1. INTRODUCTION
Bamboo is one of the fastest growing grass species that widely distributed in Indonesia. In 2017, the production of bamboo in Indonesia reached 14 million stems which were mainly supplied from Bali, Nusa Tenggara, Java, Sumatera, and Celebes Islands (Statistics Indonesia 2017). Priyanto and Abdulah (2014) reported that bamboo forests in Indonesia is around 2 million ha, consisting of 0.72 million ha of bamboo natural forests and 1.40 million ha of plantation forests.
Bamboo is a promising material to be used as substitute to wood-based products due to its advantages such as good strength, hardness, machining, and finishing properties. Febrianto et al. (2017) reported that mechanical properties of bamboo in parallel direction to the grain were superior compared to wood. Zhang et al. (2018) reported on the dimensional stability and mechanical properties of bamboo fiber-based composites. The results showed the positive linear relations between density and dimensional stability at hot- and cold pressing, indicating that the width swelling ratio, thickness swelling ratio and water absorption ratio decreased with an increase in the density of the composites. In addition, bamboo was also fast growing, abundant in its native range and light weight. Lobovikov et al. (2007) stated that bamboo had a relatively light weight compared to wood, hence making the harvesting operation easier. van der Lugt et al. (2006) and Nurdiah (2016) shows that bamboo has the potential to compete with other materials such as wood, iron, and mild steel. Therefore, the utilization of bamboo as a renewable and sustainable substitute to wood products could also contribute on reducing forest deforestation (Lobovikov et al., 2009; Kuehl et al., 2018). Apart from its advantages, bamboo has some disadvantages when used as material for construction that require wide dimension. This is due to the limited diameter and thickness of bamboo compared to wood, hence limiting its application (Febrianto et al., 2017).
Conversion of bamboo into composite panel products could be used as the solution to this problem. Oriented strand board (OSB) is one of the promising composite panel products that could adapt the raw material characteristics of bamboo. The research showed that using similar resin content of methylene diphenyldiisocyanate (MDI), bamboo OSB (BOSB) (Adrin et al., 2013; Febrianto et al., 2015; 2012) had better properties compared to OSB from mangium (Acacia mangium) and sentang (Melia excelsa) woods (Febrianto et al., 2009; Iswanto et al., 2010).
Generally, bamboo has higher carbohydrate content than wood. Therefore, it is more susceptible to powder post beetles, fungi and termites attacks (Febrianto et al., 2013; 2014; Zhang, 1995). Extractives also have a negative effect on the gluing process (Nussbaum and Sterley, 2002). Steam pretreatment on betung (Dendrocalamus asper) and andong (Gigantochloa pseudoarundinaceae) bamboo strands with 8% (phenol formaldehyde) PF resin could improve the dimensional stability and mechanical properties (Febrianto et al., 2013; Maulana et al., 2017). Furthermore, Fatrawana et al. (2019) steam-treated bamboo strands followed by washing with 1% sodium hydroxide solution prior to manufacturing BOSB with a shelling ratio (face:core) of 67:33, resulting in the change of the chemical components and the increase of dimensional stability and mechanical properties of BOSB. However, the shelling ratio resulted in a large difference between bending strength properties in parallel and perpendicular directions to the grain. Therefore, determining the optimum setting of shelling ratio is needed to achieve the targeted bending strength. Recent studies showed that a decrease of shelling ratio resulted in an increase of board strength in perpendicular direction and a decrease of strength in parallel direction to the grain (Avramidis and Smith, 1989; Chen et al., 2008; Maulana et al., 2016; Pichelin et al., 2001; Saad and Hilal, 2012, Seo et al., 2018; Suzuki and Takeda, 2000).
The mechanical properties of BOSB is generally evaluated using destructive test method, particularly static bending test. Destructive test method is easy to carry out, easier to interpret and yields more information, hence it is more widely used and applied in many standards for bending determination (Machek et al., 2001; Oh, 2018). However, the testing is relatively slow and the specimens cannot be used again after the testing (Sakshi, 2018). In the modern industry, rapid method as dynamic or non-destructive test method was developed and it has become a vital part of the quality control process (Sakshi, 2018). Determination of mechanical properties using nondestructive testing method has been carried out on wood composites and shown good correlation with the results of destructive testing method for measuring bending properties (Yang et al., 2017; Karlinasari et al., 2010; Fagan and Bodig, 1985; Pellerin and Morschauser, 1974; Ross, 1984; Ross and Pellerin, 1988). However, scientific reports on the non-destructive test of BOSB bonded with PF resin are still limited. Consequently, the objectives of this study were to evaluate the effects of shelling ratio and resin content on the physical and mechanical properties of BOSB and to determine the correlation between the results of dynamic and static bending tests.
