1. INTRODUCTION
When reinforced-concrete structures were developed in Europe in the early 20th century, it received attention as an economical material for building construction, and traditional timber structural began to be replaced by those constructed with mineral-based concrete and brick (Hong et al., 2015). At that time, the market share of wood compared with other building materials was 10% or less, and it was mainly used for timber light-weight constructions, such as residential buildings, nonresidential buildings and exhibition halls. Since then, wooden building construction and the market share of wood have increased as wood has replaced concrete in the construction of residential buildings, offices, schools, and other areas of construction. In addition, interest in wooden buildings has increased in countries where wood was not previously used. This is not only due to the development and adoption of engineered wood, such as glulam and laminated veneer lumber (LVL), but also the development of cross-laminated timber (CLT) panels in Austria in the early 1990s, which popularized the use of wood for medium-rise buildings (Antonio et al., 2021).
Subsequently, CLT (Fig. 1) began to be developed in the sawmill industry to look for its higher-value usage than in sideboards (Guttmann, 2008) and to utilize scrap wood (Sander, 2011), wood with low-machine grades, and waste wood (Cameron, 2013). CLT is a large wooden panel consisting of odd-numbered (3, 5, 7, 9) layers of semi-rigid composites or engineered wood boards where the cross-laminated layers are arranged at the 90° angle so that it can withstand both in-plane and out-of-plane loading (Ehrhart and Brander, 2018; Karacabeylli et al., 2013).
CLT, initially known by the German term Brettsperrholz (BSP), was classified as a sub-product of laminar- laminated timber product in terms of its shells, grid shells, and spatial 3D shells, and it later earned the designation “cross-laminated timber” (Schickhofer and Hasewend, 2000). The first residential building using CLT was constructed by Moser in 1995. In 1990, research was conducted in Central Europe, including Austria, Germany, and Switzerland, primarily by Graz University of Technology, which led to international research projects (Brandner et al., 2016). This research led to the development of CLT, and small- scale production facilities were built to begin its production in Europe in the early 2000s. Since then, production facilities have been built outside of Europe in countries such as Canada, the United States, Japan, China, and New Zealand, where production, R&D, and standardization activities are being actively carried out.
Research on CLT has led to an increase in the number of high-rise wooden buildings. This includes the construction of the following: Stadthaus, a wooden 9-floor apartment building in London, UK, in 2009 (Xiong et al., 2016); Forté, a wooden 10-floor apartment building (Li et al., 2019) in Melbourne, Australia, in 2012; Treet, a 14-floor apartment building in Bergen, Norway, in 2014 (Malo et al., 2016); and Brock Commons, an 18-floor wooden dormitory building at the University of British Columbia in Vancouver, Canada, in 2017 (Fast et al., 2016) (Fig. 2).
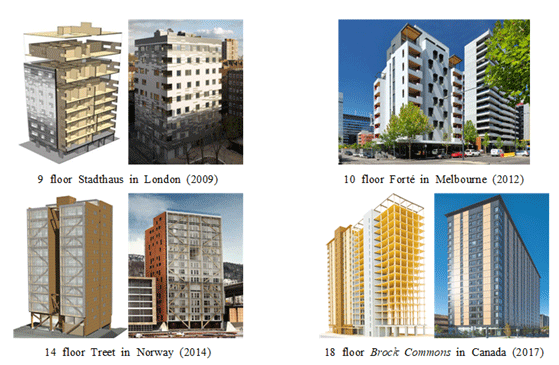
The increase in the construction of high-rise wooden buildings has led to the growth of the CLT market; annual CLT production in European was 25,000, 340,000, 650,000 m³ in 1996, 2010, and 2015, respectively. Production continues to grow rapidly and was forecast to have increased to 1.2 million m³ by 2020 (Brandner et al., 2016). In addition to the production increase in Europe, annual CLT production is also increasing in the United States, Canada, Australia, Japan, and New Zealand (Ipbal, 2018; Pei et al., 2016; Goto et al., 2018).
