1. INTRODUCTION
Fuel is required to produce energy and its supply is a major problem (Cahyani et al., 2023). The development and use of renewable energy are crucial for all countries, as rising sea levels due to global warming and environmental issues such as increased pollution are global issues. Consequently, research into renewable energy as a replacement for fossil fuels has been conducted worldwide (Heo and Choi, 2018). Fossil fuels, such as petroleum, coal, and natural gas, are natural resources composed of hydrocarbons. They are classified as nonrenewable resources because their formation involves the deposition and decomposition of organic matter over millions of years. Owing to their prolonged formation processes and growing consumption, fossil fuel reserves are rapidly depleting. Additionally, the use of fossil fuels has significant drawbacks, including the emission of harmful and carcinogenic gases such as carbon dioxide (CO2), carbon monoxide (CO), HC, nitrogen oxide (NOx), and SOx. CO and NOx generated during boiler combustion can lead to death in cases of acute poisoning (Kang et al., 2018). CO2 is a major contributor to greenhouse gas (GHG) emissions, intensifying global warming (Institute for Essential Service Reform [IESR], 2020). The declining availability of fossil fuels has become a critical issue. Fossil fuels are non-renewable energy sources (Suhasman et al., 2024). Consumption increases annually as the world’s population increases (Budiawan et al., 2014). Several bioenergy products derived from renewable energy (biomass), such as wood pellets, charcoal, briquettes, and biodiesel, have been used to minimize air pollution (Cahyani et al., 2023; Jeoung et al., 2020; Ju et al., 2020; Kang et al., 2018; Magnone et al., 2019; Pari et al., 2023; Yang and Han, 2018).
Using biomass as a fuel is advantageous in reducing atmospheric CO2. This is because biomass is carbon neutral when burned; therefore, it is more easily absorbed by plants (Jang, 2022; Mustamu et al., 2018). Several studies have reported that wood-based fuels are superior in terms of reducing the production of air pollutants during combustion and calculating the average annual GHG emissions per tree species and charcoal product. Furthermore, the use of biomass can minimize the environmental impact of energy production by replacing fossil fuels, thereby reducing GHG emissions, carbon sequestration, climate change mitigation, waste management, and energy production (Heo and Choi, 2018; Wu et al., 2018).
According to the IESR, to achieve zero emissions by 2050, the net-zero emissions target for 2050, transportation-related GHG emissions must be cut by 3 million tons of CO2 annually until 2030 and by 7 million tons of CO2 annually from 2030 to 2050 (IESR, 2020). Achieving this reduction requires a strategic framework encompassing avoidance, transition, and enhancement. Avoidance focuses on minimizing travel distances, transition emphasizes shifting to cleaner energy sources, such as biofuels and electricity, and enhancement involves improving vehicle energy efficiency. With the growing environmental concerns, renewable energy sources such as biodiesel are promising solutions for the future.
Biodiesel is produced through a chemical reaction between fats, oils, and alcohol, facilitated by a catalyst. As a renewable energy source, biodiesel offers several technical benefits over fossil fuels, including reduced exhaust emissions and toxicity, biodegradability, production from feedstocks and household waste, a higher flash point, and environmental friendliness. These advantages have encouraged many countries, including Indonesia, to develop biodiesel as an alternative fuel. Biomass, especially plant biomass, is a potential renewable energy source (Sutapa et al., 2024). Indonesia is a tropical nation with extensive plantations and agriculture, making biomass a potential energy resource estimated at 32.77GW for power generation (Primadita et al., 2020).
Renewable energy resources are abundant in Southeast Asia. Indonesia has the largest part of the global palm oil industry worldwide (Heo and Choi, 2018). Indonesia’s biodiesel production reached 9.68 million kiloliters as of October 2022 (IESR, 2022). With this production capacity, Indonesia is projected to increase biodiesel blending from B30 (30% biodiesel) to B40 (40% biodiesel) in transportation fuels by 2023. Furthermore, Indonesia devised a plan for a Renewable Fuel Standard of B30 in 2025 (Heo and Choi, 2018). However, the program faces significant challenges, including high production costs and limited funding for incentives and subsidies. To promote the use of clean fuels, the government must establish regulations for mandatory biofuel targets, ensure product quality standards, and implement effective incentive programs. In addition, securing high-quality raw materials is essential for supporting large-scale production.
