1. INTRODUCTION
With the growing interest in bio-based materials that offer excellent biocompatibility and environmental friendliness, research on natural polymer-based composite materials has garnered significant attention. Cellulose, chitosan, starch, and silk fibroin (SF) are representative natural polymers with low toxicity, minimal environmental impact, renewability, and biodegradability, making them highly suitable for various industries (Geyer et al., 2017; Park et al., 2013; Rillig, 2012; Sheavly and Register, 2007).
Cellulose is a linear polymer comprising repeating β-(1→4)-glucose units. It is abundant, cost-effective, and exhibits remarkable physicochemical properties, such as biocompatibility, water absorbency, and biodegradability, facilitating its use across diverse material industries (Feng and Chen, 2008; Fink et al., 2001; Gwak et al., 2022; Jullaprom et al., 2025; Kim et al., 2017a; Marsano et al., 2007; Mawardi et al., 2025; Seo and Kim, 2024; Setyayunita et al., 2022; Zhou et al., 2013). However, the strong intra- and intermolecular hydrogen bonding of cellulose results in a highly crystalline structure, making it insoluble in water and most organic solvents. Therefore, several solvents, including N,N-dimethylacetamide/ lithium chloride, N-methyl-morpholine-N-oxide, dimethyl sulfoxide/tetrabutylammonium fluoride, dinitrogen tetroxide/dimethylformamide, sodium hydroxide (NaOH)/urea, ionic liquids, and lithium bromide (LiBr) aqueous solutions, have been developed for cellulose dissolution systems (Feng and Chen, 2008; Gwak et al., 2024; Kim et al., 2017b; Yang et al., 2014a; Zhou et al., 2013).
Chitosan, a natural polymer obtained by deacetylating chitin derived from crustaceans, such as shrimp and crabs, or from fungi and insects, shares structural similarity with cellulose. It is non-toxic, biocompatible, biodegradable, and non-immunogenic, making it widely applicable in textiles, paper manufacturing, agriculture, and food production. Its antimicrobial properties, wound-healing capabilities, and body thermoregulation characteristics make it particularly valuable in medical applications (Abdul Khalil et al., 2016; He et al., 2011; Jang and Nah, 2008; Kuzmina et al., 2012; Ostadhossein et al., 2015; Twu et al., 2003).
Yang et al. (2018) investigated the fabrication and physicochemical properties of cellulose-chitosan composite materials. While these films are eco-friendly and biodegradable, they exhibit inherent limitations in mechanical strength and flexibility when used alone. To overcome these limitations, recent studies have actively explored strategies to incorporate various polymers to enhance material properties and introduce novel functionalities (Dungani et al., 2022; Sionkowska, 2011; Zhou et al., 2013).
Silk proteins produced by silkworms and spiders primarily comprise fibroin and sericin, with fibroin serving as the main structural protein. Fibroin is hydrophobic and exhibits outstanding mechanical strength, oxygen and moisture barrier properties, biocompatibility, and biodegradability. Thus, it is suitable for various applications, including food packaging, cosmetics, enzyme immobilization supports, cell culture scaffolds, and biomedical materials (Bhardwaj and Kundu, 2011; Cho et al., 2014; Kim et al., 2017a; Noishiki et al., 2002). In particular, SF forms a unique molecular structure incorporating β-sheet arrangements, which contributes to its exceptional mechanical strength and flexibility. Moreover, its excellent compatibility with other functional materials enables its broad application in the development of high-performance bio-based materials.
In this study, we investigated the structural and physical properties of a cellulose-chitosan composite matrix reinforced with SF. We systematically analyzed changes in microstructure, mechanical strength, elongation, and moisture resistance with varying SF content. Additionally, we investigated the interaction mechanisms between the components to optimize the composite material.
2. MATERIALS and METHODS
Alpha-cellulose (Sigma-Aldrich, St. Louis, MO, USA) and chitosan (MW 190–310 kDa, deacetylation degree greater than 75%; Sigma-Aldrich) were used as the primary materials in this study. SF obtained from silkworm cocoons (Bombyx mori) was provided by Chunzam Bio (Seoul, Korea). Sodium carbonate (Na2CO3; Daejung Chemicals & Metals, Siheung, Korea) was used for silk degumming. LiBr from Samchun Pure Chemical (Pyeongtaek, Korea) was used as the solvent for polymer dissolution.
SF was prepared by degumming silkworm cocoons in a 0.5 wt% Na2CO3 aqueous solution at 90 ± 1°C for 4 h. Degummed silk was rinsed five times with distilled water and subsequently dried in an oven at 60 ± 1°C for 24 h (Kim et al., 2017a; Shang et al., 2011; Zhou et al., 2013).
