1. INTRODUCTION
Timber products refer to 15 different types of products prescribed by the Presidential Decree of the Act on the Sustainable Use of Timbers (the Timber Use Act) (Korea forest service, 2018). wood charcoal briquette is one type of timber product, and the criteria for standard dimensions and quality are defined in Annex 14 of the National Institute of Forest Science Public Notification 2018-8 “Criteria for Standard Dimensions and Quality of Timber Products” (National institute of forest science, 2018). The wood charcoal briquette defined in the Public Notification encompasses products that are shaped into certain forms after being carbonized from raw materials such as wood, woodchips from bamboo or seeds and nuts, wood shavings, or bark, as well as products that are shaped into forms from carbonized sawdust using additives. The wood charcoal briquette is categorized into sawdust charcoal briquettes, charcoal powder briquettes, and molded charcoal for kidling holed coal briquette, depending on the manufacturing methods. While quality criteria for ash content, fixed carbon, and high heating value are different depending on the type of wood charcoal briquette, the same criteria for heavy metal content apply to all products in this category, except for barium, which is used as a complexing agent (National Institute of Forest Science, 2017). In addition, the use of construction wood wastes, residential wood wastes, wood treated with pesticides, wood treated with preservatives, and other materials including wood, bamboo, seeds and nuts, sawdust, shavings, and barks that are suspected of contamination with harmful compounds are restricted (National Institute of Forest Science, 2017).
When it comes to logging in the Republic of Korea, cutting volume is estimated to be 7,670,000 m3 in 2016, and products collected as a result are estimated to be 5,250,000 m3, therefore leaving 2,420,000 m3 of unused forest biomass (Korea forest service, 2017). Thus, it is imperative that the unused forest biomass that makes up 32% of the total cutting volume utilized in various wood industries.
Domestic manufacturers of wood charcoal briquette have pursued diversification of the raw materials based on implementation of the Timber Use Act and National Institute of Forest Science Public Notification, and wood charcoal is currently produced primarily by using branches and roots of trees from the unused forest biomass (Korea Forest Service, 2018; Choi, 2018). Also, there had been an increased number of cases where the heavy metal content of wood charcoal briquette products is found to exceed the criteria. Current situations can be viewed as a progress towards standardization of wood charcoal briquette products, as integrated quality criteria for timber products are established and managed; however, currently no consensus exists among industry, academia, research instutions, the authorities, and private corporations (Ahn et al., 2013; Kwon et al., 2018; Yang and Han, 2018).
Most of the charcoal briquettes in the Republic of Korea are manufactured using an open hearth kiln, where a pit in the ground is prepared as a carbonization chamber, and raw materials are stacked in the chamber, carbonized at 300–400 °C, and extinguished using water or soil (Yang et al., 2017; Magnone et al., 2019). Afterwards, a new batch of raw materials is added on top of the carbonized materials, carbonized, and extinguished and this process is repeated several times. Once the carbonized materials reach the top of the carbonization chamber, they are removed from the chamber and used for manufacturing wood charcoal briquettes. Carbonization time varies within the materials produced by this method in that the lowermost layer undergoes carbonization for the longest time and the uppermost layer for the shortest time; also, impurities such as soil are concentrated in certain layers during the process.
For this, the research aims to evaluate the quality of carbonized materials produced by carbonization of unused forest biomass in an open hearth kiln, which is used for manufacturing wood charcoal briquettes. Carbonized materials are collected based on the time in which they are added to the carbonization chamber, and they are mechanically processed and sorted by particle sizes. Their fuel characteristics before and after carbonization are compared based on factors including time of addition, carbonization time, and particle sizes.
2. MATERIALS and METHODS
Materials produced in an open hearth kiln used by a wood charcoal briquette manufacturer located in Chilgok-gun, Gyeongsangbuk-do, Republic of Korea, were utilized in this research. Testing materials were the byproducts of afforestation efforts, purchased by the wood charcoal briquette manufacturer, which were composed of mixed softwoods. The raw materials were carbonized at approximately 700 °C and extinguished for approximately 80 hours. Hog of softwood (HSW) and 5 types of carbonized hog of softwood (CSW) are used in this research (Fig. 1). The carbonized hog materials were divided into 5 equal layers based on their vertical position within the kiln during carbonization, labeled as CSW1, CSW2, CSW3, CSW4, and CSW5 from the uppermost layer to the lowermost layer (Fig. 2). Samples were collected from each layer for testing, and the collected samples were double sealed and stored at room temperature for a better preservation.
