1. INTRODUCTION
Bamboo is a renewable natural resource and has global significance currently as a non-wood product (Darwis et al., 2023; Hong et al., 2020; Lee et al., 2023; Maulana et al., 2021). It is an important product because of its various applications, such as a food resource owing to its nutritional content, in medicine for medicinal purposes, in textile industry, and as a construction material (Galih et al., 2020; Kadivar et al., 2021; Maulana et al., 2017; Sumardi et al., 2022; Zhang et al., 2018). There are approximately 36.8 million hectares of bamboo forests globally distributed in tropical, subtropical, and temperate areas, covering 1,400 bamboo species in total 1,200 woody and 180 non-woody (herbaceous) bamboo species (Xu et al., 2020).
Indonesia has abundant natural wealth (Arinana et al., 2022; Fadwati et al., 2023; Iswanto et al., 2021). The area under bamboo forests in Indonesia accounts for 5% of the world’s bamboo forest area and includes 11 genera and 35 species of bamboo (Park et al., 2018). Bamboo also has ecological advantages because of its faster growth rate than wood, which can facilitate its harvesting in a short time; additionally, it exhibits resistance to wind strength, has high seismic strength, and can reduce pollution in the environment by absorbing carbon dioxide and nitrogen at high temperatures (Adil et al., 2014; Basri and Pari, 2017). Bamboo also exhibits favorable physical properties, such as high strength, flexibility, easy to split, easy to form, and economical price compared to wood. However, bamboo also has several disadvantages, such as easy breakage or cracking during work and susceptibility to wood-destroying organisms (Hong et al., 2020; Wulandari et al., 2019).
Betung bamboo (Dendrocalamus asper) has great potential as an alternative raw material for wood substitution at the industrial scale in Indonesia. This is because wood raw materials can no longer cope with the needs of the domestic industry that are increasing every year (Basri and Pari, 2017). In Indonesia, micro, small, and medium enterprises, being one of the industrial categories that are involved in various bamboo handicraft products, play a large role in the use of bamboo (Rusdiyantoro and Nurcahyanie, 2016). Drying is an important process in the bamboo industry. It reduces the high moisture content (MC) of fresh bamboo that in turn reduces microbial and fungal damage, making it ready for storage, processing, and conversion to a finished product (Lv et al., 2019). Bamboo can also be split into blades and dried until the MC is below 11%, to increase its dimensional stability, strength, and uniformity (Xu et al., 2017).
Bamboo drying is an energy-consuming and time-intensive process. Currently, most bamboo products are dried using conventional technologies, such as drying and drying kilns, which are cost-effective techniques. However, these technologies result in low product quality and the drying time is relatively longer compared to that when a gas oven is used. Uneven temperatures also lead to defects, such as rupture and bending, which can hinder proper operation of traditional drying (Lv et al., 2019). Conventional drying generally involves drying considering a natural open flow, often called oven solar drying, whereas if a cabinet is used for drying, it is called direct solar drying. Forced drying that involves drying air forced using a fan is being developed. Forced solar drying that is developed using inlets and directed outlets to distribute hot air more directionally is called indirect solar drying (Banout and Ehl, 2010; Khouya, 2022).
Being an equatorial country, Indonesia can effectively utilize solar energy for drying because of long sun shine duration. However, the energy efficiency of solar drying decreases with increasing distance from the equator (that is, in temperate countries). Solar drying is a promising method in terms of energy efficiency and green energy. Thus, solar drying should be developed in countries that have geographical advantages, such as equatorial countries. Limited information on drying bamboo using sunlight, especially in tropical areas, makes research important to carry out. This study aimed to determine the effectiveness of the design of an indirect solar dryer (indirect drying) and compared it with that of a direct solar dryer (direct drying) and to determine the dryer schedule from bamboo strips. The study findings can more effectively and efficiently promote the application of the solar drying process in micro, small, and medium enterprises to reduce the drying costs.
2. MATERIALS and METHODS
A digital FY-12 thermometer and hygrometer, puncture thermometer, CAS EC digital scale (FY-12, Fujian, China), caliper, ruler, camera, an electric oven, a meter, and a sawmill were used in this study. The materials used in this study were Betung bamboo strips, aluminum foil bubbles, black paint, thick iron wire, screws, nails, AC sakaguchi fans, galvalume sheets, polycarbonate, and multiplex. This research was conducted at the Wood Laboratory and Labtech VA Forestry Building, Bandung Institute of Technology, Jatinangor Campus, for approximately two months starting from 5 October 2022 to 30 November 2022.