2. MATERIALS and METHODS
Twenty-five culms of 4-year-old betung bamboo (Dendrocalamus asper) were collected from Sukabumi, West Java, Indonesia. Their average density was 0.57 g cm-3. Bamboo culms were converted into strands as the target length, width, and thickness of 70, 25, and 0.5 mm, respectively, by using a sharp knife. Samples of one hundred strands were randomly taken to determine strand geometry as slenderness ratio (ratio between strand length and thickness) and aspect ratio (ratio between strand length and width) which was calculated according to a method described by Maloney (1993). PF resin with solid content of 42% and wax were purchased from the Palmolite Adhesive Company in Indonesia.
Strands were steam-treated in autoclave at 126 °C under pressure of 0.14 MPa for 1 hr. The steam-treated strands were then washed with 1% sodium hydroxide solution. The strands were subsequently air dried for a week and oven dried at 60-80 °C for 36 hours until reaching moisture content of less than 5%.
BOSBs with the dimensions of 30 cm (length) × 30 cm (width) × 0.9 cm (thickness) were manufactured with a target density of 0.7 g cm-3. PF resin with a solid content of 42% and resin content of 7% and 8% was used as a binder with 1% wax addition. The resin and wax were mixed with strands and divided into face, core, and back layers with perpendicular arrangement to each other. The shelling ratios were set to be 30:70, 40:60, 50:50, and 60:40. The board was hot-pressed at 135 °C with a specific pressure of 2.45 MPa for 9 min.
The evaluation of physical and mechanical properties of BOSB was conducted in accordance with the JIS A 5908: 2003 standard (JIS, 2003). All samples were conditioned at 25 to 30 °C and 60 to 65% RH for 2 weeks prior to the testing. The physical properties such as density, moisture content, water absorption, and thickness swelling were evaluated. The evaluated mechanical properties were internal bonding (IB) and bending strengths in parallel and perpendicular directions to the grain including static modulus of elasticity (MOEs) and modulus of rupture (MOR). Non-destructive testing as dynamic MOE (MOEd) test was also conducted in accordance with Yang et al. (2017). Non-destructive testing was performed using Metriguard Model 239A Stress Wave Timer which has a wave propagation time from 1 to 9,999 microseconds with a resolution of 1 microsecond. The distance of two points for sonic propagation time measurement was 18 cm. Propagation time was used to determine the stress wave velocity and be converted to MOEd.
The design of the experiment was completely randomized with two factors: resin content (two levels) and shelling ratio (four types), resulting in a total of eight possible treatment combinations. Each treatment was carried out in three replications. The data obtained were analyzed statistically by using analysis of variance (ANOVA) followed by Duncan’s multiple range test to determine significant difference of variables within each factor and the interaction between the factors (Steel and Torrie, 1995). All parameters measured were compared to those of the CSA O437.0 (2011) (Grade O-1) standard for OSB panels (SBA 2005).
3. RESULTS and DISCUSSION
The quality of strands can be reflected from its slenderness ratio and aspect ratio. According to Marra (1992), strand geometry is one of the main factors that influence the strength of strand board. The overall slenderness ratios ranged from 60 to 180 with the distribution as shown in Fig. 1. Strands for board production were randomly selected and the overall slenderness ratios had sufficient length to produce satisfactory board, showing an average value of 93.6 which was classified as a high slenderness ratio (Febrianto et al., 2015). Maloney (1993) stated that strand with high slenderness ratio attributed to a satisfying contact between strands and could produce a strong board. The results also showed an average aspect ratio of 3.71 with the distribution as shown in Fig. 1. A minimum aspect ratio value of 3 is needed to produce composite panel with a satisfactory strength property (Kuklewski et al., 1985). Juliana et al. (2012) also stated that aspect ratio is one of the important factors for achieving high MOE.
The result showed that BOSBs manufactured met the target density with homogeneous values, ranging from 0.70-0.71 g cm-3 (Table 1). The moisture content of boards also has homogeneous valued, ranging from 10.23-10.69%. Statistical analysis showed that resin content and shelling ratio did not have a significant effect on density and moisture content. The dimensional stability of the BOSBs was reflected by its water absorption and thickness swelling values. The values of water absorption and thickness swelling ranged from 26.85-31.36% and 2.54-3.91%, respectively. All BOSBs manufactured at different resin contents and shelling ratios were well corresponded to CSA O437.0 (2011) (Grade O-1) standard for OSB panels, showing overall value of less than 15%. The results of the statistical analysis showed that resin content gave a big significant effect on water absorption and thickness swelling values. The dimensional stability of BOSB manufactured with 8% PF resin was superior than using 7% PF resin. In contrast, shelling ratio and the resin content did not give a big effect on the water absorption and thickness swelling values.
