1. INTRODUCTION
Wood plastic composites (WPC), formed from wood waste and recycled polymer matrices, have recently garnered significant interest due to the demand for more sustainable materials. The creation of this eco-friendly material may provide an alternative solution to the environmental challenges caused by the overuse of natural wood products and fuel-based resources (Lazrak et al., 2023). The use of waste-derived materials may facilitate forest conservation and diminish the reliance on virgin thermoplastics sourced from fossil fuels in finished products (Lazrak and Hammi, 2024). WPC has been acknowledged as an essential natural fibre-reinforced polymer composite owing to its favourable mechanical and sustainable properties and its broad engineering applications. Its distinctive capacity to combine the benefits of wood and polymer has resulted in the widespread use of WPC in the construction, transportation, furniture, and packaging sectors (Xu et al., 2021).
Indonesia is the origin of wood agriculture and harbours diverse species of wood. Ironwood is indigenous to the island of Kalimantan, whereas teak wood flourishes on the island of Java. Construction has conventionally employed both varieties of wood owing to its resilience against heat, moisture, and humidity (Williams et al., 2015). Nonetheless, this production technique has not completely harnessed the potential of waste wood dust (Laksono et al., 2021). A prior study (Widiastuti et al., 2023) has explored the potential benefit of utilising ironwood waste as a natural filler in wood-plastic composites inside a recycled polypropylene (r-PP) matrix.
Comprehending the effect of wood species on the mechanical properties of WPC is essential for enhancing its efficacy in diverse applications. Fabiyi and McDonald (2010) established that the selection of wood species markedly affects the mechanical properties, thermal stability, and weathering resistance of WPC. Nevertheless, information is scarce regarding the effects of Indonesian wood species on the degradation of WPC’s mechanical properties during water exposure, an essential factor in tropical climates. Two Indonesian native wood species have gained extensive application across several fields, from traditional practices to modern industries, owing to their versatility and abundance.
Under standard usage settings, the WPC may exhibit mechanical properties equivalent to those of other polymeric materials. However, exposure of this composite to humidity or a wet environment may result in the deterioration of its mechanical and physical properties (Lazrak et al., 2023) due to the interfacial compatibility issues between hydrophilic wood fibres and a hydrophobic polymer matrix (Wang et al., 2019). Multiple studies have shown that the exposure of wood-based composites to humid environments results in a decline in their mechanical properties (Sanjeevi et al., 2021). Lazrak et al. (2023) discovered that the water absorption (WA) in WPC escalates with increased wood content. Additionally, WPC’s physical and mechanical properties, as well as its composition, are significantly influenced by the use of coupling agents (Khamtree et al., 2024), plastic types (Ratanawilai et al., 2024), and wood species (Fabiyi and McDonald, 2010). Nair et al. (2018) revealed that specimens immersed in seawater underwent greater mechanical degradation than those in freshwater, underscoring the necessity of assessing the effects of these distinct solutions. Furthermore, several manufacturing options must be evaluated when assessing the feasibility of utilising local wood and plastic waste materials for WPC production. Angulo et al. (2024) demonstrated significant diversity in composite performance among various process methods. Consequently, it is essential to examine the impact of Indonesian wood species, manufacturing process, and exposure to seawater or freshwater on WPC performance, addressing the research gap to promote sustainable material development and practical applications in various conditions.
This study examines the mechanical properties and WA of WPC produced from several wood species within either a recycled or virgin polypropylene (v-PP) matrix, utilising two manufacturing methods: injection and compression moulding (CM). Two distinct solutions, freshwater and seawater, were utilised to submerge the composites. After exposure to the two solutions, the WA characteristics and mechanical properties were then evaluated.
2. MATERIALS and METHODS
v-PP and r-PP served as matrix materials in the manufacturing of WPC. Granulated PP was obtained from a commercial provider in Indonesia, branded as Cosmoplene (MFI = 1.2 g/10 min). Concurrently, the r-PP was obtained from a local recycling facility in Sukoharjo, Central Java, Indonesia. After cleaning, the r-PP was sun-dried and processed through a size five mesh screen to produce small pieces.
Wood mill factories in East Kalimantan and Central Java sourced wood waste from two different species: ironwood and teakwood. Before processing, the wooden floor was submerged for 24 hours at room temperature in a 2% NaOH alkali solution (Hongsriphan, 2016). The wood fibre exhibited a mesh size between 80 and 100. Thereafter, it was rinsed with distilled water and dried in an oven at 80°C for 48 hours.
Maleic anhydride-grafted polypropylene (MAPP) served as a coupling agent. It was acquired from Shenzen Jindaquan Technology, possessing a density of 0.9 g/cm3 and a melt flow rate of 0.6 g/10 min.
