1. INTRODUCTION
With climate change becoming a growing concern, the Intergovernmental Panel on Climate Change (IPCC, 2014) reported that direct emissions from the building sector accounted for 6.4% of global greenhouse gas emissions in 2010. The most commonly used building materials in construction are concrete and steel, which emit large amounts of carbon in their production (Li et al., 2022). Wood, on the other hand, has a carbon storage effect when used as a building material by fixing the carbon it absorbs as it grows (Singh et al., 2022). Owing to the carbon storage effect of wood, it is gaining global attention as a building material to counter climate change.
In Korea, wood has long been widely used as an eco-friendly building material for Korearn traditional building. Depending on the diameter and shape of the logs, lumber is produced and used as a material for a variety of wooden structure. Timber with large dimeter have traditionally been milled and used for structural materials such as posts and rafters. However, timbers with small and medium diameter were mostly shredded and used for pulp or wood lumber, with little use as structural materials. Since the 1900s, manufacturing technological developments have led to the development of engineered wood using small and medium timbers, which have been used as structural laminated materials. Currently, engineered wood is used as an eco-friendly material in both construction and non-construction sectors. Representative engineered woods include structural glued laminated timber (GLT) and cross laminated timber (CLT), which have the advantage of being dimensionally stable and easy to process, allowing them to be manufactured in a variety of shapes and sizes. Therefore, not only the physical properties of CLT and design values for utilization as a building material have been studied, but also the manufacturing of hybrid CLT with composite applications of various materials (Choi et al., 2020, 2021; Fujimoto et al., 2021; Gong et al., 2021; Jung et al., 2020; Lee et al., 2022; Song and Kim, 2023; Trisatya et al., 2023). In particular, CLT, a building structure, has high compressive and bending strengths and has accelerated the high-rise development of wooden buildings based on performance studies such as CLT joints developed mainly in Europe and North America (Ahn et al., 2021; Lee et al., 2022).
The largest amount of forest stock in Korea is reported to be coniferous forests, followed by broadleaf forests and mixed forests, and softwood is mainly used for structural materials, according to KS F 3020 (Korean Standards Association, 2018; Korea Forest Service, 2023). Hardwood is mostly used for bioenergy rather than structural materials, depending on their growth characteristics and cellular organization, and research on high-value-added and long-term utilization of broad-leaved materials has increased in recent years in consideration of the carbon storage effect. Yellow popler (Liriodendron tulipifera L.) is a hardwood, but as a fast-growing tree, its usability as a structural material has been continuously studied since the 1990s in the U.S. In Korea, research has been conducted on the manufacture of mixed CLT by combining it with other tree species in consideration of the growth characteristics of yellow popler (Galih et al., 2020; Park et al., 2020; Song and Kim, 2022; Yang et al., 2021).
The main adhesives used to manufacture GLT and CLT are water-resistant resolvent phenolic resins and polyurethane resins, all of which are cold-setting resins. Phenolic adhesives have been used for structural applications, but with the increasing social concern for environmental and human health friendliness, adhesives with low formaldehyde emissions have been preferred. Developed for productivity and high bonding performance, one-component polyurethane adhesive is a polymeric polyisocyanurate adhesive that easily reacts with hydroxyl groups in wood and has excellent water resistance, so it is already widely used in Europe to manufacture GLT and CLT (Park, 2014). The bonding performance of CLT depends on various variables, such as the adhesion degree of the adhesive to the surface of the layer, the cohesion of the adhesive itself, the penetration depth of the adhesive into the layer, and the environmental conditions. The penetration of adhesive into wood varies depending on tree species, type of adhesive, pressure, pressure time, temperature, moisture content, adhesive moisture content, etc. (Li et al., 2021; River et al., 1991; Rowell, 2012). In hardwoods, the thin cell walls of vessels and earlywoods facilitate the penetration of adhesives, but wood fibers and latewoods hinder bonding performance. Therefore, research to understand the penetration pathway of adhesives is also being continuously studied, and microscopic analysis such as scanning electron microscopy is typical. Jakes et al. (2019) utilized X-ray computed tomography to understand the exact process of infiltration. The bonding performance of CLT is evaluated by delamination rate, shear strength, and neck wave rate, and the international standard for CLT, ISO 16696-1:2019, provides performance measurement methods and quality standards for adhesives based on ISO 20152-1:2010.
