1. INTRODUCTION
Parallel strand lumber (PSL) is manufactured from veneers clipped into long strands laid in a parallel formation and bonded together with an adhesive to form a finished structural section. The length-to-thickness ratio of the strands in PSL is approximately 300. Like laminated veneer lumber (LVL) and glulam, this product is used for beam and header applications, where a high bending strength is needed. PSL is also used frequently as load-bearing columns (APA, 2007). PSL is a type of the structural composite lumber (SCL) with high structural performance. This product is an alternative to structural lumber from the old-growth timber logs. In particular, PSL is a very efficient material for making high-strength members using low-grade timbers.
As PSL is made of veneer strands, it is possible to use low-grade logs and convert them to high-strength engineered wood products. Liu and Lee (2003) explored the basic physical and mechanical properties of PSL made from southern yellow pine and yellow poplar. They reported that PSL improves some properties of solid wood from PSL. Ahmad and Kamke (2011) presented their research results on PSL from bamboo and indicated that Calcutta bamboo was suitable as raw material for structural composite products. Kurt et al. (2012) examined the properties of PSL from hybrid poplar and showed that hybrid poplar clones could be used in PSL manufacturing. Through their research, they attempted to convert low-grade materials into high-strength members.
The performance of the connection is an important factor in engineered wood products, and studies on the bearing properties of PSL have been conducted (Cui et al., 2020; Fridiyanti and Massijaya, 2018; Hwang and Komatsu, 2002; Zhou et al., 2018). Li et al. (2019) also investigated the compression and impact resistance of PSL from bamboo and the effect of the loading conditions on the dowel bearing strength of PSL. They presented an experimental equation for a better prediction of the embedding strength of laminated bamboo parallel to the grain. Their studies focused on the efficient utilization of unused waste materials and alternatives to solid sawn lumber.
Japanese larch is the most produced softwood in Korea, but most originate from small and medium diameter logs. As Korean wood resources are being produced in earnest, interest in the effective use of these resources is increasing. Hence, there have been efforts to determine the structural properties of sawn lumber from the small and medium diameter logs (Lee et al., 2018a, b). Choi et al. (2021) studied Larch plywood suitable for cross-laminated timber (CLT) with plywood as a core. This background is in the development of engineered wood for the efficient use of Japanese larch logs. On the other hand, the Korean wood industry faces a downward trajectory, and a new turning point is needed. Although the plywood industry flourished in the past, there are many difficulties. Thus, research on PSL from veneer is needed, but research on domestic wood resources for making engineered wood products is still limited in Korea (Ahn et al., 2021; Choi et al., 2020; Fujimoto et al., 2021; Gong et al., 2021; Hendrik et al., 2019; Hwang and Oh, 2020; Jang and Lee, 2019; Kang et al., 2019; Park and Jo, 2020; Park et al., 2020a, b; Yanti et al., 2019; Yang et al., 2021).
This paper examined the bending and dowel-bearing strength of PSL from Japanese larch veneer strand made in an experimental laboratory and examined the suitability of PSL as a substitute structural material for solid sawn lumber.
2. MATERIALS and METHODS
The rotary peeled veneer of Japanese larch came from a veneer manufacturing company in Incheon. The veneer thickness was 2 ± 0.1 mm and sized to 250 × 900 mm (W × L), and then dried to approximately 10% in a drying chamber at 70°C and 35% relative humidity. After drying, the veneer sheet was clipped to 19 mm in width and 460 mm in length, as shown in Fig. 1(b). The length to thickness ratio was approximately 215, and the length of the strand was fitted to the press size.