Along with the rapidly growing CLT market, research on CLT is being conducted globally due to the interest in this large wooden panel and its increasing use as a material for the construction of high-rise buildings. Various studies on CLT as a building material are being conducted to assess its material characteristics, such as its shear-wall structural performance, thermal characteristics, fire-resistance, performance at the joints, and sound-absorption (Jang and Lee, 2019; Kang et al., 2019; Choi et al., 2018; Ahn et al., 2021; Park et al., 2020). In particular, research is expanding on the development of CLT with enhanced strength characteristics and performance based on main species to each country's forest environment. This research is mainly focused on improving CLT’s relatively low block shear strength. The block shear strength varies depending on the layer arrangement. As an example, when the red pine species was for layers, the resulting glulam showed a strength of 10 N/mm² or higher, and CLT had a strength of 3.5 N/mm² (35% of the value for glulam) or higher (Kim et al., 2013). To improve this strength, the optimal quantity of applied adhesive and resulting shear adhesion strength were evaluated using Pine (Pinus koraiensis) while adjusting the pressure. The maximum shear adhesion strength was obtained when the quantity of applied adhesive was 250 g/㎡ the pressure was 0.8 MPa. This resulted in a maximum block shear strength of 6.07 N/mm², which not reach 7.0 N/mm² of the specified block shear strength in glulam standard (Park et al., 2017). The block shear strength increases with the increase in the ring angle of the cross-laminated layer. However, as for the failure mode for block shear strength, the shear strength applied to the CLT layers reached the annual rings before the cross-laminated layer, unlike in glulam, and the resulting failure mode showed the rolling shear failure mode along the annual rings (Kim et al., 2013; Song and Hong, 2016). It has been reported that rolling shear failure indicates a low block shear strength, explaining the low rolling shear strength of CLT.
Therefore, based on established CLT standard, this study intends to identify the current status of research on CLT strength according to the species used for the layers and hybrid CLT with the aim of improving rolling shear strength of CLT and to produce base data that can be utilized in the R&D on the localization of CLT.
2. MATERIALS and METHODS
CLT, which is mainly used as an structural member in buildings, has very important quality performance and relevant specifications and standards. CLT quality standards are specified in ISO 16696-1:2019, and different countries in Europe and North America along with Japan have their own definitions. For example, Europe enacted the “Timber Structure-Cross-Laminated Timber-Requirements” (BS EN 16351:2015) specification in 2008 (Brandiner et al., 2016), while in 2012, the United States and Canada adopted the “Standard for Performance-Rated Cross-Laminated Timber” (ANSI/ APA PRG 320) (Kaboli et al., 2020). In 2013, Japan enacted and promulgated the Japanese agricultural standard for CLT (JAS 3079, 2013) (Fujimoto et al., 2021). In 2020, Republic of Korea prepared a Korean Industrial Standard for structural CLT to provide a definition and quality standard for CLT products and to set performance standards and provide guidance on inspections. This standard is currently under review.
The CLT standards in each country provide strength values according to the fiber direction of each machine-graded class of layers, and the species used in the layered material vary depending on the forest environment of each country. In Austria, where CLT was first developed, C24, C18, and C16 strength grade Norway spruce (Picea abise) are mainly used (Brandner et al., 2016), although White fir (Abies alba), Scots pine (Pinus sylvestris), European larch (Larix decidua), Douglas fir (Pseudotsuga menziesii), and Swiss stone pine (Pinus cembra) are also used (Fink et al., 2018). In Australia and Canada, species such as Spruce (Piceaspp.), Lodgepole pine (Pinus contorta), and Douglas fir (Pseudotsuga menziesii) are used for CLT production (Zhou et al., 2014), while in the U.S., CLT specification states that spruce- pine-fir (SPF) lumber, Douglas fir, Larch, Eastern softwoods, Northern species, Western wood, and Southern pine are the species that can be used in the production of CLT (ANSI/APA PRG 320, 2019). Each country tends to prefer wood procured from their own territory.
The minimum specific gravity of timber used as a building material allowed by the Canadian Lumber Standards Accreditation Board standard, CASO141 (Bejtka and Lam, 2008), and the National Design Specification for Wood Construction (Kramer et al., 2014) is 0.35. This is the lower limit value of CLT for connection systems and the minimum specific gravity of species commercially available in north America, western United States, and northern Canada.
Although only the use of species with a specific gravity of 0.35 or more is allowed, the use of species other than those specified in the CLT specification is not limited. Therefore, the layer composition of CLT is selected in the manufacturing process to meet the requirements of the physical and mechanical properties. In particular, there are increased attempts to utilize locally abundant and underutilized wood resources for CLT layers, although they might not have the specified strength properties (Espinoza and Buehlmann, 2018). Sitka spruce (Sikora et al., 2016), Italian marine pine (Fragiacomo et al., 2015), European beech (Aicher et al., 2016 (a); Aicher et al., 2016 (b)), Southern pine (Hindman and Bouldin, 2015; Sharifnia and Hindman, 2017), hybrid poplar (Kramer et al., 2014), Eucalyptus (Liao et al., 2017), and Japanese cedar (Okabe et al., 2014) have all been researched for their use for CLT layers.
In Republic of Korea, larch (Larix leptolepis) is the species most commonly used for CLT layers. The number of layer species is expanding through research on the yield and strength characteristics of cedar (Cryptomeria japonica) and pine (Pinus densiflora), considering the forest environment other than larch, and the evaluation of block shear strength of CLT specimens using Korean pine (Pinus koraiensis) and tulip tree (Liriodendron tulipifera) as a layer material.
