1. INTRODUCTION
Medium density fiberboard (MDF) is the most commonly used wooden panel material and has exhibited an average demand of 2,150,000 m3/year from 2006 to 2016 in Republic of Korea (FAO). Furthermore, approximately 2 million m3 of waste MDF is estimated to be produced every year when the average lifespan of the MDF products (used for furniture and building materials) is presumed to be a decade. However, despite increasing interests and investments in waste recycling, MDF is barely recycled as a non-thermal recycled matter even though it is the most demanded wooden panel in Republic of Korea. A previous study reviewed the manufacturability of the dyed regenerated woody fiber (Re-WF) to use waste MDF (which can be easily observed in the surroundings) as a raw material for manufacturing interior goods (Ju and Roh, 2017). Upon comparing and reviewing the dyeing properties and color fastness to light of virgin fiber and regenerated fiber with six types of reactive dyes (bis-monochlorotriazine type and vinyl sulphone type; red, yellow, and blue), three types of vat dyes (anthraquinone type), three types of direct dyes (diazo type) commonly used in dyeing cellulose fibers, and the natural dyes obtained from cape jasmine and sappan wood, the manufacturability of the dyed fiber was confirmed; however, the color fastness to light was poor.
Several studies, including a study on the ACQ-preserved wood color (Lee and Choi, 2018), a study on the color change of heat-treated wood (Hidayat et al., 2017 and Yoon et al., 2009), a study on the color change in wood through natural dyeing methods (Moon et al., 2007), and a study on the usage of the dyeing components of Neolitsea sericea Koidz bark as a natural dye for hanji (Lee et al., 2006), have investigated wood and wooden materials; however, no studies have been conducted on dyeing the woody fiber with reactive dyes. Furthermore, there are several studies that have investigated the dyeing properties of cationic agent treated cotton fiber with reactive dye (Jung et al., 1994), effects based on the types and addition amount of Canadian horseweed on the dyeing properties and color fastness while dyeing cellulose fiber using the three-primary-color reactive dye (Kim et al., 2010), the dyeing properties of the novel regenerated cellulosic fiber (Koh et al., 2004; 2005), and the superiority of ultrasonic energy dyeing when compared to conventional dyeing in cellulosic fibers (Bhatri et al., 2012; Khatri et al., 2016) and bamboo fiber textile (Larik et al., 2015), using reactive dyes; however, no studies have been conducted on regenerated woody fiber. While dyeing with reactive dyes, a covalent bond is formed by the addition or substitution reaction between the reactive group of dye (mainly vinyl sulphone or chlorotriazine groups) and hydroxyl group of cellulose, resulting in color formation with different colors and color fastness values in accordance with the dyeing conditions. Herein, the optimal dyeing conditions, i.e, OWF, temperature, pH, and amount of auxiliaries, were identified when dyeing regenerated wood fibers using red-based reactive dyes (bis-monochlorotriazine: bis- MCT/MCT and bis-monochlorotriazine/vinyl sulphone: bis-MCT/VS type).
2. MATERIALS and METHODS
MDF (12-mm thickness and 0.62 specific gravity), which was manufactured using domestic pitch pine (Pinus rigida M.) and urea resin, was obtained from an industrial source to acquire Re-WF.
Red H-E3B of bis-MCT/MCT type and Red RB133% of bis-MCT/VS type were used as reactive dyes. Table 1 presents the types and major characteristics of the used dyes. The extra pure reagents were used as sodium sulfate and sodium carbonate. The SNOPOL SR-140 (Snogen Co.) anionoid was used as the soaping agent, and the SUPERFIX RF (Snogen Co.) cationoid was used as the fixation agent.
To obtain the regenerated fiber, 250 ml of distilled water was added to the MDF that had been cut into 50 × 50 × 12 mm, which was further immersed at 25°C for 48 hours and defibrated in a home-use mixer for 5 min. Then, it was dried and manufactured after being screened through a 300-μm screen.
Fig. 1 depicts the entire dyeing process. the regenerated fiber was inserted into a tall beaker, and each dyeing condition was reviewed with respect to the following basic conditions: 5% dye (OWF), liquid ratio 1:50, 50 g/L of Na2SO4, and 20 g/L of Na2CO3 for 80 min. at 80°C. Dyeing was performed under these conditions by varying the addition amounts of the dye (0, 1, 3, 5, 7, and 10%, OWF), the addition amounts of Na2SO4 (0, 10, 30, 50, and 70 g/L), the addition amounts of Na2CO3 (0, 2, 5, 10, and 30 g/L), and the dyeing temperature (60, 70, 80, and 90°C). Then, soaping treatment was performed for 10 min. in a liquid ratio of 1:50 with an addition 1 g/L of the soaping agent at 90°C.