Samples of bamboo strips were obtained from Betung spindle bamboo from Temanggung. Bamboo was split into blades and cut using a sawmill to adjust its length. The sample size used was adjusted to the size of the solar drying prototype. The length, width, and thickness of the bamboo strips were 45, 4.0–4.5, and 1.5–2.5 cm, respectively. In total, 20 strips were used as test material for solar drying. All bamboo strips were made from fresh bamboo with a MC of 70%–80%.
The oven design was adapted from Banout and Ehl (2010) and Patra et al. (2013) for indirect drying and from Banout and Ehl (2010) for direct drying, as shown in Fig. 1. The main multiplex material of the oven was 18 mm, which was coated with a thermopack of aluminum foil bubbles on the inside to retain heat and re-coated using a galvalume sheet. It was covered using polycarbonate as a roofing material at the top.
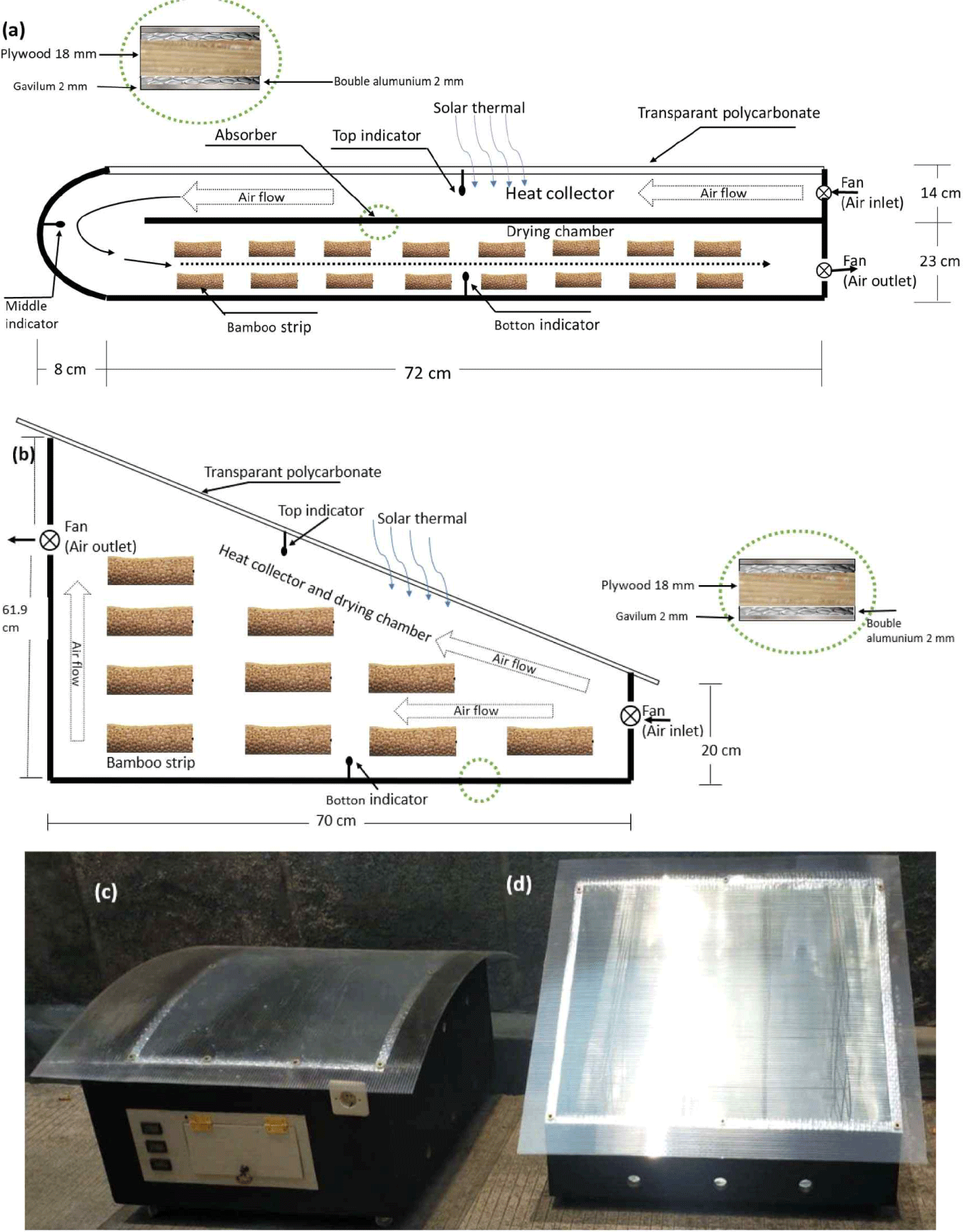
In total, 20 samples were placed in the solar dry oven. Ten bamboo samples were used for indirect drying and labeled as “B,” and 10 bamboo samples were used for direct drying and labeled as “A.” Prior to drying, the initial weight (W_initial) of the sample was measured; subsequently, the weight was measured daily (24-h interval) to record the changes in the MC of the bamboo during the drying process. MC was calculated using Equations (1) to (5) (Tang et al., 2013).
