1. INTRODUCTION
In the world, the distribution area of bamboo is about 37 million hectares (ha) (Lobovikov et al., 2007). About 11 genera and 35 bamboo species are growing in Indonesia, and total amount of Indonesian bamboo forest occupies 5 % of bamboo forest in the world (approx. 2.2 million ha, INBAR 2005). In Indonesia, bamboo has been cultivated with trees and edible crops in some of the residential gardens called “Pekarangan” and is widely distributed in Java, Bali, and Sulawesi areas. Bamboo is one of the BBC (Bamboo, Banana, Coconut) group which has played a very important role in daily life in Indonesia. It has been used for architecture, household goods, furniture, musical instruments, textiles, and mats after first simple physical processing (Febrianto et al., 2014; Yudodibroto, 1985). Moreover, bamboo has been used as materials of paper and plywood after secondary processing (Sutardi et al., 2015). Bamboo resources have been exported to Australia and Europe beyond domestic consumption, reaching up to 3 million US dollars in 2007 year (Hardiani and Dewy, 2014).
However, the use of bamboo has been steadily declining due to the appearance of alternatives, such as plastics, for wood-based products. In addition, Indonesian bamboo exports have fallen to less than half of 2007 year (1.5 million US $). Nevertheless, the Indonesian government still considered bamboo as a potential non-timber product, and aimed to change the crisis of bamboo industry by transition of bamboo to competitive resources. Under the specific goal of encouraging use of bamboo in daily life, the development of bamboo industry was proceeding in Central Java, West Java, East Java, Bali, etc. (Hardiani and Dewy, 2014). It has been recognized that the high value added process on bamboo, which can guarantee the income of farm, is one of the important key to build bamboo industry which can encourage local people to participate, and a lot of research has been done. Maulana et al. (2017) and Febrianto et al. (2015, 2012) developed a durable bamboo oriented strand board (OSB) using Andong, Betung, and Ampel bamboo, and Kim et al. (2001) evaluated the characteristics of Tali bamboo by making bamboo zephyr. Jang et al. (2013) conducted a study to isolate nanocelluloses from Betung bamboo by the delignification method and apply them as reinforcing fillers for biodegradable polymers.
In particular, converting bamboo into biomass energy is the most prevalent field of applied research on bamboo utilization. Compared to coal, biomass generally does not require long production times and cause less environmental pollution (Basu, 2013). In addition, the rapid growth of bamboo could potentially replace depleting woody resources, so research has been actively pursued in line with current trends in green and renewable energy. Bamboo biomass produced by pyrolysis and carbonization has been used mainly as fuel for household and iron smelting in the past (Nurhayati, 1990). In recent years, carbonized bamboo has been used as a soil remediation agent (fertilizer papers) using a rich inorganic component of bamboo, or as a heavy metal adsorbent that improves the adsorption performance by developing microstructure (Mizuta et al., 2004; Wang et al., 2010). However, the bamboo industry in Indonesia is still staying in simple product compared with other advanced countries in research and development on bamboo biomass.
In this study, bamboo carbonization technology was applied to search the developing direction for bamboo industry in Indonesia. The genera of Bambusa, Gigantochola and Dendrocalamus have been widely used in Indonesia according to rapid growth rate and sympodial growing pattern. These were selected in this study and these bamboos were carbonized at different temperature. The anatomical and physical characteristics were investigated.
2. MATERIALS and METHODS
Six species of bamboo (4-5 years old) belong to Gigantocloa, Bambusa and Dendrocalamus genera were collected from experimental bamboo plantation of Bogor Agricultural University, in West Java, Indonesia. The secondary node from the ground of the sampled bamboo was air-dried in ambient condition for 3 months and used in the experiment. Detailed information is given in Table 1.
One node of bamboo sample was cut at intervals of 25 mm in radial direction, and then cut at 40 mm intervals in the direction of the fiber. Cut samples (25 mm (R) × 40 mm (L)) were carbonized at 200, 400, 600, 800 and 1,000 °C. Carbonization was carried out according to the technique of producing charcoal using heat-resistant container (Park et al., 2009). It was possible to produce defect-free charcoal without additional injection of nitrogen. To prevent oxidation during the carbonization process, a dozen or more samples were alternately wrapped in newspaper and aluminum foil, and then placed in a small rectangular heat-resistant container with a lid. A heat-resistant container was placed in a laboratory electrical furnace (TST BT-F724, Korea) and carbonization was carried out at a target temperature by setting a heating rate at 50 °C/h. After reaching the target temperature of electrical furnace, it was maintained for 2 hours, and after natural cooling for sevral hours the heat-resistant container was taken out of the electric furnace and then the carbonized bamboo was taken.
