1. INTRODUCTION
Diffusion within wood involves the passage of water, nutrients, and diverse substances through its intricate cellular structure. Timber consists of numerous pores, which serve as small channels that enable the movement of water and other substances. Nevertheless, it is essential to highlight that when the moisture content (MC) within wood surpasses 20%, it experiences a notable rise in vulnerability to insect infestations and fungal attacks (van Meel et al., 2011). Wooden structures are widely used, particularly in earthquake zones, owing to their light weight, ease of application, and resistance to the external environment. Wood, an environmentally friendly and sustainable building element, will be more economical and safer than the current reinforced concrete and steel elements (Ozdemir et al., 2023). Water diffusion plays a vital role in the sustenance and glowing of living trees by facilitating the transport of essential nutrients and minerals throughout the plant (Chen et al., 2020; Jakes, 2019; Utsumi et al., 1998). The diffusion process within wood is subject to numerous factors, including wood species, pore size and shape, temperature, humidity, and pressure. Gaining a comprehensive understanding of the principles underlying diffusion in wood holds significance across diverse disciplines, such as forestry, woodworking, and engineering, due to its potential impact on the properties and functionality of wood products (Burr and Stamm, 1947).
Franke et al. (2016) conducted a study examining the hygroscopic behavior of wood and the resulting changes in its physical and mechanical properties, specifically in the glue lines of glulam and block-glued cross sections. Similarly, Mannes et al. (2014) focused on investigating the absorption and diffusion of moisture behavior of traditionally significant adhesives with gluten as the base material, such as fish glue, hide glue, and bone glue. Fundamental differences between the adhesives that had gluten as the analysis of absorption isotherms on specimens determined the base material and the artificial adhesives such as polyurethane (PUR).
Neutron radiography, a method for measuring and localizing water inside the wood sample, evaluates how moisture moves (Mannes et al., 2009). Compared with previously published research utilizing neutron scans, Mannes’s article showed an upgraded method for measuring and localizing water inside the wood sample. Nonzero starting moisture rates were allowed and accounted for any improvement or changes in specimen morphology brought by swelling or shrinking, allowing for a description of the diffusion process inside the glue layer. The neutron imaging-derived diffusion coefficients were characterized as part of a theoretical model that accounts for the glue line microstructure. The gluten-based adhesive had larger diffusion coefficient values than the PUR adhesive; this difference was not reflected in the sorption measurement. This was due to excessive penetration of the adhesive materials inside the wood with the fiber direction. It prevents an adhesive layer formation, and the reason for this phenomenon can be traced to the wood surface roughness, causing significant localized tensions, resulting in tracheid bending and distortion. Csiha and Gurau (2011) found that wood surface roughness (resulting both from manufacturing processes and anatomical structure) and adhesive penetration are interrelated and dependent on wood species.
The diffusion characteristics of bonded wood samples are assessed through sorption experiments following the specification standard (International Organization for Standardization, 2016). These experiments involve dry cup/wet cup setups. It is well-established that gluten-based adhesives exhibit greater moisture absorption compared to other types of adhesives, and they also demonstrate higher diffusion coefficients (Mannes et al., 2012).
In their study, Dietsch et al. (2015) examined various commonly used methods for determining wood MC and assessed their suitability for monitoring purposes. Their research revealed an additional consequence of changes in wood MC, namely, the resultant shrinkage or swelling of the material. High MC in wood can create favorable conditions for fungal decay or growth. As a result, accurately estimating the MC of timber and taking appropriate measures in response are critical tasks in planning, constructing, and maintaining buildings constructed with wood or wood-based products.
Sonderegger et al. (2010) conducted a study on water diffusion through the Norway spruce sample, which contained more than one layer exposed to varying climatic conditions (dry side / wet side). This study utilized neutron imaging to examine the impact of different adhesives on the diffusion process. Neutron radiography was used to detect the water content within wood. Various adhesives were investigated, including polyvinyl acetate (PVA), urea-formaldehyde resin, epoxy resin, and one-component PUR. The number of layers in the samples and the thickness of the adhesive were varied. The time-dependent water profiles in the diffusion direction were measured utilizing neutron transmission imaging.
Fick’s second law was used to compute the diffusion coefficients for radial and axial water transportation in spruce wood and the adhesive joints while accounting for MC. This article explores the diffusion coefficients of (one-component PUR, epoxy resin) adhesive at high MC levels lower than three times the magnitude of that diffusion coefficient in spruce wood. On the other hand, a lower barrier effect appears compared with wood in PVA and urea-formaldehyde resin. The advantage of this non-destructive method is its high sensitivity to hydrogen, allowing visualization of time-dependent water diffusion processes in wood. Recently, several investigations with neutron radiography were carried out to analyze the capillary water absorption by partial immersion of wood specimens into water. Mannes et al. (2009) demonstrated that even small amounts of water absorbed from air moisture can be detected and quantified. Understanding moisture diffusion through solid wood has a significant role in wood drying. Still, it is also crucial from the point of view of internal stresses, especially in the case of adhesive-bonded structural wood products. The adhesive layer may act as a barrier to moisture diffusion, causing stresses on the sides of the bond line. The internal stresses weaken the performance of a structural adhesive wood bond. This review is a resource for enhancing our understanding of water vapor diffusion through wood adhesive layers. It provides insights that have implications for reducing stresses in bonded wood assemblies and the performance of the bonded assembly over time. Furthermore, knowledge gaps are identified to establish the basis for investigating the diffusion property of cross laminated timber (CLT) panels.