A 60 wt% LiBr solution was prepared as the solvent. To prepare the cellulose-chitosan composite solution, 1 g of cellulose and chitosan (at an 8:2 mass ratio) was dissolved in 89 g of 60% LiBr solution and stirred at 145 ± 1°C for 5 min. Subsequently, an SF solution was added to the mixture and stirred for 2 min to ensure homogeneous blending.
The SF solution was prepared by dissolving solid SF in 10 g of LiBr solution, adjusting the SF content to 0, 30, 60, or 90 wt% based on 1 g of the cellulose-chitosan mixture. To completely dissolve SF, the solution was heated in a drying oven at 70 ± 1°C for 4 h before use.
The resulting homogeneous solutions were cast onto preheated glass plates at 90°C and subsequently cooled to room temperature for regeneration. The regenerated gels were washed under running water for 1 day, pressed for 30 min to remove excess water, and dried in an oven at 105 ± 1°C for 24 h to obtain the cellulose-chitosan-silk fibroin (CCF) composite films (Fig. 1).
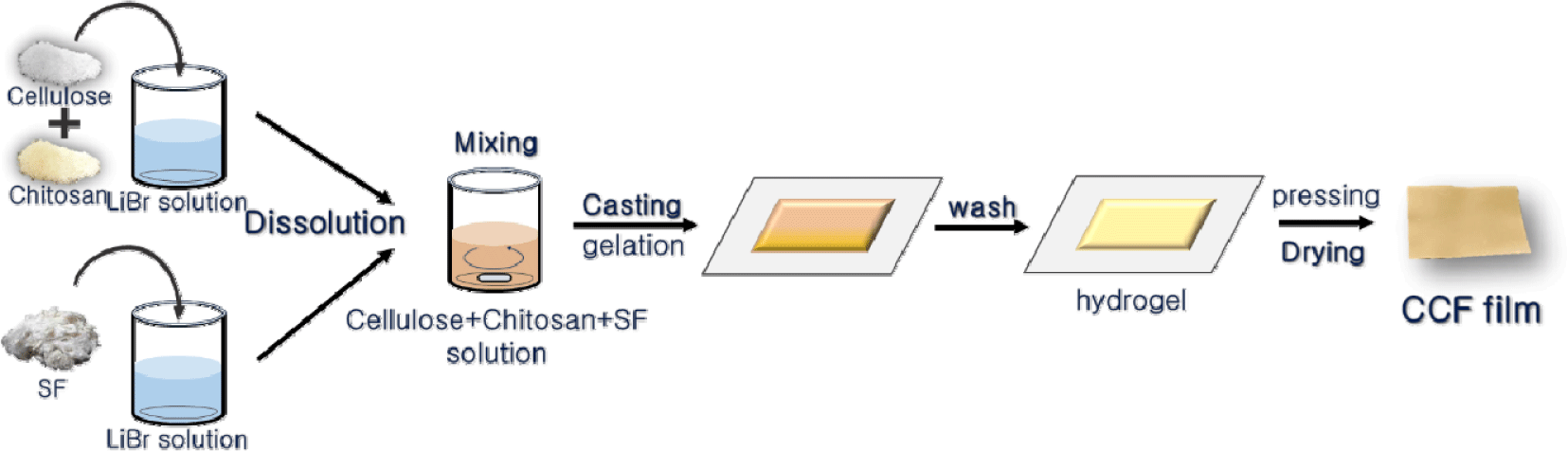
The films were named CCF0, CCF3, CCF6, and CCF9 according to their SF content ratios.
The cross-sectional structures of the CCF composite films were observed using scanning electron microscopy (SEM; EM-30 MiniSEM, COXEM, Daejeon, Korea). The samples were cryo-fractured using liquid nitrogen to observe the cut sides. The X-ray diffraction (XRD) patterns of the CCF films were obtained using an X'Pert PRO MPD X-ray diffractometer (PANalytical, EA Almelo, The Netherlands). Fourier-transform infrared (FT-IR) spectra of the films were obtained using a Vertex70 spectrometer (Bruker Optics, Ettlingen, Germany) equipped with an attenuated total reflection accessory. A universal testing machine (TO-102D, Test One, Siheung, Korea) was used to determine the mechanical properties of the films, including tensile strength, elongation at break, and elastic modulus. Film samples (15 × 60 mm) were tested, and the average of three measurements was reported. The mechanical behavior of the films was examined under both dry and wet conditions. In the wet state, the film was soaked in water for 30 min, followed by the removal of excess water and storage in a polypropylene bag. The swelling properties of the CCF films in water and physiological fluids were analyzed. The film was cut into a size of 10(W) × 30(L) mm and used, and the prepared samples were impregnated with water and physiological solution at 37 ± 1°C for 12 h; subsequently, the weight was measured. For the physiological fluids, sodium chloride (NaCl; 9 g NaCl dissolved in 1,000 mL distilled water) and urea (25 g urea in 500 mL distilled water) solutions were prepared and used.
