1. INTRODUCTION
Wood fosters sustainable production and is a representative renewable eco-environmental resource (Ahn et al., 2021; Ermeydan et al., 2014; Ghani and Lee, 2021; Hadi et al., 2022; Han and Lee, 2021; Park et al., 2020a; Park et al., 2020b). The Intergovernmental Panel on Climate Change (IPCC) recognizes wood as a representative carbon-neutral material. They also strongly encourage the use of wood as an essential means of building a carbon-neutral society (Brunet-Navarro et al., 2018).
In line with these recommendations, the French government mandated that more than 50% of new public buildings must be constructed of wood in 2022 (Walter, 2020). The popularity of wood products and constructions are also increasing in Korea (Iswanto et al., 2020; Kim and Kim, 2020; Yang et al., 2020). According to a survey of 300 people conducted by the Korea Timber Newspaper in 2019, when asked, “What type of house do you want to build in the future?”, wood was the most common response (47.9%), followed by reinforced concrete (18.6%), other material (13.2%), loess (11.4%), and brick (9%) (Kim, 2019).
Architects should consider sound control when designing a building. Noise reduction is becoming increasingly vital as urbanization advances and people spend more time indoors (Jang et al., 2018b; Kang et al., 2019b). Accordingly, the sound-absorbing material market is also increasing.
The use of sustainable and eco-friendly wood as a sound absorber is noteworthy. Wood can be used as a resonant sound absorber by creating a hole in the panel and applying a backspace. The resonance frequency and sound absorption peak are impacted by the thickness of the perforated plate, the depth and size of the voids, and the porosity (Song et al., 2016). The sound absorption capability also varies depending on the shape of the perforation (Lee et al., 2014).
Wood is a natural, porous material (Jang et al., 2018a; Jang et al., 2019), the transverse plane of which can act as a sound absorber (Jang and Kang, 2021a; Jang and Kang, 2022; Kang et al., 2019a; Kang et al., 2018). According to the results of previous studies, the transverse plane of hardwoods has better sound absorption than that of softwoods, and the sound absorption capability is excellent in diffuse-porous wood with fewer tyloses on vessels (Jang and Kang, 2021b; Jang and Kang, 2021c). In addition, it has been reported that wood by-products, such as bark particles (Kang et al., 2019b), sawdust (Boubel et al., 2021), and leaves (Jung et al., 2021), also have high sound absorption capability.
Wood pellets are generally made from by-products of wood products, are biomass-based energy carriers, and are renewable energy sources (Pradhan et al., 2018). Wood pellets have several advantages, including having more than twice the heat of combustion than the original wood. In addition, wood pellets have a straightforward structure and arrangement that can automatically supply fuel to boilers, all while not generating toxic gas during combustion (Zaichenko and Shterenberg, 2017).
This study focused on wood pellets as an eco-friendly sound absorber. Wood pellets are formed by crushing wood into small pieces and then compressing and molding the pieces at a uniform size (Lee and Kim, 2020). The size of commercially available wood pellets is approximately 5–7 mm in diameter and 20–30 mm in length (Kim et al., 2015).
These granular materials have a sound-absorbing effect due to the hollow spaces between the granules, the rough granule surface, or pores of the granules themselves (Arenas and Crocker, 2010). Wood pellets satisfy all three of these conditions.
Therefore, this study investigated the sound absorption capacity of wood pellets. The results of this study will contribute to the utilization of wood resources for climate change response by suggesting that wood pellets be used as a sound-absorber as well as an energy resource.
2. MATERIALS AND METHODS
Fig. 1 shows the preparation of wood pellets. The wood pellets used in this study were supplied by UJU Camping (Daejeon, Korea) and are made of New Zealand radiata pine (Pinus radiata).
