1. INTRODUCTION
Lignocellulosic biomass is an inexpensive, renewable, and abundant source of biorefinery fuel. Biorefinery fuel can be produced from various lignocellulosic biomasses such as wood, agricultural, or forest residues (Maurya et al., 2015). Full feedstock recovery requires the optimum utilization of all lignocellulosic components as marketable products and should be one of the major goals of optimizing a biomass-to-ethanol conversion process. Ideally, bioconversion in the wood-to-ethanol conversion process should convert all wood carbohydrates in the feedstock to ethanol. It is generally recognized that the recovery of all components will be compromised because of the complex nature of the lignocellulosic substrates and the technical difficulties associated with their separation and conversion to marketable products (Boussaid et al., 1999). Although significant advances have been made in the bioconversion of hardwood and agricultural residues, progress on softwood feedstocks has proven more difficult. Biomass from softwood, e.g., pine and spruce, is a very abundant feedstock and is a viable alternative to more typical materials such as grass and straw (Kim et al., 2016). However, implementation of softwood biomass in ethanol production is very sensitive because of the high lignin content and the difficulties associated with the steam explosion pretreatment, which is required for disrupting the lignin carbohydrate matrix. To date, no viable process for softwood-to-ethanol conversion has been established.
Steam explosion is widely used in a variety of lignocellulosic biomasses for fractionation of the main components (cellulose, hemicellulose, and lignin) (Jung et al., 2017a). To date, steam explosion is known to be one of the most desirable pretreatment methods for fractionation of biorefinery fuel because of its high yield and low capital and production costs (Avellar and Glasser, 1998). The method is effective over a wide variety of plant biomasses including hardwoods (Excoffier et al., 1991; Ramos et al., 1992; Jung et al., 2013; Jung et al., 2017a), softwoods (Schwald et al., 1989, Jung et al., 2018), and agricultural residues such as Miscanthus sinensis (Jung and Yang, 2016), sugar cane bagasse (Kling et al., 1987), wheat straw (Tenrud et al., 1989), barley husk (Jung et al., 2017b) and corn stover (Ropars et al., 1992). If softwoods are to be used, an acid catalyst must be combined with steam (Boussaid et al., 1999; Clark and Mackie, 1987). Several organic acids, particularly H2SO4, were proposed as effective catalysts (Lee and Jeffries, 2011; Galbe and Zacchi, 2002). Moreover, SO2 was shown to have several advantages as an acid catalyst, such as its rapid penetration in and uniform distribution throughout wood chips (Mamers and Menz, 1984; Wayman et al., 1984). Therefore, steam explosion is an interesting method for use in biorefinery industry, but it should be assisted by impregnation of the raw material with an acid species, such as sulfuric acid or sulfur dioxide (Galbe and Zacchi, 2007), if it is to be effective on softwood. However, the use of different impregnating agents can affect the reactivity of the pretreated biomass, the formation of microbial inhibitors, and toxicity. Furthermore, less attention was paid to the initial size and moisture content of the lignocellulosic feedstock. These two parameters are known to influence the effectiveness of steam explosion (Brownell et al., 1986; Ballesteros et al., 2000; Monavari et al., 2009; Ewanick and Bura, 2011).
Pinus densiflora (Korean red pine) is one of the major plantation tree species in the Republic of Korea because of the high value wood products and nuts (Son et al., 2007), covering about 8.6% of the total forest area in Korea (Korea Forest Service 2008). Aspenwood, douglas fir, spruce, and pine (pinus pinaster, pinus radiata) were used as raw materials in previous studies on steam explosion of softwood, and there are few studies that focus on Pinus densiflora.
The aim of this study was to elucidate the effect of steam explosion in P. densiflora wood chips after impregnation by water rather than chemicals. In particular, the effects of water impregnation (with or without) and steam explosion conditions on the color variations, chemical composition, and mass balance of P. densiflora wood chip were focused in this study.
2. MATERIALS and METHODS
Pinus densiflora was collected from the forest around the city of Hongcheon in Republic of Korea. P. densiflora was chipped to a particle size of approximately 2 × 2 × 0.5 cm3 for the steam explosion treatment and stored at 20 °C.
