1. INTRODUCTION
It is not an easy task to estimate the time for air drying of wood. It is affected by the geopolitical location of the drying facilities, and species and thickness of the wood. In general, small-density species could have a faster drying rate than greater-density species, but changing weather conditions make the results more complicated. The variables involving weather conditions, such as temperature and relative humidity that affect the drying rate, change from year to year. One of the best ways to decide on the weather conditions in a particular area is to use the averages of weather factors across several years (Simpson and Hart, 2000). Wood stacked in spring takes relatively shorter to dry because the drying period is longer, i.e. in spring and summer, whereas wood stacked in late summer or early autumn takes relatively longer to dry because of the longer period of cold days in winter.
Among the studies on air drying, those related to the change of moisture content (MC) and drying time of wood have generally used lumber with a thickness of 50 mm or less. Studies have been conducted in the United States to show the time required for air drying of softwood and hardwood lumbers 25 mm and 50 mm thick up to a target MC of 20% (Rietz and Page, 1971; McMillen and Wengert, 1978). However, the list of time periods for air drying suggested in those studies is limited to the wood stacked in a specific area and at a specific time due to lack of data for calculating the time periods. And the results for species such as hardwoods are not exact (Simpson and Hart, 2000). In these studies, variables such as initial MC, temperature, and relative humidity were put into a regression equation to apply the results obtained in a specific area across the country (Denig and Wengert, 1982). In addition, these studies have developed a numerical analysis model using moisture diffusion coefficients obtained through experiments and suggested a method of changing each coefficient by using weather data from different regions (Hart, 1982). While these studies have presented finite difference methods to analyze heat and mass transfer in arbitrary materials (Holman, 1989), the method was used to conduct one-dimensional analysis (Sutherland et al., 1992) and two-dimensional analysis (Ranta-Maunus, 1994; Perré et al., 1993). There were studies in Korea to predict the MC change during the high temperature drying of Korean red pine timber (Kim et al., 2017) and to predict the temperature distribution during heat treatment of black pine wood (Han et al., 2016). In both of these studies, the finite difference method was used. In those studies, when comparing the predicted and measured values of the MC distribution during wood drying, appropriate choice of diffusion coefficients and surface emission coefficients turned out to be very important (Kamke and Vaneck, 1994). A study on air drying in Korea reported that it took 38 and 84 days for a 25mm thick and 50 mm taun lumber to reach 20% MC, respectively (Jung, 1985) and other studies have analyzed seasonal changes in the rate of air drying of softwood and hardwood lumbers (Lee and Jung, 1989; Jung et al., 1997). One study involving the air drying of timbers and logs measured the time it took for MC to reach 18% for air drying of Korean red pine and Japanese larch (Jung et al., 2003). Another study was carried out to analyze the effect of air drying as a preliminary drying for high temperature and low humidity drying of Korean red pine wood’s large cross section (Lee et al., 2014).
The purpose of this study is to analyze the change of MC during air drying of Korean red pine logs and to suggest air drying time to reach the target. A air drying facility was set up in Seoul, and the weight of logs was measured to evaluate the changes in MC. Then, wood-related data such as initial MC, top diameter, and dry weight of Korean red pine logs and weather data such as temperature, relative humidity, and wind speed were used to conduct two-dimensional moisture transfer analysis, which led to the prediction of MC distribution of wood.
2. MATERIALS and METHODS
Test species are Korean red pine trees (Pinus densiflora) collected from Uljin-gun, Gyeongsangbukdo and 15 logs with IV-XI age class were cut to 3.6 m in length. The initial MC of the logs measured using increment borer (L 300 mm × ø 10 mm; Haglof, Sweden) ranged from 28% to 83%, and the top diameter ranged from 310 mm to 510 mm. Oven-dry specific gravity was 0.484 (0.30 SD). In Table 1, the Korean red pine logs are classified according the age class and top diameter, initial MC, oven-dry specific gravity, and annual ring width were presented. A air drying facility was temporarily installed in the National Forest Research Institute of Dongdaemun-gu, Seoul. After the bark of the logs was removed for air drying, it was end-coated with urethane-based paint to prevent the drying of cross section. Of the total 15 pine logs, six of them were stacked in early summer (June 2016) and nine were stacked in late autumn (October 2016). During the air drying, the weight of the logs was measured using a hanging scale (W 230 mm × D 370 mm × H 474 mm; 1 ton; CAS, Korea) once every 3 to 6 months (Fig. 1).