Higher resin content commonly attributes to a better the dimensional stability with the lower water absorption and thickness swelling values. According to Zhang et al. (2007) and Halligan (1970), resin level, wax, particle geometry, board density, grain direction, blending efficiency, and pressing conditions affects on water uptake behavior of strands. Lower resin content led to more water accessibility and then decreasing the dimensional stability of strand board (Zhang et al., 2007). Febrianto et al. (2015) reported that BOSB of andong (Gigantochloa pseudoarundinaceae), betung (Dendrocalamus asper) and ampel (Bambusa vulgaris) bamboos with resin content of 5% MDI had better dimensional stability compared to 3 and 4%. Resin penetrated into the cell lumen and other parts of the bamboo strands, reducing the void parts, so that reduce the water uptake capacity of the boards (Febrianto et al., 2015; Barbuta et al., 2011). Increasing resin content in boards improved the bonding between strands which should improve dimensional stability (Kelly, 1977; Liu and McNatt, 1991). Avramidis and Smith (1989) reported that increasing resin content resulted in improved physical properties of the OSB. According to Maraghi et al. (2018), increasing the resin content might be possible to have resin coating on strand which improved the dimensional stability. The increase of bonding between strands will decrease void part and prevent the penetration of water molecules.
The MOR values in parallel and perpendicular directions to the grain were ranging from 12.34-34.80 and 13.65-29.11 MPa, respectively (Fig. 2). The results showed that resin content and shelling ratio significantly affected MOR, while the correlation between resin content and shelling ratio was not significantly affected the MOR. The MOEs values in parallel and perpendicular directions to the grain ranged from 3,102-7,438 MPa and 1,094-3,738 MPa, respectively (Fig. 3). Statistical analysis showed that resin content and shelling ratio significantly affected the MOEs, while the correlation between shelling ratio and resin content was not significantly affected the MOEs value. The results showed that the MOR and MOE values of BOSB manufactured using 8% PF resin with shelling ratios of 40:60; 50:50; and 60:40 met the entire requirement of CSA O437.0 (Grade O-1) standard for OSB panels (SBA 2005). However, when using 7% PF resin, only the MOR and MOE values of BOSBs manufactured with shelling ratio of 50:50 that met the requirement of CSA O437.0 (Grade O-1) standard for OSB panels.
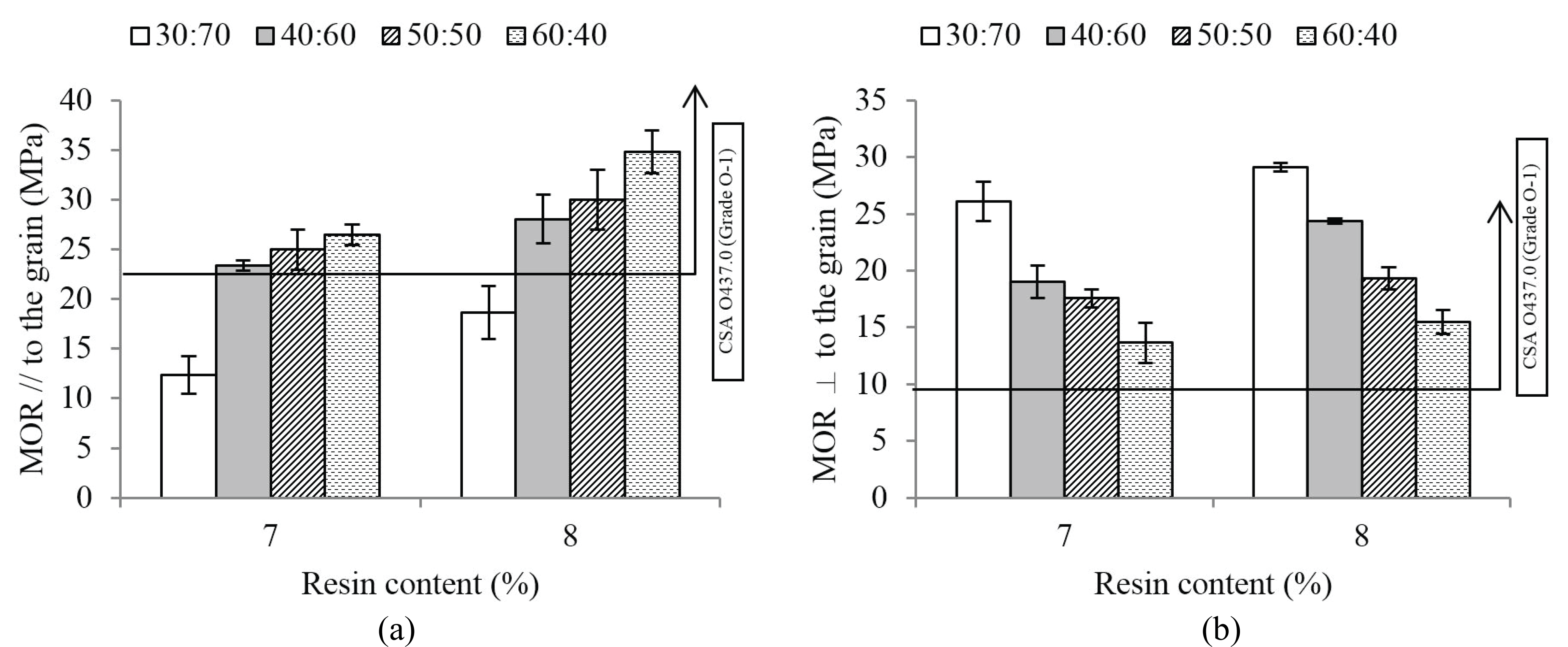