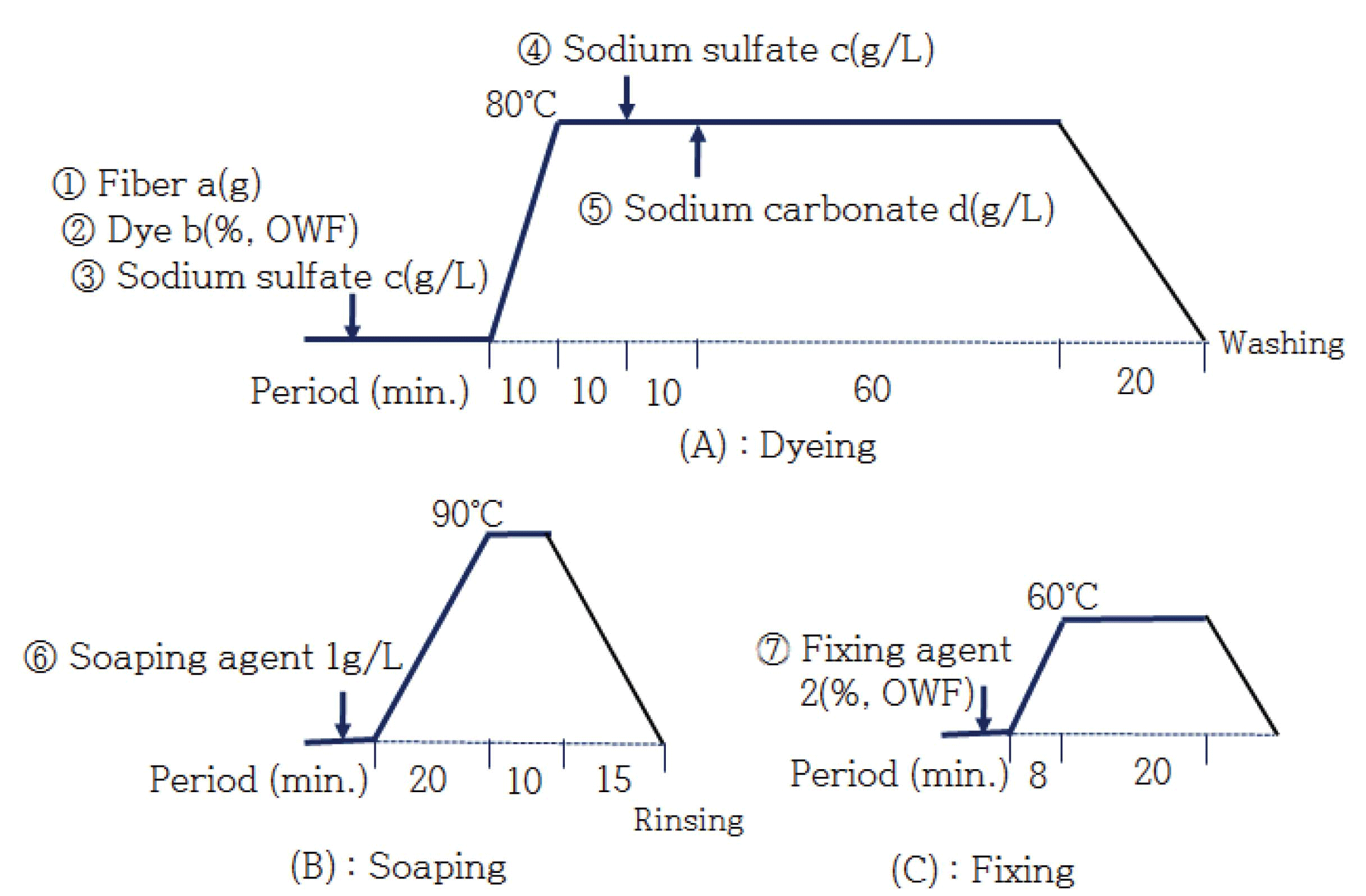
After soaping treatment, fixation treatment was performed for 20 min. in a liquid ratio of 1:50 with 2% OWF addition amount of the fixing agent at 60°C and then rinsed with water.
The sheet required for measuring the dyeing affinity, coloring, and color fastness to light was manufactured by adding the same amount of dyeing liquid and distilled water to the regenerated fiber dyed in different conditions using two types of reactive dyes that are processed in a mini-mixer for 2 min., filtered through the Whatman filtering paper, and compressed for 5 min. at 50°C.
The surface color of the regenerated dyed fiber was measured using Minolta CM-3800d (Japan). The color difference was obtained by dyeing based on the non-dyed Re-WF sheet. Further, the color difference after UV irradiation was calculated based on the differences of L*, a*, and b* before and after the irradiation. The K/S value was calculated using the following Kubelka–Munk equation after the surface reflectance of each dyed sample was measured.
K: Absorption coefficient
S: Scattering coefficient
R: Reflectance coefficient
The color fastness to light of the sheet manufactured using the fiber dyed with each dyes was assessed using the color differences in the CIE Lab color space before and after UV irradiation was performed for certain times using the accelerated weathering tester (QUV/SP, USA), UVB-313 lamp, and illumination of 0.67 W/m2 at a temperature of 50°C.