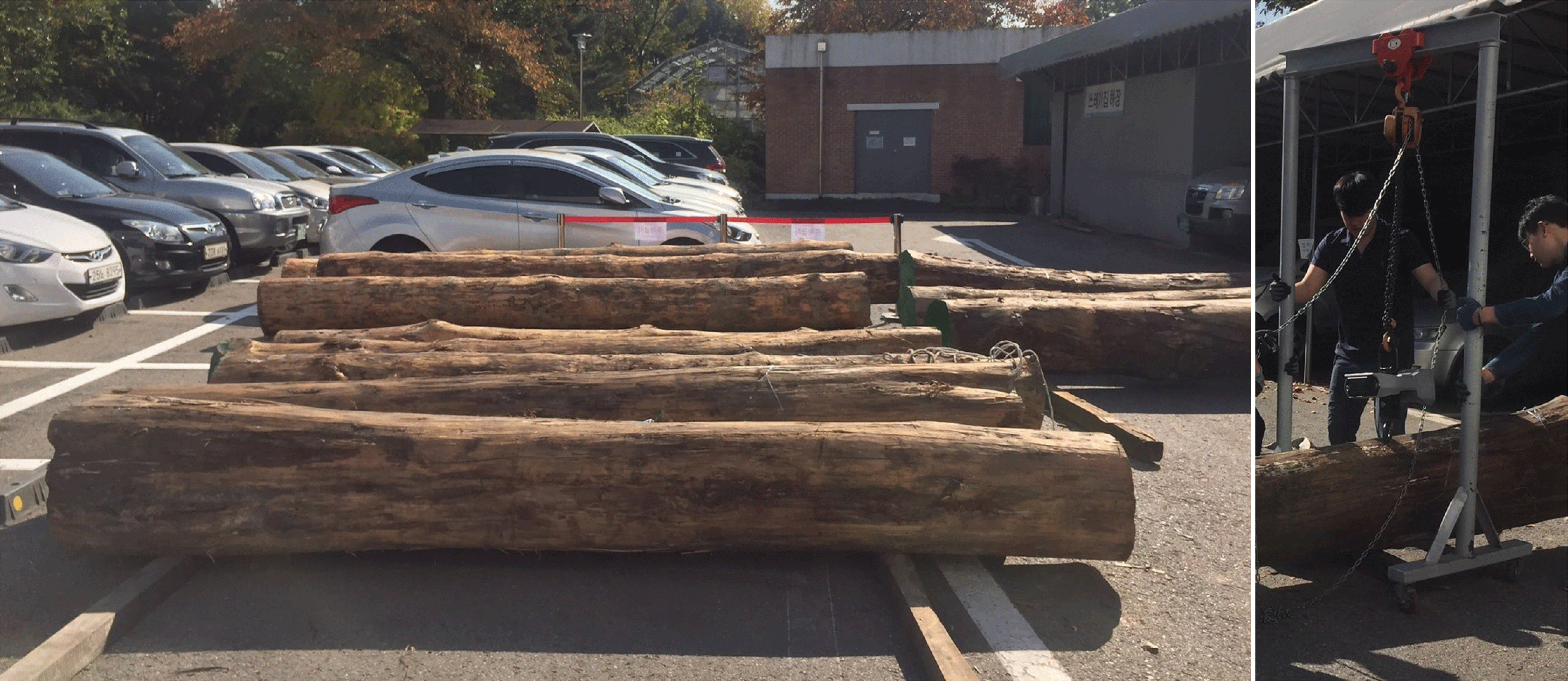
The governing equation for two-dimensional mass transfer can be shown as Equations (1).
where, Dx = diffusion coefficient in x-direction (m2/s); Dy = diffusion coefficient in y-direction (m2/s); C = mass concentration (kg/m3); x and y = distance in the direction of flow (m); t = time (s).
If a two-dimensional object is divided and increased in the x- and y-axis directions, the intersection is designed as shown in Fig. 2. In the figure, m is the increment along the x-axis direction, n is the increment along the y-axis direction, and the concentration gradient can be expressed as Equations (2)-(4).