Although species differ depending on the forest environment of each country, softwood is commonly used in CLT layers. In tropical zone such as Malaysia and Indonesia with different climates, however, there are ongoing base studies on strength and other relevant properties of hardwood so that they can be used as CLT layers instead of soft wood (Hamdan et al., 2016). Since hardwood has a similar or greater strength than softwood with equal density, they are believed to be good materials with good potential for use in CLT layers (Yusof et al., 2019).
As presented above, modern CLT was first developed in Europe, but it has spread around the world, and research is ongoing to establish standards and production processes through the optimization of species that reflect each country’s forest environment and strength performance evaluations.
3. RESULTS and DISCUSSION
In the U.S. ANSI/APAPRA PRG 320 standard, which is the most commonly used of the many enacted standards, CLT is defined as a cross-laminated engineered wood with three or more layers of sawn lumber or structural composite lumber (SCL). SCL includes laminated veneer lumber (LVL), parallel strand lumber (PSL), laminated strand lumber (LSL), and oriented strand lumber (OSL) (Wood Handbook, 2021).
In general, CLT is used all over the world by manufacturing sawn lumber into glulam panels. CLT, which is arranged with alternate major and minor direction layers, has a out-of-plane shear strength and stiffness lower than those of in-plane flexural strength and stiffness. Therefore, when an out-of-plane load is applied, it causes excessive deflection followed by rolling shear failure due to the low out-of-plane shear strength, which is its principal drawback (Sylvian et al., 2011). The rolling shear phenomenon is shown in Fig. 3 and is closely related to the composition of wood cells. When shear force is applied to a bundle of longitudinally connected fiber in tangent and radial directions, the fibers do not break individually but roll off, resulting in rolling failure at the weakest point (Enhart and Brandner, 2018). Rolling failure is mainly found in softwood, and it is generated and transmitted at the boundary when shear forces are applied due to the density difference between the earlywood (with density of approximately 300 kg/m3) and latewood (with density of 900–1,000 kg/m3). The shear properties are determined according to the earlywood ratio and earlywood density of the layers used (Enhart and Brandner, 2018).
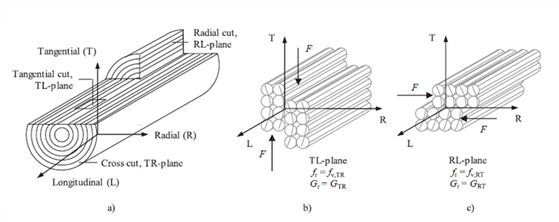
The rolling shear phenomenon that occurs in the cross-laminated layer of CLT is shown in Fig. 4, and it is reported that shear deformation may occur due to low rolling shear stiffness (Fellmoser and Blaß, 2004).
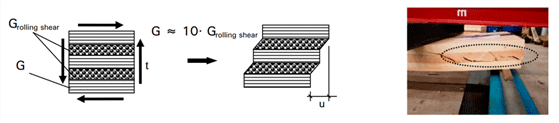
It has been reported that the rolling shear strength and stiffness in the cross layer of CLT affect the bending-load behavior due to material anisotropy (Mestek et al., 2008). To control rolling shears, studies have been conducted on a number of factors, including the species used as layers and their density, thickness, moisture content, sawing method, and the size and shape of the cross-section of the sawn lumber. These studies have confirmed that rolling shear is controllable (Steiger et al., 2008).
Research has mainly focused on improving rolling shear strength in the cross layers of CLT, which have low stiffness and strength. Examples of typical research include the use of hardwood as cross-laminated layers, changes in the angle of the layers, and the use of SCL structural panels such as LVL, LSL, plywood, and oriented strand boards (OSB) for the layers. This is called “hybrid CLT” or “composite CLT” (Fig. 5).
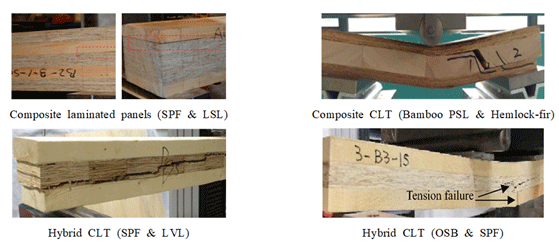
Studies are being conducted on CLT strength characteristics to expand the species utilized, such as the mixed use of softwood and hardwood as well as using tropical hardwood, to improve the low rolling shear strength of CLT layers.
