inoue and Norimoto, 1991), thermal process (Inoue et al., 1991), or steam process (Inoue et al., 1993), had been attempted. Thus, it is important to restrict the form recovery force of thermally compressed wood if it is to be used.
The previous study by the present research team (Hwang et al., 2015) reported that when thermal compression was performed for 10, 20, or 30 minutes at 140°C, 160°C, 180°C, and 200°C, the specimen at 200°C-30min showed the most superior dimensional stabilization. Another previous study (Cho et al., 2015) conducted the thermal compression at 180°C for 60min of compression period at the pressure of 80kgf/cm2, and later, the thermal process at 80°C, 100°C, or 120°C was performed for 2, 6, 12, and 24 hours. The results showed that the thickness recovery ratio of the thermally compressed wood at 120°C-24h was 3.8%, and when compared with the specimen without thermal process, the thickness recovery ratio was reduced by about 67%. As such, since there is clearly the different properties by wood species, it is absurd to say that the results of a certain wood species would represent the process condition of all species.
Toward this end, in this study, Korean pine was selected for the material considering the effective use of Korean pine in future, which has been widely planted in Gangwon and Gyeonggi regions. The test aimed to acquire the dimensional stability by the thermal compression and air-dry process of Korean pine and examine the optimal conditions for the dimensional stabilization and reviewed the result of the test.
2. MATERIALS and METHODS
This study used Korean pine (Pinus koraiensis) among Korean soft wood species. Flat-sawn Korean pine were cut in 60mm(L) × 60mm (T) × 24mm (R) to create a specimen. The air-dry specific gravity of the specimen was 0.43 (±0.01), the moisture content was 12.8% (±0.31%), and the average annual ring width was 4.59mm (±0.55).
The thermally compressed specimen was created in the same way as in the previous studies (Cho et al., 2015; Hwang et al., 2014; 2015). A Korean pine specimen in 24mm thickness was thermally compressed by 50% to create a specimen in 12mm thickness. Before the thermal compression, the material was sealed with polyethylene film to soften it and was put into a 700 W microwave oven for 90 seconds. Then the thermal plate press was used to perform the thermal compression in the radial direction at 200°C of the thermal compression temperature and 80 kgf/cm2 with different thermal compression durations at 60 minutes and 90 minutes. Fig. 1.
During the thermal compression, the swelling of the surface was observed when the process was completed while the moisture inside the heated specimen could not be extracted out. To prevent this and to allow the internal moisture to be extracted fully, the initial thermal compression, in which the compression in one minute was followed by the disengagement of the compression for another 30 seconds, was performed twice. Later, at five minutes before the completion of the thermal compression, the pressure was removed without taking the specimen out so that the internal stress generated in the process could be slowly removed. The resulting specimen was placed in a desiccator with silica gel for one day.
The post-thermal process of the specimen after the thermal compression was performed with a hot air drying oven. Five specimens were processed at 120°C, 140°C, and 160°C for 2, 6, 12, and 24 hours for each condition. The control group was set based on the data from the previous study (Hwang et al., 2015).
To verify the dimensional stability of the specimen, a 24-hour absorption test was conducted based on KS F 2204. In KS F 2204, the waterproof paint is applied to the side that is not the absorption side so that moisture cannot be absorbed. However, in this study all sides were exposed to moisture to conduct the test under the same conditions as those of the previous studies. A total of 20 specimens were used for each thermal process temperature setting. The three sides of all specimens were exposed to the air and placed in a desiccator, and using a load plate with holes, they were submerged about 50 mm below the water. To measure the amount of absorption and the swelling ratio based on the absorption time, the weight and thickness of the specimens were measured in every 30 minutes from the start to two hours, in every one hour from two to five hours, in every two hours from five to nine hours, and in every three hours from nine to 24 hours. Before each measurement, the specimens were wiped with dry towel to remove the moisture on the surface.
To examine the dimensional recovery ratio, the thickness recovery ratio of the specimens of which thickness had been reduced by thermal compression. It was measured along with the measurement of the weight and thickness during the 24-hour absorption test. After the 24-hour absorption test, the specimens were dried at 105°C, and then, the thickness of each specimen was measured to determine the final dimensional recovery ratio (Hwang et al., 2015).