Impregnation of dried P. densiflora was achieved by soaking 100 g of dry chipped wood in 1 L of water for 16 h. The excess water was filtered off after soaking. Impregnated P. densiflora was then steam-exploded in a reactor of the steam explosion apparatus with maximum operating pressure of 30 kg/cm2.
P. densiflora was steamed at 225 °C from 1~13 min (corresponding to severity factors (Ro) of 3.68~4.79) for water impregnation before a sharp decompression. The severity factor (Ro) was calculated using the following equation (Overend and Chornet, 1987): Severity log(Ro) = log{t×exp(T–100/14.75)} where t is the residence time in minutes and T is the reaction temperature in °C (Table 1). Non-impregnated, steamexploded P. densiflora was used as a control. After the explosion, the material was recovered in a cyclone. The wet material was cooled to about 40 °C and filtered to recover solids. The solid fraction was analyzed using the procedures described below.
Three grams of a sample was weighed and diluted with water into a slurry. The slurry was filtered through a clean filter paper, and one clean filter paper was placed on the top of the pad while filtering. The top side of the pad was placed in such a way that it faced a clean metal plate. Two dry blotters were also used. The pad was pressed in a sheet at 0.275 MPa for one minute.
The pad was dried at about 65 °C for 1 h with an IR lamp. The color measurement was gathered using an Elrepho 2000 brightness tester at D65 (Elrepho, L&W, Sweden). The CIE color system uses three coordinates (L, a, and b) to define a color space. L axis represents lightness, which varies from 100 (white) to 0 (black); a and b are the chromaticity coordinates, representing red-green and blue-yellow, respectively (Cetera et al., 2019).
The α–cellulose content (TAPPI T-203 OM 88) was calculated by further treating the cellulose fibers with NaOH after determining holocellulose content. 5 g of the sample was mixed with 7.5% NaOH reagent and stirred at 25 °C for 1 h. The pulp suspension was filtered at the end of this 1 h period. The chemical composition was determined using the filtrate. 25 ml of the prepared filtrate and 10 ml of 0.5 N potassium dichromate were mixed with 50 ml of concentrated sulfuric acid while stirring. 50 ml of water was added to the mixture, followed by 2 drops of ferroin indicator. This was titrated against 0.1 N ferrous ammonium sulfate solution to a purple color. 12.5 ml of 17.5% NaOH and 12.5 ml of water were used as a blank.
The hydrolysate produced via acid hydrolysis (ASTM method E1721-95) was then analyzed for the sugar content. The holocellulose (arabinose, xylose, mannose, galactose, glucose) content in this hydrolysis liquid was then analyzed using gas chromatography (GC) in a YL6100 device (Young Lin Ins. Co., Ltd., City, Korea) after hydrolysis with sulfuric acid and conversion into alditol acetates.
The lignin (NREL/TP-510-42618) and ash (NREL/ TP-510-42622) contents in the samples were determined using the ASTM method E1721-95. Biomass samples (0.3 g) were hydrolyzed with 72% sulfuric acid for 2 h at 30 °C. The hydrolyzed samples were diluted with distilled water to 3% sulfuric acid concentration and autoclaved at 121 °C for 1 h. The hydrolysates were filtered through filtering crucibles. The residues were dried overnight at 105 °C in a laboratory oven and weighed. The residues were then ash in a muffle furnace at 575 °C for 3 h, cooled in a desiccator, and weighed. The ash and acid insoluble residue contents were calculated on an oven dry basis.
The content of extractives (NREL/TP-510-42619) in the solubilized material was determined after soxhlet extraction with ethanol at the boiling point for 6 h.
The protein content (NREL/TP-510-42625) was estimated using an CHN analyzer (Flash 2000 Series, Thermo Fisher Scientific Inc, USA).
ANOVA was used to determine the impregnation and steam explosion effects from the obtained data. All analytical determinations were performed in duplicate, and the average results are shown here. Statistical analysis was conducted with SAS statistical software, and the ANOVA test results and were compared to the mean from the data using Duncan’s test. Duncan’s multiple comparison range test was used to determine significant differences (p<0.05) between the means.
3. RESULTS and DISCUSSION
The P. densiflora wood chip were subjected to steam explosion under different conditions, namely nonimpregnation or water impregnation.
