INTRODUCTION
Joints used in wooden structures vary depending on the construction material and the required structural performance. For light frame lumber structure, mainly nail joints are used, while bolts and drift pins are generally used for heavy timber structures. Cross-Laminated Timber (CLT), a paneliged engineered wood, is at the forefront of high-value added product, and various studies are being conducted (Choi et al., 2020, 2021; Jang and Lee, 2019; Jung et al., 2020; Kang et al., 2019; Yang et al., 2021). For CLT, lag screws, self-tapping screws (STS), and ring screws were developed in consideration of the characteristics of panelized material, and the design values for products according to the structural application were presented.
STS is divided into tip, shank cutter, and thread, and each part can be inserted into the wood without drilling a hole, minimizing the wood chips and powder generated during the cutting/discharging of the STS insertion process. The angle of the STS thread and gap between the STS and lumber minimized due to the chips and wood dust not coming out from the lumber, and wood dust allowed the STS and wood to self-fasten. Due to these characteristics, STS is widely used as an important fastener for wooden buildings. In the global wooden building market, especially in European countries such as the UK and Germany, STS market share as an important wooden fastener is increasing and various studies are underway (Bedon and Fragiacomo, 2019; Dietsch and Brandner, 2015; Ringhofer et al., 2015; Sullivan et al., 2018).
The European Yield Model, based on the bearing strength of lumber and the bending characteristics of fasteners, is used for the standard allowable stress of a wooden structure joint using fasteners in the structural glued laminated timber (GLT) or CLT. The specific gravity and bearing strength of lumber show a significant correlation (Santos et al., 2010), and as an anisotropic material, lumber shows different bearing strengths depending on the grain of wood (Hwang and Komatsu, 2002). The bearing strength of CLT caused by the fastener is different than the bearing strength of laminated timber because each layer of the lumber is different.
Therefore, for CLT, the performances of the bearing strengths between fasteners and lumber in each direction must be verified.
Pinus densiflora accounts for 66.8% of Korea’s forest land with 70.35% accumulation volume of trees, making it the most important forest resource; the because of plantation is the third largest after cypress and larch (Korea Forest Service, 2020). However, in the lumber industry, the utilization rate of domestic logs is 18%, of which Pinus densiflora comprises a mere 16.6% because Pinus densiflora is mostly used as sawdust (45.1%), wood pellets (17.4%), and chips (15.9%), with 3.1% utilization rate in the lumber industry (National Institute of Forest Science, 2020). Accordingly, research is being conducted to use domestic Pinus densiflora as a structural material to increase the added value of domestic Pinus densiflora (Hong et al., 2017; Kim et al., 2013, 2015). The characteristic of the bearing strength of Pinus pinaster that is conducted based on EN383 and ASTM D5764 (Hwang and Komatsu, 2002) determined a possibility of using Pinus pinaster as structural lumber. Therefore, research on the characteristic of the directional bearing strength of Pinus densiflora that utilizes STS is necessary.
In this paper, the bearing strength performance of domestic Pinus densiflora was examined through STS as a basic study to utilize domestic Pinus densiflora as CLT.
2. MATERIALS and METHODS
As the test material, Pinus densiflora (50(T) × 50(W) × 3,600(L) mm3) with an average moisture content of 13% was prepared at a length of 50 mm and used. The fastener used for the bearing strength test was STS (Galvanized carbon steel) manufactured by Rothoblaas (Italia) (Fig. 1). According to the STS diameter (d1), 8, 10, and 12 mm were classified into three types, and the length (L) was 120 mm. The shank diameters (ds) were 5.8, 7, and 8 mm, while those of the shank cutter (dc) were 6.8, 8.4, and 9 mm, larger than the shank diameter (Table 1).
d1 (mm) | Code | L (mm) | b (mm) | A (mm) | ds | d2 | dc |
---|---|---|---|---|---|---|---|
8 | HBS8120 | 120 | 60 | 60 | 5.8 | 5.4 | 6.8 |
10 | HBS10120 | 120 | 60 | 60 | 7 | 6.4 | 8.4 |
12 | HBS12120 | 120 | 80 | 40 | 8 | 6.8 | 9 |
For the bearing strength specimen, the log was quater sawn. In accordance with KS F 2156, quarter sawn lumber of 50 × 50 × 50 mm3 have a cross section (L), a radial section (R), and a tangential section (T), i.e., a specimen with a clear three-section was selected (Fig. 2).
