1. INTRODUCTION
Charcoal has long been used for agriculture and fuel in many countries (Rocha et al., 2002; Steiner et al., 2004; Yatagai et al., 1986). Today, the supply of gas, electricity and oil has reduced the production of charcoal, however, developing countries are still producing charcoal for fuel. Recently, in Korea and Japan, the value of charcoal has been re-evaluated again as a subject of interest as nature and health-friendly material. In developing countries, the use of kilns such as Degussa-retort, Lambiotte process and Calusco tunnel retort is widely used in the manufacture of charcoal (Griessacher et al., 2012). In the manufacturing process of charcoal, the constituents of wood are discharged as smoke, pyrolysis product, and liquid woody vinegary like substance is obtained as a by-product by air or water cooling. Crude wood vinegar is divided into three layers when left standing for an extended period. A thin layer of light oil on the uppermost layer, water-soluble light brown wood vinegar in the middle layer, and a black oily liquid wood tar is formed in the low layer.
Liquid vinegars of various compounds such as acetic acid and alcohol, organic acids, and phenols, which are formed by pyrolysis of wood constituents (cellulose, hemicellulose, and lignin) (Mohan et al., 2006; Mun and Ku, 2010). This wood vinegar is widely used as fertilizer. Wood tar is a substance obtained by pyrolysis of lignin (Wenzl, 1970), which is a complex mixture of aromatics and oxygenated compounds mainly composed of aromatic hydrocarbons (Amen-Chen et al., 1997; Blanco et al., 2012).
Lignin is an aromatic polymer that accounts for about 15-36% (Brebu et al., 2011; Liu et al., 2015; Saiz-Jimenez and De Leeuw, 1986) of woody biomass resources and is an amorphous material that does not have a uniform bonding unit. This ingredient is attracting attention as a renewable raw material due to the increase in market price of aromatic (petroleum) chemicals and the increase in production of shale gas in the United States (De Wild et al., 2014). Currently, Lignin is produced in a large amount in pulp mills, and research is being actively carried out to replace lignin with raw materials such as resin and plastic (Lee and Deng, 2015; Lora and Glasser, 2002; Park et al., 2008; Setua et al., 2000; Zhao et al., 2001). In addition, it is considered to be a source of potential chemical substances and has received much attention in research on pyrolysis lignin (Brebu and Vasile, 2010). Pyrolysis lignin can be used as an auxiliary in the wood-based industry since pyrolysis is an economical thermochemical process capable of converting 60-75% (by mass) of biomass into energy-dense crude oil (Jiang et al., 2010; Scholze et al., 2001). In addition, lignin can be produced as an inexpensive industrial raw material, and carbon fiber manufacturing research is being conducted as a precursor for producing low-cost carbon fiber (Jung et al., 2016). This is because carbon materials are attracting attention as an alternative to energy conservation, and the spread of carbon materials in the materials and components industries worldwide is expected to increase. Studies around the world show that coal and petroleum tar are the most promising candidates for advanced carbon material precursors. However, considering the economic and technological aspects such as lignin, it is possible to obtain many materials that can be applied from abundant and inexpensive raw materials, and to pay attention to resources that are based on the biomass of fossil resources (Prauchner et al., 2001). Therefore, it is expected that lignin-derived wood tar will be used in the future. Since these wood tar vary in the process, maturity temperature, and other factors, it is necessary to study the wood tar according to each manufacturing process (Sarohia et al., 2014).