In this study, mixed CLTs were manufactured using different tree species (Japanese larch, Korean red pine, and yellow poplar) to evaluate the adhesive performance, and the penetration depth of adhesive and bonding line thickness were measured using a stereomicroscope and scanning electron microscope to analyze the interrelationship between adhesive performance and adhesive penetration characteristics.
2. MATERIALS and METHODS
Layer materials were categorized according to the type of mixed CLT. Japanese larch mixed CLT is made of Japanese larch [Larix kaempferi (Lamb.) Carrière] as the outer and middle layers and yellow poplar (Liriodendron tulipera L.) as the inner layer. Korean red pine mixed CLT uses Korean red pine (Pinus densiflora Siebold & Zucc.) as the outer and middle layers and yellow poplar as the inner layer. Both Japanese larch and Korean red pine layer materials were sourced from trees over 40 years old in Gyeonggi-do and Gangwon-do and purchased from the Yeoju Wood Distribution Center in Gyeonggi-do. The yellow poplar layer material was 27-year-old wood grown in the Eocheon Test Forest of the National Academy of Forestry Sciences (Hwaseong City) and Suwon. The average specific gravity and moisture content of Japanese larch used were 0.54% and 10.50%, while those of Korean red pine were 0.42% and 11.20%, and those of yellow poplar were 0.51% and 11.50%. The dimensions of the layers were 100 (b) × 500 (l) × 25 (h) mm.
To investigate the adhesive characteristics of Japanese larch/yellow poplar and Korean red pine/yellow poplar mixed CLTs, adhesive specimens were prepared for each adhesive. The first adhesive was a one-component polyurethane adhesive (OTTOCOLL G10), commonly used in Europe and known as a fast-setting and eco-friendly adhesive. This adhesive is primarily used in automated CLT production facilities. However, adhesives that are exposed to outside air and moisture will cure, which can lead to problems such as clogged spray nozzles due to curing if not used consistently (Song and Kim, 2022). Therefore, polyurethane adhesives with different curing times and adhesive characteristics, as shown in Table 1, were applied. The second adhesive was a phenolic resorcinol adhesive (PRX350BT/PR-1HSE, Aica Kogyo, Nagoya, Japan), typically applied to structural aggregates and known for its durability and water resistance. However, the curing time of phenolic resorcinol adhesive is longer than other adhesives, which is a factor that reduces the productivity of CLT manufacturing. The third adhesive was a water-based polymeric isocyanurate adhesive (AUX-500/AUH-8, Aica Kogyo, Aichi, Japan), classified as an eco-friendly adhesive, not containing formaldehyde, and mainly used for furniture. It also has the advantage of low application volume due to its excellent adhesion.
To examine the adhesive characteristics of mixed CLTs according to the adhesive for CLT lamination, 5-ply CLTs were prepared. To investigate the adhesive penetration characteristics of mixed CLT, mixed CLTs composed of Japanese larch and yellow poplar (LY type) and mixed CLTs composed of Korean red pine and yellow poplar (RY type) were manufactured. The amount of adhesive application was 200 g/m2 applied on one side, and the pressure was 1 MPa using a hydraulic press (200 ton capacity, Angeon Hydraulic Machinery, Gimpo, Korea). As for the polyurethane adhesive, due to its tendency to foam when cured, the compression time and constant compression pressure are important. Therefore, CLT with polyurethane adhesive was manufactured by applying 1 hour and 4 hours of pressing time to investigate the effect of adhesive penetration. The composite CLTs were 500 mm wide by 500 mm long by 125 mm thick and cured at room temperature for one week after manufacturing (Fig. 1).
