1. INTRODUCTION
The policies for the protection of domestic wood industries in countries with wood resources have not been established because of which the lack of wood resources is likely to continue. Therefore, eco-friendly materials must be developed using the available wood resources such as waste wood resources, construction waste, and thinned logs as domestic wood prices are rising every year. To overcome this issue, a domestic timber supply and demand system must be developed that can substitute for wood fiber and other fiber resources. In addition, new material resources must be developed using other agricultural by-products. Annual production of domestic mandarins is ~640,000 tons as of 2016, and 90% of these mandarins are processed into juices and beverages. An enormous amount of peel is generated as a by-product during processing (KOSIS, 2016). Dried mandarin peel can be used as a medical herb. Pre-treated dried mandarin peel can be used as a feed (Jang et al., 2004). However, storage of this dried peel is a problem because mandarin is cultivated every two months in a year. Thus, a significant amount of mandarin peel is dumped into the ocean, thereby causing environmental pollution.
Sawdust, a by-product from wood processing, is used herein. Since sawdust has a high water uptake rate, it is mainly used for manure handling in livestock farms. Sawdust compost is used for producing by-products and for feed.
Although the quantity of sawdust generated depends on the log thickness and lumber dimension, sawdust with a volume ratio of ~10% can be generally obtained. According to the Statistical Yearbook of Forestry 2017, 979,527 m3 and 53.9 billion won worth of sawdust was produced in 2016 and consumer price was 55,000 won/m3, which is only 1/5 of the wholesale price for lumber. Therefore, if sawdust produced from thinning logs and forest wood waste is used effectively, it will significantly contribute to the activation of domestic forestry and wood processing industry.
In this study, woodceramics are manufactured using new porous carbon material developed by Okabe and Saito (1995), which was obtained by carbonizing in vacuum after impregnating with phenol formaldehyde resin. It is light and hard and has excellent corrosion resistance, durability, and thermal conductivity. It has several characteristics, including electromagnetic wave shielding effect and far-infrared radiation, and is cheaper than other C-C compounds. Thus, this new material will be used as raw materials for producing electromagnetic products, friction materials, and automobile accessories in the future (Okabe and Saito, 1995a, 1995b; Okabe et al., 1995a, 1995b).
Oh (2001, 2002, 2003) measured the physical properties of woodceramics developed from sawdust board made of thinned logs, and Oh (2002) and Oh & Byeon (2002, 2003) fabricated woodceramics under various conditions using medium density fiberboard (MDF) and determined its properties. By re-carbonizing the woodceramics made from sawdust board, Oh & Hwang (2009) prepared high-density woodceramics and determined its basicproperties. Byeon et al. (2010) investigated the effect of carbonization temperature and resin impregnation rate on the properties of the woodceramics made from Broussonetia kazinoki Sieb. Oh et al. (2014) measured the basic properties of the woodceramics made from miscanthus sinensis var. purpurascens particles, and Won et al. (2014) studied the development of new material using ligneous materials by evaluating the nondestructive bending strength of miscanthus sinensis var. purpurascens woodceramics at carbonization temperatures.
Hwang & Oh (2017) determined the physical properties of woodceramics made from sawdust and mandarin peel. Oh et al., (2018) manufactured carbonized board at carbonization temperature using ash tree board, PB, MDF, and plywood and examined the possibility of using the carbonized board as a heating plate. Various manufacturing methods and applications have been studied (Hokkirigawa et al., 1996a, 1996b; Hirose et al., 2002; Iizuka et al., 1999; Xian et al., 2002; Zhao et al., 2002; Oh and Park, 2010; Oh and Piao, 2004; Hwang and Oh. 2017). This study examined the possibility of using carbonized board as a planar heating element by evaluating the changes in surface temperature of the composite woodceramics and the far-infrared radiation properties based on the manufacturing conditions. These parameters were evaluated for boards prepared using different density and mixing ratios of mandarin peel and sawdust. These boards were impregnated with resin and ceramicized via carbonization at ≥ 600°C.
2. MATERIALS and METHODS
Sawdust obtained from the thinning of Larix kaemferi C. was purchased from sawmill. For the uniformity of the samples during the manufacture of the board, theparticle size of 18 mesh was selected and the water content was adjusted to ≤ 6%.
Mandarin peel was purchased from Jeju Island and dried under shade. To increase the bonding strength during board manufacturing, a particle size of 18 mesh was obtained by crushing the peel using a pulverizer and water content was adjusted to ≤ 5%.
To prepare a board mixed with sawdust and mandarin peel, powder phenolic resin (KNB-100PL, manufactured by Kolon Chemical Industry Co., Ltd.) was used. The amount of resin added was 10% (weight ratio) of the mixed amount of sawdust and mandarin peel. A liquid phenolic resin (KPD-L777, KOLON CHEMICAL Co., Ltd.) was used for impregnation to produce woodceramics. Table 1 shows the properties of each resin.
To manufacture the board, uniformly selected sawdust and mandarin peel and powdered phenolic resin were fully mixed and placed in a stainlesss quare mold on a hot plate of a hot press. A board size of 26 cm in width × 26 cm in length – 1.4 cm in thickness was produced via hot press molding. To obtain a board of 0.6-g/cm3 density, mandarin peel was added in the ratios of 5%, 10%, 15%, 20%, and 25%.
When the mandarin peel addition ratio was 10%, a board with a density of 0.4, 0.5, 0.6, and 0.7 g/cm3 was manufactured. A total of 10 boards of each density was manufactured at a hot pressing temperature of 190°C, pressure of 40 kgf/cm2 → 30 kgf/cm2 → 20 kgf/cm2 (three-stage pressurization), and pressing time was 6 min → 5 min → 4 min (three-step pressing time). To maintain a constant board thickness during hot pressing, a thickbar was used. A teflon plate was used to prevent the adhesion of the upper and lower surfaces of the board due to heat from the hot plate.
The size of the manufactured board was 1.4 × 12 × 12 cm3, and its density was calculated. In addition, a specimen with a target density of ± 0.03 g/cm3 was selected for each condition to keep the test conditions constant.
The prepared specimen was placed in an impregnation tank containing liquid phenolic resin. Then, decompression (1 atmosphere) and ultrasonic treatment (frequency: 28 kHz, output: 564 W) were performed for 20 min.