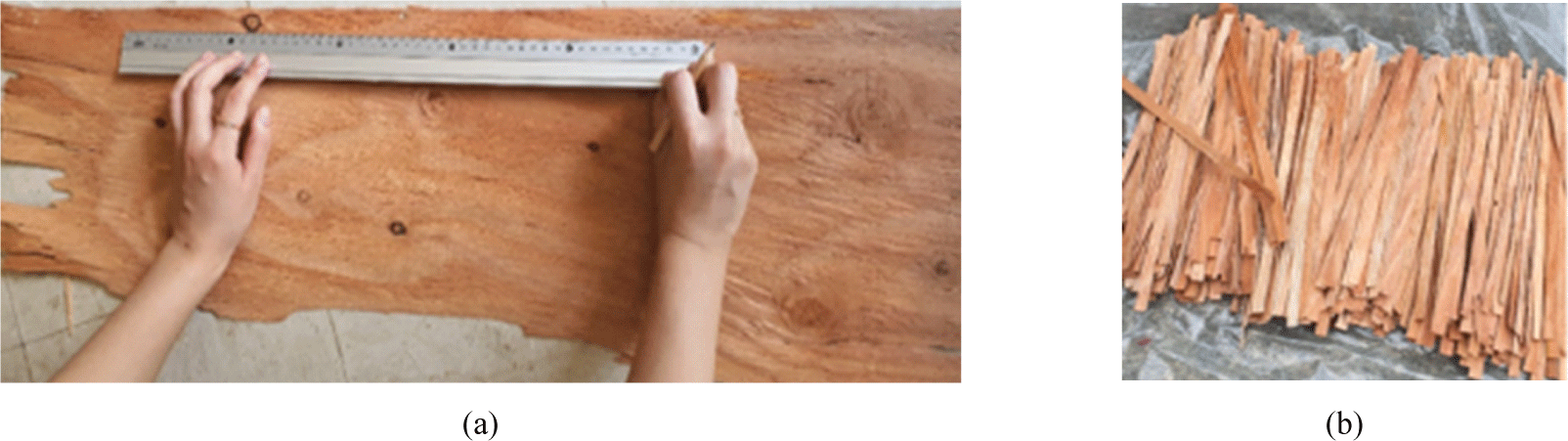
The prepared veneer strands without defects, such as knots and splits, were preselected. The formulated PF resin (viscosity 115mPa·s, solid content 41.8%, pH 11.4) was prepared by the resin manufacturing company and spread using a brush. Before spreading adhesive, the strands were weighed and then reweighed after spreading to calculate the spreading rate to match the set value of 320 g/m2. The seven strands were arranged; each layer was composed of nine strands to produce the PSL samples. The mat was pressed with 140°C, 3.0 MPa, and 8 min. After pressing, the mat was sized to a final dimension of 15 mm × 160 mm × 480 mm (T × W × L). Ten PSL billets were prepared and conditioned in a humidity chamber at 20°C and 65% RH until the test samples were prepared. Fig. 2 shows general sections of PSL. The bending and bearing strength test specimens were cut according to the KS standard, as shown in Fig. 3.

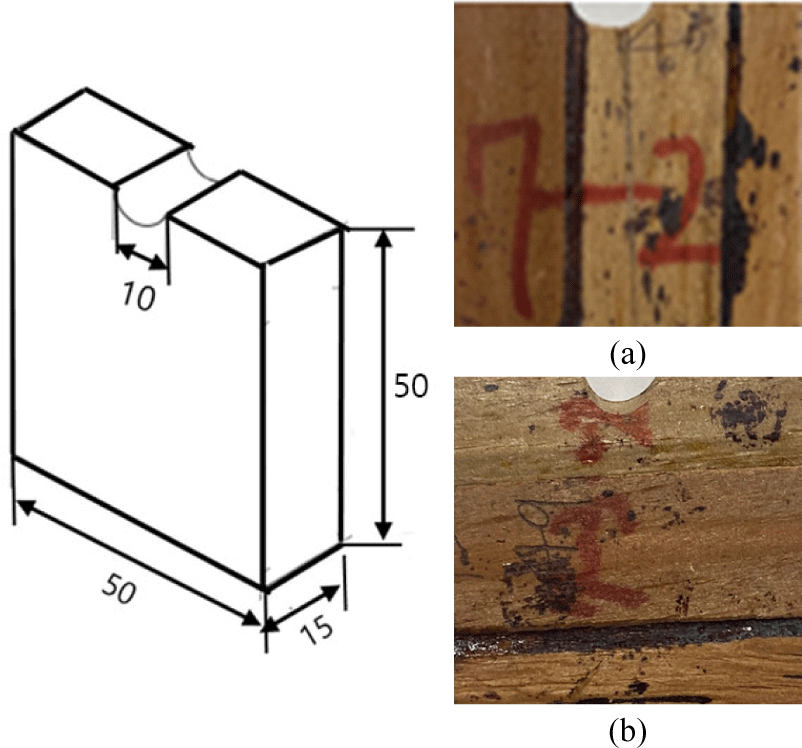
The bending test samples were prepared as two pieces per billet with a size of 15 mm × 50 mm × 250 mm (T × W × L). The flatwise-bending tests were carried out as specified in KS F 2208 with a loading rate of 5 mm/min using a universal testing machine shown in Fig. 4(a). The span to depth ratio was 15, and twenty samples were tested to obtain the modulus of elasticity (MOE) and modulus of rupture (MOR) of PSL. After testing, the moisture contents were measured as specified in KS F 2199. The dowel bearing strength test was conducted as specified in KS F 2156 [Fig. 4(b)]. The parallel and perpendicular specimens to the long axis of the billet