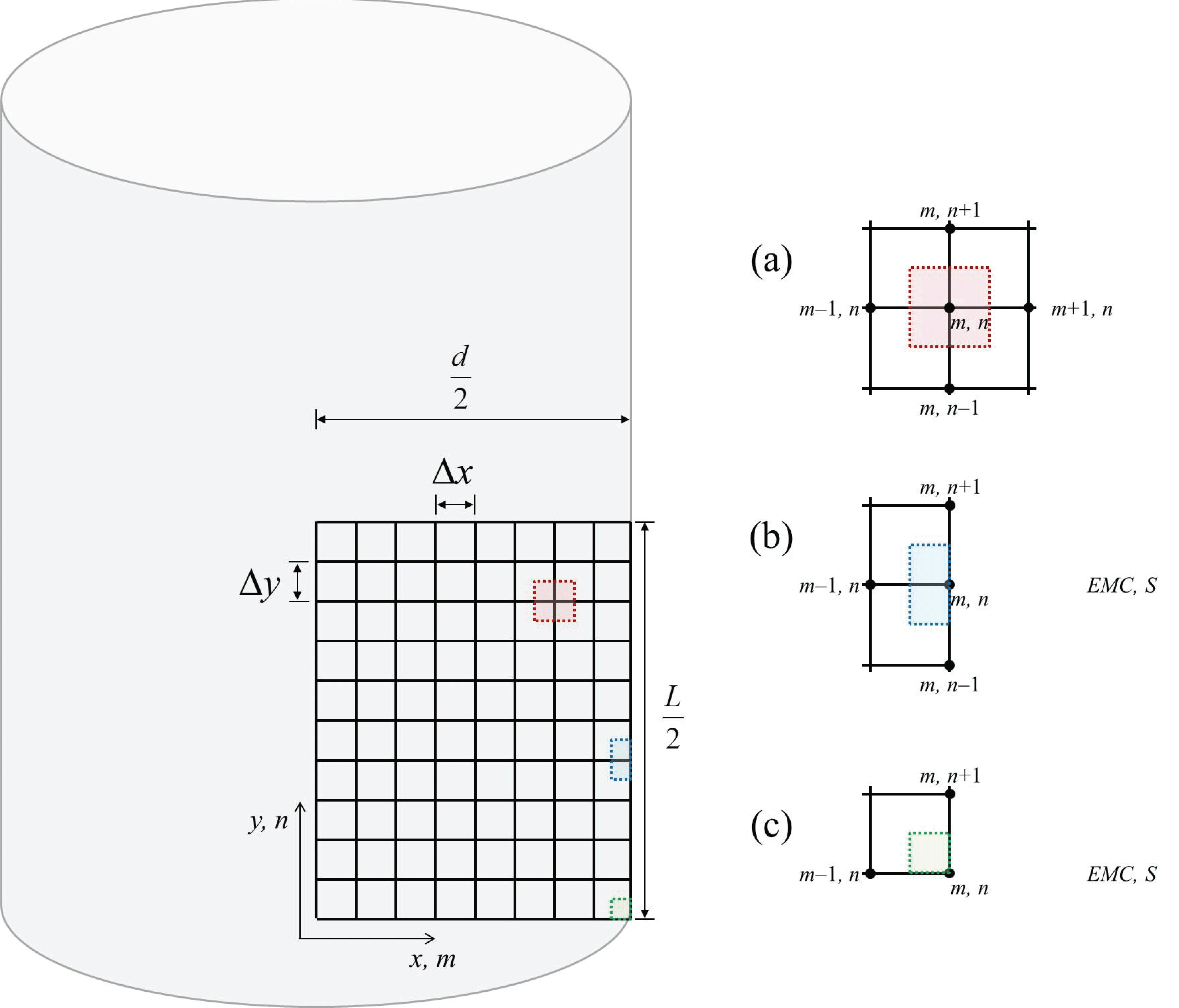
where, m and n = increment in the x- and y- direction.
The second partial derivative of the inner nodal point (m, n) of the log shown in Fig. 2 (a) can be expressed by equations (6) and (7).
The change in concentration per unit time at nodal point (m, n) can be expressed as equation (8) using time increment p.
where, p = time increment.
Equation (8) can be summarized in the form of finite difference as equation (9). Similarly, the outer surface undergoing convection (Fig. 2 (b)) and the corner node (Fig. 2 (c)) can be expressed as Equations (10) and (11), respectively.
where, S = surface emission coefficient (m/s); e = equilibrium state.
Mass transfer in arbitrary materials using the finite difference method is described in detail in Hollman (1989).
Two variables are needed for the analysis of mass transfer using finite difference method. One is the diffusion coefficient, which is the rate of moisture movement inside the wood, and the other is the surface emission coefficient, which is the rate of moisture movement from the surface of the wood to the atmosphere. Diffusion coefficients were determined using a moisture transfer model (Siau, 1995) created with a simplified cell model. Diffusion coefficient DT in the transverse direction and diffusion coefficient DL in the longitudinal direction can be expressed as Equations (12) and (13).
