1. INTRODUCTION
The use of wood materials in the field of construction dates back to the early stages of human history (Carran et al., 2012). “Laminated Wood Material,” which emerged with the development of this material, is widely used in several countries today, especially in earthquake zones, once again revealing the importance of wooden structures that have been used for thousands of years (Kasal et al., 2004; Tannert et al., 2018). The production principle of laminated wood materials is based on bonding wooden planks cut into various sizes to each other (Sikora et al., 2016). The most important advantage of this building material, which has recently become particularly effective, is that it is environmentally friendly and lightweight, making notable contributions to nature and earthquake resistance (Pei et al., 2013; Ramage et al., 2017). Owing to these properties, wooden materials are considered important candidates for building materials to prevent damage to nature caused by cement production and to curb urbanization in our country (Hildebrandt et al., 2017). Increasing environmental pollution has led to serious global warming, and one of the biggest factors contributing to environmental pollution is the release of greenhouse gases during the production of cement used in the construction industry (Arıoğlu Akan et al., 2017). The importance of reducing environmentally harmful gases and of using different building materials is evident (Pappu et al., 2007; Sharma et al., 2015). Reinforced concrete (RC) construction has not been curtailed in several countries without considering this issue (Farooq et al., 2021; Hashmi et al., 2020). In recent years, several developed countries have turned to alternative building materials other than concrete and utilized natural materials in the building sector. The most commonly used material is wood (Berglund and Burgert, 2018; Ozdemir et al., 2023).
Recently, RC buildings have suffered heavy damage owing to earthquakes, prompting them to seek alternative lightweight construction materials (Khedari et al., 2001; Vantadori et al., 2019). Wooden structures, which have become increasingly prevalent in earthquake-prone regions, include high-rise buildings, schools, and residences (Høibø et al., 2015).
Adhesives play an important role in structural wooden elements (Lee and Oh, 2023; Trisatya et al., 2023). In this study, after applying a vinyl acetate polymer adhesive between the laminated layers of the carbon-fiber-reinforced polymer (CFRP), the desired configurations were obtained by pressing. Several types of glue provide high adherence by inducing several physical and chemical reactions during adhesion. Carbon fiber composite fabric is a reinforcement material that can be applied to RC and wooden structures (Meier, 1995). These fabrics, which are applied externally to building elements, are generally used to repair and strengthen historical buildings and RC structures (Aidoo et al., 2004). Additionally, this material, which is extremely light and has a higher strength than steel, has been widely used in reinforcement work (Saad and Lengyel, 2022). Therefore, the number of studies on carbon fiber composite fabrics has increased in recent years (Maaddawy and Soudki, 2008; Xiong et al., 2007). In recent years, FRP composites have been considered as important reinforcement materials in the field of construction (Jung et al., 2016). Lee et al. (2019) reported an excellent bonding strength between samples bonded with CFRP as a reinforcement. Wooden elements reinforced with the CFRP layer were determined not to break at the top and maintained their strength (Park et al., 2009). The fracture toughness load and energy absorption capacity of FRP-reinforced laminated wood have also improved (Kim and Hong, 2011, 2015).
This innovative method involving CFRP in the field of construction has begun to be used in developed countries. It is assumed to reduce the cross-sections using this method, especially in large-span systems. As the span of the elements increases, the dimensions naturally increase, necessitating larger building elements. In this study, new strengthening methods have been developed using CFRP composite fabrics in wooden structures by placing them in the interlayers before the lamination process, without compromising the aesthetics, and reducing the dimensions of the wooden elements.
2. MATERIALS and METHODS
Suitable parts of wood material from the tree trunk in the form of plates were obtained by adhering these plates together with strong adhesives. This method, which is based on the principle of producing structural elements of the desired size, shape, and slope in these materials, not only eliminates the disadvantages of wood but also makes it more advantageous. Wooden building elements generally exhibit high bearing capacities, as well as thermal and acoustic insulation properties. However, wooden structures must maintain their natural appearance without compromising their aesthetics. Strengthening techniques are also important for increasing the resistance of wood to water and fire, preventing decay, and enhancing ecological value. Wooden structures are the best building systems tested and approved by nature.
In this study, “Larix kaempferi” was used as heat-treated wood material. The sections designated for laminating wooden elements underwent drying through the ThermoWood method at an oven-dried state of 212°C for 2 h, achieving a density of 0.630 g/cm3 with 18% moisture content. Prior to assembling the laminated wood elements, impregnation was performed before gluing.
A vinyl acetate adhesive was used to assemble the test specimens. The technical specifications of the adhesive are listed in Table 1. The adhesive type features a viscosity of 14,400 cps at 20°C, with a density of 1.05 g/mL and a water resistance class of D3. Adhesives classified under the D3 waterproof class are known for their resistance to moisture and rapid hardening during lamination processes. The technical specifications of the adhesive (D3-PVA), provided by Akfix Chemical (İstanbul, Turkey), are listed in Table 1.
Chemical structure | Appearance | Density (g/mL) | Solid matter (%) | Viscosity (cps at 20°C) | pH | Glue line pressure (kg/cm2) | Water resistance class |
---|---|---|---|---|---|---|---|
Vinyl acetate polymer | White | 1.05 | 54 | 14,440 | 5–6 | 9–12 | D3 |
In this study, wooden arches bonded with a vinyl acetate polymer adhesive were produced by placing a CFRP fabric on the interlayers before the lamination process. This adhesive material was used in both processes because of its exceptional adhesion strength, low viscosity, and ease of application. Strong adhesives have been widely used as structural elements in various studies (Park et al., 2009; Roohnia et al., 2014).
Laminated wood systems are building materials obtained by applying compression in hot or cold presses and glue between wood lamellae obtained by cutting, carving, and sawing methods. The drying, gluing, and shaping of wood are the major stages in the finishing of the surface and production of laminated wood (Fig. 1). Using laminated wood, structural elements can be produced in several forms, such as columns, beams, arches, and trusses. To improve the strength of the lamination technique, the defects of wood material must be removed. Through the application of the lamination technique, products of higher quality can be produced in the desired form by designing them (Ha et al., 2023; Hwang et al., 2022; Song and Kim, 2023).
To obtain the desired curvature in the production of wooden arch elements, a steel mold was fabricated, and clamping was applied to the vices. The production parts of the wooden arch elements are shown in Fig. 1 and the linear variable differential transformer (LVDT) locations are shown in detail in Fig. 1. A vinyl acetate polymer adhesive was used to assemble the test specimens. The desired configurations were obtained by pressing an adhesive between the laminated layers. Wooden arch elements were produced with a height of 25 cm and a span of nearly 250 cm by gluing ten wooden plates of 1.5 cm thickness and laminating them. The dimensions of the wooden arch elements are shown in detail (Fig. 1). Pressure is important for ensuring the adhesion of the wood material to be glued. The pressure was adjusted to equal the thickness by combining the two wood materials to be joined to ensure full contact between the glue and the bonded surfaces. The wooden structural element was pressed for one day. In the laminated wood production process, the correct arrangement of the layers to be laminated is crucial for durability. For this purpose, laminated wooden elements were obtained by combining parts of the tree other than the defective areas using special glue of certain sizes with the fiber directions parallel to each other (Fig. 2).