2. WATER in WOOD
Within the wood, water is present in two distinct locations: the cell walls and the porous macro-void structure of the material, as illustrated in Fig. 1. The water molecules residing within the cell walls are commonly known as “cell wall water” or “bound water” because of their close association with the polymers constituting the cell walls (Thybring et al., 2022). Cell Wall Water: the water particles found inside the wood cells in nano-voids also interact with cellulose, hemicelluloses, and lignin by hydrogen bonds with hydroxyl chemical groups [OH] (Lindh et al., 2017; Matthews et al., 2006). While cellulose possesses a large concentration of [OH] (Engelund et al., 2013; Thybring et al., 2017), hemicelluloses (one of the cell wall constituents) are the most responsible for bonding hydrogen with water. This occurs because a high amount of hydroxyl groups in cellulose prevents water particle penetration in optimum environmental conditions (Fredriksson, 2019; Hofstetter et al., 2006; Salmén and Bergström, 2009). Capillary Water: This type of water is found in the void structure of wood. The water particles enter the wood body through capillary action or capillary condensation. Capillary condensation refers to the mechanism by which water vapor can undergo condensation in tiny empty spaces, even when the relative humidity (RH) levels are below 100% (Thomson, 1871). The occurrence of capillary condensation is influenced by the size and shape of the voids and also by the RH at which it takes place (Sing et al., 2014). The MC of adhesive-bonded wood elements may be a source of internal stress.
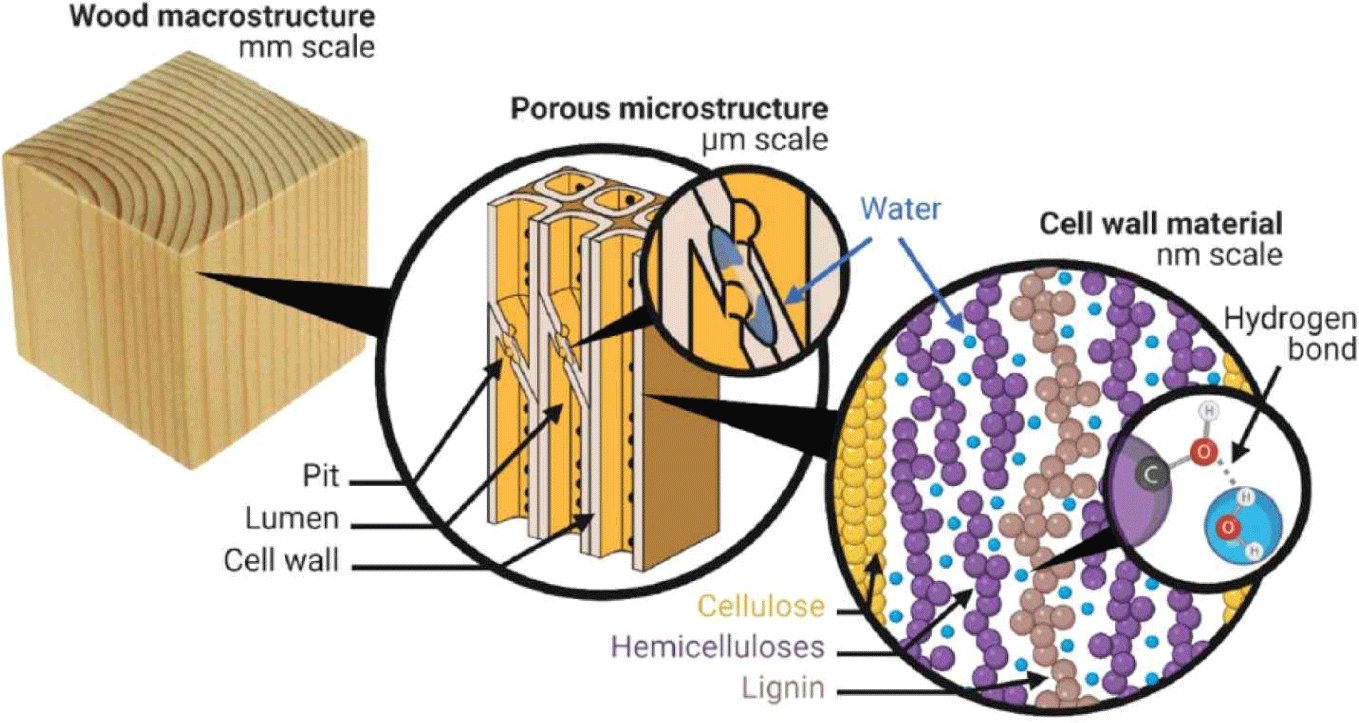
Water diffusion in wood occurs through various pathways depending on the location of water particles within the wood structure. Water transportation in wood can be categorized into three main mechanisms: water vapor diffusion, diffusion through the cell walls, and capillary water transport. The diffusion involves mass movement due to random molecular motions and can occur in the vapor phase and within the wood cell walls. In the hygroscopic range and at a constant temperature, the overall diffusion of water through wood can be mathematically described by considering the gradient in various assumed potentials, including concentration, MC, vapor pressure, RH, chemical potential, osmotic pressure, and spreading pressure (Siau, 1984; Skaar, 1988). Fick’s law is commonly used to explain water transport through diffusion (Fick, 1855).