with a size of 15 × 50 × 50 mm were prepared and tested. The bearing test specimens were prepared as four pieces per billet; two were parallel, and two were perpendicular. The dowel diameter was 10 mm, and the loading rate was 5 mm/min. The MOR, MOE, and dowel bearing strength (FD) were calculated as follows.
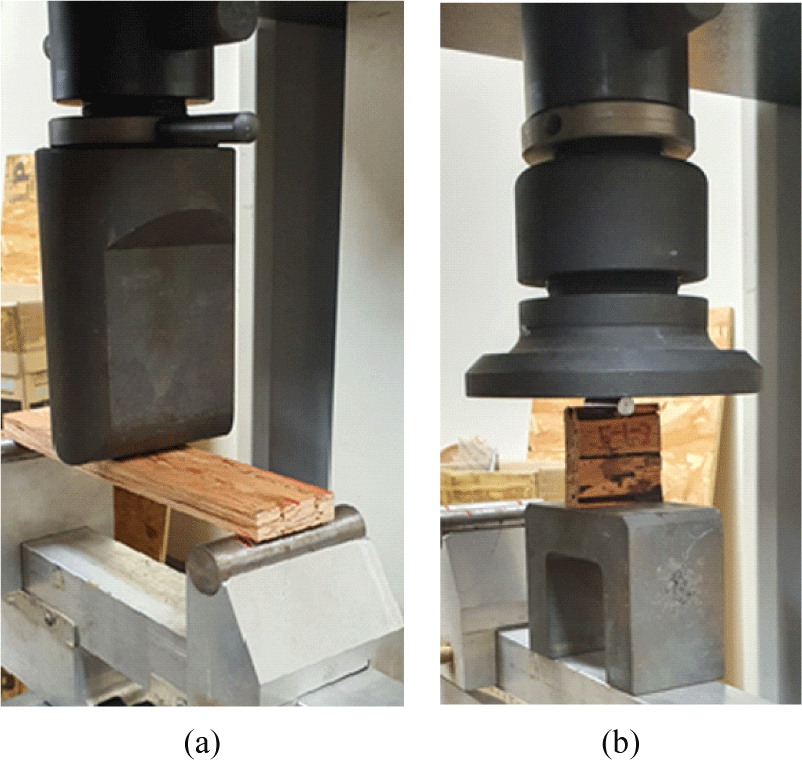
where;
Pmax = maximum load, Pprop = load to proportional limit, L = span length (mm)
b = specimen width (mm), t = specimen thickness (mm), y = deflection to proportional limit (mm)
D = dowel diameter (mm), Py = 5%-offset yield load (N)
3. RESULTS and DISCUSSION
Table 1 lists the results of the average MOR and MOE of PSL made from Japanese larch veneer strand. The average moisture content and air-dried density were 9.38 ± 0.54% and 570.6 ± 52.8 kg/m3, respectively. The average MOR value was 74.3 N/mm2 (56.7–92.1 N/mm2). The average MOE value was 10,753 N/mm2 (8,096–14,464 N/mm2). A positive linear relationship was observed between the MOR and MOE (R2 = 0.75). Liu and Lee (2003) reported that the average flatwise MOR and MOE of PSL made from southern pine were 66.50 N/mm2 and 11,790 N/mm2, respectively. Kurt et al. (2012) reported that the average flatwise MOR and MOE of PSL made from hybrid poplar I-214 were 76.3 N/mm2 and 6,578 N/mm2, respectively. They used a similar sample thickness of 20 mm and showed a lower value compared to this study. Although the sample size differed, this experiment showed meaningful results. The average value of MOR and MOE were similar to other experimental results. The average stress proportional limit (Spl) is also presented in Table 1.