Ehrhart et al. (2015) evaluated the rolling shear modulus and shear strength of six European species, including Norway spruce (Picea abies (L.) H. Karst), pine (Pinus sylvestris L.), birch (Betula pendula Roth), beech (Fagus sylvatica L.), poplar (Populus spp.), and ash (Fraxinus excelsior L.), as shown in Table 1. Although the rolling shear strength and modulus is depend on the sawing direction and the ratio of the width and thickness of the layer, hardwood species showed values of rolling shear strength and modulus about 1.3–2.3 times higher than softwood species.
fR,k (N/mm²) | GR,mean (N/mm²) | |
---|---|---|
Spruce | 1.4 | 100 |
Pine | 1.7 | 150 |
Poplar | 2.2 | 120 |
Birch | 2.7 | 180 |
Ash, Beech | 4.0 | 350 |
Aicher et al. (2016) assessed the rolling shear strength of European beech utilized as a layer material. EOTA 2015 (European Organisation for Technical Assessment), specifies 50 N/mm² as the rolling shear modulus for spruce and fir used as layer materials for design purposes. The rolling shear modulus of the European beech is measured to be 370 N/mm², which is about 7 times the stiffness of softwood, and the rolling shear strength is 4.5 N/mm². Based on this, European beech has been proposed as an ideal material for CLT layer material under out-of-plane load conditions (Aicher et al., 2016 (a)). Furthermore, Aicher et al. (2016) evaluated the bending performance of CLT manufactured by using a combination of spruce (Picea abies) layers (major direction) and European beech layers (minor direction). The results showed a rolling shear modulus of 350 N/mm² and a rolling shear strength of 2.6 N/mm². It has been reported that the high rolling shear properties can neglect the decreased in shear strength of softwood CLT (Aicher et al., 2016 (b)).
Wang et al. (2014) produced 3-ply CLT to review the usability of poplar as the layer material and compared the bending and shear strength properties (Table 2). When poplar was used with Douglas fir as the layer material, the bending strength was improved, but the modulus of elasticity in bending and shear strength decreased. When using poplar as the cross-layer material with Douglas fir or Monterey pine as the layer material, the bending strength, modulus of elasticity in bending, and shear strength were all reduced by 10%, 7.5%, and 9.2%, respectively, compared with using a single species. When poplar was used as a cross layer, it did not show a significant decrease in strength, so it was concluded that the mechanical properties of CLT using Douglas fir and Monterey pine layers and CLT including poplar were similar. Therefore, it is proposed that poplar can be used as cross-layer materials of CLT (Wang et al., 2014).
A number of studies have been conducted to improve rolling shear strength through evaluation of elastic coefficients in relation to layer angles and evaluation of the shear strength and stiffness of 3-ply CLT (Buck et al., 2016; Bahmanzad et al., 2020).
Bahmanzad et al. (2020) studied the shear strength properties of the Eastern hemlock species in relation to the angle of the cross-laminated layer arrangement in order to improve the planar shear of cross-laminated layers of CLT. The results of the elastic properties in relation to fiber direction and the short-span shear test on layer angle are set out in Tables 3 and 4. A cross-layer angle of 30° led to a shear failure strength 1.5 times greater than at 90° (Table 3), and 3-ply CLT arranged with a cross-layer angle of 30° demonstrated an effective shear stiffness 8.3 times greater than that of a cross-layer angle of 90° (Table 4). This confirmed that the failure mode caused by the cross-layer angle changes from rolling shear failure alone to tensile force and rolling shear failure. This supports the hypothesis that rolling shear and stiffness can be improved depending on the CLT cross-layer fiber orientation. Furthermore, the improvements shown in shear strength as a result of angle adjustments confirmed that it was possible to utilize low-quality wood for CLT through cross-layer angle adjustment for species that do not meet the required structural performance when the cross-layer angle is set at 90° during the CLT manufacturing process (Bahmanzad et al., 2020).
Species | Elastic properties (MPa) | ||||||
---|---|---|---|---|---|---|---|
EL | ET | G0° | G30° | G45° | G60° | G90° | |
Eastern hemlock | 8,300 | 276 | 520.56 | 191.68 | 104.11 | 83.43 | 61.36 |
Mid-layer angle | Peak load (kN) | EIapp (109 N・mm²/m) |
GAeff (106 N/m) |
fv,max (MPa) | |
---|---|---|---|---|---|
![]() |
90° | 88.3 | 117.3 | 9.5 | 2.03 |
![]() |
60° | 95.9 | 286.3 | 19.9 | 2.2 |
![]() |
45° | 102.7 | 375.9 | 34.9 | 2.4 |
![]() |
30° | 129.1 | 486.3 | 78.7 | 3.0 |
In addition to research on the mixing of softwood and hardwood and cross-layer angle changes to improve shear strength, research on evaluating shear strength is also being actively conducted by applying existing engineered woods, such as OSB, LVL, LSL, PSL, and structural plywood as cross-layer materials.
Although the current specifications do not provide strength values, design values, or other values for the different structural composite lumber (SCL) types, they also place no restrictions on their use as a layer material. Therefore, data on strength performance for engineered wood have already been existed, and interest in SCL is increasing as it has the advantage of increasing wood yield. Hybrid CLT (Fig. 5), in which SCL is used as a layer material, is utilized primarily with the aim of calculating strength values to be included in the CLT specifications established in each country.