Carbonized materials obtained from each layer were ground and sorted based on the particle sizes to analyze the distribution of their particle sizes, as shown in Fig. 3. All samples were dried for approximately 48 hours in an oven at 65°C prior to use to facilitate the subsequent screening process. A cutting mill (Pulverisette 19, FRITSCH, Germany) was used for the grinding process (Fig. 3-➀). The cutting mill was operated using a rotational speed of 300 rpm, and a sieve with 1 mm in diameter was used. Particle size sorting was performed using a vibratory sieve shaker (analysette 3, FRITSCH, Germany), with standard sieves of 40 mesh (0.4 mm) and 100 mesh (0.149). The materials were separated into 3 categories: particles with sizes above 40 mesh, between 40 and 100 mesh, and below 100 mesh, labeled as Top, Middle, and Bottom, respectively. The yield was calculated for each category at this stage using Equation (1) in order to analyze the distribution of particle sizes.
YP=Yield of the corresponding particle size (%)
WP=Weight of the corresponding particle size (g)
WS=Weight of the original sample (g)
Proximate analysis was conducted using a thermogravimetric analyzer (PrepASH229, Precisa, Switzerland) to analyze moisture content, volatile matter, ash, and fixed carbon contents of the samples. Approximately 1 g of material was used for the analysis. Analytical conditions were determined based on ISO 18122 Solid biofuels — Determination of ash content, ISO 18123 Solid biofuels — Determination of the content of volatile matter, and ISO 18134-3 Solid biofuels — Determination of moisture content — Oven dry method, published by the International Organization for Standardization (ISO). The fixed carbon content was calculated using Equation (2).
FC: Fixed carbon content (%)
MC: Moisture content ratio (%)
VM: Volatile matter content (%)
ASH: Ash content (%)
HHVs were measured uing a calorimeter (Parr 6400, Parr, USA), referring to ISO/DIS 18125 Solid biofuels — Determination of calorific value. Samples for analysis were prepared by accurately weighing 0.5 g of the powder and forming a pellet with a diameter of 13 mm under 10 tons of pressure, and they were completely dried in an oven at 105 ± 3 °C for more than 3 hours prior to measurement.
Elemental composition was analyzed using an elemental analyzer (vario MICRO cube elemental analyzer, elementar, Germany). Carbon, hydrogen, nitrogen, and sulfur contents were measured, and oxygen content was calculated according to Equation (3). Analysis conditions were as follows: samples underwent a complete combustion in the combustion chamber that was maintained at the temperature of 1150 ± 5 °C, and the gas generated from this process was purged using helium flowing at 600 mL/min to the reduction tube that was maintained at 850 ± 5 °C, where they were reduced to N2, CO2, H2O, and SO2 for analysis. 50 mg of the powder was used for the analysis, and Standard Reference Material® 2693 (National Institute of Standards and Technology, USA) was used as a reference. Samples were completely dried in an oven maintained at 105 ± 3 °C for more than 3 hours prior to elemental analysis.
C: Carbon content (%)
H: Hydrogen content (%)
N: Nitrogen content (%)
S: Sulfur content (%)
O: Oxygen content (%)
The energy yield (YE) of the samples obtained from the screening process was calculated using Equation (4). The equation is calculated based on dry weight.
YE = Energy yield (%)
HHVp = high heating value for the corresponding particle size (MJ/kg)
HHVS = high heating value of the original sample (MJ/kg)
3. RESULTS and DISCUSSION
Weight-based yields of the samples corresponding to each particle size which are categorized by the mechanical screening process, are shown in Fig. 4. The yields of Top (>40 mesh), Middle (40–100 mesh), and Bottom (<100 mesh) samples are distributed with the ranges of 43.6%, 30.6%, and 25.9%, respectively, for the HSW sample, which is not carbonized. The yields of Top, Middle, and Bottom are in the ranges of 10.7– 16.6%, 17.6–20.0%, and 63.8–71.2%, respectively, for the carbonized samples, CSW1 through CSW5. Previous studies have reported that carbonization of wood leads to thermal degradation of wood components, including hemicelluloses, celluloses, and some lignins, which causes an increase in carbon content and brittleness of wood (Lee et al., 2015; Mei et al., 2015). Therefore, it is understood that carbonized samples generate a greater amount of fine particles below 100 mesh when mechanically processed than the uncarbonized sample due to the greater grindability. While the carbonized samples show slightly different yields depending on their vertical position within the open hearth kiln during the carbonization process, the differences are rather not significant, and they indicated a relatively similar tendency of particles distribution.