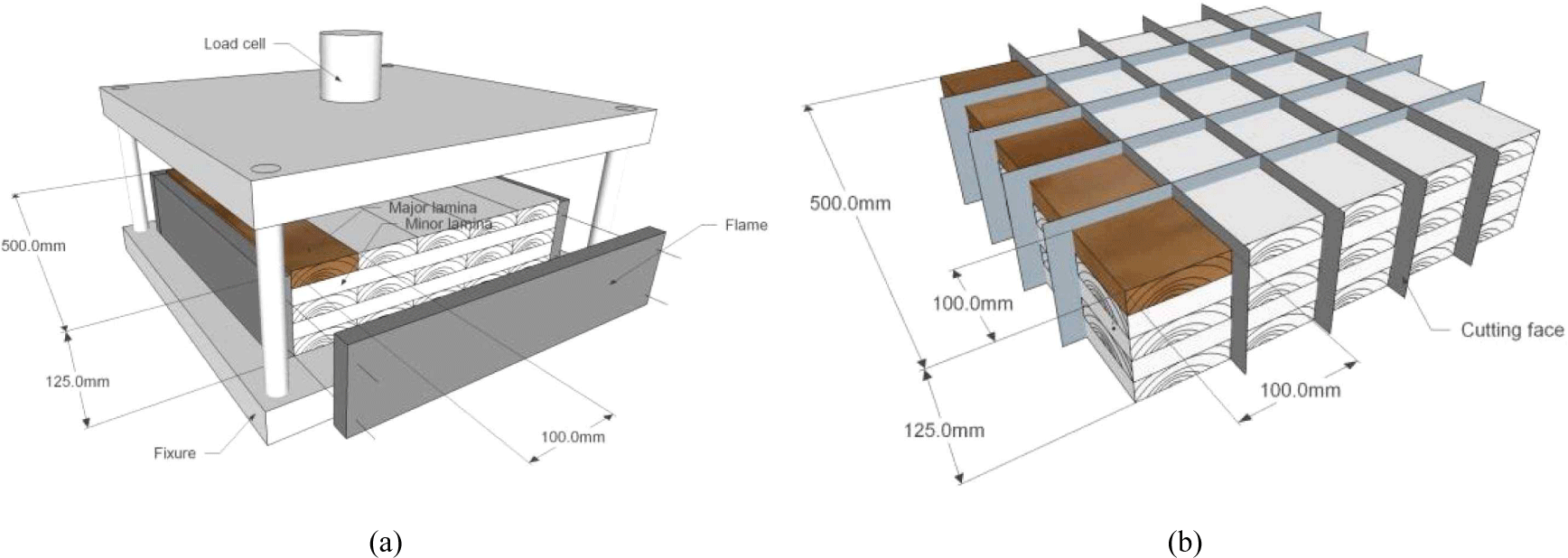
The bonding performance standards of CLT vary from country to country, and boiling water soaking delamination delamination is one of the most important performances that determine quality. To investigate the water resistance performance of adhesive-blended CLT, the water boiling test was conducted according to KS F 2081 Cross Laminated Timber (Korean Standards Association, 2021). The fabricated mixed CLT was re-cut to the dimensions of 100 × 100 × 125 mm thick, as shown in Fig. 1b, and 24 of the manufactured specimens were used. The water boiling test was performed by immersing the specimen in boiling water for 4 hours, then immersing it again in water at room temperature (10°C–25°C) for 1 hour, and then placing it in a constant temperature dryer at 70 ± 3°C to dry to a mass ranging from 100% to 110% of the pre-test mass. The delamination length in the bonding line measured on all four sides of the specimen was limited to 3 mm or more, and cracks in the wood due to drying or warping were excluded from the measurement. The delamination rate was calculated as in Equation (1).
LD: The sum of the delamination lengths in the bonding line on the four edge faces of the CLT.
LG: The sum of the bonding line lengths on the four edge faces of the CLT.
The bonding performance standard for CLT is 10% or less of the boiling water soaking delamination rate according to KS F 2081. Based on the results of the water boiling test, manufacturing conditions were selected to improve performance.
To measure the bonding line thickness of the mixed CLT, samples were taken from the specimens for microscopic observation, as shown in Table 2. The bonding line specimen was made centered on the bonding line of the major and minor axis layer materials. To examine the adhesive penetration process of each cross-section of the layering material, the transverse and radial or tangential cross-sections of the layering material were made. The fabricated specimens were cleanly cut with a silding microtome to identify the cross-section, coated with gold, and observed under a scanning electron microscope (SEMCOX EM-30, COXEM, 20 kV). The bonding line thickness was measured 10 times per specimen, and the average value was calculated.