After obtaining the MC of the bamboo during the drying process, the dryer speed was calculated as follows:
Where, MC%_t is moisture content at t time and the unit of t is h. The unit of drying rate or speed was %/h. While calculating the efficiency of oven performance, a comparison between the volume of the compartment, bamboo volume, polycarbonate absorbent area, and the amount of water lost during the drying process was calculated using the following formula:
The temperature and humidity of the oven and the environment were measured using an FY-12 digital meter that can measure temperature and humidity, which were monitored once every 1 h from 5:30–16:30 Western Indonesian Time (WIB) for at least 5 d to determine the fluctuations in temperature and humidity. In this test, the percentage and type of defects that occur are also observed, such as node check, splitting, end check, and cracks (Tang et al., 2013).
The dry weight of the oven is calculated by heating the sample to dryness using the ASTM D4442-92 standard for water content measurement. The finished bamboo sample was dried at 103 ± 2°C for 24 h (W_dry) in the oven (Kaur et al., 2016).
3. RESULTS and DISCUSSION
The performance of indirect and direct drying was compared and reviewed based on the temperature, humidity, and water content profiles of the drying results with statistical tests.
Direct drying could reach average maximum and minimum drying temperatures of approximately 64.3 ± 14.7°C and 59.7 ± 13.1°C, respectively. The maximum direct drying temperature was 82°C. In indirect drying, the highest average temperature was in the collection section (67.3 ± 13.0°C), while it was 60.2 ± 12.0°C in the middle dryer compartment and 51.2 ± 9.0°C at the lower indicator near the outlet hole. The maximum temperature in indirect drying reached 85°C in the heat collector, 70°C in the dryer compartment, and 60°C in the near part outlet.
As shown in Fig. 2(a) and (c), the indirect drying oven collector part always exhibited a higher temperature than the direct dryer part. The rapid increase in temperature in the heat collector of indirect drying was due to the difference in the ratio of the surface area of the polycarbonate to the oven volume. The collector of the indirect drying oven had a larger surface area to volume ratio (0.0451 cm2/cm3) compared to the ratio of direct dryer to compartment volume (0.0305 cm2/cm3). The 2.4 times larger indirect drying oven ratio than the direct drying oven ratio resulted in faster temperature increase because it has a larger surface area in capturing energy to heat a certain amount of space (Bergman et al., 2011).