3. RESULTS and DISCUSSION
The dyeing process of cellulose fiber with reactive dye comprises the following phases: Phase A, where the reactive dye is adsorbed onto the cellulose surface and is permeated into the fiber, Phase B, where a covalent bond, such as an ether bond, is formed between the reactive group of the dye (mainly vinyl sulphone or chlorotriazine) and the hydroxyl group of cellulose, and Phase C or the stage of washing and fixation, which eliminates the alkali that has been added to induce the covalent bond for preventing hydrolysis or fiber damage and eliminates the non-reactive dye (CIBA-GEIGY, 1990). Furthermore, the dyeing properties vary according to the conditions that have been applied in each phase. The dye concentration that directly affects the spread of the dye, the addition amount of sodium sulfate as an inert salt for relieving the electrostatic resistance between the anions of cellulose and dye (Donnan potential), the amount of sodium carbonate added to stimulate the additional reaction or nucleophilic substitution (SN2) as the alkaline catalyst. Therefore, the relations between these dyeing conditions and the dyeing affinity were examined.
For the dyeing properties of cellulose fiber with a reactive dye, substantivity is very important as the dye distribution between the fiber and reactive dye in Phase A. Because only a limited amount of dye is absorbed onto the surface of the cellulose fiber, adding the dye above the saturating concentration for the surface may reduce the substantivity.
Table 2 presents the colors and color differences according to the dye concentration observed while dyeing the Re-WF with the reactive dyes of H-E3B (Bis-MCT/MCT type) and RB133% (Bis-MCT/VS type). First, the color of the Re-WF (Control) and equally treated Re-WF (Control-Tre) without the addition of the dye was yellow, with a tint of yellow–red (YR) at 0.2Y and 0.4Y, respectively. On the contrary, the Re-WF (Control-Tre) that was equally dyed without the addition of the dye exhibited a decrease in value, a slight increase in chroma, and the color difference was 3.8. This may be because of heating or the addition of additives. According to the National Bureau Standard (NBS) in the United States, this difference is evaluated as “appreciable” (color difference of 3.6–6.0).
With H-E3B, the colors observed using a dye concentration of 1%–10% were 0.2R to 2.6R. In a low concentration, the color was closer to red, whereas the color was close to RP when the concentration increased. However, the color difference of the dyed fiber with respect to the non-dyed Re-WF was 45.9–56.3, which rapidly increased at a low concentration but almost no difference could be observed at a concentration of more than 5%. The colors of RB133% of the Bis-MCT/VS type were 0.6R–0.7R and 9.6–10.0RP at dye concentrations of 1% and 10%, respectively, which were reddish and were almost close to red. Further, almost no difference in color could be observed in accordance with the dye concentration. However, the color difference was 38.6– 55.7, exhibiting an increasing trend as the dye concentration increased.
Fig. 2 shows the dyeing yields observed in accordance with the dyeing concentration of the reactive dye. The dyeing yields of H-E3B (maximum wavelength of 540 nm) and RB133% (maximum wavelength of 530 nm) increased when the dye concentration increased from 1% to 10%. The K/S of H-E3B (Bis-MCT/MCT type) was higher than that of RB133% (Bis-MCT/VS type) at all the dye concentrations. Therefore, the adequate addition amount of dye should be adjusted for achieving the target color. The color will becomes closer to red if the concentration increases up to 10%.
Fig. 3 denotes the color fastness of the regenerated fiber dyed with varying dye concentrations when compared with the color differences before and after UV irradiation for a certain time with an illumination of 0.67 W/m2 at a temperature of 50°C. This figure denotes that there was a large color difference in non-dyed woody fiber for MDF under UV irradiation. Although it was not possible to distinguish whether the discoloration of the dyed Re-WF under UV irradiation was caused by the fiber itself or the dye, the color difference of the dyed fiber was larger than that of the non-dyed fiber. The K/S of H-E3B was higher than that of RB133%; a lower color difference was observed using UV irradiation than that obtained using RB133%, denoting better resistance to discoloration by UV irradiation. Furthermore, the color difference of the H-E3B decreased as the dye concentration increased, while the color difference of RB133% (including vinyl sulphone) comparatively increased.