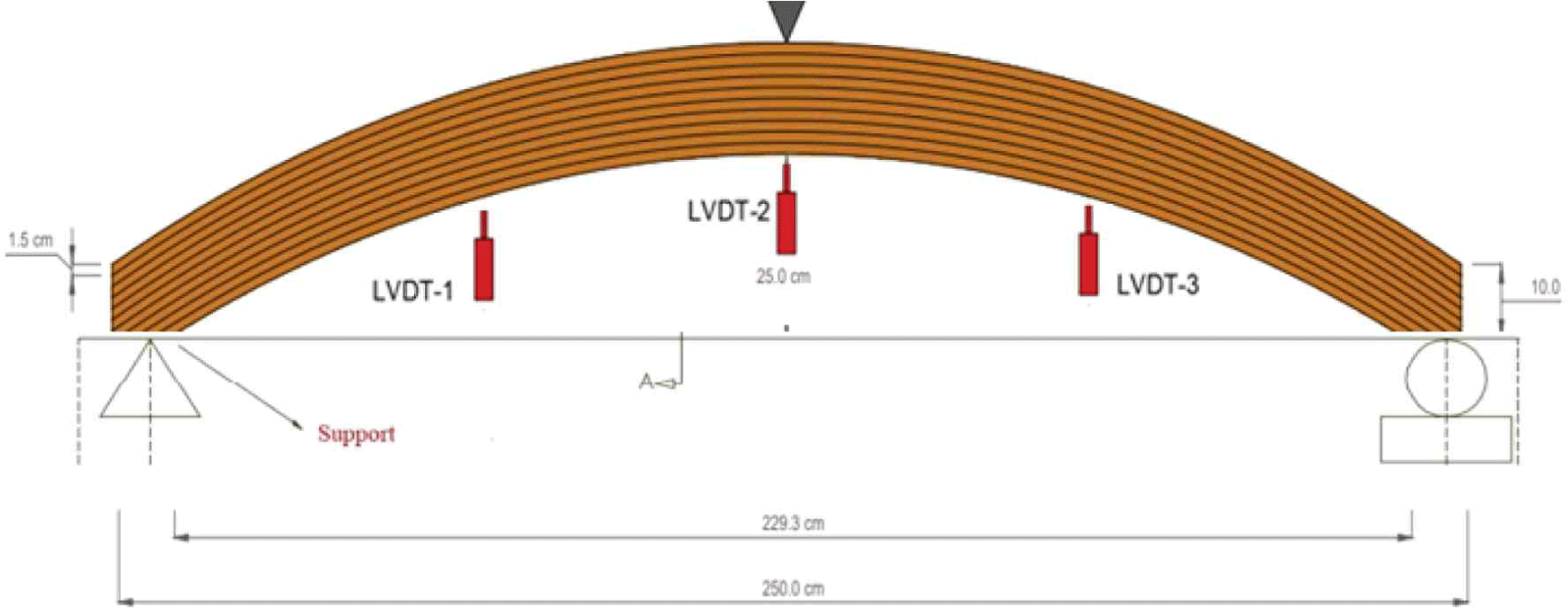
Different types of fiber-reinforced polymers (FRPs) have been used to strengthen structural elements. CFRP materials are generally preferred. As these materials have extremely high tensile strengths, they are widely used in reinforcement. The CFRP, provided by the Art Structure Project Engineering Company (Ankara, Turkey), had a thickness of 0.7 mm. The studied parameters included a carbon fiber volumetric ratio of 0.5% (SikaWrap 600C, Sika, Baar, Switzerland) and the configuration of the transverse CFRP reinforcement. Unidirectional CFRP with an area of 600 g/m2 was used as the carbon fabric. The mechanical properties of the CFRP are presented in Table 2.
Thickness (mm) | Area weight (g/m2) | Tensile strength (MPa) | Modulus of elasticity (GPa) | Elongation at rupture (%) | |
---|---|---|---|---|---|
CFRP | 0.7 | 600 | 4,137 | 242 | 1.5 |
A laminated wood material is defined as a building element obtained by gluing wooden lamellae, especially fibers, in parallel. It is produced by combining the ends of solid wood side-by-side and on top of each other to create large dimensions. These structural elements are arranged parallel to the fiber direction. In this study, a CFRP fabric was applied between laminated layers of wood using various methods (Fig. 3). Fig. 4 demonstrates how hybrid-reinforced laminated wood arches, resembling stirrups, were applied using CFRP, both between the layers and on the outside. CFRP strip tapes (5 cm thick CFRP strip tapes were applied to the wooden arch elements at 35 cm intervals. Fig. 4 shows the locations of these strips and the LVDT in detail.
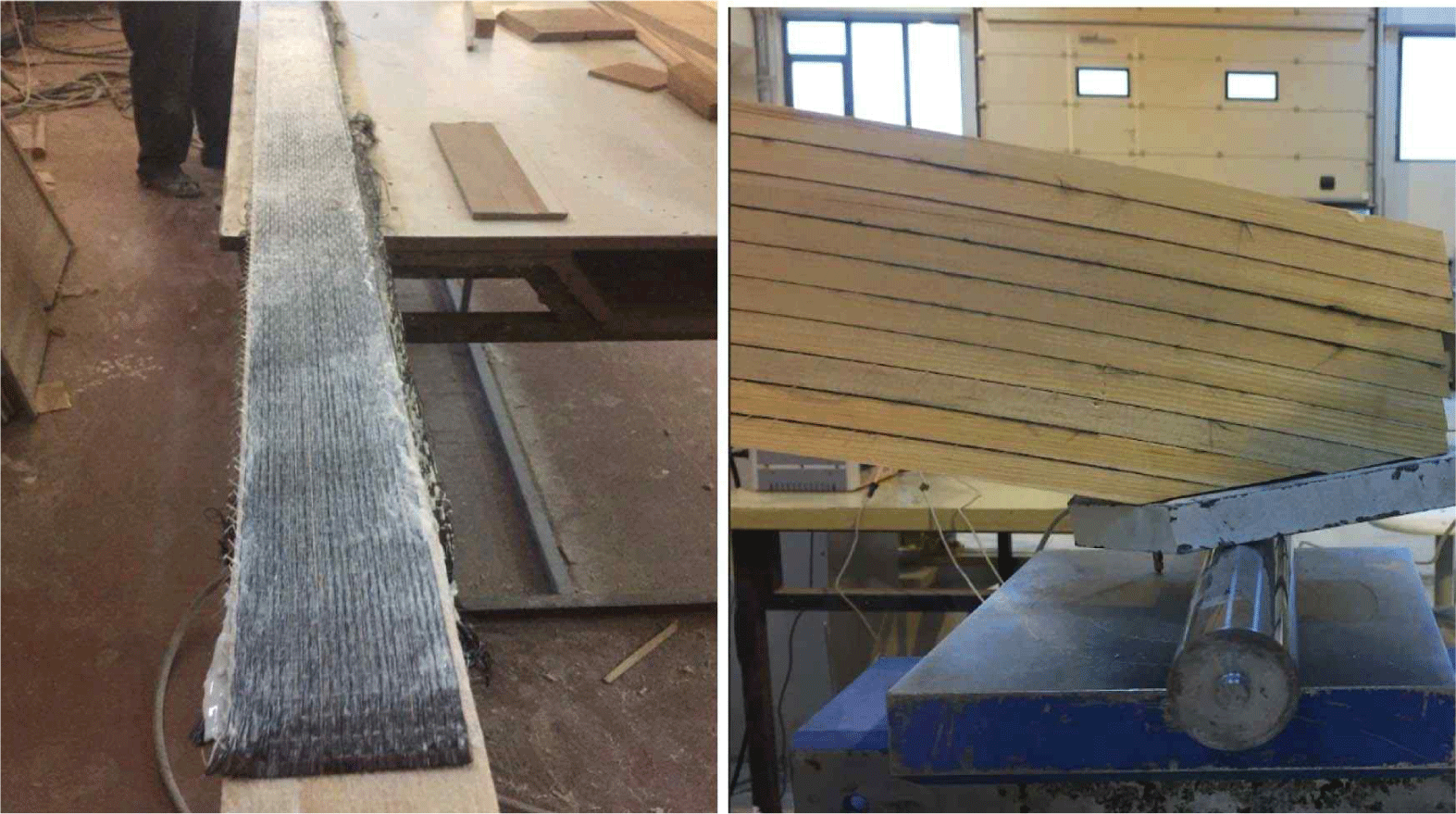
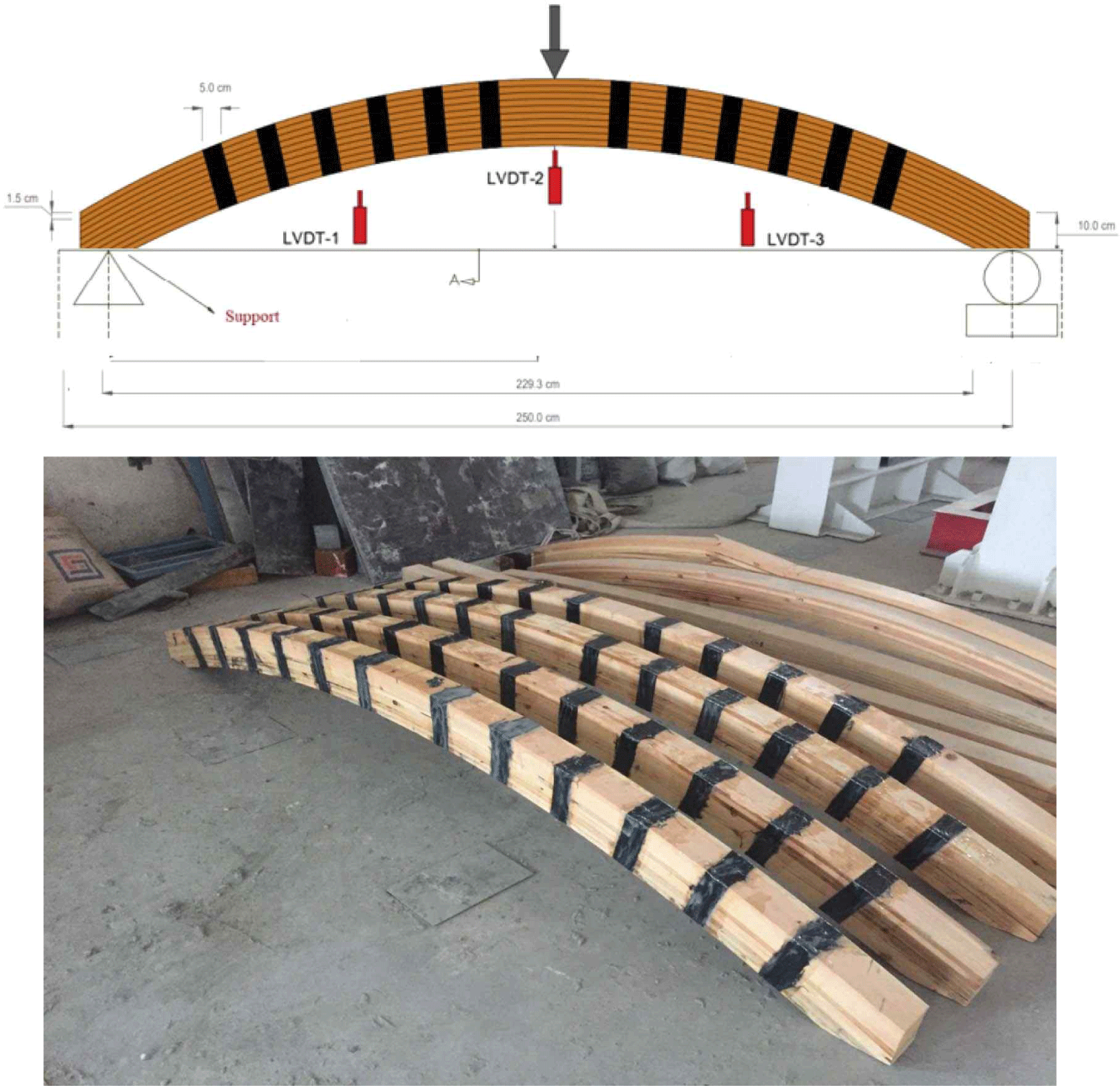
In this study, the mechanical changes in FRP composites of arch elements produced by the lamination process, each consisting of ten wooden plates, were investigated. The aforementioned strengthening process was carried out in two different ways: placing the FRP composite fabric in various combinations between the wooden board layers and wrapping the elements in strips with FRP composite fabrics. For this purpose, two preliminary test samples were produced and the applicability of the study was tested. The test results clearly showed the effect of the FRP composite fabric on the