Results of HHV measurements, proximate analysis, and elemental analysis are summarized in Table 1 for the uncarbonized HSW1 and 5 carbonized CSW samples. Samples from CSW1 through CSW5 exhibit lower volatile matter contents than the HSW by 53.5– 57.7%. The significantly lower volatile matter contents of the carbonized samples are thought to be caused by the removal of most of the volatile compounds as gas during the high-temperature carbonization process. On the other hand, ash and fixed carbon contents of the carbonized samples are 20.7–34.0% and 21.1–33.1%, respectively, which are higher than those of the uncarbonized sample (14.0% and 17.6%, respectively). A previous study has reported that mineral components within wood become concentrated in wood charcoal by 4–5 times during a carbonization process and remain as ash (Lee and Kim, 2010). It is thought that the higher ash content of the carbonized samples than that of the uncarbonized samples in this study can be attributed to similar reasons. The carbon content of HSW samples is measured to be 39.9%, and those of CSW1 through CSW5 range from 42.9% to 50.9%, which show a small increase. Lee et al. (2007) has reported that the carbon contents of Pinus Koraiensis carbonized at 300–400 °C range from 67.7% to 72.2%, which are higher than the carbon contents proposed in this study. We hypothesize that this difference, as well as the relatively high ash contents mentioned above, has been caused by a greater amount of soil and other impurities contained in the samples used in this study, which might have been mixed in when materials were collected from the ground after trees had been cut, during transport and storage of the collected materials, or during the carbonization process in the open hearth kiln. On the other hand, the carbonized samples had lower hygrogen and oxygen contents in most cases than the uncarbonized samples, which is thought to be caused by removal of hygrogen and oxygen in the form of steam and carbon dioxide, respectively, during carbonization. Nitrogen and sulfur contents are relatively small and do not exhibit significant changes. HHVs on average have increased after carbonization. Samples from the middle layer, CSW3, have the largest average HHV, 20.4 MJ/kg. Also, the bottom two layers (CSW4 and CSW5) exhibit smaller HHVs than the top two layers (CSW1 and CSW2) by approximately 1.7 MJ/kg. We conclude that HHVs of the carbonized materials produced in the open hearth kiln are not strongly affected by duration of carbonization but by blocked oxygen influx during the carbonization process.
Results of proximate analysis, elemental analysis, and HHV measurement for the carbonized samples (CSW) are summarized in Table 2 based on the particle sizes. Volatile matter and fixed carbon content are measured to be increased with decrease in particle size: these values for the Bottom particles, 15.5% and 52.3%, respectively, are approximately twice as large as the corresponding values for the Top particles, 7.4% and 26.0%, respectively. Ash content is observed to be decreased with decrease in particle size from 66.6% to 32.2%. It is thought that most of the impurities, such as soil, contained in the carbonized samples have sizes greater than 40 mesh, and as a result, they are concentrated on the Top layers during the grinding and sorting process. Carbon content exhibits a similar trend with the fixed carbon content, which increases with decreasing particle sizes; the Bottom particles are found to have the highest carbon content, 58.8%. On the other hand, oxygen content decreases with decrease in particle size, with a minimum of 38.2% exhibited by the Bottom particles. Hydrogen and nitrogen contents show a small increase as particle size decreases, and sulfur content does not show any significant changes. The Bottom particles also have the highest HHV, 21.3 MJ/kg, which is above the quality criteria for wood charcoal briquettes, 17.6 MJ/kg, prescribed in Annex 14 of the National Institute of Forest Sciences Public Notification 2018-8 “Criteria for Standard Dimensions and Quality for Timber Products.” A previous study has also reported that materials with smaller particle sizes exhibited a higher carbon content and high heating value when carbonized (Hwang et al., 2012), and that energy in the carbonized samples was concentrated in the Bottom particles (Hwang et al., 2012). Considering these results, it is concluded that selecting carbonized materials with smaller particle sizes in grinding and sorting processes will increase the quality of wood charcoal briquette, and this pre-processing is expected to be more effective for materials containing a large amount of impurities such as soil.