When using STS, pre-hole is not required, but the groove to be fixed is machined according to KS F 2156 (2017) for the bearing strength specimen. The groove was pressed with a clamp to face the same cross section of two specimen of the same pieces, and a hole was pre-drilled with the same diameter as ds (6, 7, 8 mm) of STS in the center of the facing section. The STS(8, 10 12 mm) specimen was inserted and removed to process threaded path for bearing strength test. The bearing strength specimen was divided into two types: the bearing specimen (T-type) and the shank bearing specimen (S-type). As the thread makes a threaded path even in the bearing test specimen shank where STS is inserted, both T- and S-types have a threaded path in the groove of the bearing strength specimen. The shape of the threaded Pinus densiflora test specimen is shown in Fig. 3.
The specimens were named 8T, 8S, 10T, 10S, and 12T according to the STS nominal diameter (d1) and the area for the bearing. STS with 12 mm diameter was not included because the S part was 40 mm shorter than the specimen. A total of 150 specimen were produced by applying the STS diameter by the bearing part, the three sections of Pinus densiflora (3), and ten repetitions (10). Each type was named as shown in Table 2.
The Pinus densiflora specimens were subjected to humidity control in a constant temperature and humidity chamber with 65% until they reached a constant weight, the mass was measured were measured. The average annual ring width was measured based on the cross section of each specimen, and width of early and late wood were as an annual ring to calculate the average annual ring width.
Bearing strength test method was based on KS F 2156. For T-type, Pinus densiflora bearing strength was tested by inserting it into the groove so that only the thread except the tip was in contact. The S-type was tested after inserting the STS into the groove, including both the shank and shank cutter. For the prepared specimen, a compressive load was applied to a 30 ton load cell of a universal testing machine (Instron 5585) at a rate of 0.5 mm/min (Fig. 4). Compressive load and deformation were measured with Instron 5585.