3. RESULTS and DISCUSSION
The specific gravity of the specimen after the thermal compression was 0.79 (±0.06), an about 84% increase from 0.43. This increase of specific gravity will improve the dynamic performance of Korean pine. In a previous study (Hwang et al., 2014), the thermal compression of Korean pine by reducing its thickness by 50% increased the specific gravity by about 71% compared to the control group, and the internal density distribution verified the evenness of the material quality of the lumber. Furthermore, the lateral compression strength increased by 76%, the flexural strength by 83%, and the surface hardness by 55%. Thus, it is determined that the increase in specific gravity will contribute to the improvement of the dynamic performance of Korean pine.
Shown in Fig. 2 is the moisture absorption of specimens based on the 24-hour absorption test. According to a previous study (Cho et al., 2015), the maximum absorption was shown in the first hour of the absorption test in all thermally treated samples, and later it fell drastically so that after five hours, it tended to stabilize. Such a pattern was also observed in this study. In the first hour, the maximum absorption was recorded, and after five hours, the absorption tended to stabilize, similar to the result of the previous study. Furthermore, the dimensional stabilization by thermal process also showed a similar pattern, decreasing by temperature and time.
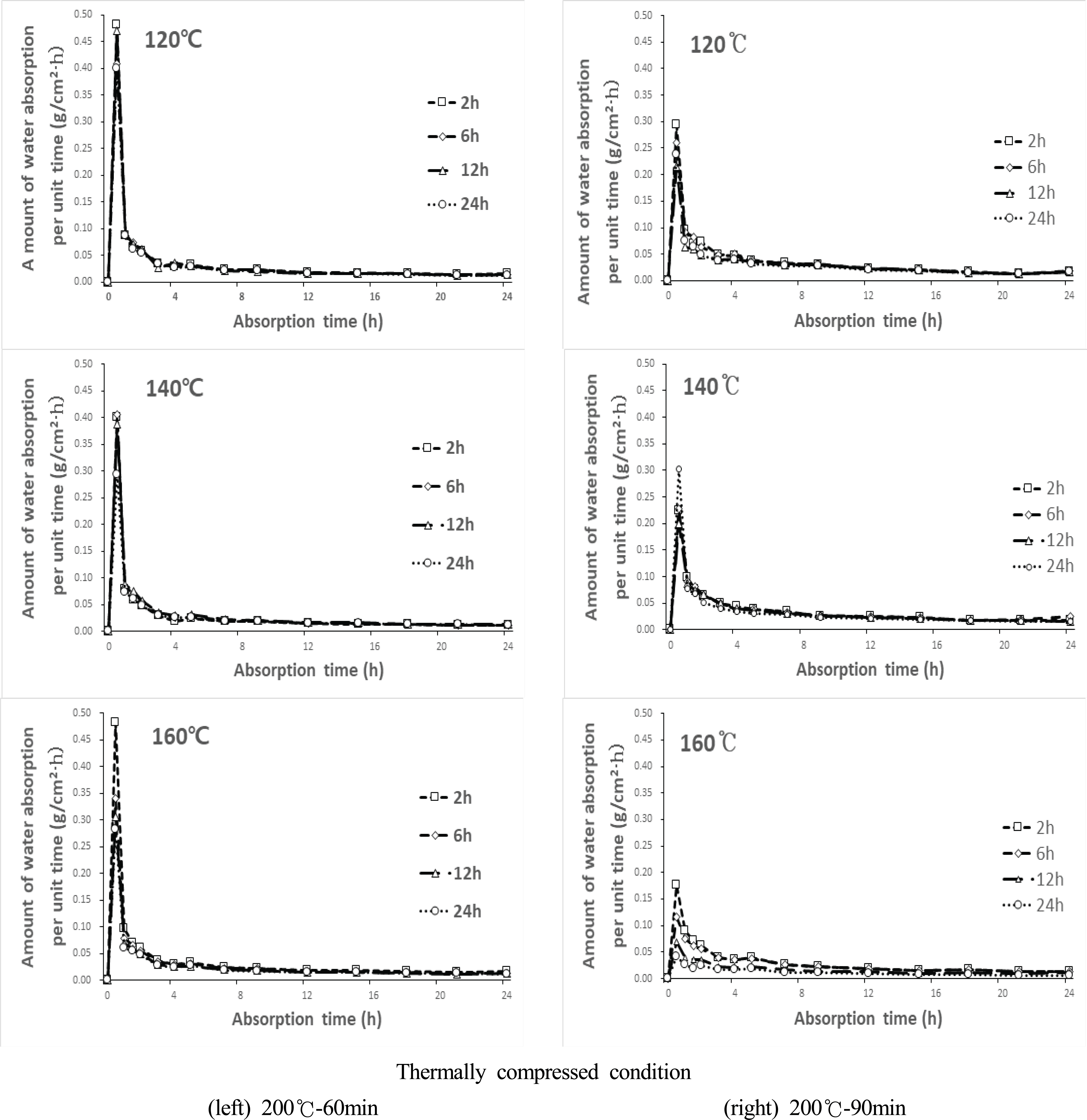
To examine the change of absorptiveness by the thermal process temperature, the test compared the amount of absorption by surface area at the point when the first hour of the absorption test passed, which showed the highest amount of absorption. The thermally processed specimen at 120°C after the thermal compression of 200°C and 60 minutes showed the amount of absorption between 0.567-0.485 g/cm2·h. At 140°C and 160°C, it was 0.479-0.365 g/cm2·h and 0.580-0.344 g/cm2·h, respectively. And, the amount of absorption after five hours when the absorption started to stabilize was 0.028 (±0.004) g/cm2·h on the average.