sample and no problems were encountered in terms of applicability. Considering the positive results obtained from the preliminary experiment, the samples were produced in accordance with their designs. A total of 16 samples were obtained. Two of these samples did not undergo any strengthening process and were chosen as the reference samples (R), whereas two of them were reinforced with 5 cm strip FRP composites only by surrounding them from the outside (RF). The remaining 12 samples were produced in four layers: one between the layers, and from bottom to top, with three (3F), five (5F), and seven (7F) layers, as shown in Fig. 5. Hybrid strengthening methods were developed for these samples using FRP strips and fabrics (3FF, 5FF, and 7FF). Subsequently, the load capacity, crack patterns, and damage patterns of the arch samples were determined. Additionally, in wooden arches, CFRP fabrics were first placed in the tension zone, which is the lower zone, and then applied to the upper zones. The tape strips were placed 15 cm away from the cutting forces and served as stirrups.
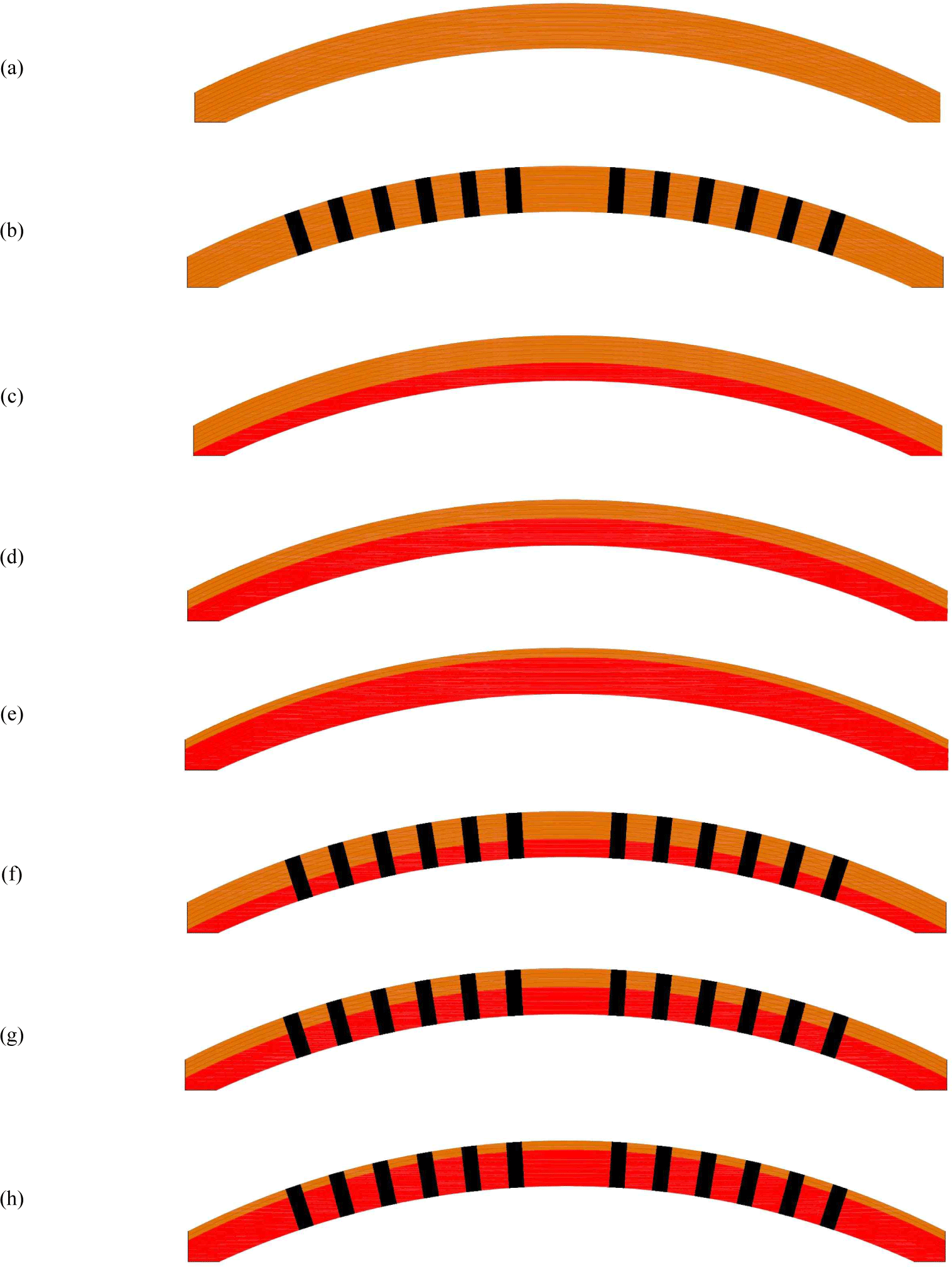
The cross sections of the laminated wood elements used to span wide openings vary depending on the aperture and element geometry. In particular, the cross sections of laminated wood elements used in wide openings can be large, which is undesirable from both architectural and technical standpoints. With the development of technology, it is now possible to reduce these undesired large sections or achieve superior mechanical properties within the same section. The novel aspect of this study lies in the application of the method used in beams to arch elements, aiming to leverage both the advantages of arch geometry and the benefits of laminated wood elements reinforced with FRP composites, thereby achieving significantly enhanced mechanical properties compared to rectangular beams. The innovative feature of this arch design is the use of strips obtained from wrapped CFRP fabrics instead of the metal band elements present in the model, with the aim of achieving mechanical properties far superior to those of metal. This material is five times lighter than traditional steel materials (Choudhari and Kakhandki, 2020), and its strength is ten times higher (Fang et al., 2021).
