1. INTRODUCTION
Noise is classified as a pollution because it disturbs human existence when the echo is too loud, causing health problems and when exposed to the environment in the long term, it may cause negative effects on physical and mental health (Ambert-Dahan et al., 2018; Basner and McGuire, 2018; Basner et al., 2014; Hahad et al., 2019; Preminger and Meeks, 2010; Sanju and Aggarwal, 2018). Noise pollution, especially at night, is a major cause of sleep disturbances. Chronic sleep disruptions can lead to mood swings, reduced work performance, and long-term impacts on health and well-being. Recent research highlights noise from aircraft, roads, and trains as significant contributors. Continuous noise above 30 dB can disrupt sleep, with specific frequencies worsening the effect (Jariwala et al., 2017). Nighttime noise is linked to long-term psychosocial consequences, increasing disturbance levels for up to 24 hours. Particularly vulnerable groups include the elderly, shift workers, individuals with health risks, and those with pre-existing sleep issues (Berglund and Lindvall, 1995). Long-term exposure to noise levels above 65 dB, or acute exposure above 80–85 dB, can lead to cardiovascular disturbances. Acute noise triggers nervous and hormonal responses, temporarily raising blood pressure, heart rate, and causing vasoconstriction. Studies on individuals exposed to occupational or environmental noise indicate that prolonged exposure raises heart rate, blood pressure, blood viscosity, and blood lipid levels (Passchier-Vermeer and Passchier, 2000).
It also includes hearing quality, which is a factor in quality of life, work, and entertainment (Foss, 2014; Fuchs et al., 2001; Obeidat and Al-Share, 2012). From many studies, it was found that sound absorbing materials can reduce the echo level. Especially in areas or rooms with limited space. There are many commercial materials produced to meet market demands. However, these materials are made from synthetic materials that are not environmentally friendly, such as foam, fiberglass, mineral fibers, asbestos, etc. It was found that they have the greatest impact on health and the environment if production is not controlled according to standards. Therefore, it is necessary to find alternative materials that are environmentally friendly (Asdrubali et al., 2012; Hatfield et al., 2002; Hume et al., 2012). Therefore, environmental protection has become an important policy for organizations around the world. Zero waste management is one of the policies that can be studied and applied in both the agricultural and industrial sectors. Waste from the agricultural industry must be managed sustainably (Stansfeld and Clark, 2015), which is part of a circular economy that focuses on reusing and restoring materials or products.
Natural fibers are increasingly vital in the composite and textile industries, primarily due to their renewable, biodegradable, and environmentally friendly properties. Researchers are increasingly exploring various natural fibers as alternatives to synthetic materials for producing sound-absorbing composites. Examples of such fibers include coconut fibers (Chin Vui Sheng et al., 2022; Mamtaz et al., 2017), pineapple leaves (Putra et al., 2018), and Hinoki cypress cubes (Jang, 2022a). Additionally, materials like peanut shells, which are easily recyclable (Jang, 2022b), and agricultural waste products, such as Acanthopanax senticosus wastes (Jang, 2022c), are also being investigated for their potential in creating natural sound-absorbing composites. These efforts are part of a broader movement to replace synthetic materials with sustainable, eco-friendly alternatives. Many studies have attempted to develop sound-absorbing materials from natural fibers with properties comparable to synthetic materials on the market, such as glass fibers, mineral fibers, and PU foam. However, further development is still needed. For example, studies using pineapple leaf fibers and polyvinyl alcohol (PVA) glue have shown performance that falls short of commercial materials (Putra et al., 2018), as do oil palm empty fruit bunch fibers with the same binder (Or et al., 2017). This may be due to production conditions and the type of binder used.