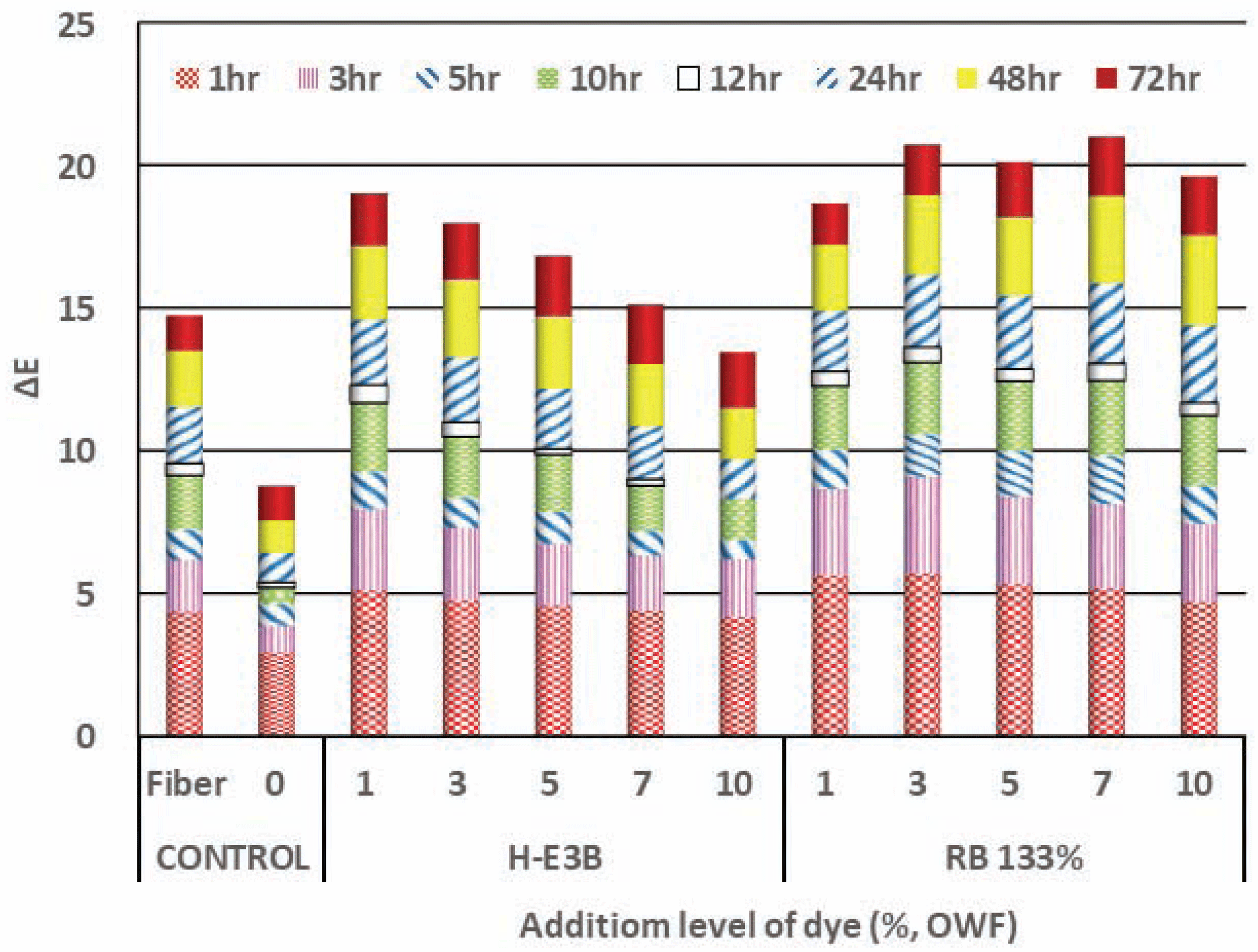
When cellulose is negatively charged in pure water and the dye is negatively charged as well, the approach and absorption of the dye to the fiber surface is interrupted because of the electrostatic resistance between the dye and fiber, resulting in weakening substantivity. If salt is added to the dyeing bath for improving the substantivity, the dye’s approach to fiber becomes easier due to the salting out effect. While dyeing the Re-WF with the reactive dyes of the Bis-MCT/MCT type H-E3B and the Bis-MCT/VS type RB133%, the colors and color difference obtained in accordance with the addition amounts of Na2SO4 (0, 10, 30, 50, and 70 g/L) were compared. The H-E3B and RB133% dyes successfully formed colors with color differences of 48.1 and 41.5, respectively, when salt was not added. However, the color difference increased as the addition amount of salt increased, and H-E3B exhibited a larger color difference than that exhibited by RB133% at all levels of salt additions.
The dyeing yield according to the salt concentration of the reactive dye is shown in Fig. 4. The dyeing yield of H-E3B with a maximum wavelength of 540 nm and that of RB133% with a maximum wavelength of 530 nm considerably increased as the salt concentration increased from 0 to 70 g/L. The K/S of H-E3B was higher than that of RB133% at all levels of salt concentrations.
