1. 서 론
탄화보드는 첨단 다기능성 신소재로서의 흡착성, 난연성, 원적외선방사, 공기정화기능 및 음이온 발 산 효과 등 과학적으로 검증된 효능이 있어서 새집 증후군 등 기타 유해환경에 살고 있는 현대인에게 필수적으로 필요한 재료에 사용될 것으로 생각된다 (KFRI, 2008). 국립산림과학원에서는 목질제품의 VOC (Volatile Organic Compound) 평가 및 개선 연 구 과제를 수행하면서 파티클보드(PB), 중밀도섬유 판(MDF)와 같은 목질 판상보드를 이용하여 VOC와 포름알데히드 방출이 전혀 없고 유해화학물질제거 능력이 뛰어난 기능성 탄화보드를 개발한 바 있다 (KFRI, 2007).
한편 탄화보드의 실용화를 위한 노력으로 탄화보 드의 표면에 칼라 코팅하는 방법, 탄화보드의 표면에 검게 묻어나는 현상을 방지하기 위하여 1 mm 정도 의 얇은 섬유판을 부착하는 방법, 표면을 세라믹으로 코팅하는 방법 등 다양한 처리가 시도되고 있다. 이 와 같이 탄화보드의 신용도개발 및 산업화를 위해서 는 용도에 맞는 기초연구가 필요한데, 이에 대한 연 구로는 KFRI (2008)가 중밀도섬유판을 이용하여 탄 화온도별로 탄화보드를 제조하고 전자파차폐효과를 측정하였고, Park et al. (2009)은 합판, 파티클보드 및 중밀도 섬유판으로 탄화보드를 제조하여 탄화온 도에 따른 수축률, 중량감소율, 밀도변화 및 표면구 조변화를 조사하였다. 또한 Oh et al. (2003)은 톱밥 보드로 우드세라믹을 제조하고 수지함침률 및 탄화 온도에 따른 표면온도를 측정하였고, Oh (2007)는 소나무로 우드세라믹을 제조하고 제조 시 승온온도 및 최고온도유지시간이 우드세라믹의 표면온도에 미 치는 영향에 대하여 검토한 바 있다.
본 연구에서는 물푸레나무판재, PB, MDF 및 합판 (Plywood)를 이용하여 탄화온도별로 탄화보드를 제 조하고 탄화보드를 발열판으로 이용가능성을 검토하 고자 실리콘 러버히터를 활용하여 탄화온도별로 각 탄화보드의 표면온도를 측정하였다.
2. 재료 및 방법
탄화보드를 제조하기 위하여 물푸레나무판재, 중밀도섬유판(MDF), 파티클보드(PB), 합판(PW)을 400 mm × 400 mm 크기의 시험편으로 재단한 후 실험용 탄화로를 사용하여 탄화온도 400~1100°C 로 100°C간격으로 승온하면서 탄화하였다. 이때 승온속도는 50°C/min.이며, 목표탄화온도에서 2시 간 동안 유지하였다. 표면온도 측정을 위하여 습도 65 ± 5%, 온도 20 ± 1°C에서 일주일간 조습처리 하 였다.
시간의 경과에 따른 탄화보드의 표면온도를 측정 하기 위하여 전기전압 조절장치에 실리콘 러버히터 를 연결하고, 20 V에서 60°C로 목표온도를 설정한 후, 온도센서를 이용하여 히터의 표면온도를 고정하 였다. 가열된 실리콘러버 히터 위에 시험편을 올려놓 고 그 위에 다른 온도센서를 부착하여 시간의 경과, 히터바닥온도의 변화 및 온도하강시간에 따른 표면 온도변화를 측정하였다. 이때 표면온도 측정은 실내 (20 ± 2°C)에서 Thermo Recorder (T and D Co., Ltd TR-71S)를 이용하여 측정하였다.
3. 결과 및 고찰
실리콘 러버히터의 표면온도를 60°C로 설정하고 그 위에 탄화온도 별로 탄화된 4종류의 탄화보드를 올려놓은 다음 3분 간격으로 30분 동안 탄화보드의 표면온도변화를 측정한 결과는 Figs. 1~4와 같다.
