1. INTRODUCTION
Since timbers that have a smaller diameter such as thinning logs have a poor yield as boards or square lumbers, boxed-heart timbers can be considered to use as an efficient method. However, since a boxed-heart timber includes juvenile wood that largely forms growth stress, there is a problem that drying defects such as checks, splits, and warps are easily produced. In order to solve this issue, studies have been conducted to find a method of drying timbers after mechanically processing them such as longitudinal kerfing and incising.
The longitudinal kerfing was proposed to prevent drying defects which often occur when drying logs with pith, such as V-type cracks (Hsu and Tang, 1974). This is known to be effective in preventing the occurrence of surface check in the early stage of drying process by inducing the concentration of stress in the groove formed in a cross section (Jung et al., 1997). In addition, although the longitudinal kerfing does not affect the drying rate much, it can influence the distribution of the final moisture content after the drying process. It can also be treated with the incising (Lee et al., 2016a; Lee et al., 2017).
The incising treatment is a method to create an artificial knife on timbers for the purpose of facilitating chemical injection to refractory wood species. It was reported that the treatment can be processed even prior to the drying process and help not only in the chemical injectability but also in reducing the duration of the drying process (Islam et al., 2009). Moreover, the knife processed on the wood surface could suppress the occurrence of the surface check by evenly dispersing the tensile stress of the surface layer at the initial phase of the drying process (Lee et al., 2017). However, the knife processed on the surface reduces several mechanical characteristics of wood (Winandy and Morrel, 2007; Park et al., 2008). In particular, since the increase in the incising density leads to the decrease in the physical characteristics, the incising density should be low when it is used as a pretreatment for the drying process (Lee et al., 2016a; Suzuki et al., 1996).
The effects of these pretreatments on the drying defects in coniferous boxed-heart timber are varied depending on the factors such as tree species, size, etc., and the bigger the size of the cross section, the more the effect tends to increase. Although several studies (150 mm thick pine, 150 mm and 180 mm thick hemlock and radiata pine) said that the longitudinal kerfing reduces the twist of the boxed-heart timber (Lee et al., 2016b; Lee et al., 2016c), other studies (200 mm thick pine, 210 mm and 220 mm thick nut pine) reported that it does not affect the reduction of the twist (Lee et al., 2013; Lee et al., 2014). In addition, it was described that the incising can make the knife of a boxed-heart timber of 200 mm thick pine evenly disperse the tensile stress of the surface layer (Lee et al., 2017), but it was said that the knives joined together resulting in the conversion to the surface check in a boxed-heart timber of 250 mm and 300 mm thick douglas-fir (Lee et al., 2016a).
The drying defects are an important factor of processing yield after the drying process, and the surface check deteriorates the quality of the dried woods. Furthermore, the twist affects the processing yield greater than the surface check does. Thus, a study needs to be conducted on the effects of the kerfing and incising pretreatments on major drying defects which occur during the drying process of cedar and larch boxed-heart timbers. Accordingly, this study aims to identify the effects of the kerfing and incising pretreatments on the high-temperature drying characteristics of cedar and larch boxed-heart timbers processed to a cross section of less than 150 mm.
2. MATERIALS and METHODS
Cedar (Cryptomeria japonica, L.F. D.Don) and larch (Larix Kaempferi C.) were selected as published tree species. The trees were processed into square and round timbers with the length of 2,400 mm, thicknesses and diameters of 90 (9), 120 (12), and 150 (15) mm. The species were prepared that contain each of the five square timbers and six round timbers, according to the tree species, sizes of cross section, and pretreatment conditions.