The composites were produced with 30% wood fibre content (Lazrak and Hammi, 2024) and incorporated 5% MAPP (Hao et al., 2021). A single-screw extruder operating at a screw speed of 25 rpm was employed to blend the wood fibres and MAPP with v-PP or r-PP. The temperature range from the first to the fourth cylinder was maintained between 175°C and 190°C (Jiang and Zeng, 2019). After compounding, the composite was pulverised into 4–5 mm for the subsequent processes of injection moulding (IM) or CM.
The composites formed through CM were subjected to processing at 165°C and 50 bars in a hot press machine for a duration of 9 minutes. The barrel temperature from hopper to nozzle was established at 180°C to 190°C for the IM process. Both manufacturing methods yielded specimens for tensile tests conforming to ASTM D638 type V standards, measuring 165 × 19 × 3 mm.
The mechanical performance of produced composites was assessed based on tensile properties. Each run was replicated five times on the Universal Testing Machine, utilising a loading rate of 5 mm/min and a gauge length of 30 mm. The tensile properties data included strength and modulus of elasticity (MoE). Tensile properties were assessed both before and after being submerged in water to determine the decrease in mechanical performance following exposure to freshwater and seawater. The seawater used for the immersion solution was sourced from Depok Beach in the Bantul region area of Yogyakarta Special Province, Indonesia.
Moreover, scanning electron microscopy (SEM) at various magnifications was employed to examine the fracture morphology of the composite specimens post-tensile testing.
In accordance with ASTM D570, a 30-day WA test on standard-sized specimens was utilised in the tensile test. Five replicates of each trial were submerged in freshwater or seawater at room temperature. The specimens were periodically extracted from the water for weighing and promptly returned to the water. Following a 30-day submersion in water, the samples were surface-dried with tissue paper before tensile testing. Finally, Equation (1) was used to determine the WA of the WPC.
Where mo denotes the mass of the samples before immersion and mt denotes the mass of the samples after immersion.
3. RESULTS and DISCUSSION
The experimental design comprised three variables: polymer matrix types, wood fibre species, and manufacturing process types. Eight trials were executed in a randomised sequence. The composite specimens were immersed in seawater and distilled water for 30 days, after which they were evaluated for tensile strength (TS), MoE, and WA. Table 1 encapsulates the experimental results.
The tensile stress-strain curves of the WPC samples produced using IM and CM exhibited distinct patterns. The curves were derived using several types of PP matrix and wood waste (Fig. 1). In general, the injection-moulded specimens exhibit superior TS compared to the compression-moulded samples in recycled-HDPE composites, as reported by Angulo et al. (2024).
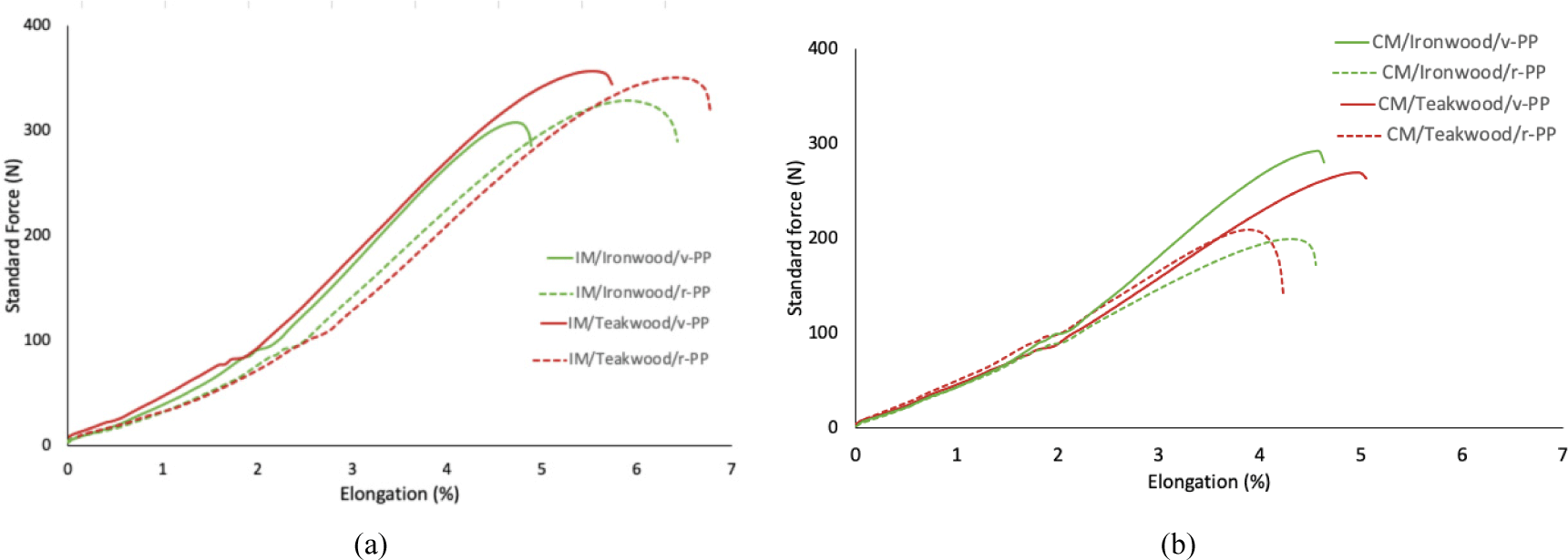
The reduced tensile properties of IM samples are attributable to inferior fibre alignment relative to those produced via CM. Moreover, irrespective of the polymer matrix, injection-moulded WPC made from teakwood exhibited superior TS compared to ironwood specimens. The figure also indicates increased stiffness in the IM specimens using v-PP as the composite matrix. Conversely, the WPC produced through CM exhibited superior TS in specimens composed of v-PP.