where, DT = transverse bound water diffusion coefficient of wood (m2/s); DBT= transverse bound water diffusion coefficient of cell wall (m2/s) = 7 × 10-6 exp[ -(38500 - 290M) / RT]; M = moisture content (%); R = universal gas constant (8.314 J/mol K); T = temperature (K); DV= water vapor diffusion coefficient of air in the lumens based on the concentration of bound water in the cell wall (m2/s) = Da × ∂Ca / ∂Cw = (0.018 Dap0 / GMw ρwRT) × (∂H / ∂M); Da = coefficient of interdiffusion of water vapor in bulk air (m2/s); Ca = concentration of water vapor in the lumen in equilibrium with the cell wall (kg/m3); Cw= concentration of bound water in the cell wall in equilibrium with the air in the lumens (kg/m3); p0 = saturated vapor pressure (Pa); GMw = specific gravity of the cell wall at moisture content M; ρw = normal density of water (kg/m3); ∂H / ∂M = slope of the sorption isotherm; a = diameter of lumens = square root of porosity.
where, DL = longitudinal bound water diffusion coefficient of wood (m2/s); DBL= diffusion coefficient of the cell wall in the longitudinal direction (m2/s) = 2.5 × DBT.
The surface emission coefficient was determined by equation (14) using the method of conversion from the convective mass transfer coefficient (Yeo and Smith, 2005).
where, S = surface emission coefficient (m/s); hp = convective mass transfer coefficient based on the potential of water vapor pressure (kg/m2sPa) = J / (ps - pe); J = moisture flux from surface to air (kg/m2s); ps = water vapor pressure in air adjacent to the wood surface (Pa); pe= water vapor pressure in ambient air at the dry-bulb temperature (Pa); SMC and EMC = surface and equilibrium moisture content (%); GSMC and GEMC = specific gravities of wood based on oven-dry weight and volume at SMC and EMC.
In this study, monthly average temperature, relative humidity, and wind speed in the Seoul area where the air drying facility was installed were used to determine diffusion coefficients and surface emission coefficients. The data from the Korea Meteorological Administration (http://data.kma.go.kr) surveyed in a previous study (Han et al., 2019) can be used to obtain average monthly temperature and relative humidity. Since the average monthly wind speed is very large compared to the flow of air through the stacked logs, the former needs to be adjusted arbitrarily. To calculate wind speed values, 25% of the weather data was applied, as used in the prediction of drying rates for six species in North America (Hart, 1982). For the weather data from June 2016 to October 2018, the transversal diffusion coefficient is ranged from 3.48 × 10-11 to 1.55 × 10-10 m2/s, and the longitudinal diffusion coefficient is ranged from 1.88 × 10-10 to 1.64 × 10-19 m2/s and surface emission coefficients ranged from 3.80 × 10-7 to 1.60 × 10-6 m/s.
Changes in MC of Korean red pine logs during air drying were calculated in two ways. One is to apply the diffusion coefficient and surface emission coefficient of each month to the actual days from January to December. The other is to apply the diffusion coefficient and surface emission coefficient of summer (June-August) to the effective air drying days calculated for each month.
3. RESULTS and DISCUSSION
Figs. 3(a) and 3(b) show changes in MC during air drying. One is for six Korean red pine logs, which started drying in the summer (June 2016), and continued for about 880 days. The other is for nine Korean red pine logs, which began drying in autumn (October 2016) and continued for about 760 days. As for the former, the initial MC was 68.7% (± 8.9), the final MC was 17.4% (± 4.0), while they were 35.8% (± 6.3) and 16.0% (± 3.1), respectively, for the latter. Since air drying was started in different seasons, the initial MC of the two conditions were different, making it difficult to make a direct comparison.