Type of mixed CLT | Layer | Observation section | |
---|---|---|---|
Major | Minor | ||
PNLY | Cross | Radial or tangential | ![]() |
WILY | ![]() | ||
PULY | ![]() | ||
PURY | ![]() | ||
PULY | Radial or tangential | Cross | ![]() |
PURY | ![]() |
The specimen for microscopic observation was taken from the center of the fabricated mixed CLT. A cross-section of the bonding line according to the adhesive type of the mixed CLT was cut and stained with a 1% safranin solution and observed. To examine the penetration depth of adhesive, the length of the adhesive penetrated into the cell on the cross-section of the laminae with the bonding line was measured 20 times as shown in Fig. 2 using the Image j program, and the average value was calculated.
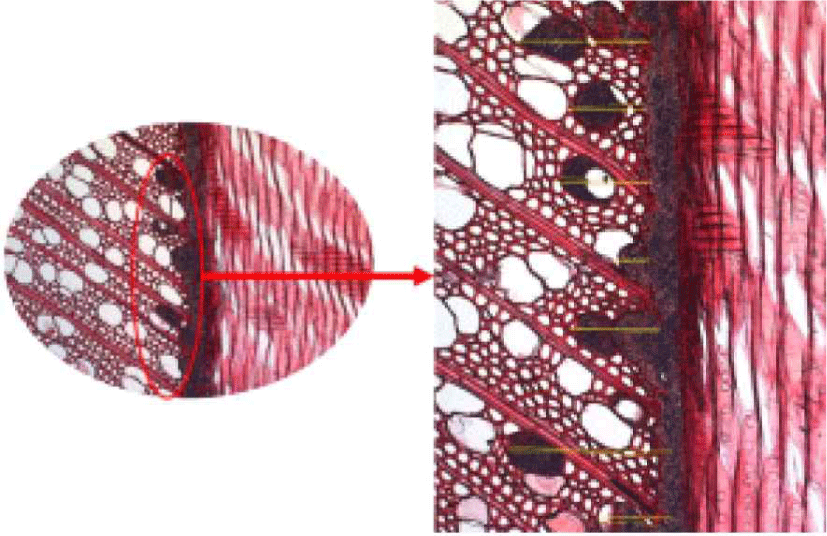
3. RESULTS and DISCUSSION
For use as a structural CLT, the boiling water delamination of mixed CLT was evaluated by adhesive type and tree species according to KS 2081. Alamsyah et al. (2007) reported that there are differences in bonding performance depending on the density and wettability of the laminate species and the contact angle of the adhesive. Therefore, depending on the species, the adhesive characteristics are also very important for its penetration into the laminate. The delamination performance of LY-type mixed CLT bonded by applying the same oppressive pressure time (4 hours) for each adhesive type is shown in Fig. 3. Japanese larch-yellow poplar mixed CLT bonded with phenolic resorcinol adhesive (PN) and polyurethane adhesive (PU) met the quality standard of boiling water soaking delamination rate of CLT set by KS F 2081 with less than 10%, but the specimen bonded with water-based polymer isocyanurate adhesive did not meet the quality standard. Therefore, the waterborne polymeric isocyanurate adhesive used in this experiment is not considered suitable for the fabrication of mixed CLTs.