3. RESULTS and DISCUSSION
Fig. 2 shows photographs of the CCF composite films prepared with varying SF ratios in a 60% LiBr solution.
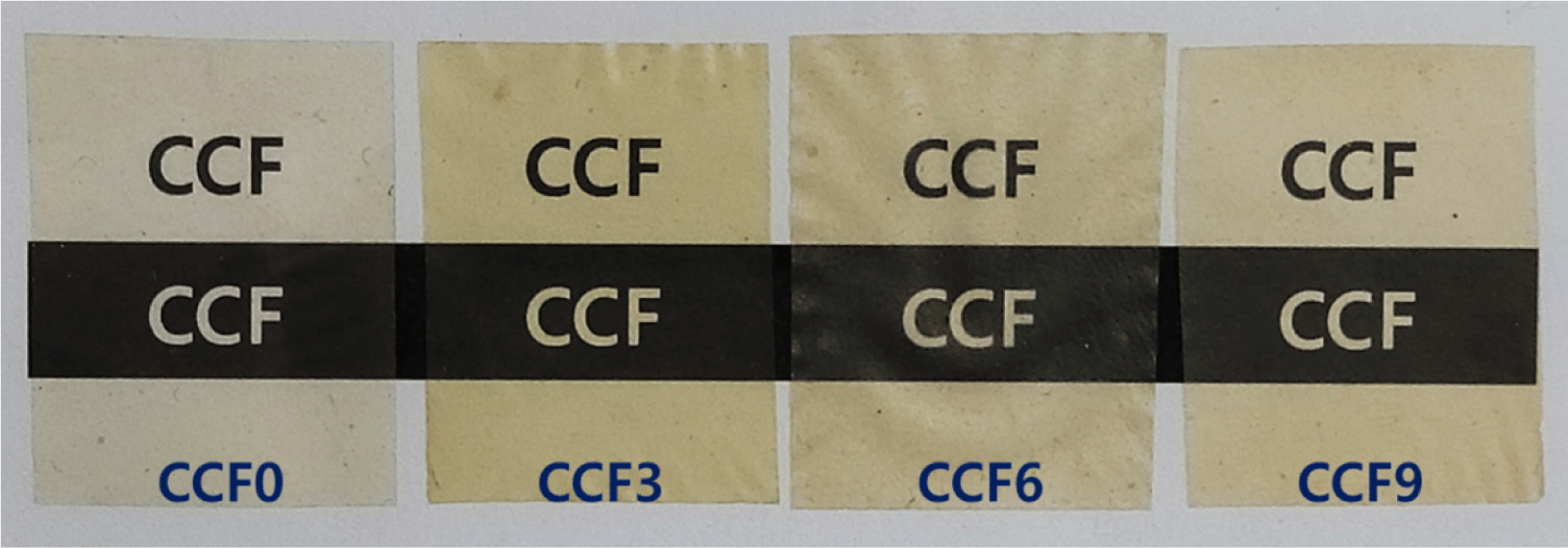
All CCF films exhibited high transparency, and the text beneath them was clearly visible. CCF0, which lacked SF, exhibited a light yellowish-beige color owing to the presence of chitosan. In a previous study (Yang et al., 2018), films solely comprising cellulose were transparent, whereas the addition of chitosan resulted in a darker coloration. The same result was observed for CCF0. In contrast, the color of CCF3, CCF6, and CCF9 progressively darkened with increasing SF content. Pure SF exhibits a pale-yellow color owing to the presence of β-sheet structures and amino acids such as tyrosine, phenylalanine, and tryptophan within the fibroin molecular chains (Perotto et al., 2017; Santos et al., 2019; Yasunaga et al., 2023). Therefore, the proportion of β-sheet structures and amino acids increases with increasing SF content in the CCF films, resulting in a darker color. Additionally, changes in intermolecular hydrogen bonding and structural density may contribute to variations in color.
Fig. 3 shows the cross-sectional images of the CCF films obtained using SEM. The cross-sections of all CCF films displayed a similar structure with a slightly rough texture, showing no significant changes with increasing SF content.