The specimen was subjected to these treatments at a normalpressure for 20 min. This process was repeated three times, and the impregnation rate was controlled by adjusting the repetition times. A decompression ultrasonic impregnation device used for impregnation comprises an impregnation tank, an ultrasonic vibration part, an ultrasonic oscillation part, and a vacuum pump. After the impregnated specimen was dried under shade for 8 h, it was placed in a drier and cured continuously at 60°C for 8 h and at 130°C for 8 h. Then, the physical properties of the board before and after impregnation were measured.
Woodceramics were prepared by selecting boards with a resin impregnation rate of 60 ± 3% among boards with a mandarin peel addition ratio of 5%, 10%, 15%, 20%, and 25% and board with a resin impregnation rate of 40 ± 3%, 50 ± 3%, 60 ± 3%, and 70 ± 3% among the impregnated boards with a mandarin peel addition ratio of 10% using a vacuum furnace. These boards were carbonized at 800°C. In addition, woodceramics were prepared by selecting specimens with resin impregnation rate of 50 ± 3% among the impregnated boards with density of 0.6g/cm3 and a mandarin peel addition ratio of 10% and carbonizing at 600°C, 800°C, 1000°C, and 1200°C, respectively. During this time, the temperature was raised from the room temperature to 4°C/min; after maintaining at the set temperature for 2 h, cold water was circulated around the carbonization furnace to cool it.
The resin impregnation rate of the impregnated material was calculated from Equation (1) as the percentage of resin injected for the oven-dry weight of the composite board.
where
W1: the oven-dry weight of board after resin impregnation (g)
Wn: the oven-dry weight of board before resin impregnation (g)
To measure the surface temperature of the woodceramics, the surface temperature of the heater was increased. A temperature sensor was attached at the center of the heater after connecting the silicon rubber heater to the electric voltage regulator at the set temperature. The variation in temperature was measured by placing the woodceramics on the heated silicon rubber heater and attaching the temperature