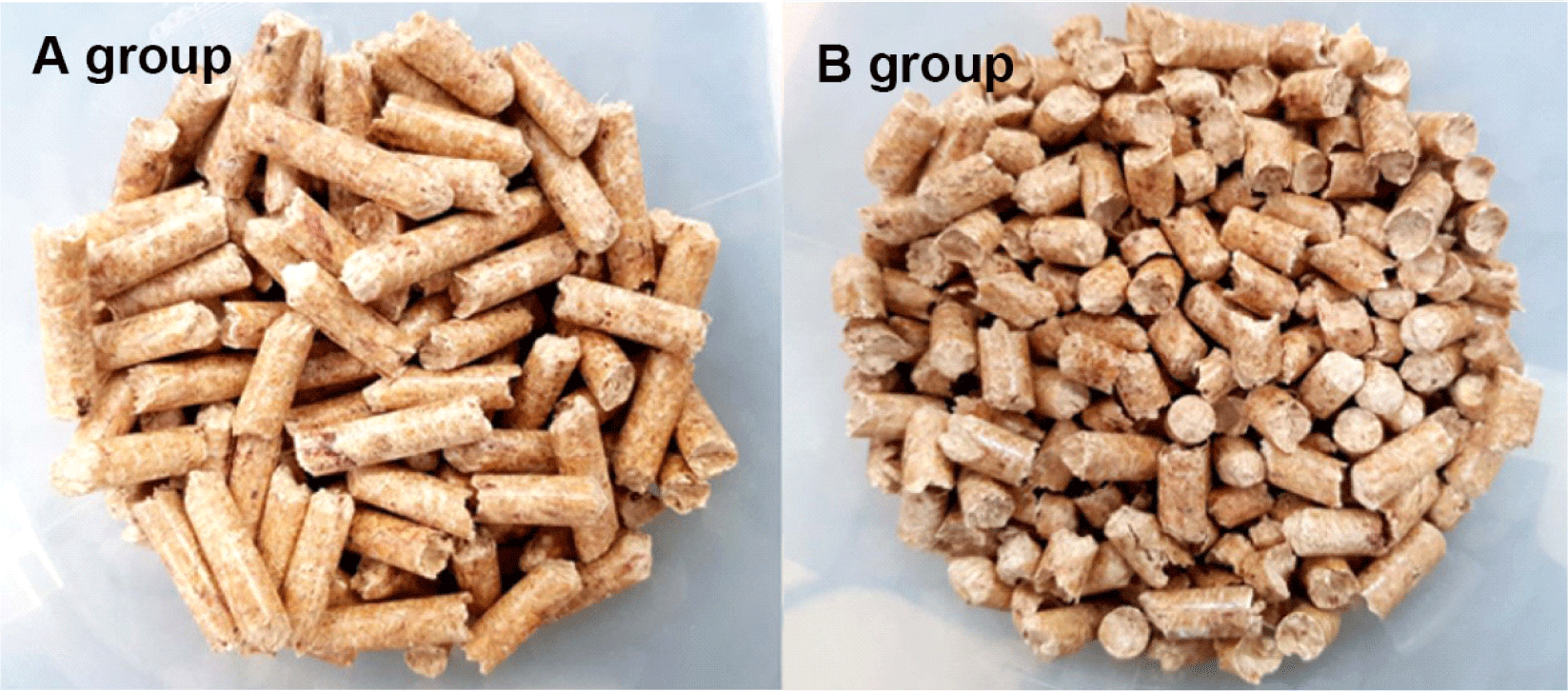
The diameter of the wood pellets was constant at 0.5 cm, but the length varied from a minimum of 0.5 cm to a maximum of 3 cm. This study classified wood pellets into two groups based on length (A group: 1.5–3 cm length and B group: less than 1.5 cm length).
Their moisture content (MC) was measured based on the original weight according to KS F 2199 (Korean Standards Association, 2016). 100 g of wood pellets was placed in an oven and dried at 105°C. After around 3 days, their weight was 93.19 g, and the MC of the wood pellets was 6.81%.