Fig. 4 shows the XRD results for CCF films with varying SF contents. In a previous study (Yang et al., 2020), which employed the same film fabrication method as in this study, the XRD patterns of cellulose films exhibited peaks at 2θ = 20.2° and 22.8°, indicating that the crystalline structure of α-cellulose, used as a raw material, transformed from cellulose I to II throughout the dissolution and regeneration processes in the LiBr aqueous solution. In the XRD pattern of α-cellulose, peaks attributed to the crystalline structure of cellulose I were observed at 2θ = 14.8°, 16.4°, 22.4°, and 34.6°. However, in CCF0, these peaks shifted to 2θ = 20.4° and 22.8°, indicating that the crystalline structure underwent a transformation from cellulose I to II during dissolution and regeneration (Cheng et al., 2012; Lee et al., 2022; Oh et al., 2005; Yang et al., 2014b; Zhou et al., 2013).
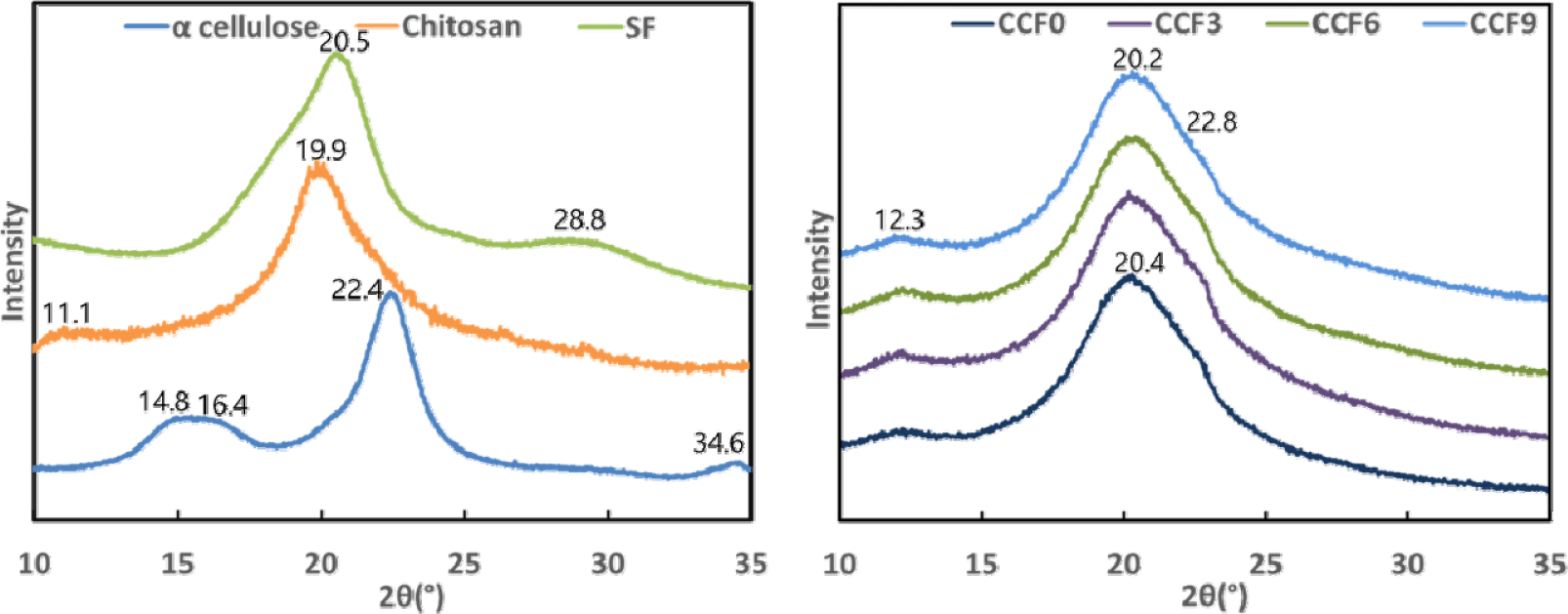
Additionally, as chitosan in CCF0 was also dissolved and regenerated, the peaks of α-chitosan at 2θ = 11.1° and 19.9° disappeared (Li et al., 2001). The regenerated cellulose peak at 2θ = 20.2° overlapped with the regenerated chitosan peak at 20.2°, slightly shifting it to 20.4°. This suggests that, during dissolution in the LiBr aqueous solution, chitosan macromolecules lost their crystalline structure and existed in a random coil state. Intermolecular hydrogen bonding occurred between the dissolved cellulose and chitosan chains, leading to molecular rearrangement and the formation of a new crystalline structure in the film. Furthermore, a diffraction peak at 2θ = 12.3°, attributed to the crystalline regions of chitosan, was observed in CCF0 and all other CCF films (Antonino et al., 2017; Fu et al., 2017; Kim et al., 2017b; Lu et al., 2004; Ma et al., 2015; Weng et al., 2017).