Fig. 1 shows a P. densiflora sample subjected to steam explosion. Steam explosion condition of P. densiflora yielded products with darker color than the raw material. The appearance of the P. densiflora samples changed considerably after steam explosion. The color of the wood gradually turned darker as Ro for the treatment increased, as shown in Fig. 1. These darker color products might have formed from Maillard reactions. A Maillard reaction can occur during steam explosion, where degrading reactions are the main contributor to sugar loss and thermal decomposition of lignin to vanillin. Some products of these reactions are very volatile, and a distinctive sweet smell can be observed during steam explosion (Sørensen et al., 2008).
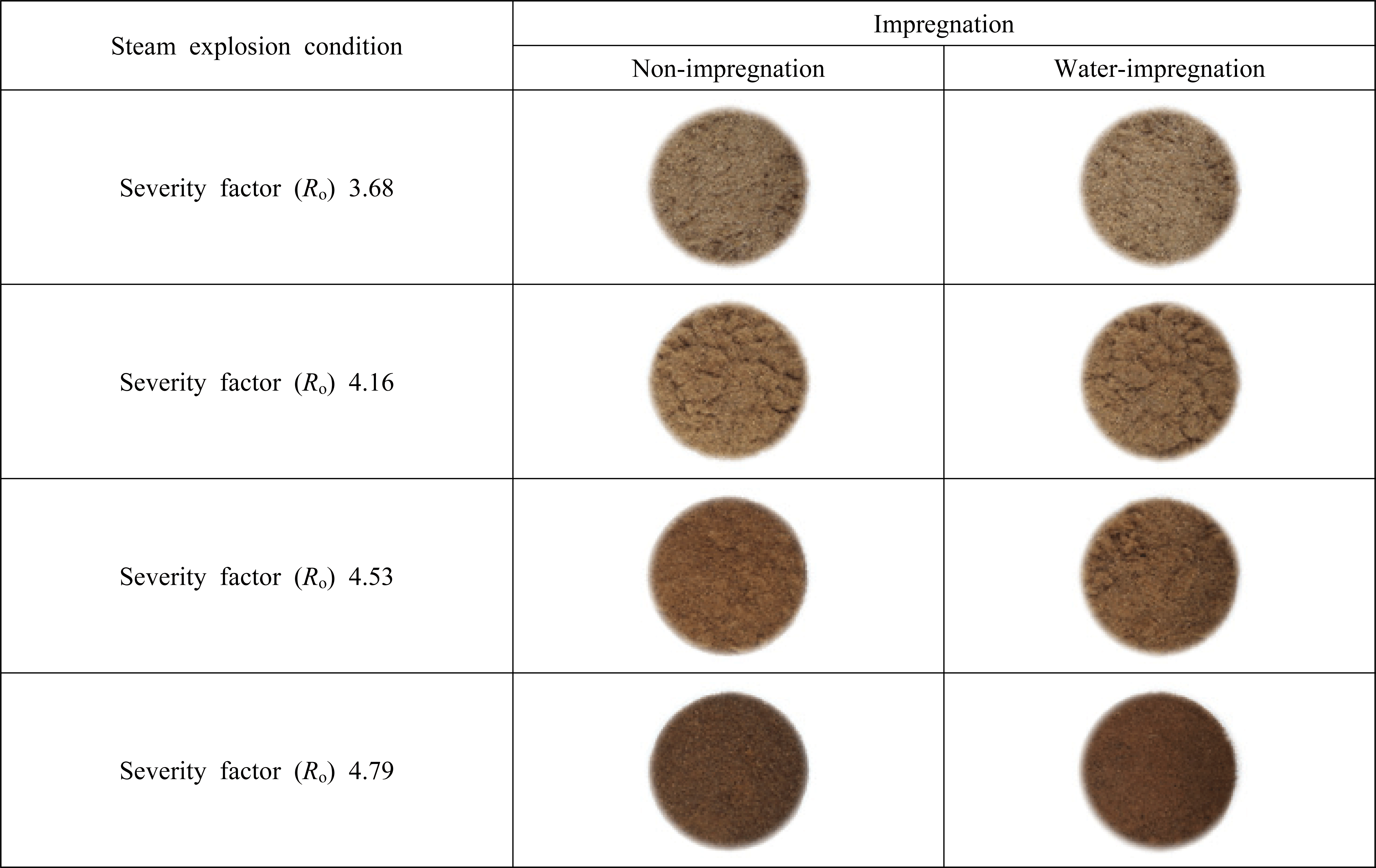
The color of the steam-exploded P. densiflora was dark brown when Ro was 4.79 due to the relatively long treatment time regardless of water impregnation.