Results of energy yield calculations based on HHVs of each sample are shown in Table 3. The energy yield in this study considers both weight-based yield from the mechanical screening process and the measured HHVs, and it represents the ratio of the final energy that can be recovered through the screening process to the total energy contained in the original sample. The energy yields of the uncarbonized samples, HSW, are measured to be 0.46, 0.31, and 0.21 for the Top, Middle, and Bottom particles, respectively. The decreasing trend in energy yield with decreasing particle size is thought to be attributable to low grindability of the HSW samples, resulting in the lower yield of smaller particles, as shown in Fig. 4. On the other hand, the energy yields of the carbonized samples are measured to be 0.05–0.12, 0.12–0.17, and 0.70–0.82 for the Top, Middle, and Bottom particles, respectively, which indicate that the energy yields dramatically increase with decreasing particle size. It is understood that the carbonized samples generate more smaller particles which have larger HHVs, thus resulting in significant differences in energy yield in which these two factors are multiplied. The highest energy yield is observed in CSW1 Bottom, 0.82; the highest HHV is observed in CSW3 Bottom, 20.67 MJ/kg, while its energy yield (0.71) is on the lower side due to its relatively low yield. This is considered to be due to having a relatively lower weightbased yield when compared to its high HHV. While the total HHVs of HSW and CSW4 are similar, making it difficult to believe that the carbonization was successful, mechanical screening helps confirm successful carbonization of the CSW4 layer, shown by a large increase in HHV of the Bottom particles from CSW4 compared to those from the uncarbonized samples.
Correlations among HHV, volatile matter, ash content, fixed carbon, and carbon content of the Top, Middle, and Bottom particles of the carbonized samples CSW1 through CSW5 are presented in Fig. 5. Ash content in the carbonized samples is statistically highly correlated with the fixed carbon content, exhibiting the largest value of R2=0.9886; this is thought to be related to the clearly decreasing trend in ash content with decreasing particle size observed in this research. HHVs of the carbonized samples are highly correlated with the carbon content (R2=0.9085). This is thought to be caused by enrichment of C-C bonds, which have high bond energy, within the carbonized samples as the hydrogen and oxygen are removed during carbonization (Lee et al., 2016). In addition, HHVs exhibit a statistically significant positive correlation with fixed carbon content (R2=0.8363). HHVs of the carbonized samples with different particle sizes have a statistically significant negative correlation with ash content (R2=0.8551). This is thought to be related to the trend that ash content of the carbonized samples decreases as particle size decreases, while HHV increases, as shown in Table 2. The correlation between HHVs of the carbonized samples and volatile matters exhibits a scattered distribution and is therefore statistically insignificant. Ash, volatile matter, and carbon content have statistically significant negative correlations (R2>0.83). Volatile matters and fixed carbon have a positive correlation (R2=0.7956); likewise, carbon content, volatile matter, and fixed carbon have statistically significant positive correlations (R2>0.75).