In the XRD pattern of SF, the characteristic peak of silk I was observed at 2θ = 28.8°, whereas that corresponding to silk II appeared at 2θ = 20.5°, indicating the presence of the typical crystalline structure of natural SF fibers. However, in CCF3, CCF6, and CCF9, no peaks corresponding to the crystalline structure of silk II were observed, suggesting that the incorporation of SF did not induce sufficient β-sheet formation to significantly affect the crystalline structure. This suggests that, during dissolution in the LiBr aqueous solution, the crystalline structure of silk I in SF was disrupted, forming a random coil conformation. Subsequently, during the regeneration process, SF did not develop a well-defined β-sheet structure, as it was immobilized in a gel-like form with the highly concentrated cellulose and chitosan.
With the addition of SF, the peak shifted slightly from 2θ = 20.4° to 20.2°, and the peak intensity increased. This indicates that the random coil structure of SF induces changes in physical interactions, such as hydrogen bonding and polymer entanglement, which affect the overall crystalline structure of the film. This suggests that the dissolved cellulose, chitosan, and SF were thoroughly and uniformly mixed during the dissolution process (Cao and Wang, 2009; Chen et al., 2012; Cheng et al., 2012; Guang et al., 2015; Kim et al., 2017a; Li et al., 2001; Marsano et al., 2008; Moraes et al., 2010; Wang et al., 2019; Yang et al., 2014b; Zhang et al., 2013).
Fig. 5 shows the FTIR spectra of the CCF composite films. All CCF films exhibited characteristic peaks associated with amorphous cellulose at 1,365 (C–H bending), 1,155 (C–O–C stretching), 1,022 (C–O vibration), and 898 cm–1 (β-glycosidic linkages; Hoang et al., 2021; Oliveira Barud et al., 2015; Park et al., 2022; Suryanto et al., 2024; Zhang et al., 2018). Chitosan exhibited similar peaks owing to its polysaccharide structure, leading to peak overlap with cellulose (Anicuta et al., 2010; Moraes et al., 2010; Yang et al., 2020). In a previous study (Yang et al., 2018), the FT-IR spectrum of a pure cellulose film exhibited a peak at 3,369 cm–1 corresponding to the OH group. However, upon chitosan incorporation, this peak shifted to 3,357 cm–1 in CCF0. Additionally, the presence of chitosan introduced a weak peak at 1,591 cm–1, attributed to NH bending of amide II. This shift and peak emergence are attributed to hydrogen bonding interactions between cellulose (-OH groups) and chitosan (-OH and -NH2 groups) during the mixing and regeneration processes (Anicuta et al., 2010; de Souza Costa-Júnior et al., 2009; Lin et al., 2012; Nawawi et al., 2023; Negrea et al., 2015; Weng et al., 2017).
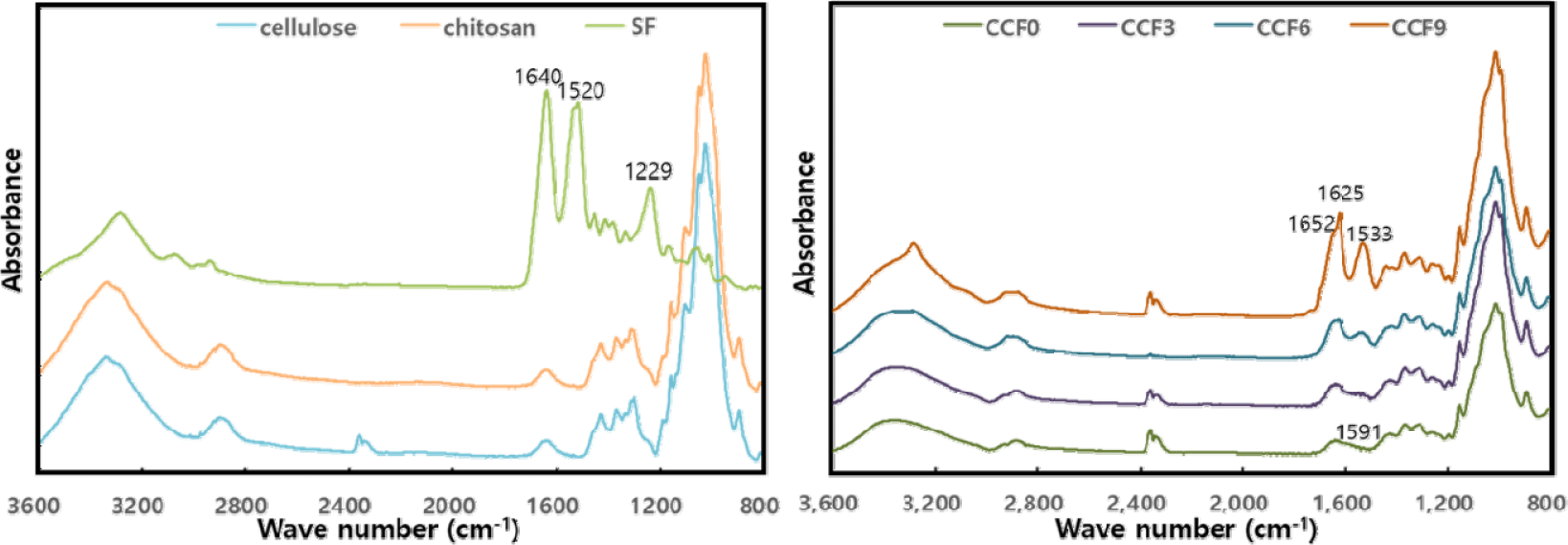