Increasing resin content commonly increased MOE values in parallel and perpendicular directions to the grain. The mechanical properties of the BOSB with 8% PF resin were superior compared to those with 7% PF resin. Maloney (1993) stated that mechanical properties were affected by resin content and type of resin. The higher resin content facilitated the more interstrands bonding. In addition, Barbuta et al. (2011), Febrianto et al. 2015 and Guntekin and Karakus (2008) reported that increasing resin content increased the mechanical properties of OSB. Sun et al. (2018) also reported the improvement of mechanical properties with increasing PF resin concentration in BOSB from Dendrocalamus giganteus. Avramidis and Smith (1989) reported similar results that MOR and MOE value of OSB from mixture of eastern white pine (Pinus strobus), hemlock (Tsuga canadensis), and aspen (Populus tremuloides) were increased with increasing PF resin content in the range 3-6%. Lin et al. (2008) revealed that the improvement of the mechanical properties (i.e., MOE, MOR) was achieved by increasing resin content, but decreased with increasing wax content.
Figs. 2 and 3 shows the MOR and MOE of BOSB manufactured under different shelling ratio and resin content in parallel direction to the grain and perpendicular direction to the grain. The increase of shelling ratio increased MOR and MOE of BOSB in parallel direction to the grain, vice versa in perpendicular direction to the grain. The similar effect of shelling ratio on bending strength also reported in several previous studies. Avramidis and Smith (1989) reported that wood OSB with shelling ratio of 60:40 has higher bending strength than that with 50:50. Saad and Hilal (2012) revealed that higher composition of bamboo in face/back layers increased bending strength in parallel direction to the grain of OSB manufactured from ater bamboo (Gigantochloa atter) and water hyacinth (Eichhornia crassipes). Suzuki and Takeda (2000) reported that MOE parallel direction to the grain was increased by increasing face layer ratio in OSB manufactured from sugi wood (Cryptomeria japonica). Chen et al. (2008) reported that the increase of face to core ratio improved MOE parallel direction to the grain. The study also showed that the increase of face to core ratio from 54:46 to 66:34 increased the MOE in parallel direction to the grain by 3.7%. Maulana et al. (2016) reported the similar results that the values of bending strength parallel direction to the grain increased with increasing outer layer ratio. The board received maximum press stresses on the face layer and maximum tensile stresses on back layer during bending evaluation. Therefore, a large number of strands in the outer layers in higher shelling ratio may restrain the load. These can explain the increase in MOE by increasing the face layer ratio.