sensor to the four spots of the surface using a paper tape. The surface temperature of the silicon rubber heater was set as 60°C and the woodceramics was placed on it. The variation in the surface temperature of the ceramics was measured for 30 min at 3 min intervals. Then, the heater was turned off, after which the surface temperature of the ceramic surface and heater was measured for 30 min at 3 min intervals to determine the heat retention of woodceramics made from the manufactured board.
3. RESULTS and DISCUSSION
To investigate the validity of the manufactured woodceramics as a planar heating element, the variations in surface temperature of the woodceramics were measured; the surface temperature of silicon rubber heater was maintained at 60°C. The results are shown in Figs. 1–6. Woodceramics’ surface temperature increases with time (Figs. 1–3). As shown in Fig. 1, surface temperature rapidly increases depending on the resin impregnation rate for 12 min and become gradual thereafter. Ceramic has a fast heat transfer rate in the beginning. After 30 min, the surface temperature was 40.5°C, 41.7°C, 40.6°C, and 41.3°C when the resin impregnation rate was 40%, 50%, 60%, and 70%, respectively, thereby showing similar values regardless of the impregnation rate. This indicates that there is no significant difference in the thermal conductivity of the specimens in accordance with the resin impregnation rate after carbonization.
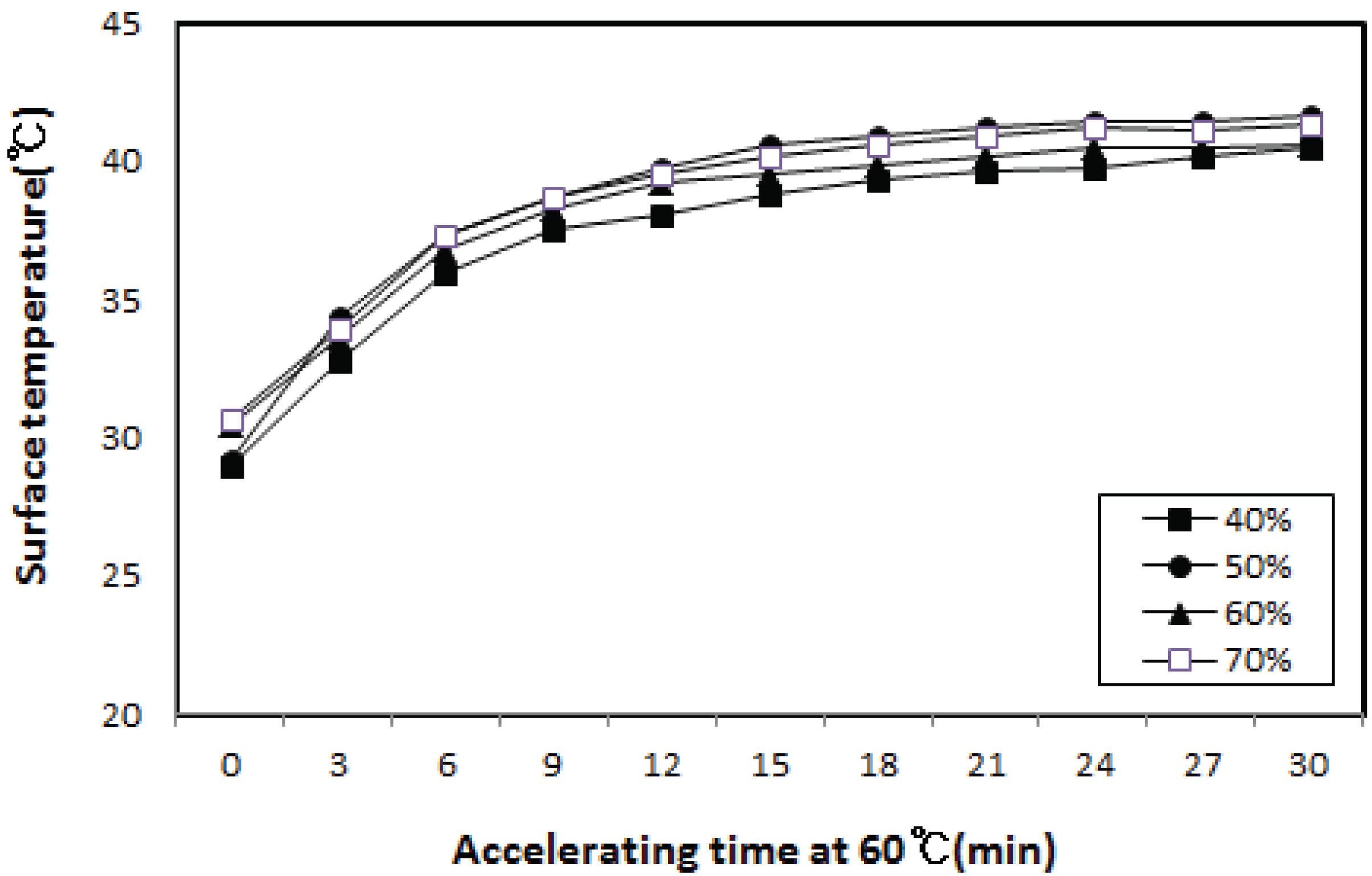
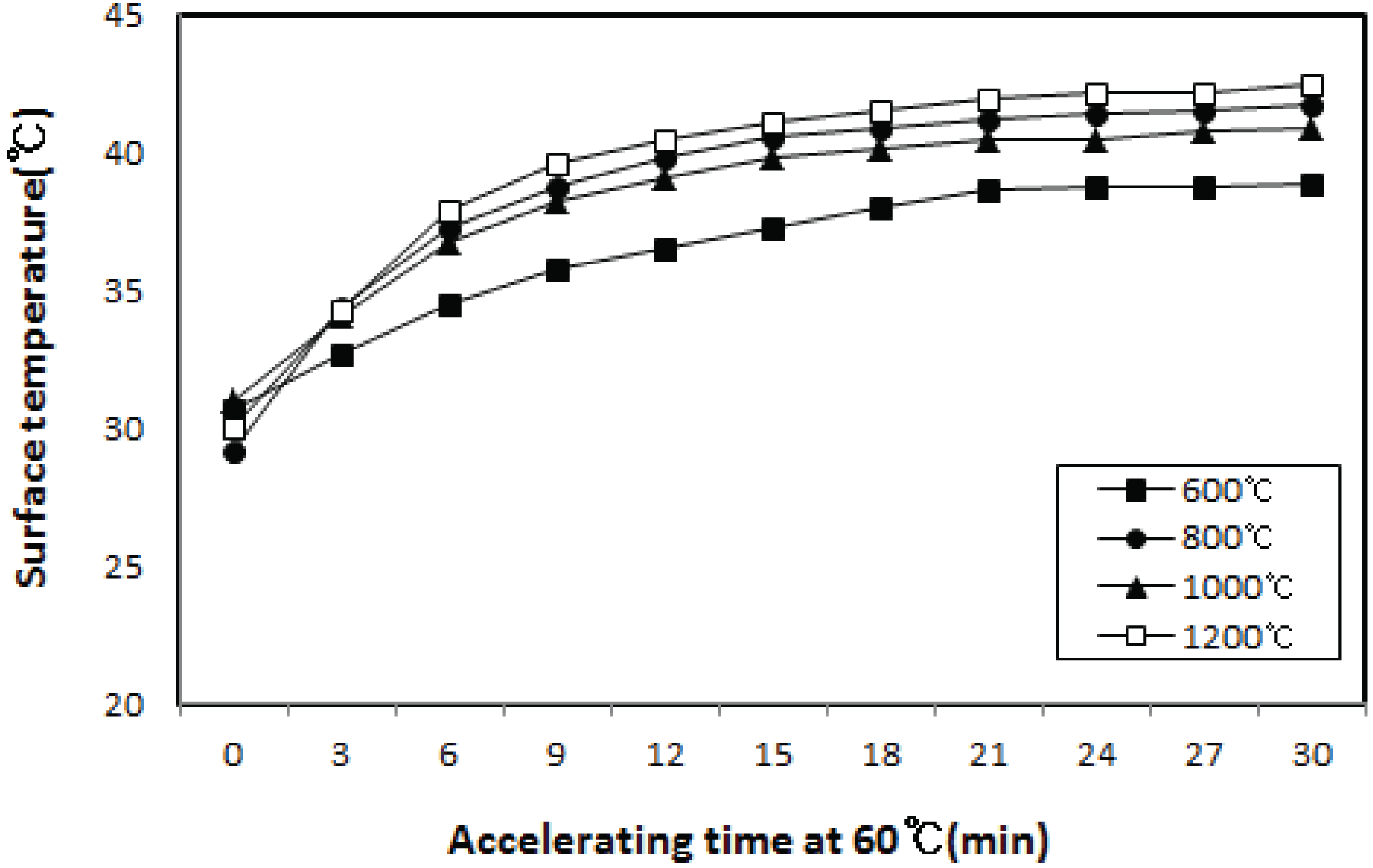
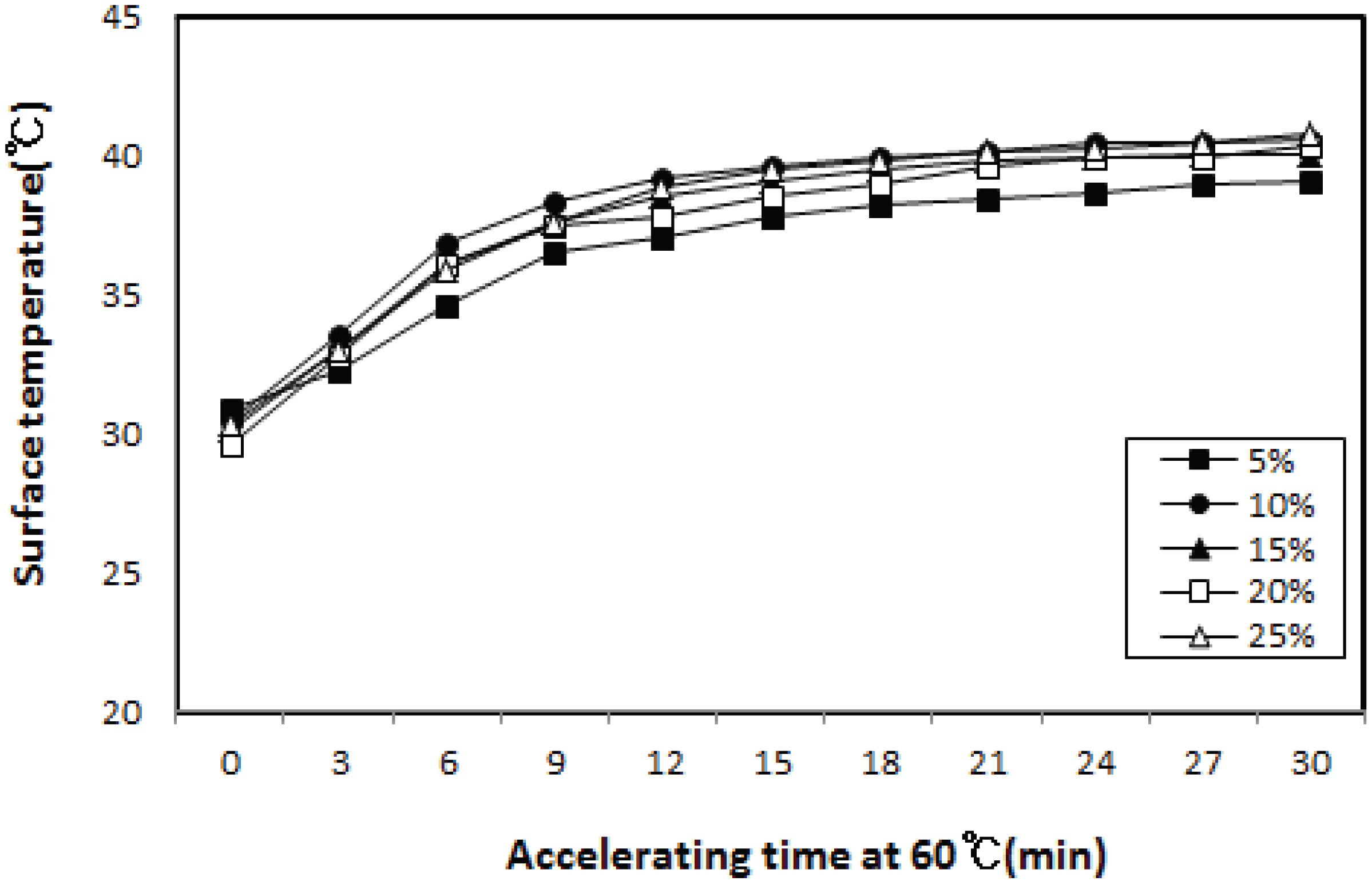
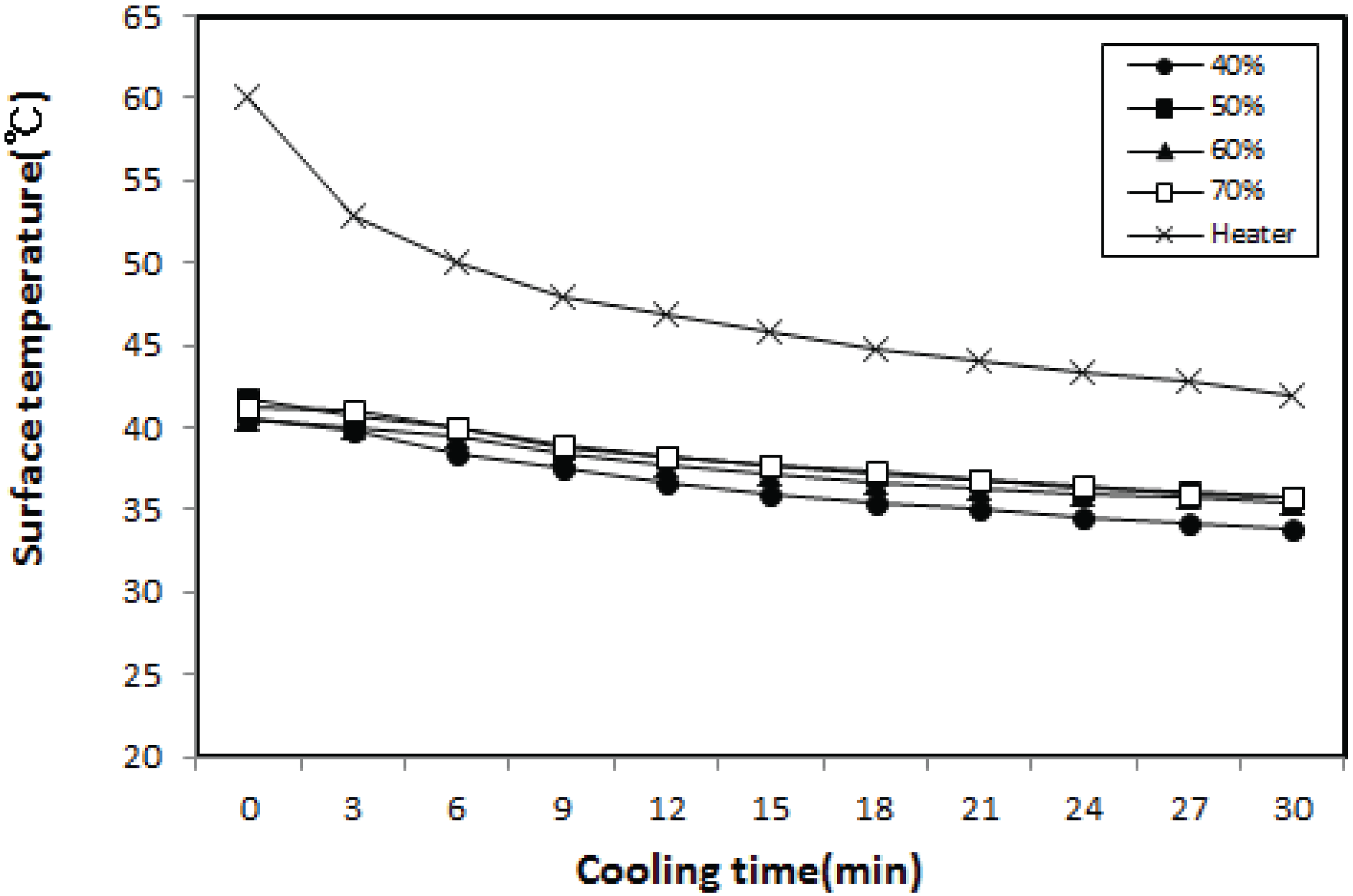
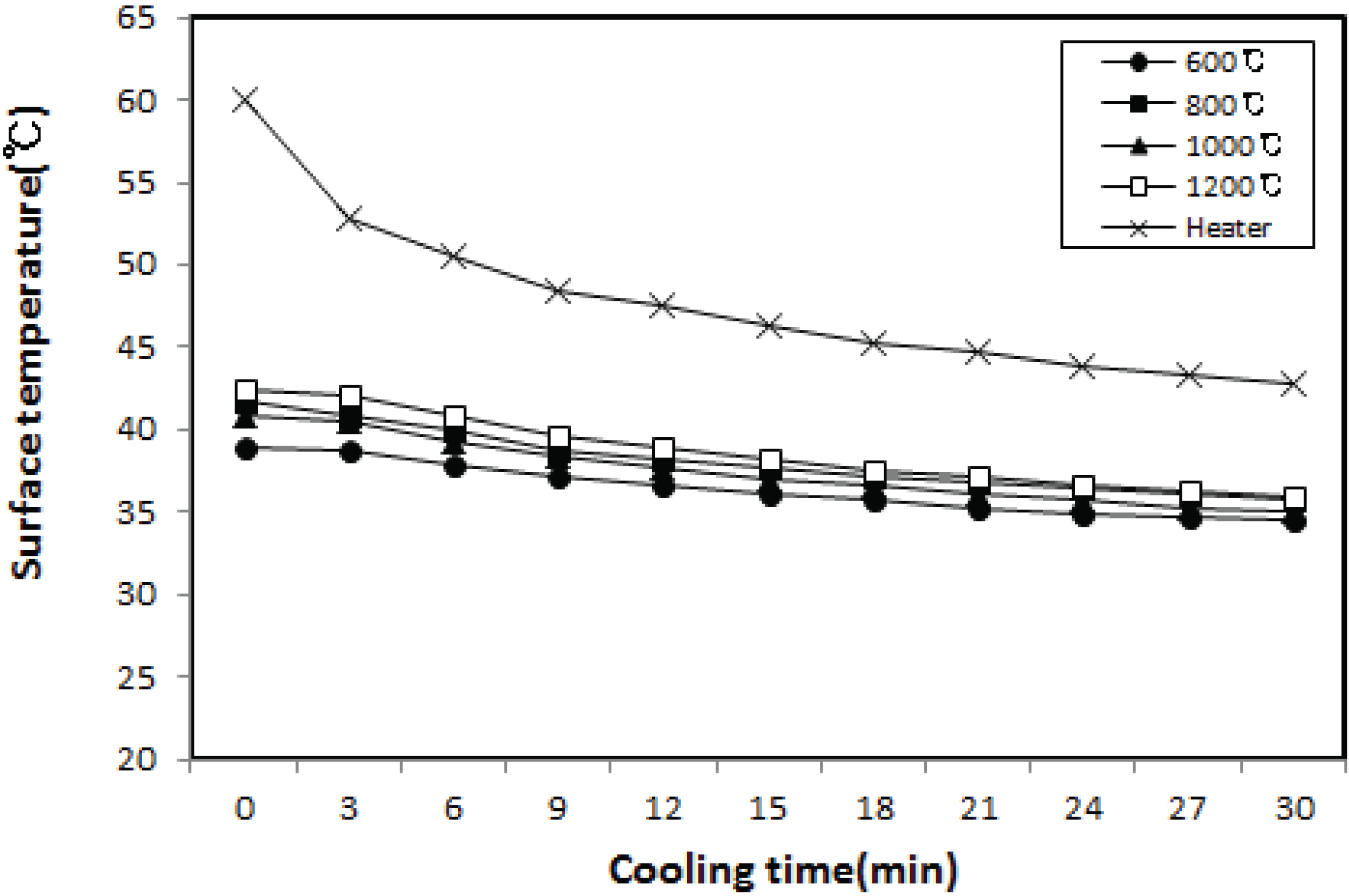
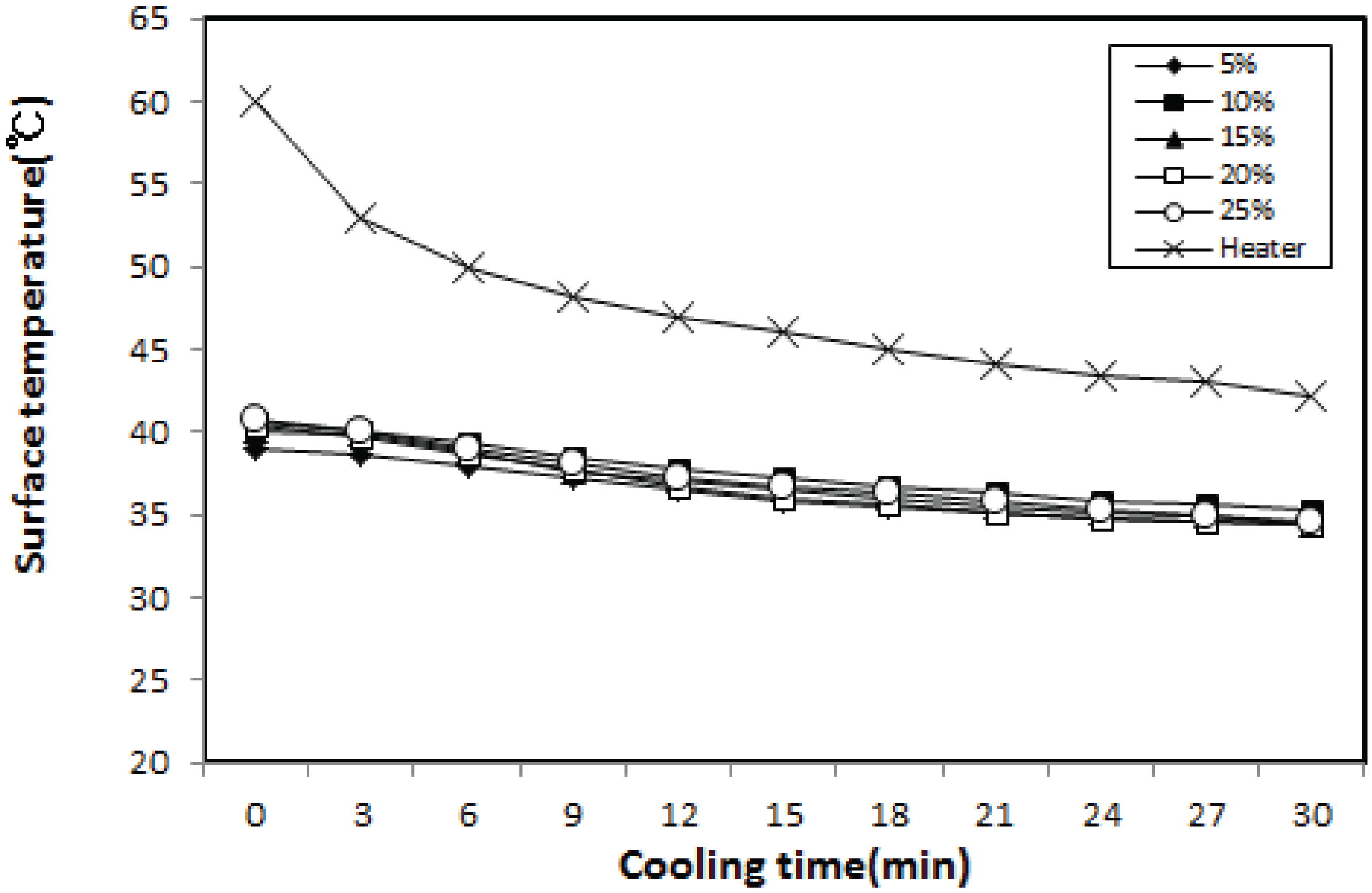
As shown in Fig. 2, the surface temperature of woodceramics rapidly increased as the carbonization temperature increased up to 9 min and increased slowly afterwards. At 30 min from the beginning of the experiment, specimens with carbonization temperature of 600°C, 800°C, and 1200°C had a surface temperature of 38.9°C, 41.7°C, and 42.5°C, respectively. At the carbonization temperature of 600°C and 1200°C, the surface temperature of the specimen was the lowest and highest, respectively.