In the CCF film, as SF was mixed, the peak at 1,533 cm–1 due to NH bending of amide II of SF and those corresponding to C = O stretching of amide I appeared at 1,625 and 1,652 cm–1, respectively. Additionally, the intensity of these peaks tended to increase with increasing SF content in the films. In particular, the peak at 1,625 cm–1 is a characteristic peak derived from β-sheet structures (silk II), indicating that some β-sheet crystal structures formed in the CCF film as SF ratio increased, resulting in a composite structure mixed with crystal structures of silk I and II. The β-sheet crystal structure of SF was not identified in the XRD results. However, although the β-sheet structure was not sufficiently formed to affect the crystal structure, some crystal structure of silk II developed inside the film with increasing SF content.
In the region of 3,600–3,000 cm–1, with increasing SF content, the peak at 3,357 cm–1 in CCF0 slightly shifted, and its intensity increased. These hydrogen bonding interactions occur between the carbonyl (C = O) and NH groups of SF and hydroxyl (OH) and amine (NH2) groups in cellulose and chitosan. These interactions suggested that molecular-level hydrogen bonding occurred during dissolution and regeneration. Furthermore, in CCF9, which contained the highest SF content, an additional peak appeared at 3,280 cm–1, corresponding to regenerated SF-NH groups (Anicuta et al., 2010; Chen et al., 2012; Fu et al., 2017; Guang et al., 2015; Moraes et al., 2010).
Table 1 presents the thicknesses of the CCF composite films in the dry and wet states. In the dry state, the film thickness did not vary significantly with the addition of SF. However, in the wet state, the difference in thickness between the dry and wet films increased with increasing SF content. This phenomenon is attributed to the increase in the number of hydrophilic groups of SF, which leads to enhanced water absorption and swelling.
Film state | CCF0 | CCF 3 | CCF 6 | CCF 9 |
---|---|---|---|---|
Dry | 43.1 ± 3.3 | 45.5 ± 4.3 | 45.5 ± 4.3 | 43.2 ± 0.9 |
Wet | 59.8 ± 2.3 | 66.5 ± 4.2 | 66.4 ± 2.4 | 66.5 ± 1.9 |
The mechanical properties of the CCF composite films, including the tensile strength, elongation, and elastic modulus, were evaluated in the dry and wet states based on the SF mixing ratio. Fig. 6 shows the mechanical properties of CCF films in the dry state. The tensile strengths of CCF0, CCF3, CCF6, and CCF9 were 84.86, 88.47, 101.18, and 102.57 MPa, respectively, indicating a gradual increase with increasing SF content. The elongation values of the CCF films were 2.40%, 3.15%, 3.64%, and 3.12%, while the elastic moduli were 3.48, 3.77, 3.28, and 3.04 GPa, respectively, indicating that these values increased and subsequently decreased with increasing SF content.