This study analyzed the side and transverse plane surfaces of wood pellets after they were dried in a laboratory oven at 40°C for 5 hours. The pellets then were coated with gold in a vacuum using an ion coating machine (SCM, Emcrafts, Gwangju, Korea). All samples were observed at 500 magnification in high-vacuum mode (7.5 × 10−5 mmHg) using SEM (Genesis-1000, Emcrafts). The side and transverse planes were observed at three locations each.
Fig. 2 shows a schematic diagram of the impedance tube. A large impedance tube system with a 9.9 cm diameter (type 4206, Brüel & Kjaer, Nærum, Denmark) was employed for measuring the sound absorption coefficient. Though an impedance tube typically is used in a horizontal position (Jang et al., 2018b), the present tube was mounted vertically to investigate the sound absorption capability of pure wood pellets without a frame.
The power amplifier (type 42176C, Brüel & Kjaer) produced a plane wave sound source in a 50 to 1,600 Hz frequency range. The sound pressure was measured with two microphones to yield a sound transfer function.
As shown in Fig. 2, the wood pellets were packed into large impedance tubes at fill heights of 3 cm, 5 cm, and 7 cm. The apparent density of the wood pellets contained in the large impedance tube was maintained at 0.65 g/cm3 for Group A and 0.67 g/cm3 for Group B. The wood pellet’s arrangement direction was random during sound absorption testing.
3. RESULTS and DISCUSSION
Fig. 3 shows the SEM images of the wood pellet side and transverse planes. The side plane surface of the wood pellet was smooth, and few pores were observed due to the compression during fabrication.
On the other hand, the transverse plane of the wood pellet had a rougher surface than the side plane. A rough surface is a significant factor that influences improvement of the sound absorption capability (Chung et al., 2017; Duan et al., 2020; Tomyangkul et al., 2016).
Fig. 4 shows the sound absorption coefficient curves of wood pellets by packing height. The maximum sound absorption coefficients of wood pellets filled to a height of 3 cm were 0.311 at 1,600 Hz for the A group and 0.409 at 1,600 Hz for the B group, a 31.5% difference. The maximum sound absorption coefficients of the wood pellets filled to a height of 5 cm were 0.670 at 1,288 Hz for the A group and 0.723 at 1,234 Hz for the B group, with a value 7.91% higher in the B group. The maximum sound absorption coefficients of the wood pellets filled to a height of 7 cm were 0.722 at 864 Hz for the A group and 0.764 at 862 Hz for the B group, with a 5.82% higher result in the B group than the A group.