The test materials were classified into control (C), incising (I), kerfing (K), and combination of kerfing and incising (KI), based on pretreatment conditions. The incising pretreatment processed with a blade thickness of 2 mm, depth of 10 mm, and incising density of approximately 2,400/m2 (Fig. 1(a)), and the kerfing pretreatment processed to a width of 3 mm and depth of 1/3 of the size of cross sectionusing a circular saw (Fig. 1(b)).
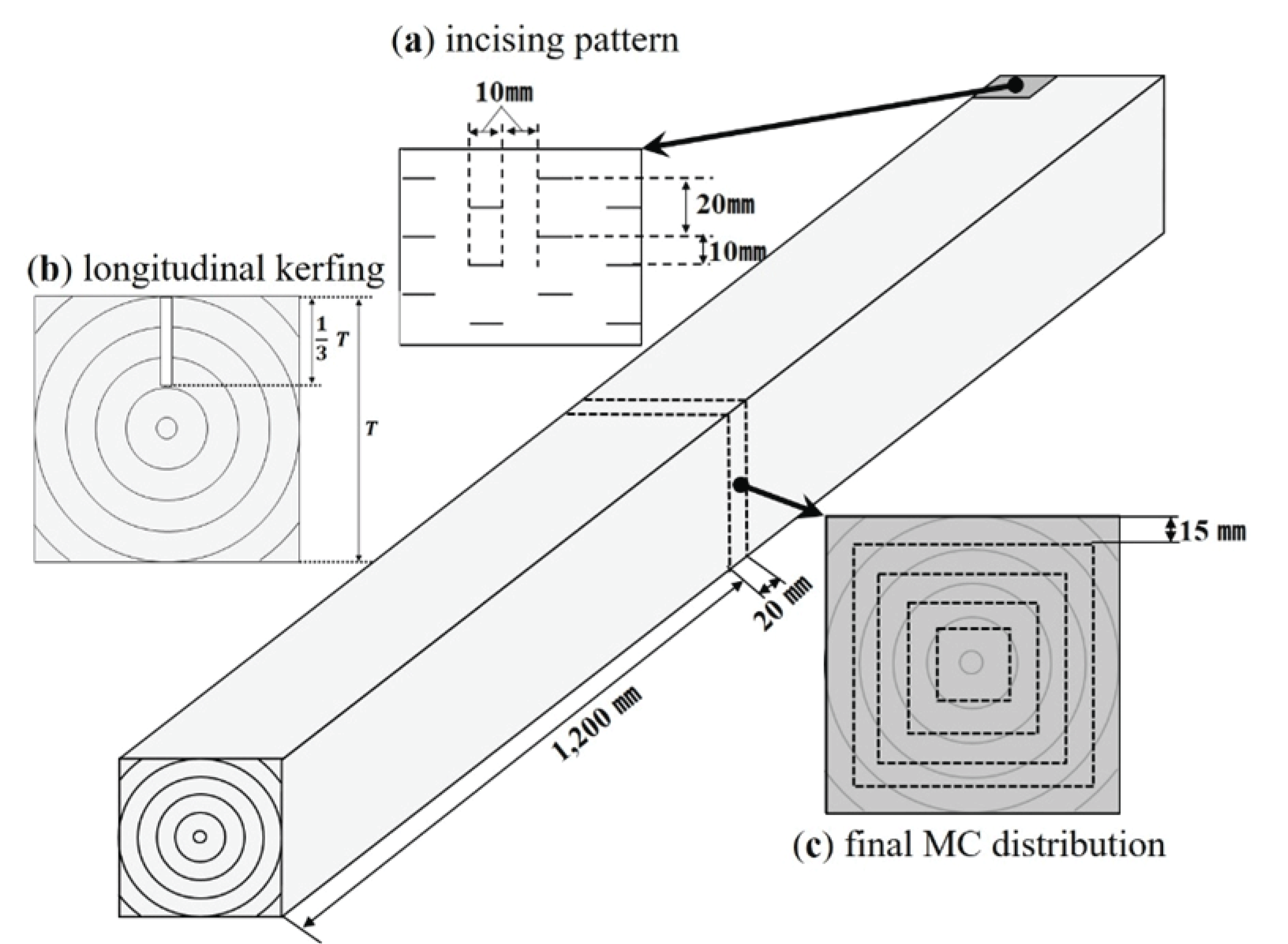
The drying test was performed between April and May by a 40 m3 commercial hot air drying machine. The drying schedule was set as shown in Table 1, based on the results of studies by Lee et al. (2013), Lee et al. (2014), Lee et al. (2016b; 2016c), and Lee et al. (2017), as well as considering the sizes of the test speciesused in this study.
Stage | Time (Hours) | Dry-bulb (°C) | Wet-bulb (°C) |
---|---|---|---|
1 | 12 | 95 | 95 |
2 | 36 | 120 | 90 |
3 | 96 | 90 | 70 |
24 | 25 | - | |
Total time | 168 |
The weights of all test materials were examined prior to the drying process. The heaviest one in each pretreatment condition was selected as a representative test material and used for the moisture content examination after the drying process. The final MC was analyzed by collecting test pieces of 20 mm thickness at the spot of 1,200 mm from the cross section and using an oven-drying method. The final moisture content distribution was investigated by dividing the collected test pieces by 15 mm intervals from the surface (Fig. 1(c)). The initial MC was calculated from the changes in weight and the final moisture content of the test materials before and after the drying process.
For the surface check, the width and length of the check that has the width of at least 2 mm were examined in all test materials after the drying process. Since the maximum width of the investigated surface check was 5 mm, the average surface check length based on the pretreatment conditions was calculated by the following equation:
where, lw length of each surface check with width 2-5 mm, N number of species.
The twist was tested only in the square timbers, and it was measured four times each in both cross sections per test material and eight times in total after the drying process.
The shrinkage and kerf widening rate were examined to find the width of the kerf and to measure the changes in thickness and diameters at the spot of 1,200 mm from the cross section before and after the drying process using a Vernier caliper.
Ws: width of a circular saw,
Wk: width of the kerf after drying
3. RESULTS and DISCUSSION
Table 2 shows the result of regression analysis between various factors of woods and the drying characteristics of larch and cedar boxed-heart timbers. The analysis result indicated factors that have made significant differences as follows: 1) tree species, shapes, sizes of cross sections, and the initial moisture content in the final moisture content; 2) sizes of cross sections, and pretreatments in the surface check; 3) shapes, sizes of cross sections, pretreatments, and the initial moisture content in the shrinkage; and 4) tree species in the twist.
The pretreatments had largely affected the surface check, and showed a significant difference in the shrinkage. In the surface check, the kerfing process was the major factor indicating a significant difference. Regarding the shrinkage, it was determined that each pretreatment affected the final moisture content distribution, which led to a significant difference.
The final moisture content and distribution showed significant differences based on the tree species, sizes of cross sections, shapes, and the pretreatment conditions (Figs. 2~3, Table 3). The moisture content of the square timbers was higher than that of the round timbers, and the increase in the size of the cross section led to the increase of the moisture content after the drying process. Although the pretreatment conditions were not significant as a result of the regression analysis, it showed a tendency of decreasing the moisture content in the order of I – K – KI.