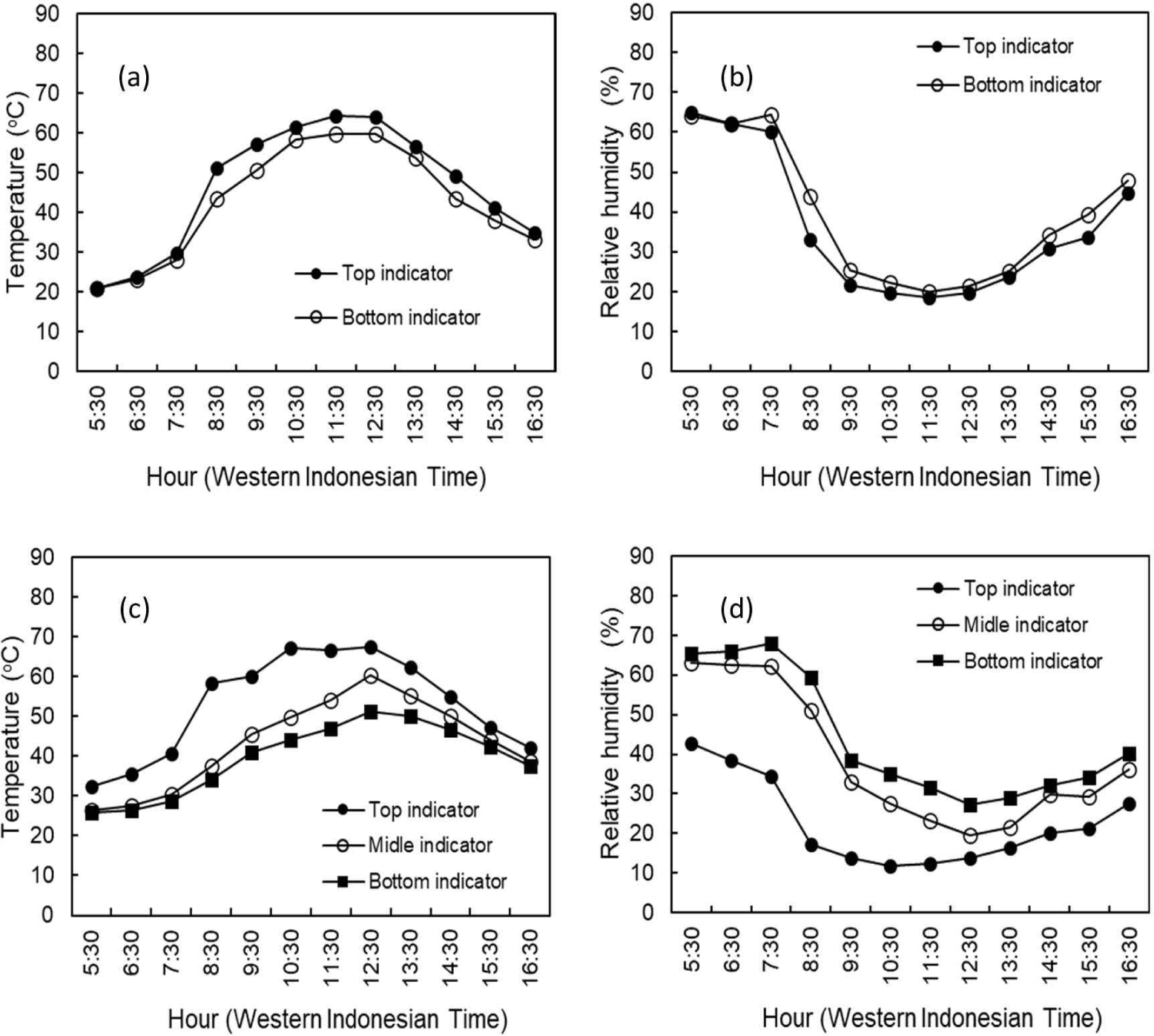
Relative humidity (RH%) decreases with increases in the oven temperature because the air has a higher capacity to hold more water than when the temperature is lower due to the increased water vapor saturation point (Simo-Tagne et al., 2018). The increase in temperature decreases RH%, such that the equilibrium MC of bamboo decreases due to low RH%; consequently, water transfer is forced from bamboo to the environment (Chanpet et al., 2020; Sasongko et al., 2020). When the dryer had the highest average temperature on the upper and lower indicator of the direct dryer, the RH was 18.4 ± 15.7% and 19.9 ± 16.4%, respectively, while in the upper, middle, and lower indicator of the indirect drying dryer, the RH was 13.8 ± 7.7%, 19.5 ± 15.5%, and 27.4 ± 16.4% [Fig. 2(b) and (d)].
Fig. 3 shows that the temperature of the direct drying compartment exhibited a higher average temperature than the indirect drying compartment from 08:30 to 12:30 WIB. This was because in direct drying, solar heat was directly passed to the drying compartment and thus, the temperature from the compartment was directly affected by the intensity of the light received. However, in indirect drying, solar heat was not received directly into the compartment but was collected in the collector section and distributed using a fan to the compartment through convection; therefore, the temperature increase was slow and exhibited more stable fluctuations. When the sunlight intensity started decreasing or was low, the temperature in the indirect drying compartment was higher than that in the direct drying oven, as observed in the morning at 05:30–07:30 and when sunlight started decreasing at 13:30–17:30 WIB.