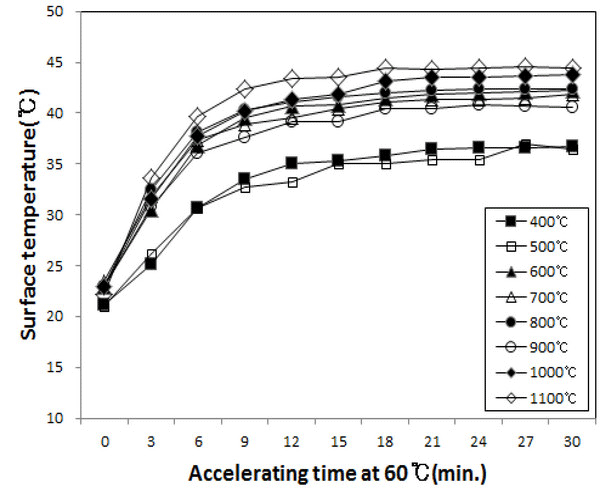
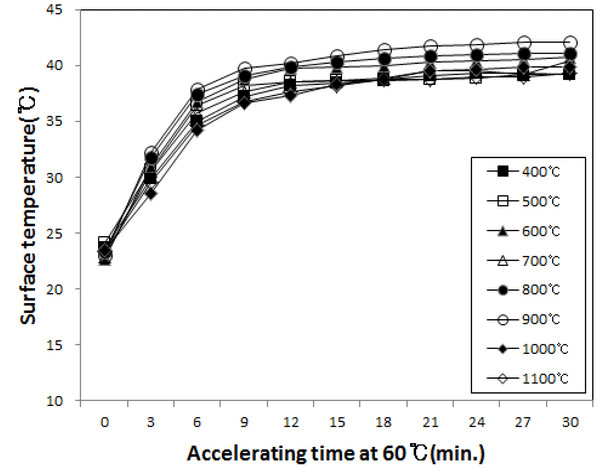
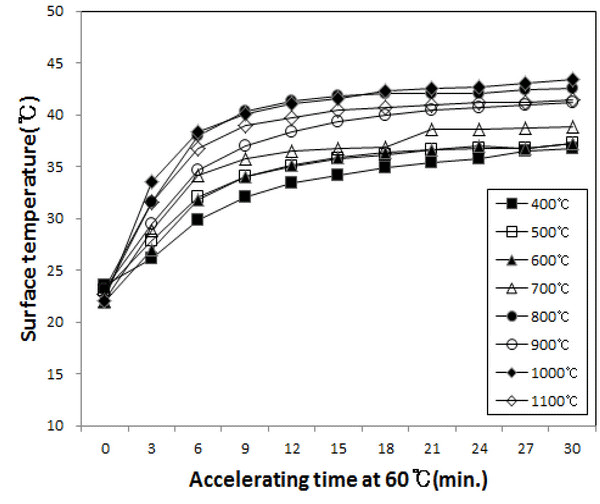
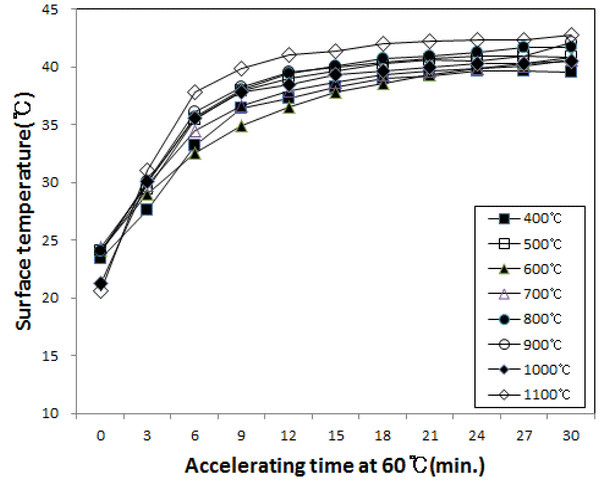
탄화온도별 탄화보드의 표면온도는 시간이 경과 함에 따라 경과시간 12분까지는 급격히 상승하다가 그 이후에는 완만한 상승을 보였고, 20분 이후부터 는 온도가 안정화되었다. 각 보드의 탄화온도에 따른 탄화보드의 30분 경과시간 후의 온도는 탄화 합판 의 경우 탄화온도 1100°C일 때 44.4°C, 탄화MDF는 900°C일 때 42.1°C, 탄화 원목은 1000°C일 때 43.4°C 그리고 탄화PB는 1100°C일 때 42.8°C로 탄 화온도가 900°C 이상일 때 표면온도 상승이 양호하 였다. Oh et al. (2003)이 낙엽송 톱밥으로 보드를 제조하고 수지함침 후 탄화하여 우드세라믹을 제조 한 다음 본 연구와 같은 방법으로 탄화온도별 표면 온도를 측정한 결과, 탄화온도 600°C시편은 52.5°C, 1000°C시편은 55.2°C이었다고 보고한 바 있다. 또한 Oh and Byeon (2004)이 소나무 간벌재로 제조된 우 드세라믹의 표면온도변화에서 측정시간 30분 후 에 탄화온도 600°C 시편은 48.3°C, 1000°C 시편은 57.9°C이었다고 하였다. 이러한 결과와 본 연구결과 에서의 온도차이는 우드세라믹 제조시 함침된 수지 가 탄화과정에서 유리질탄소(glassy carbon)로 변환 되어 열전도에 영향을 미쳤기 때문으로 판단된다.