The evaluation of diffusion through the wood was done using a method following the description of (Mannes et al., 2009). The type of mathematical equation is a second-order partial differential equation laying on Fick’s second law. This law was adjusted to calculate the diffusion coefficient depending on MC.
C: MC.
t: Time.
x: Moisture transport.
D: Diffusion coefficient.
D0: Diffusion at (MC = 0) oven dry status.
α: Constant dependent on moisture.
It was assumed that the transition from wood to adhesive occurs smoothly. In contrast, the disparity in diffusion coefficients between wood and adhesive expands by approximately three orders of magnitude as the MC increases. The authors pointed out that the examined adhesives in this study exhibit distinct diffusion coefficients. Additionally, the thickness of the adhesive layer (bond line) has a minor impact, with the diffusion coefficients increasing as the thickness increases.
Olek and Weres (2007) investigation propose a novel approach to determining wood’s bound water diffusion coefficient by solving the inverse diffusion problem. It introduces an improved algorithm for optimizing the constrained conditions and suggests an alternative submodule to capture the relationship between the diffusion coefficient and bound water content. The study focuses on identifying the diffusion coefficient for Scots pine wood using this inverse modeling approach. By comparing the accuracy of diffusion predictions obtained from traditional sorption methods and the inverse modeling approach, the research highlights the value of the inverse process in getting precise data on the bound water diffusion coefficient and boundary condition. The results indicate that the initial sorption method could be more suitable for accurately identifying the diffusion coefficient in wood, and adjustments to boundary conditions are necessary. While applying the convective boundary condition does not significantly enhance accuracy, the best agreement between diffusion modeling and experimental results is achieved through the proposed inverse identification method with the specific submodel. However, the study suggests that further improvements can be made by considering the coupling between diffusion and heat transfer and refining the submodel that describes the diffusion coefficient’s dependence on water content. Ultimately, these findings contribute to advancing the accuracy of mass transfer modeling in wood drying processes (Olek and Weres, 2007).
Wood’s water diffusion affects timber’s MC and drying processes. Recently, it was investigated by Thybring et al. (2022). The review provides a comprehensive overview of our current understanding of the basic principles of water within wood while emphasizing significant gaps in knowledge. The review encompasses various aspects, including water distribution in wood, phase changes, and equilibrium states of water within the material. It delves into the thermodynamics of sorption, relevant terminology such as cell wall water (bound water), capillary water (free water), fiber saturation point (FSP), and maximum cell wall MC. Additionally, it explores phenomena such as shrinkage and swelling, sorption hysteresis, water transport within the wood, and the kinetics of water vapor sorption within the cell wall.
The Thybring studies describe the current understanding of moisture diffusion in solid wood based on available data from experimental and computational methods and state that this research field is in continuous development. The study doesn’t cover the diffusion characteristics of coated or bonded wood surfaces.
There are various adherent and adhesive types and different processes to bond materials. Nowadays, wood adhesives are used in over 70% of wood products worldwide. This widespread usage can be attributed to their indispensable role in fastening furniture joints and facilitating the creation of wood composite materials (Gardner, 2017).
In the study conducted by Ülker (2016) the technical properties of various types of wood adhesives were examined. These included environment-friendly adhesives, semisynthetic adhesives, and synthetic adhesives. Furthermore, the article also discusses the penetration of wood adhesive materials. This aspect is explored in the section dedicated to the technical properties of wood adhesives. The penetration of adhesive into wood can be classified into two distinct groups:
-
Gross penetration: This type of penetration occurs when liquid resin flows into the porous structure of wood, primarily filling the cell lumens. Gross penetration can be attributed to hydrodynamic flow and capillary action.