Indonesia, with its vast natural landscape, diverse distributions of air and sunlight, abundant energy, and rich plant resources, is an essential foundation for the development of biodiesel. The country relies heavily on crude palm oil as its primary raw material for biodiesel production. However, non-edible plants also offer significant potential, such as Kepuh (Sterculia foetida), a versatile plant suitable for biodiesel production. Kepuh is a resilient wild plant found in tropical and subtropical regions between 30°N and 35°S. In Indonesia, it grows predominantly on Java Island, especially in West Java, East Java, and Madura, including areas below 500 m above sea level (Heyne, 1987), though some sources indicate that it thrives at altitudes between 0 and 1,000 m (Herdiana, 2005).
A single Kepuh tree can yield approximately 200–300 kg of seeds annually (Silitonga et al., 2013). These seeds are rich in oil, with a kernel containing approximately 50%–60% light-yellow fatty oil (Devan and Mahalakshmi, 2009) and an overall oil content of approximately 40% (Heyne, 1987). This high oil yield of Kepuh seeds makes them a promising alternative for biodiesel development.
Research on Kepuh (S. foetida) as a biodiesel source has primarily focused on oil extraction, biodiesel production techniques, and the impact of reaction conditions and catalyst type on biodiesel quality (Kavitha and Murugavelh, 2019; Ong et al., 2013; Silitonga et al., 2013). However, studies comparing germplasm sources to optimize biodiesel yield, quality, and stability, as well as to identify suitable growing locations for large-scale production, remain limited.
This study investigated the production of Kepuh biodiesel in various locations across Java Island. This study aimed to evaluate site-specific variations in biodiesel yield, characteristics, and chemical composition and to select superior seed sources for developing renewable energy, supporting Indonesia's efforts to advance sustainable biodiesel production.
2. MATERIALS and METHODS
S. foetida seeds were collected from 25 sites on Java Island between July and October 2023 (Fig. 1). Representative samples consisting of 1–2 kg of mature seeds were collected in bags, separated from the husk by soaking in water, and manually peeled. Seeds in good condition and not rotten were separated and dried under the sun for 1–2 days before oil extraction in the laboratory.
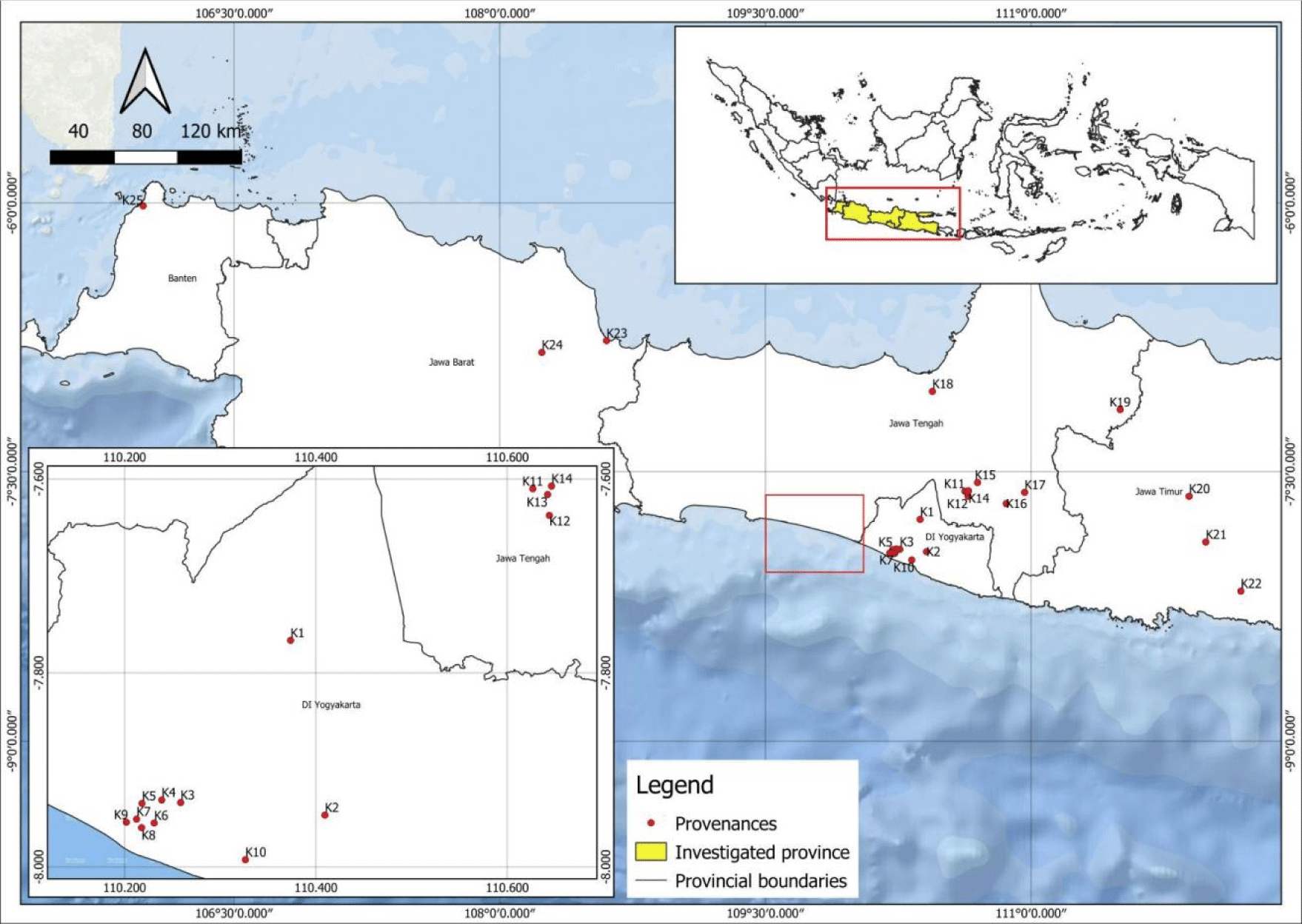