탄화 후 두께와 밀도에 따른 탄화보드의 온도변화 의 경우에도 Table 1에서 보는 바와 같이, 탄화 합판 은 탄화온도 1100°C일 때 0.34g/cm3, 탄화MDF는 1100°C일 때 0.45 g/cm3, 탄화 원목은 1000°C일 때 0.41 g/cm3 그리고 탄화PB 는 900~1100°C일 때 0.54 g/cm3로 밀도가 클수록 표면온도가 높아 밀도 가 탄화보드의 온도상승에 영향을 미친 것으로 생각 된다. Nanoka et al. (1999)은 활엽수 MDF로 제조된 우드세라믹의 밀도에 따른 열전도율을 측정한 결과, 탄화온도 650°C 시편은 밀도가 0.32 g/cm3에서 0.82 g/cm3로 증가함에 따라 열전도율은 0.085 W/mk에서 0.259 W/mk로, 탄화온도 800°C시편은 밀 도가 0.40g/cm3에서 0.84g/cm3로 증가함에 따라 열전 도율은 0.113 W/mk에서 0.386 W/mk로 증가하였다 고 보고한바 있어, 열전도율은 밀도와 깊은 관계가 있음을 밝힌 바 있다.
표면온도 상승과 관련하여 Table 2에서 보는 바와 같이 표면온도가 최고일 때 시편의 두께는 탄화 합 판의 경우 1100°C일 때 7.86 mm, 탄화MDF는 900°C 일 때 6.55 mm, 탄화 원목은 1000°C일 때 7.23 mm, 그리고 탄화 파티클보드는 1100°C일 때 7.19 mm로 동일재료에서 탄화보드의 두께 또한 열전달 특성과 관련이 있는 것으로 생각된다. 그러나 탄화PB의 경 우 탄화온도 1100°C일 때 밀도가 0.54 g/cm3, 두께가 7.19 mm인데 30분 후의 표면온도는 42.8°C이었다. 반면, 탄화 합판의 경우 1100°C일 때 밀도가 0.34 g/cm3, 두께가 7.86 mm일 때 30분 후의 온도 44.4°C 였다. 이 결과로 볼 때 밀도와 두께가 적은데도 표면 온도는 낮아 각 원재료의 특성에 따라 탄화 후 밀도 및 두께 변화가 다양하여 다각적인 검토가 필요할 것으로 생각된다.