-
Cell wall penetration: In this case, resin diffuses into the cell wall or flows into micro fissures within the wood structure.
Given that vessels in hardwoods lack pit membranes and are connected end-to-end with perforation plates, they play a significant role in the penetration of adhesives. This particular cell type tends to dominate adhesive penetration in hardwoods. Through optical microscopy, the author observed resin present in pit chambers of both hardwood and softwood species, as well as in cell lumens. Notably, the sole pathway for resin entry into these cells was through the pit structure (Song and Kim, 2022).
3. ADHESIVE TYPES for STRUCTURAL BONDING of WOOD
Various wood adhesives are available, each with unique properties and ideal applications. Natural polymer-based adhesives, such as gluten-based ones, fish glue, hide glue, and bone glue, have traditionally been widely employed in non-structural applications like furniture making, veneering, and instrument making. Casein-based resins do not have creep but have low water resistance. Only a limited number of adhesives are suitable for structural bonding with the general expectation to exhibit negligibly low or no creep and preferably high-water resistance. Emulsion polymer with isocyanate (EPI) PURs are frequently used in CLT production. Similar studies were done by Song and Kim (2022) on the effects of manufacturing in the environment on the bonding performance of CLT using a PUR adhesive; many other studies were also conducted on CLT and adhesive. Here are some of the most common structural types of wood adhesives and their general properties:
Phenol-Resorcinol-Formaldehyde (PRF) glue: RF glue is a two-part adhesive made from resorcinol and formaldehyde. It is known for its exceptional strength and is often used for bonding structural components in boats and aircraft (Schwandt and Gound, 2003).
Phenol formaldehyde (PF) glue is a type of adhesive commonly used as a wood glue synthetic polymer formed through the chemical reaction of phenol (an alcohol derived from benzene) with formaldehyde (derived from methane). These resins are renowned for their exceptional adhesive properties and find extensive application as wood adhesives, particularly in the construction industry. They are commonly employed in producing waterproof wood panels like plywood and oriented strand boards, making them indispensable for various construction-grade applications (Kaboorani and Riedl, 2011).
EPI glue is a highly effective adhesive for wood-to-wood bonding. It comprises two components: a water-based emulsion and a hardener. EPI glue formulations can vary, offering different combinations of emulsion and hardener. This adhesive is particularly suitable for wood with high MC. It finds wide applications for parquet adhesive, finger joint adhesive, and bonding wood panels. Moreover, EPI glue is suitable for doors, windows, wood veneer, and edge-glued panels, making it a versatile choice for various woodworking applications (Sandberg, 2016).
One-component PUR glue: curing these types of adhesives is initiated by the MC of the environment, most of all the water vapor of the environmental air. The bond is known for its good water resistance and is often used for outdoor applications (Kong et al., 2011).
The material components of each adhesive can vary depending on the specific type and manufacturer. However, common components include synthetic polymers.
In a study conducted by Sernek et al. (2008), the bonding performance of heat-treated wood using different adhesives was examined. The researchers utilized untreated wood, intermediate (hydro thermolysis) wood, and fully heat-treated wood, bonding them with melamine urea formaldehyde (MUF), PRF, and PUR adhesives. The results indicated that the shear strength and delamination of the laminated wood were influenced by the adhesive system employed and the degree of heat treatment. The PUR and MUF adhesives demonstrated similar performance, which was generally superior to the PRF adhesive. When bonded with MUF and PRF adhesives, the shear strength decreased for specimens made from hydro-thermolysis and fully heat-treated timber. However, the difference in shear strength between untreated, intermediate, and fully treated wood was less significant for the PUR adhesive. Delamination of the PRF bond line substantially decreased for all heat-treated specimens. Overall, the study revealed that the bonding performance of heat-treated wood depended on the adhesive system, with PUR and MUF adhesives meeting the requirements for Norway spruce and heat-treated poplar. The researchers recommended further investigation into improving the bonding performance of heat-treated wood, including modifications to adhesive composition and bonding processes, hardeners, solvents, and fillers.
4. WOOD ADHESION MECHANISMS
The mechanisms by which wood adhesives work can be broadly categorized into two groups: mechanical and chemical bonding.
Mechanical bonding mechanisms: Mechanical bonding mechanisms rely on the physical interlocking of adhesive molecules with the wood fibers to establish a mechanical bond. This bond is achieved through the penetration of the adhesive into the porous wood surface, resulting in a network of adhesive molecules that interlock with the wood fibers. Adhesives such as PVA glue commonly employ mechanical bonding mechanisms, enabling them to form robust and flexible bonds with wood, particularly for furniture bonding applications (Dunky, 2017).