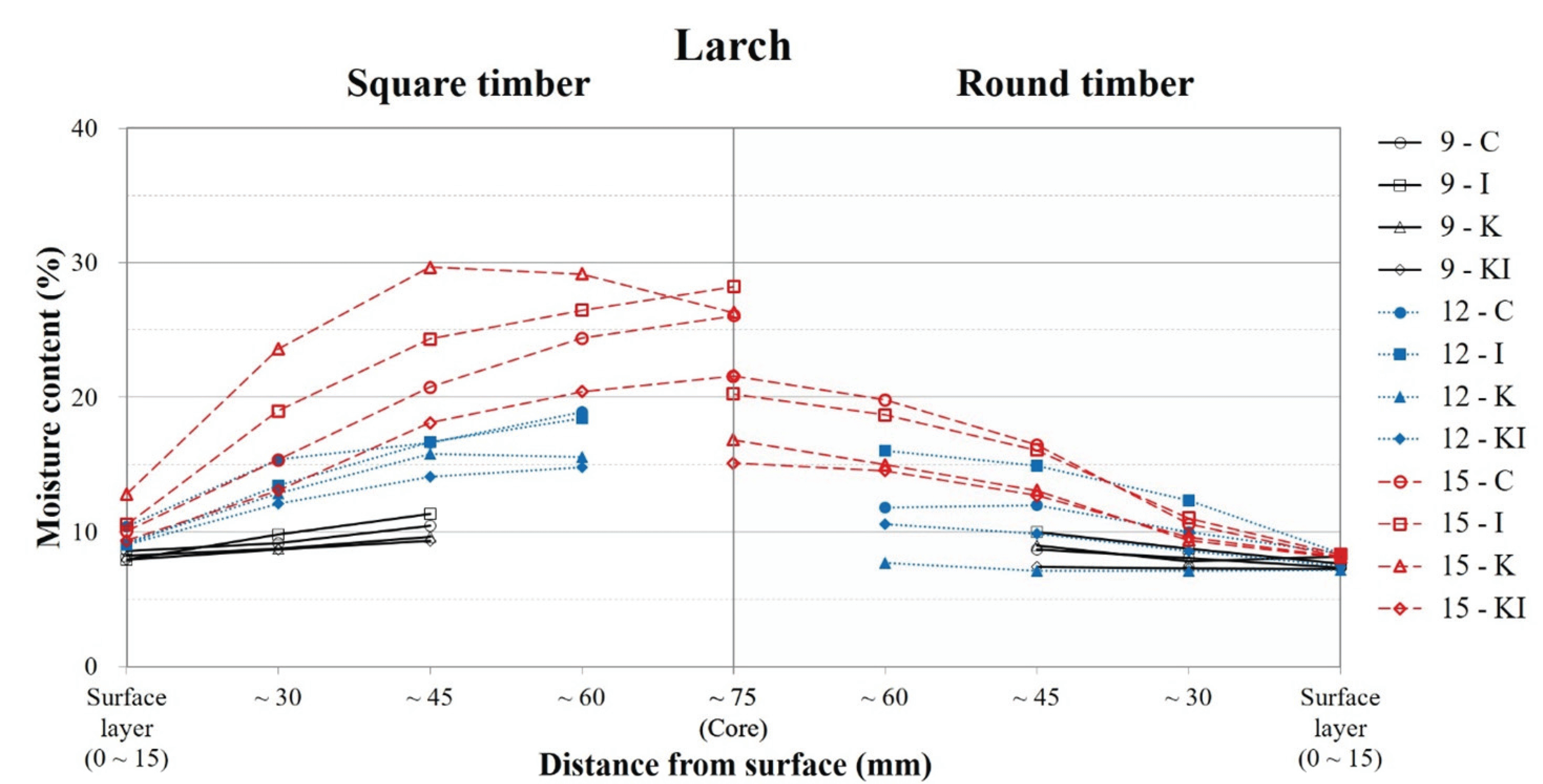
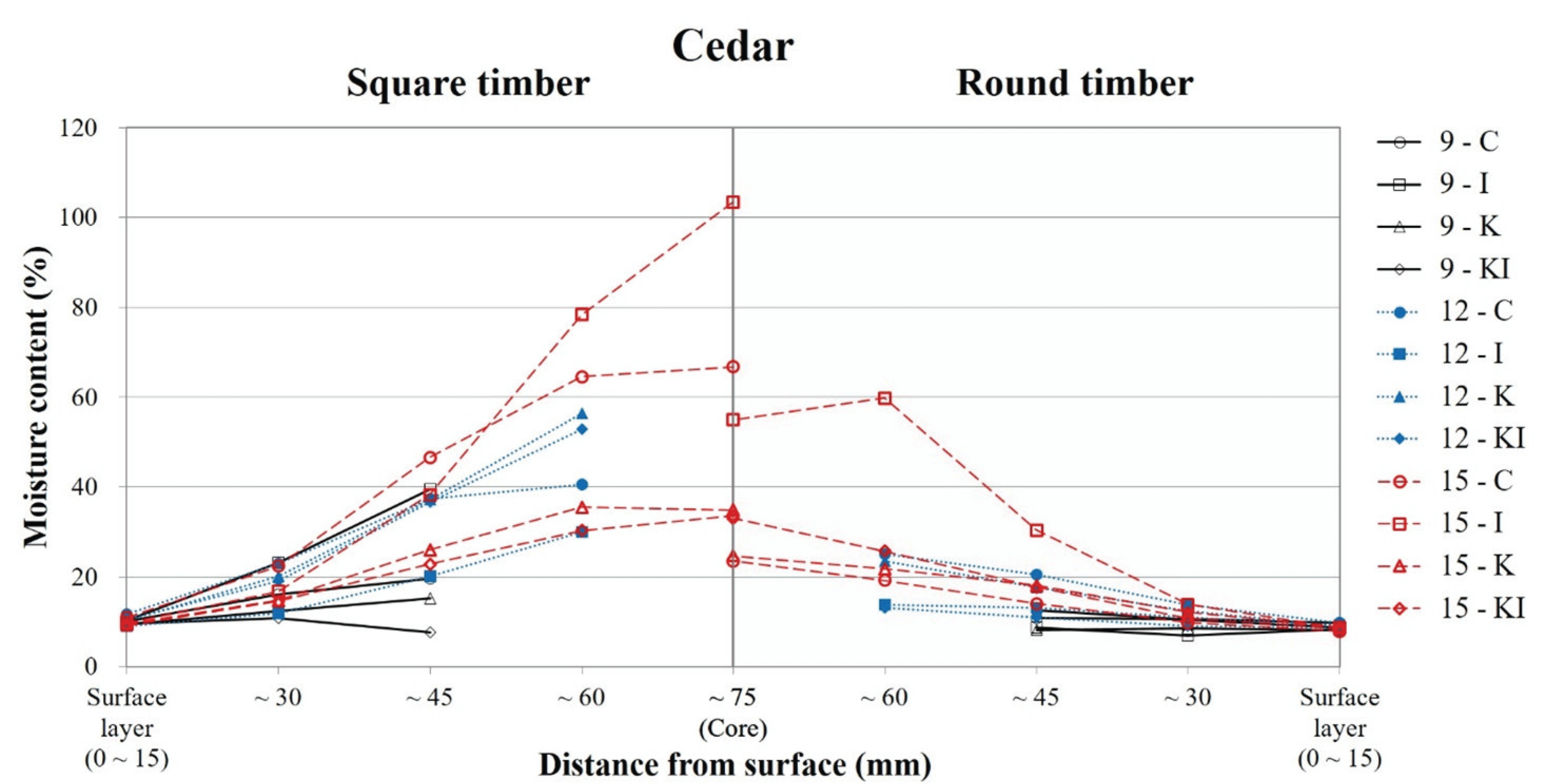
Permeability was affected by the factors, such as specific gravity, extractives, and late wood percentage, and varied depending on the tree species (Hur and Kang, 1997; Jee and Kim, 1996). Moreover, the moving distance of moisture from the center of the woods to the evaporation surfaces was affected by the factors, such as the shape of the woods, sizes of cross sections, and the pretreatment condition (Lee et al., 2013; Lee et al., 2016a; 2016c). In particular, the heartwood area of cedar is known to be the most difficult to dry since it has a high initial moisture content with poor permeability (Hermawan et al., 2012). It is also shown to have high moisture content after the drying process in this study. Hence, it is considered that the moisture content results investigated in this study were based on the final moisture content and distribution affected by the following: 1) tree species, sizes of cross sections, shapes, and pretreatments and 2) drying schedule which was uniformly applied regardless of tree species, shapes, and sizes.