The ANOVA test results, performed on specimens produced by each process (Table 2), corroborate the findings derived from the tensile curves. The type of wood waste considerably influences the TS of injection-moulded WPC specimens. In contrast, the tensile properties of compression-moulded samples were markedly affected by the types of polymer matrix.
Fig. 2 illustrates significant mechanical strength reductions for the most specimens following WA, except for the v-PP/ironwood specimens immersed in seawater solutions. The findings indicate the possible applicability of ironwood-based composites in underwater environments. The stress-strain curves for the specimens after exposure to both fresh water and seawater exhibit a pattern analogous to those observed before immersion.
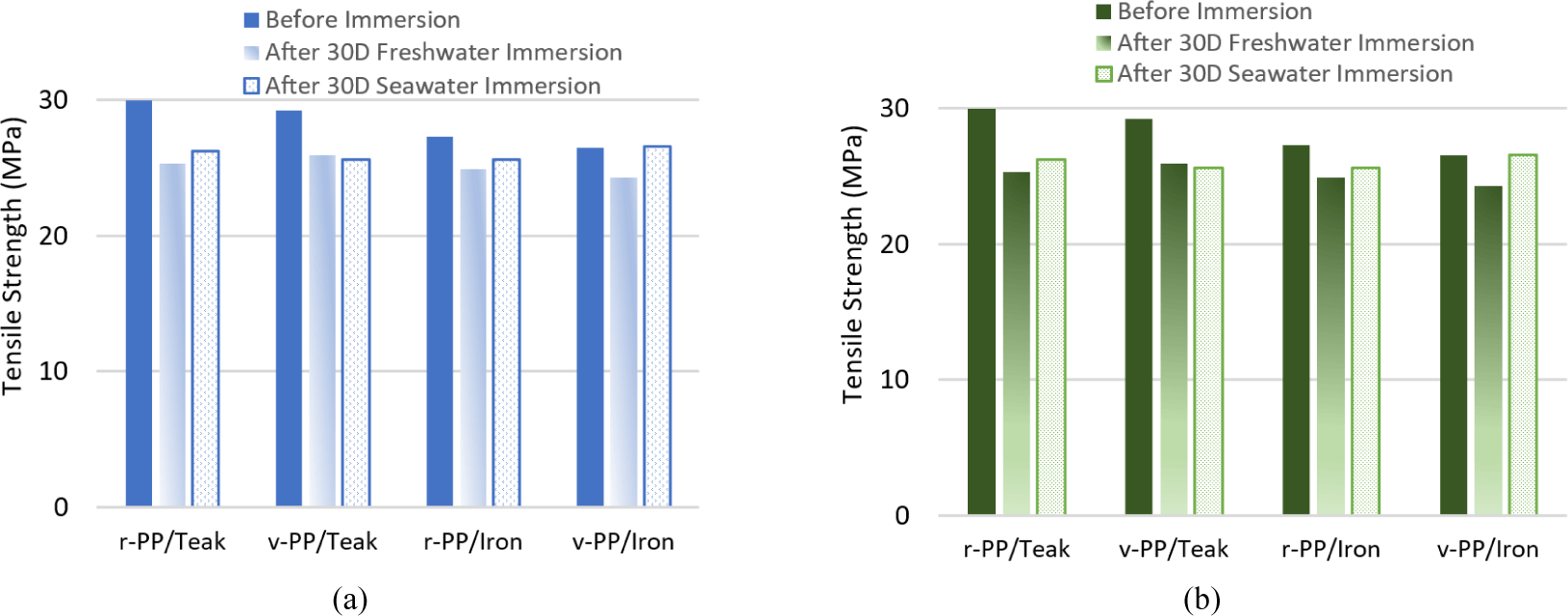
Fig. 3 and Table 3 demonstrate that wood species significantly influence the mechanical strength of IM specimens after immersion in freshwater. At the same time, the type of polymer matrix considerably affects the tensile properties of CM specimens after seawater immersion. Similar to the mechanical properties of the dry samples, the IM specimens reinforced with teakwood exhibited superior mechanical properties after 30 days of immersion in freshwater. On the other hand, CM specimens in a v-PP matrix, upon exposure to seawater, demonstrated superior TS relative to those in the r-PP matrix.