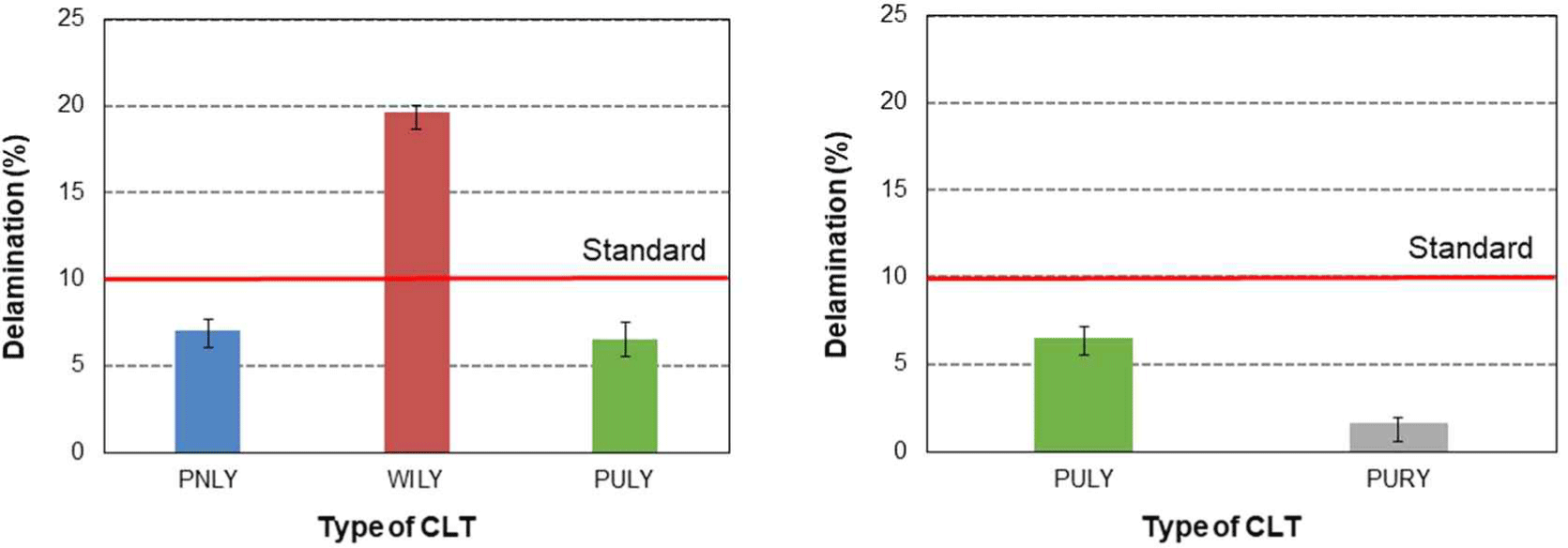
In addition, based on water boiling test results, PU adhesive showed better adhesion performance in Korean red pine-yellow poplar mixed CLT than Japanese larch-yellow poplar mixed CLT. The PU adhesive did not inhibit the deformation of the Japanese larch laminate during the drying process after immersion but inhibited the deformation of the Korean red pine laminate with a relatively low specific gravity. Therefore, the PU adhesive used in this experiment is determined to be more suitable than other adhesives for bonding Korean red pine and yellow poplar.
The adhesive penetrates into the cell lumen through the oppressive pressure of the layer material. The penetration depth of the adhesive is one of the most important factors in bonding performance. The bonding mechanism of the adhesive is not only the chemical adhesion of the adhesive to the wood surface, but also the physical adhesion of the adhesive into the cell. To determine the penetration depth of the adhesive when Japanese larch and Korean red pine, which were softwood structural materials, were used as the outer layer and yellow poplar was used as the inner layer, a microscopic analysis of the layer by section was conducted based on the bonding line. Fig. 4 is an image of the bonding line thickness observed by scanning electron microscopy. The adhesive penetrated into the tracheids of Japanese larch and Korean red pine and into the vessels of yellow poplar.