The production of charcoal in Korea has been conducted modified traditional kiln and mechanical steel kiln. Modified traditional kiln is constructed of clay and refractory bricks. It has been modified to improve the convenience and yield of charcoal. It is widely used for the production of black and white charcoal. Black charcoal refers to charcoal produced by carbonizing wood at 350 to 400°C raising the temperature to about 700°C at the end, refining the charcoal, and cooling it sufficiently to cool the wood. White charcoal is produced by carbonizing wood at a relatively low temperature for several hours at the end of the process, raising the kiln temperature to about 1000°C at the end of the process, removing the charcoal and covering it with powder and cooling it quickly. The mechanical steel kiln produces charcoal in the temperature condition of 400-500°C by using a closed machine device. In Korea, about 90% of the kilns used for the production of charcoal modified traditional kiln. Such wood tar is a combustible liquid, which has no apparent industrial use. Then, it is burned or abandoned, which causes environmental pollutants. Therefore various have been conducted to solve the problem (Ahn and Lee, 2014; Ku and Mun, 2006; Kwon et al., 2011; Kwon et al., 2010; Mun et al., 2007).
At present, massive wastes from industrial development are polluting the global environment, and this threatens the life of mankind in the future. As the environmental and sustainability problems increase, waste disposal becomes increasingly important, and new recycling methods are being sought. Therefore, it is necessary to examine the properties of wood tar for utilization of effective resources of wood tar that remain as waste resources.
This study was conducted to compare the composition, chemical structure and thermal properties of wood tar as a byproduct in the process of making charcoal using modified traditional and mechanical steel kilns.
2. MATERIALS and METHODS
Wood tar from the modified traditional kiln was obtained from the A Company producing charcoal by oak located in Hongcheon-Gun, Gangwon Province. The structure of the improved traditional carbonized furnace was clogged with mud. Since the ceiling is where maximum heat is received from the kiln, it is a structure with a thick steel plate on it, covered with soil, and the steel plate is supported with a thick beam. The chimneys are piled up with stones and clay, making the lower part wider and narrower as it goes up, minimizing the outer air flow back into the kiln. The inside of the kiln is about 340 cm in width, 310 cm in length, and 210 cm in height. The vinegar production start when the smoke has reached 80 - 90°C, and when the temperature reach 150°C, the vinegar production has stopped. The temperature inside the kiln while obtaining vinegar solution is around 600°C and it takes about 40 hours to collect wood vinegar during the whole charcoal production period.
The mechanical steel kiln was used in the production of charcoal using oak chips at B Company in Kimhae city, Kyungnam Province. In the case of mechanical steel kiln, the wood chips are less than 10 mm in size and put into the carbonizer via a conveyor belt. The temperature of the kiln is carbonized at about 400 to 450°C with a carbonization time of 5 to 10 minutes. At this time, the gas generated by pyrolysis of the wood is liquefied through the cooling device to produce wood vinegar, and the carbonized charcoal is collected downward. At this time, the amount of carbonized wood is made into a structure in which the wood chip is continuously fed through the conveyor belt.
Component analysis for wood tar was performed using Py-GC/MS. The analytical method was analyzed by dividing the sample into heat detachment section and pyrolytic section and analyzing it at 75 - 800°C by a double shot method which obtains a chromatogram each. Py-GC/MS measurements were carried out using a Double-shot pyrolyzer (PY-2020iD, Frontier Lab. Co. Ltd.) with a 6890N GC/MS system (Agilent Tech. Ltd.). A stainless steel capillary column (30 m, 0.25 mm I.D.) coated with a 0.25 μm bonded film of DB-5 ms was used for the separation. The sample (0.5 mg) was placed in a stainless steel sample cup. The cup was placed on top of the pyrolyzer at near ambient temperature. Table 1 shows analysis condition.
The chemical behavior of the wood tar was evaluated using FT-IR (Fourier Transform Infrared Spectroscopy, Excaliber FT/IR-3000). The KBr method was used to measure the range of 800 to 4000 cm-1.
1H and 13C NMR analyses were carried out using Bruker Avance III 700 MHz to examine the chemical structure of the wood. Analytical solvents were determined using CDCl3.
MALDI-TOF (Matrix-Assisted Laser Desorption Ionization-Time of Flight Mass Spectrometry) analysis was performed to examine the molecular weight distribution of wood tar. α-Cyano- 4hydroxycinnamic Acid was used as a matrix for ionization. Samples and matrix were mixed at a ratio of 1 : 20 and coated on a MALDI-TOF plate using a dried droplet method. The plate was dried at room temperature for 12 hours and analyzed. Molecular weights of 60 - 3000 m/z were measured. The equipment used was a Bruker Daltonics Autoflex MALDI-TOF mass spectrometer.