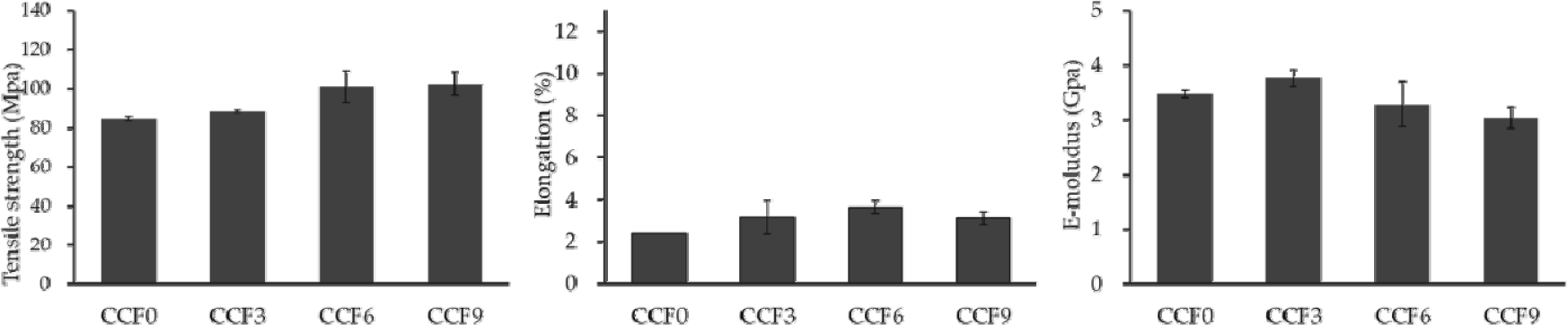
With the addition of SF, intermolecular interactions, such as hydrogen bonding between cellulose, chitosan, and SF polymers, occur, improving the mechanical properties of the dried CCF film (Zhang et al., 2014). Additionally, the physical entanglement of the polymer chains contributed to this enhancement. The crystalline regions of polymers efficiently absorb energy and withstand deformation, whereas the amorphous regions cause the polymer chains to intertwine more closely, thereby strengthening the film (Dorishetty et al., 2020; Liu et al., 2016; Zhang et al., 2014).
However, excessive SF content can lead to intramolecular rather than intermolecular hydrogen bonding, causing phase separation and reducing the uniformity of the polymer matrix. Consequently, the cohesive force between the polymer matrix and filler weakens, leading to a decrease in mechanical strength (Fu et al., 2017; Shang et al., 2011; Shih et al., 2009; Xu et al., 2005; Yao et al., 2015).
Fig. 7 shows the mechanical properties of the CCF composite films in the wet state. The tensile strength of the wet films decreased significantly compared with that of the dry films owing to the plasticizing effect of the absorbed water, which disrupted intermolecular interactions within the polymer matrix (Wu et al., 2014).
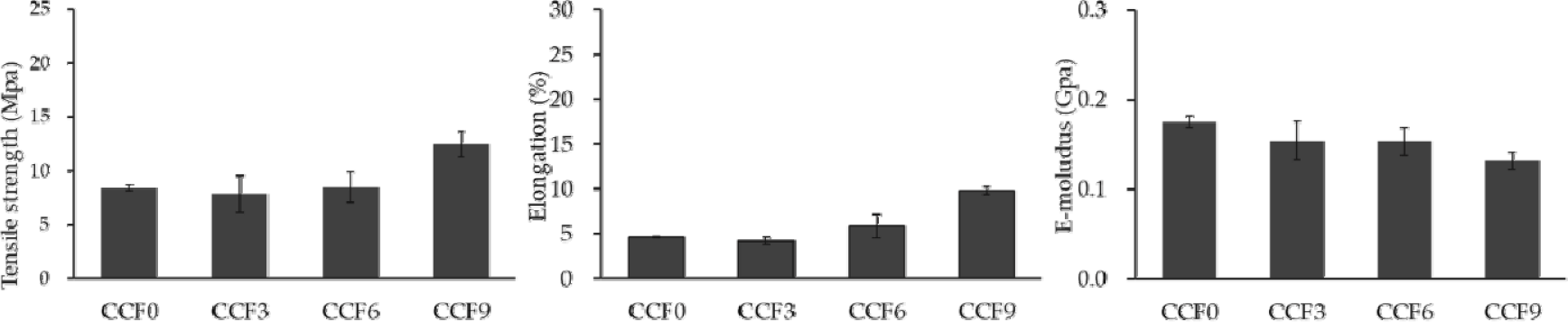
The tensile strengths of CCF0, CCF3, CCF6, and CCF9 in the wet state were 8.40, 7.84, 8.45, and 12.48 MPa, respectively. While the tensile strength remained relatively stable regardless of the SF content, it exhibited a significant increase in CCF9. The elongations at break for the wet films were 4.66%, 4.22%, 5.85%, and 9.81%, indicating an increasing trend with increasing SF content. The elastic moduli increased with increasing SF content, with values of 0.17, 0.15, 0.15, and 0.13 GPa, respectively.