3. RESULTS and DISCUSSION
The average specific gravity of the Pinus densiflora bearing test specimen was 0.45 ± 0.033, It is within the range of the Pinus densiflora specific gravity of studies (0.41–0.55) (Table 2, Kim, 2012; Park et al., 2006). The average annual width of the specimen was 4.44 mm, and the coefficient of variation was at 19.34%.
Fig. 5 displays the load-deformation curve of the Pinus densiflora bearing strength specimen using STS. The PL specimen (PL) cross section with fiber direction parallel loading direction parallel to the grain direction, the failure on abrupt decrease of load was clear, thus the maximum load and proportional limit could be measured. However, the specimen of the radial (PR) and tangential sections (PT), perpendicular to the grain and load directions, the load continued to increase even in the plastic stage after the elastic behavior as in the partial compression test in perpendicular to the grain. Therefore, it was impossible to measure the maximum load. The PR and PT specimen did not show splitting failure (Fig. 6). In the specimen with parallel load and the fiber directions, the proportional limit increased with the STS diameter increased.
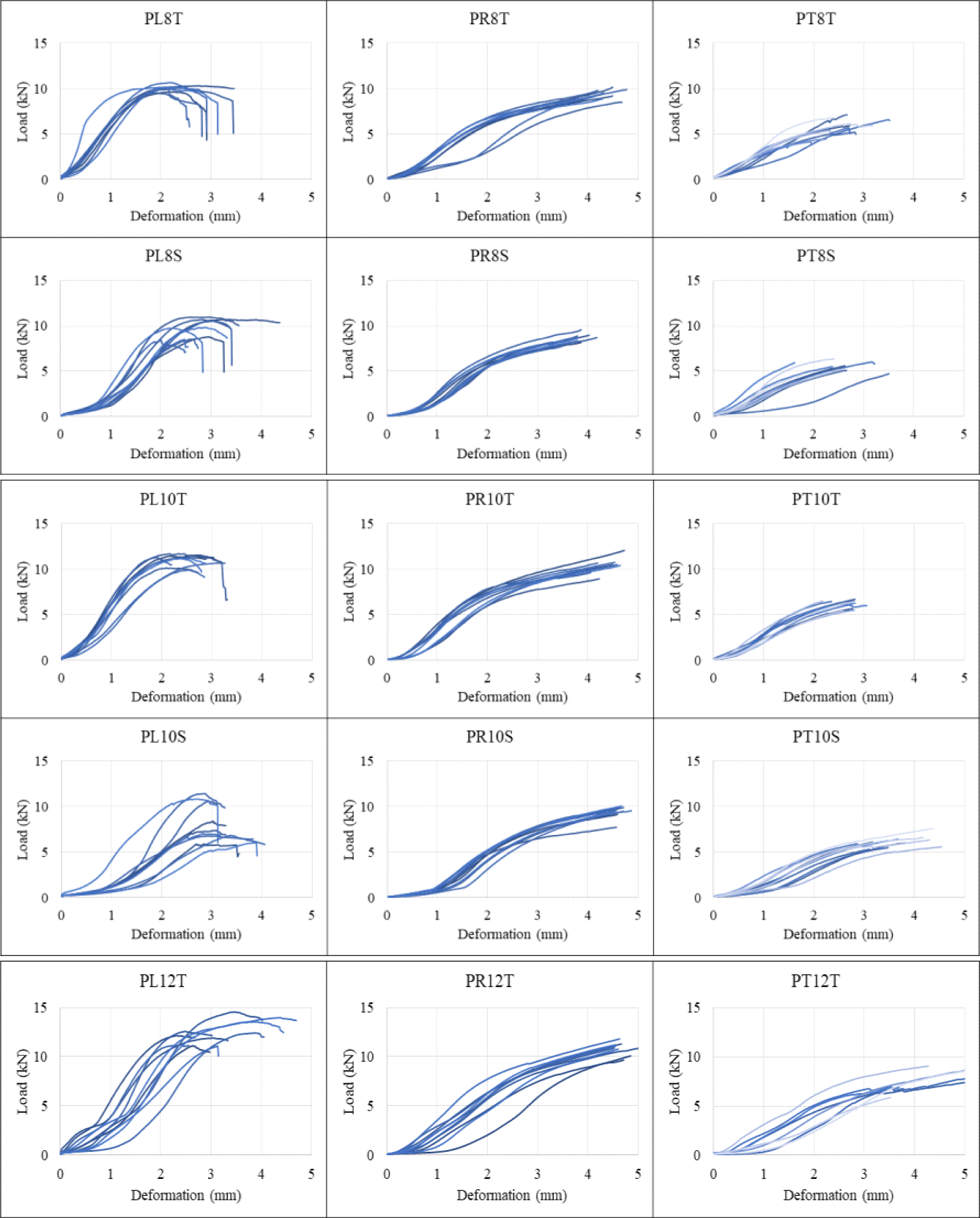
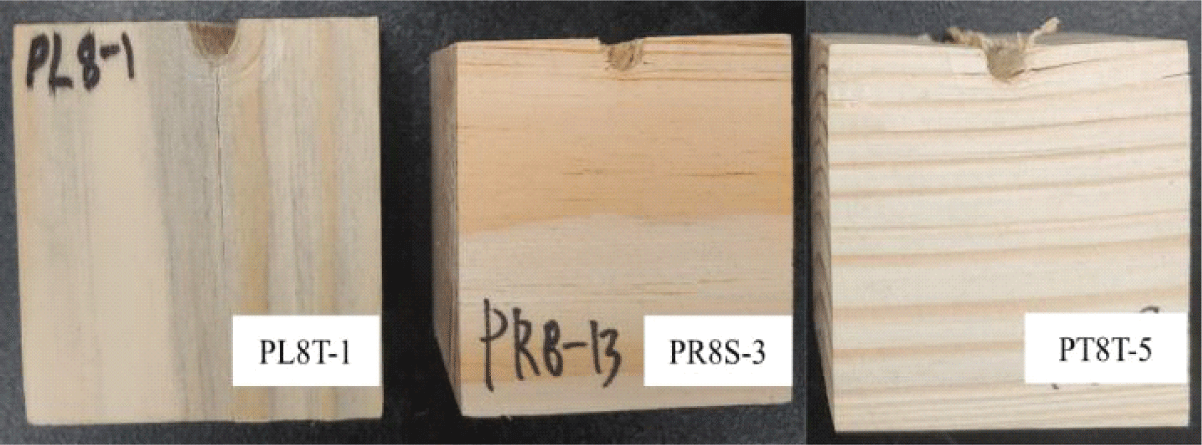
The proportional limit of the specimen (PR, PT) are as follows: For the T-type (P8T, P10T, P12T), the proportional limit increased as the diameter of the STS increased. However, for S-type (with P8S, P10S), P10S using STS with a larger diameter showed lower proportional limit than P8S attributing to the failure configuration. The proportional limit value of T-type is higher than that of the S-type (Table 3).
The yield load value of the bearing strength specimen was calculated in accordance with KS F 2156 as shown in Fig. 7. The bearing strength was calculated by dividing the 5% offset bearing load by the projected area of the part where the STS was pressed on the lumber specimen.