Chemical bonding mechanisms: Adhesive bonding involves chemical mechanisms resulting from the reaction between the adhesive and the surface of the wood, leading to the formation of a robust bond. This bonding process is facilitated by the chemical interaction between the adhesive and specific functional groups found within the wood, like hydroxyl (-OH) groups. Various adhesive types, including one-component PUR, EPI, phenol-resorcinol-formaldehyde, and phenol-formaldehyde, utilize chemical bonding mechanisms to establish enduring and resilient connections with wood surfaces (Dunky, 2017).
Various factors, including adhesive type, wood species, MC, and temperature, influence wood adhesives’ performance in wet environments. The choice of adhesive type is critical, as different adhesives have different properties that affect their ability to resist water diffusion or to be used as structural adhesives. For example, PVA adhesives are commonly used in bonding non-structural wood-based products due to their selectable water resistance, high bonding strength, and low cost. Still, being subject to creep, they are not recommended for structural bonding of wood. PF adhesives, on the other hand, have excellent water resistance and structural strength. However, they require hot pressing, which limits their application for glulam production; thus, they are commonly used in exterior-grade plywood (Bomba et al., 2014).
Some species of wood, such as teak (Opoku, 2007) and IPE (Tabebuia sp.; Jankowska, 2017), have high natural resistance to water due to their high density and oil content. Other species, such as pine and fir, have a lower density and are more porous, making them more susceptible to water absorption. The amount of water a particular species of wood can absorb also varies. For example, hardwoods like oak and maple can absorb more water than softwoods like pine and cedar. This is because hardwoods have a more complex cellular structure, which allows them to hold more water. The diffusion of water through wood is influenced by factors such as temperature, humidity, and the type of wood. Some woods have a higher diffusion coefficient, meaning they can absorb water more quickly than others. For example, pine has a higher diffusion coefficient than oak, meaning it can absorb water more rapidly and to a greater extent (Jankowska, 2017). When selecting wood for outdoor projects, such as decks and fences, it is essential to understand the relationship between wood species and water diffusion. By choosing a wood species that is naturally resistant to water and with a low diffusion coefficient, you can help ensure that your project will withstand moisture exposure over time.
The MC of the wood also affects the performance of the adhesive. High MC can reduce the adhesive’s bonding strength and increase the water diffusion rate (Bekhta et al., 2015). The MC of the wood is also influenced by the RH and the environment’s temperature. For example, wood stored in a high-humidity climate will absorb moisture and have a higher MC than wood kept in a low-humidity environment.
The surrounding temperature influences the performance of water vapor diffusion through the adhesive layer. Higher temperatures can accelerate the rate of water diffusion, leading to faster degradation of the adhesive. Conversely, lower temperatures can slow water diffusion, increase brittleness, and reduce adhesive flexibility. Hence, temperature plays a crucial role in both the rate of water vapor diffusion and the overall durability and properties of the adhesive (Heshmati et al., 2016).
Kang and Arthur Hart (1997) conducted a study to examine the impact of drying temperature on the unsteady-state moisture diffusion process. In this experiment, small specimens measuring approximately 25 mm in thickness, made from yellow poplar and red oak, were dried at four different temperatures: 32.2°C, 43.3°C, 54.4°C, and 65.6°C. The drying process was carried out at two successive equilibrium MCs (10% and 5% EMC) to evaluate the effect of temperature on moisture diffusion. This research sheds light on the relationship between drying temperature and the moisture diffusion characteristics of the wood specimens.
The drying study of the effect of four levels of temperatures (from 32.2°C to 65.6°C) and two successive levels of equilibrium MC (10% and either 3% or 5%) on the diffusion coefficients and activation energies of yellow-poplar and red oak added major data on the drying of yellow-poplar. The linearity observed in the plots of the logarithm of the diffusion coefficient against the reciprocal of absolute temperature provides evidence that moisture diffusion through wood is an activated process. This finding suggests that temperature plays a crucial role in influencing the rate of moisture movement within the wood material.
Chiniforush et al. (2019) conducted a comprehensive investigation on the effects of glue lines, MC, and temperature on diffusion coefficients of various engineered wood products. The study involved measuring diffusion coefficients in three orthogonal directions for glued laminated timber (Glulam) made from Blackbutt (Eucalyptus pilularis), Pacific Teak (Tectona grandis), Tasmanian Oak (Eucalyptus regnans/oblique/delegates), Radiata Pine (Pinus radiata), Slash Pine (Pinus elliottii), as well as laminated veneer lumber (LVL) made from Radiata Pine and Cross Laminated Timber made from Norwegian Spruce (Picea abies). Specimens were prepared both with and without glue line, and the experiments were conducted at four different temperatures: 15°C, 25°C, 35°C, and 45°C, along with three different RH gradients. Adsorption isotherms were obtained, and analytical equations were fitted to the experimental data to determine the diffusion coefficient of wood as a function of temperature and MC. The findings demonstrated that the diffusion coefficient significantly depended on temperature and MC. This highlights the importance of considering these factors when modeling moisture transport, analyzing drying stresses, distortion, and warping, and conducting long-term serviceability assessments of timber elements.