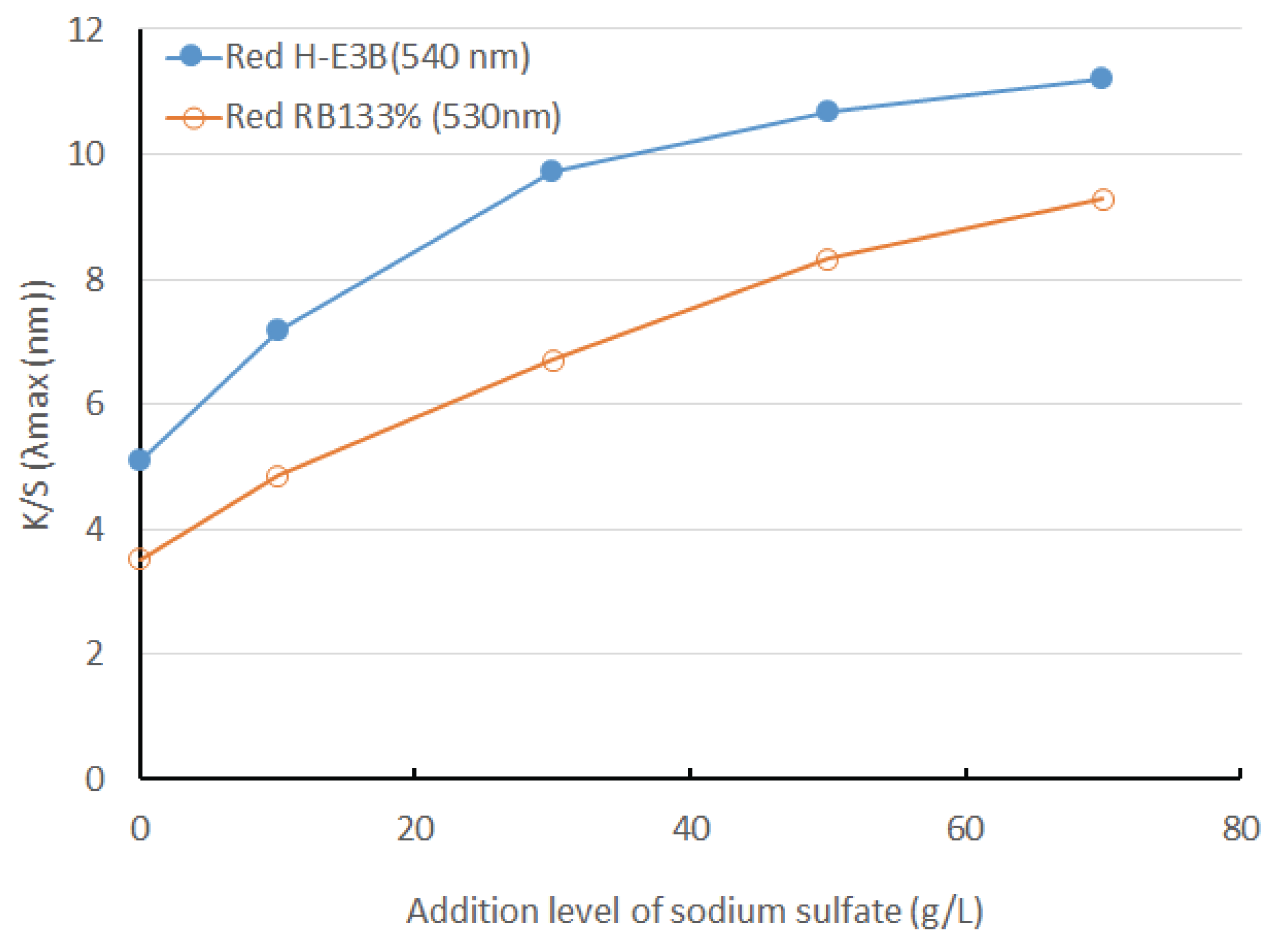
The color fastness to light of the regenerated fiber dyed using varying addition amounts of salt was observed based on the color difference before and after the UV irradiation for a certain time. H-E3B was better than the RB133% at all levels of salt concentrations. The color difference of H-E3B decreased as the addition amount of salt increased, whereas that of RB133% slightly increased up to 30 g/L but subsequently declined, indicating that 50–70 g/L was the effective addition amount of salt.
To dyeing cellulose fiber using a reactive dye, the dye is fixed to fiber through Phase A, where the reactive dye is adsorbed onto the surface of cellulose and then permeated into the fiber, and Phase B, where a covalent bond, such as an ether bond, is formed between the reactive group of the dye (mainly vinyl sulphone or chlorotriazine) and the hydroxyl group of cellulose. This reaction depends on the functional group of the dye, the MCT system depends on nucleophilic substitution (SN2), and the VS system depends on the nucleophilic addition reaction. To stimulate such a reaction, sodium carbonate is added to convert the pH of dyeing bath to alkaline for promoting the ionization of cellulose–(OH)n to cellulose–(O-)n. Table 3 lists the pH of the dying bath at each dyeing process, according to the amount of sodium carbonate addition. However, the pH did not vary according to the dye type. The pH of the dyeing bath was maintained at 4.3–4.5 before sodium carbonate was added but was converted into alkali when sodium carbonate was added. The pH increased to 9.5–10.8 as the addition amount increased.