To examine the bending test behavior of the laminated wooden arch elements, LVDTs were placed at three different points and load-deformation graphs were plotted using data obtained from the loading device. The wooden arch specimen underwent a three-point bending test, and load-displacement curves were generated. A hydraulic jack and 60-ton calibrated load cell were used for the bending test. The data were automatically recorded using a system operating at a rate of 2 Hz. Two rubber bearings were positioned under the three points of load application to prevent damage to the sample and two LVDTs were placed at the midspan of the timber arch specimen to determine the free midspan displacement. The displacements in the test samples were measured using electronic rulers called LVDTs, which provided precise measurements with an accuracy of 0.01 mm. To calibrate this process, a fixed vertical line was established on the LVDT and its accuracy was verified through a calibration test. The applied loads were recorded using a data logger equipped with a load cell and the calculations were performed based on the accumulated data and displacements (Fig. 6).
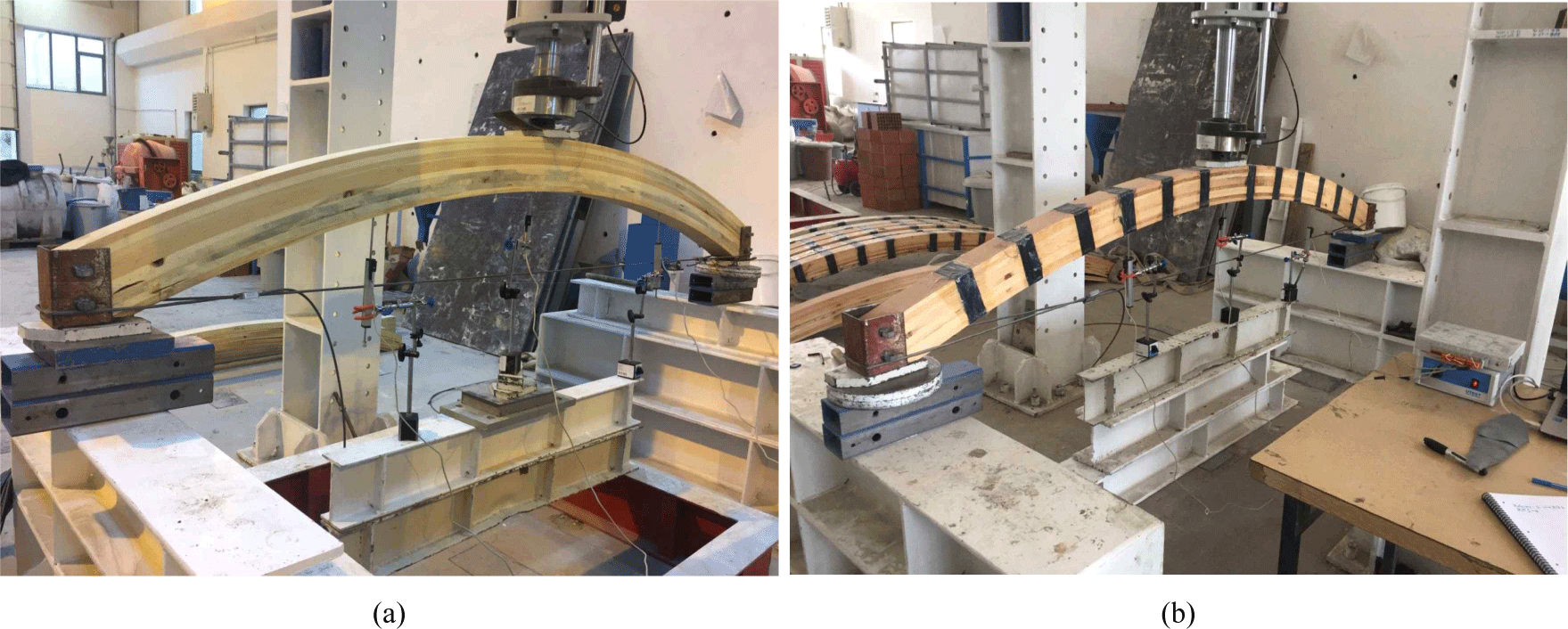
The ductility index of the specimens refers to the capacity of the structural elements to withstand inelastic deformation within their load-carrying capacity before failure. Specifically, the ductility index is defined as the ratio of the mid-span deflection at the yield limit (Δy) to the mid-span deflection at ultimate load (Δu). Maras and Kantarcı (2021) proposed a ductility index as follows:
3. RESULTS and DISCUSSION
Arch elements made of wood were subjected to a three-point bending test from the center point. As a result of the loads applied from the center point of the elements produced as flat arch specimens, unwanted tensile stresses were observed to occur in the elements. The types and sizes of the fractures resulting from these stresses were investigated and the test results were presented. Four reference samples were produced and two samples were selected for each category, with the average of the samples reported. For this purpose, two preliminary test samples were produced and their applicability was tested (R-1). The structural behaviors of the other two samples under loading were then determined (R-2). The structural behavior and ductility of the wooden arches were determined using a loading system. In Fig. 7, the load-deflection curve of the reference laminated arches is shown. The experimental findings showed that the normal laminated timber arch (R-1) specimen reached a maximum load of 14 kN and exhibited a deflection of 42 mm. In reference sample number two (R-2), the load increased smoothly to 18 kN under three-point loading. After reaching a maximum load of 27 kN, it rapidly decreased at the peak, leading to a sudden collapse. Šmídová et al. (2022) subjected various combinations of arch elements made of laminated wood materials to bending-load tests. Loads were applied to different parts of the arch elements and their load-carrying capacities, damage patterns, and areas of damage were determined. Due to the natural structure, fiber twist, heterogeneity, and the anisotropic nature of wood materials (Brol and Wdowiak-Postulak, 2019; García et al., 2012), regular inspection of structural elements and the development of appropriate strengthening methods should be provided to ensure continuous use (Corradi et al., 2017; Gilfillan et al., 2003).