The thermal properties of wood tar were analyzed by TGA (Thermogravimetric analysis) and DSC (Differential Scanning Calorimetry). The thermogravimetric analysis was carried out by thermogravimetry of a 7 mg sample in a nitrogen atmosphere using a thermogravimetric analyzer (Sinco, TGA N-1000) at 600°C at a heating rate of 10°C/ min. Differential scanning calorimetry was performed using a differential scanning calorimeter (Sinco, DSC N-650). The peak of the endothermic or exothermic reactions was observed during the heating of the 2 mg sample to 260°C at a rate of 5°C/ min. In a nitrogen atmosphere was analyzed.
3. RESULTS and DISCUSSION
The chromatogram of the wood tar produced from the modified traditional carbonized furnace using Py-GC/MS at 70-200°C, 300°C, and 450-800°C is given in Fig. 1. Whereas, Fig. 2 is a summary of the peaks in the GC/MS chromatogram by library searching and mass spectrum of acid, alcohol, aldehyde, ketone, furan, phenol, ester and hydrocarbons. Hydrocarbons were most abundant in the low-temperature region below 300°C and fatty acid ratio in the high temperature region above 450°C. The acid was detected at a high rate in the condition of 450-850°C. Overall, the proportion of phenolic compounds was low. The major components detected in each condition are as follows - components such as tetradecane (5.6%), nonadecane (7.2%), 2-propyn-1-ol (7.5%), eicosane (8.1%), hexadecane (10.9%) and heptacosane (7.9%) occupy a large proportion at 70-200°C. Friedelan-3-one (12.5%), heneicosane (5.7%) and tetradecane (4.6%) are the most important components at 300°C. Hexadecanoic acid (17.9%), methacrylic acid (23.1%) and 1-docosene (24.2%) were the most abundant in the high temperature region (450-800°C).
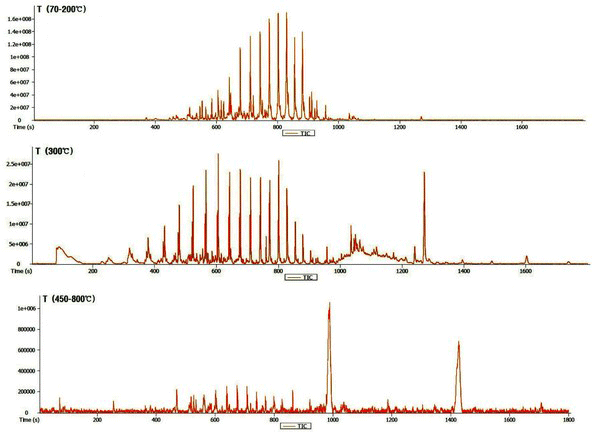
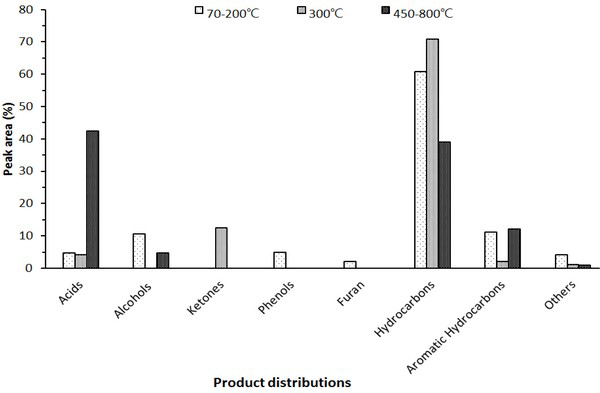
The Py-GC/MS chromatogram of the wood tar produced from the mechanical steel kiln Fig. 3, and Fig. 4 show the results of the components identified by library searching and mass spectrum of the detected peaks. Most of the wood tar produced from the mechanical steel kiln was found to contain large amounts of phenolic and aromatic hydrocarbon components. Sugar components were also detected under 500°C condition. This could probably be due to pyrolysis of the cellulose and hemicellulose constituents of the wood. At 70-100°C, components such as cresol (6.6%), 4-ethyl-2-methoxy-phenol (6.2%), 2,6-dimethoxy-phenol (25.3%), 1,2,4-trimethoxy benzene (14.8%) and 1,2,3-trimethoxy- 5-methyl (8.1) were detected. At 500°C, methyl alcohol (5.5%), 2,6-dimethoxy-phenol (7.6%), 1,2,4-trimethoxy benzene (7.5%), 1,2,3-trimethoxy- benzene (9.3%) were detected. Overall, the ratio of phenolic compounds and aromatic compounds were found to be higher in the mechanical steel kiln than in the wood tar produced in the modified traditional kiln.