In this color space, a color is defined by its Cartesian chromatic coordinates. The lightness L varies from 0 (black) to 100 (white). Coordinates a and b define the chromaticity plane; the color varies from green to magenta along the a axis and from blue to yellow along the b axis. This system is often used to quantify the natural color of woods (Mazet, 1988) or to trace color modifications during photochemical ageing of abies (Dirckx et al., 1992) or oak (Mazet et al., 1993).
Steam explosion strongly modifies the color with overall color differences (L, a, b, and whiteness) between untreated and treated samples (Table 2). The value of a increased from 8.6 to 11.1, and whiteness increased from 28.8 to 41.4 as Ro increased from 3.68 to 4.79 without impregnation. Also, the value of a increased from 6.5 to 9.9 and whiteness increased from 18.8 to 37.3 as Ro increased 3.68 to 4.79 after water impregnation. The value of L decreased from 51.1 to 38.3 as Ro increased 3.68 to 4.79 without impregnation. L also decreased from 61.6 to 42.4 as Ro increased from 3.68 to 4.79 after water impregnation.
Steam-exploded P. densiflora without water impregnation exhibited significantly darker color (lower L, higher a, and higher whiteness values) than waterimpregnated and steam- exploded P. densiflora.
The main components in the steam-exploded P. densiflora with/without impregnation and at various steam explosion conditions are shown in Figs. 2 to 4. The chemical composition of P. densiflora was obviously different depending on impregnation and steam explosion conditions.
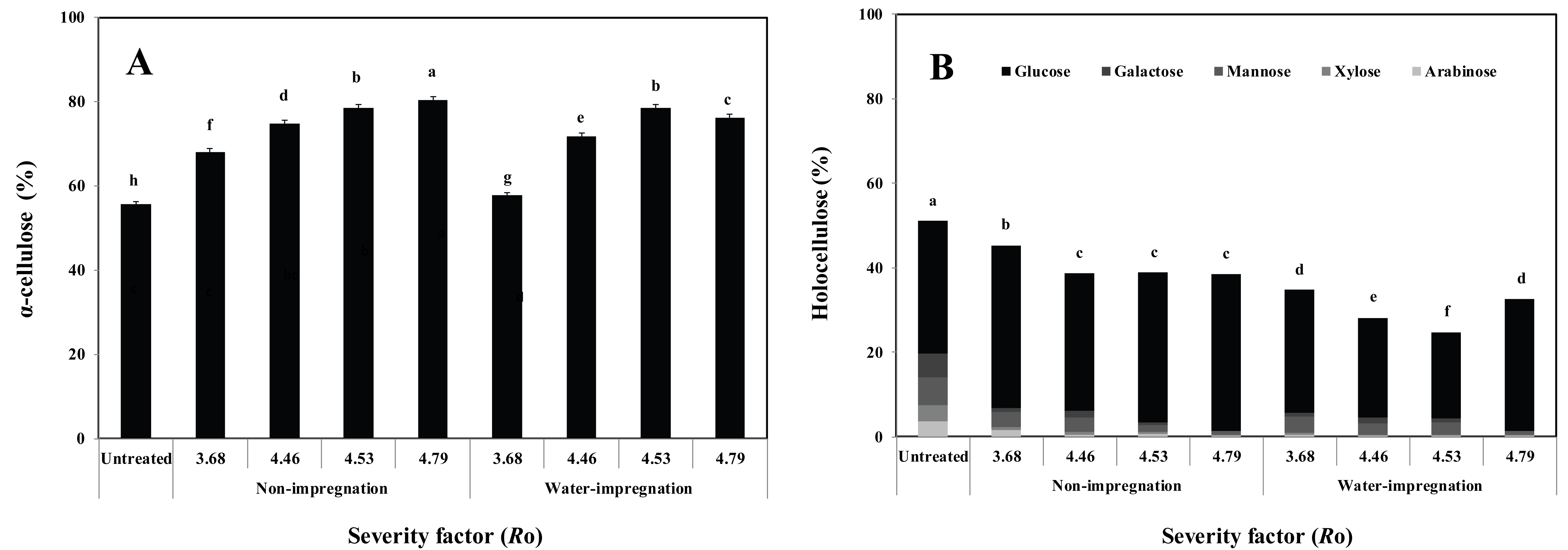
The α–cellulose and holocellulose contents in the untreated, non-impregnated/steam- exploded and water-impregnated/steam-exploded P. densiflora are shown in Fig. 2A.