Sterculia seed oil was extracted via mechanical pressing using a screw-type crusher (expeller). This study emphasized mechanical pressing, as this simple technology is the most suitable for development at the community level because of its simplicity and ease of application in forest-adjacent communities. Before extraction, the seeds were pretreated by steaming at 100°C for 30 min to maximize the oil yield. The crude oil obtained from this process was allowed to settle for 24 h, resulting in two layers: an upper oil layer and a lower layer of gum or residue. The upper oil layer was used for biodiesel production via transesterification. In the transesterification process, the oil was mixed with methanol at a 12:1 ratio, with 1% KOH (by oil weight) as a catalyst. The mixture was stirred at 1,200 rpm and heated to 60°C for 1.5 h. The resulting mixture was then transferred to a separating funnel and allowed to stand for 15 min to separate the S. foetida methyl ester (SFME) in the top layer from the methanol and glycerol residues at the bottom. SFME was further processed using a rotary evaporator at 65°C for 20 min to remove the residual methanol. The biodiesel was washed twice with distilled water in a separating funnel, dried with 100 g of anhydrous CaCl2 for 1 d, and filtered. Subsequently, the oil was dried using 100 g of anhydrous Na2SO4 for 2 h before filtration (Silitonga et al., 2013). The biodiesel yield (wt%) was calculated using the following formula:
Where Af is the weight of the biodiesel product (g) from the esterification-transesterification process and Ao is the weight of the seed (g).
To analyze fatty acid methyl esters (FAMEs), 0.1 mL of the sample was diluted with 10 mL of n-hexane. A 1 μL solution of diluted FAME was analyzed using a gas chromatography-mass spectrometry (GC-MS) system. The GC-MS was equipped with an RTX-5MS capillary column (30m × 0.25 mm ID, 0.25 μm film thickness). The column temperature was programmed to increase from 70°C (held for 2 min) to 290°C at a rate of 5°C/min. The injection temperature was set at 200°C, while the detector operated at 285°C. Mass detection ranged from 50 to 666 amu using helium as the carrier gas, with a split ratio of 1:80 and a total retention time of 45 min. The chemical components were quantified using the relative percentage of chromatographic peak areas, with identification based on the NIST-MS Library 2014 database. Each sample was analyzed once. GC-MS analysis of component concentrations of biodiesel chemistry was based on the percent peak area and focused on five dominant chemical components.
The quality of the biodiesel was evaluated based on the standards outlined. The following parameters were tested: density (ASTM-D1298-12b), kinematic viscosity (ASTM-D445-2017), acid number (ASTM-D664-04), saponification number (SNI 7182:2015), iodine number (AOCS-Cd-1-25), cetane number (Bose, 2009), total glycerol content (ASTM-D6584-17), and methyl ester content (SNI 7182:2015). Cetane number (CN) and ethyl ester content (KES) were determined using the following empirical equations:
Where SN is the saponification number (mg KOH/g), IV is the iodine value (g I2/100 g), AN is the acid number (mg KOH/g), and Gttl is the glycerol content (%).