One such natural fiber source is the areca palm, a high-fiber plant. Despite its potential, significant quantities of areca palm fibers are discarded as waste by various industries, particularly the tobacco industry (Arora and Squier, 2018; Mehrtash et al., 2017; Tigari and Rajamma, 2019). This disposal represents a missed opportunity for sustainable material use, as these fibers could be effectively utilized in the development of eco-friendly composites and textiles (Sunny and Rajan, 2022). The areca palm fiber has been researched to make particle boards using urea-formaldehyde glue. It was found that materials made from areca palm fiber can be used as soundproofing sheets in the construction industry (Muralidhar et al., 2019; Zulkarnain et al., 2023). However, it requires a high-heat thermosetting molding method in the manufacturing (Raj et al., 2020). The areca, as reinforcements for polymer composites, offering benefits such as biodegradability and reduced environmental impact. Recent studies on areca fiber reinforced composites examine factors like fiber length, chemical treatments, and surface adhesion, which impact mechanical, thermal, and acoustic properties. Applications for areca composites are expanding, particularly in low-cost construction, packaging, sports equipment, and marine structures. Further research on moisture resistance and fire retardance could broaden their use, promising a positive future for natural fiber composites (Ashok et al., 2018; Binoj et al., 2016; Kamath et al., 2017).
Researchers have been interested in using areca palm to produce sound-absorbing composite materials. Malaysia’s current particle board production faces challenges, including high costs. Areca, a plant with various uses, generates shell waste that can be repurposed. This project investigates the potential of areca fiber for particle board production as a soundproof panel, using urea-formaldehyde glue and a hardener. Tests on 5 mm and 10 mm boards show MOR values of 6.75 mg/mm2 and 2.81 mg/mm2, with sound transmission loss values of 10.3 dB and 15.4 dB. Findings suggest that areca fiber particle boards are viable as soundproof panels in construction (Raj et al., 2020). This study develops composite fiber boards using areca catechu and areca husk fibers to analyze their thermal and acoustic properties. Particle boards were fabricated with varying densities using a wet layup technique. Acoustic testing showed that sound absorption improves as density decreases, demonstrating good acoustic properties (Zulkarnain et al., 2023). This study investigates areca nut leaf sheath (ALS) fibers as efficient natural sound absorbers. ALS fibers were processed into non-woven form and tested for acoustic performance across varying thicknesses. Experimental sound absorption coefficients were compared with theoretical predictions from models such as Delany-Bazley and Allard, with accuracy assessed via root mean squared error. The study identified an optimal thickness and improved empirical model accuracy through inverse acoustical characterization using genetic algorithms. With a 50 mm air gap, a maximum noise reduction coefficient (NRC) of 0.78 was achieved on a 54 mm thick ALS sample, highlighting ALS fibers’ potential as effective natural sound absorbers (Neelappa et al., 2024). Based on the research above, researchers aim to produce sound-absorbing materials using non-heat forming techniques, with the hope that farmers can further develop agricultural waste to add value.
This research aims to develop sound-absorbing composites using PVA glue, a bonding agent that does not require heat during the molding process. This choice of glue allows for easy molding, making it accessible for farmers or small industries to produce these composites independently. The study tested composites at various thicknesses of 10, 20, and 30 mm and with fiber lengths cut to 10, 20, and 30 mm, respectively. The overarching goal is to add value to waste from the areca fiber industry in an environmentally friendly and sustainable manner, contributing to the circular economy in the future.
2. MATERIALS and METHODS
Areca nut shells (ANS) were collected from farmers in Nakhon Si Thammarat Province, Thailand. The ANS (diameter 1.0 ± 0.5 mm) were cut into 10, 20, and 30 mm lengths using a chopping machine and then dried in a drying oven at 105°C for 12 hours, achieving a moisture content of 12% on a dry basis (Fig. 1). For the preparation of the composite material, the dried ANS were mixed in various fiber length ratios: 10 mm, 20 mm, 30 mm, 10 + 20 mm, 10 + 30 mm, and 20 + 30 mm. The resulting mixture was then combined with PVA (NS-406HV, Daisy, Samut Sakhon, Thailand) in a 1:2 ratio for 40 minutes. The mixture was thoroughly stirred to ensure homogeneity, then poured into molds with diameters of 30 mm and 100 mm, and thickness of 10 mm, 20 mm, and 30 mm, respectively, the molds were left to dry at room temperature for 48 hours to evaluate the sound absorption properties. The obtained results are presented in Table 1.