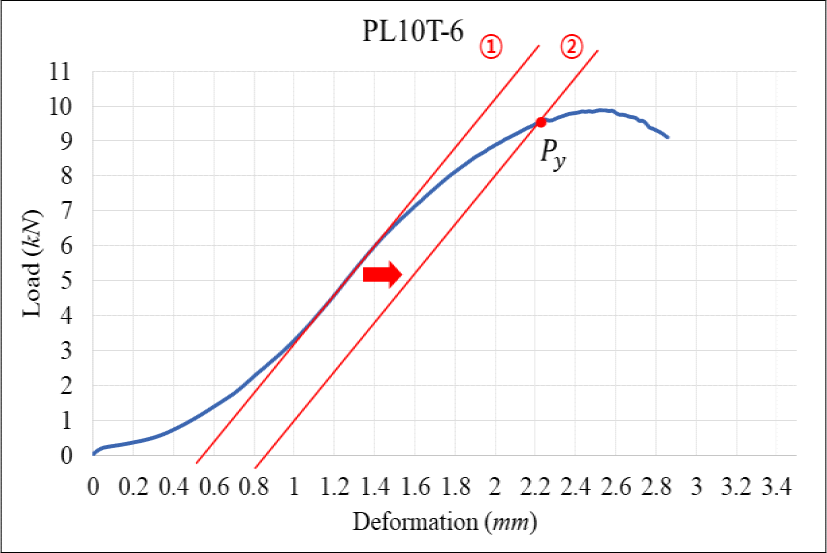
BT: STS thread partial bearing strength
Py: Pseudo Yield Load
a: length of specimen
d: STS thread diameter
BS: STS shank + shank cutter partial bearing strength
as: STS shank length
ds: STS shank diameter
ac: STS shank cutter length
dc: STS shank cutter diameter
Table 4 shows the average yield load and the bearing strength of Pinus densiflora lumber using STS. The yield load was the highest (PL12T) that pressed the cross section of 12-mm STS T-type at 11.85 kN, and the specimen (PT8S) that pressed the tangential section of 8-mm S-type was the lowest at 4.75 kN. Most of the T- (8T, 10T, and 12T) and S-types (8S and 10S) showed a tendency to increase in yield strength as the diameter increased. However, for the PL specimen with parallel fiber and load directions, the yield load of the 10S specimen was lower than that of the 8S specimen, a opposite trend to that of the maximum load value. The S-type maximum load of the 8SPL specimen was higher 10PL due to high stiffness in the fiber direction. However, the yield load showen different result due to load concentration the shank cutter mainly because of larger diameter of shank cutter (Fig. 8).
The bearing strength of all specimens decreased as the diameter of the STS increased due to the increased projected area, and the bearing strength of the S-type test specimen was higher than that of the T-type, possibly because the shank diameters (5.8, 7, 8 mm) were smaller than those of the STS thread (8, 10, 12 mm). The yield load and bearing strength in each direction of Pinus densiflora showed high values in the following order, cross section > radial section > tangential section.
Table 4 shows the bearing strength ratio of the R and T directions according to the fiber direction of Pinus densiflora. Except for the cleavage failure (10S) specimen, the bearing strength ratio of parallel to perpendicular to the grain was measured from 0.61 to 0.69.
In National Design Specification (NDS), the North American wooden structure standard, included in 2018. Suggesting that the CLT bearing strength can be calculated as the effective bearing length which reflects strength ratio of lamina of CLT by grain direction.
Therefore, the STS bearing strength of Pinus densiflora structural engineering wood for each load direction versus the fiber direction will act as an important factor for the prediction of Pinus densiflora CLT bearing strength. In the Korean Design Standard (KDS), the lumber bearing strength prediction formula was load direction grain suggested according to the fastener type and to the fiber direction. Eurocode 5 applies the prediction formula obtained through experiments focusing on the native species. For the STS fasteners, bearing strength prediction formulas have not yet been proposed in the international standards. Therefore, in this paper, to predict the STS bearing strength for each grain direction of Pinus densiflora, a similar lag screw bearing strength prediction formula (KDS and Eurocode 5) was applied and analyzed (Table 5).
KDS (NDS):
Eurocode 5:
Fe: bearing strength (N/mm2)
G: specific gravity (–)
d: fastener diameter (mm)
ρ: average density (N/mm3)
The predicted results of the bearing strength of KDS and Eurocode 5 were similar, but there was a difference between the measured bearing strengths and the predicted ones (Fig. 9). For the perpendicular load of grain direction, the measured strength values of the 8T, 10T, and 12T specimen were 53%, 53%, and 47%, It lower than the EN predicted values, and the 8S and 10S were measured 22% and 27% lower, respectively. A similar trend was also observed in the parallel load to grain direction (Fe‖), The results possibly resulting from applying the d1 diameter to the formula, although the difference in the d1 and d2 diameters of the STS thread was larger than that of a general lag screw with a wide spacing between the threads. Because the shank had a similar diameter as the lag screw, the difference was relatively small, but the predicted value was low because the failure was concentrated in the shank cutter. The prediction formula of KDS and EN is the method of calculating the bearing strength based on the maximum load, and KS F 2156 is the method of calculating the bearing strength based on the 5% offset yield load, thus the possibility of a difference is high as well.