Each parameter was measured in duplicates, and the results are presented as mean values ± SD. The biodiesel quality was compared with the specifications of the ASTM D6751, EN 14214, and SNI 7182:2015 standards.
Cluster analysis was performed using Ward’s hierarchical clustering method based on the yield and quality parameters of the biodiesel derived from Kepuh seeds. This analysis aimed to group the biodiesel samples according to similarities in quality, resulting in three distinct classes of cultivation sites.
3. RESULTS and DISCUSSION
The fatty acid profiles of S. foetida oils and their derivatives, such as alkyl esters, play a crucial role in determining the chemical and physical properties of biodiesel. This profile significantly influences the suitability of fats and oils for industrial applications, including lubrication and biodiesel production (Knothe and Kenar, 2004). The results of fatty acid profile analysis based on seed origin are summarized in Table 1 and Fig. 2.
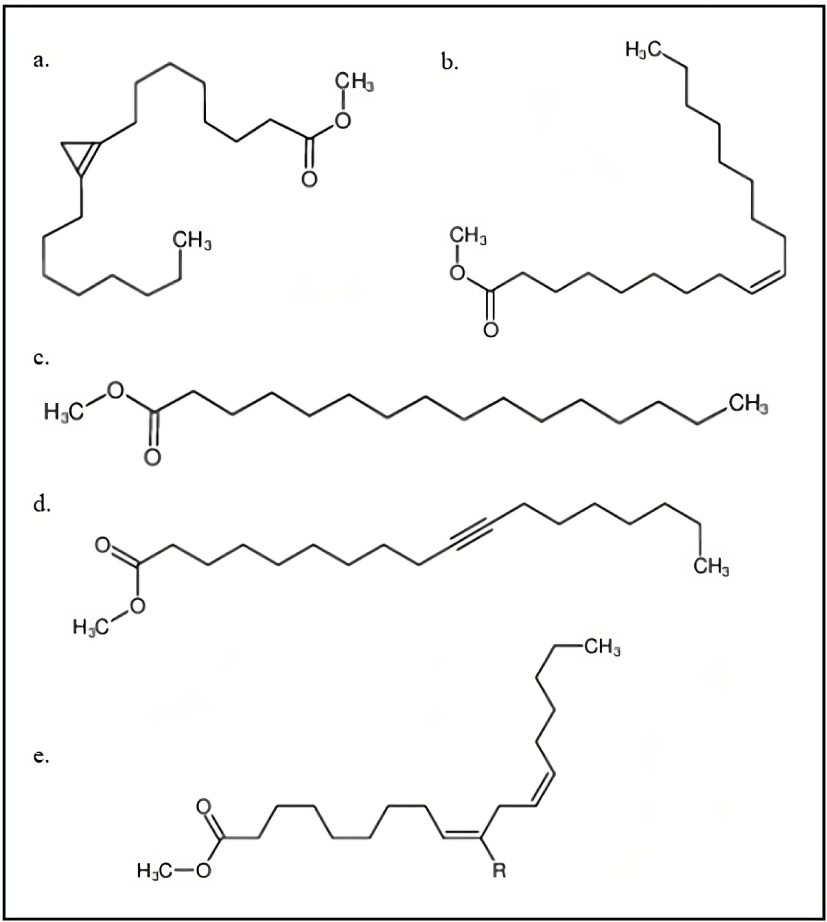
GC-MS detected five fatty acids (in methyl esters) in S. foetida biodiesel: sterculic acid was the predominant compound (57.5% to 69.16%), followed by palmitic acid (11.95% to 18.81%), linoleic acid (4.47% to 9.52%), oleic acid (3.19% to 7.12%), and 10-octadecynoic acid. The most dominant sterculic acid compound was found in Kepuh seeds from Majalengka (K24), Jati (K6), and Sidakan (K8). Kavitha and Murugavelh (2019) also reported that sterculic acid (32%) was the most abundant, followed by palmitic acid (15.88%), oleic acid (10%), linolenic acid (9.95%), and malvalic acid (9%) in S. foetida biodiesel in India. However, in this study, the concentration of each FAME was higher owing to differences in the growth location. Subsequently, the composition of unsaturated fatty acids was found to be higher than that of saturated fatty acids. Gopinath et al. (2010) stated that biodiesel with more unsaturated fatty acids produces more nitrogen oxides and has a lower thermal efficiency than biodiesel with more saturated acids. In addition, the results of the combustion analysis show that highly unsaturated fatty acid biodiesel has longer initial combustion and higher peak pressure than highly saturated fatty acid biodiesel. Biodiesel from sites K2, K9, and K12-14 had a palmitic acid content above 18%, which is a saturated fatty acid compound. The structure of fatty compounds can also affect other properties of biodiesel, such as density, cetane number, calorific value, and low-temperature properties (Gopinath et al., 2010).