Meanwhile, the study found that several test materials have higher values of moisture content despite having low initial moisture contents. This tendency was noticeable in cedar trees that have the initial moisture content in the range of 30 ~ 50%, and similar tendencies were shown in 150 mm thick larch square timbers. In general, given the same time for the drying process, the wood with high initial moisture content shows higher moisture content after the drying process. However, bordered pit aspiration which occurs when the wood is dried reduces the permeability of the wood after the drying process to the level between 1/10 and 3/10 (Erickson and Crawford, 1959). The incidence of the bordered pit aspiration is also varied due to the drying conditions (Fujii et al., 1997). Furthermore, regarding a commercial-scale drying test, the test material is exposed to the outdoor air for a longer time during preparation of the test than in industrial site and small-scale tests. Therefore, the moisture content of the surface layer may be reduced prior to the initiation of the drying test, and the bordered pit aspiration may be emerged during the process. Accordingly, the several test materials showed relatively higher moisture content after the drying process despite their lower initial moisture content. This was presumed to be because the factors, such as moisture content of the surface layer and border pit aspiration, were affected while the test materials were exposed to the outdoor air before the drying process, which in turn affected the final moisture content and distribution after the drying process.
The average length of surface check based on the width of the investigated checks after the drying process is shown in Fig. 4 and 5, and it displayed differences depending on the sizes of the cross section and pretreatment conditions.
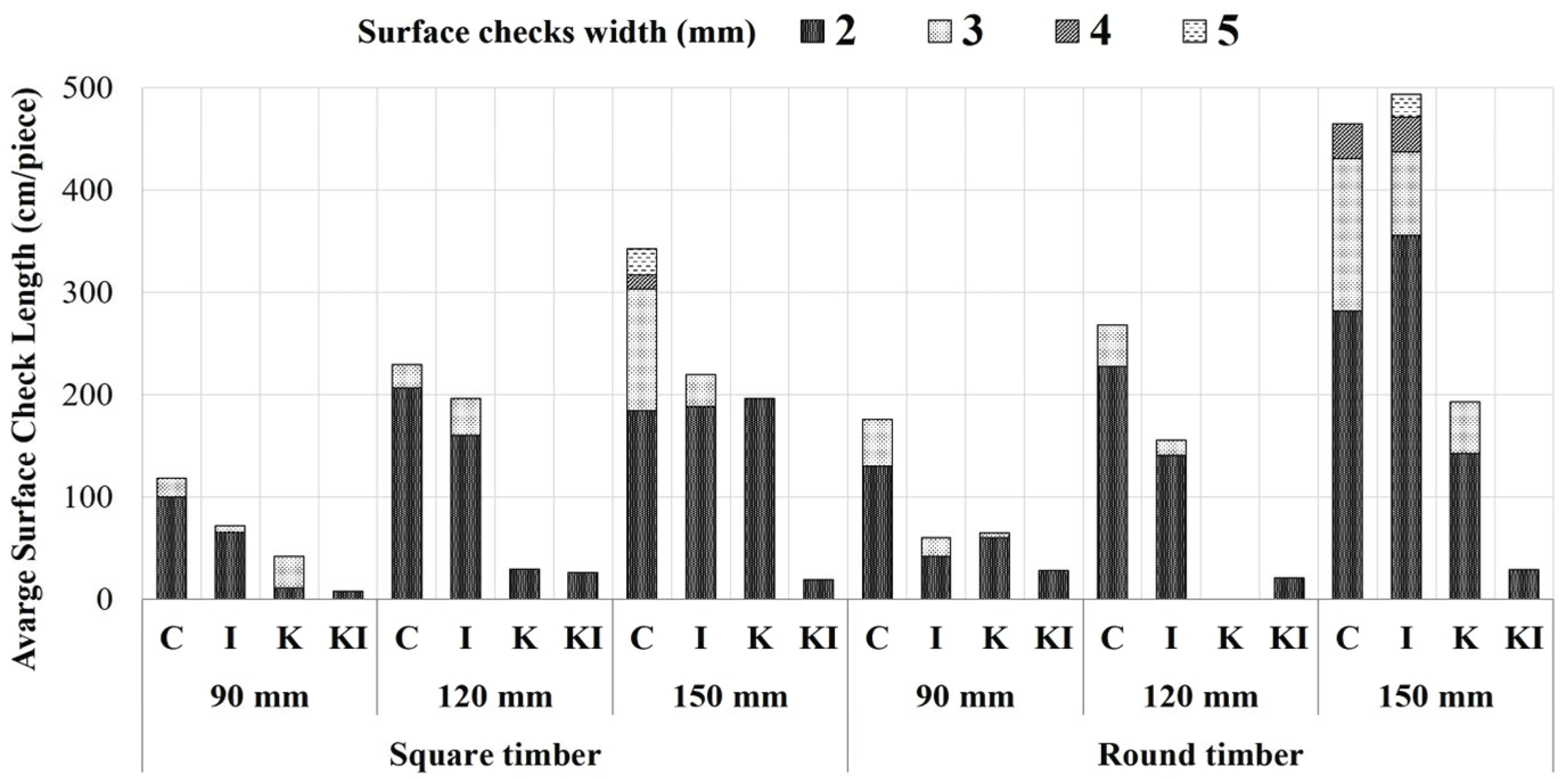
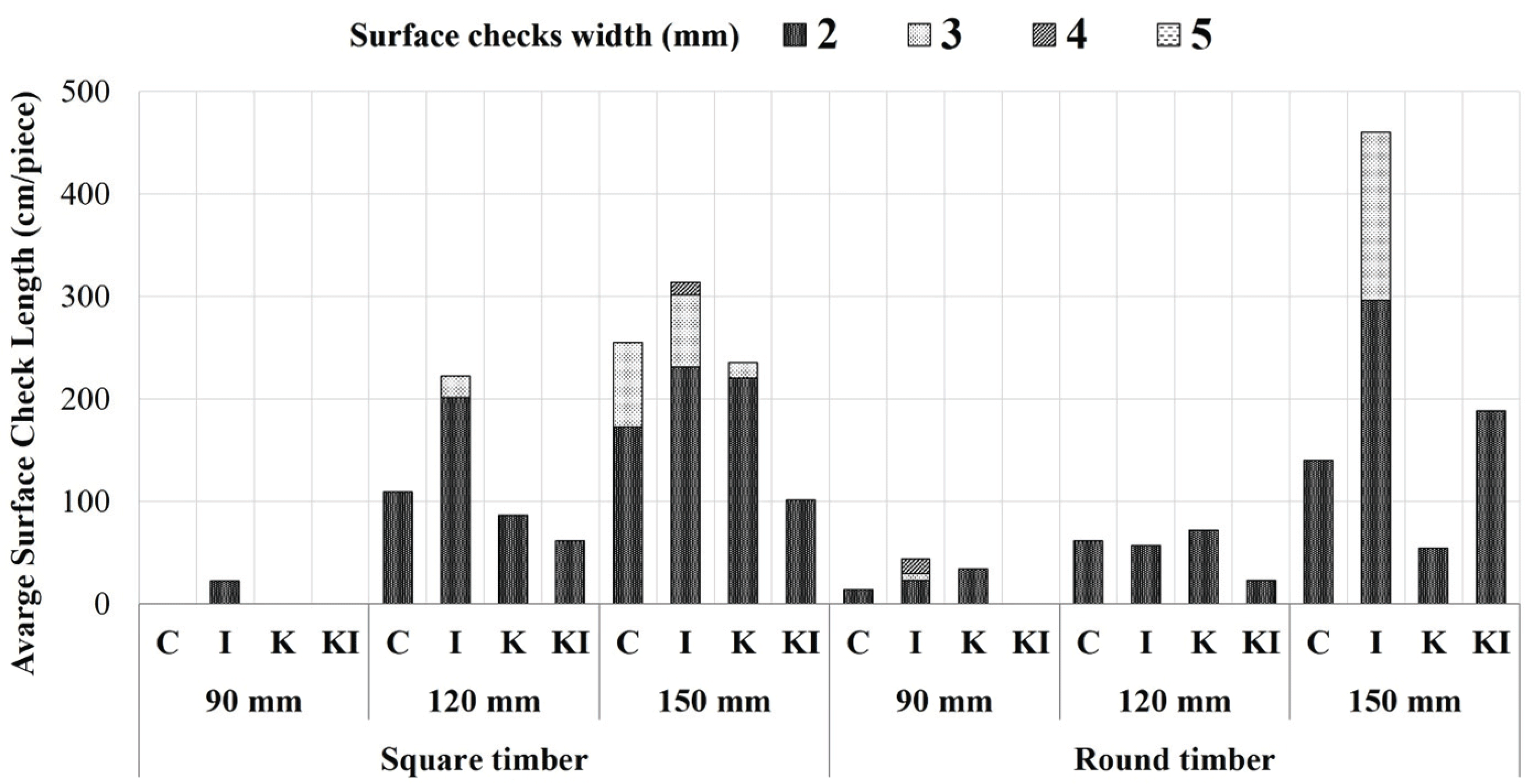
As the thickness of the wood increases, the large moisture profiles are formed. As a result, the surface layer is placed under a higher tensile condition. Moreover, since a longer time is required until the moisture inside is removed, the conversion of the tensile stress formed on the surface layer to compressive stress is delayed. Thus, the difference in the surface check based on the size of the cross section is caused because a large tensile stress is formed on the surface layer as the thickness increases, and the stress reversal is delayed, which makes the surface check to occur more easily.