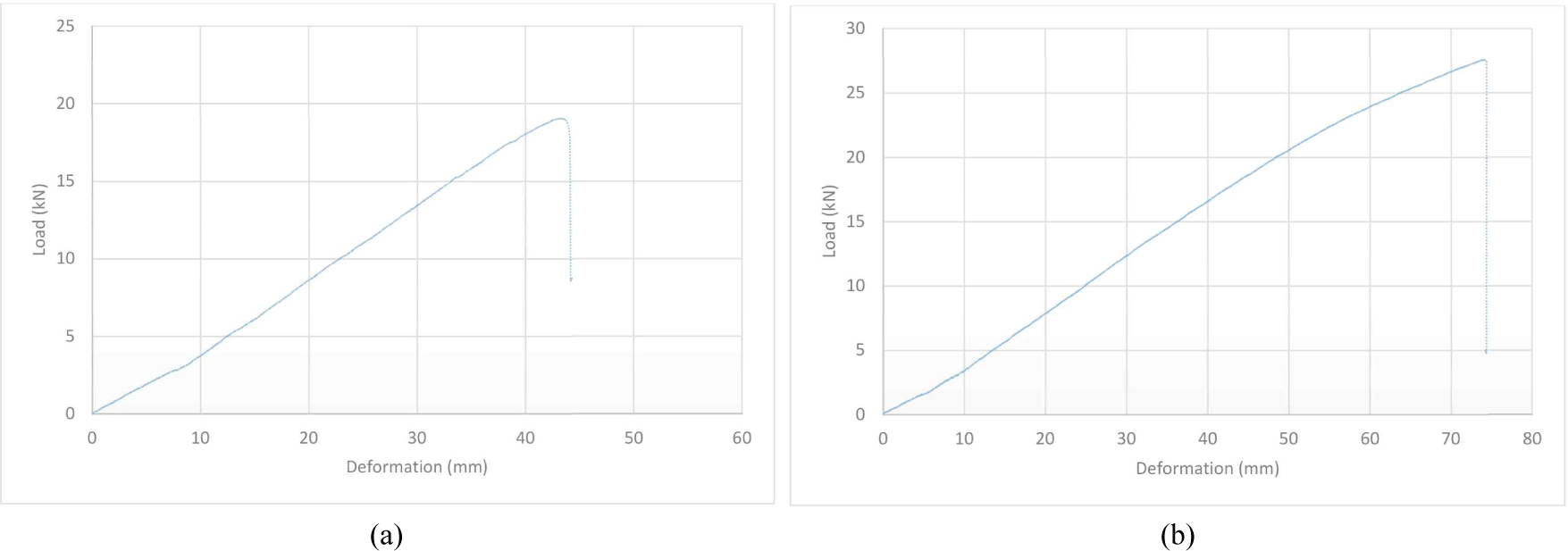
Owing to the maintenance and protection requirements of wooden materials, CFRP strip tapes in the form of stirrups are used to enhance the shear strength against external forces. In this study, glued wooden arches were subjected to three-point bending tests using CFRP strips applied to different regions at different locations. The ultimate load capacity, displacement, and ductility behaviors of the arch elements under the loading system were obtained and interpreted. Fig. 8 shows the load-deflection curves of CFRP strip-reinforced laminated arches with different variations. The wooden arch specimen (RF-1) reinforced with FRP strips reached a maximum load of 31 kN and exhibited a deformation of 92 mm. In a similar study, Zhou et al. (2020) stated that defective areas in wood structures were reinforced with FRP composite materials, resulting in positive mechanical changes. Novosel et al. (2021) placed FRP composite materials in the tensile zones of laminated wooden elements, resulting in significant increases in load-carrying capacities without any damage to the applied areas in different combinations. Owing to the lightness of the carrier elements and FRP composites in wooden systems, they are convenient for manufacturing and assembly (Astrom, 2018; Mara, 2011). The wooden arch sample reinforced with CFRP bands (RF-2), on the other hand, reached the maximum load at a 23.8 kN load and then decreased; however, the strip bands that acted as stirrups continued to load and exhibited ductile behavior by undergoing a displacement of 158 mm. The laminated wood arch sample (RF-2) reinforced with CFRP strips showed a 70% load increase and 276% deformation increase compared with the reference sample. Load-bearing systems preserve their integrity by repairing and reinforcing wooden elements with FRP composites, in which aging occurs for physical and functional reasons, and the bearing capacity becomes insufficient during the usage period (Barbero et al., 1994; Wan et al., 2014). Examination of the results obtained from the completed tests revealed that the reinforced specimens exhibited a large increase in strength and strain capacity at certain levels. Several researchers have stated that these positive contributions to the mechanical properties of the samples (Bakalarz, 2021), the reinforcements made with FRP composites on laminated wood structural elements, increase the energy absorption capacity of the elements to extremely high levels (Bakalarz and Kossakowski, 2022; Kim and Harries, 2010).
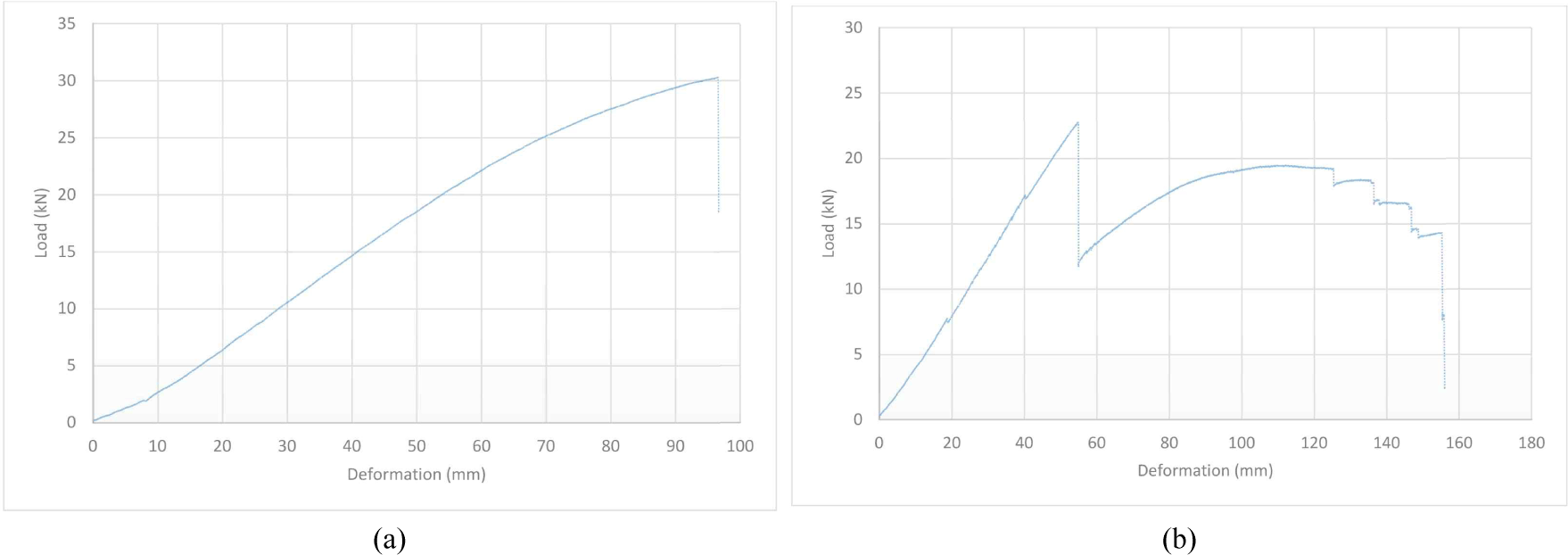
Arch elements made of laminated wood were reinforced with FRP composites by placing them in different regions between the layers and shapes. The produced samples were subjected to bending tests in the laboratory and the mechanical changes in the elements were determined. The wooden structural elements reinforced with CFRP in three layers reached a load of 20.8 kN under the loading system and exhibited a displacement of 202 mm (Fig. 9). Additionally, owing to their lightweight nature, they perform well against external forces and their use is becoming widespread (Kawecki, 2021). In studies carried out, several researchers found CFRP material to be effective in strengthening these structural elements (Socha et al., 2021). Wooden arches reinforced with CFRP placed between five layers reached a load of approximately 14 kN and exhibited high ductility and energy absorption capacity when displaced by 227 mm. Research on this application, called the interlayer FRP application, has shown that this method causes significant increases in the load capacity and ductility index values of the elements (Khelifa et al., 2014; Zhou et al., 2015). The sample with CFRP placed on all layers reached a load of 22.2 kN and a displacement of 175 mm. The wooden arches reinforced with CFRP placed between the seven layers exhibited a higher load-carrying capacity than the specimens placed in other layers. Additionally, the five-layer reinforced laminated wood arches exhibited higher toughness and ductility than the other samples. In a rigid arch system, the greater the load on the arch, the closer the arch will be to the curve of the specimen, and the more rigid it becomes under steady compression (Niu et al., 2018). The loads applied to the rigid and elastic chains were assumed balanced (Xanthakos, 1994). When uneven loads are applied, the geometric shapes of the arch and chain structures become distorted and unstable. This causes unwanted tensile stresses in the arch structure, eventually leading to its collapse (Conde et al., 2016; Milani and Valente, 2015). According to the obtained data, extremely high ductility and toughness increases were observed in the specimens reinforced with FRP composites and wide crack formation was prevented.