Although the present study confirmed a similar fatty acid composition, the percentage of each fatty acid varied depending on the origin of the seed samples. Environmental and climatic factors, as well as genetic background, are likely contributors to these variations. Zhang et al. (2015) found that the differences in fatty acid composition among plant seeds were primarily influenced by genetic factors, with environmental and climatic conditions playing secondary roles. These factors likely explain the variations observed in the fatty acid profiles of S. foetida biodiesel in this study.
The biodiesel yields of S. foetida seeds from various collection sites are summarized in Table 2. The yield based on seed weight ranged from 23.6 at Sidakan (K8) to 26% in Badal (K21). These yields are lower than those achieved in previous studies, which ranged from 90.2% to 96.01% (Kavitha and Murugavelh, 2019; Marri et al., 2020; Silitonga et al., 2013), which were calculated based on the weight of the oil. Most of the biodiesel yields in other reports were also based on oil weight, but the biodiesel yield in this study was based on a weight comparison between the biodiesel produced and the Kepuh seed, as it is expected to be the source of information for the mass production of biodiesel in Indonesia. These differences in biodiesel yield can be influenced by factors such as variations in feedstock quality, environmental conditions, differences in processing techniques, and the efficiency of the transesterification process. These results highlight the importance of optimizing production processes and selecting high-quality seed sources to improve biodiesel yield.
According to regulatory standards for quality parameters, seed oil is considered a suitable raw material for biodiesel production. In this study, biodiesel from S. foetida was evaluated for its density, kinematic viscosity, acid number, saponification number, iodine number, cetane number, total glycerol, and methyl ester content, as presented in Table 2.
Density is a critical parameter that affects ignition quality and specific energy. The densities in this study ranged from 839 to 889.74 kg/m3. In general, the biodiesel from this sample complies with the SNI 7182:2015 standard (850 to 890 kg/m3). However, the biodiesel produced from K8 did not meet this standard. Furthermore, these results align with those of previous studies, which reported densities of 875 kg/m3 (Devan and Mahalakshmi, 2009), 880.7 kg/m3 (Sudradjat et al., 2010), 850 kg/m3 (Bindhu et al., 2011), 879.1 kg/m3 (Silitonga et al., 2013), 873 kg/m3 (Ong et al., 2013), and 945 kg/m3 (Kavitha and Murugavelh, 2019). The difference in density observed in this study was related to differences in fatty acid composition. The low density of biodiesel is caused by the carbon chain of biodiesel being shorter and having fewer double bonds. The lowest density was found in K8, which was composed of double FAMEs, which were fewer in number than those in the other samples. Most of the Kepuh biodiesel used in this study was composed of unsaturated fatty acids, which leads to a greater density than saturated fatty acids (Canakci and Sanli, 2008).
The many differences observed in this study relate to the differences in fatty acid composition. Biodiesel with a lower density is attributed to shorter carbon chains, as well as fewer and shorter bonds with fewer double bonds. Samples with low density can reduce ignition delay in the engine, so injection into the diesel engine occurs over a relatively long period, enabling faster combustion, and leading to more efficient explosions. The high density of biodiesel fuel is caused by the weight of the biodiesel and/or glycerol molecules remaining in the esters (Ghazali et al., 2015). The chain length of the fatty acid composition increases the fuel density (Usta et al., 2011). The fuel injection timing is faster for fuels with higher densities (Gopinath et al., 2010).