Type of dye | pH | ||||||
---|---|---|---|---|---|---|---|
Water | Na2SO4 | Na2CO3 | Soaping | Fixing | |||
1st | 2nd | Amount (g/L) | pH | ||||
Red H-E3B, Red RB 133% | 4.4 | 4.3 | 4.4 | 0 | 4.5 | 9.8 | 8.1 |
2 | 9.5 | ||||||
5 | 10.2 | ||||||
10 | 10.5 | ||||||
20 | 10.8 |
While dyeing-Re-WF using the reactive dyes of the H-E3B and RB133%, the color differences were compared according to the addition amounts of alkali (0, 2, 5, 10 and 20 g/L). Therefore, the color differences of H-E3B and RB133% were 46.0 and 18.75, respectively, when sodium carbonate was not included. Particularly, RB133% dye of vinyl sulphone type did not properly form color until sodium carbonate was not added. However, the color difference considerably increased in 2 g/L where the pH was converted to alkali with sodium carbonate was added in both dyes. There was almost no difference in color by the further addition of sodium carbonate.
The dyeing yields of H-E3B and RB133% considerably increased while adding 2 g/L of sodium carbonate, exhibiting almost the same tendency as that exhibited by color difference; further, almost no difference can be observed by the further addition of sodium carbonate (Fig. 5).

The color fastness to light of the regenerated dyed fiber with varying addition amounts of alkali was compared before and after UV irradiation for a certain time. The color difference of the H-E3B decreased as the addition amount of alkali increased, but RB133% was almost not shown difference in the color difference until alkali was added 5 g/L or more into Bis-MCT/VS type. Therefore, the result indicates that the adequate addition amount of sodium carbonate is 5–10 g/L at pH 10.
As the dyeing temperature increases, the kinetic energy of the dye molecules increases, which further increases the dyeing speed reduces the time to reach the dyeing equilibrium, and affects the dyeing yield.
The colors and color differences were examined according to dyeing temperature in dyeing-Re-WF with the reactive dyes, such as H-E3B and RB 133%. The colors of the Re-WF dyed with H-E3B according to varied temperatures were determined as 0.2R to 1.6R. The color at a dyeing temperature of 60°C was red closer to RP becoming more red as the temperature increased. On the other side, the color difference between the non-dyed woody fiber and the dyed woody fiber ranged from 52.8 to 56.0, which increased from 60°C to 80°C but decreased at 90°C. The color of Bis-MCT/VS type RB133% was determined as reddish purple at 9.8 to 9.9RP, almost closer to red, with almost no difference being observed by temperature. However, the color difference showed the decreasing tendency ranging from 49.1 to 54.7 as the temperature increased.