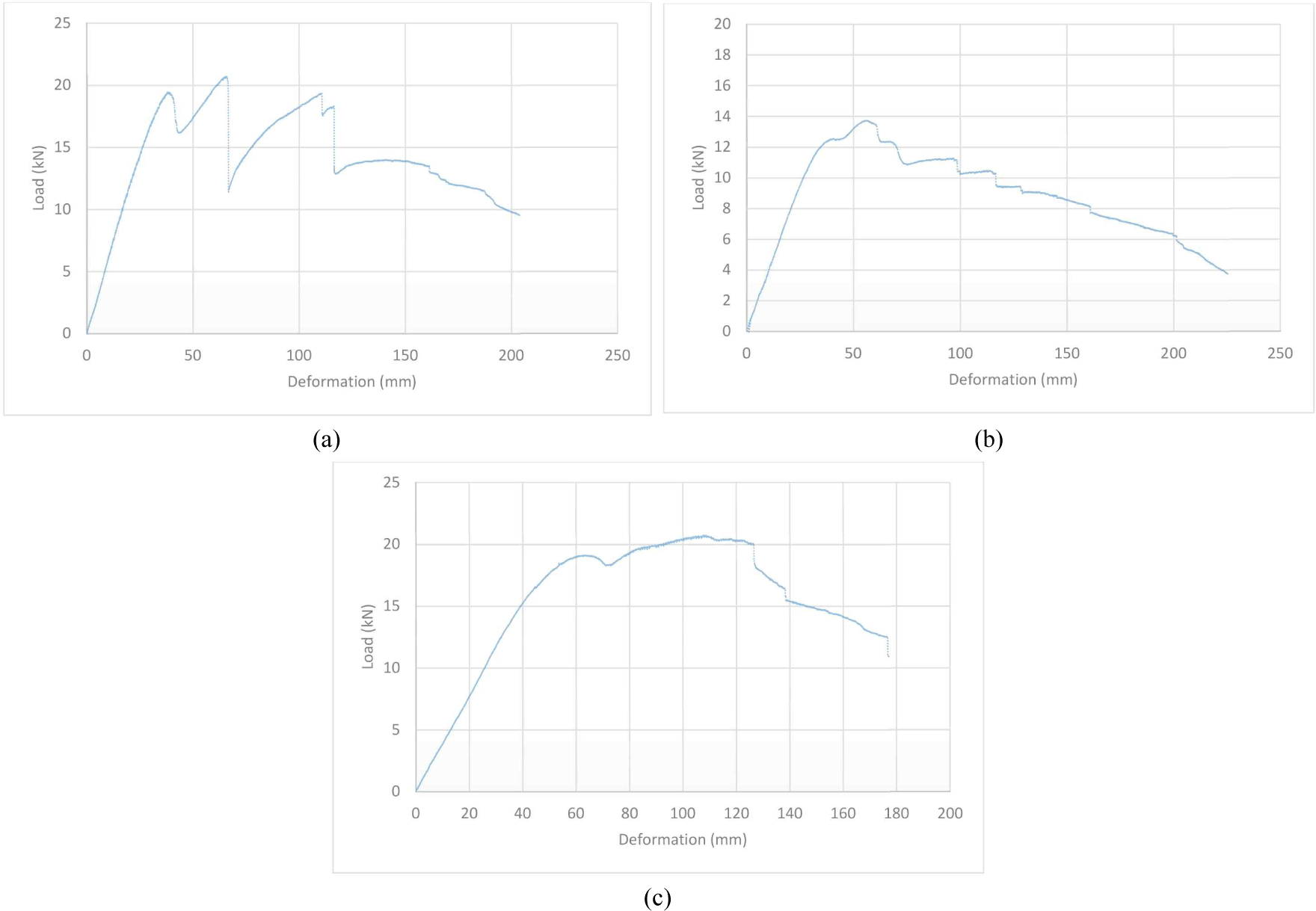
These designed elements were produced using the laminated wood method, an interlayer FRP application, and an innovative hybrid reinforcement method with strip tapes. The load-bearing capacities and ductility properties of the hybrid-reinforced wooden arches with CFRP were compared. A three-layer hybrid-reinforced wood arch specimen (3FF) exhibited an ultimate load-bearing capacity of 32 kN and a deformation of 117 mm (Fig. 10). The five-layer hybrid-reinforced wooden arch specimen (5FF) exhibited a similar load-carrying capacity; however, it increased the displacement by 61% by demonstrating high ductility and toughness. FRP reinforcement is important for enhancing these properties (Johnsson et al., 2007; Lopez-Anido and Xu, 2002). The use of these materials in the design reduces both defects and cross-sections in large-span systems. The hybrid-reinforced wooden arch specimen (7FF) with seven layers of CFRP exhibited more ductile behavior than the other reinforced specimens and had the highest displacement. During production of these structural elements, using them in different combinations and regions before lamination is crucial (Micelli, 2005; Raftery and Harte, 2011; Yang et al., 2013). One of the parameters is to alter the number of wooden plates used in the production of laminated timber elements with separate cross sections. The other parameter involves the frequency of the FRP composite material placed between the laminated wood elements and the variation in the region in which it is placed. Owing to the application of these parameters, the mechanical properties of the elements were improved and the test results are presented in detail.