MOR (N/mm2) | MOE (N/mm2) | Spl (N/mm2) | |
---|---|---|---|
Minimum | 56.7 | 8,096 | 23.3 |
Maximum | 92.1 | 14,464 | 53.1 |
Average | 74.3 | 10,753 | 38.7 |
COV (%) | 15.6 | 19.2 | 19.9 |
Relationship | MOR = 8.263 + 0.0059 MOE (R2 = 0.75) |
Table 2 lists the MOR and MOE of PSL, 2 × 4 lumber, and small clear specimens from Japanese larch. The MOR of the small clear specimens was higher than that of PSL. The MOR of PSL was higher than that of 2 × 4 lumber and was approximately 35% higher. The MOE of small clear specimens was lower than that of PSL, and the MOE of PSL was lower than that of 2 × 4 lumber; the difference was approximately 24%. From the results, PSL from the Japanese larch veneer strand can be used as a raw material for SCL.
Product | Density (kg/m3) | MOR (N/mm2) | MOE (N/mm2) |
---|---|---|---|
PSL | 571 | 74.3 | 10,753 |
2 × 41) | 543 | 55.1 | 13,663 |
Small clear specimen2) | 5883) | 84.1 | 10,100 |
Table 3 lists the process of deriving the allowable stresses of PSL made from Japanese larch veneer strand. This process is specified in ASTM D2915, and a 5%-exclusion limit and general adjustment factor for softwood were considered when deriving allowable properties. The allowable MOE was the mean value, as expressed in ASTM D 198-94. The calculation results indicated that the allowable MOR and MOE were 26.31 N/mm2 and 11,438 N/mm2, respectively. Ahmad and Kamke (2011) reported that the allowable properties of PSL from Calcutta bamboo were 24.9 and 11,700 N/mm2, respectively, as shown in Table 3. They suggested that these values are only comparisons and should not be used in structural designs. The commercial product, 1.8E Parallam PSL, has the allowable properties of MOR = 16.5 N/mm2 and MOE = 12,000 N/mm2. The estimated allowable MOR was higher than the commercial PSL, and the MOE was similar to commercial PSL. Compared to this value, this study appears to have favorable results in that PSL made with Japanese larch has potential for structural applications. These values also are comparisons and should not be applied to a design code.
Average (N/mm2) | 5%-Exclusion limit (N/mm2) | General adjustment factor | Allowable properties (N/mm2) | |||
---|---|---|---|---|---|---|
This study | 1.8E parallam PSL | Ahmad and Kamke (2011) | ||||
MOR | 74.3 | 55.3 | 1/2.1 | 26.3 | 16.5 | 24.9 |
MOE | 10,753 | 10,753* | 1 | 10,753 | 12,000 | 11,700 |
Table 4 lists the average dowel bearing strength of the tested samples. The dowel bearing strength test data were obtained from the load-displacement curve, as shown in Fig. 5, and 5% offset value was derived as dowel bearing strength described in KS F 2156. The dowel bearing strength parallel to grain ranged from 22.2 to 56.1 N/mm2, and the dowel bearing strength perpendicular to grain ranged from 10.9 to 28.3 N/mm2. Their difference between the parallel and perpendicular to grain was approximately twice as much. Kim and Hong (2008) reported that the average bearing strength of Japanese larch glulam parallel to the grain section was approximately double that perpendicular to the grain. The test results also showed a similar tendency, and the load orientation had a significant influence on the dowel bearing strength of PSL.