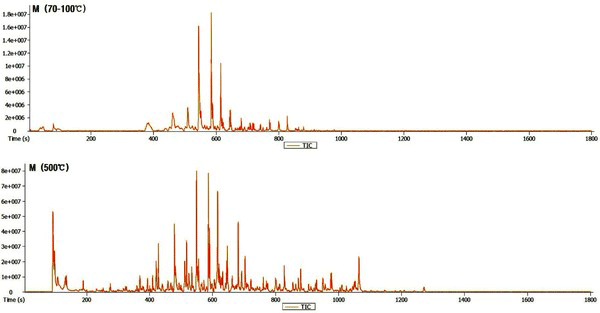
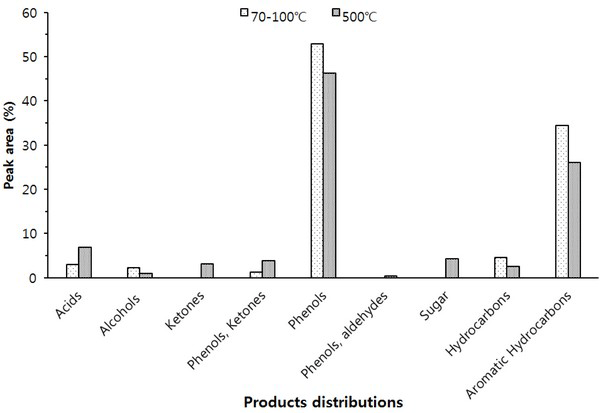
Ben and Regauskas (2011) reported that the formation of pyrolysis oil from lignin is related to pyrolysis temperature (Ben and Ragauskas, 2011), and Iatridis and Gavalas (1979) reported that hydrocarbon production increases with increasing lignin pyrolysis temperature (Iatridis and Gavalas, 1979). In addition, Alen et al. (1996) showed that lignin was converted to primary pyrolysis products such as vanillins and guaiacols at 400°C, vanillin derivatives were converted to various catechols and phenols at 600°C, and at above 800°C, thermoplastic hydrocarbons (Aromatic hydrocarbons) and other phenols were formed as major pyrolysis products (Alén et al., 1996). Therefore, it is considered that the difference in the composition of the wood tar produced in the two kilns is influenced by the carbonization temperature during the production of the charcoal. Since the carbonization temperature of the mechanical steel kiln is set at a condition of 400°C to 450°C, the temperature in the kiln can be controlled. However, since the carbonization temperature of the modified traditional kiln is manual, the temperature control is difficult and the condition in which the wood tar is produced is generated at a high temperature (600°C) compared to the mechanical steel kiln. Due to this reason, it is considered that there is a difference in the composition of the wood tar produced from the modified traditional kiln and the wood tar produced from the mechanical steel kiln.