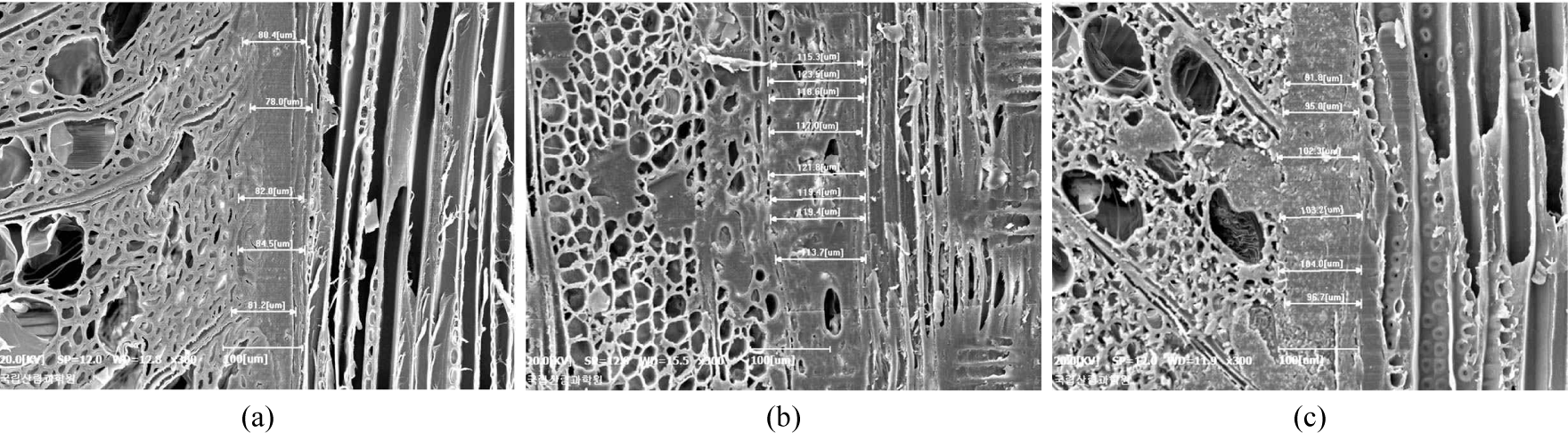
PNLY and WILY specimens have a thinner bonding line thickness compared to PULY specimens. In addition, the bonding line thickness of the composite CLT with PU adhesive did not show any significant difference with the pressure time. When used as an adhesive for the manufacture of CLT, the thickness of the bonding line is specified in BS ISO 16696-1:2019 Timber Structures as not more than 0.2 mm for the bonding line of CLT between plates and 0.3 mm for the longitudinal direction of the layer material. Comparing the bonding line thickness of mixed CLT by adhesive, PU adhesive was found to be thicker than other adhesives, but it met all EN standards (Table 3).
Specimens | Thickness of bonding line (mm) | Requirement of ISO 16696-1 |
---|---|---|
PNLY4 | 0.1 | Less than 0.2 |
WILY4 | 0.1 | |
PULY4 | 0.2 | |
PURY4 | 0.1 |
Optical microscopy was used to examine the penetration pathway of the adhesive into the layer materials of the mixed CLT. PN and WI adhesives were identified as dark and reddish in color, making them distinguishable from cells in the layer materials. For the PU adhesive, the adhesive was identified as shown by the white arrows in Fig. 5(c) and (d). In Japanese larch and Korean red pine, glue was found inside the tracheids. In yellow poplar, the penetration pathway of the adhesive into cells is considered to be through the blood