The bulk density of the composite samples was calculated by measuring their dimensions and then weighing them, as described in Equation (1):
Where ρbulk represents bulk density, m denotes mass, and V signifies volume.
The sound absorption coefficient of the composite samples was measured using the impedance tube method [Acoustic Laboratory Thailand (ALT), Bangkok, Thailand] in accordance with ISO 10534–2. Each experimental sample was tested three times, with the specimen removed and reinserted into the holder each time. This approach enhances test repeatability and minimizes errors associated with fiber placement in the pipe. All reported sound absorption coefficient results in this paper exhibit consistent variance (Or et al., 2017). Fig. 2 illustrates the schematic diagram of the SAC experiment, which was conducted across a frequency range of 63 to 6,300 Hz. The test employed tubes of different diameters to measure the SAC: 100 mm for low frequencies and 30 mm for high frequencies, as shown in Fig. 3 (de Carvalho et al., 2020; Jung et al., 2001; Putra et al., 2018).
The physical environment in the chamber, including temperature and humidity, was maintained at a constant level. Table 2 presents the SAC of the composite board across the frequency range of 63 Hz to 6.3 kHz. For samples with varying ingredient ratios of fiber length and densities, the SAC was recorded and analyzed. The experimental data, represented by the sound absorption coefficient average (SAA), were categorized into three frequency groups: low (63 Hz–1 kHz), medium (1 kHz–3 kHz), and high (3 kHz–6.3 kHz). The NRC, which is the arithmetic mean of the absorption coefficients for specific material and installation conditions, was determined based on the center octave frequencies of 250, 500, 1,000, and 2,000 Hz. It was calculated using Equation (2) (according to ISO 11654).
Examine the surface of the workpiece using a microscope. Microscopes, with a magnification range of 8X to 50X, are versatile tools that can be applied to various types of work.
Table 1 presents the physical characteristics of the sound absorbing composite made from ANS combined with PVA glue. The experimental results indicate that the sound-absorbing composite panels were categorized into three groups based on thicknesses of 10, 20, and 30 mm, and fiber lengths of 10, 20, and 30 mm, as well as combinations of fibers with varying lengths. The table also shows the density values of the sound absorbing composites. It was found that increasing the thickness of the composites resulted in a lower average density at the same fiber length. Conversely, increasing the fiber length resulted in higher density at the same composite thickness.
3. RESULTS and DISCUSSION
Table 2 presents the average values of the sound absorption coefficient (SAC) and NRC. Experimental observations revealed that the composites in the 10 mm fiber length group (ANS-T10-L10, ANS-T20-L10, and ANS-T30-L10) exhibited an increasing SAA as thickness increased. This trend was also observed in composites with 20 mm (ANS-T10-L20, ANS-T20-L20, and ANS-T30-L20) and 30 mm (ANS-T10-L30, ANS-T20-L30, and ANS-T30-L30) fiber lengths, where the SAA similarly improved with greater specimen thickness. Research supports this phenomenon, indicating that material thickness, particularly at low frequencies, significantly affects acoustic energy attenuation. Greater thickness enhances damping through viscous and thermal interactions between air and the absorber, thereby improving the SAC (Taban et al., 2020). Jiménez (2018) demonstrated that for rigid-backed acoustic panels, the thickness of the porous layer can be substantially reduced below the quarter-wavelength resonance frequency due to the tortuosity effect. This effect is particularly evident at low frequencies and becomes more pronounced as the structure’s tortuosity increases. As the fiber length increases in sound-absorbing composites of the same thickness, the SAA also increases. For example, in a 10 mm thick composite with a 10 mm fiber length, the SAA value is 0.24. When the fiber length increases to 20 mm, the SAA rises to 0.36, and at 30 mm fiber length, the SAA reaches 0.38. This trend is consistent across composites with thicknesses of 20 mm and 30 mm as well. The observation of the sound-absorbing composite material made from ANS showed that it provides good sound absorption performance at both mid and high frequencies, with the highest SAC value of 0.74 observed at mid frequency for the ANS-T30-L20 composite. In the group of composites with different fiber length combinations, it was observed that in the 30 mm thick sound-absorbing composites, the SAA value increased as more fiber lengths were added to the mix. Specifically, the combination of 20 mm and 30 mm fiber lengths yielded the highest SAA value of 0.44 in this experiment (ANS-T30-L20 + 30).