Sample preparation was conducted according to the method described by Kwon and Kim (2006). The cross section of the original bamboo specimen was prepared with a microtome after softening in water 2 weeks. After the carbonization, the specimens were machined to 5 mm (R) × 5 mm (T) and the central part was broken to obtain a clean and parallel cutted surface. These specimens were coated with gold and palladium and observed with a scanning electron microscope (COXEM-30, COXEM, Korea). The anatomical characteristics of carbonized bamboo were analyzed mainly by array observation of the parenchyma cell and measuring the diameter of the lumen and vessel.
The physical characteristics of specimens were determined according to KS F 2198 (KSA, 2016) and KS F 2199 (KSA, 2016). The dimension and weight of control specimens and carbonized specimens were measured, and then all samples were dried at 103±2 °C for 24 hours. After cooling of samples at desiccator, dimension and weight of samples were measured again. The moisture contents, volume reduction rate, weight reduction rate, and density of samples were calculated by following formulas in Table 2.
The hardness of samples was measured by using Miura hardness tester (Miura, Japan). The special metal strips, which adjusted to 20 levels from lead to iron, were used in this experiment. The surface of control and carbonized specimens was scratched by metal strips for determining hardness (Hyodo and Fujii, 2016).
Refining is an operation that removes volatile gases at final stage of charcoal process, and is an important process for increasing the quality of charcoal by uniformizing carbonization degree of entire charcoal. The refining degree meter (Miura, Japan) designed by Dr. Kishimoto is device for measuring the electrical resistance index of surface on charcoal. The values of refining degree on charcoal produced at low temperature (400 °C) and that on charcoal produced at high temperature (1,000 °C) were indicated to 9.0 (109Ω) and 0 (100 Ω), respectively (Park et al., 1998). The charcoal showing refining degree of 1 or less was considered to be in state of good carbonization and low in impurities (Kwon et al., 2011).
3. RESULTS and DISCUSSION
The cross-sectional area of the bamboo was divided into peripheral zone, transitional zone, central zone, and inner zone according to the arrangement of the vascular system and applied to this study (Grosser et al., 1971). The peripheral zone was excluded from observation due to difficulty in identification by getting damage during carbonization. Anatomical observations of three preserved zone were performed according to the methods presented by Jeon et al. (2018). The representative figures of three zone were selected from partial samples and were shown in Fig. 1.
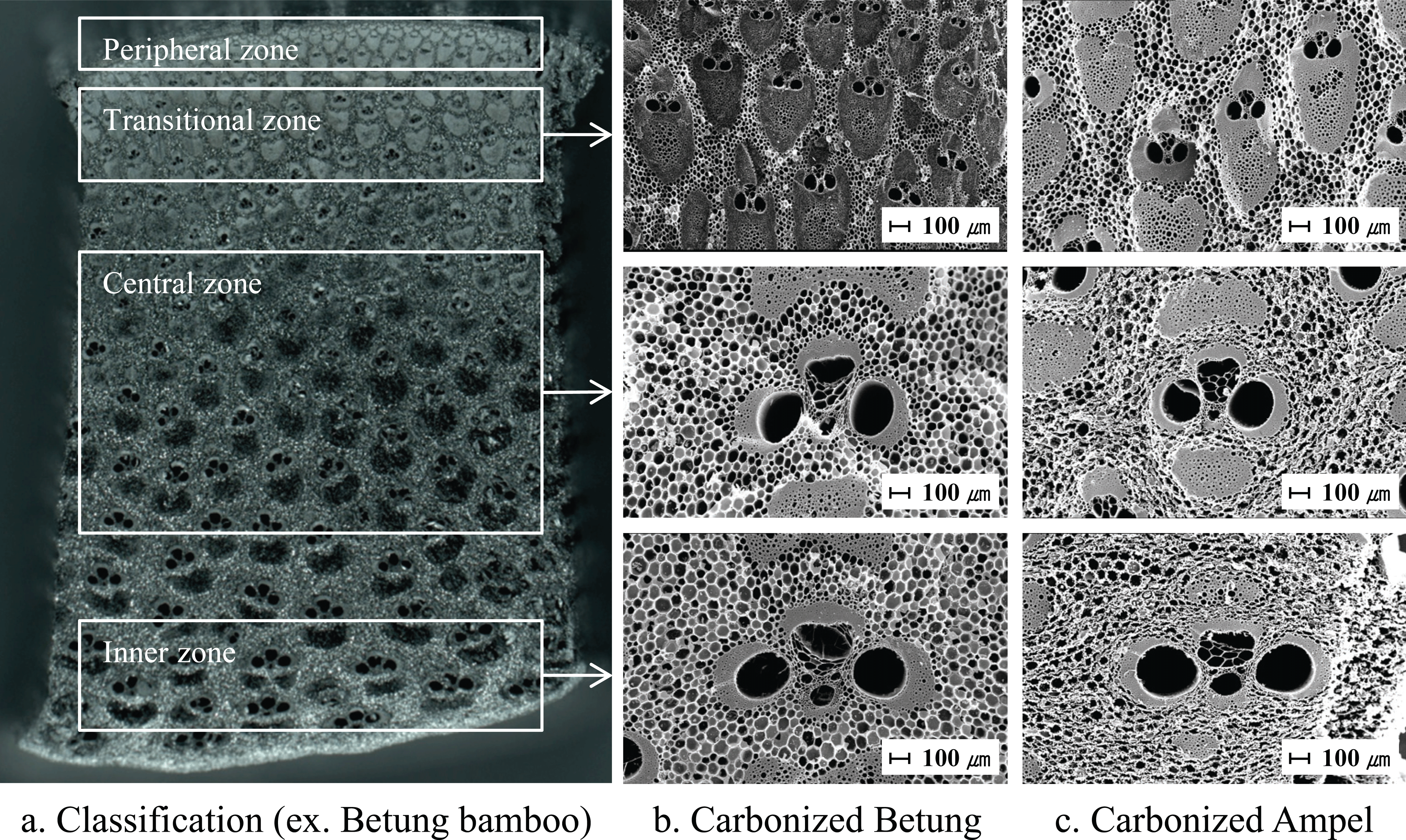
First of all, the shape of the vascular bundle was not clear in the transitional zone. The size was small and frequency of observation was high. The vascular bundle was wrapped around sclerenchyma sheath. Vascular bundle, sclerenchyma sheath, fiber bundle were fused, and these were distinguished gradually toward the central zone. In central zone, clear forms of vascular bundle consist of xylem, two large vessels, primitive