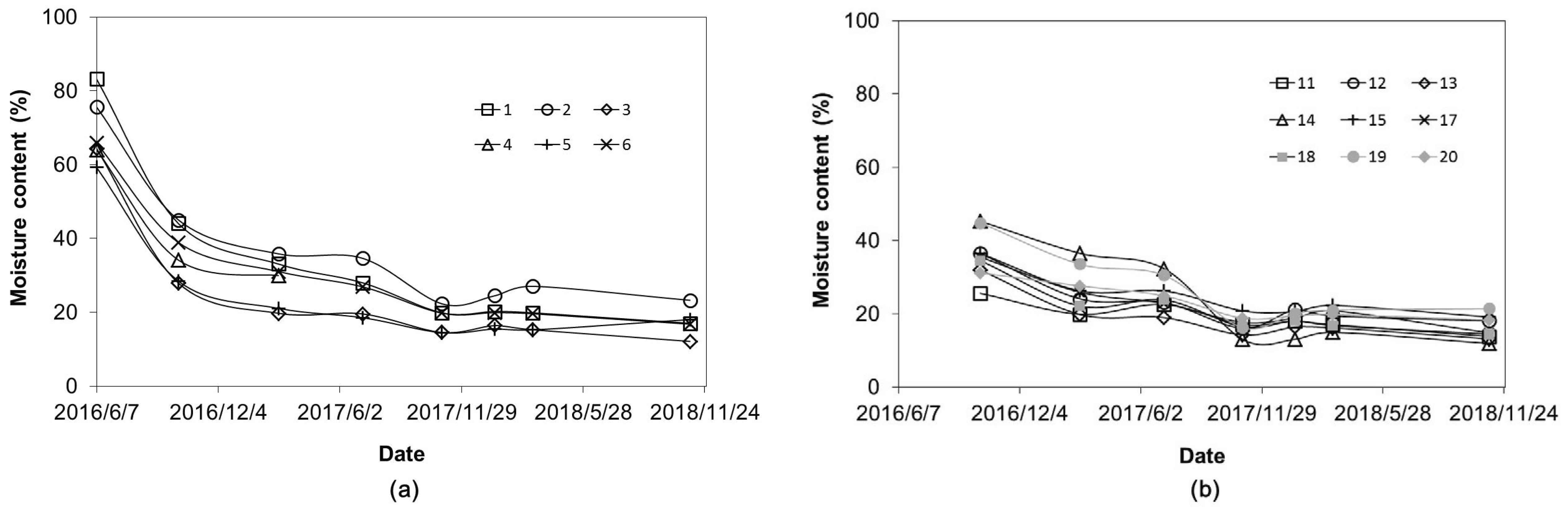
In Figs. 3(a), the average drying rates of six logs are shown after air drying began; 0.267%/day in summer (June-October 16), 0.054%/day in winter (October 16-March-17), 0.024%/day in spring (March 17-July), 0.063%/day in summer (July-October 17), ‒0.009%/day in winter (October 17-Mar March 18), and 0.008%/day in spring and summer (March‒November 18), showing differences according to seasons. In Fig. 3(b), the average drying rates of 9 logs are shown after air drying began; 0.076%/day in winter (October 16-March 17), ‒0.005%/day in spring (March 17-July), summer (July 17-October) 0.071%/day, winter season (October 17-March 18) ‒0.015%/day, spring and summer (March 18-November 18), 0.011%/day. The drying rates of 2 conditions showed the highest value at the beginning of drying when the MC of logs were higher than the fiber saturation point, and the drying rates gradually decreased as time passed. In artificial drying, the drying speed gradually slows down as the MC decreases, whereas in air drying, there is a big difference in drying speed between summer and winter, which seems to be due to the difference in weather conditions for each season. In spring and winter, after the MC of the test specimen decreased below the fiber saturation point, drying of the test specimen did not continue and there was almost no MC decrease and in the summer, the MC tended to decrease.
Table 2 shows the MC decreased during air drying according to top diameter, temperature, relative humidity, and wind speed. The MC of logs was measured from October 2016 to October 2017, with a measurement interval of 117 to 148 days (average 128 days). Temperature, relative humidity, and wind speed values are the averages over four months in the Seoul areas. The tendency was, the higher initial MC, smaller top diameter, and higher temperature, the higher the decrease in MC during air drying of Korean red pine logs.
Multiple regression was run on initial MC, top diameter, temperature, relative humidity, wind speed, and MC reduction during air drying of Korean red pine logs and the results are shown in Table 3. The regression model is Y = 0.350 × X1 ‒ 0.030 × X2 ‒ 1.38 × X3 + 8.84 × X4 + 272 × X5 ‒ 1100, and the coefficient of determination (R-squared) is 0.925, which indicates that prediction of the dependent variable by the independent variables can be done with 92.5% accuracy. Since the P-value ranges from 1.17 × 10-5 to 3.25 × 10-3, which is smaller than 0.05, the criterion for 95% statistical confidence, the regression model can be said to be adequate. The P-value for each independent variable increased in the order of initial MC, top diameter, relative humidity, wind speed, and temperature. This indicates that the initial MC and top diameter of logs have a greater effect on the MC reduction during air drying than the relative humidity, wind speed, and temperature, which are weather conditions.
Multiple regression was run with three independent variables, initial MC, top diameter, and temperature of Korean red pine logs and one dependent variable, MC decrease during air drying. The results are shown in Table 4. There are two reasons for choosing only three independent variables. First, as shown in the results of Table 3, the properties of wood have a large effect on air drying. Second, temperature among the weather conditions has a larger variation during the measurement period. Under this condition, the regression model was Y = 0.573 × X1 ‒ 0.036 × X2 + 0.218 × X3 and the coefficient of determination was 0.874. The results showed that the coefficient of determination decreased compared to the case of five independent variables in Table 3, but the range of P-value was 4.72 × 10-18 to 3.05 × 10-3, which was statistically significant.