This trend is also evident in the NRC values: as the thickness of the sound-absorbing composites increases, the NRC value rises accordingly. Similarly, increasing the fiber length or using combinations of fiber lengths also results in higher NRC values. The highest NRC value achieved was 0.57 for ANS-T30-L20 + 30 sound-absorbing composite. This finding aligns with research on the impact of asphalt layer thickness on sound absorption and noise reduction (Kim et al., 2018). Previous studies have also reported this shifting trend in sound absorption spectra, attributing it to variations in the propagation path lengths within porous structures (Li et al., 2015). And This is attributed to the longer dissipative process of viscous and thermal conduction between air and the absorbing material within the samples (Soltani et al., 2020).
Fig. 4 illustrates the effect of thickness on the sound absorption coefficient for a given fiber length. Fig. 4(a) shows the sound-absorbing composites with a fiber length of 10 mm and workpiece thicknesses of 10 mm (ANS-T10-L10), 20 mm (ANS-T20-L10), and 30 mm (ANS-T30-L10). While the sound absorption behavior of the composites was similar, the SAC varied. It was observed that as the thickness increased, the SAC value also increased at lower frequencies. Specifically, the SAC for the 10 mm thick composite reached 0.58 above 1,000 Hz, for the 20 mm thick composite it reached 0.66 above 800 Hz, and for the 30 mm thick composite, it reached 0.71 above 630 Hz. After that, the SAC value decreased and stabilized from 2,000 Hz onwards.
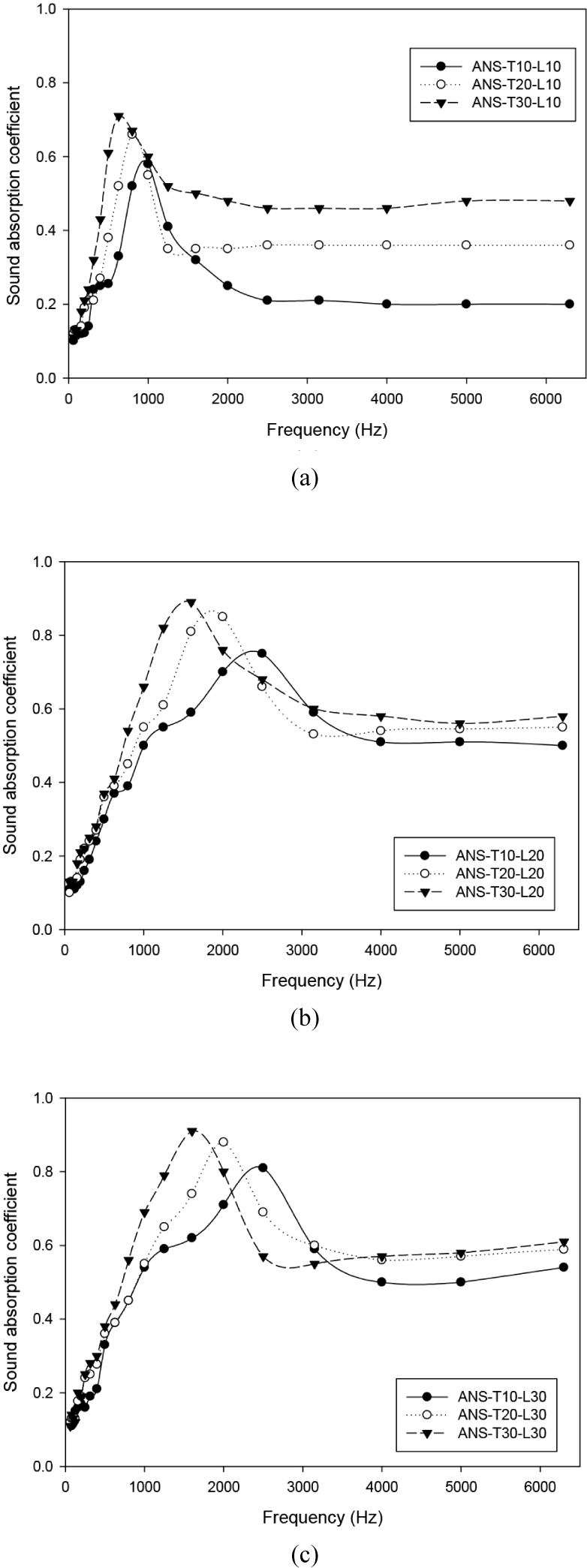
Similarly, Fig. 4(b) and (c) demonstrate that the graph exhibits a single peak. As the thickness of the sound-absorbing composite increases, the SAC value rises in the lower frequency range. In Fig. 4(b), for a fiber length of 20 mm, the 10 mm thick composite sheet (ANS-T10-L20) shows the highest