phloem were observed. The sizes of vascular bundle were increased and the appearance frequency of that reduced compared to transitional zone. Clearly distinguished fiber bundles were located on inside or outside of vascular bundle. In inner zone, finally, inner zone was area adjacent to cavity space of bamboo culm, and consist of few flat vascular bundles which spread in radial direction. Occasionally, vascular bundle displayed a tangential direction. Fiber bundle was reduced or degraded. Kim et al. (2001) reported that same anatomical characteristics were observed in other Indonesian bamboos.
The SEM images taken by bamboo type and carbonization temperatures are shown in Fig. 2. Grosser et al. (1971) classified the types of bamboo vascular bundle into four types. Type I consists of only the vascular center of the vascular system, and type II consists of the vascular center of the vascular system in which the rear wall cells adjacent to the protoxylem are expanded. Type III is composed of one fiber located in the center of the tube and in the inner direction. Type IV takes the form of fiber in the outer direction in the form of type III. As a result of morphological identification, Andong bamboo was mainly observed as type III, rarely type IV. The remaining 5 species were type IV. It is consistent with the pattern of vascular bundle on Gigantochola, Bambusa, and Dendrocalamus genera (Liese, 1987).
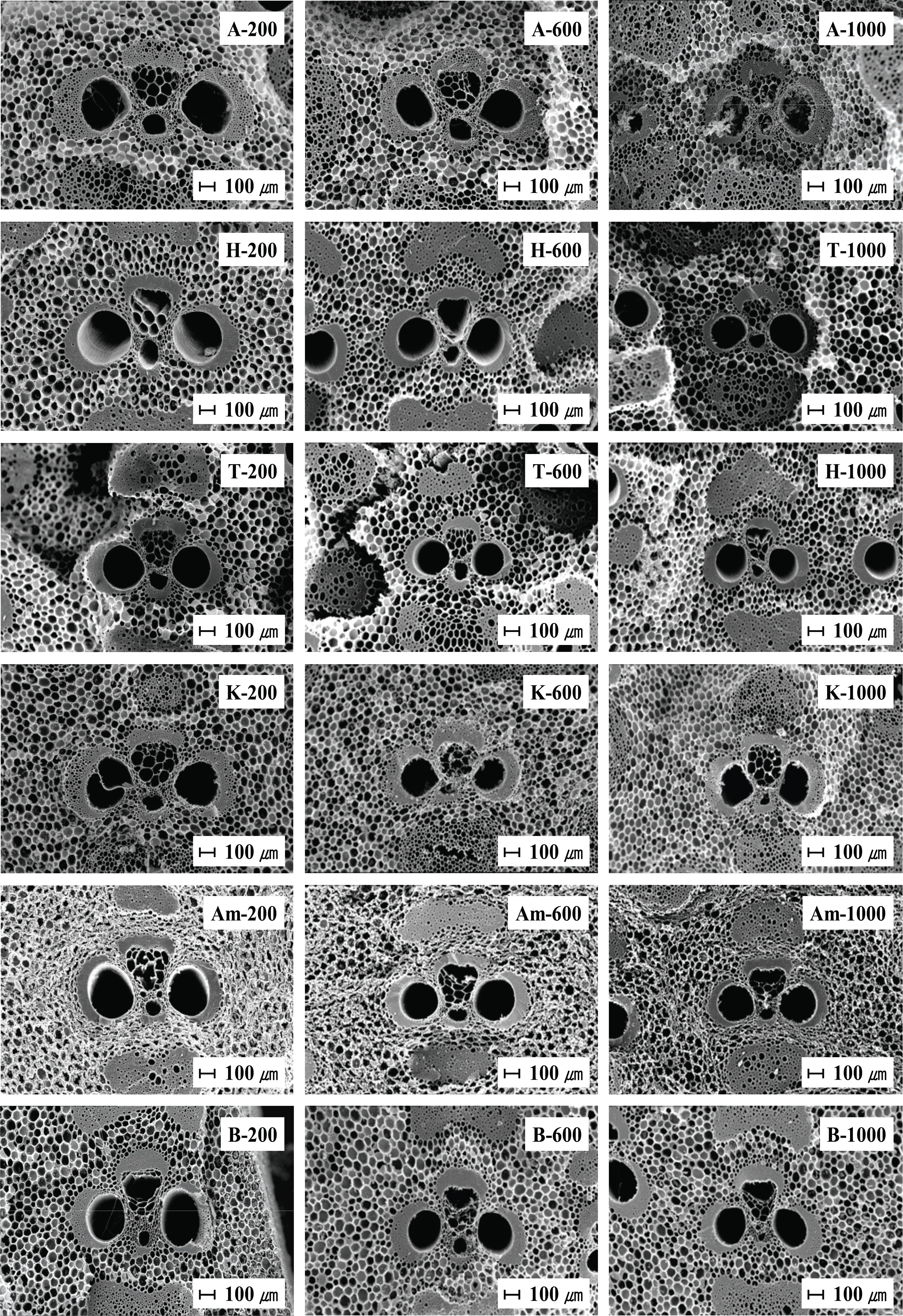