Legends : see table 1
한편 탄화보드의 표면온도 하강 변화를 알아보기 위하여 상승변화 측정 후 실리콘 러버히터의 전원을 끄고 히터 표면온도를 하강시키면서 3분 간격으로 30분 동안 탄화보드와 히터의 온도 하강을 측정하여 시간의 경과에 따른 탄화보드의 열유지 정도를 조사 한 결과는 Figs. 5~8과 같다. 히터의 표면온도가 60°C에서 26.0°C로 하강함에 따라 4종류의 탄화보드 의 표면온도도 시간이 경과함에 따라 완만히 하강하 였다. 각 탄화보드의 탄화온도별 처음 최고온도와 30 분 후의 온도 차이는 탄화 합판 1100°C일 때 14.2°C, 탄화MDF 900°C일 때 12.9°C, 탄화원목 1000°C일 때 14.2°C, 그리고 탄화PB는 1100°C일 때 13.4°C로 가장 크게 나타나 온도상승속도와 하강속도는 거의 일치하는 것으로 판단된다.
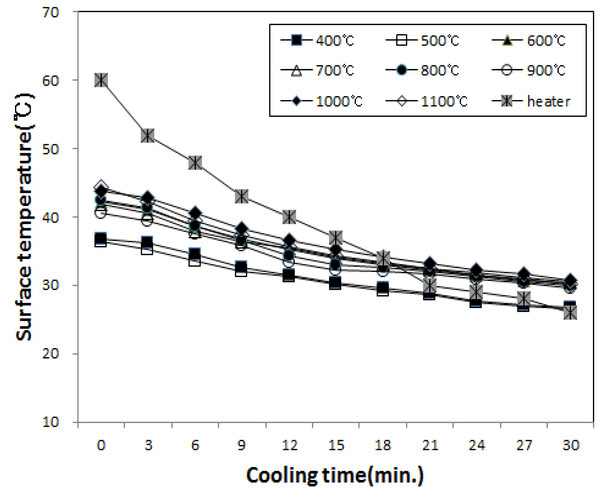
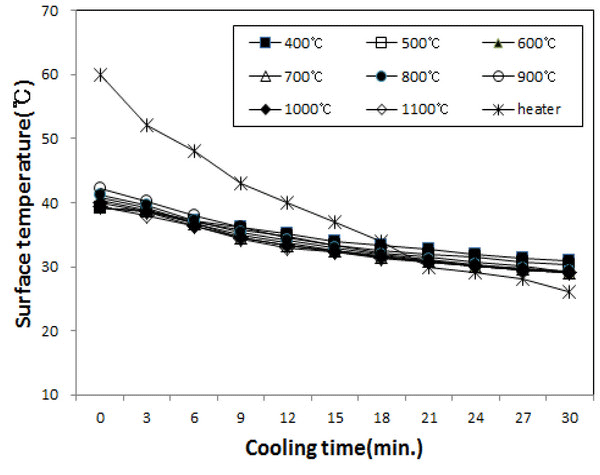
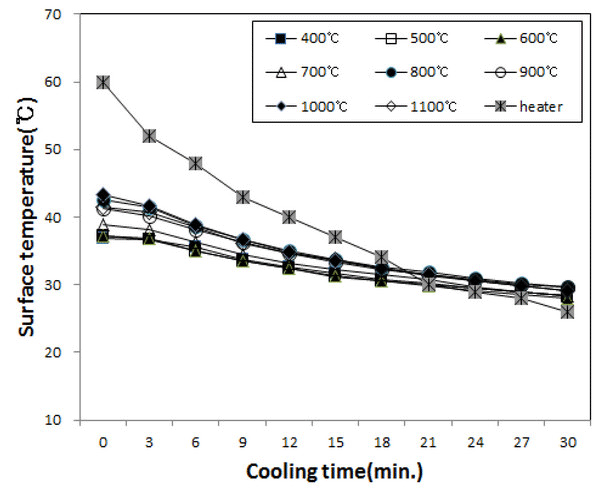
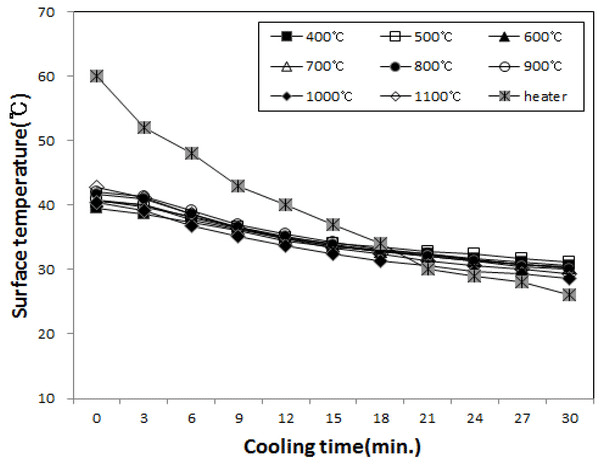
또한 하강시간 30분 후 4종류 탄화보드의 표면온 도는 탄화온도별로 탄화합판은 26.8~30.2°C, 탄화 MDF는 29.1~30.9°C, 탄화원목은 28.0~29.7°C 그 리고 탄화PB는 28.7~31.1°C로 거의 일정하였으며, 탄화온도가 낮은 시편일수록 최고온도와 30분 후의 온도 차이는 적은 것으로 나타났다.