The influence of temperature on moisture-induced shrinkage and swelling in the longitudinal direction was studied by Akbarnezhad et al. (2019). This investigation delved into the hygroscopic behavior of engineered timber, focusing on two distinct categories: a) glued-laminated timber comprising Pacific Teak, Tasmanian Oak, Blackbutt, Radiata Pine, and Slash Pine, and b) LVL constructed from Radiata Pine. The study entailed a comprehensive experimental regimen designed to scrutinize timber’s moisture-induced swelling and shrinkage at two distinct temperatures: 15°C and 50°C. The outcomes highlighted noteworthy distinctions in the swelling and shrinkage characteristics between extensive glued-laminated timber (glulam) and LVL specimens compared to their smaller clear wood counterparts. Furthermore, temperature significantly influenced the moisture-induced swelling and shrinkage of glulam and LVL beams in the transverse direction. Specifically, there was an observed decrease in the coefficient of moisture expansion and/or moisture contraction in the transverse direction with escalating temperatures. Increasing the temperature from 15°C to 50°C increased the coefficient of moisture expansion and coefficient of moisture contraction in the longitudinal (parallel to the grain) direction of the glulam and LVL. Moreover, engineered timber’s coefficient of moisture expansion and/or moisture contraction experienced a substantial drop (exceeding 90%) for MC alterations beyond the FSP. Temperature fluctuations demonstrated a limited impact on the MC at which the wood fibers attain full saturation in these specific engineered timber species. In contrast, the swelling and shrinkage coefficients in the longitudinal direction exhibited an opposing pattern.
Ganne-Chédeville et al. (2012) observed that the diffusion coefficient increases exponentially as temperature rises, with the effect of temperature being more pronounced in the longitudinal direction. Conversely, the longitudinal diffusion coefficient decreases exponentially with increasing MC, while the transverse diffusion coefficient follows the opposite trend. Furthermore, longitudinal to transverse diffusion coefficient ratios decrease exponentially as MC increases. These ratios are higher at higher temperatures and eventually converge to the same value with further increases in MC. At lower volumetric MC, the coefficient of diffusion in the longitudinal direction is approximately an order of magnitude greater than that in the transverse direction.
Coatings like adhesives can block or support water and water vapor diffusion since they are synthetic resin formulations. Contrary to adhesives, the water vapor and water resistance of coatings are well-researched. Coatings manufactured for outdoor applications, like lacquer, are formulated with molecule size adjusted conveniently to allow water vapor diffusion. Waterborne outdoor lacquer has rapidly become the majority of wood surface coatings (Han et al., 2022; Huang et al., 2022; Pan et al., 2022) due to their prolonged lifecycle and eco-friendly features (Qin and Yan, 2022; Xia et al., 2022; Yang et al., 2022). Considering their chemical structure, the majority of aqueous wood coatings are PURs (Panda et al., 2018). However, the physical and chemical properties of one-component PUR products, such as water resistance (Gunesoglu et al., 2017; Wang et al., 2020) and chemical resistance (Athawale and Nimbalkar, 2010; García-Pacios et al., 2013), are somewhat inferior to those of two-component products (Yin et al., 2017). de Meijer and Militz (2000) conducted a study on the sorption of liquid water in coated spruce. They examined the change in the overall MC of the wood over time and analyzed the MC profiles at different intervals. The study involved various outdoor coatings, including a solvent-borne alkyd coating and two waterborne acrylic coatings with varying layer thicknesses. Uncoated wood was used as a reference. The researchers analyzed the measured data using models based on capillary flow or constant and changing surface concentration diffusion. However, these diffusivities were inadequate in predicting the MC profiles in the coated wood, particularly near the surface where a significant increase in moistening was observed. The most accurate prediction of the MC profile was achieved by incorporating the changing surface concentration and the diffusion coefficient derived from the sorption data of uncoated wood. In general, diffusion was identified as the primary driving force influencing water transport in the wood. On the other hand, capillary flow had a noticeable impact on sorption only near the wood surface. This phenomenon was more significant for uncoated wood.
Sonderegger et al. (2015) conducted a research study to investigate the diffusion of water into spruce wood coated with an acrylate/PUR and a silica-based coating system. The humidity conditions varied during the experiment. Non-destructive neutron imaging techniques measured and analyzed MC. The results showed that the acrylate/PUR-based coating exhibited a stronger barrier effect against water diffusion than the silica-based coating. After ten days, the silica-based coating showed similar behavior to the uncoated reference, while the acrylate/PUR-based coating still displayed significant deceleration in sorption. Furthermore, the acrylate/PUR-based coating specimens demonstrated a strong barrier against water sorption into the wood throughout the entire measurement period, even when subjected to changing humidity conditions and direct water contact.