To determine the change in cell size with carbonization temperature, we selected the largest pore size and clear type of vessel. The results of measuring the diameter of the vessel in the radial and tangential directions, according to the area classification displayed in Fig. 1, were shown in Fig. 3, Fig. 4, and Fig. 5, respectively. Since there was no significant difference between vessel diameter in radial direction and vessel diameter in tangential direction, only the value of radial direction was mentioned.
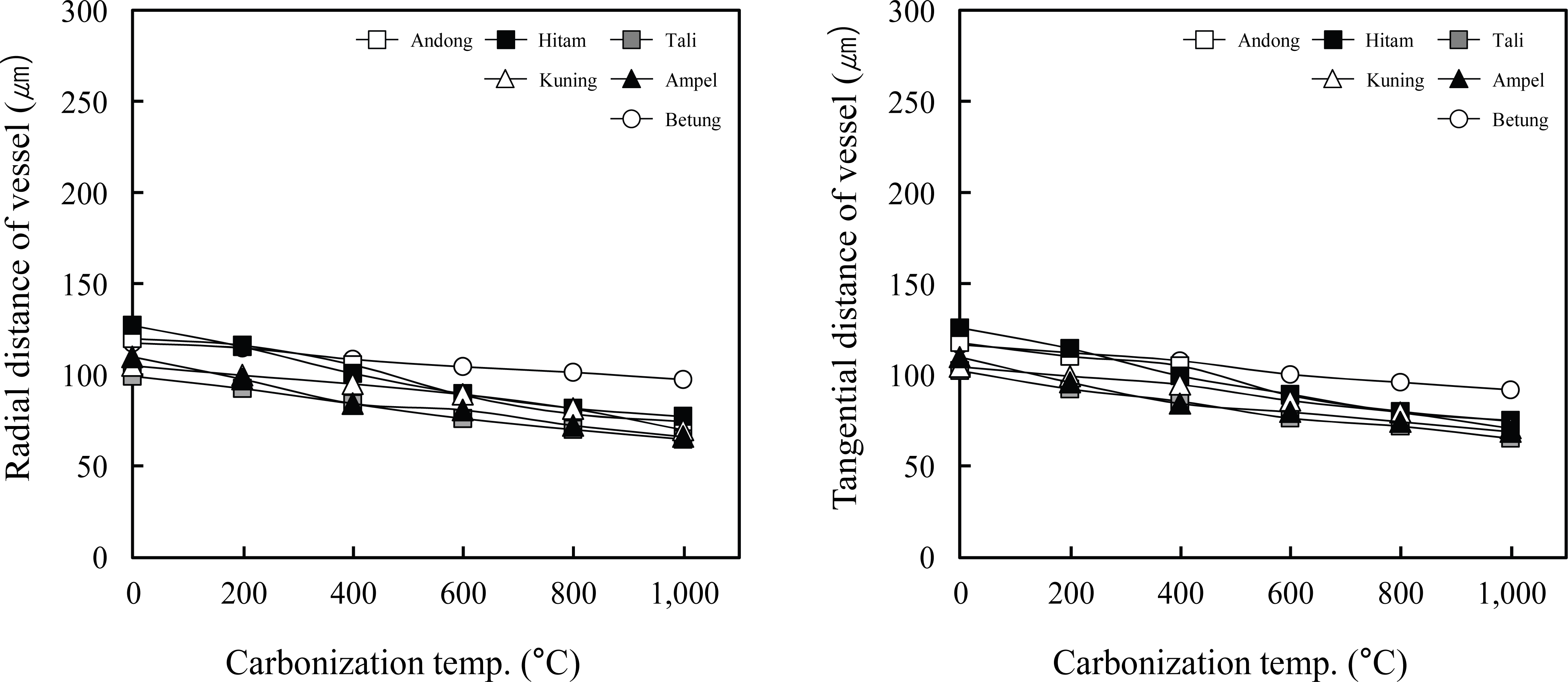
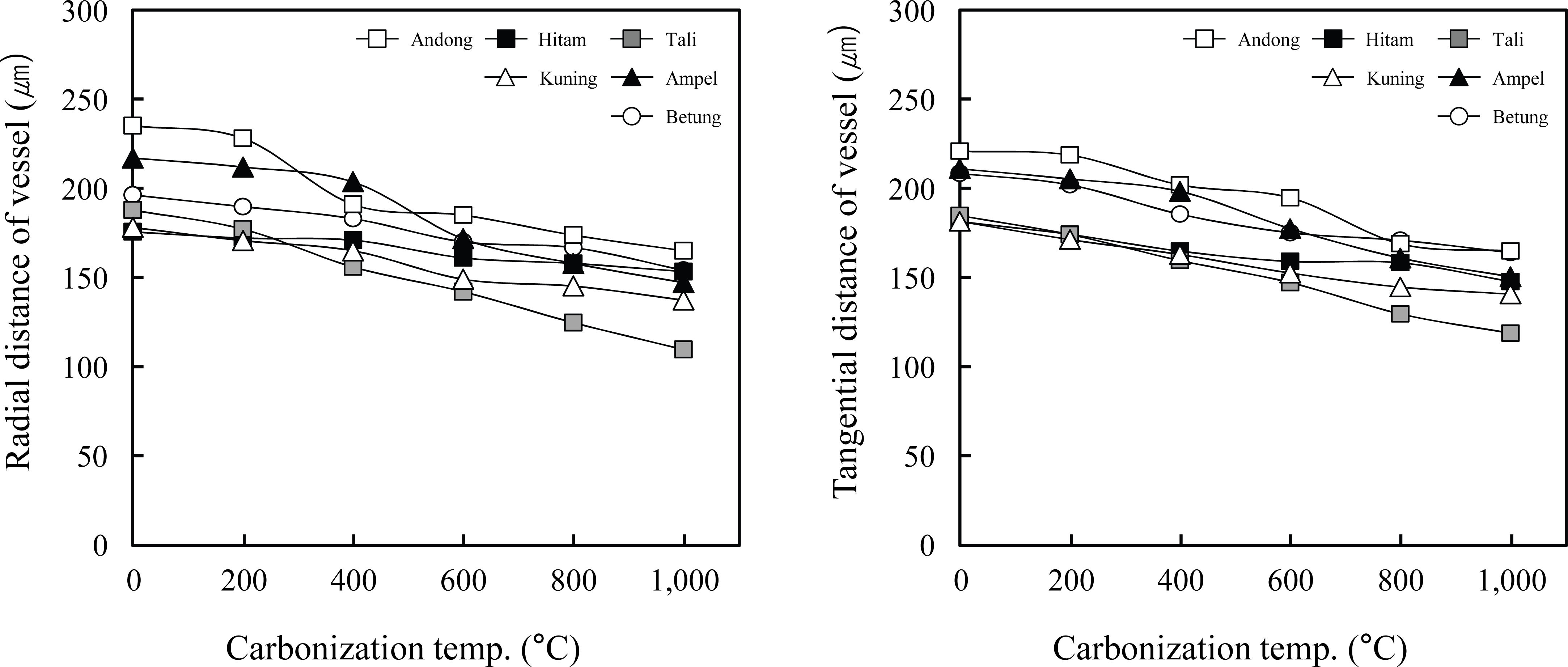

At transitional zone, the radial vessel diameters (VD) of bamboo samples were measured as 101-126 μm. As increasing carbonization temperature, VD decreased until 72-100 μm. The same tendency was observed in tangential direction. At 200 °C, Hitam bamboo showed the highest VD. After 400 °C, Betung bamboo had the highest value. Tali bamboo showed the lowest VD. Next, radial VD of uncarbonized bamboo samples in central zone were 143-233 μm, and there were no significant difference between radial VD and tangential VD. The VD decreased to 98-167 μm. Radial VD in central zone was larger than that in transitional zone, and showed clear diameter difference between species. Among bamboo species, Andong and Kuning bamboo represented the highest and lowest VD, respectively. Finally, the radial VD in inner zone were 149-235 μm in original bamboo samples. The same trend like as previous zone was observed, and VD decreased until 100-181 μm. Andong bamboo was the largest VD meanwhile, Betung bamboo showed lowest that. VD of Betung bamboo showed gentle reduction curve compared with other species. Furthermore, Betung bamboo was expected to have less cracks in carbonized product.