The α–cellulose content in steam-exploded P. densiflora ranged between 68.1% and 80.1% when Ro ranged from 3.68 to 4.79. Also, the α–cellulose content in water-impregnated/steam- exploded P. densiflora ranged between 57.8% and 76.2% when Ro ranged from 3.68 to 4.79. An increase in the α–cellulose content was detected as Ro increased. The α–cellulose content in the non-impregnated/steam-exploded P. densiflora was higher than that in the water-impregnated/steamexploded P. densiflora.
The decreased holocellulose content was detected as the severity factor increased (Fig. 2B). Holocellulose reduction occurs due to hemicellulose (arabinose, xylose, mannose, and galactose) reduction. These results show that more hemicellulose degraded with increased temperature and residence time (Ro), confirming that hemicellulose became solubilized as oligomers (Liu and Wyman, 2003). However, the increased glucose content was detected as Ro increased. These results are consistent with the increased cellulose content as Ro increased. Various studies show that thermochemical treatments tend to increase the crystallinity index of the cellulose fraction, resulting in decreased accessibility of the wood material. This increased crystallinity is attributed to recrystallization of the amorphous cellulose induced by rearrangement of the cellulose chains at high temperature and pressure (Jacquet et al., 2012).
The lignin content in the steam-exploded P. densiflora increased when Ro ranged from 3.68 to 4.79 (Fig. 3). The lignin content in the non-impregnated/ steam-exploded P. densiflora was higher than that in the water-impregnated/steam-exploded P. densiflora. Lignin softens during steam explosion of wood, becomes released from the cell wall, and distributes evenly throughout the wood (Oberberger and Thek, 2010).
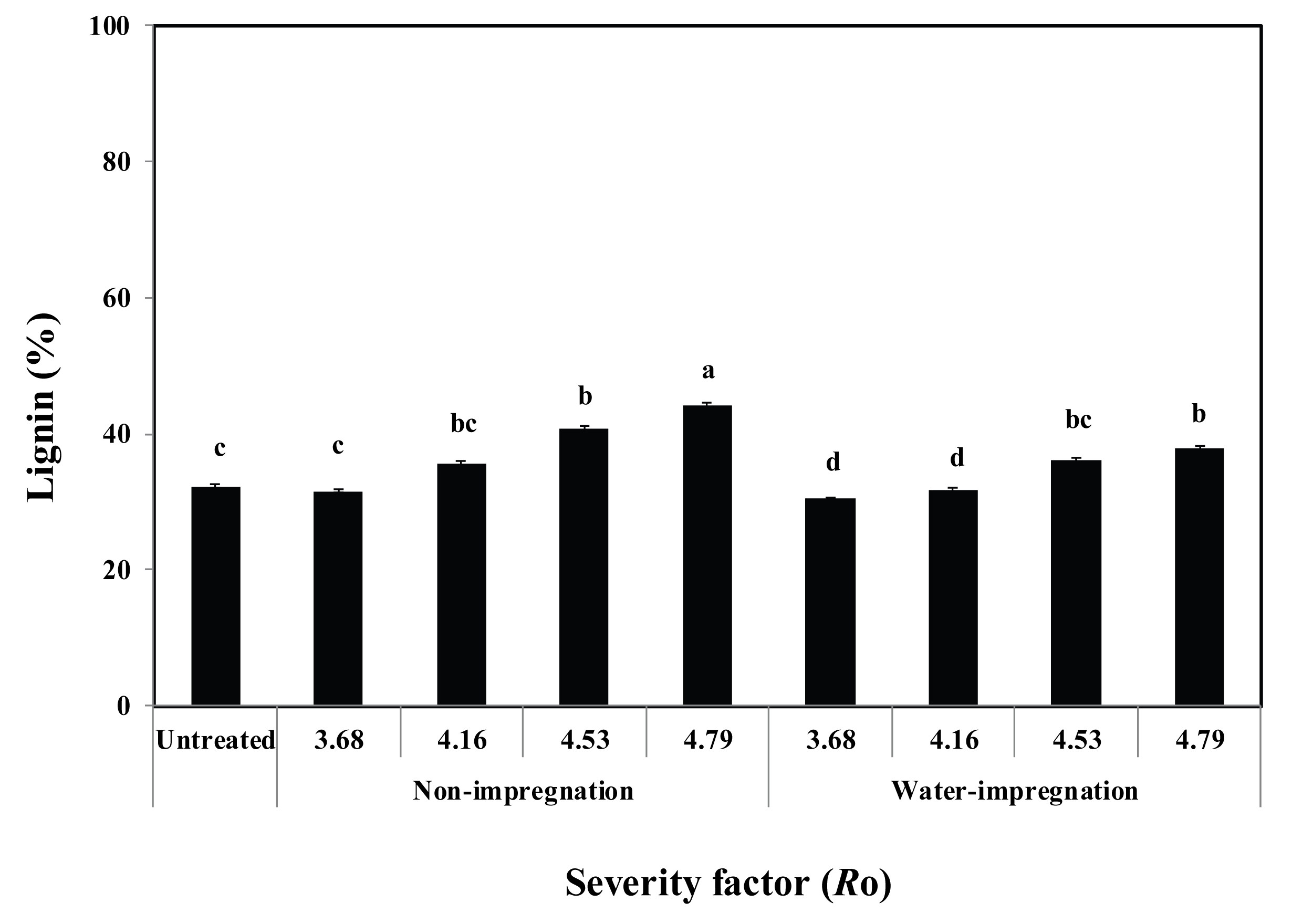
The minor components (extractive, ash, and protein) in the steam-exploded P. densiflora for different impregnation and steam explosion conditions are shown in Fig. 4.
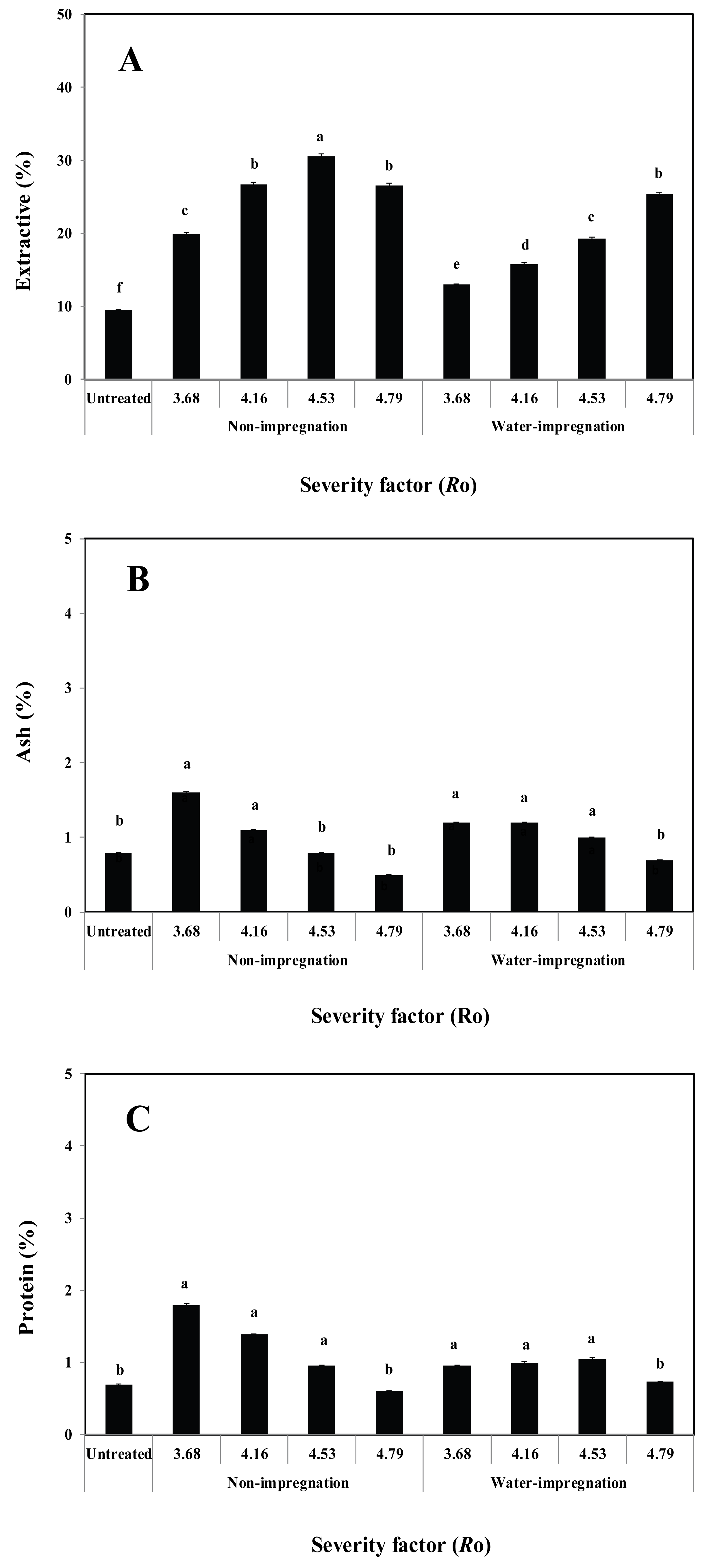
The steam explosion treatment resulted in a significant increase in the extractive content for ethanol solvents (Fig. 4A). The water-impregnated/steam-exploded P. densiflora extracted with ethanol exhibited extractive contents of 13.0% and 25.4%, respectively. The increase in extracts following steam explosion might be due to degradation of high molecular weight components and conversion from insoluble to soluble components (Shoulaifar et al., 2014).
The non-impregnated and steam-exploded P. densiflora extracted with ethanol exhibited extractive contents of 19.9% and 30.6%, respectively. However, the extractive content in steam-exploded P. densiflora decreased when Ro was 4.79. The difference is in the composition, since some new compounds form as extractable material, while other compounds volatilize or degrade. This increase in extractable material, followed by a decrease with increasing steam explosion temperature, was observed in different wood species. Pierre et al. (2011) also concluded that the extractive content tended to increase up to 250 °C, whereas they decreased at higher temperatures.
The ash and protein contents (Fig. 4B and Fig. 4C) varied within the range of 2% in water-impregnated/steam-exploded P. densiflora and decreased when Ro was 4.79. The ash and protein contents in non-impregnated/ steam-exploded P. densiflora decreased when Ro was 4.53 and 4.79, respectively.
The steam explosion treatment results from the nonimpregnated and water-impregnated samples were compared. Mass balance of non-impregnated/steam-exploded and water-impregnated/steam-exploded P. densiflora is shown in Fig. 5. When not impregnated with water, solid recovery at Ro values ranging from 3.68 to 4.79 from steam-exploded P. densiflora ranged between 70 and 98 g. Solid recovery from water-impregnated P. densiflora samples that were steam-exploded at Ro values ranging from 3.68 to 4.79 ranged between 81 and 98 g. Solids recovered from water-impregnated/steam-exploded P. densiflora was higher than that in the non-impregnated/steam-exploded P. densiflora. Also, the cellulose and hemicellulose contents in the water-impregnated/steam-exploded P. densiflora were higher than those in the non-impregnated/ steam-exploded P. densiflora. In particular, the α–cellulose content in the water-impregnated/steamexploded P. densiflora was higher than that in the non-impregnated/steam-exploded P. densiflora.