Despite the differences between coatings and adhesive materials, recent results indicate that PUR adhesives (specifically, those commonly used as structural adhesives for bonding CLT) may exhibit a similar water diffusion-blocking effect to some paints. Consequently, their water diffusion-blocking status also needs to be analyzed.
5. DIFFUSION of WATER VAPOR THROUGH the ADHESIVE MATERIAL
Structural adhesive material is used widely to make a mechanical link between joints or materials; it has advantageous properties according to the material that is the synthesis or based material types, but the major deficit in studies of this material through long-term behavior is the disadvantage of it (Heinrich, 2019; Kinloch, 1997). Water is the most frequently encountered harmful medium, and warm, damp environments significantly reduce adhesive junctions’ strength. The physicochemical changes at the interface (or interphase) between the substrate and adhesive may be responsible for the reduction in mechanical resistance caused by water infiltration (Gledhill and Kinloch, 1974; Sharpe, 1972).
Zanni-Deffarges and Shanahan (1995) conducted a classic gravimetric analysis on the diffusion of water into a bulk epoxy adhesive at 70°C under approximately 100% RH. They observed that as the diffusion progressed, the elastic modulus of the adhesive decreased. Similar effects were observed in torsional adhesive joints, but the phenomenon appeared to occur more rapidly. Since gravimetric analysis is not practical for bonded joints, a “composite” model was developed to estimate water ingress by analyzing changes in the overall elastic behavior of the polymer. The elastic moduli are influenced by the combination of rigidities resulting from the proportions of “wet” and “dry” polymer under load. The composite model provided values for the coefficient of diffusion, D, of the bulk adhesive that were in satisfactory agreement with those obtained through gravimetric analysis. However, the value of D for torsional joints was significantly higher. The researchers supposed that a phenomenon called “capillary diffusion” exacerbates water ingress. Surface tension effects near the metal (oxides) polymer interfacial region increase the effective driving force for water penetration.
Leger et al. (2010) tested industrial rubber-toughened epoxy adhesive to understand its diffusion behavior in water at different temperatures. Density measurements and gravimetric experiments were performed on bulk specimens at 25°C, 40°C, 60°C, and 70°C. The investigations revealed non-classical mass uptake and swelling phenomena. During aging, it was observed that the adhesive’s glass transition was surpassed, and cavities developed due to sorption. Some water diffused into the adhesive matrix, decreasing the adhesive’s glass transition temperature (Tg), while the remaining water entered the cavities. The study encompassed experimental work and phenomenological modeling to investigate water diffusion as a temperature function. The diffusion behavior exhibited non-classical characteristics at temperatures above 40°C, with significant water uptake. At a 5% uptake, the adhesive’s Tg decreased to 60°C, indicating a change in the physical state and diffusion kinetics during aging in water at 60°C and 70°C. The development of cavities was attributed to a cavitation phenomenon that occurred during aging, resulting in substantial water uptake. The swelling caused by water ingress was considered the most likely cause of the formation of these cavities.
Extensive research has been conducted by Huacuja-Sánchez et al. (2016) on the interaction of water with thermoplastic PUR, but the exploration in the case of PUR networks remains limited. In this study, a chemically simple yet well-defined PUR is employed as a starting point to investigate the influence of water on this type of polymer. During immersion in water for up to 15 days, no changes in the chemical composition of the PUR were observed in the infrared (IR) spectra. However, the water saturation in the PUR samples occurred earlier depending on the temperature. This saturation resulted in plasticization, as evidenced by a significant decrease in the mechanical modulus and a shift of the glass transition to lower temperatures in the polymer. Surprisingly, it was found that achieving approximately 70% water saturation was sufficient for maximum plasticization. The IR spectra analysis suggested that water weakens the interactions between polymer chains within the network. The hydrogen bonds originally present in the urethane groups are partially substituted by hydrogen bonds formed between water and the urethane moieties.
Various techniques have been developed for measuring water diffusion through wood adhesive layers. One commonly used technique is gravimetric analysis, which involves measuring the weight gain or loss of a sample of wood-based product over time as it is exposed to water. Another technique is nuclear magnetic resonance spectroscopy, which can be used to measure the distribution of water within the adhesive layer (Herbst and Goldstein, 1989; Tsushima et al., 2005). By acting as a barrier against liquid water (precipitation or dew) and water vapor diffusion, coatings slow the pace at which water is absorbed into the wood. This barrier also reduces the rate of water drying through the wood pieces. The optimum MC passing through the coating materials is variable, and the coating materials provide protective properties to the wood at low permeability. In contrast, there is the risk of fast moisture entry through a crack, open end-grain, or open corner joint in window frames (Ashton, 1979; Kuo and Hu, 1974). These cracks may cause wood decay when the surrounding wood MC exceeds 25%. On the contrary, a highly permeable coating can lead to rapid changes in MC and dimensional movements, resulting in issues such as jamming windows and doors, cracking in the coating or wood, and excessive stresses on glued structures. Therefore, determining the optimal moisture permeability is largely influenced by the type of wood used and its specific application. This distinction is also evident in European standards for exterior wood coatings, which classify end uses as stable, semi-stable, or non-stable (British Standards Institution, 1996). The humidity control of wood gently introduces significant fluctuations under the ambient RH into the slab, and fluctuations in the RH result in dimensional changes (Hwang et al., 2022). When it comes to wooden joinery and doors, the coating must have a certain level of impermeability to prevent excessive wood movement. However, as a result, water desorption from the wood will be slower. Avoiding excessive moisture uptake through the end grains is essential to address this. This can be achieved through proper protection, such as end-grain sealing, and ensuring secure window corner-joint gluing (Boxall et al., 1992; de Meijer, 2001; Miller and Boxall, 1984, 1987).