According to anatomical results, it was possible to directly observe the change of pore in carbonized bamboo. Generally, adsorption power of charcoal is known to be more effective for charcoal produced at 400 or 500 °C (Jiang, 2004). Although the specific surface area of bamboo charcoal increased with increasing of carbonization temperature, the physical adsorption to heavy metal having large molecular size is not sufficient due to excessive reduction of pores (Huang, et al., 2014). Abe et al. (1998) reported that charcoal produced at 600 °C had the highest adsorption ability to iodine and benzene. The charcoal produced at low temperature has been preferred in the industry of activated carbon (Park, 2007).
The physical properties of raw bamboo and carbonized bamboos were shown in Fig. 6, Fig. 7 and Table 3. The results showed that the weight reduction rate increased with increasing carbonization temperature. The values of weight reduction indicated 15 to 25% at 200 °C, 52 to 64% at 400 °C, 61 to 69% at 600 °C, 62 to 72% at 800 °C, and 64 to 75% at 1,000 °C. Significant weight reduction was observed between carbonization temperatures of 200 to 400 °C. On the other hand, there was no change between 800 and 1,000 °C. Andong bamboo showed the lower weight reduction rate compared with other species. Basu (2013) reported that a key component of the woody material were hemicellulose, cellulose and lignin, and they had different thermal decomposition behavior and degradation occurring in 225-300 °C, 305-375 °C and 250-500 °C, respectively. Chen et al. (1985) reported that bamboo consisted of holocellulose about 70% or more of the components, and they could be easily decomposed at 200 and 400 °C. Therefore, higher weight reduction ratio in this temperature range was observed in this experiment. The weight and volume reduction between the carbonization temperature of 400 and 600 °C was caused by thermal decomposition behavior of the lignin. Weight reduction below at 200 °C was mainly caused by the evaporation of water (Arias et al., 2008).
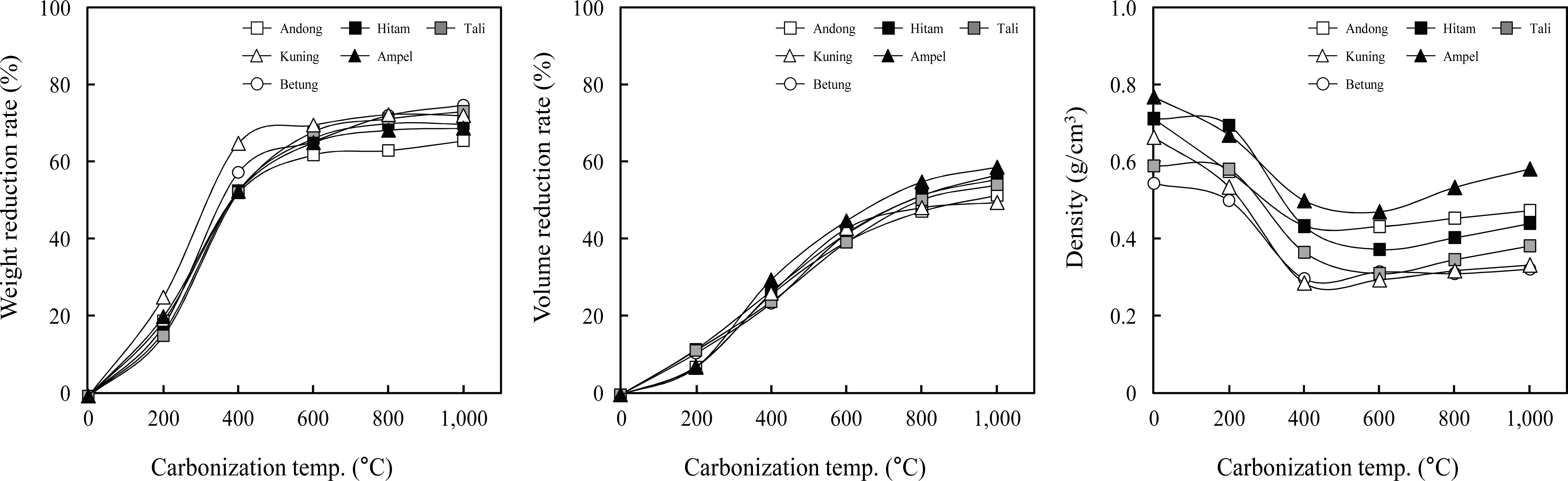
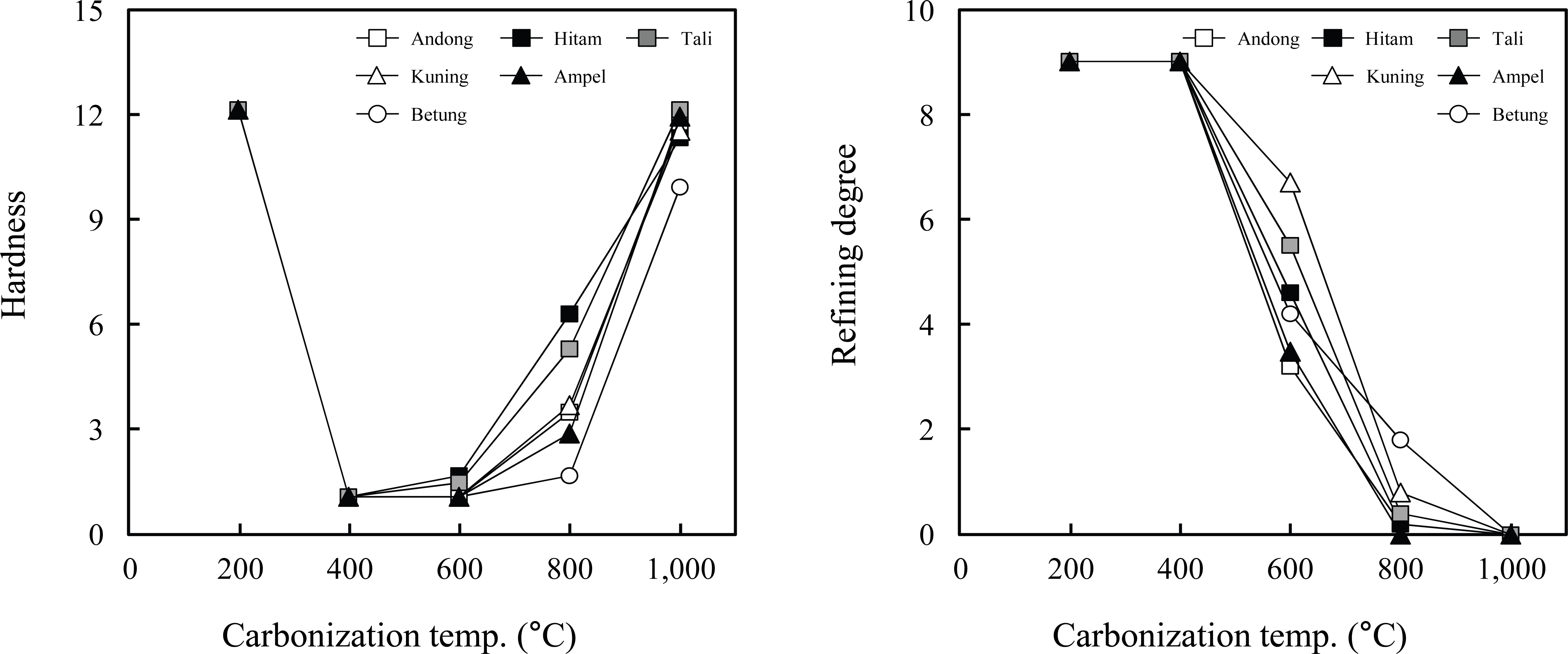
Notes: The means are averages of 10 measurements. Means within a column followed by the same capital letter are not significantly different between bamboo species and means within a column followed by the same lower case are not significantly different between carbonization temperature of each species at 5% significance level using Duncan’s multiple range test.