Fig. 3 shows that both dryers exhibited a higher average compartment temperature than the ambient temperature, although at 5:30–7:30 the temperature in the direct drying compartment was almost equal to the ambient temperature, which is a drawback of direct drying compared to indirect drying.
Heat collection in an indirect drying oven has better thermal efficiency than in a direct drying oven because the former can minimize heat loss from the heat collector (polycarbonate) and maximize heat extraction from the heat absorber (galvalume). The air flows above the absorbent plate and under the absorbent plate section and heat loss only occurs in the outlet hole and heat is transferred through polycarbonate as a heat collector (Aldabbagh et al., 2010; Chamoli et al., 2012). Compared to direct drying wherein the heat loss is high because the airflow is passive using the buoyancy principle so as to produce a stack effect (Mijorski and Cammelli, 2016). The indirect drying efficiency can reach 83.0% if fins are added or surfaces are porous to enlarge the surface area of the heat collector that can increase the ratio of surface area to a significant volume. This increases the thermal efficiency by 20%–25%, which is approximately 30%–35% higher than the thermal efficiency of direct drying heat collectors, which can achieve the highest thermal efficiency of 45.9% (Dogra et al., 2020; Kareem et al., 2013).
The MC of the drying results is shown in Fig. 4(a). During the 10-d test period, rainfall was observed for 4 d; particularly, it rained throughout the day on Day 7. During 08:30–12:30 WIB, sunlight was bright, although it was sometimes cloudy. The MC of drying using the solar dry method was 11.4% on Day 8 in indirect drying, while the direct drying still exhibited a MC of 12.5% with an average temperature of 27.1°C and 71.0% RH on Day 8. On Day 9, the MC of both the dryers was below 11.0% (10.7% and 10.0% in direct and indirect drying, respectively), with average temperature and RH of the environment being 36.8°C and 52.0%, respectively. This indicated that indirect drying can dry bamboo strips faster to MC of < 12.0% compared to direct drying. On Day 10, the SD for indirect drying was smaller than for direct drying (1.5% and 0.8%, respectively) as observed on Day 0. The SD of indirect drying was higher than that of direct drying (4.1% and 7.4%, respectively). This proved that drying in an indirect drying oven provides more uniform drying than direct drying.
The drying speed profile can be seen in Fig. 4(b). The decrease in drying speed along with the decrease in MC% is caused because the lesser the water content, the greater the energy required to decrease the speed (Phonetip et al., 2018; Ugwu et al., 2015). Drying solar drying can reach fiber saturation point of approximately 29% (Kareth and Petermann, 2014) on Day 3 of drying with 28.2% MC in direct drying and 27.8% MC in indirect drying; notably, reducing the water content below the fiber saturation point requires greater energy (Ugwu et al., 2015).
The ratio of the volume from the oven compartment to the bamboo volume in direct drying (46.5 volume/ volume) was 1.8 times greater than that in indirect drying (25.8 volume/volume; Table 1). This showed the availability of more free space during direct drying. Water loss per unit area of polycarbonate in indirect drying (0.26 g/cm2) was higher by approximately greater 18.2% compared to that in direct drying (0.22 g/cm2); additionally, the water loss per unit area of the compartment in indirect drying (0.1150 g/cm3) was 61.8% higher than in direct drying (0.0068 g/cm3). There was a larger residual space in direct drying with a larger absorbent surface area than in indirect drying. There is a larger remaining space in direct drying with a larger absorbent surface area compared to indirect drying, but the effectiveness of drying in removing water per unit absorber area and unit compartment volume in indirect drying is more effective. This is because the heat received during indirect drying is stored longer in the lower compartment so that the heat becomes more stable and lasts longer. Therefore, in addition to being more efficient in space, indirect drying proved to exhibit better heat capabilities than direct drying.
This was confirmed by the one-way analysis of variance test results, which indicated a significant difference in the 95% confidence level (p < 0.05) for the average water loss parameters per compartment volume between direct drying and indirect drying. An exception to this was observed on Day 7 due to rainy weather conditions throughout the day, with an average ambient temperature of 25.7°C and 84.0% RH (Fig. 5).