SAC of 0.75 above 2,500 Hz, the 20 mm thick sheet (ANS-T20-L20) reaches 0.85 above 2,000 Hz, and the 30 mm thick sheet (ANS-T30-L20) achieves 0.89 above 1,600 Hz. Fig. 4(c) shows that the sound-absorbing composite with a fiber length of 30 mm exhibits a similar SAC behavior, where increasing the thickness of the composite sheet results in a higher SAC value at lower frequencies. The peak SAC values are 0.81 for the 10 mm thick sheet above 2,500 Hz (ANS-T10-L30), 0.88 for the 20 mm thick sheet above 2,000 Hz (ANS-T20-L30), and 0.91 for the 30 mm thick sheet above 1,600 Hz (ANS-T30-L30).
Therefore, it is evident that the thickness of the sound-absorbing composite significantly influences the SAC value, particularly by enhancing absorption at lower frequencies. This observation is consistent with findings reported in previous research (Or et al., 2017; Putra et al., 2018).
Fig. 5 illustrates the effect of fiber length on the sound absorption coefficient for composite sheets of consistent thickness. It is evident that, at the same thickness, the 10 mm fiber group displays distinct sound absorption behavior compared to the 20 mm and 30 mm fiber groups. Fig. 5(a) shows that for 10 mm thick sound-absorbing composites, the graph still exhibits a single peak across different fiber lengths, though the SAC values vary. For ANS-T10-L10, the SAC value is highest at low frequencies and decreases at mid to high frequencies. In contrast, composites with 20 mm (ANS-T10-L20) and 30 mm (ANS-T10-L30) fiber lengths reach their highest SAC value at 2,500 Hz, after which the SAC value decreases to a stable level. Similarly, in Fig. 5(b) and (c), the 10 mm fiber length yields significantly lower SAC values compared to the 20 mm and 30 mm fiber lengths. The mid to high-frequency absorption range is notably higher for the longer fibers, indicating that using fibers longer than 20 mm results in better SAC values.