Moreover, the amount of absorption by the duration of thermal process generally decreased. At the first hour, the amount of absorption by unit hour based on the thermal process condition of 120°C and 2, 6, 12, and 24 hours was 0.567, 0.496, 0.561, and 0.485 g/cm2·h respectively, reflecting no drastic difference within 120°C. At 140°C, however, it was 0.479, 0.488, 0.475, 0.365 g/cm2·h respectively. Also, at 160°C, it was 0.580, 0.418, 0.375, 0.344 g/cm2·h respectively. Except the specimens at 120°C for 12 hours, the amount of moisture absorption per unit hour decreased as the duration amount of heat treatment increased, and after five hours when the absorption stabilized, all specimens showed similar amount of absorption regardless of the duration.
The specimen thermally compressed at 200°C for 90 minutes showed lower amount of absorption than the specimen treated for 60 minutes. This result confirmed that in a previous study that performed thermal compression by temperature and time verified that higher the compressed temperature, or longer the thermal compression duration is generally associated with less amount of moisture absorption (Hwang et al., 2015). The amount of absorption of the specimen at 120°C for the first hour was 0.389, 0.353, 0.278, and 0.312 g/cm2·h, by the duration of the thermal process. At 140°C, it was 0.323, 0.318, 0.285, and 0.380 g/cm2·h, and at 160°C, it was 0.266, 0.192, 0.110, 0.068 g/cm2·h. While the specimen at 160°C showed some drastic change by time, the specimen at 120°C and 140°C did not. Furthermore, the amount of absorption after five hours when it became stabilized was lower at 160°C than at the other temperature settings, and particularly, the specimen at 160°C for 24 hours showed that the amount of absorption was initially 0.019 g/cm2·h and decreased to 0.006 g/cm2·h when the test completed.
The reduction of the absorption by thermal treatment changed the properties of cellulose, hemicellulose, lignin, and other extracts at high temperature, which was known to affect absorptiveness, stability, diffusion, and moisture permeability (Hillis, 1984). Moreover, it has been reported that the deteriorated hemicellulose by thermal process would greatly affect the reduction of the absorptiveness of wood (Hillis, 1984; Inoue et al., 1993).
Gerhards (1982) conducted a strength test on wood based on moisture content and showed that in the zone of lower moisture content, the strength increased by 8 to 35%, and in the zone of higher moisture content, it decreased by 13 to 35%. The higher the moisture content, the more reduction of the mechanical strength resulted. Such reduction of the mechanical strength works against the aim of this study, which is to propose Korean pine as flooring materials, and therefore, the reduction or minimization of moisture in wood is considered essential.
Therefore, only considering the amount of moisture absorption, the thermally compressed wood at 160°C for 24 hours after the thermal compression at 200°C for 90 minutes, which allows the least amount of moisture absorption, is believed to be the most suitable condition.
It is generally known that the swelling of the thermally compressed wood by the absorption test shows the most steep graph slope in the initial period and tends to stabilize afterwards (Jung and Lee, 1998; Laine et al., 2013). As opposed to the above prediction, the previous study showed that a higher swelling slope was observed at one to two hours than at the first hour. It is determined that such a phenomenon is because a large amount of resin included in Korean pine wood was extracted out during the thermal compression and the thermal process and coated the surface of wood. It was determined that such coating somewhat delayed the swelling of the specimens (Cho et al., 2015).