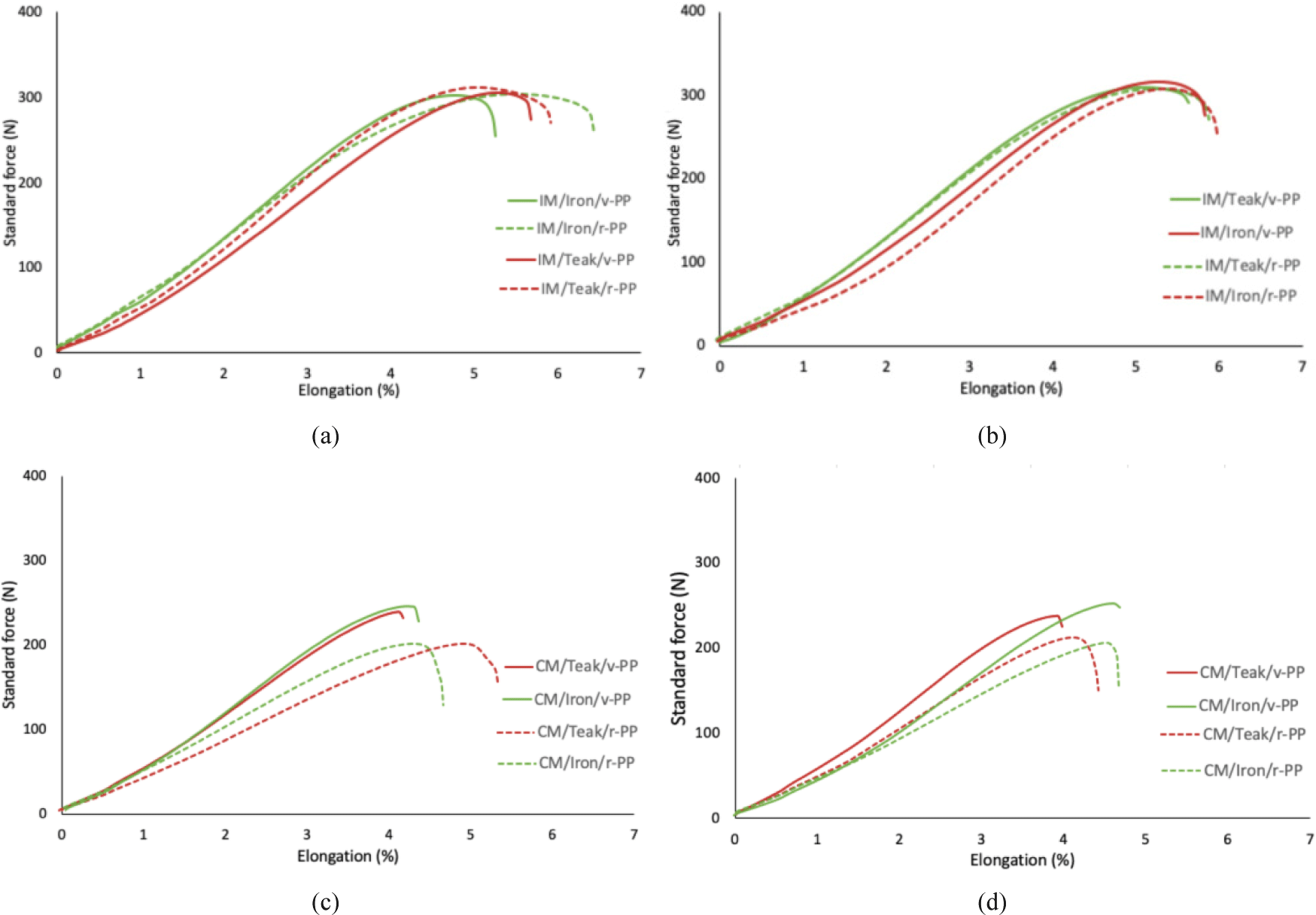
Homkhiew et al. (2015) discovered that the polymer matrix influenced the mechanical properties of WPC in their investigation of a PP matrix containing rubber wood powder. This study revealed that the mechanical properties of composites with a v-PP matrix surpassed those of composites with a r-PP matrix. The disparity is due to v-PP possessing a lower melt flow index compared to r-PP, leading to a composite with reduced flexibility. Moreover, Rohmat et al. (2021) discovered that a virgin polymer matrix demonstrates superior mechanical properties compared to a recycled polymer matrix in bamboo wood fibre composites. Zhang et al. (2023) examined the mechanical properties of polymer matrix composites and noted that the crystallinity of recycled polymers is generally inferior to that of virgin polymers, resulting in higher strength in virgin polymers relative to recycled polymers.