Wang et al. (2015), Davids et al. (2017), and Niederwestberg et al. (2018) conducted research using LSL as layers, and Wang et al. (2017) conducted a study on the bending and shear strength properties of LVL following changes to the cross-layer and layer composition. Fujimoto et al. (2021), Choi et al. (2018), Pang et al. (2019), Choi et al. (2021), and Choi et al. (2020) conducted research into bending properties and block shear strength when using structural plywood as a CLT cross-layer material, while Li et al. (2020 (b)), using OSB, and Li et al. (2020 (a)) and Nurdiansyah et al. (2020), using bamboo boards as a layer material, conducted research into shear properties according to the changes in layer composition and number of laminated layers. The results of the research into the bending and shear strength properties of hybrid and composite CLT are shown in Table 5 and 6.
CLT type | Panel type | Panel lay-up | Layer direction* | Specimen dimension (mm) | Span-depth ratio | Major direction | |
---|---|---|---|---|---|---|---|
MOE (GPa) | MOR (MPa) | ||||||
Hybrid CLT (Wang et al., 2015) |
- | pine-pine-pine | //-⊥-// | 114(T)×197(W)×2,438(L) | 20 | 9.7 | 35.4 |
LSL | pine-LSL1)-pine | //-//-// | 10.8 | 44.0 | |||
LSL-pine-LSL | //-⊥-// | 11.2 | 44.2 | ||||
LSL-LSL-LSL | 11.6 | 48.2 | |||||
Hybrid SPFs-LSL CLT (Davids et al., 2017) |
- | SPFs-SPFs-SPFs | //-⊥-// | 114(T)×406(W)×2,560(L) | 20.4 | 7.3 | 40.7 |
LSL | LSL2)-LSL-LSL | 5.3 | 33.4 | ||||
LSL-SPFs-LSL | 5.5 | 33.6 | |||||
SPFs-LSL-SPFs | 7.0 | 50.1 | |||||
Composite laminated panels (Niederwestberget al., 2018) |
- | SPF-SPF-SPF-SPF-SPF | //-⊥-//-⊥-// | 184(T)×195(W)×2,743(L) | 13.6 | 8.0 | 110 |
LSL | SPF-LSL-SPF-LSL-SPF3) | //-//-//-//-// | 9.5 | 164.5 | |||
LSL-SPF-LSL-SPF-LSL | //-//-//-//-// | 11.6 | 205.4 | ||||
LSL-SPF-LSL-SPF-LSL | //-⊥-//-⊥-// | 8.9 | 106.3 | ||||
Hybrid SPFs-LVL CLT (Wang et al., 2017) |
- | SPF-SPF-SPF | //-⊥-// | 114(T)×89(W)×2,000(L) | 16.4 | 7.9 | 28.6 |
LVL | SPF-LVL4)-SPF | 7.2 | 25.7 | ||||
LVL-SPF-LVL | 9.3 | 30.1 | |||||
Korean Larch CLT (Song and Hong, 2018) |
Plywood | L-L-L5) | //-⊥-// | 81(T)×170(W)×1,700(L) | 18.5 | 9.2-10.1 | 43.9-47.1 |
Korean Pine CLT (Pang et al., 2021) |
PL-PL-PL6) | //-⊥-// | 90(T)×300(W)×2,900(L) | 30 | 8.0-8.8 | 28.2-30.1 | |
Ply-lam (Fujimoto et al., 2021) |
Plywood | C-P-C-P-C7) | //-//-//-//-// | 150(T)×300(W)×3,450(L) | 21 | 12.3 | 49.0 |
CLT with plywood (Choi et al., 2018) |
D-P-D-P-D8) | //-//-//-//-// | 40(T)×40(W)×600(L) | 13 | 10.8 | 67.8 | |
D-P-D-P-D9) | 8.6 | 43.9 | |||||
Ply-lam CLT (Choi et al., 2021) |
L-P-L-P-L10) | //-//-//-//-// | 75(T)×300(W)×2,400(L) | 29 | 15.1 | 61.6 | |
D-P-D-P-D11) | //-//-//-//-// | 13.0 | 65.5 | ||||
Tropical Hybrid CLT (Nurdiansyah et al., 2020) |
Bamboo laminated board | L-B.S-L12) | //-//-// | 54(T)×305(W)×1,260(L) | 19.6 | 21.83 | 39.41 |
Bamboo-wood composite cross laminated timber (Li et al., 2021) |
Bamboo woven panel (BMCP) |
L-L-L | //-⊥-// | 51(T)×145(W)×1,630(L) | 30 | 10.28 | 47.3 |
L-BMCP-L13) | //-//-// | 9.6 | 45.0 | ||||