Avramidis et al. (2007) investigate the way of measuring diffusion water coefficient in wood, namely, the steady-state and unsteady-state methods.
A) The first method involves using a diffusion cup and a thin wood specimen tightly placed at the top of the cup, as illustrated in Fig. 2. The cup is partially filled with distilled water (achieving 100% RH) or a salt solution, and a magnetic stirrer is used to maintain a controlled RH at the bottom part of the specimen, which is lower than 100%. The cup and the attached specimen are placed in a conditioning chamber where the ambient temperature and RH are precisely controlled. The assembly will either gain or lose weight depending on the RH (or vapor pressure) inside and outside the cup. A steady-state condition is eventually reached by plotting the weight change over time, characterized by a linear relationship between weight change and time. The diffusion coefficient through the bulk wood (Dg) can then be calculated using the following formula (Siau, 1995).
Where:
m: Mass of water vapor transferred through the specimen (g).
L: Specimen thickness (m).
t: Time (sec.).
A: Surface area of specimen (m2).
G: Specific gravity of wood at _ X.
ρw: Normal density of water (kg/m3).
ΔM: Moisture difference between the two parallel surfaces of the specimen calculated from the sorption isotherm (%).
Where:
Mb: Bottom specimen surface MC%.
Mt: Top specimen surface MC%.

The unsteady-state method involves placing thin wood specimens in a controlled environment chamber with a constant temperature and RH. The specimens’ weight change and MC are monitored until equilibrium is reached. The initial MC of the specimen (Mt) is known. It can be higher or lower than the equilibrium MC (Memc), resulting in either water loss (desorption) or water gain (adsorption) by the specimen. Once the final MC (Mf) at equilibrium is reached, the dimensionless MC (E) changes are plotted against time. From the initial linear portion of the plot, the unsteady-state diffusion coefficient can be calculated using the analytical solution of Fick’s second law for parallel-sided specimens.
In each sorption step, the average MC (M) reported for the calculated diffusion coefficient is given by
The unsteady-state methods can be used in thick specimens in controlled environment chambers or very thin specimens (less than 1 mm) in diffusion columns suspended from quartz springs. It is important to note that specimen thickness can impact the calculated diffusion coefficients, as demonstrated by Avramidis and Siau (1987) and Chen et al. (1996).
Both methods have their advantages and limitations. In the steady-state method, minimizing potential vapor flow paths other than the specimen is crucial. In the unsteady-state method, preventing specimen exposure to the ambient environment during weight measurements is essential. Additionally, low air velocities in the unsteady-state method can amplify the influence of the surface resistance coefficient, and non-Fickian diffusion phenomena may affect the calculation of diffusion coefficients.
It is worth mentioning that the diffusion coefficients calculated using the two methods for the same specimen do not coincide numerically. They are similar at lower MCs, but at higher MCs, the steady-state diffusion coefficients tend to be approximately double those obtained from the unsteady-state method. This difference is primarily attributed to the stress relaxation phenomena involved in the latter case. In drying modeling, the focus is mainly on the values of unsteady-state diffusion coefficients (Choong and Skaar, 1972; Comstock, 1962).
6. CONCLUSIONS
With the production of CLT panels manufactured for wooden houses, the question arises of how long the bonded structure will keep its integrity, as due to moisture diffusion blockage, inevitable tensions appear in the glue line. As a result of tensions, strain occurs inside and between the wood and adhesive layer, negatively affecting the panel’s lifecycle. As discussed in each section of this review, many knowledge gaps persist about water vapor diffusion in bonded wood, or adhesive materials used for wood bonding. Furthermore, only a limited number of scientific results are available. On the other hand, structural wood adhesives used for CLT production may have strong water and water vapor diffusion-blocking effects through the adhesive layer. Thus, their diffusion behavior should be systematically analyzed, and the molecular structure of the adhesive needs to be adjusted to a diffusion like that of the wood. This paper identifies the knowledge gaps and collects the available techniques to establish the basis for investigating the diffusion property of CLT panels.