Shown in Fig. 3 are the swelling ratios of the specimens by moisture resulting from the 24-hour absorption test. The thermally compressed specimen at 200°C for 60 minutes showed a rapid swelling speed for the first two hours similar to the result of the previous study. Except the specimen processed at 120°C, there was a reduction of swelling by the temperature of the thermal process. Particularly, the specimen at 160°C for 24 hours showed the swelling ratio at 7.56% (±1.44%).
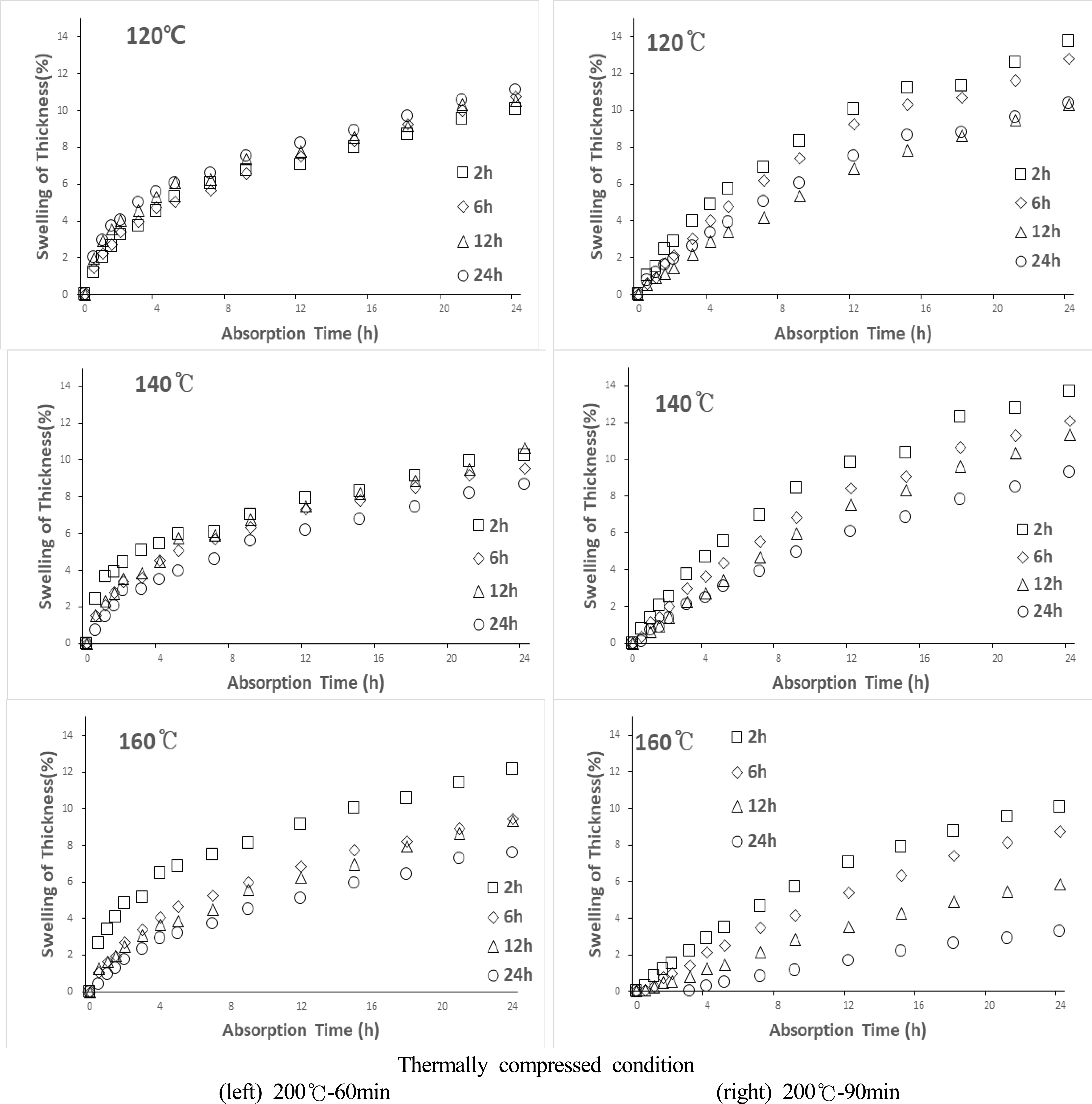
There was a drastic difference among the specimens under another thermal compression condition at 200°C for 90 minutes. As the temperature increased, the specimens showed marked differences at 160°C than at 120°C or 140°C. Particularly, the specimen at 160°C for 24 hours showed the swelling ratio at 3.24% (±0.34%). Compared to the previous study, a clearly reduced swelling ratio was observed with the specimen at 160°C.