BMCP-L-BMCP | //-⊥-// | 6.27 | 31.3 |
* // and ⊥ represent the parallel and perpendicular to the majoir strength direction of CLT, Hybrid CLT, composite CLT
4) SPF; shear modulus 84.92 N/mm², shear strength 1.41 N/mm² LVL was made from douglas fir (pseudotsuga menziesii) veneer, 2.0E grade (shear modulus 47.88 N/mm², shear strength 1.07 N/mm²)
5) L; korean larch (Larix kaempferi Carr.), outer tension laminae: 13 kN/mm², middle laminae: 7-9 kN/mm², outer compression laminae: 11kN/mm²
7) C; japanese cypress lamina, outer layer 11 kN/mm², inner layer 9 kN/mm², P; korean larch (larix kaempferi) plywood (major direction–MOE 10.9 kN/mm², MOR 44.1 N/mm², minor direction–MOE 5.19 kN/mm², MOR 18.7 N/mm²)
10) L; larch lamina (outer 11 kN/mm², inner 9 kN/mm²), P; korean larch plywood. thickness 15 mm, density 0.5 g/cm³, MOR 42.8 N/mm², MOE 7.1 kN/mm²
11) D; douglas fir lamina (outer 12-13 kN/mm², inner 9-10 kN/mm²), P; korean larch plywood. thickness 15 mm, density 0.5 g/cm³, MOR 42.8 N/mm², MOE 7.1 kN/mm²
CLT type | Panel lay-up | Layer direction* | Specimen dimension (mm) | Span-depth ratio | Shear strength (MPa) |
---|---|---|---|---|---|
Hybrid SPFs-LSL CLT (David et al., 2017) |
SPFs-SPFs-SPFs | //-⊥-// | 114(T)×406(W)×823(L) | 5.4 | 2.03 |
LSL-LSL-LSL | 2.61 | ||||
LSL-SPFs-LSL | - | ||||
SPFs-LSL-SPFs | 2.96 | ||||
Composite laminated panels (Niederwestberg et al., 2018) |
SPF-SPF-SPF-SPF-SPF | //-⊥-//-⊥-// | 184(T)×195(W)×1,200(L) | 5.5 | 1.3 |
SPF-LSL-SPF-LSL-SPF | //-//-//-//-// | 2.9 | |||
LSL-SPF-LSL-SPF-LSL | //-//-//-//-// | 3.6 | |||
LSL-SPF-LSL-SPF-LSL | //-⊥-//-⊥-// | 1.4 | |||
Hybrid SPFs-LVL CLT (Wang et al., 2017) |
SPF-SPF-SPF | //-⊥-// | 114(T)×305(W)×610(L) | 5 | 2.25 |
SPF-LVL-SPF | 2.11 | ||||
LVL-SPF-LVL | 2.40 | ||||
Ply-lam (Fujimoto et al., 2021) |
C-P-C-P-C | //-//-//-//-// | 150(T)×300(W)×1,050 | 5 | 3.87 |
Hybrid CLT with OSB1) (Li et al., 2020 (b)) |
SPF-SPF-SPF | //-⊥-// | 72(T)×190(W)×720(L) | 9 | 3.6 |
SPF-OSB-SPF | //-//-// | 7.0 | |||
SPF-OSB-SPF | //-⊥-// | 6.7 | |||
OSB-SPF-OSB | //-⊥-// | 5.4 | |||
OSB-OSB-OSB | //-⊥-// | 6.4 | |||
SPF-SPF-SPF-SPF-SPF | //-⊥-//-⊥-// | 120(T)190(W)×1,200(L) | 3.7 | ||
SPF-OSB-OSB-OSB-SPF | //-//-//-//-// | 5.9 | |||
SPF-OSB-OSB-OSB-SPF | //-⊥-//-⊥-// | 5.7 | |||
OSB-SPF-OSB-SPF-OSB | //-⊥-//-⊥-// | 3.7 | |||
OSB-OSB-OSB-OSB-OSB | //-⊥-//-⊥-// | 5.9 | |||
Tropical Hybrid CLT (Nurdiansyah et al., 2020) |
L-B.S-L | //-//-// | 54(T)×305(W)×270(L) | 4.6 | 6.93 |
Bamboo-wood composite cross laminated timber (Li et al., 2021) |
L-L-L | //-⊥-// | 51(T)×145(W)×406(L) | 6 | 2.4 |
L-BMCP-L | //-//-// | 3.3 | |||
BMCP-L-BMCP | //-⊥-// | 2.5 |
Wang et al. (2015) reported a 1.19 times increase in MOR and a 1.1 times increase in MOE when using LSL as a cross layer in existing CLT structures (species used for the layers was lodgepole pine [Pinus contorta]), and a 1.24 times increase in MOR and 1.15 times increase in MOE compared with existing CLT when utilizing LSL as the outermost layer and pine as the cross layer (Wang et al., 2015).