As shown in Fig. 3, in case of mixed woodceramics for which specimen with a resin impregnation rate of 60% was carbonized at a carbonization temperature of 800°C, change in surface temperature of woodceramics according to the mixing ratio of mandarin peel showed a tendency to rise rapidly until the elapsed time of 9 min and gradually increased thereafter. When the addition ratio was 5%, 10%, 15%, 20%, 25%, the surface temperature of the woodceramics at the elapsed time of 30 min was 39.1°C, 40.6°C, 40.1°C, 40.4°C, and 40.8°C, respectively. All five specimens showed similar values, indicating that the mixing ratio of mandarin peel does not influence the thermal conductivity after carbonization. Conversely, after measuring the increase in surface temperature, the power of the silicone rubber heater was turned off to lower the surface temperatures of the heater and the woodceramics. The decrease in surface temperature of the heater was measured for 30 min at 3 min intervals; results are shown in Figs. 4–6.
As shown in Fig. 4, a decrease in surface temperature of the woodceramics according to the resin impregnation rate was observed as the surface temperature of the heater decreased from 60°C to 42°Cfor 30 min. The surface temperature decreased from 40.5°C to 33.8°C for specimen with a resin impregnation rate of 40% and from 40.6°C to 35.4°C for specimen with a resin impregnation rate of 60%. It decreased from 41.3°C to 35.7°C when with the resin impregnation rate was 70%. Accordingly, the surface temperature of woodceramics decreased gradually after a point of time. As shown in Fig. 5, the surface temperature of the woodceramics decreased as the surface temperature of the heater decreased from 60°C to 42.8°C for 30 min. The surface temperature decreased from 38.9°C to 34.5°C for the specimen carbonized at 600°C and from 40.9°C to 35.0°C for the specimen carbonized at 1000°C. It decreased from 42.5°C to 36.0°C for the specimen carbonized at 1200°C, continuing to decrease gradually with time. The difference between the initial temperature of the specimen prepared at carbonization temperature of 1200°C and the temperature after 30 min was large (6.5°C), and the surface temperature of the specimen at 600°C was relatively low (4.4°C). Regarding the decrease of surface temperature of the woodceramics, a lower carbonization temperature was associated with higher degree of heat retention. As shown in Fig. 6, the surface temperature of the mixed woodceramics according to the mixing ratio of mandarin peel decreased as the surface temperature of the heater decreased from 60°C to 42.2°C. The surface temperature decreased from 39.1°C to 34.4°C for the specimen with mandarin peel addition ratio of 5% and from 40.1°C to 34.4°C for the specimen with mandarin peel addition ratio of 15%. It decreased from 40.8°C to 34.6°C for the specimen with mandarin peel addition ratio of 25%.
The higher the addition ratio, the rapidly the ceramic surface temperature decreases but the difference is insufficient. Thus, woodceramics manufactured with the resin impregnation ratio of ≥70% and mandarin peel addition ratio is 5% at 1200°C can be used as a raw material. Further, since the manufactured woodceramics retains heat for a long time, it can be used as a material for a planar heating element. However, as the change in surface temperature of woodceramics seems to be most closely related to the density of the specimen, parameters, such as resin impregnation rate, carbonization temperature, temperature rise, material properties, and electrical properties, required for woodceramic manufacturing must be studied in the future.
Far-infrared emissivity and infrared-radiation emission power were measured for mixed woodceramics with a resin impregnation rate of 60% carbonated at 800°C. Results are shown in Figs. 7 and 8. Total emissivity compared to ideal blackbody in the 5-20-μm wavelength region of the woodceramics was 0.929, 0.927, 0.929, and 0.930 when the mandarin peel addition ratio was 5%, 10%, 15%, and 20%, respectively. The far-infrared emissivity by mandarin peel addition ratio increased slightly with increasing mandarin peel addition ratio. IR emission power was 375, 373, 374, and 375 W/m2 when the mandarin peel addition ratio was 5%, 10%, 15%, and 20%, respectively. Thus, the IR emission power was the highest when the mandarin peel addition ratio was 5% but there was no significant difference when compared to other specimens.