Effah et al. (2018) elucidated the effect of wood types on mechanical properties. A study evaluated six types of sawdust as reinforcement materials for WPC, including pine, eucalyptus, black wattle, LL wattle, port jackson, and beefwood. The findings indicated a substantial effect of wood species on the performance of the composite. The softwood-based composite (pine) demonstrated performance comparable to the eucalyptus composite and surpassed all other hardwood-based composites. This exceptional performance is due to the composite’s high TS, stemming from the improved interaction among wood particles, polymers, and compatibilisers. Furthermore, the incorporation of a compatibiliser improves the compatibility between hydrophilic wood particles and hydrophobic polymers. Similarly, Kumar et al. (2019) established that the wood dust type affects the mechanical properties of WPC, encompassing TS, flexural stiffness, hardness, wear resistance, and impact strength. Notably, babool wood and Sheesham sawdust composites had superior average TS compared to mango and mahogany. In a similar vein, Fabiyi and McDonald (2010) investigated the effect of various species by comparing five wood species as reinforcements in WPCs: hybrid poplar (Populus deltoides × Populus tremuloides), ponderosa pine (Pinus ponderosa), white oak (Quercus alba), Douglas fir (Pseudotsuga menziesii), and black locust (Gleditsia triacanthos). Their study found that wood species significantly influenced the mechanical properties of WPCs. In general, wood species play a crucial role in the performance of WPC composites, suggesting that meticulous wood selection might enhance the composite’s overall performance.
The gravimetric test assessed the weight increase of composite specimens in two immersion solutions: freshwater and seawater. Fig. 4 depicts the WA in all composite specimens following 30 days of immersion. During this period, the composite samples consistently demonstrated rising WA, failing to attain equilibrium, which suggests a propensity for non-Fickian behaviour. Likewise, Balogun et al. (2020) noted that with prolonged immersion time, composites exhibited non-Fickian WA characteristics. This behaviour is often defined by the prolonged duration necessary to attain equilibrium during a WA test (Almeida-Naranjo et al., 2022). Fig. 4 illustrates that the WA of WPC produced via IM was significantly lower than that of WPC manufactured through CM. The IM specimens exhibited a weight increase of approximately 2% after 720 hours of immersion, whereas the CM specimens demonstrated a weight rise of 5%–12%. Nonetheless, no significant d ifferences were found between the immersion solutions.