The effects of kerfing and incising pretreatments on the occurrence of surface check were comprehensively reviewed along with previous studies (Lee et al., 2013; Lee et al., 2014; Lee et al., 2016a; 2016b; 2016c; Lee et al., 2017). As a result of the review, the kerfing was proved to be suitable as a pretreatment for reducing the surface check. However, the kerf widening rate indicated that it had no correlation to the surface check (Table 4). This is because even if the kerf is expanded in the early stage of the drying process, the kerf widening rate is affected by the shrink behavior and creep effect based on the decrease in moisture content in the inner layers after the middle stage of the drying process. On the other hands, the incising was determined to be not suitable as a pretreatment since it caused the conversion into the surface check as each knife joined together. However, it is considered that the incising can be used as a pretreatment method for boxed-heart timbers, if the size and gap of the incising are adjusted to the extent that it can prevent each knife joining together.
Meanwhile, in the condition above the fiber saturation point, the drying is proceeded rapidly as the initial moisture content increases (Han et al., 2019a). Furthermore, the equilibrium moisture content in the period when the wood is exposed to the outdoor air (April~May) before the drying process was 9.6 ~ 11.7%, which was the period when natural drying was easily performed (Han et al., 2019b). Since the surface of the boxed-heart timber is configured with a tangential section, not only the moisture is quickly evaporated, but also the bordered pit aspiration and surface check occurred in this process cause a negative impact on the permeability and drying defects of the wood (Amer et al., 2019; Lee et al., 2014).
In addition, regarding thick woods such as the boxed-heart timber, even if the moisture content at its core is indicated to be above the fiber saturation point, the movement of free water during the drying process cannot be removed as quickly as it was on the surface layer (Kim et al., 2017; Park et al., 2020). Furthermore, since the pressure inside the timber increases with the increase in temperature during the drying process, the boiling point of water increases, so that most of the free water at the core cannot be evaporated in the form of steam, but remains as liquid. Therefore, the movement of the free water located at the core of the test material is interfered. Particularly, since this problem is occurred more severely with a poor permeability, it leads to more severe moisture profiles on the surface and inner layers. In addition, as the time of maintaining the moisture profiles on the surface and inner layers is prolonged, it is affected by creep, which leads to its impact on the shrinkage. Thus, it causes a negative impact on the occurrence of the closed checks after the middle stage of the drying process.