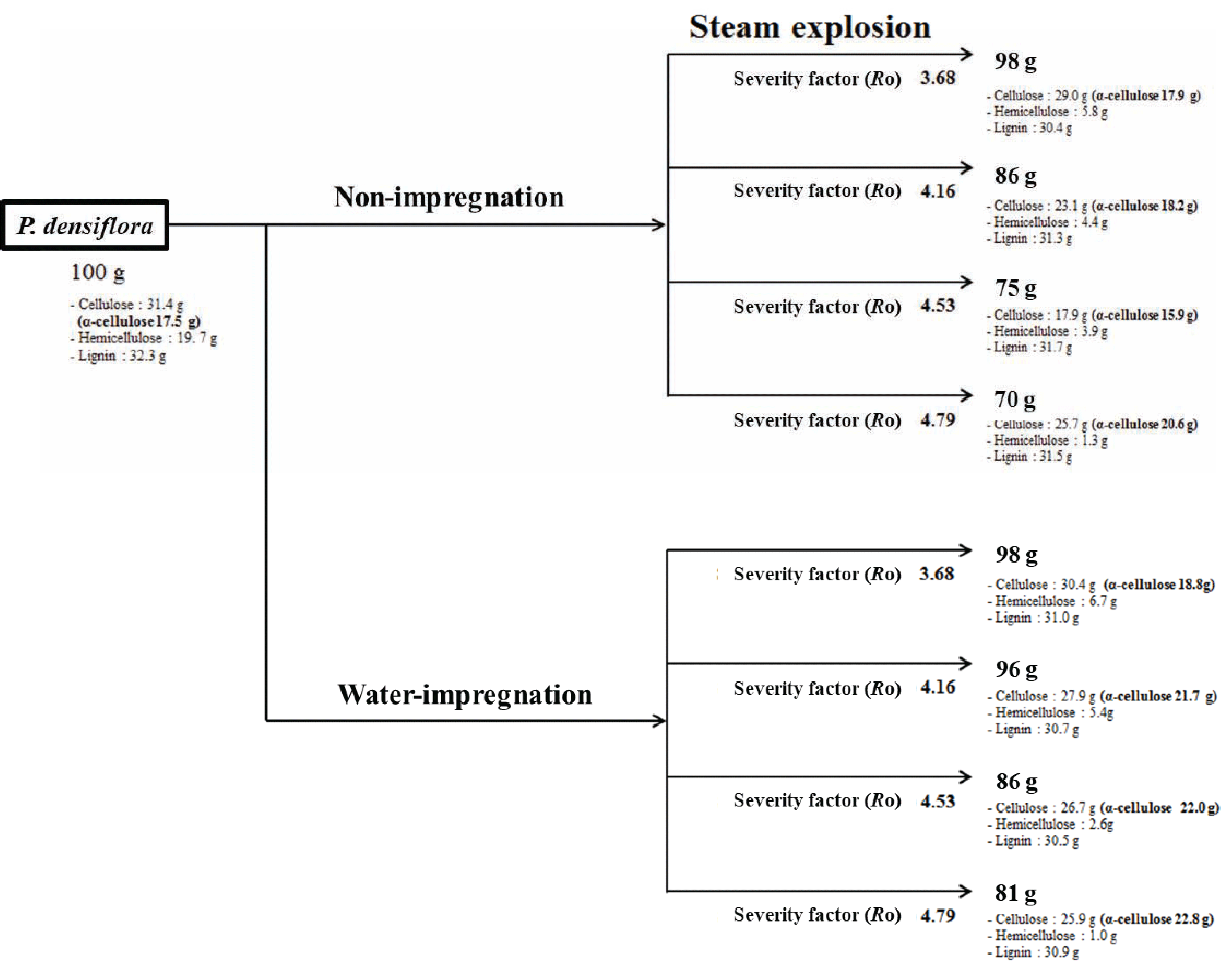
P. densiflora that was steam-exploded from the initial biomass when Ro was 3.68 exhibited a recovery yield and overall production of holocellulose (cellulose and hemicellulose) of 68.1% and 34.8 g, respectively, for the non-impregnated sample. Recovery yield and overall production of holocellulose from the water-impregnated P. densiflora samples were 72.6% and 37.1 g, respectively.
After water impregnation, the amount of residual holocellulose was 5% higher than that from the steam-exploded biomass without water impregnation. Thus, the holocellulose yield from the water-impregnated/steam-exploded P. densiflora was higher than the yield from the non-impregnated P. densiflora.
4. CONCLUSION
Steam explosion is effective in fractionation of lignocellulosic biomass for producing biorefinery fuel. Although significant advances in fractionation of hardwood have been made, progress on that of softwood has been proven difficult. Nevertheless, a combination of water impregnation and steam explosion is considered to be more efficient to this end as it increases holocellulose yield. Steam explosion with water impregnation provides high holocellulose yield from softwood species with higher efficiency than that from the non-impregnated P. densiflora. This result suggests a potential process for producing biorefinery fuel from softwood biomass by combining water impregnation and steam explosion.