Two-dimensional mass transfer analysis was used to predict changes in MC of Korean red pine logs during air drying. Two methods were used to determine the drying duration, diffusion coefficient, and surface emission coefficient that are associated with prediction of MC change. The first method is to apply the actual days from January to December of the year and the average weather conditions for each month to the calculation of diffusion coefficients and surface emission coefficients. The second method is to apply the effective air drying days of each month and weather conditions in the summer (June to August) to the calculation of diffusion coefficients and surface emission coefficients. To predict the changes in MC, the dimension and MC of two logs, whose internal MC during air drying was measured, were applied to the moisture transfer analysis model.
Fig. 4 shows the predicted changes in MC of the Korean red pine logs that were air-dired with an initial MC of 64%, a top diameter of 430 mm and a length of 3.6 m for 270 days from June 2016 to March 2017. Fig. 4(a) shows the results of actual air drying days and monthly average weather conditions, whereas Fig. 4(b) shows the results of using the effective air drying days of 190 days and weather conditions in summer.
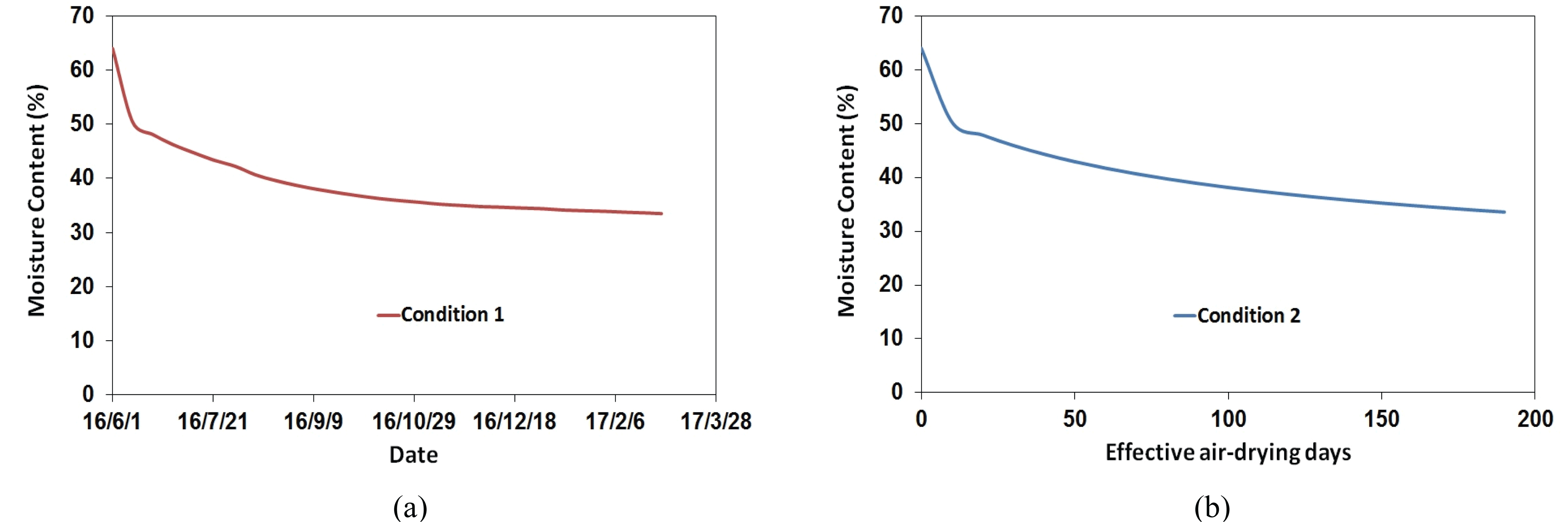
In Fig. 4(a), the MC of Korean red pine log was predicted to be 38.7% after 90 days of actual air drying, 34.8% after 180 days, and 33.5% after 270 days. In Fig. 4(b), the MC of logs was predicted to be 38.9% after 90 days of effective air drying, 34.8% after 160 days, and 33.6% after 190 days. The two methods of predicting the internal MC of the wood during air drying had an error of 0.1%. By applying the same prediction model during the same drying period to the data with MC range below the fiber saturation point, Korean red pine log with 35% initial MC, 300 mm top diameter and 3.6 m length that were dried for 750 days from October 2016 to October 2018 were used to predict changes in MC for air drying. As shown in Fig. 4, Fig. 5(a) shows the results of the actual air drying days and monthly average weather conditions, whereas Fig. 5(b) shows the results of effective air drying days of 490 days and weather conditions in summer.