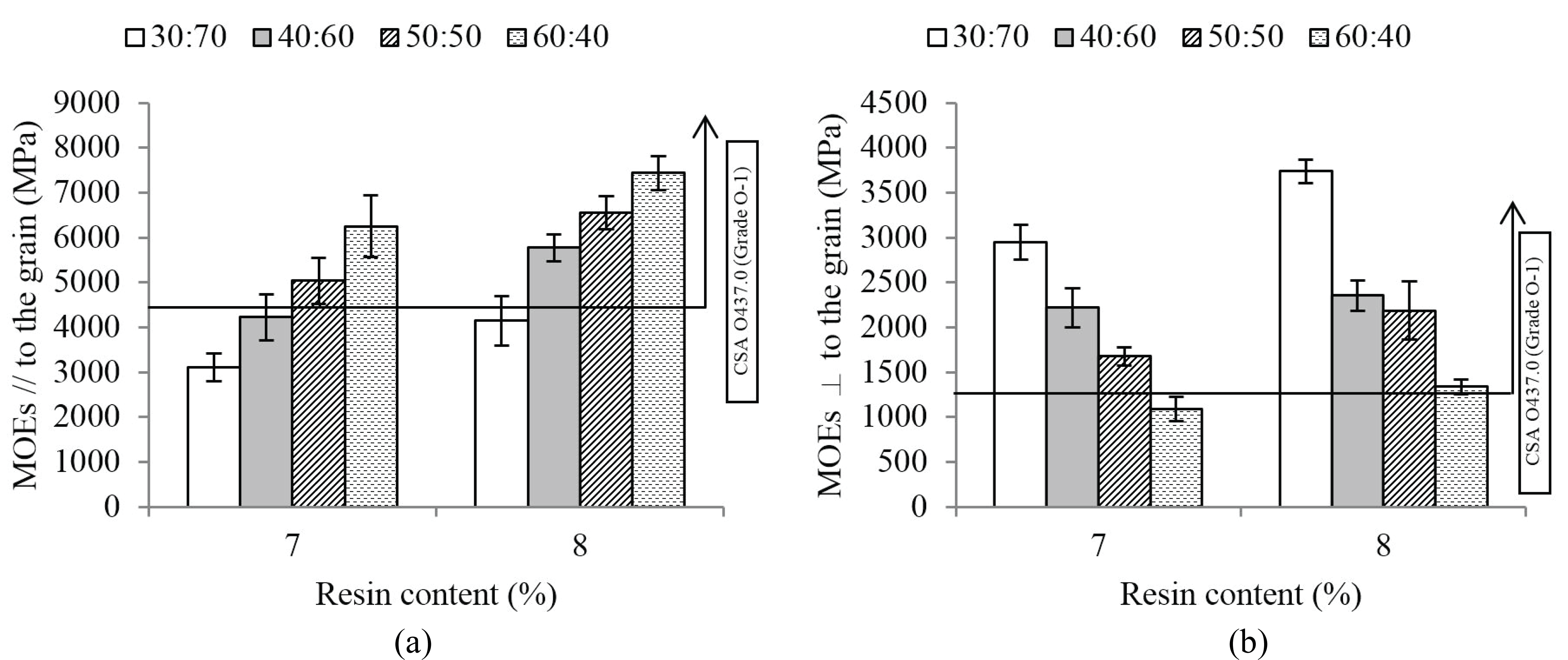
The IB values were ranging from 0.34 and 0.42 MPa (Fig. 4). IB values were significantly affected by resin content, whereas the correlation between resin content and shelling ratio was not significant. The IB values of BOSB with 8% PF resin were higher than those with 7% PF resin. According to Wu and Piao (1999), different resin content affected the number of bonds that occur in composite products. Resin penetrated into void in BOSB, resulting in the more bonding between resin and strands. Therefore, IB value can be improved by increasing the resin content. These phenomena were in line with several studies. Hong et al. (2017) reported that resin content had positive correlation with IB value. IB values were improved by increasing bonding between strands and resin due to the increase of resin content (Febrianto et al., 2009; Febrianto et al., 2015; Gamage et al., 2009; Guntekin and Karakus, 2008; Lin et al., 2008; Zheng et al., 2006).