Parallel (N/mm2) | Perpendicular (N/mm2) | Ratio* | |
---|---|---|---|
Minimum | 22.2 | 10.9 | 2.10 |
Maximum | 56.1 | 28.3 | |
Average | 35.1 | 16.7 | |
COV (%) | 27 | 34 |
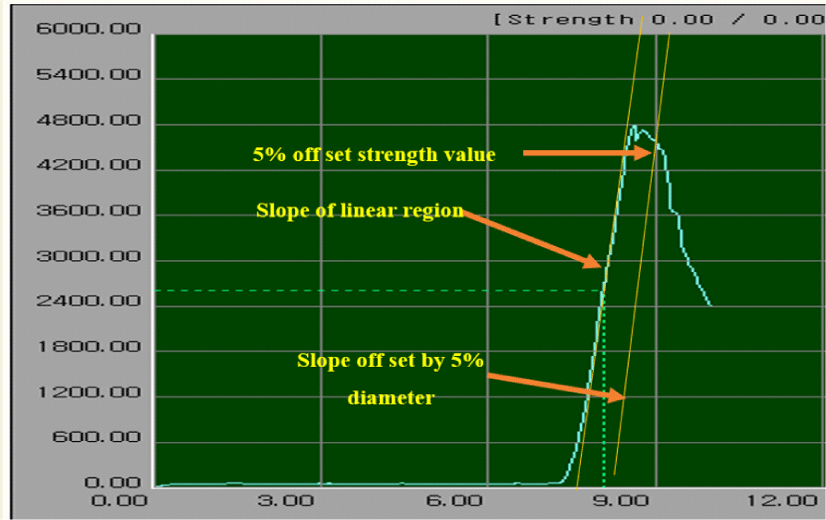
Regarding the bearing strength of wood, the experimental predicting formula has been proposed (American Forest & Paper Association, 2012; Architectural Institute of Korea, 2015). Most formulae are based on the density and diameter and have been adopted in standards. These formulas are as follows.
The Architectural Institute of Korea (2015) defined the dowel bearing strength parallel and perpendicular to grain as
where G is the oven-dry density, and D is the dowel diameter.
The American Forest & Paper Association (2012) proposed the dowel bearing strength parallel and perpendicular to the grain is defined as
Table 5 compares the experimental results and the different national codes. The calculation results of Korean building code (KBC) and National Design Specification for Wood Construction (NDS) were slightly higher than that of the experimental results in the case parallel to the grain, but the difference was higher in the case perpendicular to the grain. The calculation results indicated that the KBC, NDS equations were close to the experimental results (∼10% difference) when parallel to the grain but not when perpendicular to the grain as shown in Fig. 6. A similar test result was also found in the bearing properties of Korean Larix glulam (Kim and Hong, 2008). In the case of parallel to the grain, their difference was not considered significant among KBC, NDS but the difference was relatively high when perpendicular to the grain. The two calculation equations are based on wood. Hence, PSL-bonded products can be affected by several conditions, such as type of glue, hot press conditions, and various manufacturing conditions. Cui et al. (2020) reported that the NDS, CSA (Canada Standard Association), and Japanese code for the dowel bearing strength are too conservative and show that engineered bamboo and wood are not entirely consistent. The PSL made from small stands in the laboratory has the potential that product configurations may be weaker than manufacturing factory-like insufficient bonding between the strands and press conditions. Regarding failure, brittle splitting occurred in specimens parallel to the grain, and splitting and crushing failure occurred in specimens perpendicular to the grain, as shown in Fig. 7.