Water molecules absorbed by the film interfere with the interaction between the polymers, thereby weakening the binding force. Nevertheless, the tensile strength increases in the wet state with increasing SF content as the bonding strength between the polymers improves with increasing number of hydrogen bonds. Additionally, the partial formation of β-sheet structures in SF contributes to improved crystallinity, which enhances the mechanical strength of the film. This is because the main random coil structure of SF promotes physical entanglement between cellulose and chitosan, which are linear polymers, thereby improving the network stability. Finally, this increased physical entanglement likely improves elongation by inhibiting the loosening of the polymer chain, thereby increasing the resistance to shear force (Adel et al., 2014; Plaza et al., 2008). In particular, the greater elasticity of SF in the wet state than in the dry state influenced the strength characteristics of the wet CCF film. Additionally, insufficient development of the silk II structure in SF likely affects the mechanical strength of the composite film in a wet environment (Aytemiz et al., 2018; Plaza et al., 2008).
Fig. 8 shows the swelling properties of the CCF composite films in water and physiological fluids. With increasing SF content, the water absorption rate of the CCF films increased slightly or showed similar results. This is because with increasing SF content in the film, the hydrogen bond between the polymers is strengthened owing to the increase in the hydroxyl, amide, and carboxyl functional groups of the fibroins, and the network density increases with increasing physical entanglement. Consequently, water cannot easily penetrate into the film; however, simultaneously, the water absorption capacity of fibroins is partially supplemented by the hydrophilic functional groups. Consequently, despite the increase in the SF content, the overall water absorption rate remained relatively stable or only slightly increased.
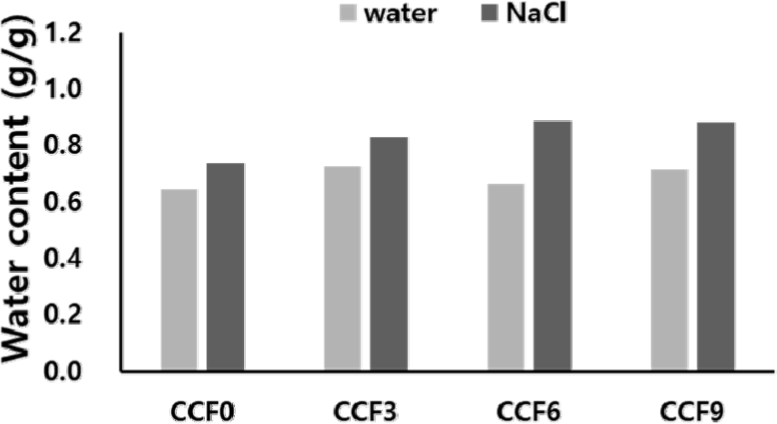
In contrast, the absorption rate of the CCF film in the NaCl solution was higher than that in water, and the rate of increase in absorption also exhibited a greater trend with increasing SF content. This can be attributed to electrostatic interactions between Na+ and Cl– ions and the amino acids present in fibroin, which facilitated the diffusion of ions and water into the film matrix. With increasing SF content, the electrostatic interactions within the polymer network increased, enabling the diffusion of more ions and water into the film.
4. CONCLUSIONS
In this study, CCF composite films were fabricated using a 60% LiBr solution, and their physicochemical properties were investigated. All CCF films exhibited a light yellowish-white color with high transparency, and the film color darkened with increasing SF content in the CCF film. No distinct differences were observed in the cross-sectional structures. During the dissolution and regeneration processes, cellulose I was transformed into a cellulose II crystal structure, and the presence of chitosan and SF influenced the crystalline structure of the films. The high concentrations of cellulose and chitosan hindered the formation of a well-defined β-sheet structure in SF, resulting in a composite structure with mixed silk I and II conformations. Intermolecular hydrogen bonds were formed among the three polymers.
Considering the mechanical properties of the CCF films, the tensile strength and elongation at break increased with increasing SF content in the dry state. However, excessive SF incorporation decreased the e-modulus. In the wet state, both the tensile strength and elongation increased with increasing SF content, and the tensile strength of the CCF9 sample was the highest. This is ascribed to the enhancement of hydrogen bonds, partial formation of β-sheet structures in SF, and physical entanglement between polymers. The swelling properties of the CCF films in water and physiological fluids showed a general increase in swelling ratio with increasing SF content. In particular, the swelling ratio continued to increase more prominently in physiological fluids as the interaction between water molecules and ions increased with increasing hydrophilic functional groups of SF.
Therefore, the β-sheet structure in the film was partially formed when the content ratio of SF was 60% or more, and the swelling rate and film strength increased owing to the strengthening of hydrogen bonds. This indicates the potential applicability of CCF films in various industries, such as cosmetics, food packaging, and biomaterials. These films can potential be used in wound dressings, tissue engineering scaffolds, and drug delivery systems for biomedical applications.