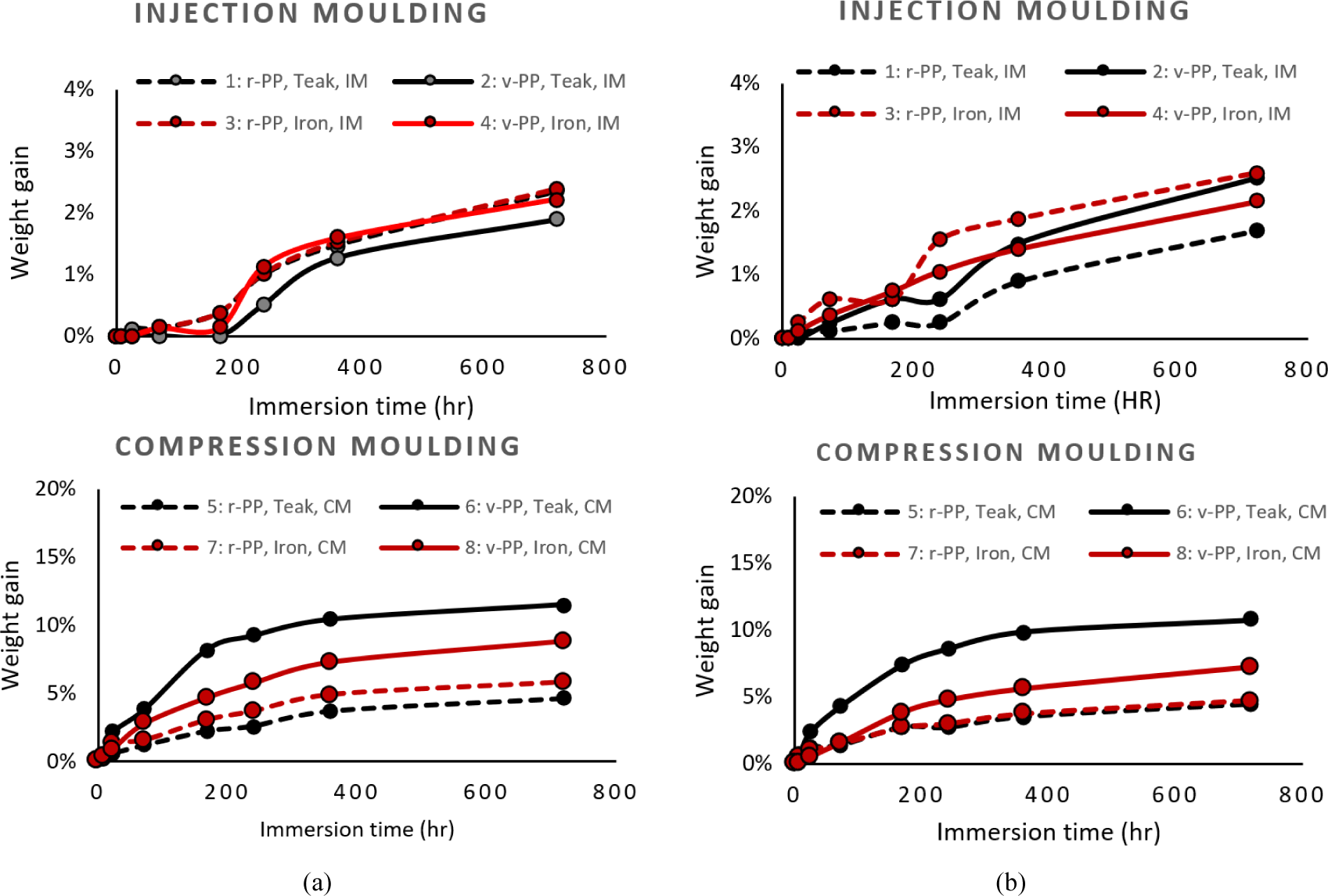
The specimens experience weight gains due to the high cellulose content in natural fibres, which facilitates WA that penetrates the interface through microcracks induced by fibre swelling (Gupta, 2016). This phenomenon represents a weakness in WPCs, as elevated WA induces swelling, hence decreasing mechanical strength and reducing the lifespan of the composite material (Teklu et al., 2019). Furthermore, Wang et al. (2020) identified voids on the surface of composite cracks, attributable to inadequate mixing between the matrix and wood fibres. The existence of voids in WPC specimens significantly enhances WA capacity (Rajkumar et al., 2015). Consequently, a reduced number of voids leads to decreased water penetration into the composite’s depth (Kord et al., 2022). The SEM images in the subsequent section distinctly demonstrate the increased prevalence of voids in CM specimens.
The ANOVA presented in Table 4 indicates that material constituents have no significant impact on the WA of IM specimens. The types of matrix and filler materials significantly influence WA in CM specimens. Moreover, the selection of natural fibre type affects WA qualities; specific natural fibres exhibit significant hydrophilic properties, enabling enhanced WA (Ghani and Ahmad, 2011). Feng et al. (2020) contend that fungal degradation and wood fibre’s intrinsic properties affect WPC’s WA behaviour. Furthermore, the characteristics of wood fibre significantly affect the WA in the pores of WPC (Jin et al., 2021). Therefore, the inconsistent blending of the polymer melt with wood fibres, which possess differing cellulose content based on wood species, explains that varied WA properties of composite specimens including polymer matrices. The variations in cellulose content, along with the hydrophilic nature of various wood types, result in disparate water penetration in the composite specimens.
The SEM images of fractured specimens (Figs. 5 and 6) after tensile testing enhance the comprehension of the composites’ mechanical properties.