Therefore, the followings are significant factors causing the occurrence of the surface check in addition to the sizes of the cross section and pretreatments shown in the results of the regression analysis: 1) differences in inner moisture content due to a poor permeability of the cedar boxed-heart timber; 2) effects of creep; 3) changes in moisture content on the surface layer by exposure to the outdoor air before the drying process.
The shrinkages of the cedar and larch boxed-heart timbers are shown in Figs. 6~7. The shrinkage of the timber appears with the changes in moisture content, and the kerfing and incising pretreatments cause differences in moisture moving distance from the core of the timber to the evaporation surface. This may also affect the stress behavior which occurs inside the timber during the drying process (Lee et al., 2016a). Moreover, creep and tension set which occur inside the timber during the drying process show differences based on the tree species, sizes of cross section, and the ratio of sapwood-heartwood. As the size of the cross section increases, the shrinkage decreases due to the effects of creep and tension set (Hwang and Park, 2009; Lee et al., 2016c; Yamashita et al., 2014). This shrinking behavior indicates differences depending on the degree of moisture profiles formed inside the timber and time of its maintenance, and it plays a role as a significant cause of the drying defects. In addition, as previously mentioned, a commercial- scale drying test is exposed to the outdoor air for a relatively longer time during its preparation. Therefore, the shrinkage of the boxed-heart timber is caused by following factors affecting the stress behavior inside the timber: 1) anisotropy of juvenile wood; 2) moisture removed during the exposure to the outdoor air; 3) difference in moisture of surface and inner layers (the degree of moisture profiles); 4) differences in permeability based on the tree species; and 5) drying time and creep effect based on the sizes of the cross section. It is also considered that the stress behavior inside the timber affected the occurrence of surface check and twist.
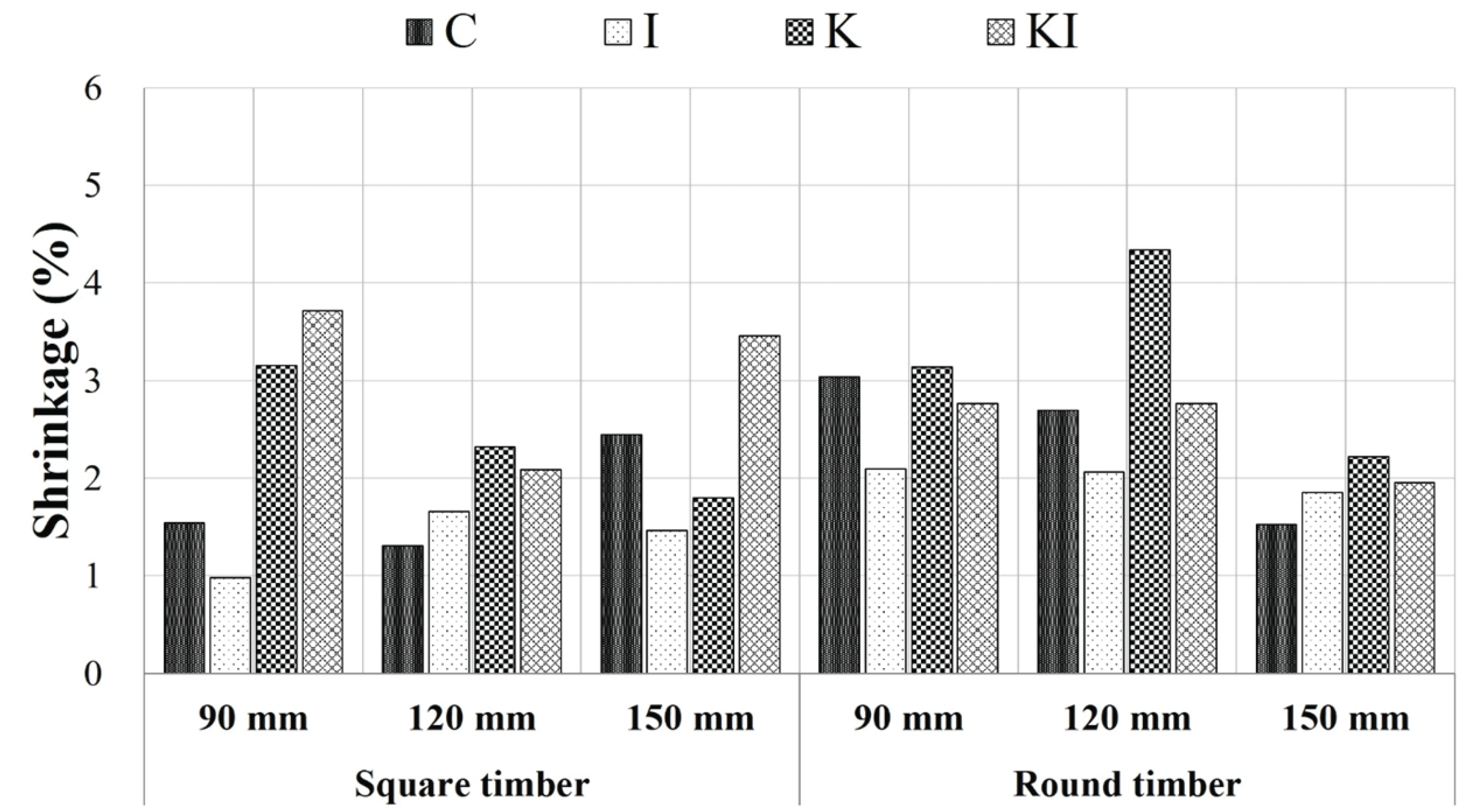
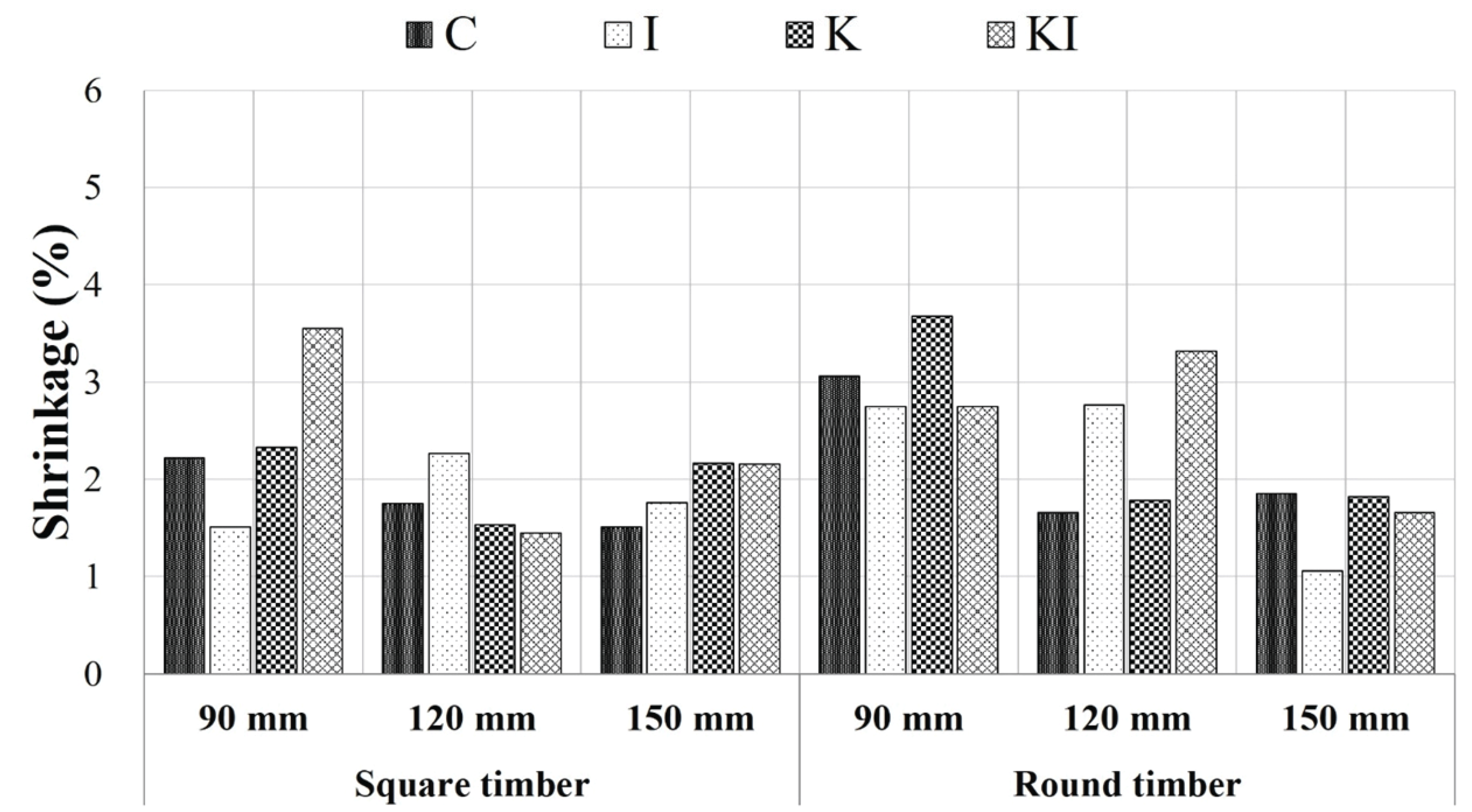
The twist of cedar and larch square timbers is shown in Fig. 8, and it showed that a more severe twist occurred in larch than cedar. Although juvenile wood has a severe anisotropy, the twist of timber is related to the distance from the pith and grain angle. In particular, the grain angle is the most significant factor of the twist occurrence (Frühwald 2006; 2007; Nilsson et al., 2007; Kubojima et al., 2013; Straže et al., 2011). Thus, the cause of the difference in twist between two tree species is the grain angle, and the difference in twist based on the thickness in each tree species is due to the anisotropy of the juvenile wood. Furthermore, since the twist was more severely occurred on larch than cedar, it was considered that the twist of boxed-heart timbers was affected by the grain angle more than by the anisotropy of the juvenile wood.