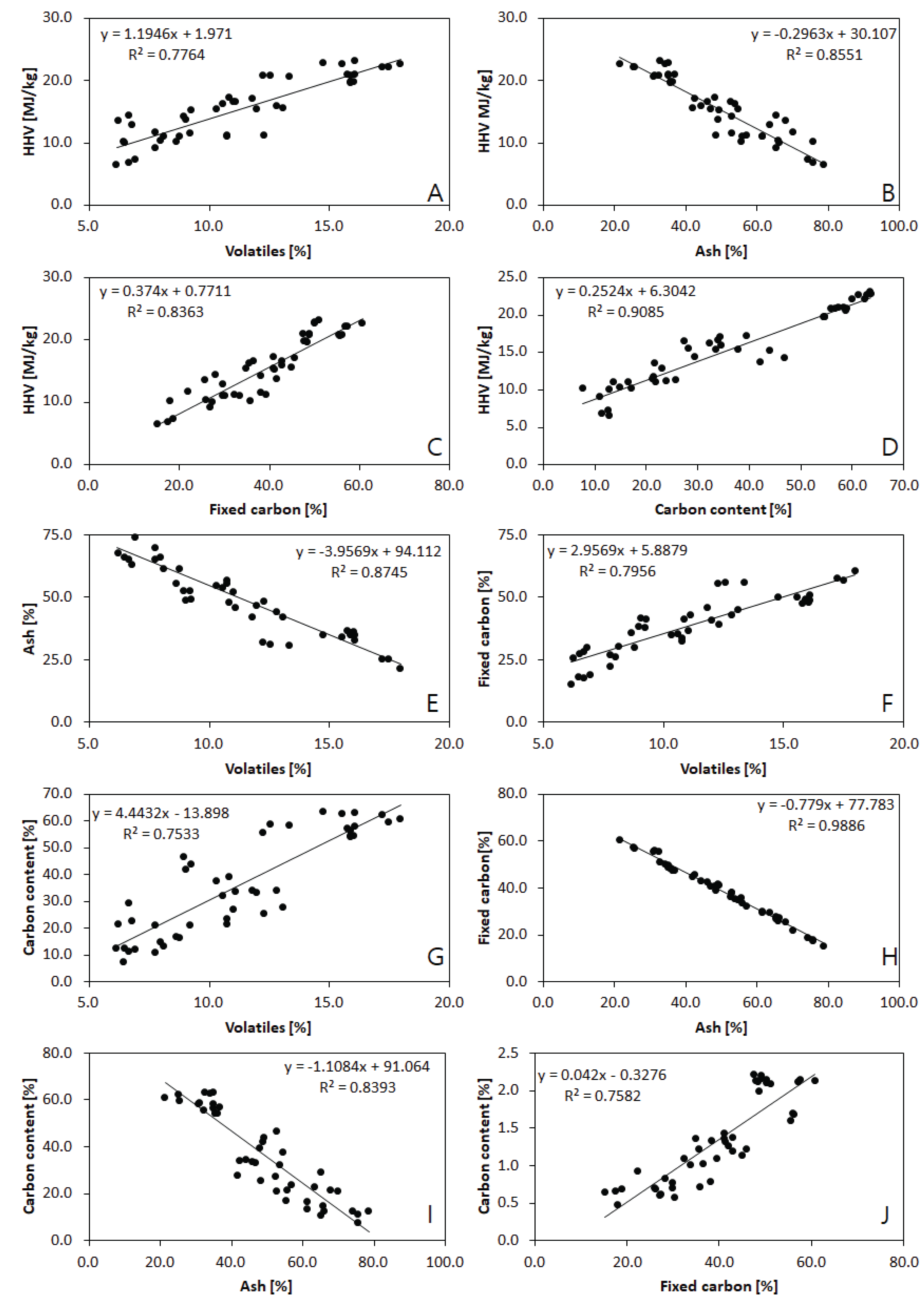
4. CONCLUSIONS
In this study, characteristics of carbonized samples produced using a wood charcoal briquette manufacturing process based on an open hearth kiln are analyzed. For the carbonized samples collected based on their vertical position within the kiln, it was originally expected that the bottommost layer would exhibit the highest quality, but the experimental results suggest that the quality decreases in the order of middle layer, top layers, and bottom layers. Fuel quality of the carbonized materials produced using the open hearth kiln is observed to be not related to carbonization time; the middle layer exhibits the highest quality due to a relatively uniform carbonization reaction arising from heat transfer from both directions, i.e., from the layers above and below. When characteristics of the carbonized samples are analyzed based on particle size, HHV, carbon content, and fixed carbon content increase as the particle size decreases. In particular, the carbonized samples below 100 mesh exhibit an HHV, carbon content, and fixed carbon content of 21.3 MJ/kg, 58.8%, and 52.3%, respectively, which are directly related to an increase in fuel quality. A relatively large increase in quality can be expected if carbonized samples below 100 mesh are selected after carbonization and grinding, in a case where screening is not feasible prior to carbonization in existing processes.