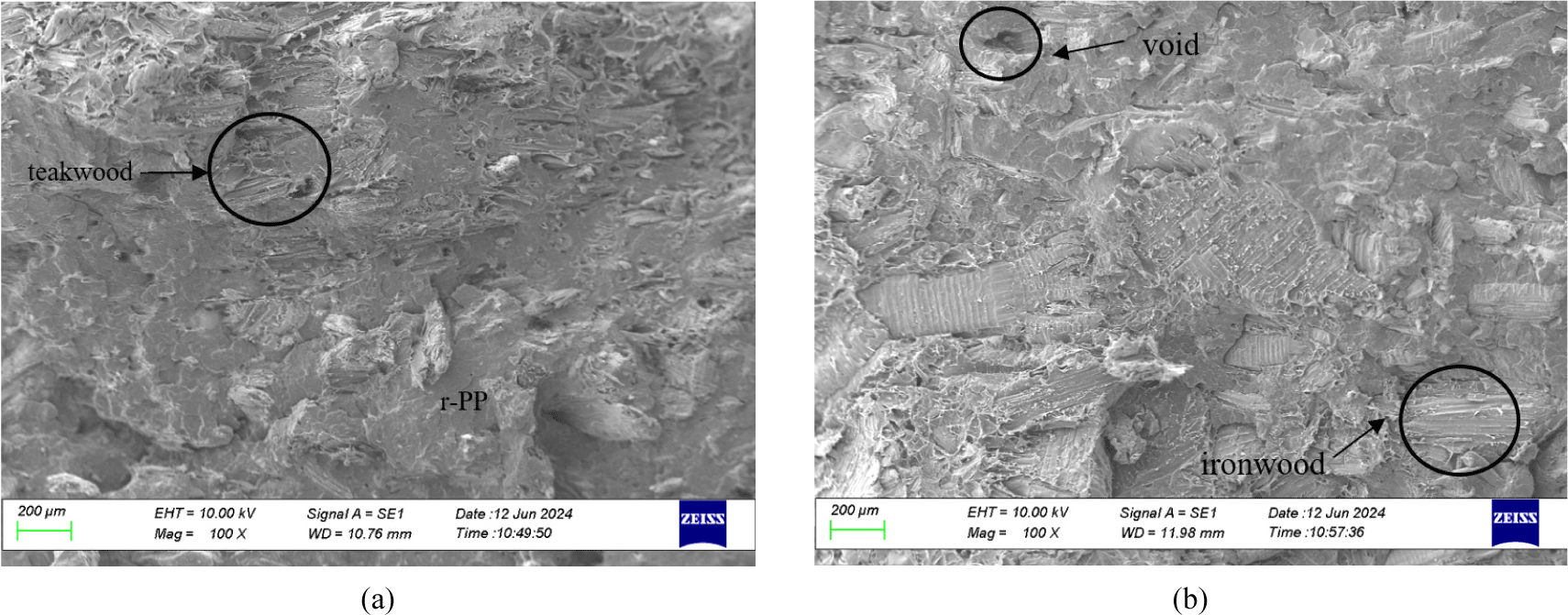
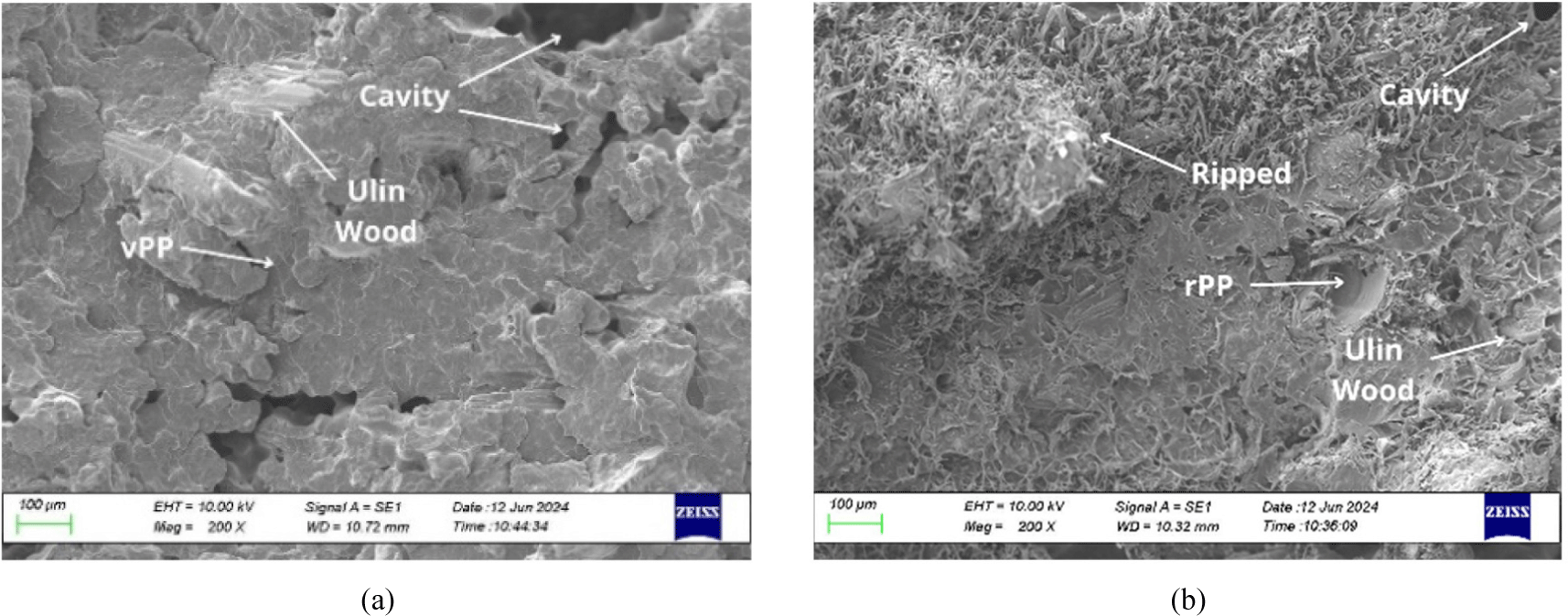
Fig. 5 presents the SEM image of teakwood/r-PP/IM interfacial bonding specimens, exhibiting a 100 × magnification of the teakwood fibre. The r-PP matrix uniformly distributes the wood particles, demonstrating negligible agglomeration or clustering. This homogeneous distribution signifies the efficient amalgamation of teakwood fibre and r-PP, which is crucial for improving the composite’s mechanical properties and reducing WA. The homogeneous distribution of wood particles facilitates the transfer of stress between the matrix and the reinforcement during mechanical loading, hence enhancing the composite’s TS (Koyuncu, 2022). Additionally, it reduces the formation of weak interfacial zones, which are susceptible to moisture absorption and degradation over time (Xian et al., 2021). The reduced number of cracks and gaps in teakwood/r-PP composites markedly improves water resistance, as faults frequently act as entry points for water (Spear et al., 2015). This underscores the necessity of reducing microstructural flaws to enhance the durability of WPC. In contrast, SEM analysis of ironwood/r-PP composites reveals the existence of voids or pores, presumably resulting from oxygen entrapment during the manufacturing process. These voids adversely affect the mechanical properties and WA of the composite (Sun et al., 2017).
Overall, SEM analysis indicates that teakwood/r-PP composites possess a superior and more homogeneous microstructure compared to ironwood/r-PP composites. Teakwood/r-PP composites exhibit reduced WA and enhanced durability relative to ironwood composites, attributed to the uniform distribution of sawdust, and a diminished presence of voids, pores, fractures, or gaps.