As shown in Fig. 5(a), the MC of Korean red pine log was predicted to be 29.5% after 150 days of air drying, 26.7% after 300 days, 23.4% after 450 days, 22.1% after 600 days, and 19.7% after 750 days. As shown in Fig. 4(b), the MC of log was estimated to be 26.3% after 150 days of effective air drying, 22.3% after 300 days, and 18.9% after 490 days. The two methods of predicting the internal MC of log during air drying had an error of 0.8%. The reason for the large error compared to that of the prediction of MC change above fiber saturation point (Fig. 4) is as follows. When the average weather conditions for each month were applied, the MC of Korean red pine log increased in March, July, and April 2018, as shown in Fig. 5(a). However, when summer weather conditions were applied, as shown in Fig. 5(b), the MC decreases constantly. To verify the prediction model of MC changes measured under two conditions during air drying of Korean red pine logs, the internal MC of two different condition of logs was presented. One is the log with 64% initial MC, 430 mm in top diameter and 3.6 m in length that was dried for 270 days from June 2016 to March 2017 (Fig. 6(a)), and the other one is the log with 35% initial MC, 300 mm in top diameter and 3.6 m in length that was dried for 750 days from October 2016 to October 2018 (Fig. 6(b)). The average MC of test samples collected in the middle of 3.6m of pine logs was 30.0% and 16.7%, respectively. The difference in MC changes between measured and predicted values ranged from 3.5% to 3.6% above the fiber saturation point and 2.2 to 3.0% below the fiber saturation point. It means that about 3% error between the measured and predicted MC change takes about 120-140 air-drying days for log with 20% MC.
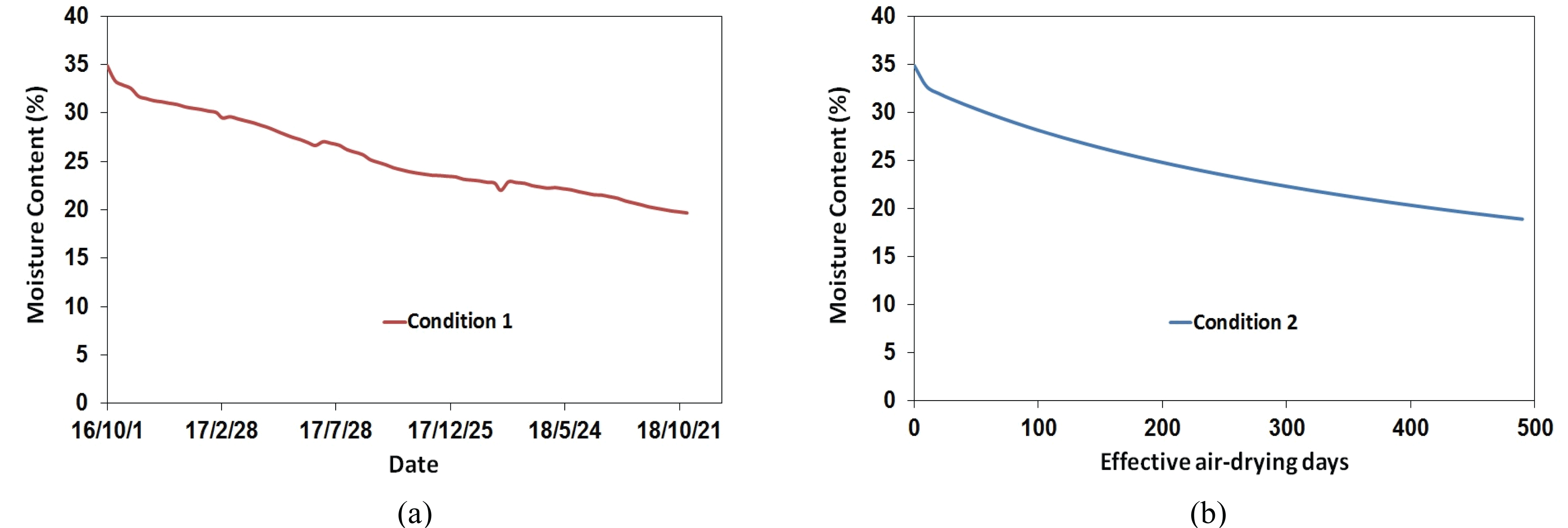
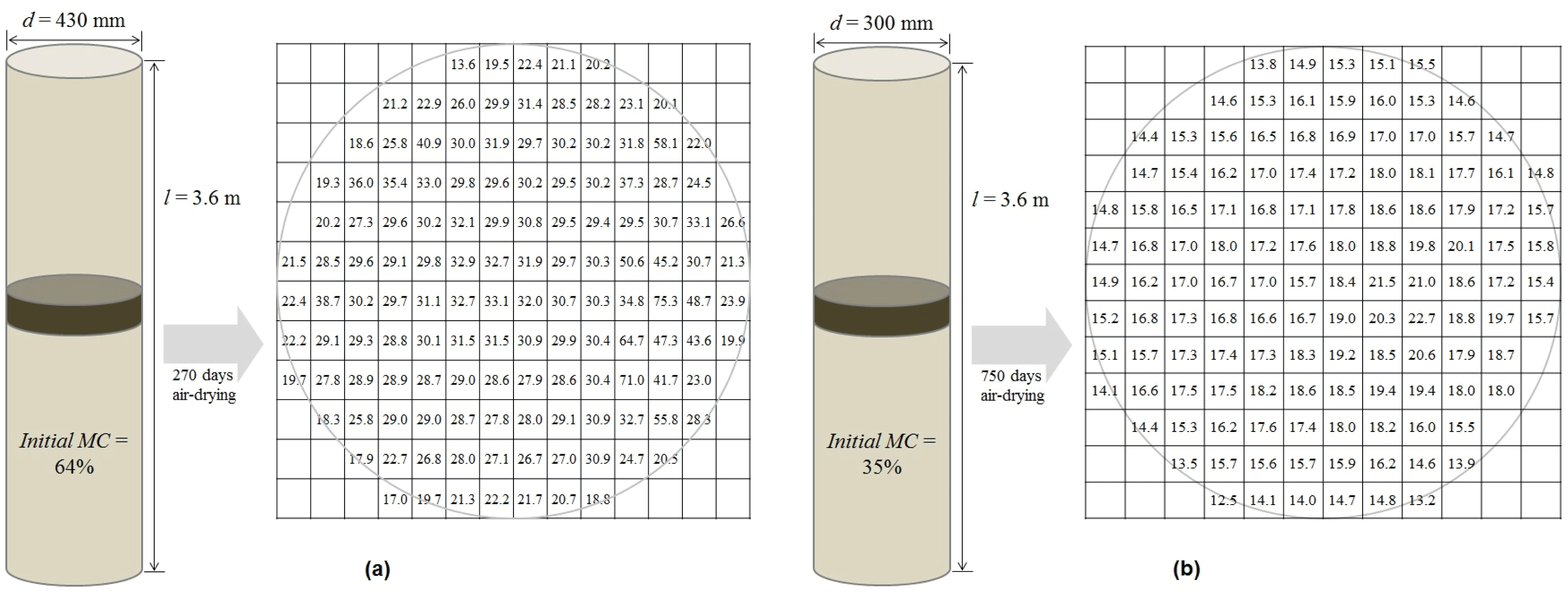
One of the ways to reduce the error rates in the prediction model seems to be measuring the internal MC during air drying of woods with various initial MCs and top diameters, and calculating the moisture transfer coefficient in wood for each weather condition.
4. CONCLUSION