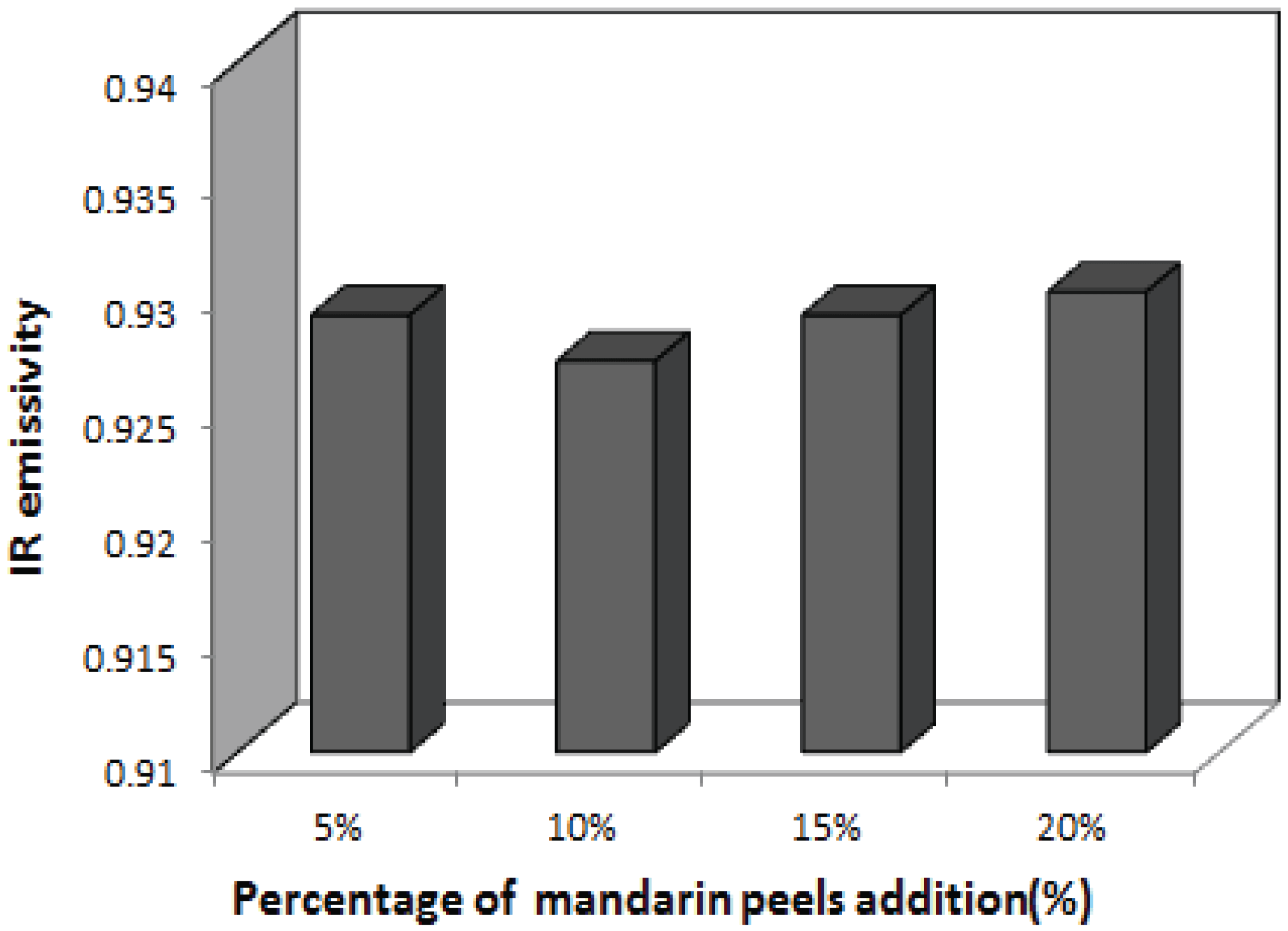
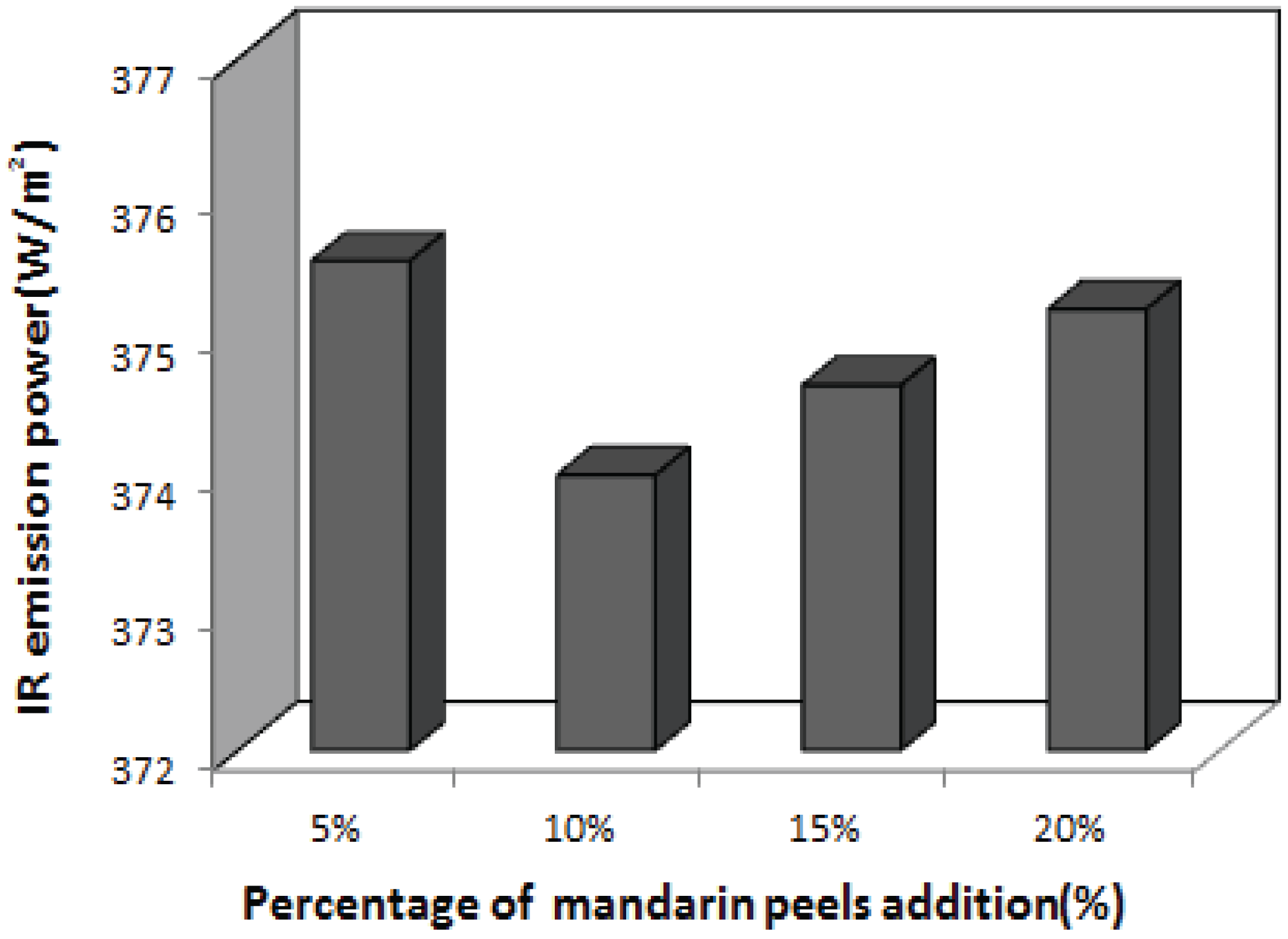
Moreover, far-infrared emissivity and IR emission in accordance with the carbonization temperature of the mixed woodceramics were measured after carbonizing the board with a resin impregnation rate of 60% and a mandarin peel addition ratio of 10%. Results are shown in Figs. 9 and 10. The far-infrared emissivity was 0.930 and 0.927 when the carbonization temperature was 600°C and 800°C, respectively. The far-infrared emissivity was 0.927 and 0.922 when the carbonization temperature was 1000°C and 1200°C, respectively. This indicates that the far-infrared emissivity decreased as the carbonization temperature increased. IR emission power was 374 and 373 W/m2 when the carbonization temperature was 600°C and 800°C. IR emission power was 374 and 371 W/m2 when the carbonization temperature was 1000°C and 1200°C, respectively. IR emission power tended to decrease as the carbonization temperature increased. Oh (2016) reported that higher carbonization temperature is associated with decreasing emissivity in far-infrared emissivity measurement of woodceramics made with sawdust and rice husk. This far-infrared emissivity was higher than silica sand (0.60 ~ 0.80), elvan (0.90), and SiO2 (0.83) and similar to charcoal (0.93), graphite (0.93), and ceramic-coated board (0.924). In particular, woodceramics made with sawdust and rice husk showed higher value than the measured far-infrared emissivity of woodceramics made from thinned logs (Oh and Byeon,2006).