The determining area of microfibril during the thermal compression often shows elasticity. At this point, the elastic energy is stored in high molecules of cellulose, and it is believed that the emission of this elastic energy generates internal stress, which is stored in the non-crystalized areas of hemicellulose, lignin, and the non-crystalized area of cellulose. The thermal compression process causes restructuring of the wood structure, and the hydrogen bond between cellulose and hemicellulose and the covalent bond between hemicellulose and lignin change. Because this change is not completely stable, reversible swelling occurs, which can be recovered by the contact with moisture and heat. However, if the cell walls are damaged by the defect in the bond between micro-fibril and matrix, the internal stress generated in the thermal compression process is partially resolved. Thus, the irreversible swelling decreases, and as a result, swelling also decreases (Morsing, 2000; Laine et al., 2013).
The thermally compressed wood is a process material deformed by applying pressure in the radial direction, and thus, at swelling, the dimensional change in the radial direction should be carefully observed. Thus, the specimen with the most stable swelling ratio was the one with the thermal compression at 200°C for 90 minutes and heat treated at 160°C for 24 hours. It showed the most stable swelling ratio at about 3%.
To examine the degree of thickness recovery that had been reduced during the thermal compression process during the 24-hour absorption test, a heat treatment was conducted for 24 hours, and shown in Fig. 4 are the thickness recovery ratios of the specimens.
According to the results of a previous study, dimensional stability generally improves by a heat treatment process after the thermal compression (Cho et al., 2015). Cho et al. showed that the thermally compressed specimen at 180°C for 30 minutes and then passed to a heat treatment at 120°C for 24 hours showed a 3.8% of thickness recovery ratio, but all of the specimens subjected to heat treatment for 24 hours showed a thickness recovery within 1%. There was a drastic difference by temperature, and particularly, at 160°C, the thickness recovery ratio reached almost to 0%, showing very stable dimensional stability.
It has been reported that dimensional fixation by the process of thermal compression is affected by the reduction of absorptiveness and the increase in the degree of crystallinity, the crosslink formation between molecules and improvement of cohesiveness, and the weakening recovery from the deformation due to the decomposition of components (Dwianto et al., 1997). In addition, Norimoto et al. (1993) pointed out that to prevent the compression recovery of thermally compressed wood, one would need to watch out for the crosslink formation between the molecules in the matrix components, the resolution of internal stress formed inside wood, the high molecular components in wood, particularly, hemicellulose, from moisture and heat. Therefore, it appears that the securing of dimensional stability based on the heat treatment after thermal compression is the result of the crosslink formation that prevents the form recovery of the thermally compressed wood, and the covalent bond at the softened and compressed state of lignin during the heat treatment process (Inoue et al., 2008).
Such results showed that the post-heat process after the thermal compression was very effective in securing the dimensional stability of thermally compressed wood. Also, the heat treatment of thermally compressed wood at 160°C could result in very stable thermally compressed wood. Compared to the results of the previous studies, those of this study showed that the heat treatment after the thermal compression resulted in thermally compressed wood with better dimensional stability than those with only the thermal compression. As a result, the specimen with the best dimensional stability was the one heat treated at 160°C for 24 hours.
4. CONCLUSION
The study examined the dimensional stability of thermally compressed wood of Korean pine after the post-heat treatment based on each of the thermal compression conditions and the heat treatment conditions. The wood of Korean pine of which specific gravity was 0.43 was thermally compressed by the thickness compression ratio at 50%, resulting in thermally compressed wood with the specific gravity at 0.79. The higher the thermal compression temperature, and the longer the duration of the process, the more reduction of absorptiveness and swelling resulted. Furthermore, the higher the temperature of the post-heat process, and the longer the heat process, the more reduction of absorptiveness and swelling resulted. The dimensional stability of thermally compressed wood improved with the post-heat treatment after the thermal compression. Particularly, the thickness recovery ratio of the specimen heat-treated at 160°C for 24 hours reached almost to 0%. Therefore, when all of the results of the aforementioned moisture absorptiveness, swelling, and dimensional stability were examined, the thermally compressed specimen at 200°C for 90 minutes and post-heat treated at 160°C for 24 hours showed the highest dimensional stability.