The volume reduction rate of bamboo increased as increasing carbonization temperature. Unlike the weight reduction, the volume reduction rate increased gradually and continued to increase after 600 °C. This might be due to carbon component. Carbon which is the main structure of bamboo, remained without emmision of volatile matter below 600 °C, and then was compressed by higher temperature (Basu, 2009). Ampel bamboo showed the highest reduction rate and Kuning showed the lowest reduction rate in this study. Kim and Hanna (2006) reported that the volume reduction rates of Quercus variablilis were about 22%, 29%, 31% and 35% at 400, 600, 800 and 1,000 °C, respectively. In this study, the volume reductions of bamboo specimens were significantly larger than that of wood.
The density was 0.4-0.6 g/cm3 for Andong, 0.4-0.7 g/cm3 for Hitam, 0.3-0.6 g/cm3 for Tali, 0.3-0.6 g/cm3 for Kuning, 0.5-0.7 g/cm3 for Ampel, and 0.3-0.5 g/cm3 for Betung. Nurhayati (1990) reported that the density of Andong, Tali, and Betung bamboos carbonized at 400 °C were 0.48 g/cm3, 0.40 g/cm3, and 0.53 g/cm3, respectively, that were similar to the results of this study. As a result of measurement of the density by carbonization temperature, it was 0.56-0.71 g/cm3 at 200 °C, 0.32-0.51 g/cm3 at 400 °C, 0.32-0.49 g/cm3 at 600 °C, 0.34-0.55 g/cm3 at 800 °C, and 0.35-0.59 g/cm3, respectively, and decreased to 600 °C, but slightly increased from 800 °C. Generally, the char yield is an important factor to determine market values, and is high correlated with density of raw materials in the producing charcoal. Hidayat et al. (2017) reported that high-density wood species (A. Manigum) resulted in higher char yield compared to low-density wood.
Fig. 7 showed the results of hardness and refinement of carbonized bamboo according to carbonization temperature. As a result, the hardness showed a high value of 12 at the carbonization temperature of 200 °C. However, the hardness decreased rapidly from 1 to 2 at carbonization at 400 to 600 °C, and then increased again after 800 °C. Park et al. (1998) reported that the hardness of carbonized Phyllostachys pubescens and Phyllostachys bambusoides were 2 at low temperature (400 °C), 5 at medium temperature (600 °C) and 8 at high temperature (1,000 °C). The electric resistance between two points on the surface of carbonized material is called the refining index which is measured with a constant pressure electrode. This is an important factor in determining the degree of carbonization of char, generally 0 for white charcoal, 1 to 8 for black charcoal, lower classified as 9 (Unrinin and Yatagai, 1989). The carbonized bamboo in this study was found 9 at 200- 400 °C, 3-6 at 600 °C, and 0 at 800-1,000 °C. Kwon et al. (2011) showed that the degree of refinement of carbonized oak at 1,000 °C was 1. The refining degree of bamboo was slightly lower than wood during same carbonization progress. Table 3 showed the results of the significance tests for the above analysis items, showing statistically differences in the groups classified by the bamboo type and the carbonization temperatures.
In order to prove this expectation and collect scientific data on anatomical experiments, the correlation between reduction rate of vessel diameter and reduction rate of whole sample was investigated. A simple regression analysis was performed to verify the statistical significance. The results are shown in Table 4 and 5. The central section of carbonized bamboo was targeted and investigated due to lower deviation.
All of the P-value (P-value) on each specimens type was lower than 0.05 and were considered statistically significant. Kim et al. (2006) suggested that the physical properties of woody material were generally related to the structure and observing the structure of charcoal according to the carbonization temperature would be important in assessing the quality of charcoal. Vessel element of carbonized bamboo measured in this study could be utilized as anatomical indicators related to part of physical properties.
4. CONCLUSION
Based on the results of physical and anatomical characteristics of Indonesian bamboo carbonized at various temperatures, we can conclude that:
The volume and weight of carbonized bamboo decreased with increasing carbonization temperature and showed the greatest change between 200 and 400 °C. Kuning and Ampel bamboo showed highest weight reduction and weight reduction, respectively.
The density of carbonized bamboo decreased until 600 °C and then increased slightly until 1,000 °C. Density was the highest in Ampel bamboo and the lowest in Betung bamboo.
According to result of hardness and refining degree test, carbonized bamboo of all species seemed to be good carbonization quality when manufactured above 800 °C.
It was confirmed that the arrangement of the vascular bundles was different depending on the position of bamboo structure in cross section. Unlike other bamboo species, the type III of vascular bundle was frequently observed in Andong bamboo.
As the results of measuring vessel diameter, it was found that the difference between radial direction and tangential direction of all species was not significant. The reduction tendency of vessel diameter on Betung bamboo was different with other species.
Correlations between reduction of whole-sample and reduction of vessel were considered to be statistically significant. Therefore, it was considered that vessel element could be used as antomical indicators related to part of physical properties.