Furthermore, when Davids et al. (2017) and Wang et al. (2015) used LSL as the cross layer in SPF 3-ply CLT, MOR demonstrated a 1.23 times increase; however, MOE showed a similar average value and the rolling shear strength improved 1.45 times. When laminating the LSL in the same way as the general 3-layer CLT structure (arrangement //-⊥-//), rolling shear strength improved 1.28 times. This can improve the rolling shear strength when LSL is composed of CLT structure instead of sawn lumber (Davids et al., 2017; Wang et al., 2015).
Niederwestberg et al. (2018) researched bending and shear strength properties by preparing 5-ply CLT with SPF and LSL used as CLT layers. When using an LSL cross layer in SPF 5-layer CLT, MOR improved 1.49 times, MOE 1.18 times, and rolling shear strength 1.2 times. CLT (LSL-SPF-LSL-SPF-LSL-LSL with a parallel SPF layer) with LSL as the outermost layer demonstrated a 1.86 times improvement in MOR, a 1.13 times improvement in MOE, and a 1.77 times improvement in rolling shear strength. However, even with LSL used as the outermost layer, MOR, MOE, and rolling shear strength values were the same as those of CLT when the of 2 or 4-ply SPF was cross laminated (Niederwestberg et al., 2018; Davids et al., 2017).
Research by Wang et al. (2015), Davids et al. (2017), and Niederwestberg et al. (2018) confirmed that when using LSL as the cross layer, MOR improved 1.2 times and MOE 1.1 times. In particular, rolling shear strength improved 0.5–1.8 times. As the arrangement direction of LSL used as a cross-layer material is closely related to CLT bending properties, it was proposed that layers be placed in the same direction as the fibers to improve strength (Wang et al., 2015; Davids et al., 2017; Niederwestberg et al, 2018).
Wang et al. (2017) also researched bending and shear properties in relation to changes in the cross-layer and layer configuration while using SPF and LVL as CLT layers. Compared with SPF 3-layer CLT, CLT with LVL used as the cross-layer material showed a decrease in MOR by 10.1%, MOE by 8.9%, and rolling shear strength by 6.2%. This was determined to be due to the low planar shear properties of LVL when LVL was used in the orthogonoal direction for the cross layer (Fellmoser and Blaß, 2004). In addition, it was suggested that hybrid CLT can also improve bending strength performance due to the uniform mechanical properties of LVL as well as strength improvement when the outermost layer is used as LVL (Wang et al., 2017).
Fujimoto et al. (2021), Choi et al. (2018), Pang et al. (2019), Choi et al. (2020), and Choi et al. (2021) evaluated the strength characteristics of CLT with structural plywood laminated in a parallel direction to the CLT cross-layer material, known as ply-lam or ply-lam CLT (Fujimoto et al., 2021; Choi et al., 2018; Choi et al., 2021). Fujimoto et al. (2021) studied the manufacture and strength properties of ply-lam using Korean structural larch plywood (P) and a Japanese cypress layer (C) at the Miyazaki University and Wood Use Research Center in Japan. The composition of ply-lam consists of 5 layers (C-P-C-P-C) and the results of an MOR 49.0 MPa, an MOE 12.3 GPa, and a rolling shear strength 3.87 MPa showed results (Fujimoto et al., 2021). Choi et al. (2020) evaluated the block shear strength according to the lamination method of glulam, CLT, and ply-lam CLT. The block shear strength of ply-lam CLT was found to be over 7.1 N/mm², which is the glulam standard. Choi et al. (2021) manufactured ply-lam CLT using larch (machine grades E11, E9) and Douglas-fir layer material (machine grades E13–14, E9–10) and evaluated strength performance of ply-lam CLT. As there was no significant strength reduction according to the layer species and modulus of elasticity, they were able to confirm that the change in bending strength resulting from ply-lam CLT cross-layer plywood using different species was not significant (Choi et al., 2021). Song and Hong (2018) also conducted a study on the bending strength of larch (layer machine grades E13, E9, E11) in 3-ply CLT. Among the layers used for larch CLT and ply-lam CLT, the mechanical grades of the outermost layer subjected to compressive stress were different, but compared to CLT, the ply-lam CLT reported improved MOR 1.3 times and 1.5 times (Song and Hong, 2018).