13C NMR and 1H NMR were used to evaluate the properties of the functional groups of the wood tars produced from the modified traditional kiln and the mechanical steel kiln. The results of 13C NMR analysis of the wood tar produced in the modified traditional kiln in chloroform is shown in Fig. 5. The internal reference material peak at 0.0004 ppm, followed by 14 ppm aliphatic carbon equivalent signal, a 23 ppm, and 32 ppm aliphatic signal, and a 77 ppm chloroform solvent peak. The 1H NMR spectra of the wood tar produced from the modified traditional kiln are given Fig. 6, with the internal standard material signal at 0.0 ppm, and 7.3 ppm solvent signal. A signal corresponding to the aliphatic proton is between 0.9 to 1.3 ppm, this region represents a C=C double bond or an aliphatic proton attached to a carbon atom with at least two bonds removed from a heteroatom (O or N) [29]. A 3.6 - 3.8 ppm signal of the CH2 bridge (diphenylmethane), represents a methylene group linking a proton or two aromatic rings in the aliphatic alcohol or the carbon atom next to the ether (Mullen et al., 2009).
The results of 13C NMR analysis of the wood tar produced in the mechanical steel kiln are given in Fig. 7. A signal corresponding to aliphatic is seen at 30 ppm, and 56 ppm shows methoxyl group signal of aromatic compound. Signals for aromatic compounds appeared in the 105 to 148 ppm range. Fig. 8 shows the results of 1H NMR analysis for the wood tar produced in the mechanical steel kiln. In the wood tar of mechanical steel kiln, a signal corresponding to aliphatic proton appeared at 1.3 ppm and a signal corresponding to CH2 bridge (diphenylmethane) appeared at around 3.8 ppm. A comparison of the 13C NMR spectra of the modified traditional kiln wood tar and mechanical steel kiln wood tar shows that the aromatic compound signal was observed in the wood tar of the mechanical steel kiln. However, when comparing the 1H NMR spectra, the overall pattern was similar.
Fig. 9 shows the MALDI-TOF spectra of the matrix and standard calibration used to measure the molecular weight distribution of wood tar. The x axis represents the molecular weight of the cation by mass / charge and the y axis represents the absolute intensity. Molecular weight distribution of wood tar was analyzed except for the peaks in the matrix and standard calibration. Fig. 10 shows the molecular weight distribution of wood tar on samples using MALDI-TOF mass spectrometry. The modified traditional kiln wood tar (Fig. 10a) has a molecular weight ranging from 260 to 680 m/z. The mechanical steel kiln wood tar (Fig. 10b) shows a molecular weight distribution in the range of 255 to 880 m/z, indicating that there is a somewhat broader range of molecular weight than the wood tar produced in the modified traditional kiln.
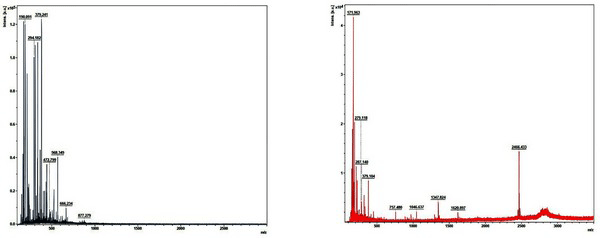
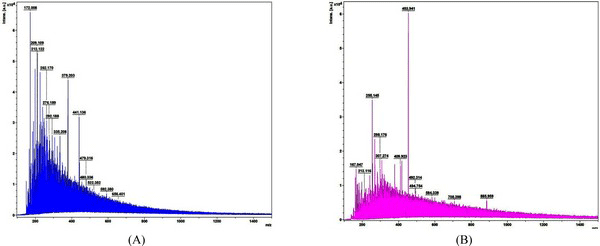
The molecular weight distribution of the wood tar analyzed by MALDI-TOF is shown in Fig. 11. Molecular weight classification of wood tar was divided into fraction 1 (1-149 m/z), fraction 2 (150-299 m/z), fraction 3 (300-449 m/z), fraction 4 (450-599 m/z), fraction 5 (600-749 m/z), and fraction 6 (750-899 m/z). The average molecular weight distribution of the wood tar (Fig. 11. T) produced in the modified traditional kiln shows the highest distribution in Fraction 2, suggesting that many compounds with molecular weights of 150-299 m/z exist. The fraction of wood (Fig. 11. M) produced in the mechanical steel kiln was the highest in fraction 3. A comparison of the average molecular weight distributions of the two wood tars indicates that the tar-oligomers present in the mechanical steel kiln are present in a higher degree of polymerization than the wood tar produced in the modified traditional kiln.