This trait influences the performance of the fuel injection system, particularly at low temperatures. Furthermore, viscosity is the most important property of biodiesel because it affects the operation of pressurized combustion systems. The kinematic viscosity of S. foetida biodiesel ranged from 2.58 to 4.53 mm2/s, which is in accordance with ASTM D6751-2012 and SNI 7182:2015 standards but does not meet the requirements of EN 14214-2012 for some samples. The lowest kinematic viscosity was found in sample K 17 (Jantiharjo, Karanganyar), with a value of 2.58 cSt. Low kinematic viscosity in biodiesel occurs because of the use of excessive alcohol, causing biodiesel to have a lower viscosity than diesel oil. In addition, the presence of short-chain fatty esters impacts the low kinematic viscosity, which can be observed in BK 18. The kinematic viscosity of the biodiesel in this study was slightly lower, in line with that observed in previous studies, which report viscosities of 6.0 cSt (Devan and Mahalakshmi, 2009), 4.28 cSt (Sudradjat et al., 2010), 4.72 cSt (Bindhu et al., 2011), 3.96 cSt (Silitonga et al., 2013), 4.92 cSt (Ong et al., 2013), 5.67 cSt (Kavitha and Murugavelh, 2019) and 5.579 cSt (Marri et al., 2020). The presence of long-chain fatty esters in Kepuh biodiesel results in a high kinematic viscosity (Pasae, 2020). Kepuh biodiesel, which was dominated by sterculic acid methyl ester, has a long-chain structure, and many are dominated by methyl esters with double bonds; thus, its kinematic viscosity tends to be high. High viscosities tend to result in the formation of larger droplets during injection, leading to poor atomization. This increases fuel consumption, engine deposits, injector and fuel pump wear, exhaust smoke, and emissions (Folayan et al., 2019).
The acid number reflects the presence of minerals and free fatty acids (FFAs). The acid number in this study ranged from 0.039 to 0.502 mg KOH/g. All the samples conformed to the ASTM D6751-2012, EN 14214-2012, and SNI 7182:2015 standards, indicating a low potential for corrosion or formation of engine deposits. The acid number observed in this study were lower than those of previous studies, which ranged from 0.14 to 5.11 mg-KOH/g (Devan and Mahalakshmi, 2009; Kavitha and Murugavelh, 2019; Ong et al., 2013; Silitonga et al., 2013; Sudradjat et al., 2010). The low acid number in this study is due to the low FFA content of the raw material used in the form of Kepuh oil. Low FFA content has a linear effect on the low acid number of biodiesel. The acid content of Kepuh seed oil is typically less than 5 mg KOH/g. At this level, Kepuh seed oil does not require esterification (Gerpen, 2005).
The saponification number indicates the molecular weight of the biodiesel. The number of saponifications ranged from 195.51 to 253.27 mg KOH/g. The results of this study are greater than those reported by Hendra et al. (2018), who reported that the saponification value of Kepuh biodiesel was 118.16 mg KOH/g. Biodiesel with a high saponification number has low contents of intermediate compounds (mono-and diglycerides) and unreacted triglycerides (Kartika et al., 2011). Higher saponification values correspond to smaller fatty acids and better oil quality, whereas lower saponification values correspond to larger fatty acids and poorer oil quality (Wijayanti, 2012).
The iodine value represents the level of unsaturation; the higher the number of unsaturated or double bonds, the higher the iodine number (Pullen and Saeed, 2014). In this study, the iodine value of the sample ranged from 59.71 to 110.0 mgI2/100 g. Furthermore, all samples were within the standard limit of less than 120, ensuring good oxidative stability. The iodine number observed in this study was similar to that of previous studies, which had values of 103 g-I2/100 g (Ong et al., 2013), 98.0 g-I2/100 g (Devan and Mahalakshmi, 2009), and 88.95 g-I2/100 g (Hendra et al., 2018). Notably, the majority of existing standards indicate iodine values below iodine numbers below 115. The iodine index reflects the degree of oil unsaturation, that is, the number of bonds available for oxygenation (the higher the iodine index, the higher the number of bonds suitable for the formation of hydroperoxides). The presence of hydroperoxides increases the risk of polymerization, acidification, and the formation of insoluble deposits and gums, which can lead to filter plugging and deposits in fuel systems (Gopinath et al., 2010). The low iodine value of biodiesel makes it more easily combustible (Folayan et al., 2019). The lower iodine value indicates that the biodiesel has a better combustion quality. Biodiesel with low iodine content also exhibits lower NOx emissions (Bart et al., 2010).