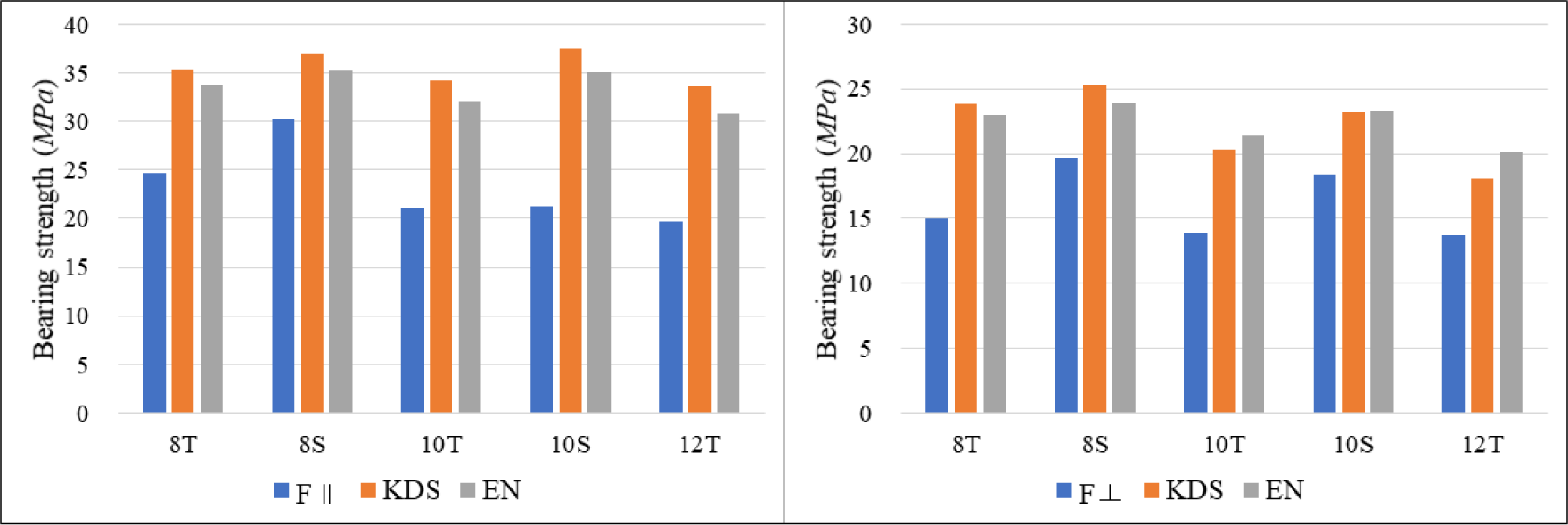
Due to the structural difference between the lag screw and STS, the empirical coefficient applied to the lag screw may not be applied to the STS. In the future, when diameters d1 and d2 of the thread and the coefficients of shank and shank cutter are applied, and the bearing strength for STS is calculated with the lumbers of various specific gravity to determine the appropriate empirical coefficient, a prediction formula for STS can be proposed. Our research team aims to derive a suitable empirical formula by calculating the bearing strength of STS for various species in the future.
4. CONCLUSION
In this study, STS was used to calculate the bearing strength for each load direction according to the grain direction of domestic Pinus densiflora. STS was 8, 10, and 12 mm in diameter, and the larger the diameter, the higher the yield load value in all grain directions of Pinus densiflora. The part with STS threads showed 11% lower strength value than the part without threads. As for the bearing strength of each direction of Pinus densiflora, the PL specimen parallel to the load and grain directions showed the best bearing strength, and the tangential section showed the lowest bearing strength. The bearing strength of the radial section was 19.3% lower than that of the cross section, and the bearing strength of the tangential section was 42% lower than that of the cross section. The strength ratio for each direction was calculated as 0.7 based on the specimen with parallel grain and load directions. The lumber bearing strength prediction formula using a lag screw was not suitable for STS bearing strength prediction. If an empirical formula is derived by calculating the bearing strength using tree species of various specific gravity in the future, the bearing strength prediction formula using STS according to the specific gravity can be proposed.