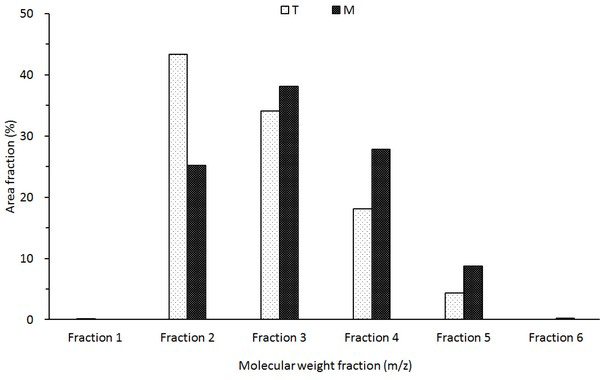
The FT-IR spectra of the wood tars produced from the modified traditional kiln and the mechanical steel kilns are shown in Fig. 12. In both wood tars, 1114 cm-1 (C-O-C stretch of aliphatic ether), 1464 cm-1 (CH bending deformations and aromatic ring vibrations), 1633 cm-1 (stretching of aromatic C=C groups), 1710 cm-1 (CH3 and CH2 groups) and 3434 cm-1 (OH group of phenolic and aliphatic structure) peaks are seen. However, the symmetrical stretching vibration of CH3 was observed at 1383 cm-1 in the wood tar produced from the modified traditional kiln. C-C and C-O stretching vibration peaks were observed at 1211 cm-1 in the wood tar produced from the mechanical steel kiln. Ben & Ragauskas (2011) suggested that formation of aromatic C-O bonds are due to radical reactions between aromatic and aliphatic hydroxyl groups, and aromatic C-C bonds are formed by cleavage of methoxyl groups and aromatic C-H bonds during pyrolysis (Ben and Ragauskas, 2011). FT-IR analysis showed that the structure of the wood tar produced by the pyrolysis of the aliphatic side of the lignin component affected the characteristics of the wood tar structure.
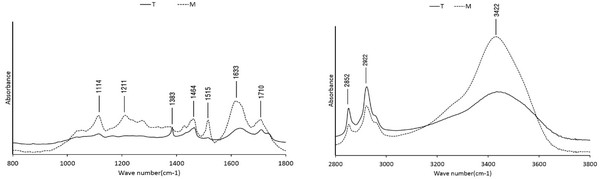
The results of thermogravimetric analysis of the modified traditional kiln and the mechanical steel kiln are shown in Fig. 13. As seen in Fig. 13 (T), pyrolysis started at 143°C and proceeded to 287°C. At this temperature range, the weight decreased to about 94%. Thereafter, pyrolysis proceeded gradually. The final yield at 600°C was about 3%. The wood tar (Fig. 13, M) produced from the mechanical steel kiln began pyrolysis at 50°C and proceeded rapidly to 300°C, with a 72% decrease in weight. Thereafter, the weight was gradually decreased, and the final yield was 17% at 600°C. The pyrolysis initiation temperature of the two samples was low in the manganese produced from the mechanical steel kiln. However, the final yield was high for the wood tar produced by the mechanical steel kiln.