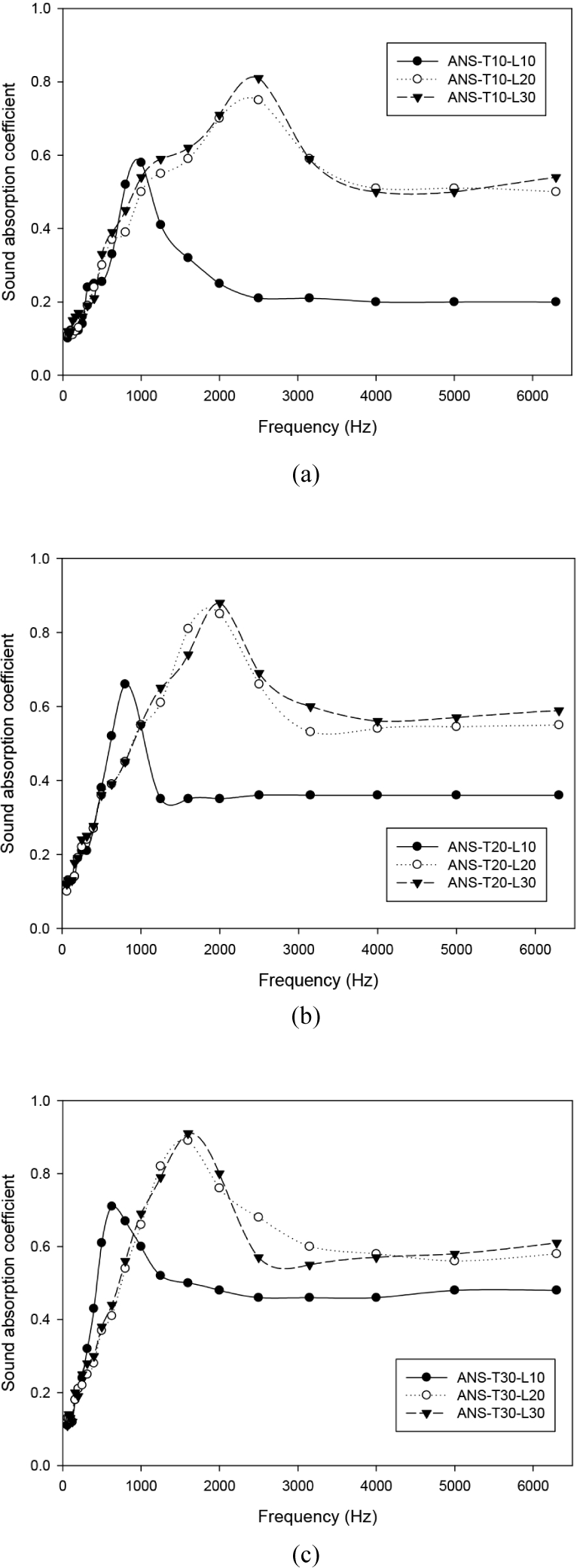
Fig. 6 illustrates the effect of the fiber length ratio on the sound absorption coefficient for composites made from different fiber lengths, with the thickness of these sound-absorbing composites being 30 mm. It was found that the SAC values exhibited a different pattern compared to those observed with a single fiber length ratio. The graph showed two peaks, with a dip in the mid-frequency range followed by an increase at higher frequencies.
One noticeable observation is that when longer fiber lengths are mixed, the SAC values tend to be higher at lower frequencies. For instance, ANS-T30-L10 + 20 exhibits a peak SAC of 0.82 above 2,500 Hz. When 30 mm fibers are added, the SAC increases, with ANS-T30-L10 + 30 showing a peak SAC of 0.88 above 1,600 Hz, and ANS-T30-L20 + 30 achieving a peak SAC of 0.90 above 1,600 Hz. The sound absorption behavior depicted in the graph may be attributed to the complexity of the multi-sized pores formed within the sound-absorbing composite as a result of the varying fiber lengths.
Fig. 7 presents a comparison of the sound absorption coefficients for fiber blends of different lengths, all with a thickness of 30 mm. When comparing the sound-absorbing composites with fiber lengths of 10 and 20 mm to those with blended fiber lengths of 10 + 20 mm and 10 + 30 mm, as shown in Fig. 7(a), it was observed that the composites with blended fibers exhibited higher SAC values in the low-frequency range. However, as the frequency transitioned into the mid-range, the SAC values decreased before rising again in the high-frequency range. And when comparing the sound-absorbing composites with fiber lengths of 20 and 30 mm to the blend of two fiber lengths 20 + 30 mm shown in Fig. 7(b), the SAC values were found to be very close. The ANS-T30-L20 + 30 composite exhibited a drop in the SAC around the 2,500 Hz range before rising again at higher frequencies.