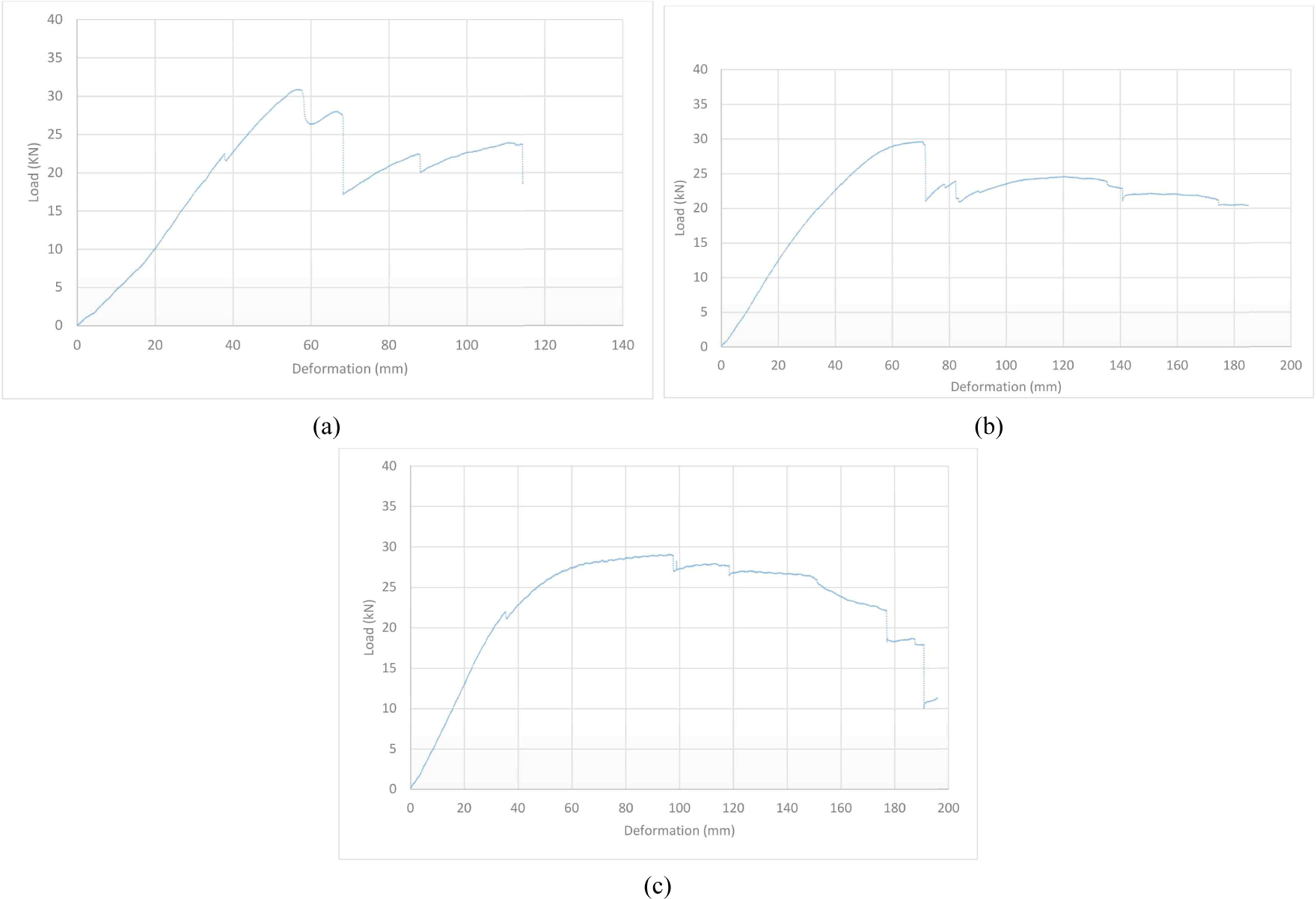
The data obtained from the tests were analyzed and the mechanical changes in the arch element based on the reinforcement applications applied in different combinations are presented below. The impact of CFRP placed between laminated woods on unwrapped wooden arch samples was assessed. Higher deformations were observed in these samples as the number of fabric layers increased. The highest energy absorption and toughness were achieved with the seven-layer CFRP fabric sample, whereas the load-carrying capacities were comparable. Wood building materials reinforced with CFRP offer long-term use with high durability and low dead weight. It has been emphasized that selecting the appropriate reinforcement method for these wood materials provides an optimal structural static solution (Ribeiro et al., 2009; Rubino et al., 2020) and is advantageous for easy and fast assembly processes (Lu et al., 2015).
The application of FRP in wooden structures has enhanced the load-bearing capacity and rigidity, proving to be a viable alternative for both new designs and reinforcements (Saad and Lengyel, 2022). Conversely, the CFRP-wrapped wooden arch samples exhibited higher ductility as the number of composites applied between the layers increased. The application of carbon fiber fabrics to each layer resulted in high toughness and prevented damage to the wooden elements and formation of cracks. In areas where CFRP was not applied between the upper layers, cracks were initiated in the upper layers, and the damage was contained by not propagating from the carbon fiber composite layers to the lower layers. FRP composites are favored for their cost-effectiveness in repairing damaged wood-building materials rather than replacing them entirely. Researchers have noted that FRP composite materials offer numerous advantages, such as high strength, modulus of elasticity, and corrosion resistance (Das and Nizam, 2014; Jian et al., 2022). Similar studies have shown that FRP tape strips significantly enhance the tensile stress of wooden elements under loading, thereby directly contributing to the yielding behavior of the fibers and the bending capacity (Fig. 11; Solarov and Glišić, 2014; Vahedian et al., 2017).
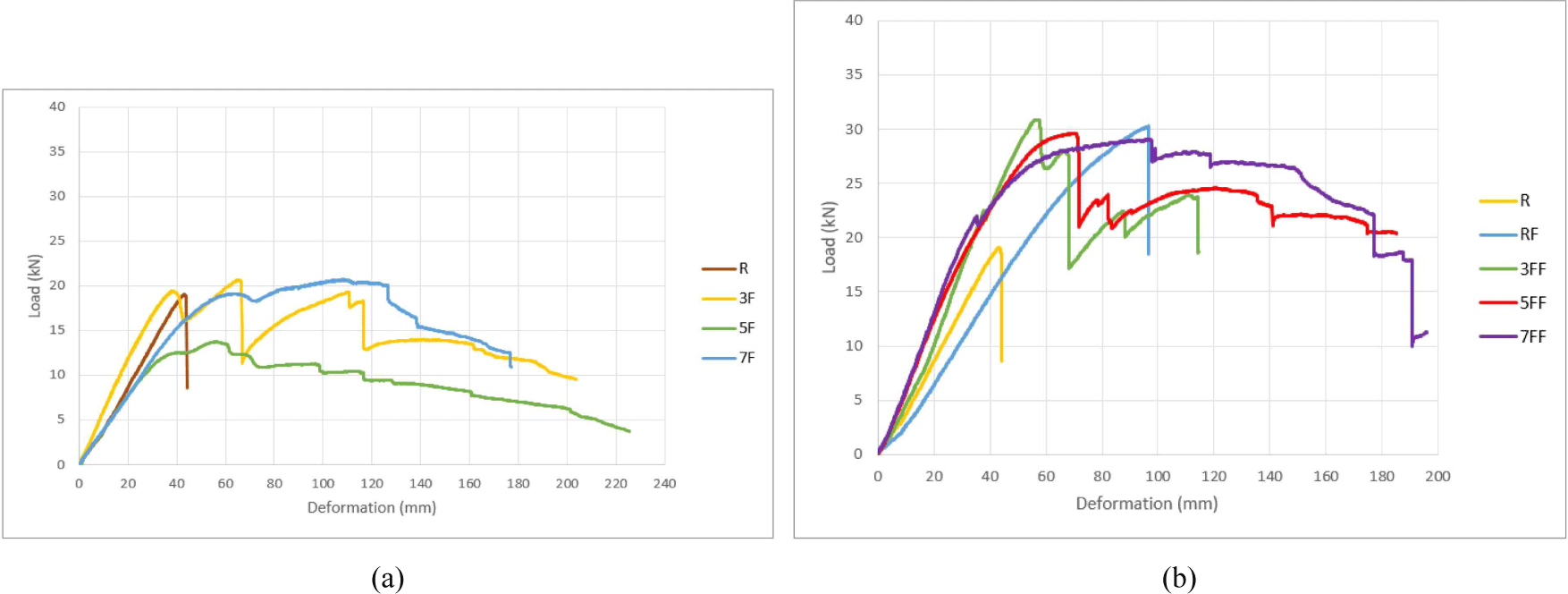
The typical failure modes and damage patterns of the wooden arches under bending loading were determined (Table 3). Cracks in unreinforced laminated-wood arches are formed at the finger joints, which are the weakest parts of solid wood. When these areas do not provide sufficient adherence, cracks initiate from the top layer, where the load is applied, and propagate toward the bottom layer, resulting in damage. Finger joints are widely used in the production of glued laminated wood elements. Owing to the loading on the wooden arch elements, the lamella was observed to be finger-jointed in the middle of the arch (Fig. 12) to achieve the maximum bending moment. The failure of the adhesion line caused by the loss of adhesion in the finger joints under the effect of the load occurred in the middle region of the belt. One of the major disadvantages of wood is its tendency to deform over time, which leads to the formation of wide cracks and other defects (Franke and Quenneville, 2014).