The cetane numbers in this study ranged from 46.47 to 60.03. Most samples met the ASTM D6751-2012 standard. However, biodiesel production from Nomporejo (K7), Dalangan (K11), and Badal (K21) did not comply. This might be due to higher levels of unsaturation (e.g., linoleic acid content). Previous studies have reported cetane numbers ranging from 54 to 57.9 (Devan and Mahalakshmi, 2009; Hendra et al., 2018; Ong et al., 2013; Silitonga et al., 2013). The low cetane numbers in this study were related to the percentage of non-saturates in the biodiesel samples, such as linoleic and oleic esters. In this study, high cetane content was associated with the number of ester components, sterculic fatty acids (sterculic acid methyl ester), and saturated fatty acid esters in the sample, as observed in K24. The cetane number is influenced by chain length and degree of unsaturation (Saxena et al., 2013).
The cetane number is a key indicator of ignition quality. Gopinath et al. (2010) stated that with a lower cetane fuel, the ignition delay is longer and more fuel is present in the lean flame region (LFR) at the start of combustion. A longer ignition delay results in a higher gas temperature during combustion early in the cycle, and more NO was formed in the LFR. Notably, the cetane number decreases with increasing unsaturation.
Lower glycerol content correlates with reduced viscosity, thus improving the biodiesel performance. High total glycerol content causes problems in the engine. High total glycerol can clog fuel filters, foul fuel injectors, and form deposits at the bottom of fuel storage tanks (McCormick and Westbrook, 2007). Glycerol content in this study ranged from 0.013% to 0.052%, which is in accordance with the standards (ASTM D6751-2012, EN 14214-2012, and SNI 7182:2015). Other studies on total glycerol in palm oil biodiesel reported values of 0.19% (Matinja et al., 2019) and 0.21% (Obaidah et al., 2012). The total glycerol content in this study was lower than that reported in biodiesel studies using palm oil as a raw material. These results demonstrate the superiority of the Kepuh biodiesel.
The highest methyl ester content was found in Bendosari (K16), whereas the lowest was found in Selopamioro (K2). All the samples met the EN 14214-2012 and SNI 7182:2015 standards. In this study, the methyl ester content ranged from 99.28% to 99.79%. This value was slightly higher than that of previous studies, which ranged from 96.06% to 96.8% (Marri et al., 2020; Ong et al., 2013). Compared to other studies on biodiesel, which report a high acid number, the methyl ester content in this study is greater; therefore, Kepuh biodiesel can be considered purer and of better quality. In addition to the acid number, saponification and total glycerol are factors that influence the methyl levels of biodiesel esters. The greater the total acid and glycerol numbers, the greater the effect of low methyl ester levels. As the soaping rate increases, the methyl ester content increases.
Thus, with a high methyl ester content, the Kepuh biodiesel used in this study was purer and of better quality. Overall, the biodiesel properties indicate that S. foetida seed oil is a promising feedstock for biodiesel production, although some variations require further optimization to consistently meet all standards.
Ward’s hierarchical clustering method was employed to classify the S. foetida biodiesel samples based on similarities in yield, quality, and FAME composition. The seed site collections were divided into three distinct clusters (Fig. 3). Cluster I includes biodiesel samples from Sendowo (K1), Srandakan (K3), Jati (K6), Tirtorahayu (K9), Surocolo (K10), Pocung (K19), Tanjung Anom (K20), Sotojayan (K22), Semboja (K23), and Kubangsari (K25). These samples exhibited the lowest acid values, along with high biodiesel yields, kinematic viscosities, and total glycerol and methyl ester contents. Biodiesel from Selopamioro (K2), Pusur (K14), Sawit (K15), Bendosari (K16), Jantiharjo (K17), and Majalengka (K24) were included in Cluster II. These samples were characterized by high density, acid number, and cetane value but had low kinematic viscosity, saponification number, iodine value, total glycerol, and methyl ester content. Finally, the biodiesel samples with the highest saponification number and iodine number but the lowest yield, density, and cetane value were grouped in Cluster III.