전체적으로 실리콘 러버히터의 표면온도보다 탄화 보드의 표면온도하강 속도가 느려 탄화보드가 비교 적 오랜 시간 열을 유지하고 있음을 알 수 있었다.
탄화온도별로 제조된 탄화보드를 실온에서 실리콘 러버히터 위에 올려놓고 실리콘 러버히터의 표면온 도를 25°C에 80°C까지 상승시키면서 탄화보드의 표면 온도 상승변화를 측정한 결과는 Figs. 9~12와 같다.
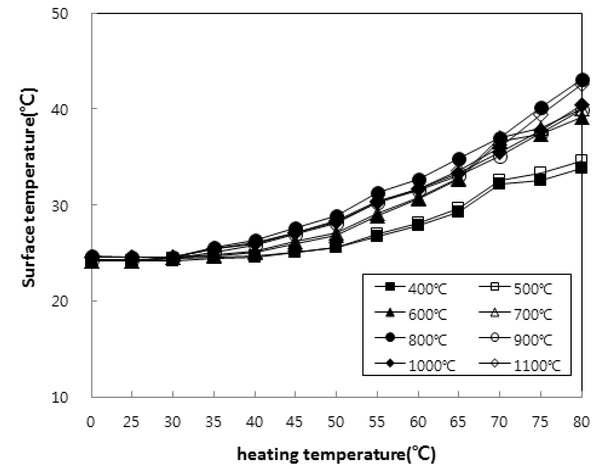
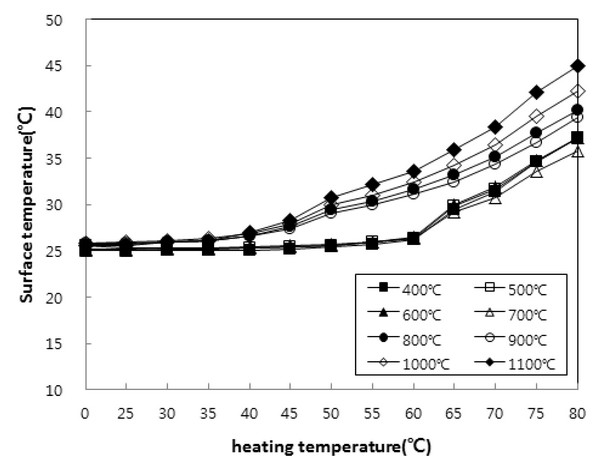
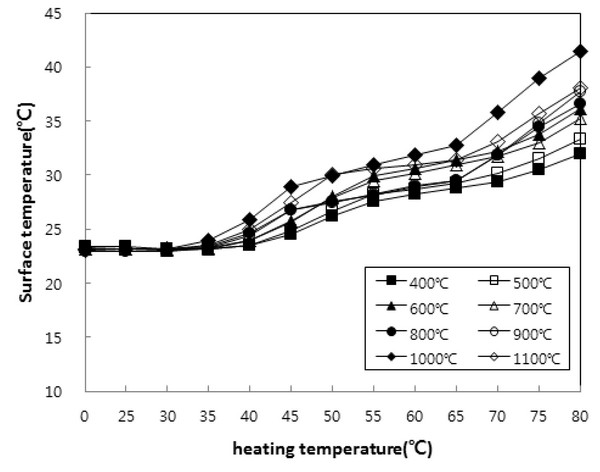
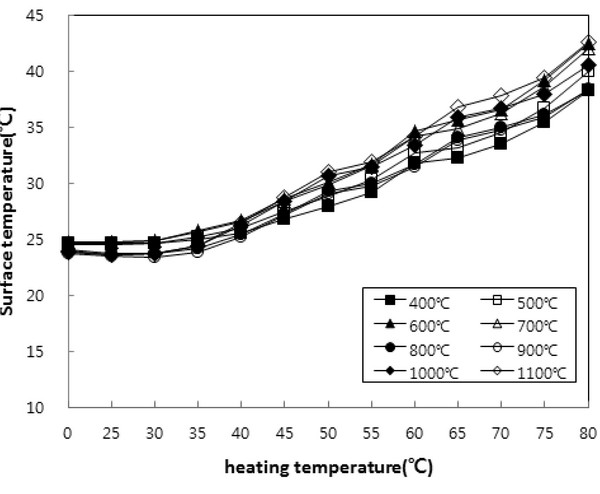
4종류 탄화보드 모두 히터 온도 50°C정도까지는 표면온도가 완만히 상승하다가 그 이후에는 급격히 상승하는 경향을 보였다.
시편의 밀도와 표면온도 상승과의 관계에서 탄화 합판의 경우 탄화온도 800°C일 때 밀도 0.34 g/cm3 인 시편의 온도가 24.7°C에서 43.1°C로 큰 상승을 한 반면, 밀도가 0.28 g/cm3로 가장 작은 400°C로 탄 화된 시편은 표면온도가 24.2°C에서 33.8°C로 상승 하여 비교적 상승폭이 적었다. 탄화 MDF의 경우 탄 화온도 1000°C일 때 밀도 0.44 g/cm3인 시편의 온도 가 25.5°C에서 45.0°C로 가장 크게 상승하였으며, 탄 화온도 400°C일 때 밀도 0.39 g/cm3 시편의 온도는 25.0°C에서 37.2°C로 가장 적게 상승하였다.