Fig. 6 depicts the dyeing yield of two types of reactive dyes. The dyeing yield of the H-E3B, where a covalent bond is formed through nucleophilic substitution (SN2), increased as the temperature increased but declined again at 80°C. The RB133% showed almost the same dyeing yield up to 60–70°C through nucleophilic substitution and addition reaction but subsequently decreased. This is presumably because the cellulose fiber is dyed with reactive dye through the simultaneous fixing reaction and hydrolysis and because the hydrolysis reaction rate is higher than fixation reaction rate during the rise in temperature. Therefore, the application of optimal temperature according to the dye is important, suggesting that 80°C and 60–70°C are adequate for H-E3B and RB 133%, respectively.
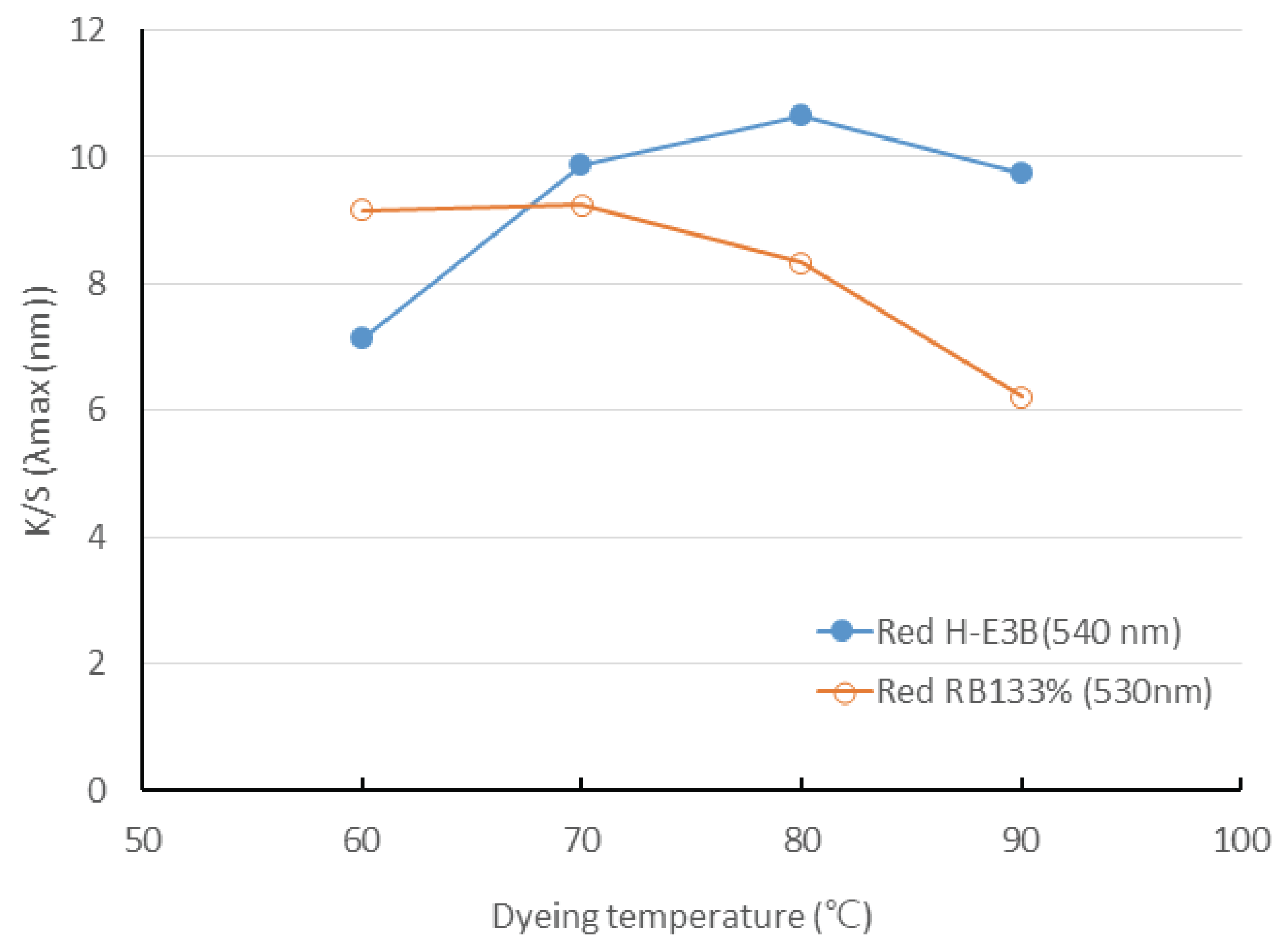
If the non-fixed dye is not sufficiently removed after dyeing is completed, the color fastness may deteriorate. Therefore, a soaping agent with high dispersibility and cleansing power is used to remove the non-fixed dye. Furthermore, the cationic fixing agent is mainly used to fix the reactive dye for preventing the repetition of readhesion and detachment of the fixed dye on fiber through hydrolysis. In terms of the color of a regenerated fiber that did not contain any dye, Fig. 7 depicts the color difference between the regenerated fiber dyed (W) that was dyed and simply washed with water for 70 min at 80°C with 5% dye (OWF), liquid ratio of 1:50, 50 g/L of Na2SO4, and 20 g/L of Na2CO3; with respect to the color of the dyed and soaping treatment fiber(W+S) that was treatment for 10 min. at 90°C with a liquid ratio of 1:50 and 1 g/L of the added soaping agent, the color difference of dyed, soaping, and fixation treatment (W+S+F) fiber that had been fixed the dye to the fiber for 20 min. at 60°C with the liquid ratio of 1:50 and 2% OWF of fixing agent added after soaping and cleansing.
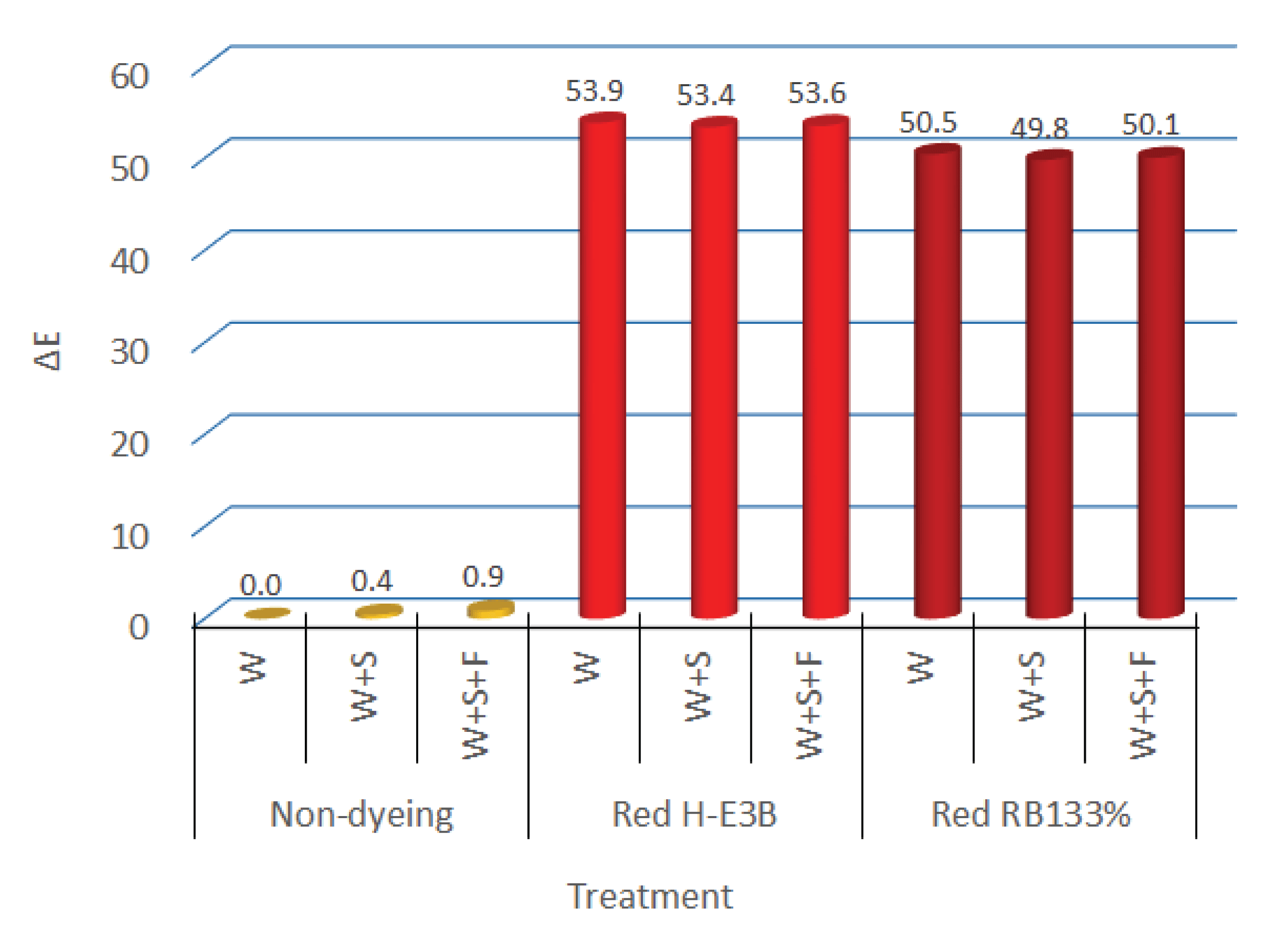
For the two types of dyes, the color differences of the regenerated fiber that was washed, soaped, and fixed without the addition of dye after each treatment were all below 0.5, which was evaluated as “trace” (color difference 0 to 0.5) according to the NBS. Furthermore, the colors of the regenerated fiber that was dyed with reactive H-E3B and RB133% and then washed were 1.8R and 10.0RP, respectively. After the soaping treatment, the colors were 1.6R and 9.90RP, whereas they were 1.6R and 10.0RP after fixing treatment, exhibiting only a minor difference. The color differences in the regenerated dyed (W), soaped (W+S), and fixed (W+S+F) fiber were determined as being at a similar level before and after UV irradiation for a certain time.