Experimental | KBC | NDS | |
---|---|---|---|
Parallel | 35.1 | 39.8 (13%) | 38.9 (11%) |
Perpendicular | 16.7 | 25.3 (52%) | 24.8 (48%) |
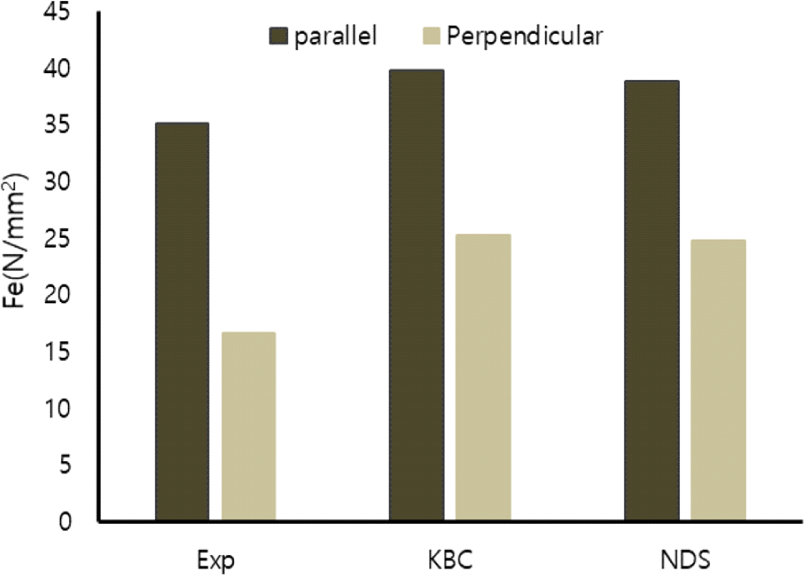
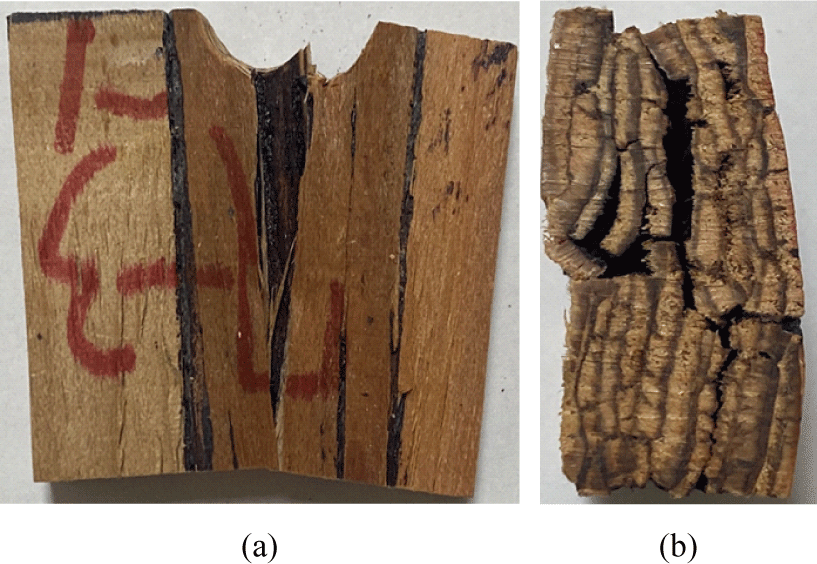
4. CONCLUSIONS
PSL from the Japanese Larch veneer strand was manufactured in the laboratory and characterized by bending and dowel bearing strength tests. The main conclusions of this study are as follows.
The average MOR and MOE were similar to other experimental results, and a positive linear relationship was observed between the MOR and MOE. A comparison of the MOR and MOE among PSL, 2 × 4 lumber, and small clear specimens showed that the PSL could be used as a structural material. The allowable bending stress was calculated and showed favorable results, but these values are only comparisons and should not be used in a structural design. The comparisons of empirical equations described in several national codes for the dowel bearing strength of wood indicated that it was close in the specimens parallel to the grain but significantly different in the specimens perpendicular to the grain. Regarding the failure mode, brittle splitting was observed in the specimens parallel to the grain, and splitting and crushing failure occurred in the specimens perpendicular to the grain. This study determined the general performance of PSL made from Japanese larch veneer strands in the laboratory. Hence, more study will be needed to determine the more precise structural performance of the PSL from Japanese larch veneer strand.