탄화PB의 경우 탄화온도 1100°C일 때 밀도 0.54 g/cm3인 시편의 온도가 23.9°C에서 42.6°C로 크게 상승하였으며, 탄화온도 900°C 이상의 시험편 표면 온도는 거의 비슷한 상승경향을 보였다. 이와 같이 실리콘 러버히터의 표면온도 상승에 따른 탄화보드 의 표면온도 상승도 밀도와 밀접한 관련이 있음을 알 수 있었다.
4. 결 론
본 연구에서는 탄화원목과 3종류의 탄화보드를 탄 화온도별로 제조하고 이를 실리콘 러버히터를 이용 하여 표면온도를 측정한 결과 다음과 같은 결론을 얻었다.
탄화온도별 탄화 보드의 표면온도는 경과시간 12분까지 급속히 상승하다 그 이후에는 완만한 상승을 보였고 20분 이후부터는 안정화되었다.
표면온도는 탄화합판의 경우 1100°C일 때 44.4°C, 탄화MDF는 900°C일 때 42.1°C, 탄화 목재는 1000°C일 때 43.4°C, 탄화PB는 1100°C일 때 42.8°C로 가장 높았다. 또한 실리콘 러버히터의 표면온도보다 탄화보드의 표면온도 하강 속도 가 느려 탄화보드가 오랜 시간 열을 유지하였다.
이상과 같은 연구결과를 토대로 탄화보드가 열을 오랜 시간동안 유지하고 있기 때문에 발열체의 재료 로 사용이 가능할 것으로 생각된다.