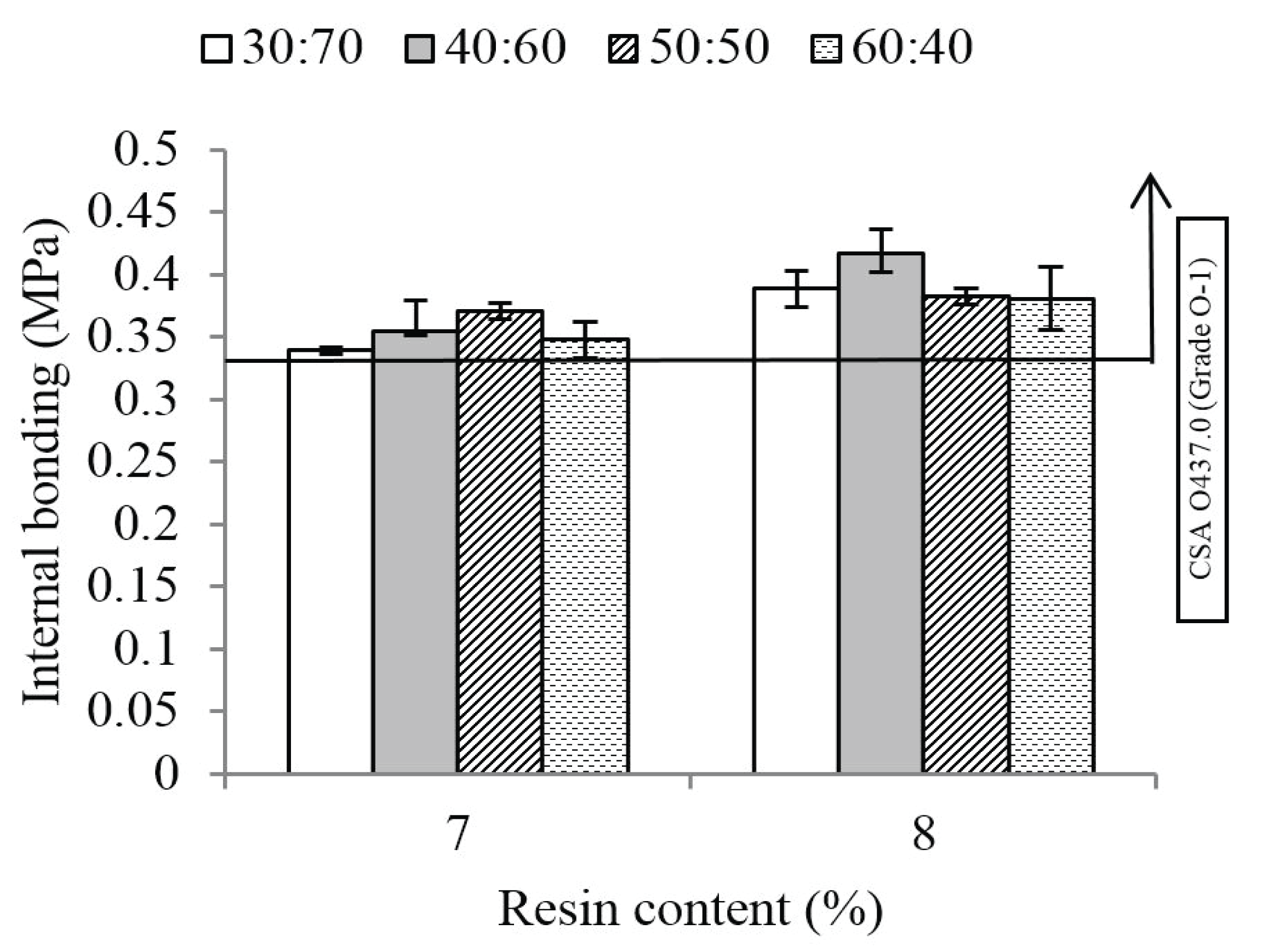
In our previous study, BOSB from the steam-treated betung bamboo strand followed by washing with 1% sodium hydroxide and with shelling ratio of 67:33, and bonded with 8% PF concentration met the entire requirement of CSA O437.0 (Grade O-1) standard (Fatrawana et al. 2019). However, the results of this study showed that when using 7% PF resin in BOSBs manufactured with shelling ratios of 50:50 could meet the entire requirement of CSA O437.0 (Grade O-1) standard for OSB panels. The results provided a valuable finding, because the shelling ratio of 50:50 reduced the consumption of PF resin by 1%.
Non-destructive test could be used as an efficient evaluation method for mechanical properties of BOSB, especially for a large-scale production. Stress waves velocity by non-destructive testing can be converted to MOEd. The evaluation of MOE using non-destructive test showed that the MOEd values ranged from 4,977-7,505 MPa and 3,280-6,032 Mpa for the MOEd in parallel and perpendicular directions, respectively (Fig. 5). The values of MOEd under various shelling ratio and resin content had similar trend with MOEs. Morales et al. (2013) suggested the possibility using stress wave testing to determine mechanical properties of Brazilian commercial OSB panel. The results showed that resin content and shelling ratio significantly affected the MOEd, while the correlation between resin content and shelling ratio did not significantly affect the MOEd. The value of MOEd in parallel and perpendicular directions to the grain increased with increasing resin content. MOEd in parallel direction to the grain was increased by increasing shelling ratio. Godin (2011) stated that the speed of sound in solid and liquid media is faster than in gas. Therefore, the more resin penetrated will reduce the void space in the boards and increase sonic propagation speed, resulting in the the values of MOEd. However, linear regression is required to determine the precise relationship of non-destructive (i.e., MOEd) and destructive (i.e., MOEs and MOR) for bending specimens.