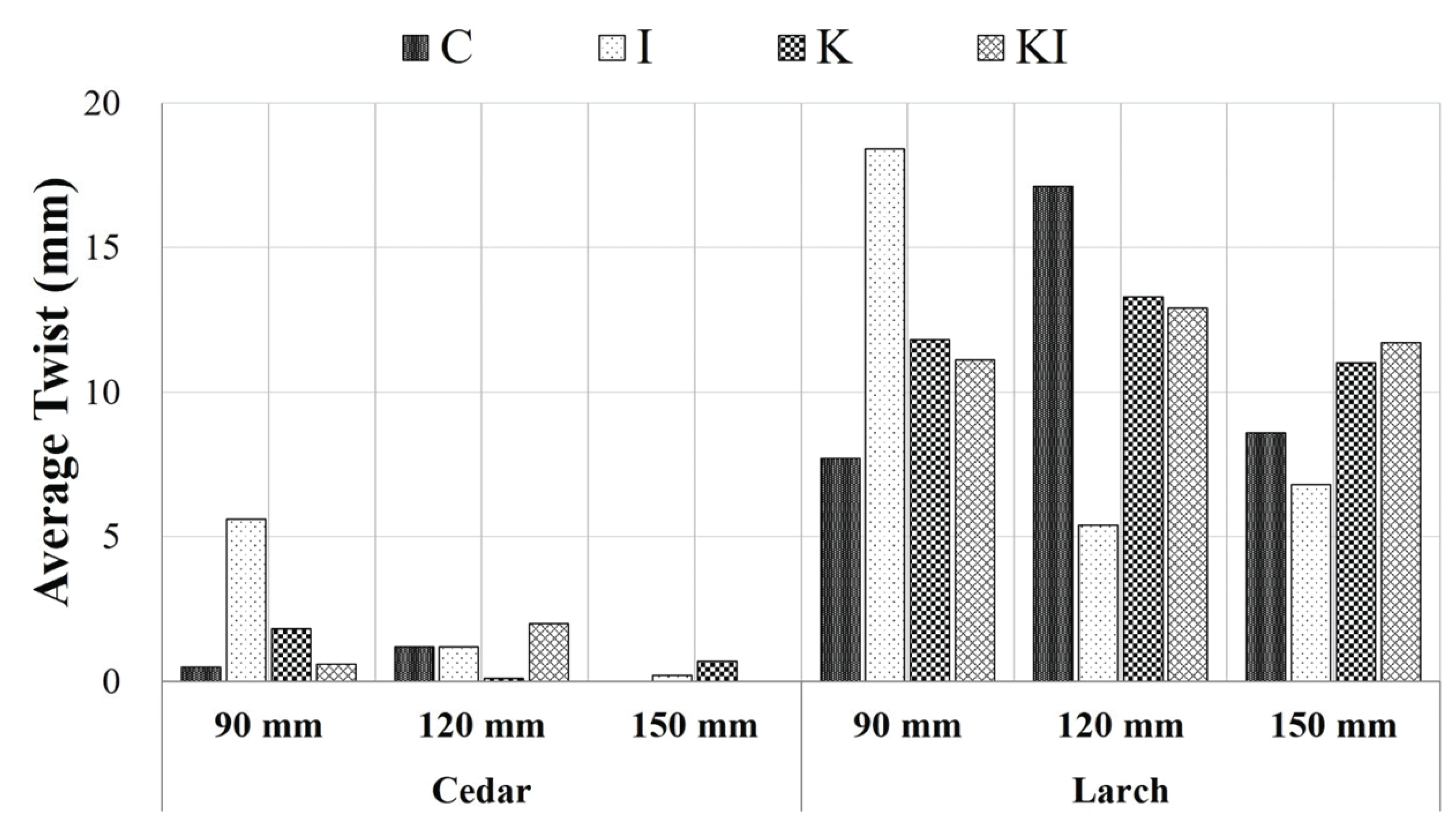
Since a commercial-scale drying test consumes a tremendous amount of time for its preparation, there is a problem that test materials are exposed to the outdoor air for a longer time in the industrial site. In order to derive a result which can be applied to the industrial site, this study prepared a total of 264 cedar and larch boxed-heart timbers without using dummy boards by filling a commercial drying machine with the size of 40 m3 to perform the drying test between April and May (spring). Nevertheless, this study was able to observe the differences of the shape of test material, size of cross section, initial moisture content, and kerfing and incising pretreatments in high-temperature drying characteristics of cedar and larch boxed-heart timbers. Thus, the drying schedule used in this study maybe applied to the industrial sites if it is improved based on tree species, shapes, and sizes. Since the industrial sites have a shorter time for the exposure to the outdoor air than in this study, it is also considered that the effects of the outdoor air can be reduced.
Meanwhile, the study was able to identify that the moisture content inside the test materials shown in Fig. 2 and 3 had a significant difference from the final moisture content shown in Table 3. As reported by Lee et al. (2016a), this is because the ratio of volume possessed by each surface layer and inner layer with respect to the entire volume of the timber, or the solid volume, displayed a large difference. Given the 150 mm thick square timber used in this study as an example, the ratios that each layer possessed based on the distance from surfaces are as follows: 0~15 mm - 36%, ~30 mm - 28%, ~45 mm - 20%, ~60 mm - 12%, and ~75 mm - 4%. Therefore, even though the moisture content at the core and areas adjoined with the core showed high values, it has a small impact on the final moisture content. Thus, if the drying time is excessively applied based on the moisture content at the core of timber at the industrial sites, an unnecessary energy waste and additional defects may occur due to the excessive drying process. Regarding thick timbers such as the boxed-heart timbers, it will be important to evaluate the moisture content suitable for the purpose of products based on “one-fourth to one-fifth thickness rule (ASTM 1968)”.
The reality is that the industrial sites require information which can be immediately applied to manufacture and processing of products. In order to provide study results that conform with the needs from the site, a commercial-scale study needs to be conducted. However, timbers show differences by tree species, population within the species, and areas within the population. Therefore, for the timber specimens, there is no other option than preparing different conditions including ages of hardwood, areas processed within population (large end diameter and upper end diameter), configuration ratio of cross section (heart timber ratio and summerwood ratio), etc. Furthermore, since it takes a tremendous amount of time for sawing, pretreatment processing, and basic data research prior to the drying process compared to a research center-scale test, it is highly difficult to control the environment where test materials are exposed to the outdoor air during the preparation of testing.