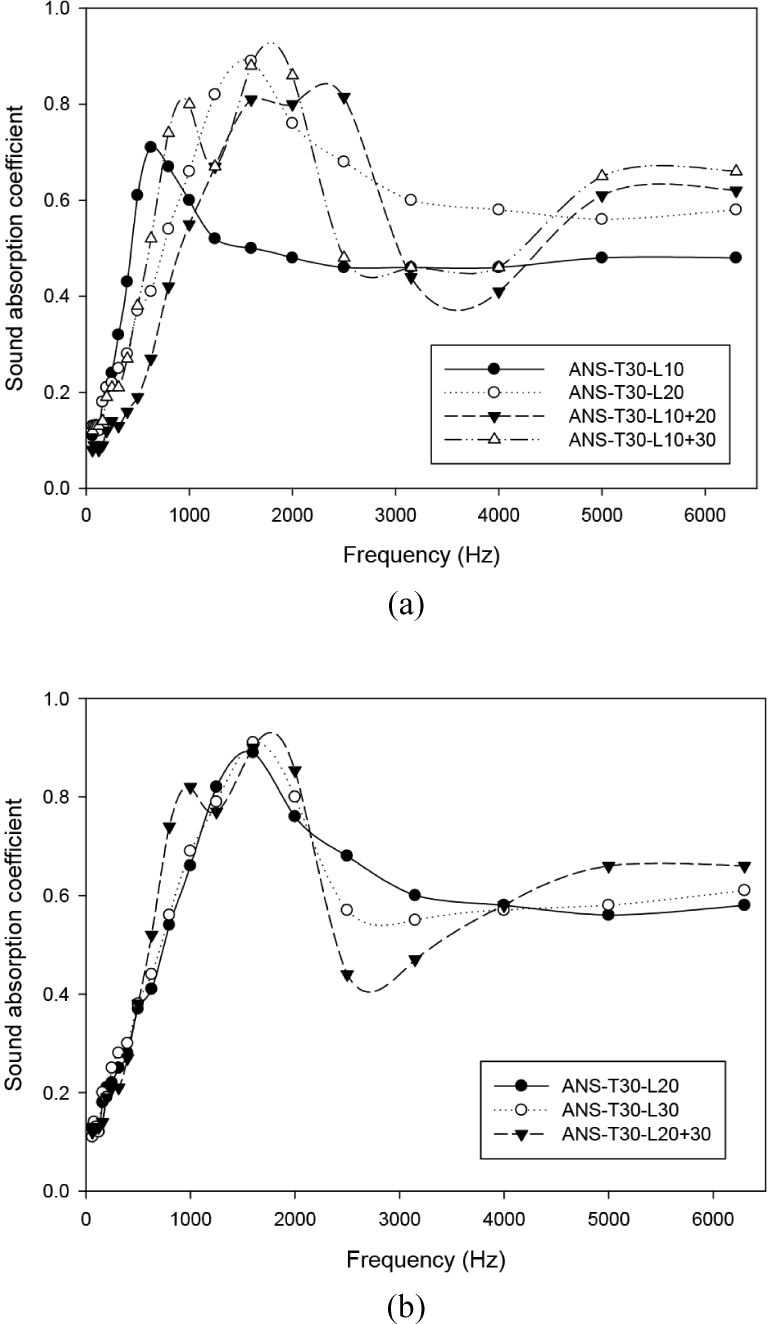
Fig. 8 illustrates the condition of the fibers prior to forming the sound-absorbing composite [Fig. 8(a)] and the surface of the ANS fiber sound-absorbing composite bonded with PVA glue. The images reveal that the glue effectively bonds the fibers together, creating a complex network of gaps within the composite [Fig. 8(b)] under a microscope.