Following tensile testing of specimens produced by CM, the SEM images reveal the surface morphology of a v-PP matrix reinforced with ironwood fibre. Composites with a v-PP matrix have a microscopically torn matrix on the surface, indicating the matrix’s robust mechanical strength (Haq and Srivastava, 2017). Consequently, composites using virgin polymer matrices demonstrate superior mechanical strength compared to those employing recycled polymer matrices. Furthermore, the SEM images of compression-moulded specimens exhibit a higher WA rate compared to injection-moulded specimens, presumably attributable to the increased occurrence of voids.
4. CONCLUSIONS
This study investigated the effects of processing methods, polymer matrix types, and wood fibre reinforcement on the TS and WA of WPC. The results indicated that the IM process produced WPC with superior TS compared to CM. Specifically, the type of wood waste significantly influenced the TS of injection-moulded specimens, whereas the polymer matrix type played a more pivotal role in the performance of compression-moulded specimens.
WA rates were not significantly affected by the polymer matrix or wood fibre reinforcement in injection-moulded specimens. However, compression-moulded WPC specimens exhibited considerable variations in WA, depending on the polymer matrix and type of wood fibre used. r-PP demonstrated lower WA compared to v-PP, making it a feasible alternative for sustainable composite manufacturing.
Further research is recommended to thoroughly examine the mass viscosity of WPC materials in both injection or CM processes, as inadequate viscosity can lead to incomplete mould filling. The findings from this study showed that WA in WPC resulted in a marked increase in weight over 30 days of immersion. To gain a more comprehensive understanding of WPC’s long-term WA performance, it is advisable to extend the immersion duration beyond 30 days. Further investigation with extended immersion duration would provide more precise data on the stability and durability of WPC under more extreme immersion conditions. This is essential to ensure that WPC retains its mechanical properties in long-term applications, particularly in wet or waterlogged environments.