In general, bamboo is most prone to cracking at 42%–12% MC. Bamboo has elastic, thick-walled fiber cell components as well as parenchymal components and vascular beams near the epidermis of bamboo strips. Bamboo shrinks on drying which is important for fluctuations in the stress of the bamboo components. When the bamboo is dried again from 40% to 20%, the voltage at 291 tangential shrinkage decreases and cracks begin to occur (Yan et al., 2020). Due to the continuous evaporation of free water in the lumen of the cell, the capillary stress also weakens. At the last stage, the MC of the various parts of the bamboo is under the fiber saturation point evaporation from the bound water that accelerates fiber shrinkage and parenchymal networks, consequently, increasing tangential shrinkage again and resulting in cracks in various parts (Yan et al., 2020).
Table 2 shows that the number of damages in indirect drying is relatively smaller and for a longer duration than in direct drying. This is because an indirect drying oven has heat stability that increases more regularly compared to a direct drying oven, the fluctuations of which are directly influenced by the intensity of sunlight because it is a direct oven type (Banout et al., 2010; Dogra et al., 2020; Kareem et al., 2013). On Day 1 of direct drying, blades with defects were observed, while on Days 3–8, the percentage of defects was on average smaller than that during direct drying.
Drying type | Day | |||||||||
---|---|---|---|---|---|---|---|---|---|---|
1 | 2 | 3 | 4 | 5 | 6 | 7 | 8 | 9 | 10 | |
Direct drying | 0 | 1 | 3 | 3 | 3 | 3 | 4 | 4 | 5 | 5 |
Indirect drying | 0 | 0 | 1 | 1 | 2 | 2 | 2 | 2 | 2 | 2 |
This damage is caused due to the unevenness of heat during the drying process. When bamboo is exposed to high and uneven temperatures, the MC is lost quickly and shrinkage does not occur evenly, resulting in cracks on bamboo. The outer part of bamboo has a greater shrinkage due to the distribution of higher vascular density such that cracks occur from the inside to the outside of the bamboo (Lv et al., 2019; Shu et al., 2020). Fluctuations in temperature and humidity also cause a gradient difference between the surface and the inner part of bamboo and thus, cracks occur due to repeated development and shrinkage (Liese, 2015).
Drying using an indirect drying oven has a smaller occurrence probability of defects due to its more stable temperature compared to drying in a direct drying oven. Fig. 6 compares check nodes and cracks in indirect drying and direct drying. The cracks were caused because the stain part has shorter fibers than the node part and because simultaneous thickening of the walls causes the stain part to be more prone to breakage under pressure. Further, the node part has varying high-density fluctuations in both the tangential and longitudinal directions caused because the beams of the vessels are not in the same direction, causing uneven voltage distribution (Huang et al., 2015; Liese, 2015). Moreover, too fast drying at high temperatures has a greater probability of damage than at low temperatures (Shu et al., 2020).
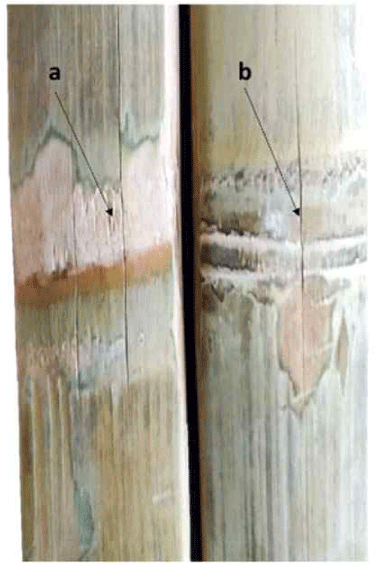
4. CONCLUSIONS
This research was conducted to determine the effectiveness of using solar energy to dry bamboo which is effective in direct and indirect drying. The results show that the temperature that can be reached with direct drying was higher than that with indirect drying, but a stable temperature was observed in indirect drying. The high temperature fluctuations in direct drying caused more defects in bamboo compared to that in indirect drying. Further, there is a difference in the ratio of water loss per compartment volume between the drying performance of direct drying and indirect drying. This was because indirect drying exhibited significantly higher thermal efficiency than direct drying. Generally, the solar drying oven can air-dry bamboo up to 14% MC for 7 d from an initial MC of 70%–80% and can reduce operational costs. The research results can develop small-scale bamboo industries which have limitations in using electrical energy.