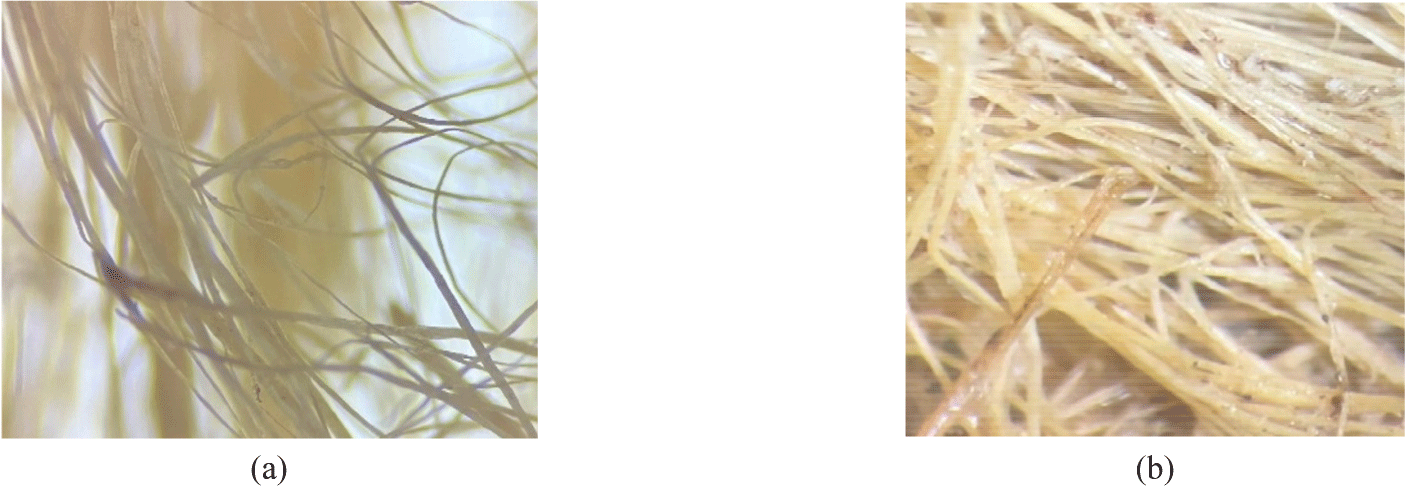
Based on the experimental results and comparison of SAC values for sound-absorbing composites made from ANS fibers bonded with PVA glue, the optimal conditions were found to be ANS-T30-L20 + 30, ANS-T30-L10 + 30, and ANS-T30-L30, respectively. The thickness of the composites significantly enhances their sound absorption properties. Additionally, fibers with a length of 30 mm proved to be the most suitable for enhancing sound absorption. The mixing ratio of fibers with different lengths also significantly improves the SAC values of the composite in the low-frequency range, suggesting potential for commercial development.
This study is limited to testing sound absorption properties using impedance tubes. To develop sound-absorbing materials suitable for the industrial sector, additional methods should be tested, such as the random-incidence method for reverberation room (ISO 354 standard), fire resistance testing, and the use of human-friendly materials.
4. CONCLUSIONS
The study on the development of sound-absorbing composites from ANS fibers with PVA glue, using varying thicknesses and fiber lengths, aimed to determine the absorption coefficient through the impedance tube technique. The following conclusions were drawn:
-
The effect of thickness on the SAA and NRC values of ANS sound-absorbing composite panels bonded with PVA glue was clearly evident, with 30 mm identified as the most suitable thickness in this study, specifically within the frequency range of 1,500 to 2,500 Hz.
-
The length of the ANS fibers significantly influences the increase in SAA and NRC values of sound-absorbing composite panels within the low-to-mid frequency range, with a fiber length of 30 mm yielding particularly satisfactory results.
-
The combination of ANS fibers of varying lengths in the sound absorption composites leads to a distinct SAC behavior compared to using fibers of a single length. This approach allows for targeted sound absorption at specific frequencies. Among the tested configurations, ANS-T30-L20 + 30 demonstrated the most satisfactory results in this experiment.
In this research, the following recommendations are made: Since PVA glue is water-soluble, the resulting sound-absorbing composite is unsuitable for use in moist environments or in contact with water. This represents a limitation in the current experiment, necessitating further development and testing under various conditions. Nevertheless, this study provides a valuable guideline for repurposing waste from the areca processing industry, contributing to environmental sustainability in the future.