vessels around the radial tissue. Kim and Park (2021) reported that the adhesive penetration process in wood was confirmed by using a specially treated adhesive to penetrate into the radial tissues and tracheids of softwood.
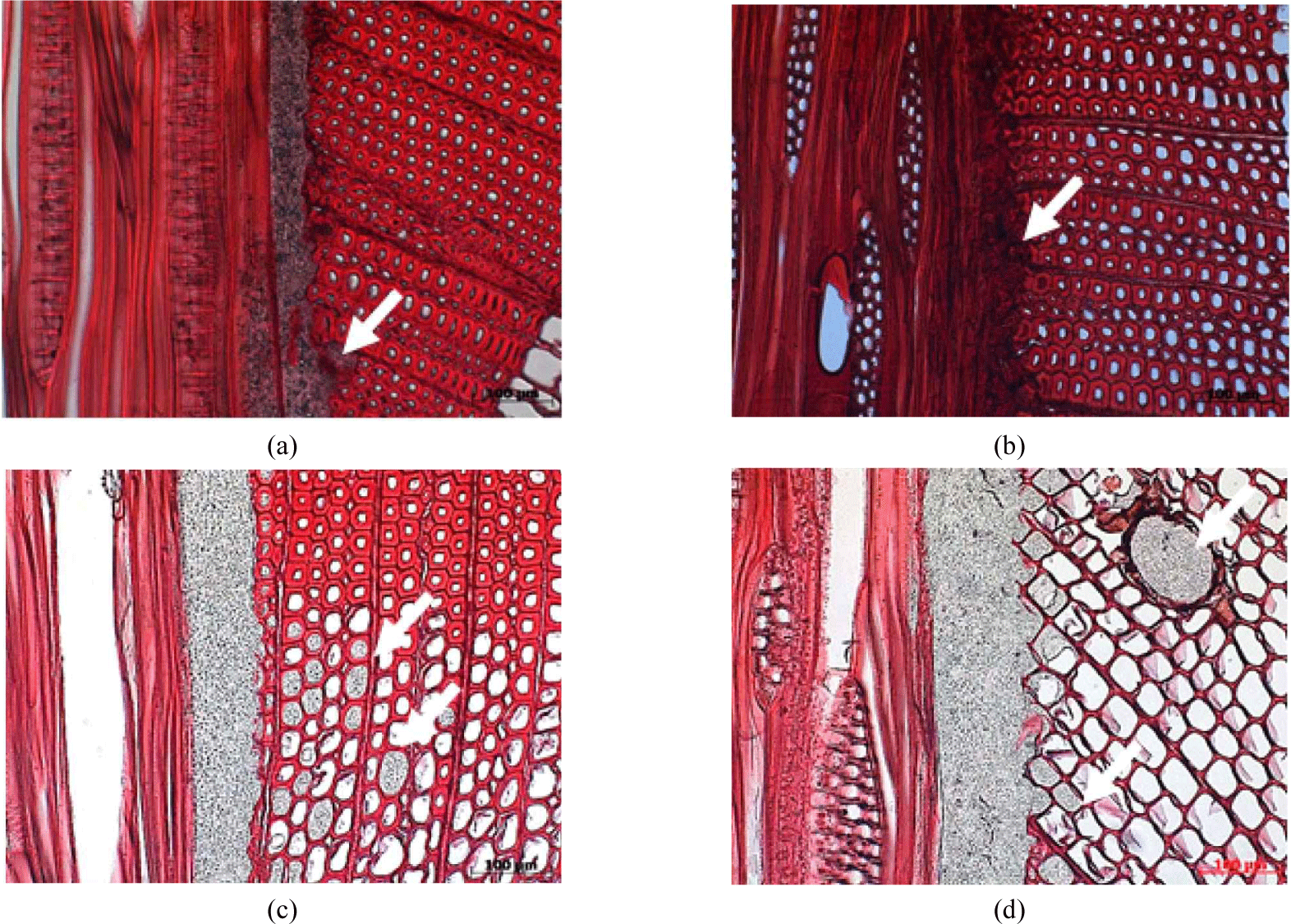
During microscopic observation, it was difficult to distinguish between WI and PN adhesives when the cell lumen was small, as the degree of staining of the cell affected the color of the adhesive. Various studies have been conducted to investigate the penetration process using confocal micrographs, SEM, and fluorescence microscopy (Frihart, 2005; Kamke and Lee, 2007; Singh et al., 2008; Fig. 6).
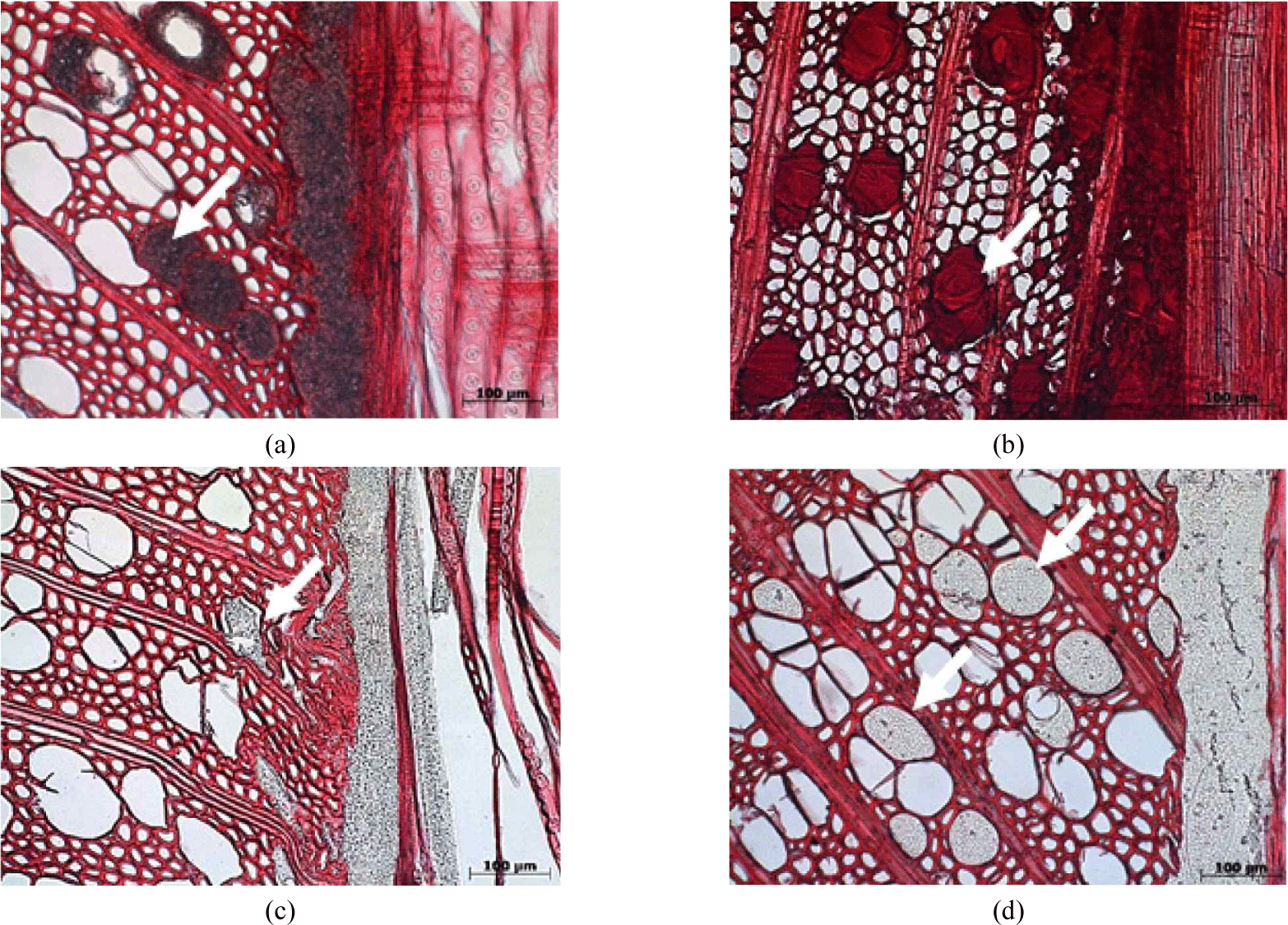
Table 4 shows the adhesive penetration depth of each composite CLT. Comparing the penetration depth of each type of adhesive in the yellow poplar layer of the mixed CLT bonding line, PN and PU adhesives were measured to penetrate the most, and the PU adhesive penetrated the RY specimen more than the LY specimen. As for the pressure time, the 1-hour specimen was penetrated deeper than the 4-hour specimen. The PU adhesive with fast curing speeds is difficult to penetrate into the substrate after an adequate curing reaction time. As for the test specimen using the WI adhesive, the penetration depth from the bonding line was similar to that of PU adhesive with the same pressure time, but it did not meet the boiling water soaking delamination criteria, indicating that the water resistance of the adhesive and the strength of the adhesive itself were important factors.
4. CONCLUSIONS
Depending on the type of adhesive used in the manufacturing process of mixed CLT, the boiling water soaking delamination of the adhesive was evaluated, and the penetration depth of the adhesive into the layer material and the thickness of the adhesive layer were compared. The results of comparing the penetration depth of the adhesive according to the type of layer material with an optical microscope and the thickness of the bonding line with a scanning microscope are as follows.
-
The results of the water boiling test of mixed CLT met the quality performance standards for phenolic adhesive and polyurethane adhesive, and all mixed CLT specimens with polyurethane adhesive according to tree species met the quality performance standards.
-
The penetration pathway of the adhesive in the layer material was found in the tracheids of Japanese larch and Korean red pine, while yellow poplar laminates showed penetration into the vessels through the radial tissues.
-
The penetration depth of the adhesive was measured to be the largest for the phenolic adhesive under the same pressure time condition, while the bonding line thickness was inversely related to the penetration depth for the polyurethane adhesive.