In this study, Korean red pine logs were air-dried to analyze the changes in internal MC of wood during air drying. Multiple regression was run on air drying test results for 15 logs with weather variables. In order to predict the changes in internal MC during air drying of Korean red pine logs, we used moisture diffusion coefficients and surface emission coefficients calculated based on effective air drying days along with weather data from Seoul. This led to the following conclusions.
The test subjects were six Korean red pine logs for which drying started in summer and continued for about 880 days and nine logs for which drying started in autumn and continued for about 760 days. Their average final MC was 17.4% and 16.0%, respectively. The drying rate was the fastest at MC above the fiber saturation point after the start of drying, and then gradually decreased. Due to the difference in the initial MC, it was not possible to directly compare the drying rates according to season. However, it was confirmed that drying did not continue at a MC below the fiber saturation point in spring and winter.
Multiple regression was run and the dependent variable was the reduced MC during air drying, while the independent variables included the initial MC, top diameter, temperature, relative humidity and wind speed of pine logs. The regression model was “reduced MC (%) = 0.350 × initial MC (%) ‒ 0.030 × top diameter (mm) ‒ 1.38 × temperature (°C) + 8.84 × relative humidity (%) + 272 × wind speed (m/s) ‒ 1100” with a coefficient of determination of 0.925. Regression analysis showed that the initial MC and top diameter of the Korean red pine logs had a greater effect on MC reduction during air drying than the weather conditions such as temperature, relative humidity and wind speed.
Two-dimensional mass transfer analysis was used to predict the MC distribution and its changes during air drying. Two different methods of analysis were used; one was to apply the actual drying days and the average weather conditions for each month, and the other to apply the effective air drying days and summer weather conditions. The errors in the two methods ranged from 0.1 to 0.8% and the difference in the measured values ranged from 2.2 to 3.6%.
Two methods are available to possibly reduce the error rate of the prediction model. One is to measure the internal MC of Korean red pine logs with variety of initial MCs and top diameter during air drying, and the other is to calculate the moisture transfer coefficient in wood for each weather condition.