However, this does not mean that controlling such problems is impossible. The first method is to proceed with the test in winter. In winter, moisture evaporation takes the longest time during the test preparation. Thus, it is the period when the problems caused by the exposure to the outdoor air before the drying process can be minimized. The second method is to reduce the time required for sawing, pretreatment processing, and basic data research prior to the drying process by minimizing the quantity of timber species. Finally, it can be considered to come up with the third method to filling vacant spaces inside the drying room with dummy, etc. Through these methods, the problems occurred in a commercial-scale study can be minimized. However, the drying process is not only proceeded in winter at the industrial sites, and if the quantity of timber species is reduced, the test results may be indicated differently due to timbers which belong to dummies filling the vacant spaces inside the drying room. Hence, the first method can be the most effective when proceeding with a commercial-scale drying test, and properly combining the second and third methods may be an alternative depending on the situations.
4. CONCLUSION
This study was performed to identify the effects of kerfing and incising pretreatments on high-temperature drying characteristics of cedar and larch boxed-heart timbers with the size of the cross section less than 150 mm. The study results displayed significant differences of the pretreatments only in the surface check and shrinkage. Significant differences were shown in each drying characteristic based on the following factors: 1) final moisture content – tree species, shapes, sizes of cross section, and initial moisture content; 2) surface check – sizes of cross section and pretreatments; 3) shrinkage – shapes, sizes of cross section, pretreatments, and initial moisture content; and 4) twist – tree species. For the surface check, the kerfing treatment was the major factor which showed a significant difference, whereas for the shrinkage, the pretreatment condition showed a significant difference as it reduces the final moisture content after the drying process in the order of I – K – KI.
Although the kerfing was suitable as a pretreatment for reducing the surface check, the incising was not suitable as a pretreatment since each knife joined together to cause a conversion to the surface check.
For the twist, the grain angle affected more than the anisotropy of the juvenile wood, and there were no effects of pretreatments.