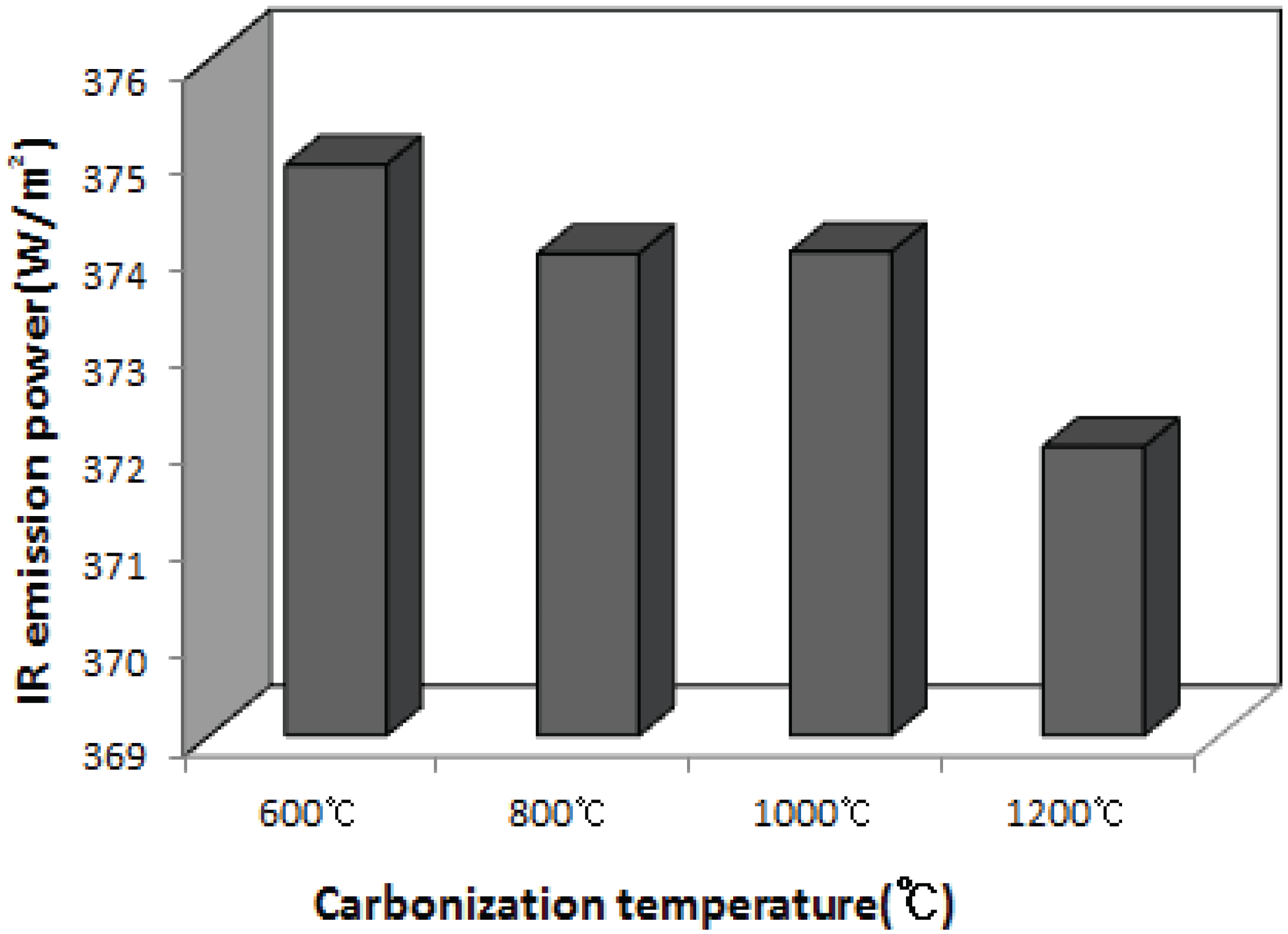
4. CONCLUSION
Using sawdust and mandarin peel, a mixed woodceramics was prepared using various resin impregnation rates, carbonization temperatures, and mandarin peel addition ratios. The surface temperature and far-infrared radiation characteristics of the mixed woodceramics were determined and the following conclusions were deduced:
As the surface temperature of the mixed woodceramics rapidly increased until the elapsed time of 10 min, the rate of temperature rapidly increased at the initial time of heat transfer. At the elapsed time of 30 min, the surface temperature increased as the carbonization temperature increased and the mandarin peel addition ratio had no significant effect on the surface temperature variations.
The far-infrared emissivity did not have a certain trend depending on mandarin peel addition ratio and decreased as carbonization temperature increased. IR emission power also showed a similar tendency as the far-infrared emissivity.