Li et al. (2020 (b)) manufactured hybrid CLT using SPF and OSB and evaluated rolling shear strength according to the number of layers and direction of the arranged layers. In 3-layer CLT, it was reported that shear strength improved by 1.94 times when OSB was applied to the cross layer in the fiber direction, and 1.86 times when applied in the direction perpendicular to the fibers in the cross layer. In addition, when 2, 3, 4-ply were placed in the direction of the OSB fiber in a five-layer SPF CLT, the shear strength improved 1.59 times. It has been shown that the shear strength of the CLT cross-arranged with the OSB as in the general CLT structure is improved by 1.59 times than that of the general SPF CLT. Unlike previous studies on LVL and LSL, where single panels were placed in the same direction, OSB had a slight strength reduction of less than 5% depending on the direction of the cross-layer arrangement. LSL and OSB panels have the same arrangement of strands in the direction of the fiber, but as the adhesive area in the width direction is large due to the difference in width of strand between LSL and OSB (LSL strands are 12–16 mm and OSB strands are 30–80 mm), the shear strength was presumed to improve when at right angles to the fiber (Li et al., 2020 (b)). There was a difference between LSL and OSB not only in the size of the strand used but in the direction of the strands. Unlike LSL, in which the strands are arranged in a single direction, OSB has a multilayer structure, with the strands in each layer arranged differently, and it is manufactured by cross laminating in the same way as plywood. As the difference in strength as a result of fiber direction is not significant, it is presumed that there is no difference in strength as a result of fiber direction when used as a CLT layer material.
Nurdiansyah et al. (2020) studied the bending and shear properties of CLT by combining acacia laminate (Acacia mangium willd.) and bamboo solid boards. As a result, due to the high MOE of bamboo solid boards, CLT showed the highest MOE and shear strength values (Nurdiansyah et al., 2020). Li et al. (2021) used a hem-fir and bamboo woven panel (BMCP) as a layer material and evaluated the strength characteristics of three-ply CLT according to the layer composition. When using BMCP as the cross layer in conventional CLT, the bending characteristics showed similar values, but the shear strength increased 1.37 times from 2.4 MPa to 3.3 MPa (Li et al., 2021).
Research is continuously being conducted on the use of previously developed engineered wood and structural wood panels as cross-layer materials in order to improve the low rolling shear strength of CLT cross layers and the raw material yield. When structural composites such as LSL, LVL, OSB, plywood, and bamboo board are used as the cross-layer material, it can be seen that the strength is improved by up to 2 times for rolling shear, up to 1.5 times for MOE, and up to 1.35 times for MOR.
Therefore, it was decided that the selection of the structural wood material for manufacturing hybrid CLT suitable for the required strength characteristics is important because the bending characteristics of the structural wood material layer affect the shear and bending characteristics of the CLT (Davids et al., 2017; Wang et al., 2015).
When assessing prior research results indicating that the fiber orientation in materials used as cross-layer materials, such as LSL and LVL, may lead to a lower strength compared with conventional CLT, the direction of the CLT layers needs to be taken into account. However, for materials with the same bending properties both in terms of the fiber direction and direction orthogonal to the fiber, such as structural plywood and BMCP, strength in the minor direction can also be achieved when these panels are placed in the outermost layer.
4. CONCLUSION
In this study, basic data that can be used in the R&D for localization of CLT by analyzing the research and development trend of hybrid CLT to improve the low rolling shear strength of CLT, a large wooden panel used in high-rise wooden buildings in Europe and the United States, etc. was intended to provide. As a measure to improve shear strength, the strength characteristics of CLT were compared by using hardwood, changing angle of lamina, and using structural wood-based materials. The result is as follows.
-
When comparing the rolling shear strength and shear modulus of softwood and hardwood used to manufacture CLT, hardwood has both rolling shear strength and shear modulus values up to twice as high as those of softwood. The use of hardwoods a cross-layer material has advantages such as improvement of rolling shear properties and utilization of unused species, but it is judged that it is necessary to additionally evaluate the adhesion performance between softwoods and hardwoods.
-
CLT cross-layer materials are currently manufactured with a 90° arrangement, but we confirmed that adjusting the angle of the layers can lead to a 1.5 times improvement in rolling shear strength of CLT, an 8.3 times improvement in its shear modulus, and a 4.1 times improvement in its bending stiffness. Accordingly, it is judged that it is possible to improve the strength of CLT as well as expand the use of wood with low mechanical grade by adjusting the angle of layer arrangement.
-
By using structural wood-based materials with a proven strength performance, such as LVL, LSL, and plywood, for the CLT cross layer, MOR improved by up to 1.35 times, MOE by up to 1.5 times, and the rolling shear strength 1.59 times. Structural wood-based materials used in hybrid CLT with improved strength had bending property values of MOE 7.0 GPa or higher and MOR 40.0 MPa or higher. It can be confirmed that this is the standard of the bending characteristics of the structural wood-based material that can be used as a cross-layer material. In particular, materials manufactured by layering in the direction of the fiber and at right angles to the fiber, such as structural plywood and OSB, demonstrate a small difference in strength depending on the fiber direction of the test piece when an out-of- plane load is applied. When used as a layer material for CLT, it is judged that uniform strength values out-of-plan and in-plane strength can be obtained. However, for materials arranged in the same strand direction as LSL, as the bending properties are degraded to some extent when subjected to out-of-plane loads, materials with the same fiber orientation, such as LVL and LSL, require further study with a focus on the composition of their layers.