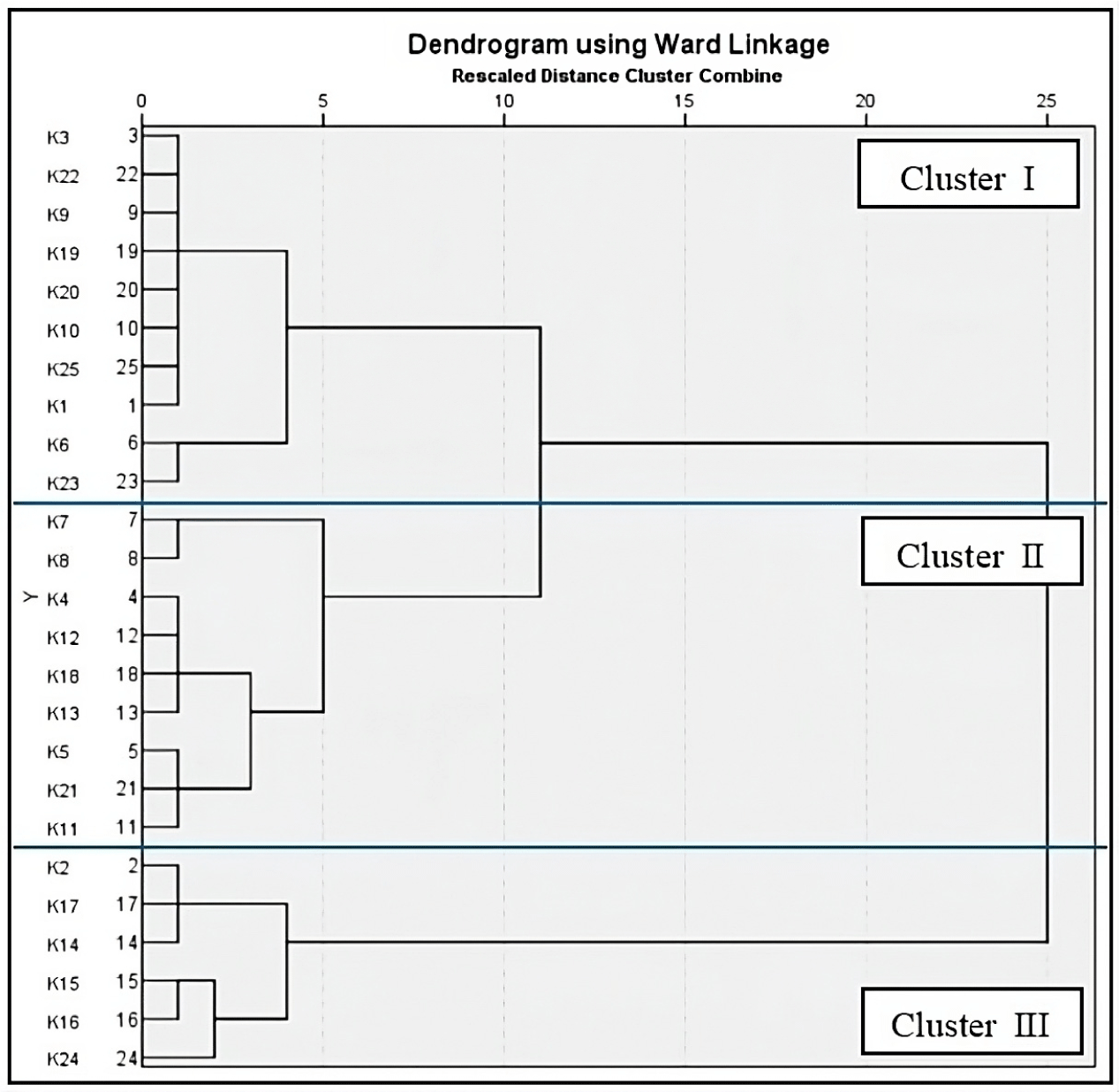
This clustering analysis provides valuable insights for selecting optimal seed sources and improving biodiesel production efficiency and quality through targeted breeding and cultivation. Based on clustering analysis, Cluster II samples were promising candidates for further selection and improvement programs because of their higher cetane number, which indicates better ignition quality. These samples could serve as parental materials for breeding programs aimed at combining desirable traits, leading to superior varieties for biodiesel production. Future efforts should focus on the large-scale cloning and planting of these trees to enhance both the quantity and quality of biodiesel products.
4. CONCLUSIONS
This study examined S. foetida seed populations from 25 different locations across five provinces of Java, Indonesia. Based on a comparison of biodiesel yield and quality across sites, we concluded that biodiesel from Cluster II sites demonstrated the most favorable characteristics for biodiesel production. Among the Cluster II sites, biodiesel from Majalengka (K24) stood out as the most promising source of planting material because of its superior performance. Furthermore, research on other properties of Kepuh biodiesel from Cluster II must be conducted to select and cultivate specific population sources of planting materials for biodiesel production in Indonesia.