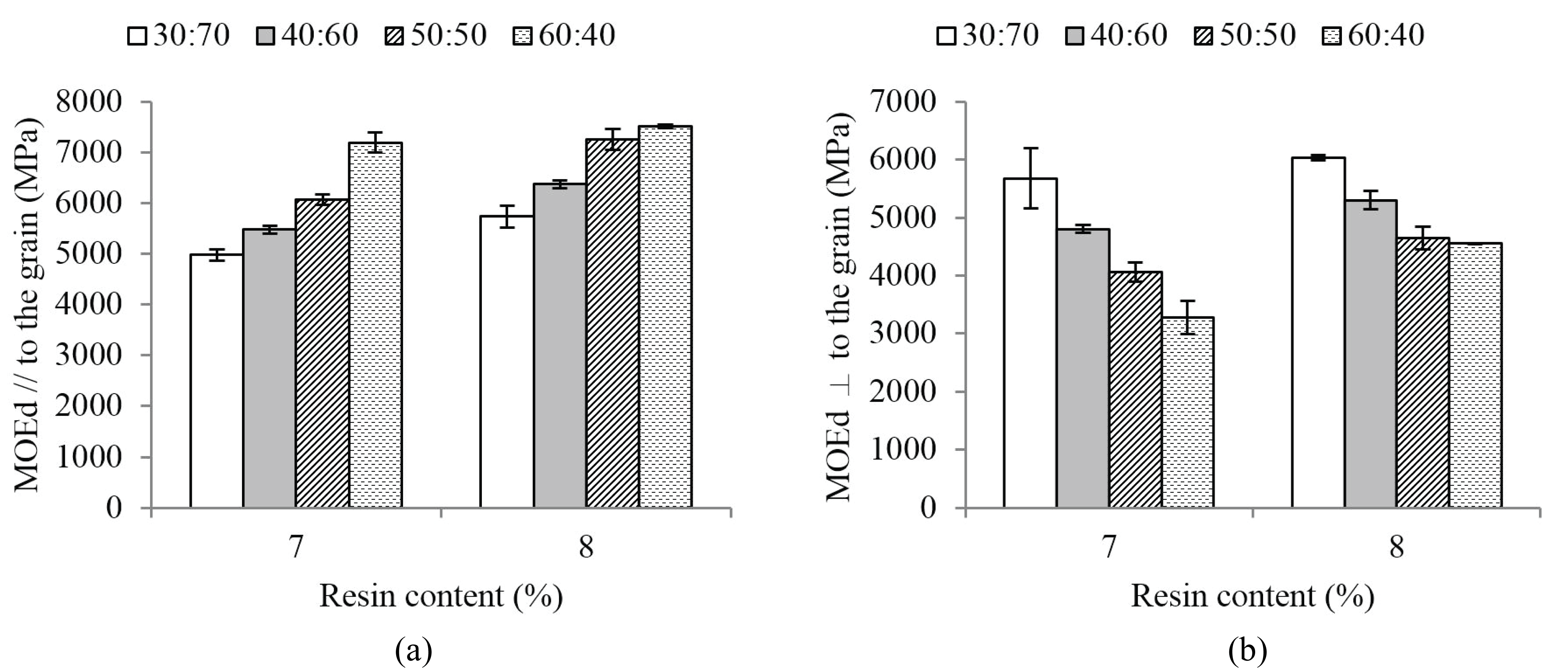
The linear regression was calculated for all specimens to show the relationship between the results of non-destructive and destructive tests. Non-destructive testing has shown high correlation between dynamic and static in other composite materials (Fagan and Bodig, 1985; Pellerin and Morschauser, 1974; Ross, 1984; Ross and Pellerin, 1988). In this study, a high correlation between static and dynamic test methods for the MOE prediction was achieved, showing correlation coefficient (r) ranging from 0.88-0.93 (Fig. 6). High correlation was also found between the MOEd and MOR in both parallel and perpendicular directions to the grain (Fig. 7). According to EN 326-2 2002 (European Committee for Standardization 2010) the regression equation may be used to calculate the value of independent variables if the calculated value of correlation coefficient is higher than or equal to 0.70, which is the same as R2=0.49. The correlation in this study was better than the result by Han et al. (2006). They reported that the value of R2 were 0.60 and 0.81 for the MOE and 0.58 and 0.82 for the MOR in parallel and perpendicular directions to the grain, respectively. The results suggested that the non-destructive method could provide a consistent results with the results of destructive testing.