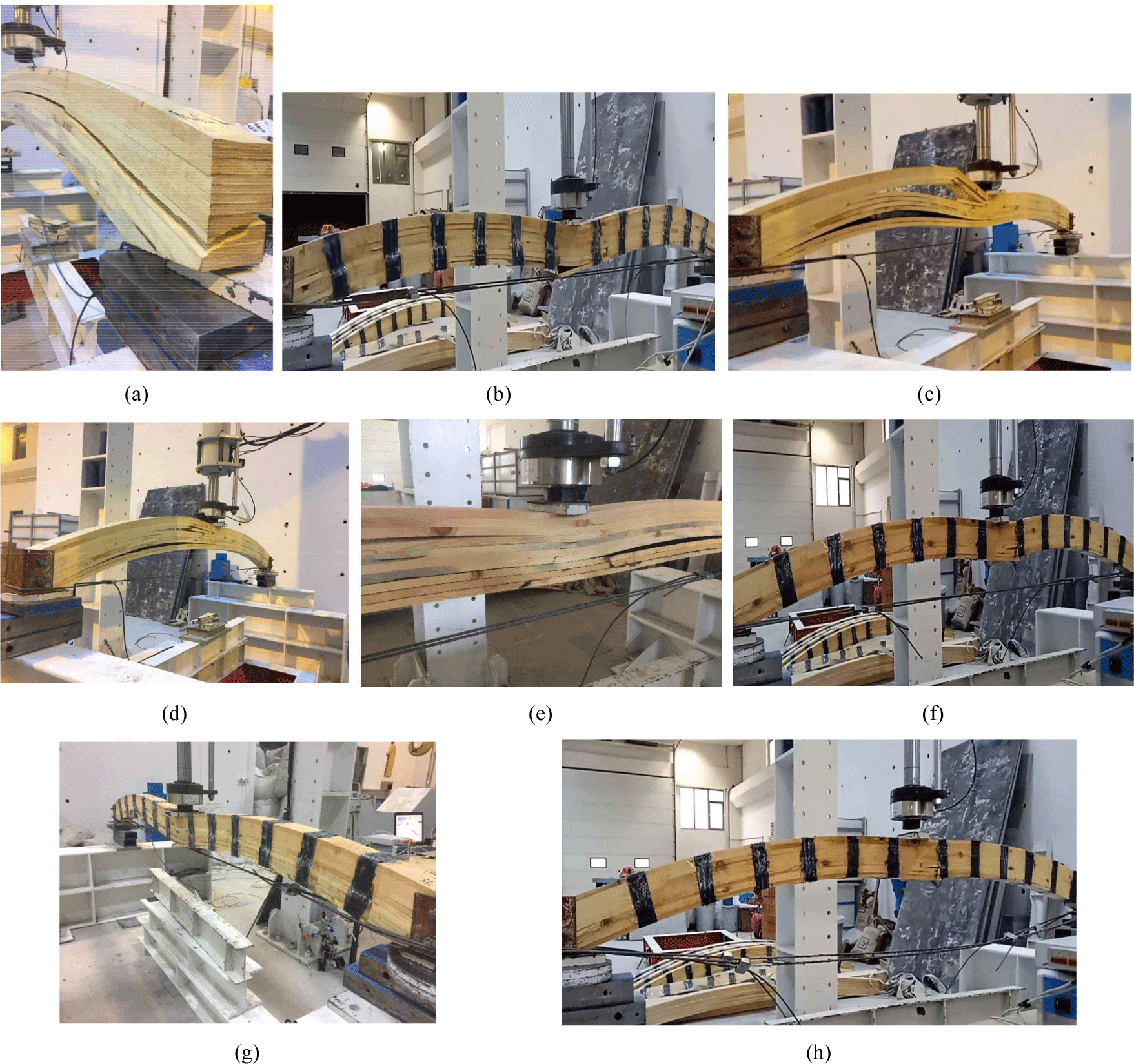
In the samples reinforced with the FRP composite between layers, the fabric reached the applied areas; however, crack development was prevented before reaching the layer areas applied in the lamination process. This resulted in a higher deformation capacity under the loading system and exhibited a higher energy absorption and ductility index. Although the samples with the CFRP fabric placed between the layers in the lower region prevented crack formation under the effect of the load, they were less effective than the other methods. The CFRP fabrics placed throughout the entire layer contributed significantly more than the other samples. CFRP composites play an important role in preventing the failure of reinforced wood elements (Ajdukiewicz et al., 2000; Nowak et al., 2013). Reinforcement sample 5F, which was placed in five layers, had a greater impact than sample 3F; however, its strength and toughness were lower than sample 7F. Similarly, reinforced wooden arches between the layers exhibited high ductility as the flexural strength and joint width increased (Raftery et al., 2009).
When assessing the damage conditions of the reference samples, the most critical points were the junctions of the wood during lamination, where openings occurred. The CFRP fabric placed between them prevented cracks from propagating to the lower layers, thereby preventing damage. Initially, the CFRP fabrics were applied to the lower surface of the wood in the tensile zone without wrapping the fabric and then placed in the pressure zone to determine their structural behavior. CFRP, with its high permeability on the wooden arch element, can be easily applied to the other surface, providing strong adherence.
The wooden arches reinforced with strip tape prevented cracks from expanding and ensured that shear cracks did not gradually form up to the loading point. The crack propagation process in wooden arches varied depending on the cross-sectional dimensions and applied region. These wooden structural elements, which exhibit high toughness, contribute significantly by demonstrating ductile behavior under the loading system. Similarly, when evaluating the effectiveness of reinforcement techniques with CFRP strips, the strips showed a higher load-carrying capacity and toughness when applied vertically in the lower region of their usage degree (Dempsey and Scott, 2006; Gilfillan et al., 2003). Examining the fatigue performance and creep behavior of CFRP-reinforced wood members is crucial (Jacob and Barragán, 2010).
4. CONCLUSIONS
In this study, CFRP fabrics were positioned between wooden layers before the lamination process, and their structural performance was assessed.
- The wooden arch sample reinforced with CFRP bands (RF-2) reached its maximum load of 23.8 kN, after which the load decreased. However, the strip bands, which functioned as stirrups, continued to bear the load and exhibited ductile behavior by displacing 158 mm.
- The investigated parameters included a 0.5% carbon fiber volumetric ratio of the transverse CFRP reinforcement, which resulted in a more than two-fold increase in the strength ratios.
- Wooden arches reinforced with CFRP placed between seven layers demonstrated a higher load-carrying capacity than specimens reinforced in other layers.
- The five-layer hybrid-reinforced wooden arch sample (5FF) exhibited a similar load-carrying capacity. However, it increased displacement by 61%, indicating high ductility and toughness.
- In the samples reinforced with FRP composites between layers, the fabric reached the applied areas, effectively preventing crack development before reaching the layer areas subjected to the lamination process.