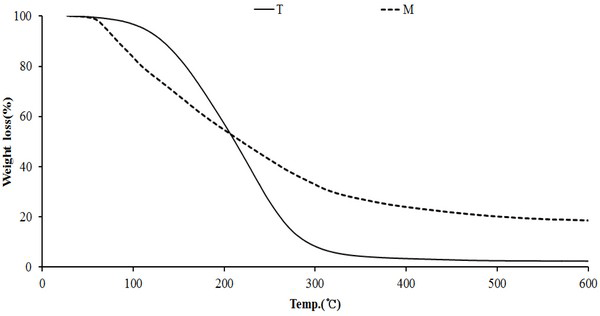
Fig. 14 DTG curve for wood tar produced from the modified traditional kiln showed a weight reduction rate in the temperature range of 80°C to 350°C. The temperature range of 220-240°C showed the highest weight loss rate. However, the wood tar produced from the mechanical steel kiln showed a weight reduction rate in the temperature range of 50-340°C. Among them, the highest weight reduction rate was seen in the temperature range of 70-110°C. These results show that volatiles in the initial stage of the mechanical steel kiln is more volatile than those in the modified traditional kiln.
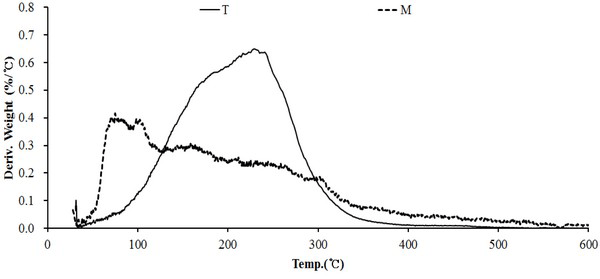
The DSC curve for wood tars produced from the modified traditional kiln and mechanical steel kiln is shown in Fig. 15. The endothermic peaks appear to be melting at temperatures below 60°C. There were no significant changes. However, the endothermic peaks generated by the melting of various components between 30°C and 81°C and between 113°C and 125°C were found in the wood tar produced from the mechanical steel kiln. Mechanical steel kiln wood tar showed higher thermal properties than modified traditional kiln wood tar. Wood tar is a substance produced by condensation or polymerization by thermochemical reaction of wood components. It is difficult to control the temperature of the modified traditional kiln when compared with the mechanical carbonization furnace and the pyrolysis compounds generated during the production of charcoal are generated by the thermochemical reaction generated by the long residence time in the carbonization furnace under the high temperature condition. Therefore, it is considered that the temperature during the production of wood vinegar greatly affects the composition of wood tar.
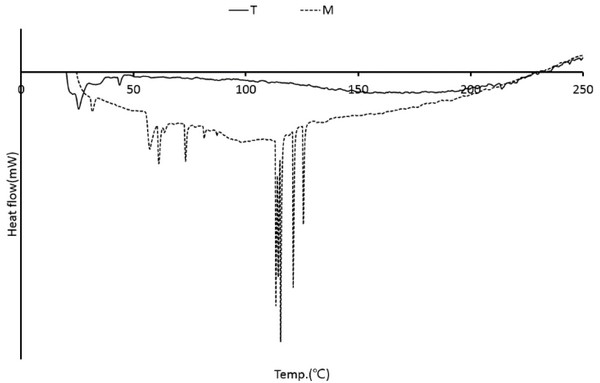
4. CONCLUSIONS
The chemical structure and thermal properties of wood tar produced as by - products in the modified traditional kiln and mechanical steel kiln were investigated. Pyrolytic GC/MS and NMR analysis showed that most of the hydrocarbons produced in the modified traditional kiln were the most abundant hydrocarbons, and the wood tar produced in the mechanical steel kiln contained many phenolic and aromatic hydrocarbons. Using MALDI-TOF, the molecular weight of the two kind of wood tars ranged from 255 to 880 m/z. It has been confirmed that the wood tar produced from the mechanical steel kiln have a higher degree of polymerization than those produced from the modified traditional kiln. The characteristic peak of the symmetrical stretching vibration of CH3 was found in the modified traditional kiln wood tar, and the C-C and C-O stretching vibration peaks of the mechanical steel kiln wood tar were characteristic. Due to this structural difference, the wood tar produced in the mechanical steel kiln showed a somewhat higher thermal stability. It was found that the properties of the wood tar significantly affected kiln temperature during wood vinegar recovery and the kiln type.