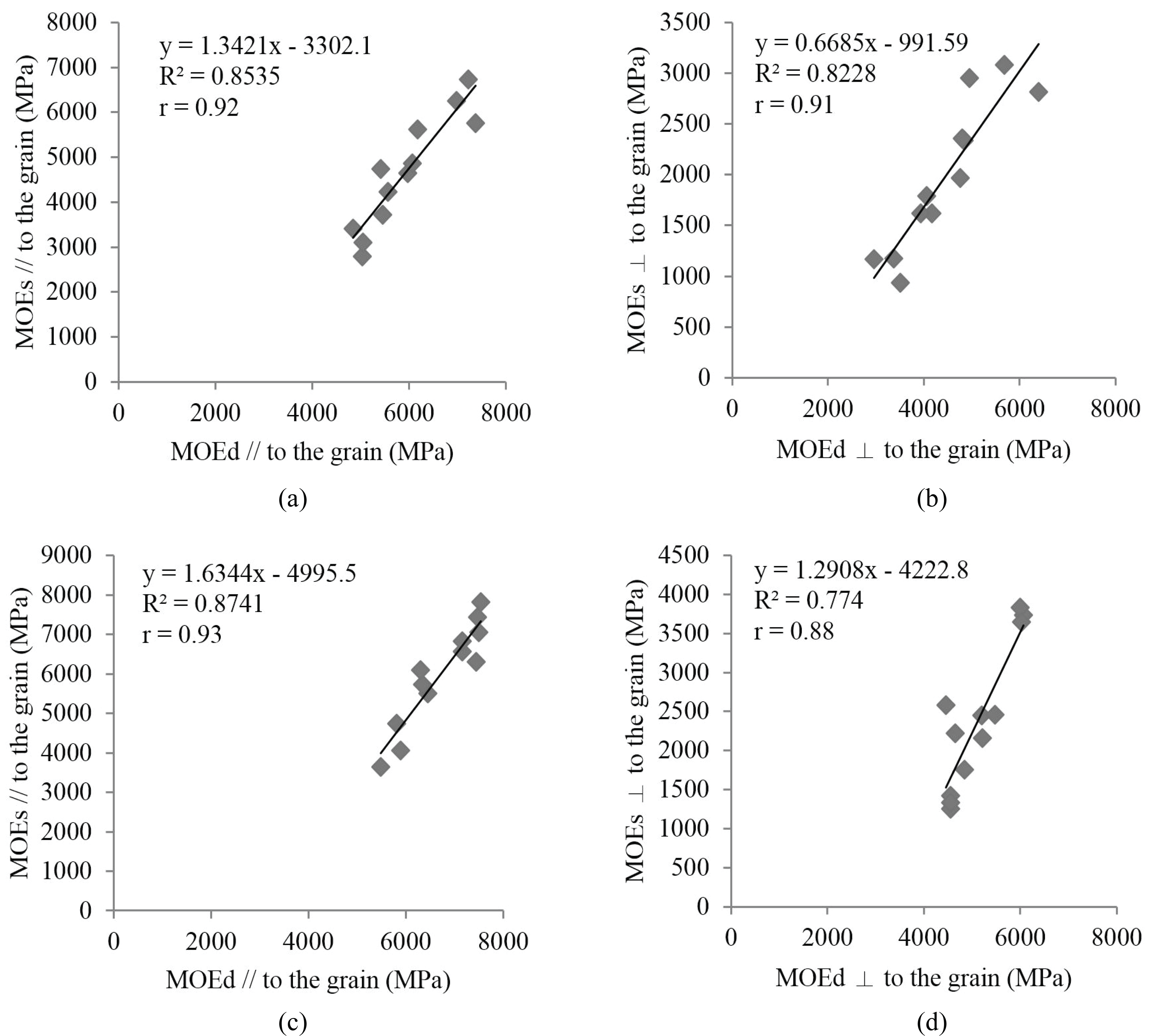

4. CONCLUSION
Strands with high slenderness and aspect ratios were prepared from betung bamboo. BOSB with 8% PF resin content at various shelling ratios had superior physical and mechanical properties than that with 7% PF resin content. An increase of shelling ratio increased the bending strength of BOSB in parallel direction to the grain, and vice versa in perpendicular direction to the grain. The shelling ratio of 50:50 could be applied as a simple way to reduce resin consumption from 8 to 7% and at the same time met the requirements of commercial standards. The results of non-destructive and destructive tests showed a strong correlation, suggesting non-destructive test can be used to estimate the bending properties of BOSB.