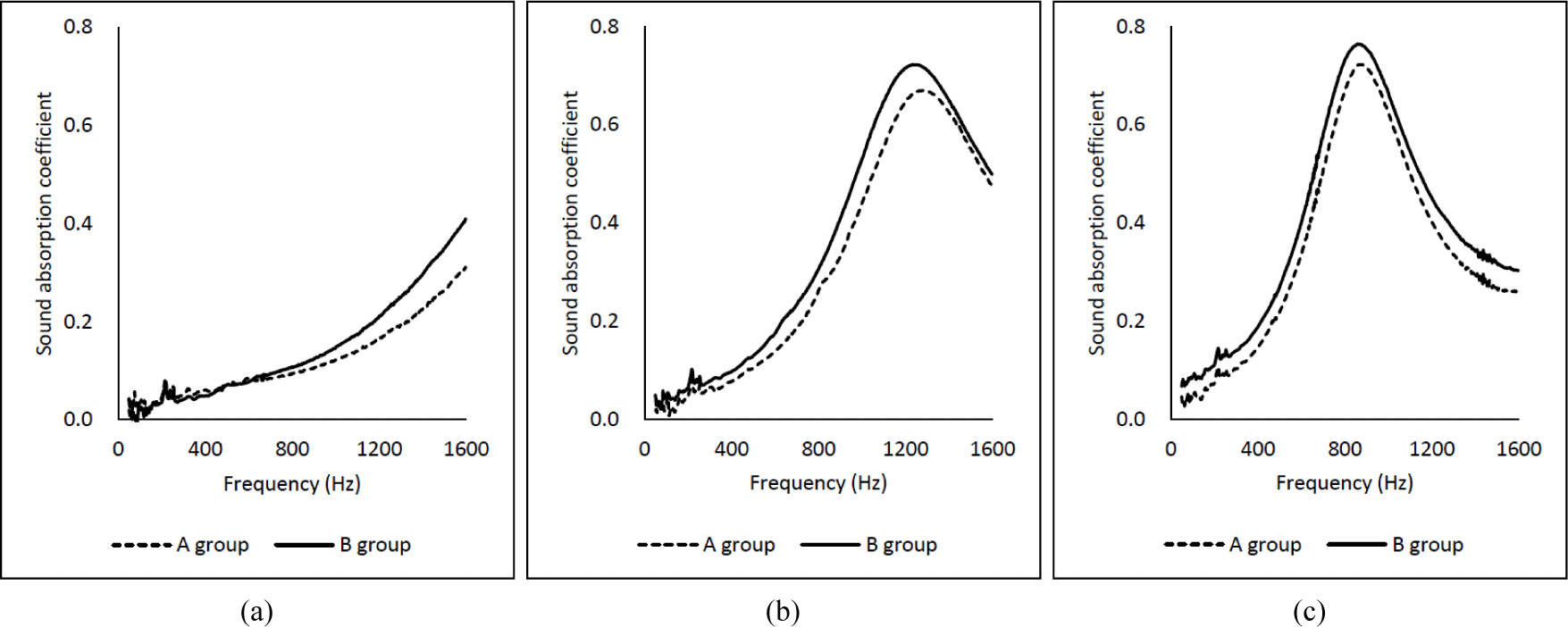
Overall, as the filling thickness of the wood pellets increased, the sound absorption peak shifted in the low-frequency direction. This is a typical characteristic of granular sound-absorbing materials (Borrell et al., 2020). In addition, the B group had better sound absorption than the A group. The reason for this is that the shorter is the length of the wood pellet, the more complicated is the tortuosity of the void volume between pellets. A complex tortuous path can efficiently dissipate incident sound waves (Cao et al., 2018).
Also, the wood pellets of the B group had a shorter length than those of the A group, resulting in higher exposure frequency of the rough transverse section. A rough surface affects the sound absorption performance (Chung et al., 2017; Duan et al., 2020; Tomyangkul et al., 2016). Conclusively, filling to a large height, the complex paths between wood pellets, and the rough surface of the transverse section affect the sound absorption capability.
Wood pellets were initially designed to be utilized as energy resources. However, this study furthers the use of wood pellets based on their sound absorption effects. This study proposes the use of wood pellets as sound-absorbing mats covered with non-woven fabrics. Additionally, such materials can be easy to install if they are manufactured on a board by applying adhesive to the wood pellets. However, since the adhesives block the space between the wood pellets, the sound absorption performance is expected to be significantly lowered. In the future, it will be necessary to study the difference between mat-type sound-absorbing materials without the use of adhesives and board-type sound-absorbing materials coated with adhesives.
4. CONCLUSIONS
This study investigated the sound absorption capability of wood pellets. In sum, as the filling thickness of the wood pellets increased, the sound absorption performance at low frequencies was improved. In addition, short-length wood pellets of sound absorption ability was better than that of long-length wood pellets. This is because the shorter is the length of the wood pellets, the more complex is the tortuosity of the void volume between them. The shorter wood pellets had a higher exposure frequency for the rough transverse plane than did the longer wood pellets, which also increased the sound absorption performance. This study reported for the first time the sound absorption capability of wood pellets. This work will contribute to an increase in wood resource utilization.