4. CONCLUSION
The findings regarding the influences on dyeing properties and color fastness to light due to dye concentrations, additional amounts of salt and alkali, and dyeing temperature in dyeing for Re-WF obtained from waste MDF manufactured with pitch pine and with the two types of reddish reactive dyes (H-3EB: bis-MCT/MCT and RB 133%: bis-MCT/VS) are as follows:
The colors of the Re-WF dyed at a dyeing concentration of 1% to 10% with reactive H-E3B were determined as 0.2R to 3.6R, ranging from red close to RP at low concentrations to a reddish color at higher concentrations. The color difference of the non-dyed Re-WF was 45.9 to 56.3, which rapidly increased at low concentrations, but hardly varied at concentrations of 5% or higher. The colors of the Bis-MCT/VS type RB133%, ranging from 9.6RP to 10.0RP, were determined as reddish purple closer to red at dyeing concentrations of 3% and 7%, showing almost no color difference according to the dyeing concentration. The dyeing yield of the two types of dye increased as the dyeing concentration increased, and the K/S of H-E3B was higher than that of RB133% at all the dyeing concentrations. The color difference obtained using UV irradiation was lower in RB133% than that in H-E3B.
As the addition amount of sodium sulfate increased in H-E3B and RB133% dyes, the color difference and K/S increased and the color fastness to light was good. Therefore, the result suggests that the adequate addition amount of salt was 50–70 g/L.
The color difference and K/S of H-E3B and RB133% considerably increased when the pH was converted into alkaline by adding 2 g/L of sodium carbonate, but there was almost no difference by adding further amount of sodium carbonate. For H-E3B, the color difference before and after UV irradiation decreased when the addition amount of alkali increased; however, RB133% showed almost no difference when the addition was 5 g/L or more. Therefore, the adequate addition amount of sodium carbonate was 5–10 g/L at pH 10.
Even though the dyeing yield of H-E3B increased as the dyeing temperature increased but again decreased at 80°C, the dyeing yield of RB133% exhibited an almost identical up to 60–70°C but decreased subsequently. Therefore, the result suggests that the temperatures of 80°C and 60°C are adequate for H-E3B and RB133%, respectively.